怎樣對鈦合金攻絲.doc
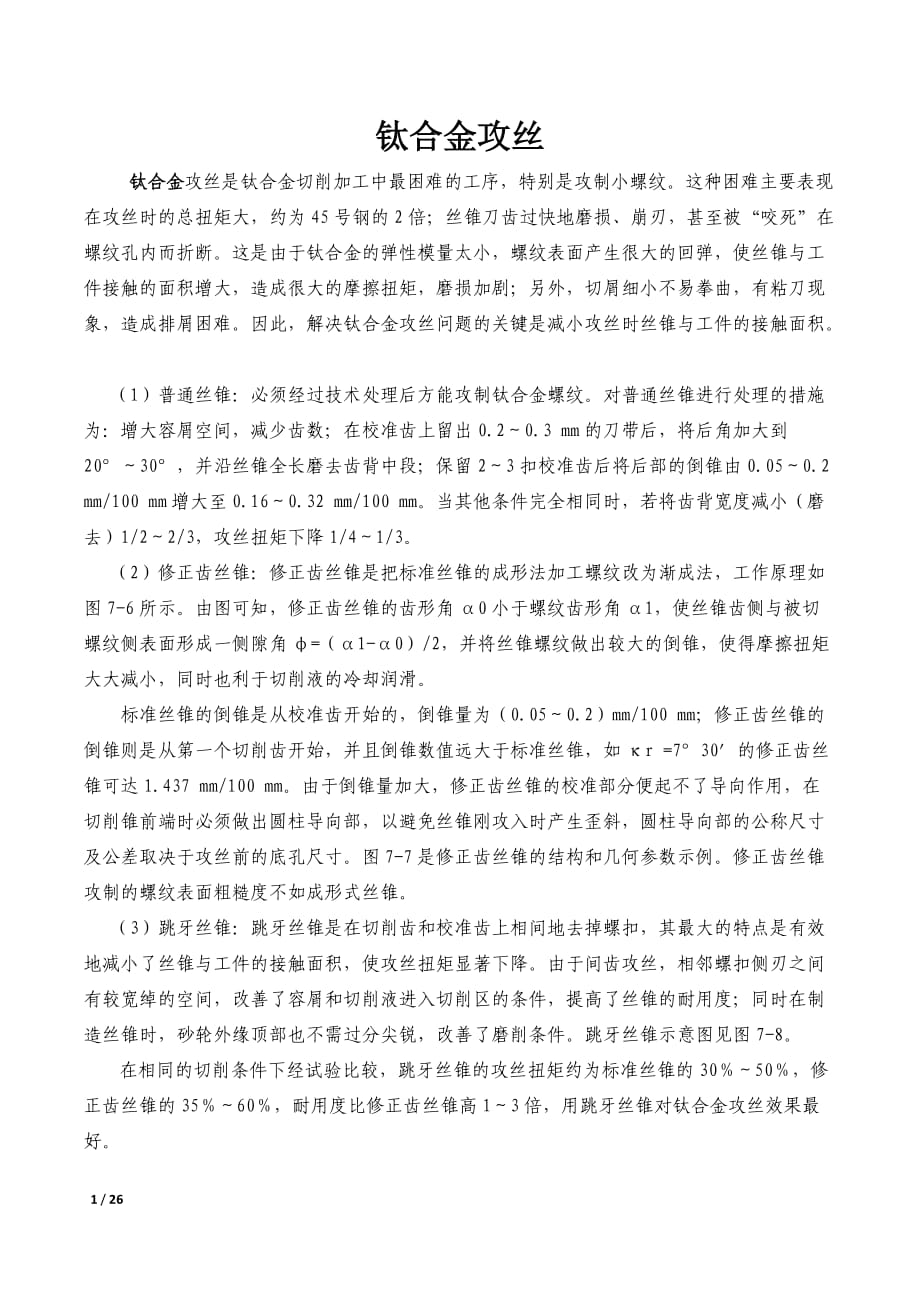


《怎樣對鈦合金攻絲.doc》由會員分享,可在線閱讀,更多相關(guān)《怎樣對鈦合金攻絲.doc(26頁珍藏版)》請在裝配圖網(wǎng)上搜索。
1、鈦合金攻絲 鈦合金攻絲是鈦合金切削加工中最困難的工序,特別是攻制小螺紋。這種困難主要表現(xiàn)在攻絲時的總扭矩大,約為45號鋼的2倍;絲錐刀齒過快地磨損、崩刃,甚至被“咬死”在螺紋孔內(nèi)而折斷。這是由于鈦合金的彈性模量太小,螺紋表面產(chǎn)生很大的回彈,使絲錐與工件接觸的面積增大,造成很大的摩擦扭矩,磨損加?。涣硗?,切屑細小不易拳曲,有粘刀現(xiàn)象,造成排屑困難。因此,解決鈦合金攻絲問題的關(guān)鍵是減小攻絲時絲錐與工件的接觸面積。 (1)普通絲錐:必須經(jīng)過技術(shù)處理后方能攻制鈦合金螺紋。對普通絲錐進行處理的措施為:增大容屑空間,減少齒數(shù);在校準齒上留出0.2~0.3 mm的刀帶后,將后角加大到20~30,并沿絲錐
2、全長磨去齒背中段;保留2~3扣校準齒后將后部的倒錐由0.05~0.2 mm/100 mm增大至0.16~0.32 mm/100 mm。當(dāng)其他條件完全相同時,若將齒背寬度減?。トィ?/2~2/3,攻絲扭矩下降1/4~1/3。 (2)修正齒絲錐:修正齒絲錐是把標準絲錐的成形法加工螺紋改為漸成法,工作原理如圖7-6所示。由圖可知,修正齒絲錐的齒形角α0小于螺紋齒形角α1,使絲錐齒側(cè)與被切螺紋側(cè)表面形成一側(cè)隙角φ=(α1-α0)/2,并將絲錐螺紋做出較大的倒錐,使得摩擦扭矩大大減小,同時也利于切削液的冷卻潤滑。 標準絲錐的倒錐是從校準齒開始的,倒錐量為(0.05~0.2)mm/100 mm;
3、修正齒絲錐的倒錐則是從第一個切削齒開始,并且倒錐數(shù)值遠大于標準絲錐,如κr =730′的修正齒絲錐可達1.437 mm/100 mm。由于倒錐量加大,修正齒絲錐的校準部分便起不了導(dǎo)向作用,在切削錐前端時必須做出圓柱導(dǎo)向部,以避免絲錐剛攻入時產(chǎn)生歪斜,圓柱導(dǎo)向部的公稱尺寸及公差取決于攻絲前的底孔尺寸。圖7-7是修正齒絲錐的結(jié)構(gòu)和幾何參數(shù)示例。修正齒絲錐攻制的螺紋表面粗糙度不如成形式絲錐。 (3)跳牙絲錐:跳牙絲錐是在切削齒和校準齒上相間地去掉螺扣,其最大的特點是有效地減小了絲錐與工件的接觸面積,使攻絲扭矩顯著下降。由于間齒攻絲,相鄰螺扣側(cè)刃之間有較寬綽的空間,改善了容屑和切削液進入切削區(qū)的條件
4、,提高了絲錐的耐用度;同時在制造絲錐時,砂輪外緣頂部也不需過分尖銳,改善了磨削條件。跳牙絲錐示意圖見圖7-8。 在相同的切削條件下經(jīng)試驗比較,跳牙絲錐的攻絲扭矩約為標準絲錐的30%~50%,修正齒絲錐的35%~60%,耐用度比修正齒絲錐高1~3倍,用跳牙絲錐對鈦合金攻絲效果最好。 (4)螺紋底孔:對鈦合金攻絲一般按牙高率(螺孔實際牙型高度與理論高度的比率)不超過70%為依據(jù)來選取底孔直徑大小,即螺紋底孔直徑d1=d0-0.757 8p(d0為螺紋公稱尺寸,p為螺矩)。小直徑或粗牙螺紋牙高率可取大一些,被加工材料強度低或螺紋深度小于螺紋基本直徑時,可適當(dāng)增大牙高率,但過大會增大攻絲扭矩,
5、甚至折斷絲錐。為保證攻絲精度和表面質(zhì)量,螺紋底孔應(yīng)為鉸后的孔。 鈦合金的攻絲速度要根據(jù)材料的類型和硬度來確定。α鈦合金的攻絲速度一般取Vc=7.5~12 m/min,α+β鈦合金取Vc=4.5~6 m/min,β鈦合金取Vc=2~3.5 m/min;鈦合金的硬度≤HB350時選用較高的切削速度,反之選用較低的切削速度。對鈦合金攻絲時,一般用含Cl、P的極壓切削液效果較好,但含Cl的極壓切削液攻絲后必須清洗干凈,防止零件晶間腐蝕;也可用蓖麻油60%、煤油40%的混合油作切削液。 鉆孔為半封閉式切削,對鈦合金鉆孔過程中切削溫度很高,鉆孔后回彈大,鉆屑長而薄,易粘結(jié)而不易排出,經(jīng)常造成鉆頭被咬住
6、、扭斷等惡性事故。因此要求鉆頭具有高的強度和好的剛性,鉆頭與鈦合金的化學(xué)親和性要小,最好采用硬質(zhì)合金鉆頭,但目前最常用的仍是麻花鉆,經(jīng)過采取一些措施改進后,也能取得較好的效果。 (1)改進鉆頭:為滿足對鈦合金鉆孔的需要,應(yīng)對麻花鉆采取以下改進措施: 加大鉆頭頂角,2Ф=135~140;增大鉆頭外緣處后角,取12~15;增大螺旋角,p=35~40;增大鉆心厚度,取(0.22~0.4)do(do為鉆頭直徑)。 采用“S”形或“X”形修磨鉆頭橫刃,橫刃長度b=(0.08~0.1)do,同時保證橫刃的對稱度≤0.06 mm。兩種形式的橫刃均可形成第二切削刃,起到分屑作用和
7、減小鉆孔時的軸向力。 最常用的是在麻花鉆上磨出適于對鈦合金鉆孔的切削刃形,即鈦合金群鉆,其切削部分的形狀見圖7-1。圖中外內(nèi)刃頂角2φ和2φ′在鉆頭直徑do>3~10mm時均為130~140,do>10~30 mm時為125~140;外刃后角α在do>3~10 mm時為12~18,do>10~30 mm時為10~15;橫刃斜角ψ=45;內(nèi)刃前角γτ=-10~-15;內(nèi)刃斜角τ=10~15;圓弧刃后角aR=18~20。 鈦合金群鉆的有關(guān)參數(shù)和鉆削用量見表7-8和表7-9。 鈦合金鉆削和攻絲的工藝分析及研究 摘 要:主要敘述了鈦合金的性能特點,同時分析了影響鈦合金鉆削和
8、攻絲加工的主要因素,并提出改進鈦合金鉆削和攻絲加工的工藝參數(shù)和相應(yīng)措施。 關(guān)鍵詞:鈦合金;鈦合金鉆削;鈦合金攻絲 0 引言 鈦合金材料重量輕,密度是4.4 kg/m3,比強度高,是航空航天等領(lǐng)域的重要金屬材料。但其加工性能較差,特別是鉆孔和攻絲的效率很低,在很大程度上制約著產(chǎn)品中鈦合金零件的加工質(zhì)量和生產(chǎn)效率。這里分析了鈦合金材料及其切削特性在鉆孔和攻絲中表現(xiàn)出來的具體特點,特別對刀具材料、刀具結(jié)構(gòu)和刀具幾何參數(shù)等進行了反復(fù)研究和試驗,并采取了相應(yīng)措施,較好地解決了鈦合金鉆削和攻絲加工過程中存在的難題。 1 鈦合金性能特點和加工特性分析 1.1 鈦合金性能特點
