英文資料圓鋼送料機(jī)械手,上下料機(jī)械手畢業(yè)設(shè)計(jì)
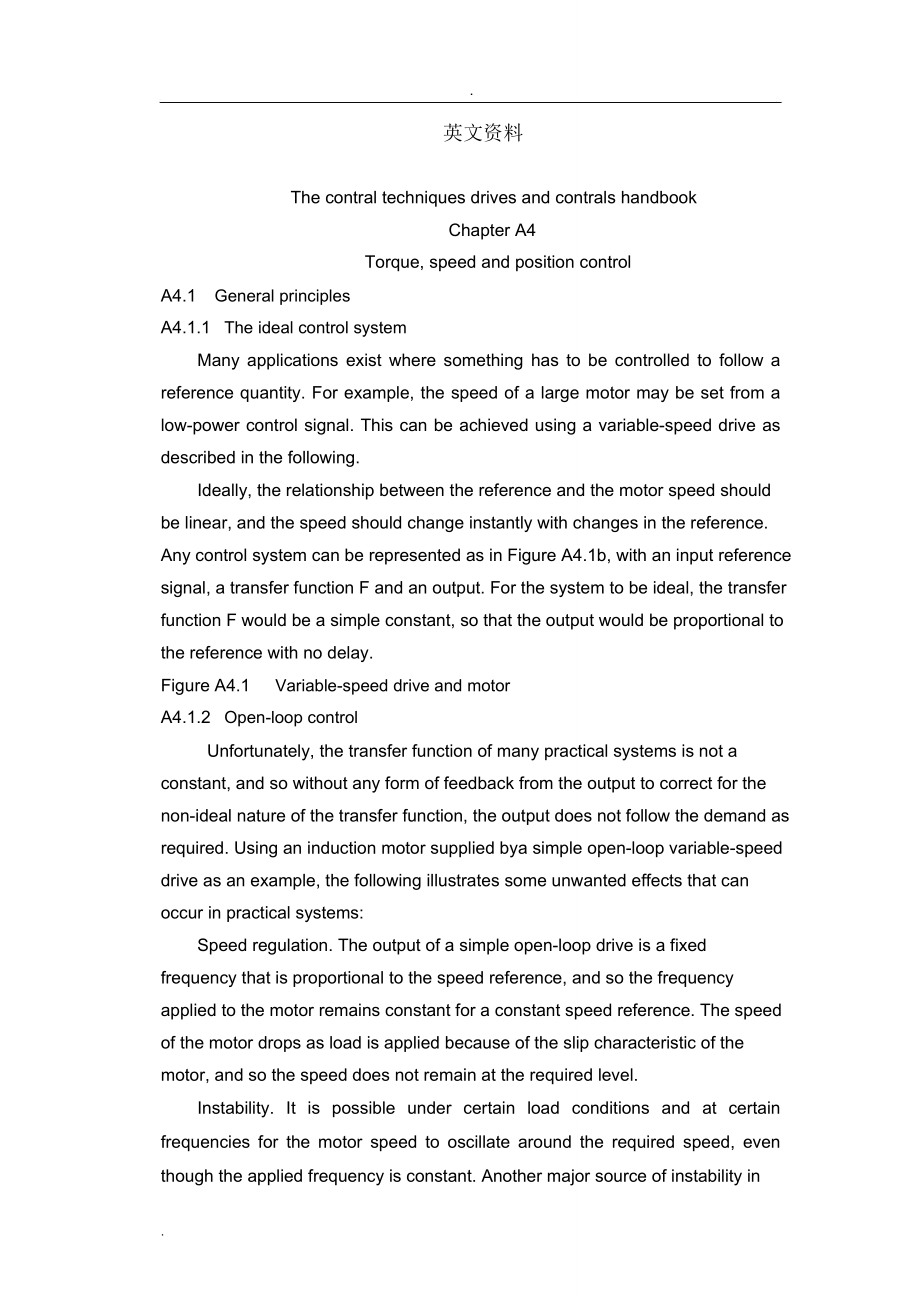


《英文資料圓鋼送料機(jī)械手,上下料機(jī)械手畢業(yè)設(shè)計(jì)》由會(huì)員分享,可在線(xiàn)閱讀,更多相關(guān)《英文資料圓鋼送料機(jī)械手,上下料機(jī)械手畢業(yè)設(shè)計(jì)(12頁(yè)珍藏版)》請(qǐng)?jiān)谘b配圖網(wǎng)上搜索。
1、 . 英文資料 The contral techniques drives and contrals handbook Chapter A4 Torque, speed and position control A4.1 General principles A4.1.1 The ideal control system Many applications exist where something has to be controlled to follow a reference quantity. For example, th
2、e speed of a large motor may be set from a low-power control signal. This can be achieved using a variable-speed drive as described in the following. Ideally, the relationship between the reference and the motor speed should be linear, and the speed should change instantly with changes in the ref
3、erence. Any control system can be represented as in Figure A4.1b, with an input reference signal, a transfer function F and an output. For the system to be ideal, the transfer function F would be a simple constant, so that the output would be proportional to the reference with no delay. Figure A4
4、.1 Variable-speed drive and motor A4.1.2 Open-loop control Unfortunately, the transfer function of many practical systems is not a constant, and so without any form of feedback from the output to correct for the non-ideal nature of the transfer function, the output does not follow the demand a
5、s required. Using an induction motor supplied bya simple open-loop variable-speed drive as an example, the following illustrates some unwanted effects that can occur in practical systems: Speed regulation. The output of a simple open-loop drive is a fixed frequency that is proportional to the spe
6、ed reference, and so the frequency applied to the motor remains constant for a constant speed reference. The speed of the motor drops as load is applied because of the slip characteristic of the motor, and so the speed does not remain at the required level. Instability. It is possible under certa
7、in load conditions and at certain frequencies for the motor speed to oscillate around the required speed, even though the applied frequency is constant. Another major source of instability in . rotating mechanical systems is low-loss elastic couplings and shafts. Non-linearity. T
8、here are many possible sources of non-linearity. If, for example, the motor is connected to a gearbox, the speed at the output of the gearbox could be affected by backlash between the gears. Variations with temperature. Some aspects of the system transfer function may vary with temperature. Fo
9、r example, the slip of an induction motor increases as the motor heats up, and so for a given load the motor speed may reduce from the starting speed when the motor was cold. Delay. With a simple open-loop inverter and induction motor there can be a delay before the motor speed reaches the demand
10、ed level after a change in the speed reference. In very simple applications such as controlling the speed of a conveyor belt, this type of delay may not be a problem. In more complex systems, such as on a machine tool axis, delays have a significant effect on the quality of the system. These are
