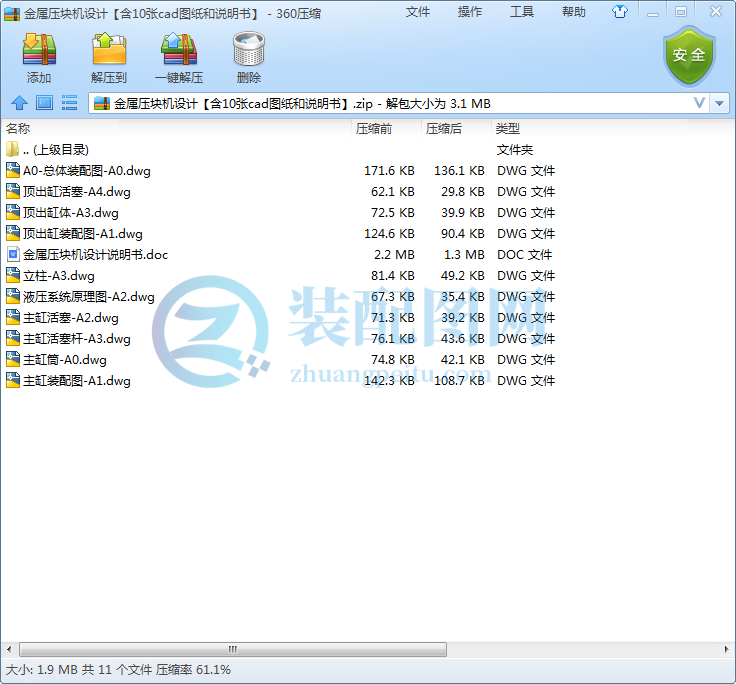
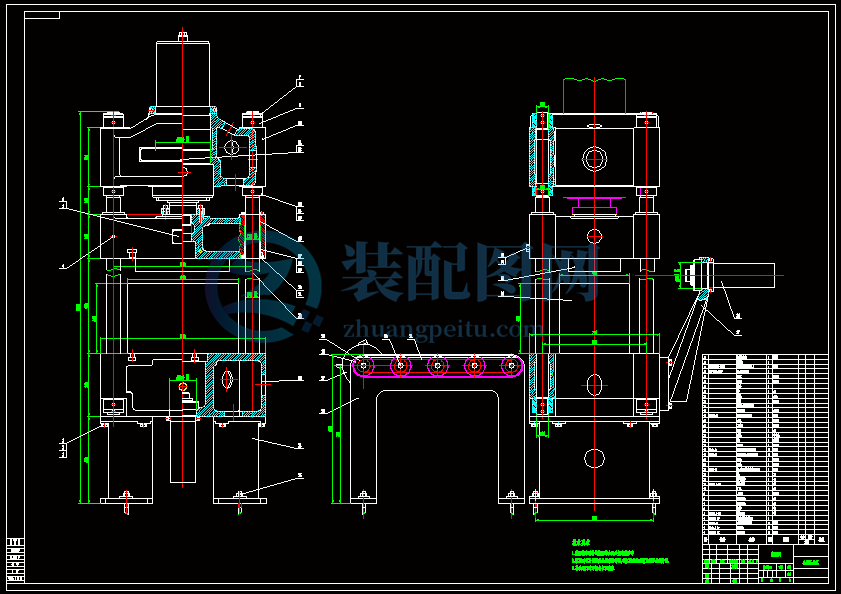

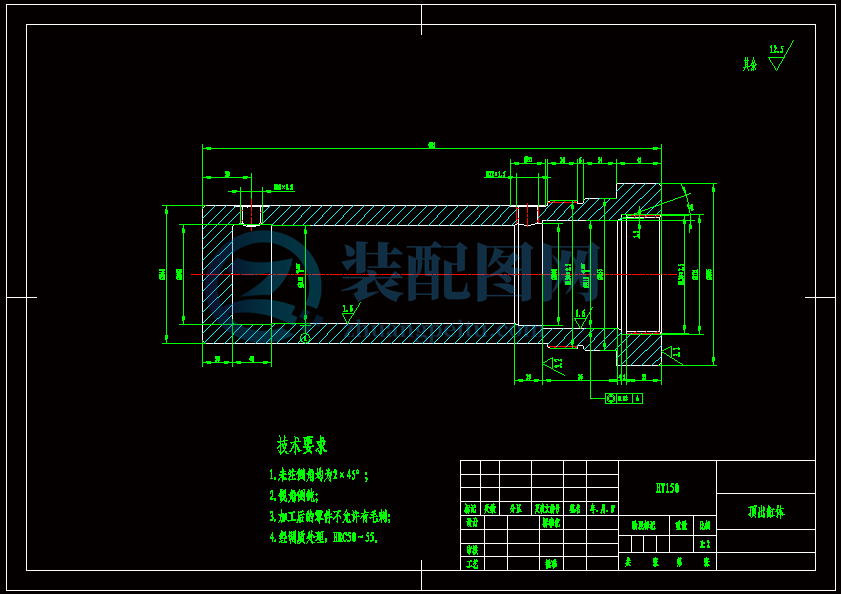
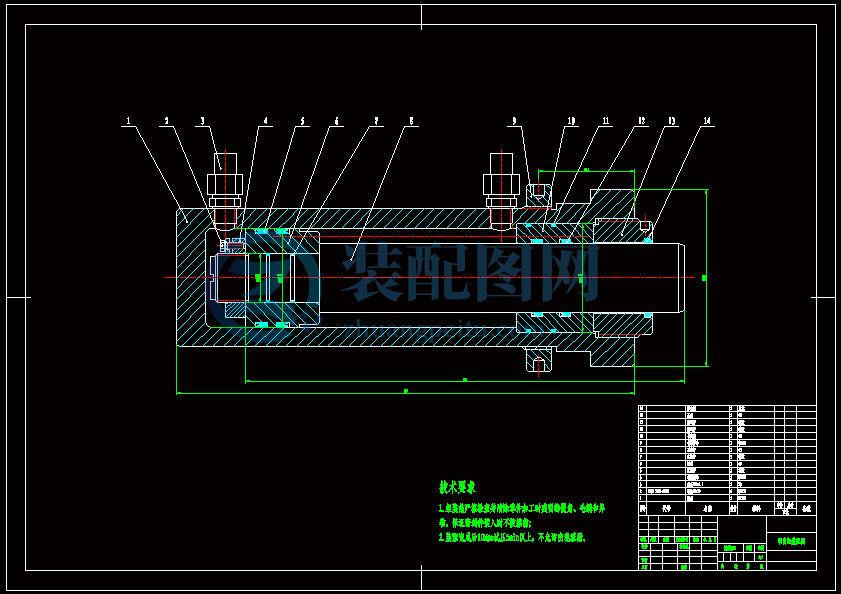
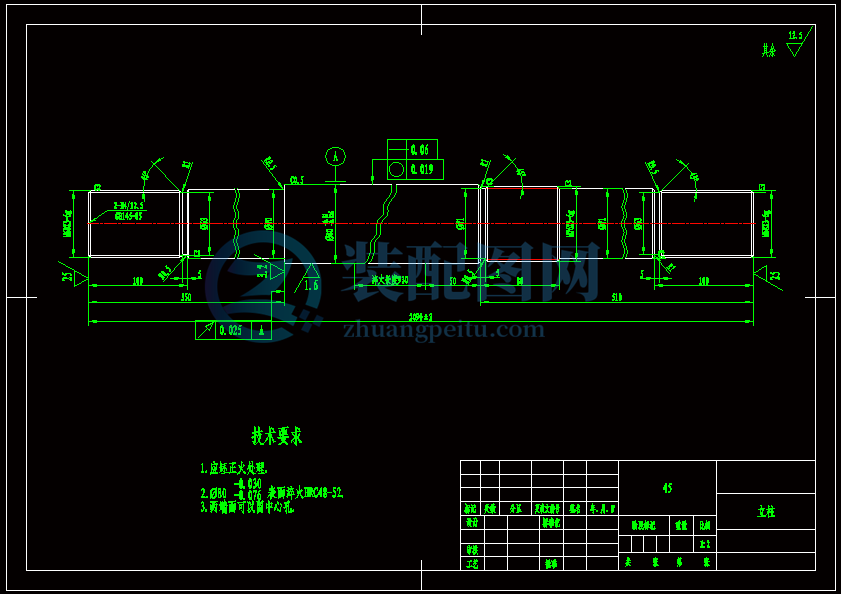
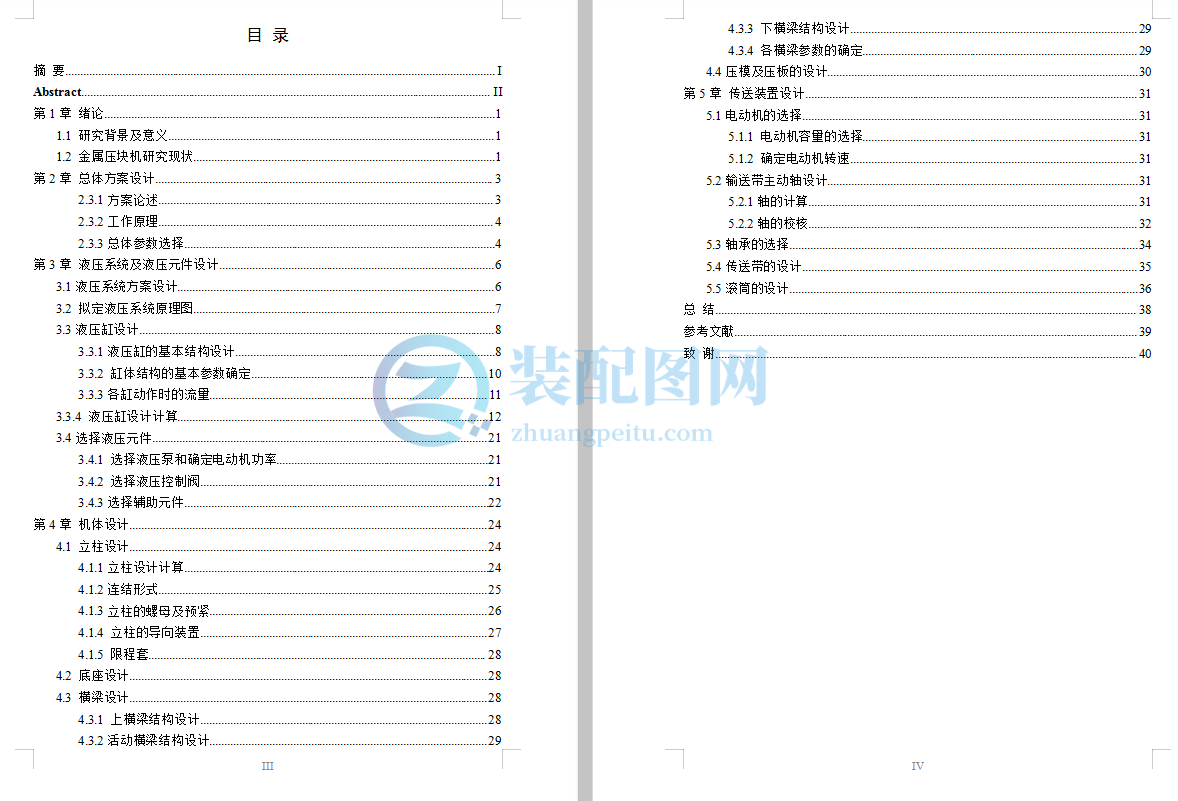
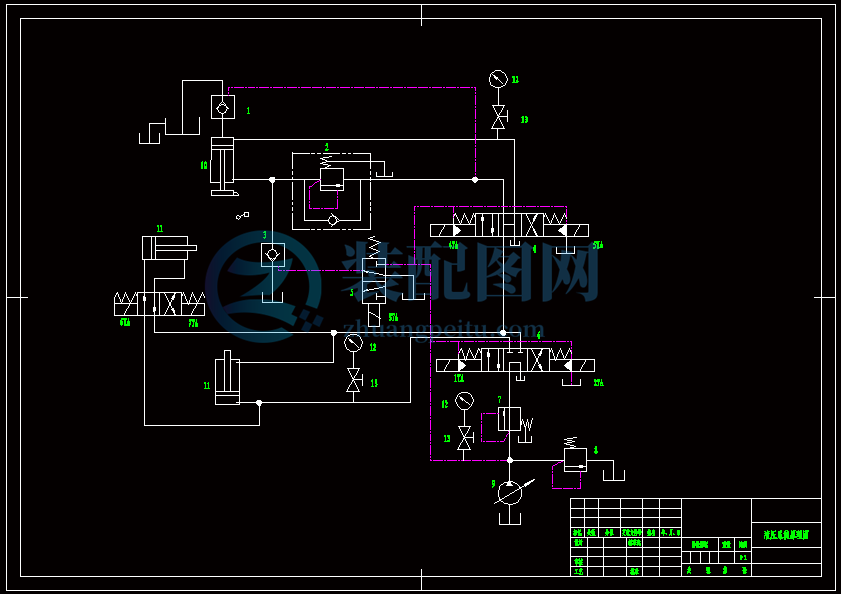
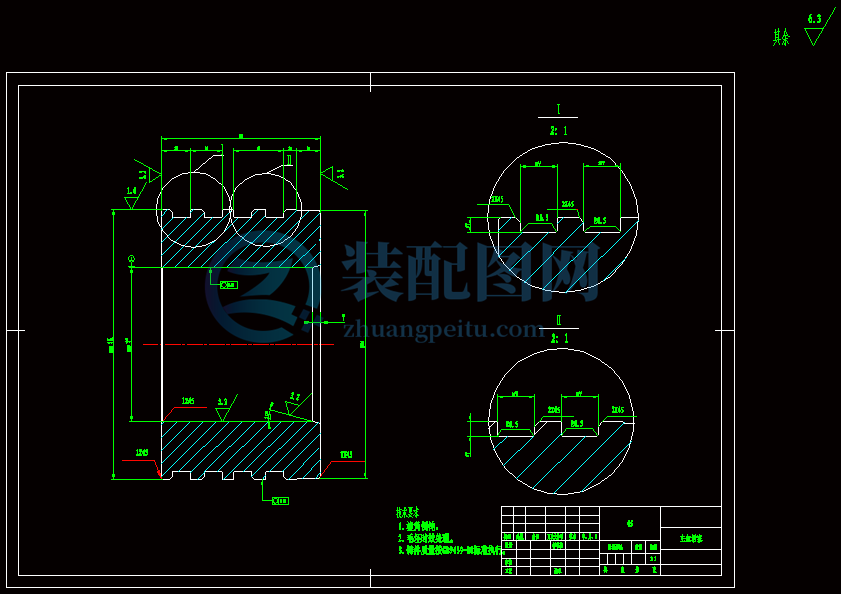
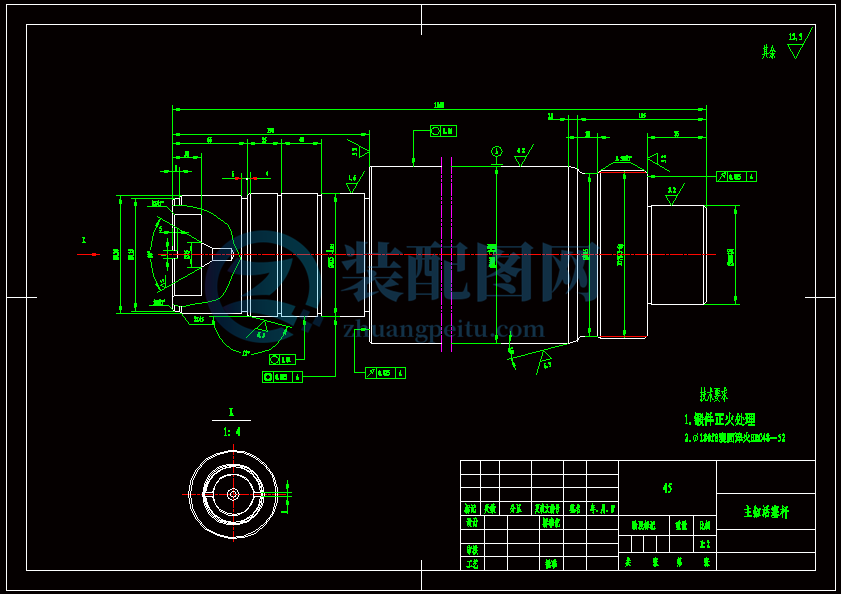
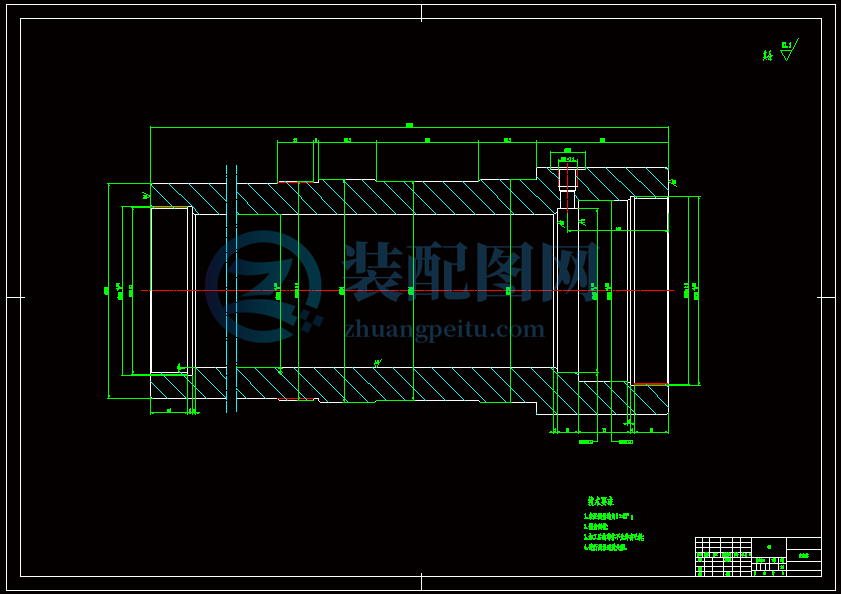
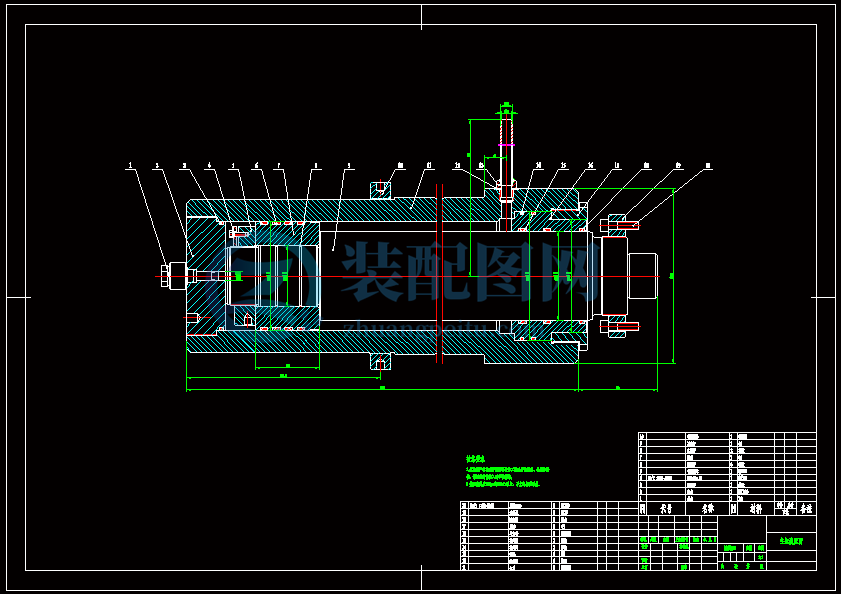
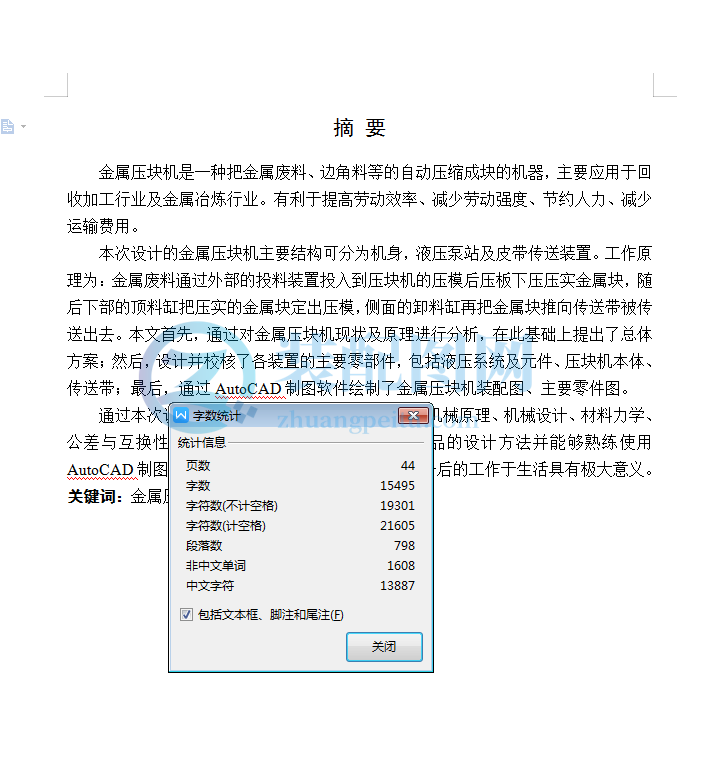
壓縮包內含有CAD圖紙和說明書,Q 197216396 或 11970985
摘 要
金屬壓塊機是一種把金屬廢料、邊角料等的自動壓縮成塊的機器,主要應用于回收加工行業(yè)及金屬冶煉行業(yè)。有利于提高勞動效率、減少勞動強度、節(jié)約人力、減少運輸費用。
本次設計的金屬壓塊機主要結構可分為機身,液壓泵站及皮帶傳送裝置。工作原理為:金屬廢料通過外部的投料裝置投入到壓塊機的壓模后壓板下壓壓實金屬塊,隨后下部的頂料缸把壓實的金屬塊定出壓模,側面的卸料缸再把金屬塊推向傳送帶被傳送出去。本文首先,通過對金屬壓塊機現(xiàn)狀及原理進行分析,在此基礎上提出了總體方案;然后,設計并校核了各裝置的主要零部件,包括液壓系統(tǒng)及元件、壓塊機本體、傳送帶;最后,通過AutoCAD制圖軟件繪制了金屬壓塊機裝配圖、主要零件圖。
