
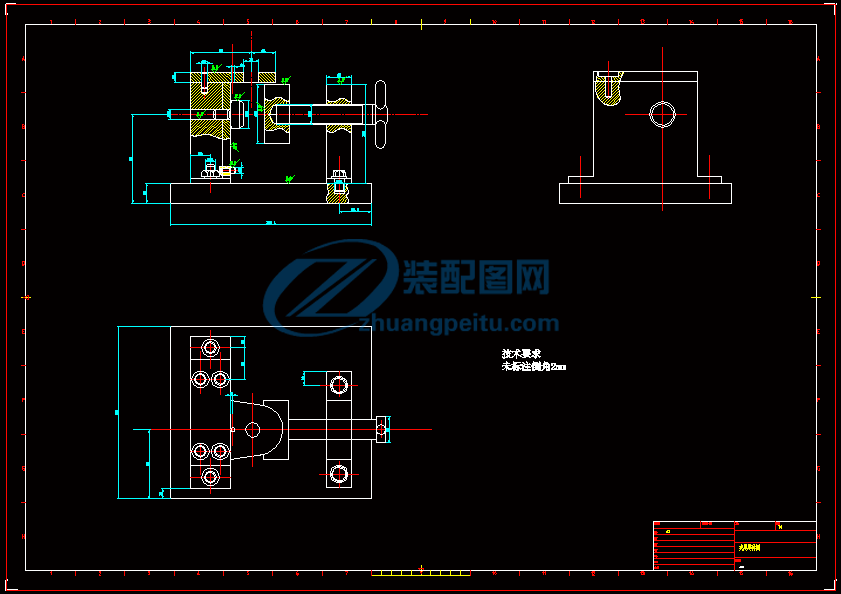


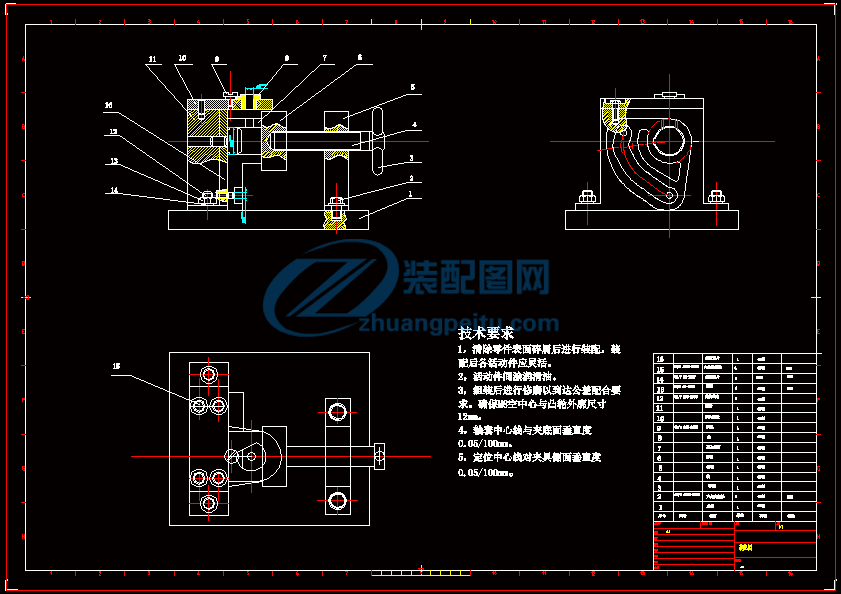

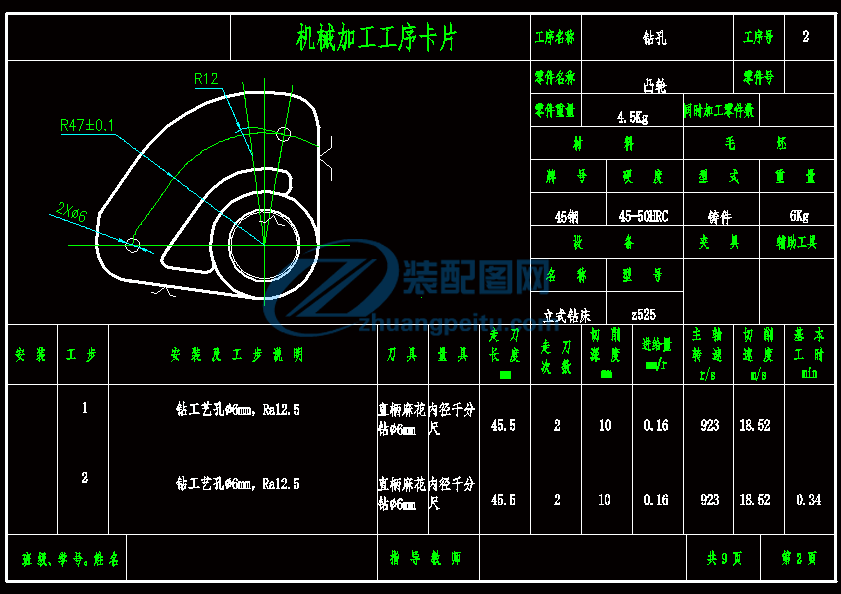
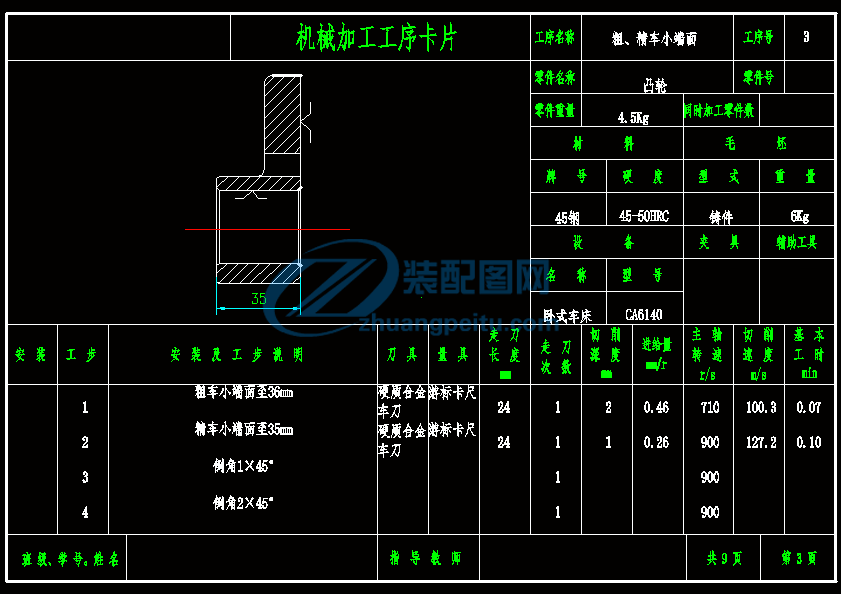



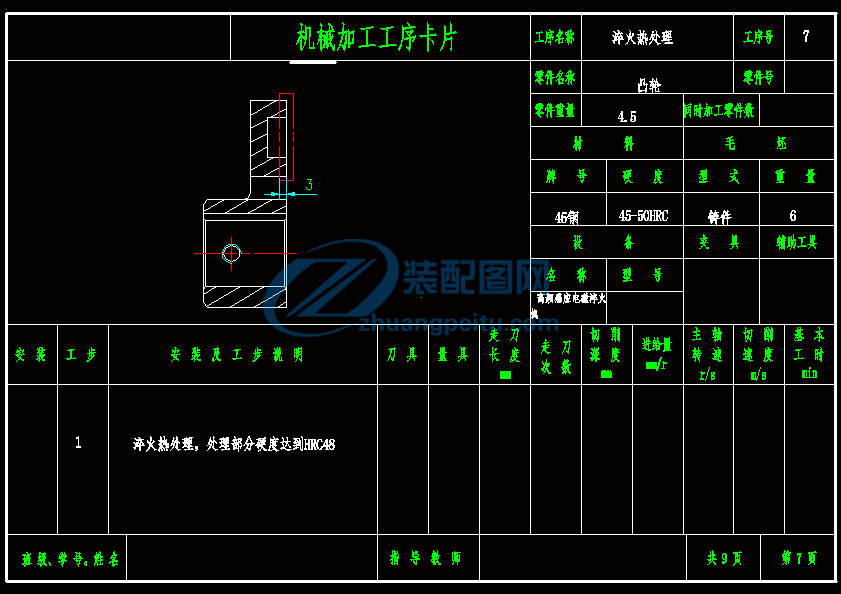
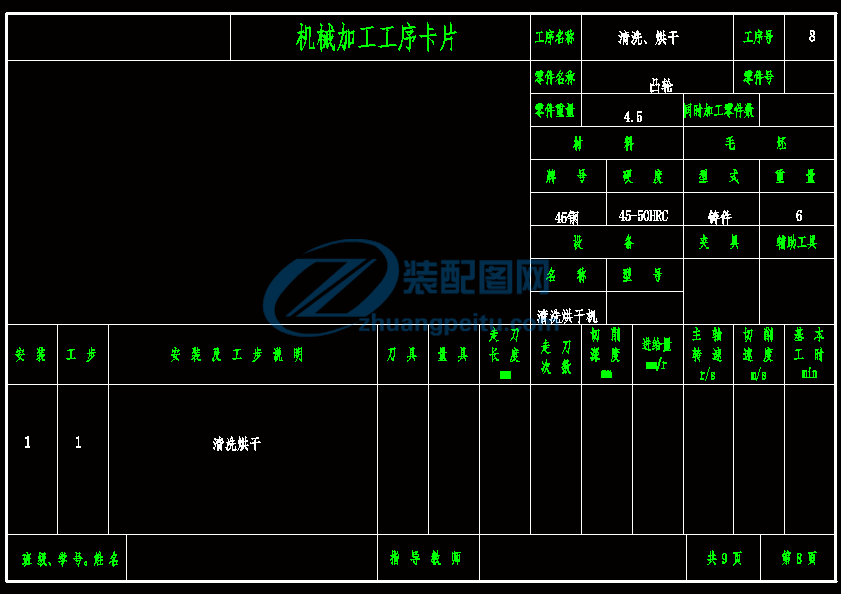

機械制造技術(shù)基礎
課程設計說明書
設計題目:凸輪零件的機械加工工藝規(guī)程及夾具設計
機械制造技術(shù)基礎課程設計任務書
題目:凸輪零件的機械加工工藝規(guī)程及夾具設計
內(nèi)容:1、零件圖 1張
2、毛坯圖 1張
3、機械加工工藝規(guī)程 10張
4、夾具結(jié)構(gòu)設計裝配圖 1張
5、夾具結(jié)構(gòu)設計零件圖 1張
6、課程設計說明書 1份
目錄
第一節(jié) 凸輪的工藝分析 3
一、凸輪用途 3
二、凸輪的技術(shù)要求 3
第二節(jié) 確定毛坯、繪制毛坯圖 4
一、選擇毛坯 4
二、確定毛坯的尺寸公差和機械加工余量 4
第三節(jié) 擬定工藝路線 5
一、定位基準的選擇 5
二、表面加工方法的確定 5
三、工序順序安排 5
四、確定工藝路線 6
第四節(jié) 切削用量、時間定額的計算 6
一、切削用量的計算 6
二、時間定額的計算 13
第五節(jié) 機床夾具設計 14
一、夾具設計任務 14
二、夾具設計定性分析 15
三、夾具使用要點 16
參考文獻 17
第一節(jié) 凸輪的工藝分析
一、凸輪用途
該凸輪應用在汽車變速箱的換擋機構(gòu)中。凸輪以孔通過鍵固定在軸上,與變速機構(gòu)連接的連桿安裝在凸輪槽內(nèi),凸輪擺動驅(qū)動連桿運動,實現(xiàn)換擋變速。
該凸輪在改換檔位時主要承受沖擊載荷的作用,因此該零件應具有足夠的強度,以適應凸輪的工作條件。該零件的主要工作表面為凸輪槽的兩側(cè)面、大端面、鍵槽。
二、凸輪的技術(shù)要求
表1-1 凸輪零件技術(shù)要求
加工表面
尺寸誤差
mm
表面粗糙度Ra
mm
形位誤差
mm
大端面
35mm
3.2
f28mm孔
3.2
鍵槽