9、 鈦合金即在工業(yè)純鈦中加入合金元素,以提高鈦的強度。鈦合金可分為三種:α鈦合金,β鈦合金和α+β鈦合金。α+β鈦合金,如TC4(Ti-6Al-4V),此種鈦合金由α和β雙相組成,這類合金組織穩(wěn)定,高溫變形性能、韌性、塑性較好,能進行淬火和時效處理使合金強化,是航空業(yè)重要的原材料。鈦合金的性能特點,主要表現(xiàn)在: a)比強度高。鈦合金密度小(4.4 kg/m3),重量輕,其比強度卻大于超高強度鋼。 b)熱強性高。鈦合金熱穩(wěn)定性好,在300 ℃~500 ℃條件下,其強度約比鋁合金高10倍。 c)化學(xué)活性大。鈦的化學(xué)活性大,與空氣中的O、N、CO、水蒸氣等產(chǎn)生強烈的化學(xué)反
10、應(yīng),在鈦合金表面易形成TiC及TiN硬化層。 d)導(dǎo)熱性差。鈦合金導(dǎo)熱性差,鈦合金TC4在20 ℃時的熱導(dǎo)率λ=16.8 W/m℃,導(dǎo)熱系數(shù)是0.036 cal/(cms℃)。 1.2 鈦合金加工特性分析 由于鈦合金導(dǎo)熱系數(shù)低,僅是鋼的1/4、鋁的1/13、銅的1/25,因而散熱慢,不利于熱平衡,特別是在鉆孔和攻絲加工過程中,散熱和冷卻效果很差,在切削區(qū)形成高溫,加工后回彈大,造成鉆頭和絲錐扭矩增大,刃口磨損快,耐用度降低。同時,由于鈦合金變形系數(shù)小于或接近于1,這是鈦合金加工時的一個顯著特點。因此,切屑在前刀面上滑動摩擦的路程加大,加 速刀具磨損。此外,鈦合金化學(xué)活性高,在高溫
11、高壓下加工,與刀具材料起反應(yīng),形成溶敷,擴散而成合金,造成粘刀具,切屑不易排除,往往產(chǎn)生鉆頭被咬住、扭斷鉆頭等現(xiàn)象。 2 鈦合金的鉆削加工 通過對鈦合金加工特性的分析,了解了影響鈦合金鉆削加工的因素,即在加工過程中及易出現(xiàn)燒刀、斷鉆、刀具磨損快等問題。因此,著重對鉆頭材料、鉆頭幾何參數(shù)、鉆削用量以及冷卻液等進行了研究,并較好地解決了這一問題。 2.1 鉆頭材料 鉆頭材料應(yīng)滿足以下要求: a)足夠的硬度。鉆頭和絲錐的硬度必須大于鈦合金的硬度。 b)足夠的強度和韌性。由于鉆頭和絲錐在加工鈦合金時承受很大的扭轉(zhuǎn)力和切削力。因此,必須有足夠的強度和韌性。 c)足夠的
12、耐磨性。由于鈦合金韌性好,加工時切削刃要鋒利,因此刀具材料必須有足夠的抵抗磨損能力,這樣才能減少加工硬化。 d)刀具材料與鈦合金親合能力要差。由于鈦合金化學(xué)活性高,因此要求刀具材料和鈦合金親合能力要差,以免形成溶敷,擴散而成合金,造成粘刀、斷鉆等現(xiàn)象。 綜上所述,經(jīng)過對常用的刃具材料W18Cr4V、硬質(zhì)合金(YG8)、W6Mo5Cr4V3Al、W12Cr4V4Mo和W2Mo9Cr4VCo8等制造的鉆頭和絲錐進行試驗分析,結(jié)果表明由材料W2Mo9Cr4VCo8制造的鉆頭和絲錐加工鈦合金時刃口鋒利、磨損小,效率有了顯著的提高,是比較理想的刃具材料。 W2Mo9Cr4VCo8(M
13、42)屬于高速鋼的一種,用該材料制造的鉆頭和絲錐之所以適合加工鈦合金,與該材料的化學(xué)成分有關(guān)(材料化學(xué)成分見表1)。該材料含有7.5%~8.5%的金屬元素鈷。鈷的主要作用是能加強二次硬化的效果,提高紅硬性和熱處理后的硬度,同時,具有良好的散熱性。因此,含鈷高速鋼具有高的切削加工性能。 2.2 改變鉆頭幾何參數(shù) 鈦合金的加工特性決定標準麻花鉆頭鉆削加工鈦合金時存在許多問題,主要表現(xiàn): a)鉆頭頂角2Ψ小,切削刃長,切下的切屑寬,因而鉆頭扭矩大,軸向抗力也大。同時,切屑卷曲成螺旋狀程度大,切屑所占的空間也大,排屑不順暢,影響冷卻。 b)鉆頭鉆心厚度K小。由于鉆削加工鈦合
14、金時鉆頭承受很大扭矩和軸向抗力。鉆心厚度小,則鉆頭強度低,鉆頭易折斷。 c)鉆頭螺旋角β小。螺旋角直接影響主切削刃的前角。螺旋角大,則刃口鋒利,切削輕快,否則會造成加工硬化。 d)鉆頭外緣處后角αf小,影響鉆心處切削刃的前角。 鉆頭的各基本參數(shù)見圖1。 2.2.1 增大鉆頭頂角2Ψ a) 鉆頭頂角決定切屑寬度和鉆頭前角的大小。當(dāng)鉆頭直徑和進給量一定時,增大頂角2Ψ,則切削寬度變窄,單位切削刃上的負荷減輕。同時,鉆頭外圓處的刀尖角減小,減小了刀尖角的磨損速度,同時有利于散熱,耐用度也得到提高(見圖2)。 b) 頂角對前角有很大影響。當(dāng)頂角等于90時,主截面
15、為軸向截面,其前角就是某點所處的螺旋角。因此,增大頂角2Ψ有利于改善鉆心處的切削條件。 c) 頂角影響切屑流出的方向。頂角大,切屑卷曲成螺旋的程度減小,且比較平直,容易排除,即提高了排屑性能。 通過分析試驗,在加工鈦合金時,采取增大鉆頭頂角2Ψ, 2Ψ范圍是135~140,結(jié)果表明鉆削效果良好。 2.2.2 選擇合適的鉆頭螺旋角β a) 鉆頭螺旋角β直接影響主切削刃前角的增加和減小。β角增加,前角也增加,切削輕快, 易于排屑,扭矩和軸向力也小。見圖3。 式中,D為鉆頭直徑;P為螺旋槽導(dǎo)程。 b) 由上式看出,切削刃上各點β角是變化的??拷鈭A處β角最大,前角也最大,切削
16、刃鋒利,切削性能好。而靠近鉆心處β角最小,切削性能較差, 將通過此處磨成圓弧狀,以改善切削條件。 隨β角增加,切削刃強度減弱,磨損快,甚至?xí)l(fā)生切削刃燒毀等現(xiàn)象。因此合理選擇β角,以適合鈦合金鉆削加工。 通過分析試驗,增大后鉆頭的螺旋角β見表2。 2.2.3 增大鉆心厚度 由于在鉆削加工鈦合金時鉆頭承受很大扭矩和徑向抗力,特別是小直徑鉆頭,容易折斷,因此增大鉆心厚度,以提高鉆頭強度。鉆心厚度一般為: 式中,D為鉆頭直徑。 2.2.4 增大鉆頭外緣處后角 鉆頭切削刃各點上的后角是不等的,愈接近中心,其后角愈大,因此,鉆頭后角的標注和要求,都以
17、鉆頭外緣處為準,見圖4(計算略)。 由于切削表面為螺旋面,切削刃上任一點的切削速度的方向為螺旋線,由展開圖5可以看出,實際后角減小了一個ψ角。其大小由下式計算: 式中,f為鉆頭走刀量;D為鉆頭在該點的直徑。 由上式看出,走刀量增加,切削刃上的點愈接近中心,ψ角愈大,鉆頭實際后角愈小。這就要求有不等的后角ψ,由此向鉆心逐漸增加。為了適合鈦合金加工,總結(jié)出的后角αf見表3。 增大鉆頭外緣處后角,可以使橫刃鋒利,改善切削性能。特別是對鉆心處的鉆削加工有明顯改善。 2.2.5 鉆頭加工成倒錐K 鉆頭加工成倒錐,減小棱帶同孔壁摩擦,使鉆頭切削時扭矩減小