通過本次設計,鞏固了大學所學專業(yè)知識,如:機械原理、機械設計、材料力學、公差與互換性理論、機械制圖等;掌握了機械產品的設計方法并能夠熟練使用AutoCAD制圖及Pro/E軟件進行三維設計軟件,對今后的工作于生活具有極大意義。
關鍵詞:金屬壓塊;液壓系統(tǒng);機體;傳送帶
Abstract
Metal baler is a kind of machine that automatically compresses metal scrap, scrap and so on. It is mainly used in recycling processing industry and metal smelting industry. It is conducive to improving labor efficiency, reducing labor intensity, saving manpower and reducing transportation costs.
The main structure of the metal briquetting machine can be divided into fuselage, hydraulic pumping station and belt conveyor. The principle of the work is that the metal scrap compacts the metal block under the pressure die of the press through the external feeding device, and then the top cylinder of the lower part sets the compacted metal block out of the die, and the unloading cylinder on the side then push the metal block to the conveyor belt to be sent out. First, through the analysis of the status and principle of the metal pressing machine, the overall plan is put forward. Then, the main parts of each device are designed and checked, including the hydraulic system and components, the block press body and the conveyor belt. Finally, the assembly drawing of the metal pressing machine is drawn by the AutoCAD drawing software. Want part drawing.
Through this design, we have consolidated the professional knowledge of the University, such as mechanical principle, mechanical design, material mechanics, tolerance and interchangeability theory, mechanical drawing, and so on. It has mastered the design method of mechanical products and is able to use AutoCAD drawing and Pro/E software to carry out three-dimensional design software skillfully. It is of great significance.
