麥肯錫供應鏈管理-流程與績效(英文原版).ppt
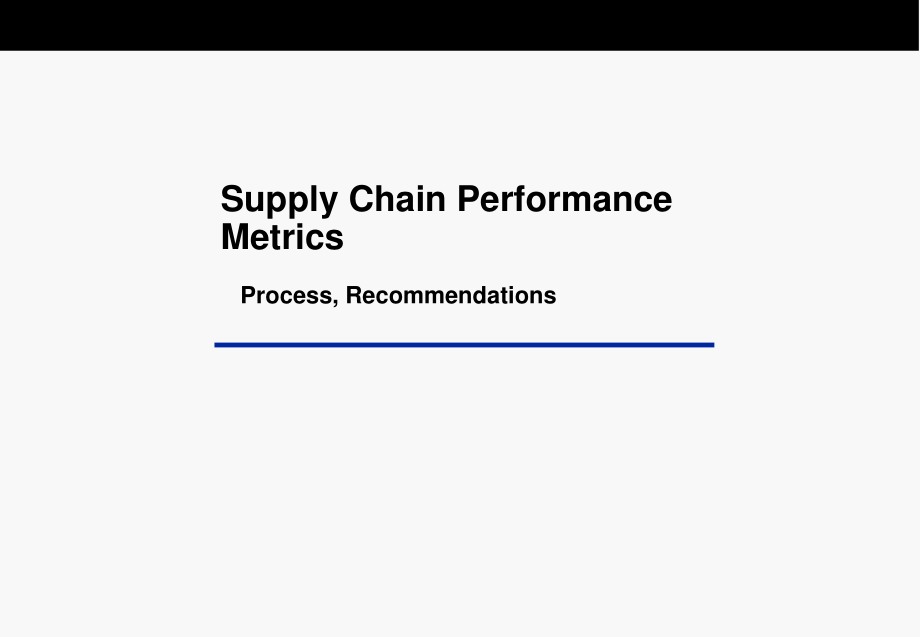


《麥肯錫供應鏈管理-流程與績效(英文原版).ppt》由會員分享,可在線閱讀,更多相關《麥肯錫供應鏈管理-流程與績效(英文原版).ppt(28頁珍藏版)》請在裝配圖網(wǎng)上搜索。
1、Supply Chain Performance Metrics Process, Recommendations - 2 - This document gives an overview of the different metrics that can be used to measure supply chain performance The Supply Chain CoEs objective is to define a benchmarking framework capable of: Comparing generic metric performances for us
2、e on projects. Capturing further benchmarking data in a consistent format. The London Shops task: Develop an overview of the different metrics to measure supply chain performance. Select the most important metrics that can be used across industries. Discuss how the most important metrics link other
3、operational metrics within each stage of the supply chain. Suggest how the supply chain CoE should continue concerning this topic. - 3 - We used information from several sources during our project Internal and external documents: High level benchmarking framework for supply chain performance (H .Coo
4、k): Shop Study (March 1997) accessing information from available experts and past projects. Supply chain benchmarks and best practice (Dow Polyurethane In-Industry and In-Company similarities and differences. Blind-sided Intuition Opinion Discussion Survey Functional Measures KPIs External Best Prac
5、tice Qualitative Quantitative Objective 1 KPI KPI KPI KPI Objective 2 KPI and xxx measure Dual service measures (cost In-Industry; and In-Company similarities and differences. Interface the solution to the current clients measures, systems, processes and culture: . . . and guide migration over time.