18、.倒錐角度見表4。 經(jīng)過分析試驗,按照上述幾何參數(shù)加工的鉆頭鉆削加工鈦合金時效果良好,效率可提高40%左右。 2.3 鉆削用量 鈦合金的性能特點要求鉆削加工鈦合金時轉(zhuǎn)速要低,進給量要適中。表5是鉆削加工鈦合金的鉆削用量。 效果:我單位在鈦合金上鉆削Φ4.2, Φ5, Φ8, Φ12, Φ23孔,一次鉆出效率比標準麻花鉆頭有顯著提高。例如:鉆孔直徑Φ4.2,深18 mm,鉆一個孔約需4 min,約鉆25~30個孔,刃磨一次;鉆孔直徑Φ5,深18 mm,鉆一個孔約需4 min,約鉆25~30個孔,刃磨一次;鉆孔直徑Φ8,深20 mm,鉆一個
19、孔約需8 min,約鉆18~22個孔,刃磨一次;鉆孔直徑Φ12,深20 mm,鉆一個孔約需14 min,約鉆15~20個孔,刃磨一次; 鉆孔直徑Φ23,深24 mm,鉆一個孔約需24 min,約鉆10~15個孔,刃磨一次。 2.4 冷卻液 鉆削和攻絲加工鈦合金時最好不用含氯的冷卻液,避免產(chǎn)生有毒物質(zhì)和引起氫脆。鉆削淺孔時,可用電解切削液,其成分是:葵二酸7%~10%,三乙醇胺7%~10%,甘油7%~10%,硼酸7%~10%,亞硝酸鈉3%~5%,剩余為水。 鉆削深孔時,用N32機械油加煤油,配比是3:1.5,也可用硫化切削液。 3 鈦合金的攻絲加工 鈦合金攻絲加工,特別是
20、小孔攻絲加工是很困難的。其主要原因是由于鈦合金導(dǎo)熱系數(shù)低,在攻絲加工過程中,切削區(qū)形成高溫,造成鈦合金熱膨脹,另外,鈦合金加工后回彈大,孔壁擠壓絲錐,甚至將牙型面包住,絲錐不能轉(zhuǎn)動,否則將絲錐折斷。 經(jīng)過大量分析試驗,最后主要通過改進絲錐結(jié)構(gòu)形式和選擇適合鈦合金刀具材料,解決了這一難題。 3.1 絲錐材料 絲錐材料同鉆頭材料。 3.2 絲錐結(jié)構(gòu)形式 標準絲錐一次切削成形,切削量大,扭矩也大,孔壁熱膨脹和回彈后,絲錐轉(zhuǎn)動困難。為了解決這一問題,改進了絲錐的結(jié)構(gòu)形式,將標準絲錐的一次切削加工,分為Ⅰ、Ⅱ、Ⅲ三錐切削,同時,將絲錐加工成跳齒型,很好地解決了斷屑問題,切
21、削輕快,效果非常好,效率大大提高,冷卻效果也得到了改善。M5跳齒絲錐的結(jié)構(gòu)形式,見圖6。跳齒絲錐的幾何參數(shù),見表6。 絲錐的技術(shù)條件:a)切削部分的硬度HRC62-64,其余HRC32-42;b)刀齒寬度的2/3沿螺紋齒形鏟成030′。 3.3 螺紋底孔設(shè)計 根據(jù)鈦合金的特性,加工螺紋底孔時,孔徑公差可放大一些。螺紋公差帶位置和精度等級確定后,在滿足內(nèi)螺紋小徑D1公差等級的情況下,適當(dāng)加大螺紋底孔直徑,冷卻后螺紋底孔的收縮量,能夠抵消這一部分的加大量,加工后的螺紋滿足設(shè)計精度要求。由于不同牌號的鈦合金、不同的鍛造熱處理方法、不同的結(jié)構(gòu)形式等原因,螺紋底孔加大的量也不同,根據(jù)
22、具體情況進行試加工來確定。 3.4 冷卻液 鈦合金攻絲時使用的冷卻液與鉆削加工時使用的冷卻液相同。 4 結(jié)束語 通過對鈦合金的特性分析,重點解決了鈦合金鉆削和攻絲加工過程中存在的難題,并取得良好效果,得出如下結(jié)論: (1) W2Mo9Cr4Vo8材料的鉆頭和絲錐適合鈦合金加工; (2) 改進鉆頭幾何參數(shù),可使鈦合金零件的加工效率有顯著的提高; (3) 改進絲錐結(jié)構(gòu)形式, 可使鈦合金零件的加工效果得到明顯的改善; (4) 配制適合鈦合金加工的冷卻液,可延長切削刀具的壽命。 鈦合金的切削加工 1. 鈦合金可分為哪幾類? 鈦是同素異構(gòu)體,熔點為172
23、0℃,在低于882℃時呈密排六方晶格結(jié)構(gòu),稱為α鈦;在882℃以上呈體心立方品格結(jié)構(gòu),稱為β鈦。利用鈦的上述兩種結(jié)構(gòu)的不同特點,添加適當(dāng)?shù)暮辖鹪兀蛊湎嘧儨囟燃跋喾趾恐饾u改變而得到不同組織的鈦合金。室溫下,鈦合金有三種基體組織,鈦合金也就分為以下三類: (1) α鈦合金:它是α相固溶體組成的單相合金,不論是在一般溫度下還是在較高的實際應(yīng)用溫度下,均是α相,組織穩(wěn)定,耐磨性高于純鈦,抗氧化能力強。在500℃~600℃的溫度下,仍保持其強度和抗蠕變性能,但不能進行熱處理強化,室溫強度不高。 (2) β鈦合金:它是β相固溶體組成的單相合金,未熱處理即具有較高的強度,淬火、時效后合金得
24、到進一步強化,室溫強度可達1372~1666 MPa;但熱穩(wěn)定性較差,不宜在高溫下使用。 (3) α+β鈦合金:它是雙相合金,具有良好的綜合性能,組織穩(wěn)定性好,有良好的韌性、塑性和高溫變形性能,能較好地進行熱壓力加工,能進行淬火、時效使合金強化。熱處理后的強度約比退火狀態(tài)提高50%~100%;高溫強度高,可在400℃~500℃的溫度下長期工作,其熱穩(wěn)定性次于α鈦合金。 三種鈦合金中最常用的是α鈦合金和α+β鈦合金;α鈦合金的切削加工性最好,α+p鈦合金次之,β鈦合金最差。α鈦合金代號為TA,β鈦合金代號為TB,α+β鈦合金代號為TC。 2.鈦合金有哪些性能和用途? 鈦是
25、一種新型金屬,鈦的性能與所含碳、氮、氫、氧等雜質(zhì)含量有關(guān),最純的碘化鈦雜質(zhì)含量不超過0.1%,但其強度低、塑性高。99.5%工業(yè)純鈦的性能為:密度ρ=4.5g/cm3,熔點為1800℃,導(dǎo)熱系數(shù)λ=15.24W/(m.K),抗拉強度σb=539MPa,伸長率δ=25%,斷面收縮率ψ=25%,彈性模量E=1.078105MPa,硬度HB195。 (1) 比強度高:鈦合金的密度一般在4.5g/cm3左右,僅為鋼的60%,純鈦的強度接近普通鋼的強度,一些高強度鈦合金超過了許多合金結(jié)構(gòu)鋼的強度。因此鈦合金的比強度(強度/密度)遠大于其他金屬結(jié)構(gòu)材料,見表7-1,可制出單位強度高、剛性好、質(zhì)輕的零部件