Key words: Metal briquetting; Hydraulic system; Airframe; Conveyor belt
目 錄
摘 要 I
Abstract II
第1章 緒論 1
1.1 研究背景及意義 1
1.2 金屬壓塊機研究現(xiàn)狀 1
第2章 總體方案設計 3
2.3.1方案論述 3
2.3.2工作原理 4
2.3.3總體參數(shù)選擇 4
第3章 液壓系統(tǒng)及液壓元件設計 6
3.1液壓系統(tǒng)方案設計 6
3.2 擬定液壓系統(tǒng)原理圖 7
3.3液壓缸設計 8
3.3.1液壓缸的基本結構設計 8
3.3.2 缸體結構的基本參數(shù)確定 10
3.3.3各缸動作時的流量 11
3.3.4 液壓缸設計計算 12
3.4選擇液壓元件 21
3.4.1 選擇液壓泵和確定電動機功率 21
3.4.2 選擇液壓控制閥 21
3.4.3選擇輔助元件 22
第4章 機體設計 24
4.1 立柱設計 24
4.1.1立柱設計計算 24
4.1.2連結形式 25
4.1.3立柱的螺母及預緊 26
4.1.4 立柱的導向裝置 27
4.1.5 限程套 28
4.2 底座設計 28
4.3 橫梁設計 28
4.3.1 上橫梁結構設計 28
4.3.2活動橫梁結構設計 29
4.3.3 下橫梁結構設計 29
4.3.4 各橫梁參數(shù)的確定 29
4.4壓模及壓板的設計 30
第5章 傳送裝置設計 31
5.1電動機的選擇 31
5.1.1 電動機容量的選擇 31
5.1.2 確定電動機轉速 31
5.2輸送帶主動軸設計 31
5.2.1軸的計算 31
5.2.2軸的校核 32
5.3軸承的選擇 34
5.4傳送帶的設計 35
5.5滾筒的設計 36
總 結 38
參考文獻 39
致 謝 40
41
第1章 緒論
1.1 研究背景及意義
工業(yè)化初期由于盲目擴大生產,金屬浪費現(xiàn)象嚴重,金屬回收利用較少,廢金屬對環(huán)境的污染與日劇增。隨著我國經(jīng)濟增長方式由粗放型向集約型的轉變和人們環(huán)保意識的增強,市場對廢金屬處理的工藝及設備需求將越來越大。因此,將廢金屬的有效回收和利用迫在眉睫,所以我想要設計一個可以把廢金屬進行壓塊的機器使得金屬垃圾在運輸和投爐時變得方便。
隨著科學技術的發(fā)展和人民生活水平的提高,各工業(yè)部門的金屬下腳料及生活用金屬制品的廢棄物都日益增多,這無疑將會對人類環(huán)境產生污染;另方面人類社會的不斷消耗,各類礦物資源也會逐漸減少。如何利用金屬廢棄物,即防止污染,又變廢為寶,資源永續(xù)成為一個重要的研究課題擺在人類面前。近年來,社會各界十分重視提高壓塊機械及整個壓塊系統(tǒng)的通用能力和多功能集成能力,液壓金屬壓塊機研制的最終目的是將各種金屬邊角料(鋼刨花、廢鋼、廢鋁、廢銅、廢不銹鋼以及報廢汽車廢料等)擠壓成長方體形狀的合格爐料,既可降低運輸和冶煉成本,又可提高投爐速度。目前,我國壓塊機械還是以仿制為主,對國外的產品稍加改進,談不上開發(fā)研究,在企業(yè)管理上,往往重生產加工、輕研究開發(fā)、創(chuàng)新不夠,所以我們要敢于創(chuàng)新,在自身方面探索研究實踐,加強自身的技術,為我國包裝機械的發(fā)展做出自身的貢獻[1]。
1.2 金屬壓塊機研究現(xiàn)狀
工業(yè)化初期由于盲目擴大生產,金屬浪費現(xiàn)象嚴重,金屬回收利用較少,廢金屬對環(huán)境的污染與日劇增。隨著我國經(jīng)濟增長方式由粗放型向集約型的轉變和人們環(huán)保意識的增強,市場對廢金屬處理的工藝及設備需求將越來越大。因此,將廢金屬的有效回收和利用迫在眉睫。
從第一臺壓塊機出現(xiàn)以來,已引起眾多研究者的興趣,并研究開發(fā)了許多原型壓塊機和試驗裝置,從而大大推動了液壓廢金屬壓塊機的發(fā)展。但是,應該清楚地認識到,研究開發(fā)液壓廢金屬壓塊機的最終目的是克服傳統(tǒng)壓塊機的某些不足之處,進一步滿足用戶對提高機床動態(tài)性能.降低零件加工成本的需求。液壓廢金屬壓塊機設計的第一步就是認真分析市場需求和明確應用領域,諸如待壓零件的形狀材料尺寸和精度,所采用的加工工藝以及批量和預期加工成本等。
對壓塊機的研究現(xiàn)在已經(jīng)達到一個很高的水平,但開始,人們還只是對這種機構停留在理論分析上。這是因為液壓壓塊機在理論和實踐上有一系列的難題,難以在短期內解決。
目前,國內外有許多公司和研究單位在研究液壓廢金屬壓塊機。我國的液壓壓塊機研究起步較晚,但成果顯著。
由我國研制的YJD1250金屬壓塊機,吸收了國內外同類機器的特點,大膽采用了新結構,不僅具有國內外同類機器的功能,而且結構更加緊湊,運行良好,成本比進口同類機低得多。
由南京工業(yè)學校研制的YJY2500液壓金屬壓塊機將金屬廢料壓塊成形,為冶金企業(yè)提供合格的回爐料,該機是目前壓塊機中性能先進的一種。其中主要參數(shù)公稱壓力(KN)①主缸2500②側缸2×1250③蓋缸1250④輔助缸400⑤壓塊密度(kg/m3)≥2000(對黑色金屬)⑥壓縮室尺寸(mm)2500×1800×900⑦壓塊尺寸(mm)(460-500×460×600)⑧機器外形尺寸(mm)8000×6000×4000⑨機動循環(huán)時間(s)240
中南工業(yè)大學機電學院機電所研制的銅鋁屑壓塊機介紹了銅鋁屑壓塊機液壓系統(tǒng)和電氣系統(tǒng)設計, 以PLC 為核心的電氣系統(tǒng)和“柔性”的液壓設備相結合,大大提高了工作效率。應用PLC 控制的壓塊機, 性能優(yōu)良、工作可靠,企業(yè)只投入?yún)^(qū)區(qū)幾萬元, 大大改善工作環(huán)境, 降低工人勞動強度, 而且便于貴金屬鋸屑回收, 提高了生產效率, 降低產品成本。
第2章 總體方案設計
2.1設計要求
設計一款可以把金屬進行壓塊的機器。
要求:
(1)盡可能滿足工藝要求,便于操作。
(2)有良好的剛度,使用可靠不易壞。
(3)有好的經(jīng)濟性,使用方便。
2.2金屬壓塊機原理
液壓金屬壓塊機的基本原理就是利用金屬材料在外力作用下,能產生塑性變形的性質,給金屬材料以足夠的、能聚集并產生永久形變的外力,從而形成緊密的束塊。所以不能產生塑性形變,或塑性變形很小的金屬,不能直接進行壓塊處理。如高碳鋼、工具鋼、鋼絲繩及鑄鐵等,就不能直接裝機進行壓塊。
金屬壓塊的基本要求:(1)要有足夠的擠壓力。能使被處理的金屬材料產生塑性變形束塊,并使被束塊達到一定要求的密度。(2)要有一個能容納金屬物料、并能封閉起來承受擠壓力的料箱。在滿足這兩項基本要求的前提下,又根據(jù)不同的應用要求和不同的處理對象,就產生了許多不同類型的金屬壓塊機。金屬壓塊機的工作原理,就是在一個封閉的料箱內,使用工作力推動壓頭對金屬物料進行擠壓,使金屬物料形成一定尺寸和密度的束塊。
2.3總體方案及參數(shù)選擇
2.3.1方案論述
常用的金屬壓塊機有立式和臥式兩種結構:
立式金屬壓塊機占地面積小,而且其主機通常可以用普通的壓力機改造而成,所以應用比較廣泛,但是立式金屬壓塊通常壓塊的料箱比臥式的小,單次壓塊體積相對要小,所以壓塊效率相對較低,但壓緊度比臥式的要高。