11、just some of the unwanted effects that can be produced if an open-loop control system is used. One method that improves the quality of the controller is to use a measure of the output quantity to apply some feedback to give closed-loop control. A4.1.3 Closed-loop control The simple open-loop d
12、rive of Section A4.1.2 can be replaced with a control system as in Figure A4.2. This control system not only provides a means to correct for any error in the output variable, but also enable a stable response characteristic A4.2 Controllers in a drive A4.2.1 General Although a modern variable-
13、speed drive includes many features, the basic function of the drive is to control torque (or force), speed or position. Before proceeding to the specific details of how different types of variable-speed drive function, the theory of control for each of these quantities is discussed. A position contr
14、ol system is shown in Figure A4.5. This includes an inner speed controller, and within the speed controller there is an inner torque controller. It is possible to create a system where the position controller determines the mechanical torque that is applied to the load directly without the inner spe
15、ed and torque loops. However, the position controller would need to be able to control the complex 2 combined transfer function of the motor windings, the mechanical load and the conversion from speed to position. Therefore it is more usual to use the format shown in Figure A4
16、.5. The other advantage of this approach is that limits can be applied to the range or rate of change of speed and torque between each of the controllers. When a system is required to control speed only, the position controller is omitted, and when a system is required to control torque only, the po
17、sition and speed controllers are omitted. A position sensor is shown providing feedback for the system, but this may be replaced by a speed sensor or it may be omitted altogether as follows. Position information is required by the torque controller to function in an a.c. motor drive (see the dott
18、ed line). If position feedback is provided the speed feed-back is derived as the change of speed over a fixed sample period. Sensorless schemes are possible for speed and torque control of a.c. motors, in which case the sensor is not required. Position feedback is not necessaryfor the torque cont
19、roller in a d.c. motor drive, so a speed feedback device such as a tacho-generator can be used to provide the feed-back for the speed controller. Again, sensorless schemes are possible where a speed feedback device is not required. A4.2.2 Torque control A torque controller for a rotary motor,
20、or a force controller for a linear motor, is the basic inner loop of most variable-speed drives. Only torque control is discussed here, but the principles also apply to force control for a linear application. In order to explain the principles of torque control, the simple d.c. motor system in Figur