26、。目前飛機的發(fā)動機構(gòu)件、骨架、蒙皮、緊固件及起落架等都使用鈦合金。 (2) 熱強度高:對于α鈦合金,在350℃時TA6的鞏達422MPa、TA7的σb達491MPa,在500℃時TA8的σb達687MPa;對于α+β鈦合金,在400℃時TC4的σb達618MPa、TC10的σb達834 MPa,在450℃時TC6和TC7的σb均達589MPa、TC8的σb達706MPa,在500℃時TC9的σb達785MPa。這兩類鈦合金在150℃~500℃范圍內(nèi)仍有很高的比強度,而鋁合金在150℃時比強度明顯下降。鈦合金的工作溫度可達500℃,鋁合金則在200℃以
27、下。 (3) 抗蝕性好:鈦合金在潮濕的大氣和海水介質(zhì)中工作,其抗蝕性遠優(yōu)于不銹鋼;對點蝕、酸蝕、應(yīng)力腐蝕的抵抗力特別強;對堿、氯化物、氯的有機物品、硝酸、硫酸等有優(yōu)良的抗腐蝕能力。但鈦對具有還原性氧及鉻鹽介質(zhì)的抗蝕性差。 (4) 低溫性能好:鈦合金在低溫和超低溫下,仍能保持其力學(xué)性能。在-100℃和-196℃時TA4的σb分別為893MPa和1207MPa,在-196℃和-253℃時TA7的σb分別為1216MPa和1543MPa、TC1的σb分別為1133MPa和1354MPa、TC4的σb分別為1511MPa和1785MPa。因此,鈦合金也是一種重要的低溫結(jié)構(gòu)材料。 (5)化
28、學(xué)活性大:鈦的化學(xué)活性大,與大氣中O、N、H、CO、CO2、水蒸氣、氨氣等產(chǎn)生強烈的化學(xué)反應(yīng)。含碳量大于0.2%時,會在鈦合金中形成硬質(zhì)TiC;溫度較高時,與N作用也會形成TiN硬質(zhì)表層;在600℃以上時,鈦吸收氧形成硬度很高的硬化層;氫含量上升,也會形成脆化層。吸收氣體而產(chǎn)生的硬脆表層深度可達0.1~0.15 mm,硬化程度為20%~30%。鈦的化學(xué)親和性也大,易與摩擦表面產(chǎn)生粘附現(xiàn)象。 (6)導(dǎo)熱系數(shù)小、彈性模量小:鈦的導(dǎo)熱系數(shù)λ=15.24W/(m.K),約為鎳的1/4,鐵的1/5,鋁的1/14,而各種鈦合金的導(dǎo)熱系數(shù)比鈦的導(dǎo)熱系數(shù)約下降50%。鈦合金的彈性模量約為鋼的1/2,故其
29、剛性差、易變形,不宜制作細長桿和薄壁件,切削時加工表面的回彈量很大,約為不銹鋼的2~3倍,造成刀具后刀面的劇烈摩擦、粘附、粘結(jié)磨損。 鈦合金的牌號、性能見表7-2。 3.鈦合金有哪些切削特點? 鈦合金的硬度大于HB350時切削加工特別困難,小于HB300時則容易出現(xiàn)粘刀現(xiàn)象,也難于切削。但鈦合金的硬度只是難于切削加工的一個方面,關(guān)鍵在于鈦合金本身化學(xué)、物理、力學(xué)性能間的綜合對其切削加工性的影響。鈦合金有如下切削特點: (1)變形系數(shù)?。哼@是鈦合金切削加工的顯著特點,變形系數(shù)小于或
30、接近于1。切屑在前刀面上滑動摩擦的路程大大增大,加速刀具磨損。 (2)切削溫度高:由于鈦合金的導(dǎo)熱系數(shù)很小(只相當(dāng)于45號鋼的1/5~1/7),切屑與前刀面的接觸長度極短,切削時產(chǎn)生的熱不易傳出,集中在切削區(qū)和切削刃附近的較小范圍內(nèi),切削溫度很高。在相同的切削條件下,切削溫度可比切削45號鋼時高出一倍以上。 (3)單位面積上的切削力大:主切削力比切鋼時約小20%,由于切屑與前刀面的接觸長度極短,單位接觸面積上的切削力大大增加,容易造成崩刃。同時,由于鈦合金的彈性模量小,加工時在徑向力作用下容易產(chǎn)生彎曲變形,引起振動,加大刀具磨損并影響零件的精度。因此,要求工藝系統(tǒng)應(yīng)具有較好的剛性。 (4)
31、冷硬現(xiàn)象嚴重:由于鈦的化學(xué)活性大,在高的切削溫度下,很容易吸收空氣中的氧和氮形成硬而脆的外皮;同時切削過程中的塑性變形也會造成表面硬化。冷硬現(xiàn)象不僅會降低零件的疲勞強度,而且能加劇刀具磨損,是切削鈦合金時的一個很重要特點。 (5)刀具易磨損:毛坯經(jīng)過沖壓、鍛造、熱軋等方法加工后,形成硬而脆的不均勻外皮,極易造成崩刃現(xiàn)象,使得切除硬皮成為鈦合金加工中最困難的工序。另外,由于鈦合金對刀具材料的化學(xué)親和性強,在切削溫度高和單位面積上切削力大的條件下,刀具很容易產(chǎn)生粘結(jié)磨損。車削鈦合金時,有時前刀面的磨損甚至比后刀面更為嚴重;進給量f<0.1 mm/r時,磨損主要發(fā)生在后刀面上;當(dāng)f>0.2 mm/
32、r時,前刀面將出現(xiàn)磨損;用硬質(zhì)合金刀具精車和半精車時,后刀面的磨損以VBmax<0.4 mm較合適。 4.切削鈦合金時怎樣選擇刀具材料? 切削加工鈦合金應(yīng)從降低切削溫度和減少粘結(jié)兩方面出發(fā),選用紅硬性好、抗彎強度高、導(dǎo)熱性能好、與鈦合金親和性差的刀具材料,YG類硬質(zhì)合金比較合適。由于高速鋼的耐熱性差,因此應(yīng)盡量采用硬質(zhì)合金制作的刀具。常用的硬質(zhì)合金刀具材料有YG8、YG3、YG6X、YG6A、813、643、YS2T和YD15等。 涂層刀片和YT類硬質(zhì)合金會與鈦合金產(chǎn)生劇烈的親和作用,加劇刀具的粘結(jié)磨損,不宜用來切削鈦合金;對于復(fù)雜、多刃刀具,可選用高釩高速鋼(如W12Cr4V4Mo
33、)、高鈷高速鋼(如W2Mo9Cr4VCo8)或鋁高速鋼(如W6Mo5Cr4V2Al、M10Mo4Cr4V3Al)等刀具材料,適于制作切削鈦合金的鉆頭、鉸刀、立銑刀、拉刀、絲錐等刀具。采用金剛石和立方氮化硼作刀具切削鈦合金,可取得顯著效果。如用天然金剛石刀具在乳化液冷卻的條件下,切削速度可達200 m/min;若不用切削液,在同等磨損量時,允許的切削速度僅為100m/min。 5.切削鈦合金時怎樣選擇刀具幾何參數(shù)? (1)前角γ0:鈦合金切屑與前刀面的接觸長度短,前角較小時既可增加刀屑的接觸面積,使切削熱和切削力不至于過分集中在切削刃附近,改善散熱條件,又能加強切削刃,減小崩損的可能性。