臥式金屬壓塊機,機體龐大占地面積大,需要專用的液壓站配套,且設備壓力較高,通常只專門的金屬廢料處理企業(yè)或者廢料量大的金屬加工企業(yè)才會選用,其壓塊的料箱可以做得非常大,單次壓塊體積也大,所以壓塊效率比較高,但壓緊度比立式的要小,而且要想提高壓緊度需要較大的提高設備壓力。
通過對上述立式和臥式金屬壓塊機的對比分析,本次設計的金屬壓塊機是為了適用更多場合,要求經(jīng)濟性好,使用方便,因此本次采用立式結構,其結構簡圖如下圖2-1所示。
圖2-1 立式金屬壓塊機結構簡圖
2.3.2工作原理
本次設計的金屬壓塊機工作原理為:首先金屬廢料通過外部的投料裝置投入到壓塊機的壓模;接著壓板下壓壓實金屬塊,壓實完成后下部的頂料缸把壓實的金屬塊定出壓模,隨后置于側面的卸料缸把頂出壓模的金屬塊推向傳送帶被傳送出去,如此一次壓塊完成。
2.3.3總體參數(shù)選擇
根據(jù)表2-2可知1000 kN 壓塊機的基本參數(shù)。
表2-2 壓塊機的基本參數(shù)(JB/T 9957.2—1999)(節(jié)選)
名稱
單位
參數(shù)
公稱力P
kN
1000
滑塊行程S
mm
600
開口高度H
mm
900
空程下行
mm/s
22
工作
mm/s
14
回程
mm/s
47
工作臺面有效尺寸
左右x前后(BxT)
mm
720x580
頂出力P1
kN
190
頂出行程S1
mm
500
推料力P1
kN
190
推料行程S1
mm
500
第3章 液壓系統(tǒng)及液壓元件設計
3.1液壓系統(tǒng)方案設計
壓塊機液壓系統(tǒng)的特點是在行程中壓力變化很大,所以在行程中不同階段保證達到規(guī)定的壓力是系統(tǒng)設計中首先要考慮的。
確定壓塊機的液壓系統(tǒng)方案時要重點考慮下列問題:
(1)快速行程方式
壓塊機液壓缸的尺寸較大,在快速下行時速度也較大,需要的流量較大(289.4 L/min),這樣大流量的油液如果由液壓泵供給;則泵的容量會很大。壓塊機常采用的快速行程方式可以有許多種,本機采用自重快速下行方式。
(2)減速方式
壓塊機的運動部件在下行行程中快接近制件時,應該由快速變換為較慢的壓制速度。減速方式主要有壓力順序控制和行程控制兩種方式;壓力順序控制是利用運動部件接觸制件后負荷增加使系統(tǒng)壓力升高到一定值時自動變換速度;
(3)壓制速度的調整
制件的壓制工藝一般要提出一定壓制速度的要求,解決這一問題的方很多。本例中采用機動伺服變量泵,故仍利用行程擋塊(塊擋的形狀)來使液壓泵按一定規(guī)模變化以達到規(guī)定的壓制速度。
(4)壓制壓力及保壓
在壓制行程中不同階段的系統(tǒng)壓力決定于負載,為了保證安全,應該限制液壓系統(tǒng)的最高壓力,本系統(tǒng)擬在變量泵的壓油口與主油路間并聯(lián)一只溢流閥作安全閥用。
有時壓制工藝要求液壓缸在壓制行程結束后保壓一定時間,保壓方法有停液壓泵保壓與開液壓泵保壓兩種,本系統(tǒng)根據(jù)壓機的具體情況擬采用開液壓泵保壓;此法的能量消耗較前一種大。但系統(tǒng)較為簡單。
(5)泄壓換向方法
若泄壓過快,將引起劇烈的沖擊、振動和驚人的聲音,甚至會因液壓沖擊而使元件損壞。此問題在大型壓塊機中愈加重要。本例采用帶阻尼狀的電液動換向閥,該閥中位機能是H型,控制換向速度,延長換向時間,就可以使上腔高壓降低到一定值后才將下腔接通壓力油。此法最為簡單,適合于小型壓機。
(6)主缸與頂出缸、卸料缸的互鎖控制回路
為保障頂出缸、卸料缸的安全,在主缸動作時,必須保證頂出缸、卸料缸的活塞下行到最下位置。本例采用兩個換向閥適當串聯(lián)的方法來實現(xiàn)兩缸的互鎖控制(見圖4-1)。
3.2 擬定液壓系統(tǒng)原理圖
在以上分析的基礎上,擬定的液壓系統(tǒng)原理圖如圖4-1所示。
圖4-1 壓塊機液壓系統(tǒng)原理圖
系統(tǒng)的工作過程如下:
液壓泵起動后,電液換向閥4及6處于中位,液壓泵輸出油液經(jīng)背壓閥7再經(jīng)閥6的中位低壓卸荷,此時主缸處于最上端位置而頂出缸、卸料缸在最下端位置,電磁鐵2YA得電,換向閥6在右位工作,此時5YA得電,換向閥4也在右位工作,液壓泵輸出的壓力油進入主缸上腔,此時3YA也得電,控制油路經(jīng)閥5通至液控單向閥3,使閥3打開,主缸下腔的油能經(jīng)閥3很快排入油箱,主缸在自重作用下實現(xiàn)快速空程下行,由于活塞快速下行時液壓泵進入主缸上腔的流量不足,上腔形成負壓,充液筒中的油液經(jīng)充液閥(液控單向閥)1吸入主缸。
當電氣擋塊碰到行程開關時3YA失電,控制油路斷開,閥3關閉,此時單向順序閥(平衡閥)2使主缸下腔形成背壓,與移動件的自重相平衡。自重快速下行結束。與此同時用行程擋塊使液壓泵的流量減小,主缸進入慢速下壓行程,在此行程中可以用行程擋塊控制液壓泵的流量適應壓制速度的要求。由壓力表刻度指示達到壓制行程的終點。
行程過程結束后,可由手動按鈕控制使5YA失電,4YA得電,換向閥4換向,由于閥2帶阻尼器,換向時間可以控制,而閥4的中位機能是H型,閥處于中位時使主缸上腔的高壓油泄壓,然后閥4再換為左位,此時壓力油經(jīng)閥2的單向閥進入主缸下腔,由于下腔進油路中的油液具有一定壓力;故控制油路可以使閥1打開,主缸上腔的油液大部分回到充液筒,一部分經(jīng)閥4排回油箱,此時主缸實現(xiàn)快速回程。充液筒油液充滿后,溢出的油液可經(jīng)油管引至油箱。
回程結束后,閥4換至中位,主缸靜止不動。
1YA得電,2YA失電,閥6換至左位,壓力油進入頂出缸、卸料缸下腔,頂出缸、卸料缸頂出制件,然后1YA失電,2YA得電,閥6換至右位,頂出缸、卸料缸回程;回程結束后,2 YA失電,閥6換至中位,工作循環(huán)完成,系統(tǒng)回到原始狀態(tài)。液壓系統(tǒng)電磁鐵動作見表4-1。
4.1 電磁鐵動作循環(huán)表
元件
動作
1YA
2YA
3YA
4YA
5YA
主缸快速下行
–
+
+
–
+
主缸慢速下壓
–
+
–
– –
+
主缸泄壓
–
+
–
-
–
主缸回程
–
+
–
+
–
頂出缸、卸料缸頂出
+
–
–
+
–
頂出缸、卸料缸回程
–
+
–
+
–
原位卸荷
–
–
–
–
–
3.3液壓缸設計
3.3.1液壓缸的基本結構設計
(1)液壓缸的類型
圖3-1雙作用單活塞桿液壓缸
液壓缸選用雙作用單活塞桿液壓缸,活塞在行程終了時緩沖。因為工作過程中需要往復運動,從圖可見,油缸被活塞頭分隔為兩腔,側面有兩個進油口,因此,可以獲得往復的運動。實質上起到兩個柱塞缸的作用。此種結構形式的油缸,在中小型壓塊機上應用最廣。
(2)鋼筒的連接結構
在設計中上、頂出缸、卸料缸都選擇法蘭連接方式。這種結構簡單,易加工,易裝卸。
主缸采用前端法蘭安裝,頂出缸、卸料缸采用后端法蘭安裝。
缸口部分采用了Y形密封圈、導向套、O形防塵圈和鎖緊裝置等組成,用來密封和引導活塞桿。由于在設計中缸孔和活塞桿直徑的差值不同,故缸口部分的結構也有所不同。
(3)缸底結構
缸底結構常應用有平底、圓底形式的整體和可拆結構形式。
平底結構具有易加工、軸向長度短、結構簡單等優(yōu)點。所以目前整體結構中大多采用平底結構。圓底整體結構相對于平底來說受力情況較好,因此,在相同應力,重量較輕。另外,在整體鑄造的結構中,圓形缸底有助于消除過渡處的鑄造缺陷。但是,在壓塊機上所使用的油缸一般壁厚均較大,而缸底的受力總是較缸壁小。因此,上述優(yōu)點就顯得不太突出,這也是目前在整體結構中大多采用平底結構的一個原因。然而整體結構的共同缺點為缸孔加工工藝性差,更換密封圈時,活塞不能從缸底方向拆出,但由于較可拆式缸底結構受力情況好、結構簡單、可靠,因此在中小型壓塊機中使用也較廣。