6、 Ensure accountability for collecting and actioning is clear. - 11 - Proposed Supply Chain KPIs KPIs help to identify “where” the performance problem is within the supply chain, and steer towards areas to explore “why”. Accuracy (as % of sales) Customer satisfaction % of satisfied customers Total cy
7、cle time Time (for customer) from placing order to receiving goods % of products delivered on time Total supply chain cost as % of sales Cost per product sold as % of sales Cost as % of sales % of products delivered according to customer order (quantity/quality) % of customers satisfied with service
8、 % of products ordered already in stock Defect rate of products as % of production % of goods delivered according to order (quantity/quality) by supplier Time from order placement to reception of goods Time from production order to delivery into finished product warehouse Downtime as % of total prod
9、uction time % of goods delivered on time by supplier Cost as % of sales Cost as % of sales Cost as % of sales Number of stock turns/years Total Supply Chain Forecasting Purchasing Inbound Logistics Manufacturing Maintenance Inventory Management Marketing Order Entry; Packaging; Product quality; Ship
10、ping Error # of complaints as % of total orders # of customer contacts per order # of enquiries (including complaints) that were not answered to the customers satisfaction # of information requests as % of customer orders % of calls abandoned, answered by recording, delayed % of customer contact thr
11、ough customer service % of customer follow-up handled by Customer Service Representative; Department Manager; Field Representative; Responsible Manager % of invoices containing errors % of orders delivered complete and without error (order fill rate) % of orders that are damaged on arrival at custom
12、er site % of respondents that can handle complaints without handing off to other person/dept. Average % of disputed invoices % of products delivered according to customer order (quantity/quality) Degree of utilisation of facilities (%) Equipment utilisationload Equipment utilisationweight Time from
13、order placement to start of delivery Customer satisfaction (rating) % of satisfied customers % of information on credit history limit available On-line % of information on open-order history available On-line % of information on outstanding balance available On-line % of information on pricing avail
14、able On- line % of information on product history available On-line % of information on product ID code available On-line % of information on shipping points available On-line Ratio of operations labour as % of passive labour Average # of orders rejected Average product time in warehouse No. of days
15、 consumption in stock (A- goods) No. of days consumption in stock (B- goods) No. of days consumption in stock (C- goods) No. of days safety stock (A-goods) No. of days safety stock (B-goods) No. of days safety stock (C-goods) No. of products with duplication stock Planned days of inventory on hand %
16、 of accounts receivable settled before due date % of accounts receivable settled in 130 days % of accounts receivable settled in 3160 days % of accounts receivable settled in 91 days % of accounts receivable settled in 6190 days Delivery time % of products delivered early # of deliveries per manhour
17、 % of orders delivered on time (as defined by customer) % of orders delivered with an average delay of 1 month Average # of days delay after scheduled ship date Total cycle time Time (for customers) from placing order to receiving goods % of products delivered on time Average customer quoted leadtim
18、e Average leadtime from receipt of order to shipment Average time taken to access information Cash to cash cycle Longest customer quoted leadtime New product introduction time Product changeover time Shortest customer quoted time Time from receipt of order to receipt of shipment by customer Time tak
19、en to rectify incorrect or damaged orders Average time taken to respond to requests Cost as % of sales # of stock turns/year Cost as % of cost of goods purchased Carried worth of expired lots A-goods as a percent of inventory Average stock level B-goods as a percent of inventory C-goods as a percent
20、 of inventory Inventory cost as % of total assets (gross assets) Maximum stock level Minimum stock level Cost as % of sales Cost as % of sales Cost per delivery # of route miles per delivery # of warehousing facilities # of warehousing of locations % of transportation units owned by company Cost per
21、 order Cost per route Total supply chain cost as % of sales Cost per product sold as % of sales % of profit from base purchase % of profit from increased purchases % of profit from premium pricing % of revenue generated by largest customer group (top 20%) Cost per product sold as % of sales Operatin
22、g profit per customer as % of operating costs per customer Total cost per order Total cost per unit produced Cost as % of sales Source: H. Cook - 14 - Given the multitude of metrics we suggest to analyse supply chain performance using a hierarchy of measures . . . digging through the causal tree to
23、improve business performance. Key KPI Supporting Metrics Other Operational Measures Type of Measure Example Highest Level Use Who Uses It Forecasting accuracy (as % of sales) Integrated supply chain Generic benchmarking Consultant Top management Supply chain stage manager % of suppliers connected vi