34、一般取γ0=5~15。 (2)后角α0:鈦合金已加工表面彈性恢復(fù)大、冷硬現(xiàn)象嚴重,采用大后角可減小對后刀面造成的摩擦、粘附、粘結(jié)、撕裂等現(xiàn)象,以減小后刀面的磨損。各種切削鈦合金刀具的后角基本上都大于等于15。 (3)主偏角κr和副偏角κr:切削鈦合金時切削溫度高、彈性變形傾向大,在工藝系統(tǒng)剛性允許的條件下,應(yīng)盡量減小主偏角,以增加切削部分的散熱面積和減小切削刃單位長度上的負荷,一般采用κr=30,粗加工時取κr=45。減小副偏角可以加強刀尖,有利于散熱和降低加工表面粗糙度值,一般取κr =10~15。 (4)刃傾角λs:由于毛坯有硬皮和表層組織不均勻,粗車時切削刃容易崩損,為了增加切削刃
35、的強度和鋒利程度,應(yīng)加大切屑的滑動速度,一般取λs =-3~-5,精車時λs =O。 (5)刀尖圓弧半徑rε:切削鈦合金時刀尖是最薄弱的部分,容易崩掉和磨損,需磨出刀尖圓弧,一般rε=0.5~1.5mm。 車削時采用負倒棱(bγ=0.03~0.05 mm,γ01=-10~0),斷(卷)屑槽的槽底圓弧半徑Rn=6~8 mm。 另外,刀具刃磨質(zhì)量對提高其耐用度也十分重要。硬質(zhì)合金刀具宜用金剛石砂輪刃磨,切削時刃口必須鋒利,前后刀面的表面粗糙度Ra值應(yīng)小于0.4um,刃口部分不允許有微小的缺口。刀具刃磨后進行研磨,其耐用度可提高30%。 6.切削鈦合金時怎樣選擇切削用量? 切削鈦合金時
36、,切削溫度高、刀具耐用度低,切削用量中切削速度對切削溫度的影響最大,因此應(yīng)力求使所選擇的切削速度下產(chǎn)生的切削溫度接近最佳范圍。高速鋼刀具切削鈦合金時的最佳切削溫度約為480℃~540℃,硬質(zhì)合金刀具約為650℃~750℃。切削鈦合金一般采用較低的切削速度、較大的切削深度和進給量。 (1)切削速度Vc:切削速度對刀具耐用度影響最大,最好能使刀具在相對磨損最小的最佳切削速度下工作。切削不同牌號的鈦合金,由于強度差別較大,切削速度應(yīng)適當(dāng)調(diào)整。切削深度對切削速度也有一定影響,應(yīng)根據(jù)不同的切削深度來確定切削速度的大小,核正系數(shù)見表7-3和表7-4。 (2)進給量f:進給量
37、對刀具的耐用度影響較小,在保證加工表面粗糙度的條件下,可選較大的進給量,一般取f=0.1~0.3 mm/r。進給量太小,使刀具在硬化層內(nèi)切削,增加刀具磨損,同時極薄的切屑在高的切削溫度下容易自燃,因此不允許f<0.05 mm/r。 (3)切削深度αp:切削深度對刀具耐用度的影響最小,一般選用較大的切削深度,這樣不僅可以避免刀尖在硬化層內(nèi)切削,減小刀具磨損,還可增加刀刃工作長度,有利于散熱,一般取αp=1~5 mm。車削鈦合金的切削用量見表7-5。 7.切削鈦合金時怎樣選擇切削液? 切削鈦合金時,為了降低切削溫度,應(yīng)當(dāng)向切削區(qū)域澆注大
38、量的以冷卻作用為主的切削液。對切削液的要求有導(dǎo)熱系數(shù)大、比熱大、熱容量大、汽化熱大、汽化速度快、流量大、流速快。一般說來,水比油的導(dǎo)熱系數(shù)大3~5倍,比熱大1倍,汽化熱幾乎大10倍左右,故用水溶性切削液較為合適。車、銑削鈦合金時,常采用乳化液,或采用有極壓添加劑的水溶性切削液。 極壓乳化劑的配方為: 石油磺酸鈉 10% 油酸 3% 石油磺酸鉛 6% 三乙醇胺 3.5 % 氯化石蠟 4% 20號機油 70.5% 氯化硬脂酸 3% 極壓添加劑的水溶性切削液的配方為: 氯化脂肪酸、聚氯乙烯 0.5%~0.8% 磷酸三鈉 0.59% 三乙醇胺 1%~2% 亞硝酸鈉 1.2% 水 其余
39、 對于鉆孔、擴孔、鉸孔、拉削、攻絲等工序,應(yīng)該采用潤滑作用較大的極壓可溶性油作切削液,如蓖麻油、油酸、硫化油、氯化油等。 冷卻潤滑的方法最好采用高壓噴霧冷卻法、高壓內(nèi)冷卻法等,這樣才可起到良好的冷卻、潤滑作用。切削液流量不少于15~20 L/min。 8.切削鈦合金時應(yīng)注意哪些問題? 在切削鈦合金的過程中,應(yīng)注意的事項有: (1)由于鈦合金的彈性模量小,工件在加工中的夾緊變形和受力變形大,會降低工件的加工精度;工件安裝時夾緊力不宜過大,必要時可增加輔助支承。 (2)如果使用含氯的切削液,切削過程中在高溫下將分解釋放出氫氣,被鈦吸收引起氫脆;也可能引起鈦合金高溫應(yīng)力腐蝕開裂。
40、(3)切削液中的氯化物使用時還可能分解或揮發(fā)有毒氣體,使用時宜采取安全防護措施,否則不應(yīng)使用;切削后應(yīng)及時用不含氯的清洗劑徹底清洗零件,清除含氯殘留物。 (4)禁止使用鉛或鋅基合金制作的工、夾具與鈦合金接觸,銅、錫、鎘及其合金也同樣禁止使用。 (5)與鈦合金接觸的所有工、夾具或其他裝置都必須潔凈;經(jīng)清洗過的鈦合金零件,要防止油脂或指印污染,否則以后可能造成鹽(氯化鈉)的應(yīng)力腐蝕。 (6)一般情況下切削加工鈦合金時,沒有發(fā)火危險,只有在微量切削時,切下的細小切屑才有發(fā)火燃燒現(xiàn)象。為了避免火災(zāi),除大量澆注切削液之外,還應(yīng)防止切屑在機床上堆積,刀具用鈍后立即進行更換,或降低切削速度,加大進給量
41、以加大切屑厚度。若一旦著火,應(yīng)采用滑石粉、石灰石粉末、干砂等滅火器材進行撲滅,嚴禁使用四氯化碳、二氧化碳滅火器,也不能澆水,因為水能加速燃燒,甚至導(dǎo)致氫爆炸。 9.怎樣對鈦合金進行銑削? 鈦合金在惰性氣體介質(zhì)中低速銑削時,切屑變形系數(shù)大于1.0;但在大氣中,銑削速度Vc=30 m/min時,切屑變形系數(shù)小于1.0,這是因為鈦合金在高溫銑削時,對大氣中氧和氮的親和性很大,在800℃高溫條件下,鈦合金的切屑便激烈地從周圍大氣中吸收這些氣體,產(chǎn)生相變并使縮短的銑屑重新伸長。鈦合金銑削時溫度很高,沖擊力大,應(yīng)選用能很好地承受交變載荷和熱沖擊的銑刀刀齒材料。通常選用YG類硬質(zhì)合金,也可用鈷、鋁超
42、硬高速鋼。 鈦合金銑刀的幾何參數(shù)和銑削用量見表7-6和表7-7。 銑削鈦合金時,宜采用不對稱順銑法,這樣刀齒前面遠離刀尖部分首先接觸工件,刀齒切離時的切屑很薄,不易粘結(jié)在切削刃上。而逆銑時正相反,容易粘屑,當(dāng)?shù)洱X再次切入時切屑被碰斷,造成刀具材料剝落崩刃。 端銑刀與工件軸線間的偏移量e可決定銑刀刀齒與工件首先接觸的最佳部位,順銑或逆銑及切離時切屑厚度的大小,一般以偏移量e=(0.04~0.1) do為宜(do為端銑刀直徑)。 由于鈦合金的彈性模量小,順銑造成讓刀現(xiàn)象,要求機床和刀具有較大的剛性。銑