在設計中選用的是平底結構。
(4)油缸放氣裝置
通常油缸在裝配后或系統(tǒng)內有空氣進入時,使油缸內部存留一部分空氣,而常常不易及時被油液帶出。這樣,在油缸工作過程中由于空氣的可壓縮性,將使活塞行程中出現(xiàn)振動。因此,除在系統(tǒng)采取密封措施、嚴防空氣侵入外,常在油缸兩腔最高處設置放氣閥,排出缸內殘留的空氣,使油缸穩(wěn)定的工作
排氣閥的結構形式包括整體式和組合式。在設計中選用的是整體式。
整體式排氣閥閥體與閥針合為一體,用螺紋與鋼筒或缸蓋連接,靠頭部錐面起密封作用。排氣時,擰松螺紋,缸內空氣從錐面間隙中擠出,并經(jīng)斜孔排出缸外。這種排氣閥簡單、方便、但螺紋與錐面密封處同心度要求較高,否則擰緊排氣閥后不能密封,會造成泄露。
(5)緩沖裝置
緩沖裝置的工作原理是使鋼筒低壓腔內油液(全部或部分)通過節(jié)流把動能轉換為熱能,熱能則由循環(huán)的油液帶到液壓缸外
緩沖裝置的結構有恒節(jié)流面積緩沖裝置和變節(jié)流型緩沖裝置。在設計中我采用的是恒節(jié)流面積緩沖裝置,此類緩沖裝置在緩沖過程中,由于其節(jié)流面積不變,故在緩沖開始時,產生的緩沖制動力很大,但很快就降低下來,最后不起什么作用,緩沖效果很差。但是在一般系列化的成品液壓缸中,由于事先無法知道活塞的實際運動速度以及運動部分的質量和載荷等,因此為了使結構簡單,便于設計,降低制造成本,仍多采用此種節(jié)流緩沖方式。
3.3.2 缸體結構的基本參數(shù)確定
1、主缸參數(shù)
(1)主缸的內徑
(注:所用公式都來源于文獻【10】【17】)
===0.226M (3-1)
按標準取整=0.220m
(2)主缸活塞桿直徑
===0.175m (3-2)
按標準取整=0.180m
(3)主缸實際壓力:
= (3-3)
(4)主缸實際回程力:
= (3-4)
2、頂出缸、卸料缸參數(shù)
(1)頂出缸、卸料缸的內徑
===0.0984m
按標準取整=0.1m
(2)頂出缸、卸料缸的活塞桿直徑
===0.0485m
按標準取整=0.05m
(3)頂出缸、卸料缸實際頂出力:
=
(4)頂出缸、卸料缸實際回程力:
=
3.3.3各缸動作時的流量
1、主缸進油流量與排油流量
(1)快速空行程時的活塞腔進油流量
= (3-5)
(2)快速空行程時的活塞腔的排油流量
== (3-6)
(3)工作行程時的活塞腔進油流量
==
(4)工作行程時的活塞腔的排油流量
==
(5)回程時的活塞桿腔進油流量
==
(6)回程時的活塞腔的排油流量
==
2、頂出缸、卸料缸的進油流量與排油流量
(1)頂出時的活塞腔進油流量
=
(2)頂出時的活塞桿的排油流量
==
(3)回程時的活塞桿腔進油流量
==
(4)回程時的活塞腔的排油流量
==
表3-1主缸鋼筒所選材料
型號
≥/MPa
≥/MPa
≥/%
45
610
360
14
3.3.4 液壓缸設計計算
1、主缸的設計計算
(1)筒壁厚計算
公式: =++ (3-7)
當~0.3時,用使用公式:
==0.042 m (3-8)
取 =0.050m
--為缸筒材料強度要求的最小,M --為鋼筒外徑公差余量,M
--為腐蝕余量,M --試驗壓力,16M時,取=1.25P
P—管內最大工作壓力為25 M --鋼筒材料的許用應力,M =/n
--鋼筒材料的抗拉強度,M n—安全系數(shù),通常取n=5
當時,材料使用不夠經(jīng)濟,應改用高屈服強度的材料.
(2)筒壁厚校核
額定工作壓力, 應該低于一個極限值,以保證其安全.
MPa=0.35=44MPa (3-9)
=外徑 D=內徑
同時額定工作壓力也應該完全塑性變形的發(fā)生:
=2.3320=98.3MPa (3-10)
--缸筒完全塑性的變形壓力, --材料屈服強度MPa
--鋼筒耐壓試驗壓力,MPa
=34.4~41.3 MPa (3-11)
(3)缸筒的暴裂壓力
=2.3610=187.4MPa (3-12)
(4)缸筒底部厚度
缸筒底部為平面時:
0.4330.433mm (3-13)
取 mm --筒底厚,MM
(5)核算缸底部分強度
按照平板公式即米海耶夫推薦的公式計算,缸底進油孔直徑為φ20cm則
Ψ===0.6875 (3-14)
= =69.8 MPa (3-15)
按這種方法計算[]=100MPa <[] 所以安全
(6)缸筒端部法蘭厚度:
==40.4mm (3-16)
取 h=45mm
--法蘭外圓半徑; --螺孔半徑; 螺釘 – M20
b—螺釘中心到倒角端的長度
=32cm = 42cm =48.5cm = =10cm h=10cm
= =37cm = = =47.25cm
圖3-2 部分工作缸
(7)校核法蘭部分強度:
==0.067cm (3-17)
(3-18)
其中P===110.2=11.02KN/cm (3-19)
==0.0335 (3-20)
=0.367 (3-21)
=1 (3-22)
==0.42 (3-23)
所以 =95.1MPa
(3-24)
=57.1+34.6=91.7 MPa<[] 滿足要求
依據(jù)上面公式當墊片的厚度為大于10cm時就能滿足要求,為了滿足橫梁的強度和工藝性,墊片厚度選用25cm。因此可以推算橫梁的厚度取大于25cm即滿足要求。
(8)缸筒法蘭連接螺釘:
表2.2 螺釘所選材料
型號
≥/MPa
≥/MPa
≥/%
35
540
320
17
(a)螺釘處的拉應力
=MPa==4.5MPa (3-25)
z-螺釘數(shù)8根; k-擰緊螺紋的系數(shù)變載荷 取k=4; -螺紋底徑, m
(b)螺紋處的剪應力:
=0.475MPa (3-26)
=MPa (3-27)
-屈服極限 -安全系數(shù); 5
(c)合成應力:
== MPa (3-28)
(9)墊片與橫梁間螺釘?shù)男:耍?
(a)螺釘處的拉應力
=MPa==3.8MPa (3-29)
z-螺釘數(shù)8根; k-擰緊螺紋的系數(shù)變載荷 取k=4; -螺紋底徑, m
(b)螺紋處的剪應力:
=0.475 MPa (3-30)
= MPa (3-31)
-屈服極限 -安全系數(shù); 5
(c)合成應力:
== MPa (3-32)
(9)活塞桿直徑d的校核
表2-3 活塞桿所選材料
型號
≥/MPa
≥/MPa
≥/%
45MnB
1030
835
9
(3-33)
d=0.05m滿足要求
F—活塞桿上的作用力
—活塞桿材料的許用應力,=/1.4
2、頂出缸、卸料缸的設計計算
表2.4鋼筒所選材料
型號
≥/MPa
≥/MPa
≥/%
45
610
360
14
(1)頂出缸、卸料缸管壁厚:
公式: =++
當~0.3時,用使用公式:
==0.0196m
取 =0.025m
--為缸筒材料強度要求的最小,M --為鋼筒外徑公差余量,M
--為腐蝕余量,M --試驗壓力,16M時,取=1.25P
P—管內最大工作壓力為25 M --鋼筒材料的許用應力,M =/n
--鋼筒材料的抗拉強度,M n—安全系數(shù),通常取n=5
當時,材料使用不夠經(jīng)濟,應改用高屈服強度的材料.
(2)頂出缸、卸料缸筒壁厚校核
額定工作壓力, 應該低于一個極限值,以保證其安全.
