萬向節(jié)滑動叉的加工工藝規(guī)程及工裝夾具設(shè)計【優(yōu)秀含SW三維16張CAD圖紙+銑φ39mm二孔端面+鉆擴花鍵底孔Φ43mm及锪沉頭孔Φ55mm夾具帶過程工序卡片】-jjsj29
萬向節(jié)滑動叉的加工工藝規(guī)程及銑φ39mm二孔端面+鉆擴花鍵底孔Φ43mm及锪沉頭孔Φ55mm工裝夾具設(shè)計【含SW三維16張CAD圖紙】
摘 要
萬向節(jié)滑動叉主要用于在兩個不同的心軸或有一定夾角的軸間傳遞動力,使用萬向節(jié)滑動叉可以簡化萬向傳動裝置的結(jié)構(gòu),因此對于萬向節(jié)滑動叉的研究具有深遠的意義。
本次設(shè)計的主要內(nèi)容就是制訂萬向節(jié)滑動叉的相關(guān)工藝規(guī)程,并設(shè)計其中的兩套專用夾具,運用三維軟件建立實體圖并導(dǎo)出裝配動畫和爆炸圖,導(dǎo)出二維圖并應(yīng)用CAD修改。設(shè)計內(nèi)容需要運用各方面的機械專業(yè)知識,是對我們學(xué)習(xí)成果的全面考察也是對專業(yè)軟件應(yīng)用熟練程度的一次考驗。
總的來說本次設(shè)計是對四年專業(yè)知識學(xué)習(xí)的總結(jié)與提高,是一種知識層次的升華。
關(guān)鍵詞:萬向節(jié)滑動叉;工藝分析;專用夾具
Abstract