6.3
凸輪槽側(cè)(底)面
16±0.1
3.2(6.3)
小端面
35mm
3.2
螺紋孔
M8
該凸輪形狀特殊,結(jié)構(gòu)簡單,屬于典型的偏心輪零件。凸輪槽兩側(cè)面在工作中需要承受沖擊載荷,為增強其耐磨性,該表面要求淬火處理,硬度為48HRC;為保證凸輪在驅(qū)動連桿運動過程中受力均勻,要求凸輪大端面對xx孔軸線的垂直度要求為0.05mm。
依據(jù)設計題目知:該零件的生產(chǎn)類型為大批大量生產(chǎn)。
第二節(jié) 確定毛坯、繪制毛坯圖
一、選擇毛坯
由于該凸輪在工作過程中要承受反復沖擊,小載荷,為增強凸輪的強度,且考慮零件材料為45鋼,因此選用鑄件。該零件的輪廓尺寸不大,且生產(chǎn)類型屬大批大量生產(chǎn),為提高生產(chǎn)率和鑄件精度,宜采用金屬模機器造型制造毛坯。毛坯的鑄造斜度為2°~3°
二、確定毛坯的尺寸公差和機械加工余量
由表2.3-5③可知,確定毛坯的尺寸公差和機械加工余量,如下表所示:
表2.3-5凸輪零件毛坯尺寸公差及機械加工余量
主要尺
寸名稱
基本
尺寸
加工余
量等級
加工余
量數(shù)值
總余量
公差CT
說明
厚度
35mm
G
3.00mm
6.00mm
2.80mm
雙側(cè)加工
孔
f28mm
H
1.15mm
3.30mm
2.60mm
孔降一級,雙側(cè)加工
三、繪制凸輪鑄造毛坯簡圖
見附圖2。
第三節(jié) 擬定工藝路線
一、定位基準的選擇
1.精基準的選擇
根據(jù)該零件的技術(shù)要求和裝配要求,選擇凸輪孔作為精基準,零件上的很多表面都可以采用它作為基準進行加工,即遵循“基準統(tǒng)一”的原則。Xx的軸線是設計基準,選用其作為精基準定位加工大端面、工藝孔、鍵槽、凸輪槽和小端面,實現(xiàn)了設計基準和工藝基準的重合,保證了被加工表面的垂直度要求。
2. 粗基準的選擇
作為粗精準的表面應平整,沒有鑄造毛刺和其他表面缺陷。本設計選擇f45mm外圓表面作為粗基準。采用f45mm外圓面定位加工內(nèi)孔可保證壁厚均勻;同時也能保證大端面與f28mm孔軸線的垂直度要求。
二、表面加工方法的確定
根據(jù)凸輪零件圖個加工表面的尺寸精度和表面粗糙度,確定加工工件各表面的加工方法,如表1-2所示。
表1-2 凸輪零件各表面加工方案
加工表面
尺寸精度等級
表面粗糙度Ra/mm
加工方案