21、e A4.6 is used as an example. The analysis of torque control in an a.c. motor can be done in exactly the same way, provided suitable transformations are carried out in the drive. These transformations will be discussed later. The torque demand or reference (Te*) is converted by the torque control
22、ler into a current in the motor armature, and the motor itself converts the current into torque Figure A4.6 Torque and current controllers in a d.c. motor drive: (a) torque control; 3 (b) current control to drive the mechanical load. Figure A4.6b shows the system required t
23、o convert the torque reference into motor current. The torque reference (Te*) is first transformed into a current reference (ia*) by including the scaling effect of the motor flux. The motor flux, controlled by the motor field current (if ), is normally reduced from its rated level at highe
24、r speeds when the terminal voltage would exceed the maximum possible output voltage of the power circuit without this adjustment. Current limits are then applied to the current reference so that the required current does not exceed the capa-bilities of the drive. The current reference
25、(limited to a maximum level) becomes the input for the PI controller. The electrical equivalent circuit of the motor consists of a resistance (Ra), an inductance (La) and a back emf that is proportional to flux and speed (Kevc/crated). The PI controller alone could successfully control t
26、he current in this circuit because as the speed increases, the voltage required to overcome the back emf would be pro-vided by the integral term. The integral control is likely to be relatively slow, so to improve the performance during transient speed changes a voltage feed-forward term equivalent
27、to Kevc/crated is included. The combined output of the PI controller and the voltage feed-forward term form the voltage reference (va*), and in response to this the power circuit applies a voltage (va) to the motor ’ s electrical circuit to give a current (ia). The current is measured by a sensor an
28、d used as feedback for the current controller. As well as the linear components shown in Figure A4.6, the current control loop in a digital drive includes sample delays as well as delays caused by the power circuit. In practice, the response of the controller is dominated by the proportional gain
29、. In particular, if a voltage feed-forward term is used, the integral term has very little effect on the transient response. Setting of the control loop gains is clearly very important in optimising the per-formance of the control loop. One of the simplest methods to determine a suitable proporti
30、onal gain is to use the following equation: where La is the motor inductance and Ts the current controller sample time. K is a con-stant that is related to the current and voltage scaling, and the delays present in the control system and power circuit. Most modern variable-speed drives include au
31、to-tuning algorithms based on measurement of the electrical parameters of the 4 motor taken by the drive itself, and so the user does not normally need to adjust the current controller gains. It is useful to know the closed-loop transfer function of the torque controller (i.e.