Universal joint sliding fork is located in the top of the transmission shaft. The main use of it is transferring power between the two different heart shaft or the shaft that is having certain angle. The use of universal joint sliding fork may simplify the structure of universal transmission device, so it is important to make a research of it.
The main purpose of research is improving the processing efficiency by making some process procedures. Due to the complexity of its structure, it needs the assistant of special jig during the processing process. So we need to design two special jigs that is used during the processing process. In the process of designing, we need to use some professional drawing software, such as Solidworks or CAD. So the graduation design is not only the test for our professional knowledge, but also the investigation for our use of some software. Through the professional knowledge work out relevant process planning and design related fixture. Then we need to draw the fixture assembly drawings and explosion figure and using CAD modify 2d figure.
Generally, the graduation design is an actual combat maneuvers for our abilities. It is important for us about the development of our future.
Key words: gimbal sliding fork;process analysis;special fixture
目錄
第一章 緒論 1
1.1研究背景 1
1.2 國內(nèi)外研究現(xiàn)狀與發(fā)展 1
1.3 汽車零部件企業(yè)存在的問題 2
1.4 研究目的和意義 2
1.5本課題的主要研究內(nèi)容 2
第二章 零件的分析 4
2.1 零件的作用 4
2.2 零件的材料 4
2.3 零件的工藝分析 5
2.3.1 結(jié)構(gòu)分析 5
2.3.2加工表面技術(shù)要求分析 5
第三章 工藝規(guī)程設(shè)計 7
3.1策劃零件工藝規(guī)程的規(guī)定以及技術(shù)指導(dǎo) 7
3.1.1工藝要求 7
3.1.2技術(shù)依據(jù) 7
3.2生產(chǎn)類型的確定 7
3.3確定毛坯的制造形式 7
3.4制定工藝路線及其方法 8
3.4.1加工方法的選擇 8
3.4.2基準的選擇 8
3.4.2.1粗基準的選擇 9
3.4.2.2精基準的選擇 9
3.4.3制定工藝路線 9
3.4.3.1工藝路線一 9
3.4.3.2工藝路線二 10
3.4.3.3 工藝路線方案三 10
3.4.3.4分析和比較工藝方案 11
3.5 機械加工余量,工藝尺寸及毛坯尺寸的確定 18
3.6確定切削用量和基本工時 20
3.6.1加工條件 20
3.6.2計算切削用量 20