備注
1
擴孔、鉸孔
數(shù)控機床
銑刀
2
通工藝孔
鉆床
直柄麻花鉆
3
粗精銑上下斷面
數(shù)控銑床
銑刀
4
加工鍵槽
拉床
拉刀
5
粗精加工凸輪槽
數(shù)控機床
莫氏立銑刀
6
鉆螺紋孔
鉆床
直柄麻花鉆,絲錐
7
局部淬火
8
倒角
鏜床
鏜刀
三、工序順序安排
1.機械加工工序
(1)遵循“先基準后其他”原則,首先加工精基準——xx
(2)遵循“先粗后精”原則,先安排粗加工工序,后安排精加工工序。
(3)遵循“先主后次”原則,先加工主要表面——xx孔、大端面和鍵槽、凸輪槽,后加工次要表面——小端面
(4)遵循“先面后孔”原則,先加工大端面,在加工2-f6mm工藝孔。
2.熱處理工序
凸輪槽在辦精工之后進行局部高頻淬火處理,提高其耐磨性和在工作中承受沖擊載荷的能力。
3.輔助工序
在辦精工之后,安排去毛刺和中間檢驗工序,最后清洗和終檢工序。
綜上所述,該凸輪工序的安排順序為:基準加工——主要表面粗加工及一些余量大的表面粗加工——主要表面半精加工和次要表面加工——熱處理。
四、確定工藝路線
工序I 粗銑孔至,半精銑孔,保證尺寸,表面粗糙度。
工序II 鉆工藝孔,保證設計尺寸,,,以孔軸線為定位基準,同時加一個厚度的側(cè)面。
工序Ⅲ 粗銑、半精銑大端面至。以φ28內(nèi)圓表面為粗基準,進行定位夾緊。粗車、半精車小端面,保證尺寸,表面粗糙度,并倒角內(nèi)孔倒角,以大端面為定位基準
工序Ⅳ 拉鍵槽,保證尺寸,槽頂面距離孔下母線 ,表面粗糙度。以孔軸線為定位基準。
工序Ⅴ 粗半精銑凸輪槽,保證槽深,寬,兩側(cè)面粗糙度,底面,以孔、鍵槽一側(cè)面和其中一個工藝孔進行定位。
工序Ⅶ 鉆螺紋孔,用絲錐攻絲,以小端面為工序基準。
工序Ⅷ 凸輪槽局部淬火,深度,保證HB348HRC。
工序Ⅸ 倒角 倒角1x45° 倒角2×45°
第四節(jié) 切削用量、時間定額的計算
一、切削用量的計算
1.工序1
(1)要求:保證孔尺寸,粗糙度;
機床:數(shù)控機床 KX5012
刀具:銑刀
(2)計算切削用量
1)粗銑孔工步
①切削深度
②進給量 根據(jù)已知條件,從表2-5②查得,根據(jù)所用的CA6140車床的技術(shù)參數(shù),實際選取。
③切削速度采用查表法確定,從表2-7②查得,實際選取 ,由可推出機床的主軸轉(zhuǎn)速