32、 Te/Te*) so that the response of a stand-alone torque controller, or the effect of an inner torque controller on outer loops such as a speed controller, can be predicted. As the response is dominated by the system delays it is appropriate to represent the closed-loop response as simple gains and a u
33、nity gain transport delay as shown in Figure A4.7. The torque reference could be in N m, but it is more conventional to use a value that is a percentage of the rated motor torque. Figure A4.7a gives the transfer function when the torque controller is used alone. Kt is the torque constant of the m
34、otor in N m A21. If the torque controller is used with an outer speed controller a slightly different representation must be used, as in Figure A4.7b. The speed controller pro-duces a torque reference where a value of unity corresponds to a current level that is specified for the size or rating of t
35、he drive. From a control perspective it is unimportant whether this is the maximum current capability of the drive, the rated current or some other level. The actual level used is defined as Kc (in amperes), and should be included in the transfer function as shown. These simple models allow the d
36、rive user to predict the performance of a stand-alone torque controller or a torque controller with an outer speed loop. A4.2.3 Flux control The motor flux and hence the motorterminal voltage for a given speed are defined by the flux producing current. In the example of a simple d.c. motor dri
37、ve used pre-viously, the motor flux level is set by the field current, if. The flux controller (Figure A4.8) includes an inner current loop and an outer loop that maintains rated flux in the motor until the armature terminal voltage reaches its maximum limit. When the motor speed increases above rat
38、ed speed it then controls the field current and hence the flux, so that the armature voltage remains at the maximum required level. A4.2.4 Speed control A4.2.4.1 Basic speed control 5 Closed-loop speed control can be achieved by applying a simple PI controller aro
39、und the torque controller described previously. For the purposes of this analysis it is assumed that the load is an inertia J, with a torque Td that is not related to speed (friction is neglected). The resulting system is shown in Figure A4.10 Figure A4.10 Speed controller If the PI controller is
40、 represented as Kp t Ki/s, the torque controller is assumed to be ideal with no delays so that the unity transport delay can be neglected, and the inertia load is represented as 1/Js then the forward loop gain in the s domain is given by The closed-loop transfer function in the s domain v(s)/v*(s
41、) is given by G(s)/ [1 t G(s)]. Substituting for G(s) and rearranging gives If the natural frequency of the system is defined as vn ? (KcKtKi=J ) and the damping factor is defined as j ? vnKp/(2Ki) then As with the torque controller, it is useful to know the closed-loop response so that the re
42、sponse of a stand-alone speed controller, or the effect of an inner speed controller on an outer position loop, can be predicted. If a moderate response is required from the speed controller it is not significantly affected by system delays, and a linear transfer function such as equation (A4.4) can
43、 be used. All the constants in these equations and the delays associated with the current controllers are normally provided to users so that calculations and/or simulations can be carried out to predict the performance of the speed controller. In addition to providing the required closed-loop ste
44、p response, it is important for the system to be able to prevent unwanted movement as the result of an applied torque transient. This could be because a load is suddenly applied or because of an uneven load. The ability to prevent unwanted movement is referred to as stiffness. The com-pliance angle
45、of the system is a measure of Figure A4.11 Responses of an ideal speed controller: (a) closed-loop step response; Figure A4.12 Unwanted delays in a practical digital drive Dynamics 115UMC 3 000 rpm servo motor (Kt ? 1.6 N m A21, J ? 0.00078 kg m2) with the speed controller gains set to Kp ?