43、削時刀具與切屑的接觸長度短,不易卷屑,要求刀具具有較好的刀齒強度及較大的容屑空間,否則切屑堵塞會造成刀具劇烈磨損。 10.怎樣對鈦合金進行鉆孔? 鉆孔為半封閉式切削,對鈦合金鉆孔過程中切削溫度很高,鉆孔后回彈大,鉆屑長而薄,易粘結(jié)而不易排出,經(jīng)常造成鉆頭被咬住、扭斷等惡性事故。因此要求鉆頭具有高的強度和好的剛性,鉆頭與鈦合金的化學(xué)親和性要小,最好采用硬質(zhì)合金鉆頭,但目前最常用的仍是麻花鉆,經(jīng)過采取一些措施改進后,也能取得較好的效果。 (1)改進鉆頭:為滿足對鈦合金鉆孔的需要,應(yīng)對麻花鉆采取以下改進措施: 加大鉆頭頂角,2Ф=135~140;增大鉆頭外緣處后角,取12~15;增大螺旋角
44、,p=35~40;增大鉆心厚度,取(0.22~0.4)do(do為鉆頭直徑)。 采用“S”形或“X”形修磨鉆頭橫刃,橫刃長度b=(0.08~0.1)do,同時保證橫刃的對稱度≤0.06 mm。兩種形式的橫刃均可形成第二切削刃,起到分屑作用和減小鉆孔時的軸向力。最常用的是在麻花鉆上磨出適于對鈦合金鉆孔的切削刃形,即鈦合金群鉆,其切削部分的形狀見圖7-1。圖中外內(nèi)刃頂角2φ和2φ′在鉆頭直徑do>3~10mm時均為130~140,do>10~30 mm時為125~140;外刃后角α在do>3~10 mm時為12~18,do>10~30 mm時為10~15;橫刃斜角ψ=45;內(nèi)刃前角γτ=-10~
45、-15;內(nèi)刃斜角τ=10~15;圓弧刃后角aR=18~20。 鈦合金群鉆的有關(guān)參數(shù)和鉆削用量見表7-8和表7-9。 在鉆頭上做出四條導(dǎo)向刃帶,加大鉆頭截面慣性矩,提高剛性,還自然地形成兩條輔助冷卻槽,耐用度比標準鉆頭提高3倍左右,切削溫度約降低20%。同時由于導(dǎo)向穩(wěn)定減小了孔擴張量,如Ф3 mm的四刃帶鉆頭鉆孔孔擴張量為0.03~0.04 mm,而標準鉆頭為0.05~0.06 mm。 (2)選擇適宜的槍鉆:在鉆鈦合金長徑比大于5的深孔時,當(dāng)孔徑小于等于30 mm時,一般采用硬質(zhì)合金槍鉆,見圖7-2;當(dāng)孔徑大于30 mm時,采用硬質(zhì)合金B(yǎng)T
46、A鉆頭或噴吸鉆等。用圖7-2所示槍鉆鉆削TC11的孔,孔深204 mm(長徑比約為26),可保證表面粗糙度Ra為1.6 μm,生產(chǎn)率提高4倍,切屑呈“梅花”形或“C”形碎屑,排屑正常。 用硬質(zhì)合金槍鉆鉆長徑比大于30的深孔時,在軸向施加小于100Hz的振動進行振動鉆孔,可使得工件表面粗糙度Ra為0.3 μm,生產(chǎn)率提高5倍。具體參數(shù)為Vc=17 m/min,f=0.033 min/r,振幅為0.07 mm,頻率35 Hz,工件圓度4 μm,表面粗糙度Ra為0.33 μm。 (3)選擇合適的切削液:鉆淺孔時可選用電解切削液,其成分為癸二酸7%~10%,三乙醇胺7%~10%,甘油7%~
47、10%,硼酸7%~10%,亞硝酸鈉3%~5%,其余為水。 鉆深孔時不宜選用水基切削液,因為水在高溫下可能在切削刃上形成蒸汽氣泡,易產(chǎn)生積屑瘤,使鉆孔不穩(wěn)定。宜采用N32機油加煤油,其配比為3:1或3:2,也可采用硫化切削油。 11.怎樣對鈦合金進行鉸孔? 用高速鋼和YG類硬質(zhì)合金制作的鉸刀都可用于鈦合金零件上鉸孔。高速鋼鉸刀主要用于純鈦鉸孔,YG類硬質(zhì)合金鉸刀主要用于鈦合金鉸孔。鈦合金鉸刀有直齒鉸刀、階梯鉸刀和帶刃傾角的階梯鉸刀三種,直齒鉸刀鉸出的工件孔徑最大,階梯鉸刀次之,帶刃傾角的階梯餃刀最小。階梯鉸刀的第一錐在切削的同時為第二錐起了導(dǎo)向作用,也為第二錐留下了極為穩(wěn)定的余量,實際
48、上起到了粗鉸和精鉸的作用;帶刃傾角的階梯鉸刀在刃傾角的作用下,提高鉸孔過程的平穩(wěn)性,并使切屑向下排出,不會摩擦、劃傷孔壁,因而鉸出的孔徑精度比階梯鉸刀更高些。 鈦合金鉸刀的幾何參數(shù)一般選用前角γ0=0~5,硬質(zhì)合金鉸刀取小值;后角α0=10~15;切削錐角κr=15~30。階梯鉸刀的第二錐角為15,刃傾角λs=-15。為了加大鈦合金鉸刀的容屑空間,齒數(shù)應(yīng)少于標準鉸刀,齒槽角δ=85~90。各種鈦合金鉸刀參數(shù)見圖7-3、圖7-4和圖7-5。 鈦合金鉸刀的直徑由鉸出孔的擴張量大小來確定,一般高速
49、鋼鉸刀擴張量取0.008mm,硬質(zhì)合金鉸刀擴張量取0.006mm。 對鈦合金鉸孔時,粗鉸余量2αp=0.15~0.5 mm,精鉸余量2αp =0.1~0.4 mm,直徑小時取小值,反之取大值。硬質(zhì)合金鉸刀的切削用量Vc=15~50 m/min,f=0.1~0.5mm/r,鉸孔直徑大時取大值,反之取小值。高速鋼鉸刀的鉸削用量見表7-10。 鉸削鈦合金時,最好使用切削液,常用的是電解切削液或混合油(成分為蓖麻油60%和煤油40%)。 12.對鈦合金拉削時應(yīng)注意哪些問題? 首先,根據(jù)鈦合金材料的特性和切削特點,在拉刀設(shè)計時應(yīng)注意以下幾個方面的問題: (1)拉刀的前后角直接影響拉刀
50、的切削效果。用高速鋼制作的拉刀前角一般取γ0=10~20,硬質(zhì)合金拉刀γ0=8~15。用于外拉的拉刀切削齒后角αp =10~12,校準齒后角αk =8~10;用于內(nèi)拉的切削齒后角αp =5~8,校準齒后角αk=2~3;高速鋼和硬質(zhì)合金拉刀的這兩個后角相同。對于粗拉刀前后角用小值,精拉刀用大值。 (2)鈦合金拉刀只要條件允許應(yīng)盡可能做出刃傾角,一般取λs=5~10。 (3)拉刀前后刀面的粗糙度Ra≤0.32 μm。 (4)校準齒上盡可能不留刃帶,若需要時,其寬度應(yīng)小于等于0.12 mm。 (5)由于鈦合金的彈性模量小,加工后回彈大,開槽拉刀刀齒寬度至少應(yīng)等于或稍大于槽寬的下限尺寸