根據(jù)所用機床的主軸轉(zhuǎn)速數(shù),取,故實際切削速度為
④切削工時根據(jù)表5-39①,計算
式中
2)半精孔工步
①切削深度
②進給量 根據(jù)已知條件,從表2-5②查得,根據(jù)所用的技術(shù)參數(shù),實際選取。
③切削速度,車床主軸轉(zhuǎn)速,同上。
④切削工時
2.工序2
(1)要求:保證,,,。
機床:立式鉆床ZF5132
刀具:直柄麻花鉆
(2)計算切削用量
①進給量(見《切削手冊》表2.7)
②計算切削速度,按《切削手冊》表2.13及表2.14按5類加工性質(zhì)考慮
③確定主軸轉(zhuǎn)速
④按機床選取 (按《工藝手冊》表9-3)
所以實際切削速度
⑤切削工時
其中切入切出長度分別定為
3、工序3
要求:粗銑、半精銑大端面至,小端面至35mm。
機床:數(shù)控機床 KX5012
刀具:銑刀
粗銑大端面工步
①切削深度
②進給量 根據(jù)已知條件,從表2-5②查得,根據(jù)所用的技術(shù)參數(shù),實際選取。
③切削速度采用查表法確定,從表2-7②查得選取 ,由可推出機床的主軸轉(zhuǎn)速
根據(jù)所用的主軸轉(zhuǎn)速數(shù),取,故實際切削速度為
④切削工時根據(jù)表5-39①,計算
式中
4)半精大端面工步
①切削深度 ,
②進給量 根據(jù)零件圖附圖1提供的加工表面粗糙度的要求,從表2-6②查得,根據(jù)所用的進給量數(shù)列取。
③切削速度采用查表法確定,從表2-7②查得選取 ,由可推出機床的主軸轉(zhuǎn)速
根據(jù)所用的主軸轉(zhuǎn)速數(shù),取,故實際切削速度為
④切削工時 根據(jù)表5-39①,計算
式中
粗車、半精車小端面
(2)計算切削用量
1)粗車小端面工步
①切削深度
②進給量 根據(jù)已知條件,從表2-5②查得,根據(jù)所用的CA6140車床的技術(shù)參數(shù),實際選取。
③切削速度采用查表法確定,從表2-7②查得選取 ,由可推出機床的主軸轉(zhuǎn)速
根據(jù)所用CA6140型車床的主軸轉(zhuǎn)速數(shù),取,故實際切削速度為
④切削工時根據(jù)表5-39①,計算
式中
4)半精車小端面工步
①切削深度 ,
②進給量 根據(jù)零件圖附圖1提供的加工表面粗糙度的要求,從表2-6②查得,根據(jù)所用的CA6140車床的進給量數(shù)列取。