46、 0.0693j and Ki ? 14.32. As the damping factor is increased, the closed-loop response overshoot is reduced and the speed of response improves. The closed-loop response includes 10 6 per cent overshoot with a damping factor of unity because of the s term in its numerator. As
47、 the damping factor is increased, the overshoot of the response to a torque tran-sient is reduced and the response becomes slower.In this case there is no s term in the numerator and the response includes no overshoot with a damping factor of unity. It would appear from these results that the hig
48、her the proportional gain, and hence the higher the damping factor the better the responses; however, the results so far assume an ideal torque controller and no additional unwanted delays. In a real digital drive system the delays given in Figure A4.12 are likely to be present. A delay is included
49、to represent the sample period for speed measurement, but this is only relevant if the speed feedback is derived from a position feedback device such as an encoder and is measured as a change of position over a fixed sample period. The effect of the unwanted delays can be seen in the closed-loop
50、step response for a real system as shown in Figure A4.13. In each case the response of the real system has more overshoot than the ideal system. If the damping factor is set to unity then the overshoot may be acceptable, but with a damping factor of 1.25 the response is quite oscillatory and is l
51、ikely to be unacceptable. The effect of the unwanted delays is more pronounced the longer the delay and also as the set bandwidth of the speed controller is increased. The effect of the additional delays can be seen in the Bode plot of the closed-loop response of the speed controller set up to gi
52、ve unity damping factor (Figure A4.14). The frequency at the 23 dB point of the gain characteristic has increased significantly from the ideal speed controller, whereas the frequency at the 608 point of the phase characteristic is almost unchanged. If this is to be used as a stand-alone controller t
53、he gain characteristic could be used to predict the bandwidth, although it should be noted that the gain is greater than unity at some frequencies. Often the bandwidth based on the gain characteristic is the only bandwidth that is quoted, because this makes the performance appear to be better, in th
54、is case 2 000 rad s21. Figure A4.13 Effect of delays on a closed-loop step response: (a) damping factor ? 1; (b) damping factor ? 1.25 based on the phase delay 7 (672 rad s21 for this example) must be used, as this affects the performance of the outer loop. Unwanted
55、delays limit the performance of the speed controller. The quantised nature of speed feedback when it is derived from a position sensor as the change of position over a fixed sample period can also limit this. A high proportional gain in the speed controller, and hence high bandwidth, generate high-f
56、requency torque ripple and acoustic noise from the quantised speed feedback. Figure A4.14 Bode plot of closed-loop response of a speed controller The characteristic defined by equation (4.11) is shown in Figure A4.15. The required damping factor must first be selected, and from this the ratio
57、vbw/vn is taken from the graph. For example, if a damping factor of unity is required, the value of vbw/vn is 2.5. Figure A4.15 Effect of damping factor on bandwidth The definition of damping factor is j ? vnKp/(2Ki). By rearranging this and substitut-ing for natural frequency, a suitable valu
58、e for the proportional gain can be derived: Selection based on compliance angle From equation (A4.9) the steady-state response to a torque transient can be derived by setting s ? 0. The resulting change of output angle for a given steady-state torque Td is If the compliance angle is defined