24、a EDI Supply chain stage diagnostic Consultant Supply chain stage manager A-goods as a % of inventory Supply chain stage diagnostic Supply chain stage manager Objective Find “where” the problem is within the supply chain Identify the “why” within the supply chain stage Give more in- depth informatio
25、n about supply chain stage - 15 - For example, the quality of customer service performance can be clearly measured at three different levels Quality Key KPIs Suggested Supporting Metrics Other Operational Measures % of customers satisfied with service # of complaints as % of total orders # of phone
26、calls to customer service department per order shipped # of complaints due to: order entry, packaging, shipping error, . . .) % of calls abandoned, answered by recording, delayed, . . . % of complaints handled by: customer service rep., department manager, . . . KPIs will be measured for generic ben
27、chmarks, whilst operational metrics will be measured by a customer service manager. . . . # of complaints that were not answered to customer satisfaction Average number of orders rejected - 16 - Key KPIs Suggested Supporting Metrics Other Operational Measures Outbound logistics performance . . . % o
28、f products delivered according to customer order (quantity/quality) (These can often be driven by customer service metrics) Degree of utilisation of facilities (%) Equipment utilisation (load/weight) Delivery time % of orders delivered on time (as defined by customer) # of deliveries/man hour % of o
29、rders delivered early % of orders delivered with an average delay of 1 month Average number of days of delay after scheduled ship date Cost as % of sales # of route miles per delivery # of warehousing facilities/locations % of transportation units owned by company . . . Cost per delivery Cost per or
30、der Cost per route Quality Time Cost - 17 - Key KPIs Suggested Supporting Metrics Other Operational Measures Quality Time Cost For maintenance, commonly used supply chain performance metrics relate to time and cost The quality of maintenance is commonly measured by lag measures in terms of cost or a
31、s a production measure (downtime). We suggest the use of two lead measures that proactively monitor maintenance performance. . . . Number of service contract Number of training days for maintenance staff Downtime as % of total production time Cost as % of sales Cost per unit produced Downtime due to
32、 parts shortage (or stock outs in general) Hours of unplanned downtime - 18 - Just remember . . . A large number of metrics exist, so be selective. A step by step approach to measuring supply chain performance should be undertaken in order to avoid being overwhelmed by data. The following segmentati
33、on gives us such an approach: 23 key KPIs allow us to identify where the problems exist within the supply chain. Key supporting metrics then allow us to answer why the problems exist. Operational metrics allow us to go analyse the supply chain stage in more detail. The “right” set of metrics does no
34、t exist for a given industry or even a specific company. The “right” set of metrics is dynamic like the business it measures and will change with the type of industry/problem and over time. . . . - 19 - Next Steps for the Supply Chain CoE Agree on how you will go forward after this project. Agree on
35、 objectives, scope and accountabilities. Eg. Discuss if each GMT needs its own supply chain metrics. Further populate the supply chain benchmarking framework. See example for Purchasing. Championing (S. Beck/Disc. Heads). . . . and roll-out. Continuous improvement process. - 20 - Appendix KPI Defini
36、tions. Causal Trees: Quality Time Cost - 21 - Purchasing Data: KPIs H. Cook shop research. Industry Sector Benchmarking Range/Best Practice (Validate source) Average Manufacturing (Validate source) Chemicals Best Practice (Validate source) Global Chemical Purchasinga 0.06%3.0% 0.30% Measure QUAL ITY
37、 TIM E COS T Automotive (Global)a Pharma. (Global)a Eng./Constr . (Global)a % of correct orders placed # of alternative sources of supply # of suppliers involved in product development/innovation # of active suppliers per purchasing professional # of vendors products ordered % of all active supplier
38、s that account for 90% of total purchase value % of purchases handled by purchasing department Purchasing head count as % of total head count % purchases handled by purchasing function % spend on long-term basis (2yrs) % firms using consortium buying Training per purchasing professional % of account
39、s payable handled before due date % of accounts payable handed in 130 days % of accounts payable handled in 3160 days % of accounts payable handled in 6190 days % of accounts payable handled in over 90 days % of suppliers connected via EDI Average actual time to developed/negotiate a contract % good
40、s delivered on time by supplier Time from order placement to receipt of goods Cost as % of sales Cost as % of total costs Cost of orders purchased (range Cost of vendor transactions (range) Cost of expedite repair materials Purchasing spend per supplier Purchasing spend per purchasing Purchase Dept.