第四章 夾具設(shè)計 32
4.1 夾具設(shè)計的基本要求 32
4.2專用機床夾具的組成 32
4.3 專用夾具的設(shè)計方法和步驟 32
4.4 專用夾具設(shè)計方案 33
4.5 銑床專用夾具設(shè)計 34
4.5.1 定位方案 34
4.5.2定位基準的選擇 35
4.5.3定位誤差分析 35
4.5.4 切削力及夾緊力計算 36
4.5.5銑床夾具設(shè)計總結(jié) 37
總 結(jié) 38
致 謝 39
參考文獻 40
【詳情如下】【需要咨詢購買全套設(shè)計請加QQ1459919609】.bat
cjjzpt.stp
swljt.stp
v型塊-鉆擴花鍵底孔43mm及锪沉頭55mm車非標夾具零件.dwg
xjjzpt.stp
萬向節(jié)滑動叉的加工工藝規(guī)程及工裝夾具設(shè)計【銑φ39mm二孔端面+鉆擴花鍵底孔Φ43mm及锪沉頭孔Φ55mm】.doc
萬向節(jié)滑動叉的工藝規(guī)程及工裝設(shè)計中期檢查.doc
萬向節(jié)滑動叉的工藝規(guī)程及工裝設(shè)計任務(wù)書.doc
萬向節(jié)滑動叉的工藝規(guī)程及工裝設(shè)計開題報告.doc
萬向節(jié)滑動叉零件圖.dwg
三維.SLDPRT
壓板-鉆擴花鍵底孔43mm及锪沉頭55mm車非標夾具零件.dwg
壓板-銑φ39mm二孔端面非標夾具零件.dwg