51、,以免拉出的槽窄達不到要求。 (6)拉刀卷屑臺的形式與拉削高溫合金的基本相同。 (7)鈦合金拉刀的磨鈍標準一般為:粗拉刀VB≤0.3~0.4 mm,精拉刀VB≤0.15~0.2 mm。 再就是選用合理的拉削用量,在保證刀具耐用度的前提下提高生產(chǎn)效率。高速鋼拉刀的拉削速度Vc=4.5~6 m/min,粗拉刀的齒升量為0.06~0.10 mm,精拉刀為0.02~0.04 mm;硬質(zhì)合金拉刀的拉削速度Vc=15~30 m/min,粗拉刀的齒升量為0.08~0.12 mm,精拉刀為0.03~0.04mm。 拉削鈦合金工件時必須使用切削液,一般采用油基切削液,常用的是混合油(蓖麻油60%
52、,煤油40%)。還可選用另一種切削油,其成分為:聚醚30%,酯類油30%,N7機械油30%,防銹添加劑和抗泡沫添加劑10%。 13.怎樣對鈦合金進行攻絲? 鈦合金攻絲是鈦合金切削加工中最困難的工序,特別是攻制小螺紋。這種困難主要表現(xiàn)在攻絲時的總扭矩大,約為45號鋼的2倍;絲錐刀齒過快地磨損、崩刃,甚至被“咬死”在螺紋孔內(nèi)而折斷。這是由于鈦合金的彈性模量太小,螺紋表面產(chǎn)生很大的回彈,使絲錐與工件接觸的面積增大,造成很大的摩擦扭矩,磨損加劇;另外,切屑細小不易拳曲,有粘刀現(xiàn)象,造成排屑困難。因此,解決鈦合金攻絲問題的關(guān)鍵是減小攻絲時絲錐與工件的接觸面積。 (1)普通絲錐:必須經(jīng)過技術(shù)處
53、理后方能攻制鈦合金螺紋。對普通絲錐進行處理的措施為:增大容屑空間,減少齒數(shù);在校準齒上留出0.2~0.3 mm的刀帶后,將后角加大到20~30,并沿絲錐全長磨去齒背中段;保留2~3扣校準齒后將后部的倒錐由0.05~0.2 mm/100 mm增大至0.16~0.32 mm/100 mm。當(dāng)其他條件完全相同時,若將齒背寬度減小(磨去)1/2~2/3,攻絲扭矩下降1/4~1/3。 (2)修正齒絲錐:修正齒絲錐是把標準絲錐的成形法加工螺紋改為漸成法,工作原理如圖7-6所示。由圖可知,修正齒絲錐的齒形角α0小于螺紋齒形角α1,使絲錐齒側(cè)與被切螺紋側(cè)表面形成一側(cè)隙角φ=(α1-α0)/2,并將絲錐螺紋
54、做出較大的倒錐,使得摩擦扭矩大大減小,同時也利于切削液的冷卻潤滑。 圖中各角度間的關(guān)系式為: tanδ=tan κr (tan(α1/2)˙cot(α0/2) -1) 設(shè)計攻制普通螺紋的修正齒絲錐時,為檢驗方便,一般取絲錐齒形角α0=55,切削錐角δ可在230′~730′之間選取。 標準絲錐的倒錐是從校準齒開始的,倒錐量為(0.05~0.2)mm/100 mm;修正齒絲錐的倒錐則是從第一個切削齒開始,并且倒錐數(shù)值遠大于標準絲錐,如κr =730′的修正齒絲錐可達1.437 mm/100 mm。由于倒錐量加大,修正齒絲錐的校準部分便起不了導(dǎo)向作用,在切削錐前端時必須做出圓柱導(dǎo)向部,
55、以避免絲錐剛攻入時產(chǎn)生歪斜,圓柱導(dǎo)向部的公稱尺寸及公差取決于攻絲前的底孔尺寸。圖7-7是修正齒絲錐的結(jié)構(gòu)和幾何參數(shù)示例。修正齒絲錐攻制的螺紋表面粗糙度不如成形式絲錐。 (3)跳牙絲錐:跳牙絲錐是在切削齒和校準齒上相間地去掉螺扣,其最大的特點是有效地減小了絲錐與工件的接觸面積,使攻絲扭矩顯著下降。由于間齒攻絲,相鄰螺扣側(cè)刃之間有較寬綽的空間,改善了容屑和切削液進入切削區(qū)的條件,提高了絲錐的耐用度;同時在制造絲錐時,砂輪外緣頂部也不需過分尖銳,改善了磨削條件。跳牙絲錐示意圖見圖7-8。 在相同的切削條件下經(jīng)試驗比較,跳牙絲錐的攻絲扭矩約為標準絲錐的30%
56、~50%,修正齒絲錐的35%~60%,耐用度比修正齒絲錐高1~3倍,用跳牙絲錐對鈦合金攻絲效果最好。 (4)螺紋底孔:對鈦合金攻絲一般按牙高率(螺孔實際牙型高度與理論高度的比率)不超過70%為依據(jù)來選取底孔直徑大小,即螺紋底孔直徑d1=d0-0.757 8p(d0為螺紋公稱尺寸,p為螺矩)。小直徑或粗牙螺紋牙高率可取大一些,被加工材料強度低或螺紋深度小于螺紋基本直徑時,可適當(dāng)增大牙高率,但過大會增大攻絲扭矩,甚至折斷絲錐。為保證攻絲精度和表面質(zhì)量,螺紋底孔應(yīng)為鉸后的孔。 鈦合金的攻絲速度要根據(jù)材料的類型和硬度來確定。α鈦合金的攻絲速度一般取Vc=7.5~12 m/min,α+β鈦合金取
57、Vc=4.5~6 m/min,β鈦合金取Vc=2~3.5 m/min;鈦合金的硬度≤HB350時選用較高的切削速度,反之選用較低的切削速度。 對鈦合金攻絲時,一般用含Cl、P的極壓切削液效果較好,但含Cl的極壓切削液攻絲后必須清洗干凈,防止零件晶間腐蝕;也可用蓖麻油60%、煤油40%的混合油作切削液。 14.磨削鈦合金有哪些特點? (1)磨削力大:磨削鈦合金時,和一般磨削規(guī)律一樣,徑向力大于切向力。在相同條件下磨削TC9的徑向分力幾乎比45號鋼大4倍,切向分力大80%左右。 (2)磨削溫度高:鈦合金磨削時滑擦過程所占比重大,產(chǎn)生強烈的摩擦,急劇的彈性、塑性變形和大量的熱量,致使
58、磨削區(qū)的溫度很高。在相同條件下,磨削TC9的磨削溫度為45號鋼的1.5~2倍,最高時可達1000℃。 (3)砂輪磨損失效:磨削鈦合金時,除粘結(jié)、擴散外,鈦合金與磨粒之間起化學(xué)作用,從而加速了砂輪的磨損過程。觀察磨削后的砂輪,鈦呈云霧狀分布,幾乎看不到砂輪磨粒。 (4)表面質(zhì)量不易保證:鈦合金磨削時,工件表面容易產(chǎn)生有害的殘余拉應(yīng)力和表面污染層,表面粗糙度數(shù)值較大。磨后表面殘余拉應(yīng)力數(shù)值大小隨磨削用量的加大而增大,磨削速度是殘余應(yīng)力的主要影響因素。 (5)生產(chǎn)率低:在保證所要求的零件加工精度的條件下,很難獲得較高的生產(chǎn)率。磨削時砂輪容易變鈍失效,磨削比很低,在相同條件下磨削Tc4的磨
59、削比只有1.53,而45號鋼為71.5,約為45號鋼的1/47。 15.磨削鈦合金時怎樣選擇砂輪? (1)磨料的選擇:白剛玉WA砂輪一般只能在Vc≤10 m/s的條件下磨削鈦合金,因為Vc加大會使磨削溫度升高,鈦合金表層會發(fā)生組織轉(zhuǎn)變;而且在高溫下很容易吸收空氣中的氧形成氧化鈦,并與Al2O3生成固溶體,因而增大了鈦與Al2O3的粘附結(jié)合力,加劇砂輪的粘結(jié)磨損。 綠碳化硅GC及鈰碳化硅CC磨料與鈦合金粘附較輕,尤以CC砂輪的磨削力小且磨削溫度低。采用混合磨料(以GC及CC為主磨料,以鉻剛玉PA、單晶剛玉SA、鋯剛玉ZA或微晶剛玉MA為副磨料)磨削效果能得到很大提高,磨削溫度降低到6