③切削速度 采用查表法確定,從表2-7②查得選取 ,由可推出機床的主軸轉(zhuǎn)速
根據(jù)所用CA6140型車床的主軸轉(zhuǎn)速數(shù),取,故實際切削速度為
④切削工時 根據(jù)表5-39①,計算
式中切入切出長度分別定為
4.工序4
(1)要求:保證尺寸,,粗糙度。
機床:臥式拉床,L6120
刀具:鍵槽拉刀,
(2)計算切削用量
1)單面齒升 根據(jù)有關手冊定為
2)拉削速度定為(即)
3)切削工時:
式中Z-單面余量
-拉削長度
-考慮校準部分的長度系數(shù) 取1.2,
k-考慮機床返回行程系數(shù) 取1.4,
v-拉削速度,-拉刀單面齒升
拉刀同時工作的齒數(shù),拉刀齒距
4)拉刀同時工作的齒數(shù)
所以
5、工序5
(1)要求:槽深,寬,兩側(cè)面粗糙度,底面
機床:立式鉆床Z525
刀具:莫式錐柄立銑刀
(2)計算切削用量
1)粗加工凸輪槽深度工步
①進給量齒
②切削速度參考有關手冊。定為,
③確定主軸轉(zhuǎn)速莫氏立銑刀,,則
④切削工時
式中切入切出長度分別定為
2)精加工凸輪槽至8mm深
①進給量,切削速度,主軸轉(zhuǎn)速同上。
②切削工時
式中切入切出長度分別定為
6、工序6
(1)要求:M8螺紋孔
機床:立式鉆床ZF5132
刀具:直柄麻花鉆,絲錐
(2)計算切削用量
1)鉆孔工步
①進給量取根據(jù)《切削手冊》表2.7當鋼的時,
②確定切削速度:根據(jù)《切削手冊》表2.13及表2.14的切削速度,
③確定主軸轉(zhuǎn)速 ,
④根據(jù)機床說明書取 ,
故實際切削速度為 ,
⑤切削工時
式中切入切出長度分別定為
2)攻螺紋工步
①進給量取
②確定切削速度 取
③確定主軸轉(zhuǎn)速
④按機床說明書選取,則
⑤切削工時
式中切入切出長度分別定為
二、時間定額的計算
時間定額計算包括基本時間、輔助時間其他時間(布置工地時間和休息與生理需要時間)以及單件時間的計算。上面部分以對基本時間做了計算,下面就對其余三項進行計算。
1.根據(jù)第五章第二節(jié)所述,輔助時間與基本時間之間的關系為┄①;