壓緊螺栓-鉆擴花鍵底孔43mm及锪沉頭55mm車非標夾具零件.dwg
外文翻譯
外文翻譯.zip
定位心軸-鉆擴花鍵底孔43mm及锪沉頭55mm車非標夾具零件.dwg
定位心軸-銑φ39mm二孔端面非標夾具零件.dwg
工序15.dwg
工序20.dwg
工序25.dwg
工序30.dwg
工序35.dwg
工序40.dwg
工序45.dwg
工序50.dwg
工序55.dwg
工序60.dwg
工序65.dwg
工序70.dwg
工藝卡1.dwg
工藝卡2.dwg
底座-鉆擴花鍵底孔43mm及锪沉頭55mm車非標夾具零件.dwg
支柱-鉆擴花鍵底孔43mm及锪沉頭55mm車非標夾具零件.dwg
支柱-銑φ39mm二孔端面非標夾具零件.dwg
毛坯圖.dwg
立柱-銑φ39mm二孔端面非標夾具零件.dwg
車床夾具CAD副本可以刪
車床夾具CAD副本可以刪.zip
車床夾具SW三維
車床夾具SW三維.zip
過程卡.doc
鉆擴花鍵底孔43mm及锪沉頭55mm車夾具體.dwg
鉆擴花鍵底孔43mm及锪沉頭55mm車夾具裝配圖.dwg
銑φ39mm二孔端面夾具體底座.dwg
銑φ39mm二孔端面夾具裝配圖.dwg
銑床夾具SW三維.zip
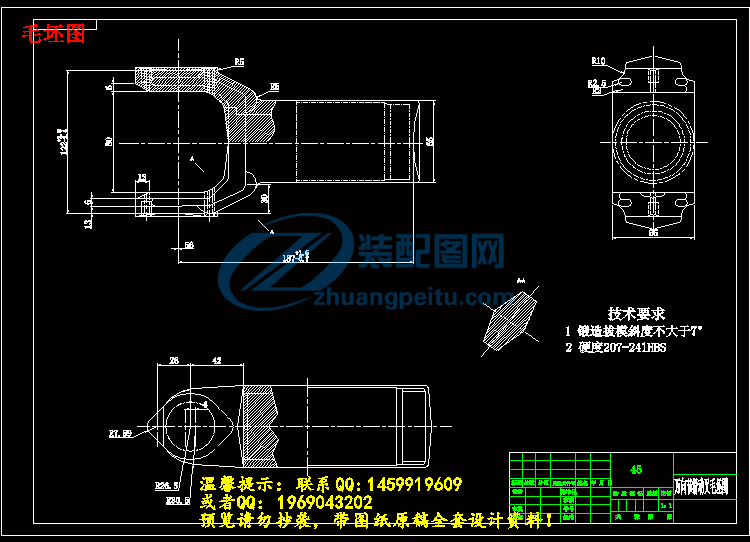

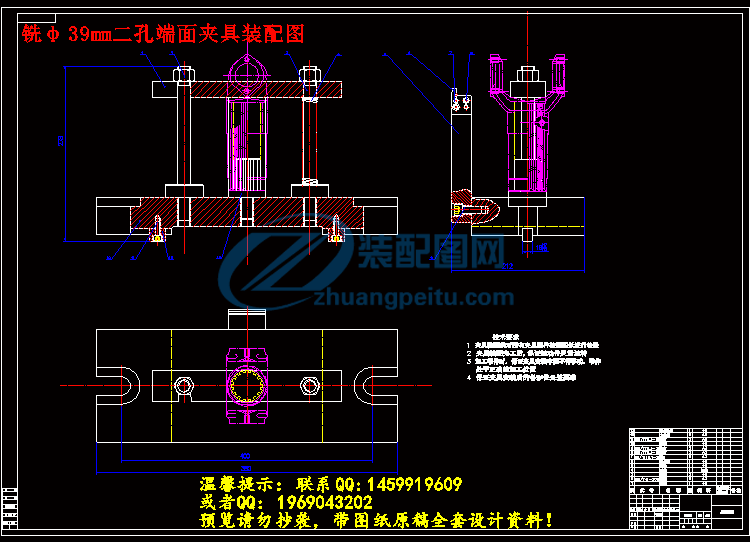