60、00℃以下,磨削比可達12。 采用人造金剛石JR和立方氮化硼CBN超硬磨料磨削鈦合金效果最好。CBN砂輪磨削鈦合金的磨削比比采用混合磨料高50~60倍,且工件表層殘余應(yīng)力幾乎都為壓應(yīng)力,陶瓷CBN砂輪磨削效果見表7-11。 (2)粒度和硬度的選擇:粒度和硬度都影響磨削比,粒度的影響大些。磨削鈦合金時,常用粒度號為36號~80號的磨料、硬度為K~M的砂輪;較軟的砂輪磨削力較小且磨削溫度較低,但磨損較大。實踐證明,既能減小磨削力又能適當(dāng)提高磨削比,采用粒度為80號、硬度為J的砂輪為宜。 (3)結(jié)合劑的選擇:磨削鈦合金的砂輪一般選用陶瓷結(jié)合劑V,這種結(jié)合劑的砂輪磨削力比較大;
61、對大而薄的砂輪選用橡膠結(jié)合劑R,可降低磨削溫度和磨削力。 (4)組織的選擇:采用中等偏疏松或疏松的砂輪組織5~8號為宜。成型磨削及精密磨削時,為保持砂輪型面及磨削表面粗糙度,可選用組織較為緊密的砂輪。 磨削鈦合金時,不同磨削方式使用砂輪的具體選擇見表7-12。 16.磨削鈦合金時怎樣選擇磨削用量? 由于鈦合金的磨削溫度高,再加上鈦合金的化學(xué)活性大,工件表層組織很容易發(fā)生相變,而且容易產(chǎn)生有害的殘余拉應(yīng)力,會降低零件的疲勞強度,因此在選擇鈦合金的磨削用量時首先要考慮的是降低磨削溫度。磨削速度對磨削溫度的影響最大,即磨削鈦合金時的速度不宜太高。具體的鈦合金磨削用量見
62、表7-13。 17.磨削鈦合金時怎樣選擇磨削液? 磨削鈦合金時,要求磨削液具有冷卻、潤滑和沖洗作用,更重要的是應(yīng)具有抑制鈦與磨料的粘附作用和化學(xué)作用。目前用得較多的是水溶性磨削液,有亞硝酸鉀溶液、亞硝酸鉀和甲酸鈉溶液、亞硝酸鈉溶液、亞硝酸鈉和甲酸鈉溶液、亞硝酸胺溶液等。使用含極壓添加劑S、Cl、P的極壓油,效果較好,尤以氯(Cl)極壓油效果最好,但磨后應(yīng)清洗零件,以防降低零件的抗疲勞強度。 對于緩進給磨削推薦選用下述配方制備磨削液:亞硝酸鈉1%,苯甲酸鈉0.5%,甘油0.5%,三乙醇胺0.4%,水(其余)。使用立方氮化硼CBN砂輪磨削時不宜使用水溶性磨削液,因BN與
63、水在800℃左右會起化學(xué)反應(yīng),造成砂輪過快磨損(BN+H2O→H2BO3+NH3)。 使用磨削液時,應(yīng)特別注意流量要足夠大,每毫米砂輪寬度一般不低于0.5 L/min。砂輪線速度越高,流量應(yīng)越大。水箱容量一般為流量的1.5~3倍,以保持磨削液處于較低的溫度。另外,鈦合金的磨削溫度較高,鈦屑容易引起自燃,在使用油劑磨削液時,應(yīng)注意防止發(fā)生火災(zāi)。 18.鈦合金有哪些其他的磨削方法? 磨削鈦合金除了常用的普通磨削法外,還可采用緩進給磨削法和低應(yīng)力磨削法。 (1)緩進給磨削法:鈦合金的緩進給磨削的特點與高溫合金類同,有關(guān)的詳細情況參照高溫合金的緩進給磨削部分。鈦合金的緩進給磨削一般選用
64、GC60G~JV的砂輪,磨削速度Vc=28~30 m/s,工件速度Vw=70 mm/min,磨削深度αp=1~2 mm。工件表面粗糙度值要求較小時,應(yīng)采用較硬的砂輪;成形磨削時,可用金剛石滾輪或鋼滾輪來修整砂輪。 (2)低應(yīng)力磨削法:鈦合金的低應(yīng)力磨削是靠減小磨去單位體積金屬消耗的能量,來降低磨后工件表層的殘余拉應(yīng)力,消除燒傷、變形和裂紋,很適合鈦合金的磨削。低應(yīng)力磨削應(yīng)采取以下措施:使用較軟的砂輪,經(jīng)常保持砂輪和修整工具的鋒利,減小徑向進給量(或磨削深度),降低磨削速度,大量充分使用性能好的磨削液。但此法生產(chǎn)率低,只適用于承受很高應(yīng)力的零件(如:高循環(huán)應(yīng)力或在腐蝕條件下工作的零件),用這種磨削法可提高零件的疲勞強度。其磨削用量見表7-14。
- 溫馨提示:
1: 本站所有資源如無特殊說明,都需要本地電腦安裝OFFICE2007和PDF閱讀器。圖紙軟件為CAD,CAXA,PROE,UG,SolidWorks等.壓縮文件請下載最新的WinRAR軟件解壓。
2: 本站的文檔不包含任何第三方提供的附件圖紙等,如果需要附件,請聯(lián)系上傳者。文件的所有權(quán)益歸上傳用戶所有。
3.本站RAR壓縮包中若帶圖紙,網(wǎng)頁內(nèi)容里面會有圖紙預(yù)覽,若沒有圖紙預(yù)覽就沒有圖紙。
4. 未經(jīng)權(quán)益所有人同意不得將文件中的內(nèi)容挪作商業(yè)或盈利用途。
5. 裝配圖網(wǎng)僅提供信息存儲空間,僅對用戶上傳內(nèi)容的表現(xiàn)方式做保護處理,對用戶上傳分享的文檔內(nèi)容本身不做任何修改或編輯,并不能對任何下載內(nèi)容負責(zé)。
6. 下載文件中如有侵權(quán)或不適當(dāng)內(nèi)容,請與我們聯(lián)系,我們立即糾正。
7. 本站不保證下載資源的準確性、安全性和完整性, 同時也不承擔(dān)用戶因使用這些下載資源對自己和他人造成任何形式的傷害或損失。
最新文檔
- 6.煤礦安全生產(chǎn)科普知識競賽題含答案
- 2.煤礦爆破工技能鑒定試題含答案
- 3.爆破工培訓(xùn)考試試題含答案
- 2.煤礦安全監(jiān)察人員模擬考試題庫試卷含答案
- 3.金屬非金屬礦山安全管理人員(地下礦山)安全生產(chǎn)模擬考試題庫試卷含答案
- 4.煤礦特種作業(yè)人員井下電鉗工模擬考試題庫試卷含答案
- 1 煤礦安全生產(chǎn)及管理知識測試題庫及答案
- 2 各種煤礦安全考試試題含答案
- 1 煤礦安全檢查考試題
- 1 井下放炮員練習(xí)題含答案
- 2煤礦安全監(jiān)測工種技術(shù)比武題庫含解析
- 1 礦山應(yīng)急救援安全知識競賽試題
- 1 礦井泵工考試練習(xí)題含答案
- 2煤礦爆破工考試復(fù)習(xí)題含答案
- 1 各種煤礦安全考試試題含答案