2.除了作業(yè)時間(基本時間和輔助時間之和)以外,每道工序的單件時間還包括布置工地時間和休息與生理需要時間、準備和終結(jié)時間。由于凸輪的生產(chǎn)類型為大批大量生產(chǎn),分攤每個工件上的準備和終結(jié)時間甚微,可忽略不計;布置工地時間是作業(yè)時間的,休息與生理需要時間是作業(yè)時間的,本設計均取,則各工序的其他時間()可按關系式┄②計算;
3.單件時間┄③;
綜上所述,可以得到單件時間,
因此各工序的單件時間分別為:
工序1的單件時間:1.34min
工序2的單件時間:0.34min
工序3的單件時間:26.98min
工序4的單件時間:0.14min
工序5的單件時間:2.24min
工序6的單件時間:0.94min
工序7的單件時間:0.8min
工序8的單件時間:0.5min
第五節(jié) 機床夾具設計
一、夾具設計任務
為了提高生產(chǎn)效率,保證加工質(zhì)量,降低勞動強度,需要設計專門的夾具經(jīng)過指導教師的協(xié)商,決定設計對凸輪M8螺紋孔的加工的夾具。
二、夾具設計定性分析
1.問題的提出
本夾具主要用來對凸輪M8螺紋孔的加工,在本道工序加工時,應主要考了如何提高勞動生產(chǎn)率,降低勞動強度。
2.夾具設計
1)將凸輪放置于夾具工作臺的平面上,使M8螺紋孔與水平面垂直;
2)將凸輪放于夾具工作臺底面,心軸穿過凸輪直徑28mm孔和直徑6mm孔;
3)通過旋轉(zhuǎn)手柄壓緊凸輪達到完全定位目的;
3.定位方案
通過定位螺栓對直徑28mm孔和直徑6mm孔的定位,限制了凸輪的3個自由度。以此達到對凸輪的定位。
4.夾緊力分析
夾緊力的作用點位于凸輪豎直面的最大厚度上,與加工表面垂直,利于夾緊穩(wěn)固可靠。
三、夾具使用要點
工件裝夾時, 應先定位凸輪的直徑28MM孔,然后調(diào)節(jié)定位螺釘,待定位螺釘處的工藝孔定位準確后,最后旋轉(zhuǎn)固定手柄壓緊,得到定位。
參考文獻
[1]于俊一,鄒青主編.機械制造技術(shù)基礎.北京:機械工業(yè)出版社2004.1
[2]鄒青主編.機械制造技術(shù)基礎課程設計指導教程.北京:機械工業(yè)出版社2004.8
[3]李洪主編.機械加工工藝手冊.北京:北京出版社 1990.12
[4]上海市金屬切削技術(shù)協(xié)會主編.技術(shù)切削手冊 第二版.上海:上??茖W技術(shù)出版社1984.4
[5]趙家齊主編.機械制造工藝學課程設計指導書 第二版.哈爾濱工業(yè)大學機械工業(yè)出版社 2002
14