59、 as the change of output angle with a steady-statetorque equal to KcKt (i.e. the torque produced by the motor with a torque producing current equal to Kc) then a suitable value of integral gain can be selected for a given compliance angle uc asThe proportional gain can then be determined in the same
60、 way as for the selection based on bandwidth using equation (A4.14). If the load (including motor) inertia is known, or it is possible for the drive to measure the load inertia using an auto-tuning algorithm, then the user need only enter the required damping factor and the speed loop bandwidth o
61、r compliance angle into the drive parameters. The drive can then automatically set suitable values for the speed controller gains. A4.2.4.3 Speed control with torque feed-forward There are situations where it is desirable to have low-speed controller gains, 8 for exampl
62、e in a winder application where the inertia of the load may change in time, Figure A4.16 Speed controller with torque feed-forward or an elevator where high gains would excite resonances in the system, making it unstable. The disadvantage of using low gains is that the response of the speed co
63、n-troller is degraded. If the load torque characteristic is known, it is possible to use a torque feed-forward term to significantly improve the response and still use low-speed controller gains. Figure A4.16 shows a system with a known inertia load using torque feed-forward. The profile generato
64、r produces the required speed reference v*, which may be a simple linear ramp that accelerates and decelerates the load. It also produces the rate of change of speed or acceleration sv* (dv*/dt in the time domain). When this is scaled to include the inertia and the system constants, it gives a curre
65、nt reference that should accelerate and decelerate the load as required. Now the speed controller is only required as a trim to compensate for inaccuracies in the torque feed-forward. The response of the system is only limited by the response of the current controllers and the sample rate of the pro
66、file generator, and not by the response of the speed controller. A4.2.5 Position control A4.2.5.1 Basic position control If position control is required, an additional outer loop is applied to the speed control-ler as shown in Figure A4.17. The position control loop only includes a proportional term Kv. An integral term is not generally required as any static error gives a speed reference v*, and the integral term in the speed controller forces the load to move until the position error
- 溫馨提示:
1: 本站所有資源如無(wú)特殊說(shuō)明,都需要本地電腦安裝OFFICE2007和PDF閱讀器。圖紙軟件為CAD,CAXA,PROE,UG,SolidWorks等.壓縮文件請(qǐng)下載最新的WinRAR軟件解壓。
2: 本站的文檔不包含任何第三方提供的附件圖紙等,如果需要附件,請(qǐng)聯(lián)系上傳者。文件的所有權(quán)益歸上傳用戶(hù)所有。
3.本站RAR壓縮包中若帶圖紙,網(wǎng)頁(yè)內(nèi)容里面會(huì)有圖紙預(yù)覽,若沒(méi)有圖紙預(yù)覽就沒(méi)有圖紙。
4. 未經(jīng)權(quán)益所有人同意不得將文件中的內(nèi)容挪作商業(yè)或盈利用途。
5. 裝配圖網(wǎng)僅提供信息存儲(chǔ)空間,僅對(duì)用戶(hù)上傳內(nèi)容的表現(xiàn)方式做保護(hù)處理,對(duì)用戶(hù)上傳分享的文檔內(nèi)容本身不做任何修改或編輯,并不能對(duì)任何下載內(nèi)容負(fù)責(zé)。
6. 下載文件中如有侵權(quán)或不適當(dāng)內(nèi)容,請(qǐng)與我們聯(lián)系,我們立即糾正。
7. 本站不保證下載資源的準(zhǔn)確性、安全性和完整性, 同時(shí)也不承擔(dān)用戶(hù)因使用這些下載資源對(duì)自己和他人造成任何形式的傷害或損失。
最新文檔
- 110中國(guó)人民警察節(jié)(筑牢忠誠(chéng)警魂感受別樣警彩)
- 2025正字當(dāng)頭廉字入心爭(zhēng)當(dāng)公安隊(duì)伍鐵軍
- XX國(guó)企干部警示教育片觀后感筑牢信仰之基堅(jiān)守廉潔底線(xiàn)
- 2025做擔(dān)當(dāng)時(shí)代大任的中國(guó)青年P(guān)PT青年思想教育微黨課
- 2025新年工作部署會(huì)圍繞六個(gè)干字提要求
- XX地區(qū)中小學(xué)期末考試經(jīng)驗(yàn)總結(jié)(認(rèn)真復(fù)習(xí)輕松應(yīng)考)
- 支部書(shū)記上黨課筑牢清廉信念為高質(zhì)量發(fā)展?fàn)I造風(fēng)清氣正的環(huán)境
- 冬季消防安全知識(shí)培訓(xùn)冬季用電防火安全
- 2025加強(qiáng)政治引領(lǐng)(政治引領(lǐng)是現(xiàn)代政黨的重要功能)
- 主播直播培訓(xùn)直播技巧與方法
- 2025六廉六進(jìn)持續(xù)涵養(yǎng)良好政治生態(tài)
- 員工職業(yè)生涯規(guī)劃方案制定個(gè)人職業(yè)生涯規(guī)劃
- 2024年XX地區(qū)黨建引領(lǐng)鄉(xiāng)村振興工作總結(jié)
- XX中小學(xué)期末考試經(jīng)驗(yàn)總結(jié)(認(rèn)真復(fù)習(xí)輕松應(yīng)考)
- 幼兒園期末家長(zhǎng)會(huì)長(zhǎng)長(zhǎng)的路慢慢地走
相關(guān)資源
更多