MPa=0.35=62.2MPa
=外徑 D=內徑
同時額定工作壓力也應該完全塑性變形的發(fā)生:
=2.3320=78.9 MPa
--缸筒完全塑性的變形壓力, --材料屈服強度MPa
--鋼筒耐壓試驗壓力,MPa
=27.62~33.14 MPa
(3)缸筒的暴裂壓力
=2.3610=150.4MPa
(4)缸筒底部厚度
缸筒底部為平面:
0.4330.433mm
取 mm
--筒底厚,MM
(5)核算缸底部分強度
按照平板公式即米海耶夫推薦的公式計算,缸底進油孔直徑為φ8cm,則
Ψ===0.68= =43.1MPa
按這種方法計算[]=100MPa <[] 所以安全
(6)缸筒端部法蘭厚度:h
==36.3mm
取 h=40mm
--法蘭外圓半徑; --螺孔直徑; 螺栓 – M12
b—螺栓中心到倒角端的長度
=12.5cm = 16cm =20.2cm = =3.5cm h=4cm = =14.25cm = = =20.1cm
(7)校核法蘭部分強度:
==0.182cm
其中 P===137.1=13.71KN/cm
==0.364
=0.175
=1.493
==0.48
所以 =53.9 MPa
=264+39.2=303.2 MPa<[] 滿足要求
(8)缸筒法蘭連接螺釘:
表2.5 螺釘所選材料
型號
≥/MPa
≥/MPa
≥/%
35
540
320
17
(a)螺栓處的拉應力
=MPa==2.9MPa
z-螺栓數(shù)8根; k-擰緊螺紋的系數(shù)變載荷 取k=4; -螺紋底徑, m
(b)螺紋處的剪應力:
=0.475MPa
=MPa
-屈服極限 -安全系數(shù); 5
(c)合成應力:
== MPa
(9)墊片與橫梁間螺栓的校核
(a)螺栓處的拉應力
=MPa==2.9 MPa
z-螺栓數(shù)8根; k-擰緊螺紋的系數(shù)變載荷 取k=4; -螺紋底徑, m
(b)螺紋處的剪應力:
=0.475MPa
=MPa
-屈服極限 -安全系數(shù); 5
(c)合成應力:
== MPa
(10)活塞桿直徑d的校核:
表2.6 活塞桿所選材料
型號
≥/MPa
≥/MPa
≥/%
45MnB
1030
835
9
d=0.018m 滿足要求
F—活塞桿上的作用力
—活塞桿材料的許用應力,=/1.4
3.4選擇液壓元件
3.4.1 選擇液壓泵和確定電動機功率
① 液壓泵的最高工作壓力就是液壓缸慢速下壓行程終了時的最大工作壓力
pp = = = 24.6 MPa
因為行程終了時流量q=0,管路和閥均不產生壓力損失;而此時液壓缸排油腔的背壓已與運動部件的自重相平衡,所以背壓的影響也可不計。
② 液壓泵的最大流量
qp≥K(∑q)max
泄漏系數(shù)K = 1.1~1.3,此處取K = 1.1。由工況圖(圖1.3)知快速下降行程中q為最大(q =64.8L/min),但此時已采用充液筒充液方法來補充流量,所以不按此數(shù)值計算,而按工作行程時的流量計算。
qmax = q3 =41.23L/min
qp=1.1q3 = 1.1×41.23=45.35L/min
③ 根據(jù)已算出的qP和pP,選軸向杜塞泵型號規(guī)格為63CCY14-1B,其額定壓力為28MPa,滿足25~60%壓力儲備的要求。排量為63m L/r,電動機同步轉速為1500 r/min,故額定流量為:q = qn = = 94.5 L/min,額定流量比計算出的qP大,能滿足流量要求,此泵的容積效率ηv = 0.92。
④ 電動機功率 驅動泵的電動機的功率可以由工作循環(huán)中的最大功率來確定;由工況分析知,最大功率為5.76 kW,取泵的總效率為η泵 = 0.85。
則P ===6.78kW
選用功率為7.5 kW,額定轉速為1440 r/min的電動機。電動機型號為:Y132m-4(Y系列三相異步電動機)。
3.4.2 選擇液壓控制閥
閥2、4、6、7通過的最大流量均等于qP,而閥1的允許通過流量為q
q = q1–qP=289.4–65.9=223.5 L/min
閥3的允許通過流量為q = q1 = 289.4 = 67.9 L/min
閥8是安全閥,其通過流量也等于qP。
以上各閥的工作壓力均取p=32 MPa。
本系統(tǒng)所選用的液壓元件見表4-2。
表4-2 壓塊機液壓元件型號規(guī)格明細表
序號
元件名稱
型 號
規(guī) 格
1
液控單向閥
SV30P-30B
華德:31.5MPa,30通徑,流量400L/min
2
單向順序閥
(平衡閥)
DZ10DP1-40BY
華德:10通徑,流量80L/min,
控制壓力(25~210)×105Pa
3
液控單向閥
SV20P-30B
華德:31.5MPa,20通徑,流量400L/min
4
電液換向閥
WEH25H20B106AET
華德:28MPa,25通徑,流量1100L/min
5
電磁換向閥
3WE4A10B
華德:21MPa,4通徑,流量25L/min
6
電液換向閥
WEH25G20B106AET
華德:28MPa,25通徑,流量1100L/min
7
順序閥
DZ10DP140B210M
華德:10通徑,流量80L/min,
控制壓力(25~210)×105Pa
8
溢流閥
(安全閥)
DBDH20P10B
華德:20通徑,流量250L/min,
調壓范圍(2.5~40)MPa
9
軸向柱塞泵
63CCY14-1B
32MPa,排量63mL/r,1500r/min
10
主液壓缸
自行設計
11
頂出液壓缸
自行設計
12
壓力表
Y-100
(0~400)×105Pa
13
壓力表開關
KF-L8/20E
3.4.3選擇輔助元件
(1)確定油箱容量
由資料,中高壓系統(tǒng)(p>6.3 MPa)油箱容量V =(6~12)qP。
本例取V = 8×qP = 8×94.5 = 756 L(qP用液壓泵的額定流量).
取油箱容量為800 L。
充油筒容量V1 =(2–3)Vg = 3×25 = 75(L)
式中 Vg——主液壓缸的最大工作容積。
在本例中,Vg = A1Smax = 804×31 = 24924cm3 ≈ 25(L)
(2)油管的計算和選擇
如參考元件接口尺寸,可選油管內徑d = 20mm。
計算法確定:液壓泵至液壓缸上腔和下腔的油管
d = 取v = 4m/s,q = 65.9 L/min
d = = 1.87 cm,選d = 20 mm.
與參考元件接口尺寸所選的規(guī)格相同。
充液筒至液壓缸的油管應稍加大,可參考閥1的接口尺寸確定
選d = 32 mm的油管,油管壁厚:δ≥。
選用鋼管:[σ] = ≈ 83.25MPa,取n = 4, σb = 333MPa(10#鋼)。
σ = = = 3.84 mm,取σ = 4 mm
第4章 機體設計
4.1 立柱設計
4.1.1立柱設計計算
先按照中心載荷進行初步核算,許用應力[]不應大于55,并參照同類型壓塊機的立柱,初步定出立柱直徑。
按標準選取立柱螺紋。
立柱螺紋區(qū)到光滑區(qū)過渡圓角應盡可能取大些,最好在30~50mm之間。
原設計主要參數(shù)為:
F=1000KN
H=900mm
B=360mm(寬邊立柱中心距)
d=30cm(立柱光滑部分直徑)
e=10cm(允許偏心距)
n=4(立柱的根數(shù))
立柱材料為45#鋼,中頻淬火≥620MPa,≥375MPa
中心載荷時的應力:
===22.2
偏心載荷靜載荷合成應力 由于小型壓塊機,可將立柱考慮為插入端的懸臂梁,m=0.25
=+=+=22.2+74.1=96.3
<150,因此是安全的。
對于截面的45#鋼,≥375MPa,尺寸系數(shù)已考慮在內,立柱表面為精車,對于正火的45#鋼,表面質量系數(shù)為0.9,因此[]可取為300MPa.過渡圓角半徑為30mm.