41、 expense ( per $ sales) 65% 29% 4% 1% 1% 9 weeks 59% $24.8m 31/100 18 cos 12bn 226 weeks 50% 42% 6% 1% 1% 61% 26.5 15/100 !0 cos $23bn 5087 20% 110% 6182 9267 575% 0.3%4.5% 165 7.9% (18% xxx) 82 1.4% 82% 50% 22 26 1% 97% 272 0.4% 27% 26% 42 hrs 30 21 5.5% 11% 79% 33% 1% 19% 26 10/100 19 cos $3.5bn 4
42、 59/100 - 22 - Service Product Delivery Wrong Info. Higher Prices Than Competitors Higher Margin Than Competitors Badly Set Customer Expectations Wrong Order Information Unable to Meet Customer Demand Produced Faulty Goods Products Damaged After Mfg Price Product Quantity Product Quality Delivered F
43、aulty Goods Quality - 23 - Did Not Have the Right Materials Forecasts Incorrect Information Failure Human Failure Technical Failure Late Arrival Late Departure Late Arrival Information Failure Infrastructure Failure Product Failure Wrong Information Info. Sent to Wrong Person Information Sent Late P
44、roduct Not in Stock Faulty Product Human Failure Technical Failure Un- controllable Factors Information Failure Infrastructure Failure Human Failure Did Not Produce Anymore Did Not Produce Enough Information System Failure Technical Failure Human Failure Could Not Produce To Capacity Total Capacity
45、Too Small Other Production Priorities Materials Not Delivered Wrong Materials Delivered Materials Delivered Late Suppliers Forgot We Did Not Order Suppliers Got Order Wrong We Got Order Wrong Suppliers Delivered Late We Ordered Late Time - 24 - Purchasing Cost Customer Service Cost Inventory Cost De
46、livery Cost Production Cost Too Much Stock Wrong Type of Products Obsolete Stock Infrastructure Stock Human Resources Costs Used More Expensive Materials Materials Arrived Late Human Failure Technical Failure Human Resource Cost Maintenance Cost Complaints Wastage Planning Used More Raw Materials Hi
47、gher Cost Than Competitor Ordered Late Different Materials People Systems Same Suppliers Worse Deal Different Suppliers Skills Product MOT Promotion Sales Volumes Lower Dont Know How to Negotiate Many Suppliers Cost - 25 - Definitions for the Supply Chain KPIs Forecasting: Accuracy (as %of sales). P
48、urchasing: % active suppliers for 90% spend. Time from order placement to receipt. % of goods delivered on time. Cost as % sales. Inbound Logistics: % of good delivered according to order (quantity/quality) by supplier. Time from order placement to reception of goods. % of goods delivered on time by
49、 supplier. - 26 - Back Up Panels - 27 - Drivers and KPIs are however linked throughout the supply chain They form a “causal tree” along the supply chain which varies between industries and over time They do not simply drive and explain just quality, time or cost, they may drive or explain all three
50、We have simplified the tree in this presentation: We have left out the links and kept the model on a generic level We have not developed a “perfect” model Function/Process Stage Quality Time Cost - 28 - These operational metrics should be used with care Ideally they should support key KPIs by explai
51、ning why performance is meeting/below expectations. They should also give an in-depth picture into how well each supply chain stage is performing. However, their use calls for judgement: They vary across companies and industries (which explains the large quantity of metrics available). Many are not
52、directly linked to key KPIs but are useful secondary indicators of performance. They do not necessarily link to performance at just one stage in the supply chain (but accountability must be assigned to someone within one stage). For example: inaccurate order making could lead to more time being spent on puchasing, suppliers delivering the wrong goods and/or suppliers delivering the goods late.
- 溫馨提示:
1: 本站所有資源如無特殊說明,都需要本地電腦安裝OFFICE2007和PDF閱讀器。圖紙軟件為CAD,CAXA,PROE,UG,SolidWorks等.壓縮文件請下載最新的WinRAR軟件解壓。
2: 本站的文檔不包含任何第三方提供的附件圖紙等,如果需要附件,請聯(lián)系上傳者。文件的所有權益歸上傳用戶所有。
3.本站RAR壓縮包中若帶圖紙,網(wǎng)頁內容里面會有圖紙預覽,若沒有圖紙預覽就沒有圖紙。
4. 未經權益所有人同意不得將文件中的內容挪作商業(yè)或盈利用途。
5. 裝配圖網(wǎng)僅提供信息存儲空間,僅對用戶上傳內容的表現(xiàn)方式做保護處理,對用戶上傳分享的文檔內容本身不做任何修改或編輯,并不能對任何下載內容負責。
6. 下載文件中如有侵權或不適當內容,請與我們聯(lián)系,我們立即糾正。
7. 本站不保證下載資源的準確性、安全性和完整性, 同時也不承擔用戶因使用這些下載資源對自己和他人造成任何形式的傷害或損失。