疲勞強度校核:
==0.1
==0.107
從文獻【10】中查出=1.58
K=1=0.70(1.58-1)=1.41
=K=1.41×96.3=104.4<300
[]為200MPa, 因此是安全的。
立柱是四柱壓塊機重要的支承件和受力件,同時又是活動橫梁的導向基準。因此,立柱應有足夠的強度與剛度,導向表面應有足夠的精度,光潔度和必要的硬度。
4.1.2連結形式
立柱式機架是常見的機架形式,一般由4根立柱通過螺母將上、下橫梁緊固地連結在一起,組成一個剛性的空間框架。在這個框架中,既安裝了壓塊機本體的主要零部件,又在壓塊機工作時,承受壓塊機的全部工作載荷,并作為壓塊機運動部分的導向。整個機架的剛度與精度,在很大程度上取決于立柱與上、下橫梁的連接形式與連接的緊固程度。
圖4-1中、小型壓塊機立柱連結形式
在中、小型壓塊機中,常用的連結形式有以下4種:
(1)立柱用臺肩分別支承上、下橫梁,然后用外鎖緊螺母上、下予以鎖緊。這種結構中,上橫梁下表面(工作臺)上表面間的距離與平行度,全靠4根立柱臺肩間尺寸的一致性來保證,因此裝配簡單,不需調整,裝配后機架的精度也無法調整,且對立柱臺肩間尺寸精度的加工要求很高。因此,這種結構僅在無精度要求的小型簡易壓塊機中采用。
(2)內外螺母式,即在立柱上分別用內、外兩個螺母來固定上、下橫梁,用內螺母來起上述臺肩的支承作用,用外鎖緊螺母上、下予以鎖緊。上橫梁下表面的水平度以及下橫梁(工作臺)上表面的水平度,兩個表面之間的平行度與間距的保持,全靠安裝時內螺母的調整,因此,對立柱的有關軸向尺寸要求不高,但對立柱螺紋精度(與立柱軸線的平行度)及內螺母精度(內螺母的螺紋對于上、下橫梁貼合面的垂直度)要求較高,安裝時調整比較麻煩。
(3)在與上橫梁連結處用臺肩代替內螺母,精度調節(jié)和加工均不很復雜,但立柱預緊不如第2種方便。
(4)與第3種形式基本相同,只是在下橫梁處用臺肩代替內螺母,但精度調節(jié)比第3種簡便可靠。
在設計中選用的是第四種連結方式。
圖4-2 組合式立柱螺母
4.1.3立柱的螺母及預緊
立柱螺母一般為圓柱形,小壓塊機的立柱螺母是整體的,立柱直徑在150mm以上時,做成組合式,由兩個半螺栓緊固而成,材料用35~45鍛鋼或鑄鋼。因為在設計中我選用的立柱為300mm,所以采用此種結構。
立柱螺母的尺寸已有機械行業(yè)標準JB/T 2001.73——1999,螺母外徑約為螺紋直徑的1.5倍,內螺母一般與螺母等高,約為螺紋直徑的0.9倍。
25MN以下的壓塊機,其立柱多做成實心的,實心的立柱的兩端要鉆出預緊螺母用的加熱孔。
立柱的預緊分加熱預緊與液壓預緊。本次設計選用的是加熱預緊方式。
加熱預緊 比較常用的方法,為此,立柱端部應鉆有加熱孔,其深度應大于橫梁的高度。在立柱及上橫梁安裝好后,先將內、外螺母冷態(tài)擰緊,然后用電熱棒或通入蒸汽等加熱方法使立柱端部伸長,達到一定溫度后,將外螺母再向下擰過一個角度,一般是用螺母外徑上一點轉過的弧長來度量。立柱冷卻后,就在螺母與橫梁之間產生一個很大的預緊力,使螺母不易松動。加熱時應注意兩對角立柱同時加熱。
4.1.4 立柱的導向裝置
活動橫梁運動及工作時,一般以立柱為導向,由于活動橫梁往復運動頻繁,且在偏心加壓時有很大的側推力,因此,不可能讓活動橫梁與立柱直接接觸,互相磨損,必須選擇耐磨損、易更換的材料作為兩者之間的導向裝置。導向裝置的質量直接關系到活動橫梁的運動精度及被加工件的尺寸精度,也會影響到工作缸密封件與導向面的磨損情況,對模具壽命及機身的受力情況也均有影響,為此,必須合理選擇導向裝置的結構及配合要求。
圖4-3 導套
導向裝置可分為導套與平面導板兩大類。
(1)導套
對于圓截面的立柱,都是在活動橫梁的立柱孔中采用導套結構,又可分為圓柱面導套和球面導套。
(2)圓柱面導套
在活動橫梁的立柱孔中,各裝有上、下兩個導套,它們由兩半組成,為了拆裝方便,兩半導套的剖分面最好有的斜度,導套兩端裝有防塵用的氈墊。這種導套結構簡單,制造方便。
本次設計中采用這種形式的導套。
導套的材料計算
導套材料一般采用鑄錫青銅ZQSn6-6-3,小壓塊機也有用鐵基粉末冶金的。
導套比壓q的計算
=1.33 MPa 滿足要求
式中 T——機架計算中求得立柱上的側推力(N)
d——導套內孔直徑 (m)
c——導套高度(m)
[q]——許用比壓 (MPa),對于ZQSn6-6-3,[q]=6~8 MPa
4.1.5 限程套
為防止運動部分超程,有些壓塊機在下橫梁的4個立柱上安裝限程套,一般為對開式,上、下兩端應平行,4個限程套高度應一致,內孔比立柱直徑大1-2mm,用鑄鐵制造。
圖4-4 立柱安裝限程套
4.2 底座設計
底座安裝于工作臺下部,與基礎相連。底座僅承受機器之總重量。
底座材料可選用鑄鐵件或焊接結構。主要考慮到外形的美觀,對精度無要求。
4.3 橫梁設計
4.3.1 上橫梁結構設計
橫梁由鑄造制成,目前以鑄造為多,一般采用ZG35B鑄鋼。 橫梁的寬邊尺寸由立柱的寬邊中心距確定,上梁和活動梁的窄邊尺寸應盡可能小些,以便鍛造天車的吊鉤容易接近壓塊機中心,梁的中間高度則由強度確定。
設計上橫梁時,為了減輕重量,根據(jù)“ 等強度梁”的概念,設計成圖所示的不等高梁,即立柱柱套處的高度h 小于中間截面的高度H。但在過渡區(qū)( A處) 會有應力集中。
由于上橫梁外形尺寸很大,為了節(jié)約金屬和減輕重量,盡量使各個尺寸在允許的范圍內降到最小。梁體做成箱形結構,在安裝缸的地方做成圓筒形,安裝立柱的地方做成方筒形,中間加設筋板,以提高剛度,降低局部應力。
圖4-5梁的不等高結構
4.3.2活動橫梁結構設計
(1)活動橫梁的主要作用
與工作缸柱塞桿連接傳遞壓塊機的壓力,通過導向套沿立柱導向面上下往復運動;安裝固定模具及工具等。因此需要有較好的強度、剛度及導向結構?;顒訖M梁上部與工作缸柱塞相連,下部與上模座相連,梁體結構和受力狀態(tài)都很復雜。當壓塊機工作時,高壓液體作用于柱塞的力是通過活動橫梁及上砧傳遞到鍛件上而做功,活動橫梁的上下運動則依靠梁與立柱的導向裝置。
(2)活塞桿與橫梁的連接
剛性連接 柱塞下端插入活動橫梁內。此種連接方式在偏心載時,柱塞跟隨活動橫梁一起傾斜,將動梁所受偏心力矩的一部分傳給工缸導向套,使導向套承受側向水平推力或一對力偶,從而加劇導向套及封的磨損。單缸壓塊機或三缸壓塊機的中間工作缸多采取此種結構。
在活塞桿焊接法蘭用螺釘與橫梁連接,用12根M30的螺釘,達到預緊的目的。
4.3.3 下橫梁結構設計
下橫梁的剛度要求應略嚴一些,以保證整個壓機的剛性。下橫梁直接與立柱、拉桿、工作臺、回程缸和頂出器相連,梁體結構和受力狀態(tài)都很復雜。對于下橫梁,其設計原則與上橫梁相同,是在滿足相連部件最小幾何尺寸要求和工藝要求的條件下,盡可能縮減其縱向、橫向尺寸,這是有效提高梁的剛度、強度和減輕梁的重量應首先把握的主要原則。
4.3.4 各橫梁參數(shù)的確定
因為液壓缸與橫梁間的墊片厚度為25cm,因此可以推算橫梁的厚度取大于25cm即滿足要求??紤]在墊片與橫梁的連接面積比墊片與液壓缸的連接面積少一半所以上橫的受力部分厚度選用50cm,因為有空心部分,所以整體厚度選用75cm?;顒訖M梁受力部分為35cm,整體厚度選用50cm。因為頂出缸、卸料缸的公稱壓力小,但受力打,所以整體厚度選用40cm。
4.4壓模及壓板的設計
本次設計的金屬壓塊機采用上下模的形式,下部分為壓模,上部分為壓塊。
壓模即是一規(guī)則的空腔箱體,用于盛放待壓塊的金屬廢料,以及在壓緊過程中限制金屬塊形狀。其置于壓塊機平臺上,由灰鐵HT250鑄造而成,根據(jù)不同需要壓模大小可選用不同尺寸,本次選擇壓模尺寸為:長×寬×高=640mm×500mm×400mm。
壓板是配合壓模使用的,用于壓實金屬廢料,其與壓塊機上部移動橫梁相連,也是由灰鐵HT250鑄造而成,其根據(jù)不同壓模大小可選擇匹配的尺寸,本次選擇的壓板尺寸為:長×寬×高=540mm×300mm×100mm。
第5章 傳送裝置設計
5.1電動機的選擇
5.1.1 電動機容量的選擇
電動機所需的功率為:
由電動機到運輸帶的傳動總功率為:
—聯(lián)軸器的傳動效率:0.9925
—軸承的傳動效率: 0.9875
則:
本次選定出輸送功率為
5.1.2 確定電動機轉速
初定圓筒直徑:d=45mm
設計數(shù)據(jù)給出傳送速度:v=0.05m/s
微型精密減速箱減速比:1:30
表5.1 電機軸和滾筒軸轉速
V
0.05
(軸)
22.99
(電機)
229.86
根據(jù)上述所求,取用電動機A02-5622[18]。
5.2輸送帶主動軸設計
5.2.1軸的計算
將傳動裝置各軸由高速到低速依次定為聯(lián)軸器和軸承,電機軸,滾筒軸(以0.05m/s速度為例