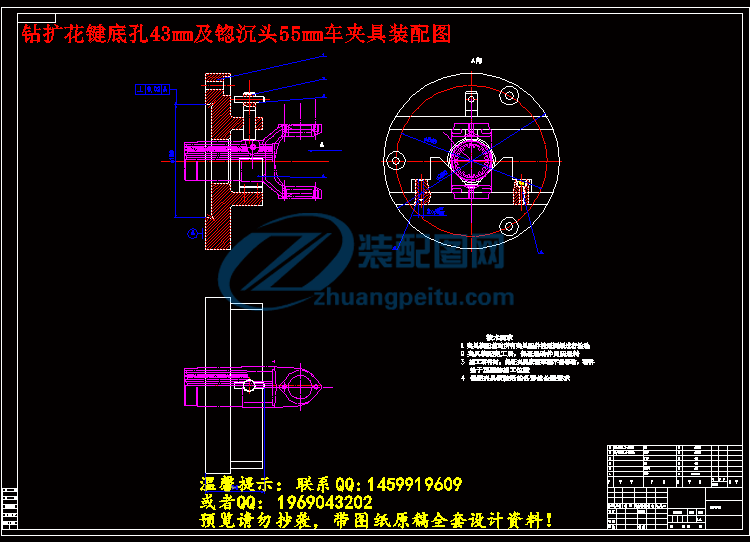

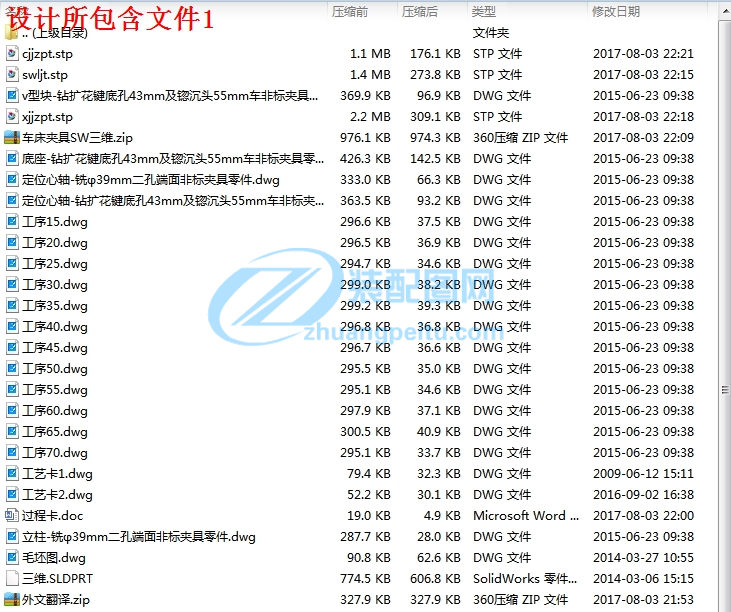
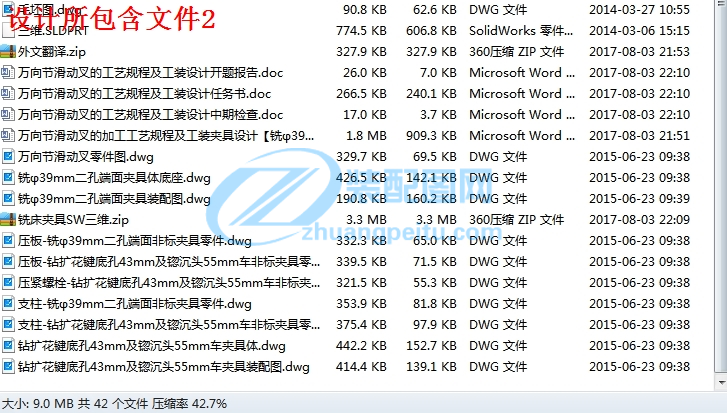
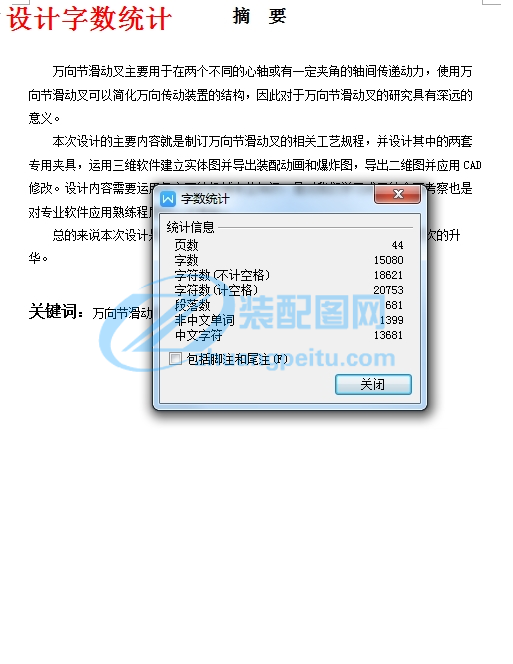
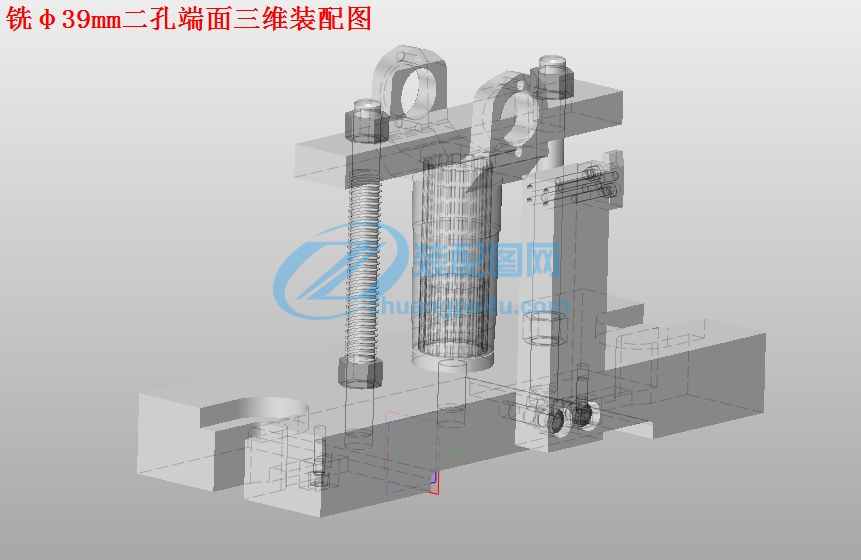

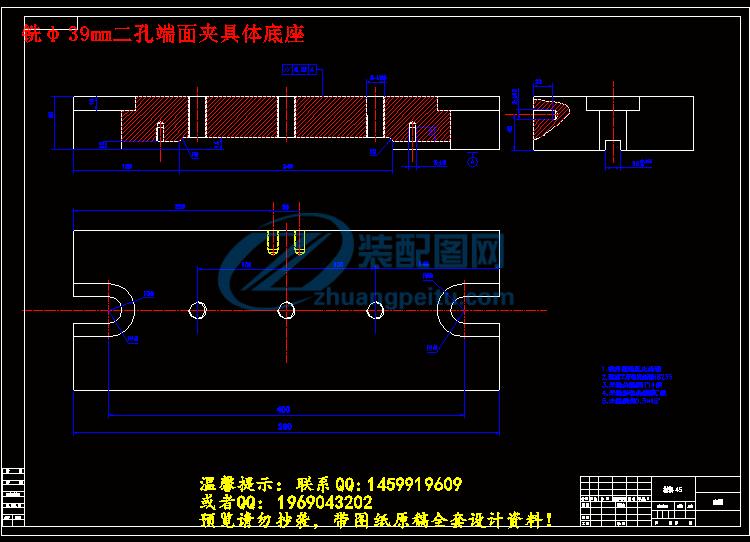
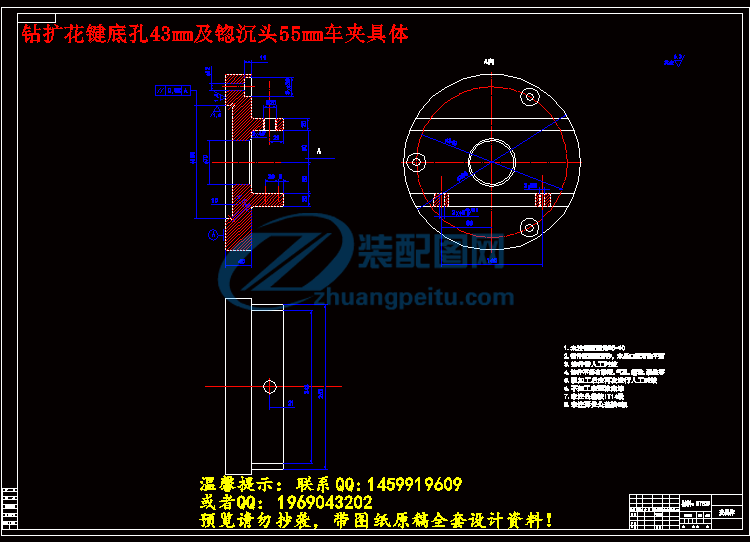
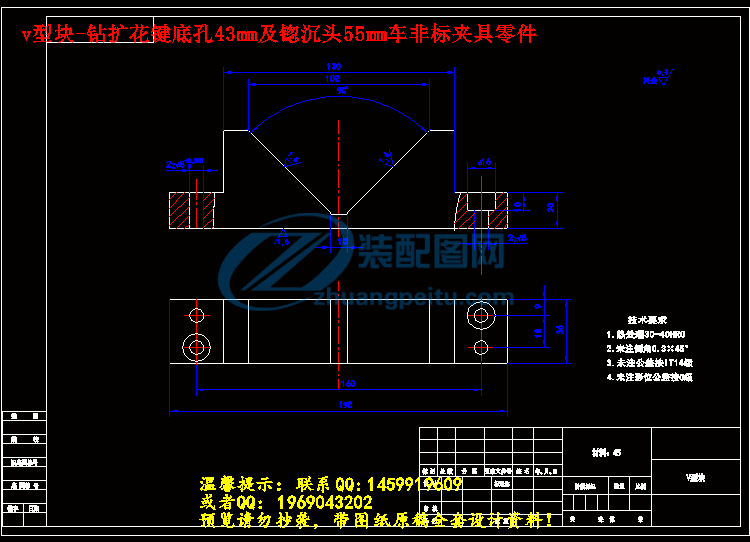

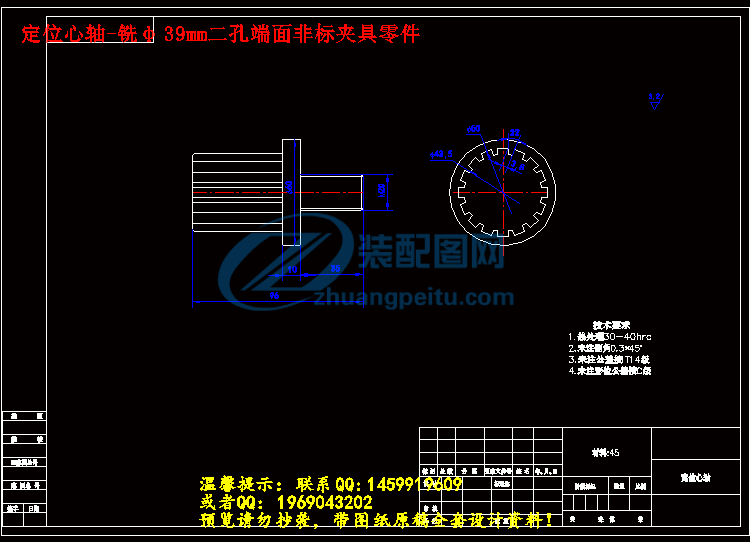
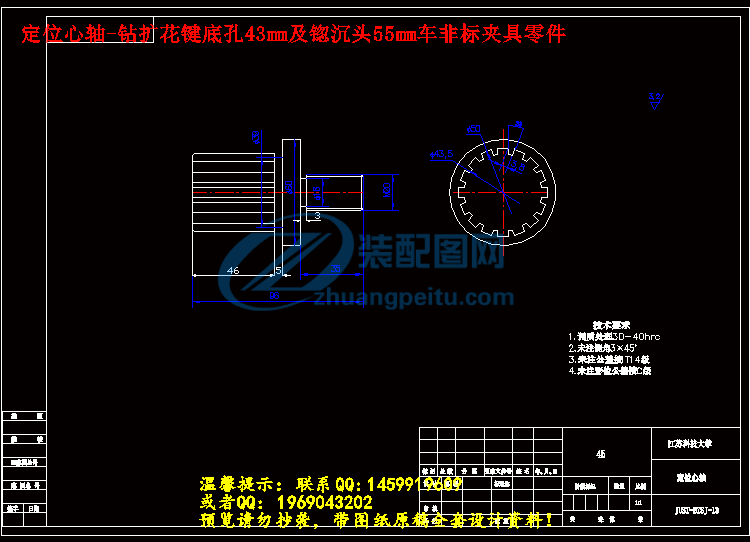
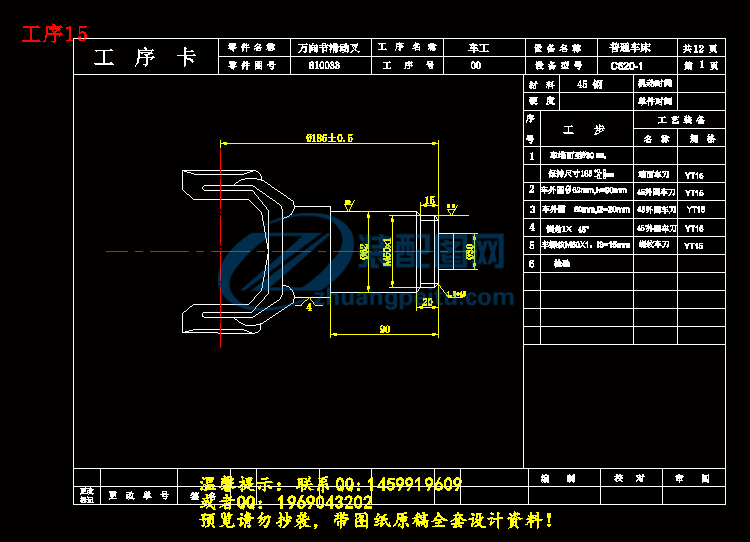
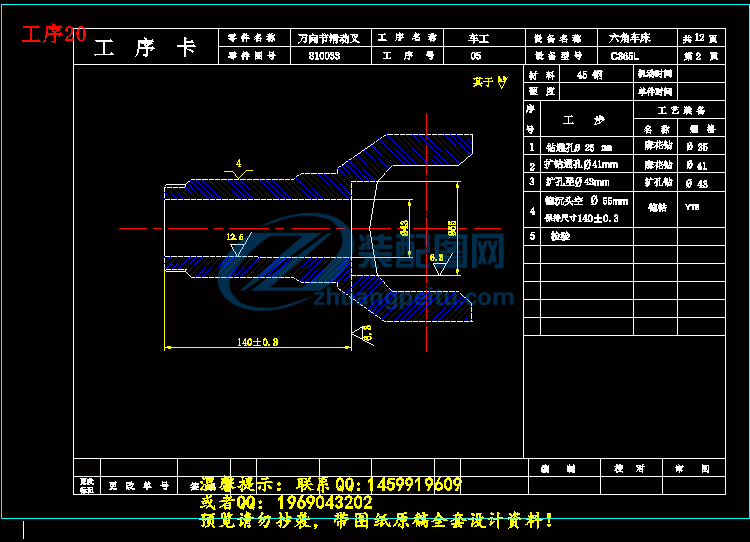

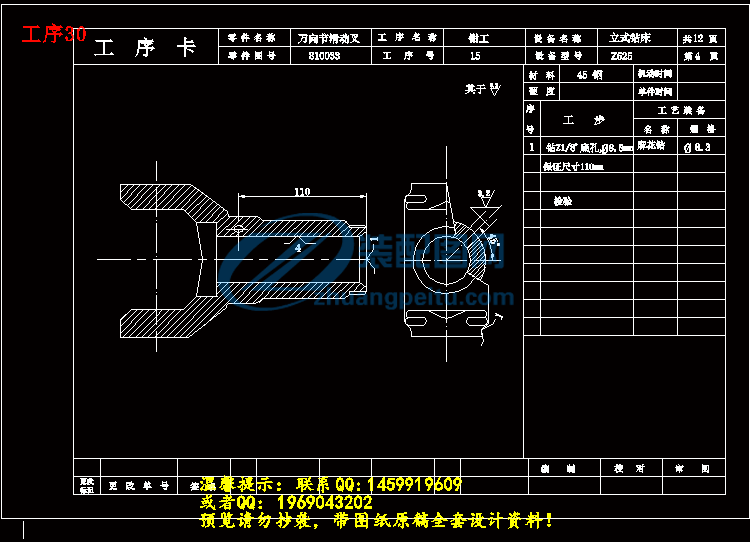

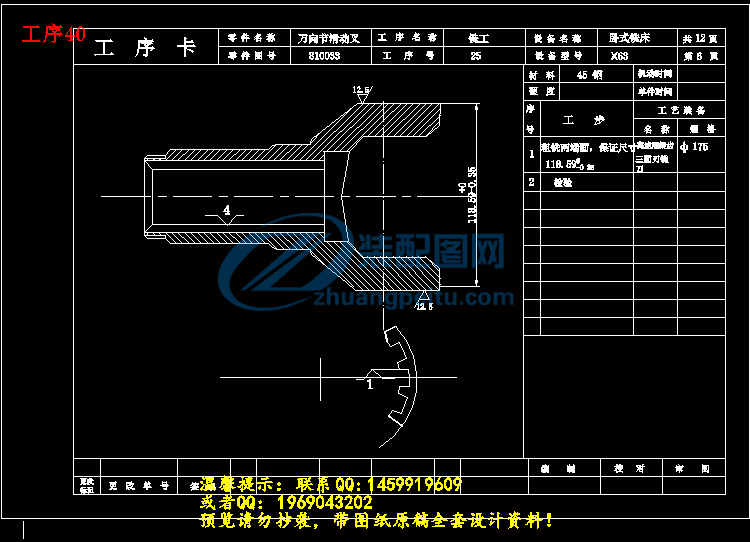

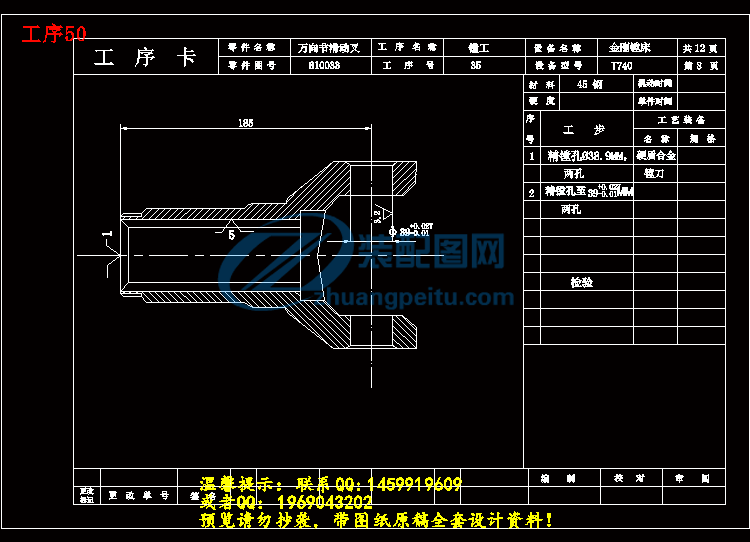
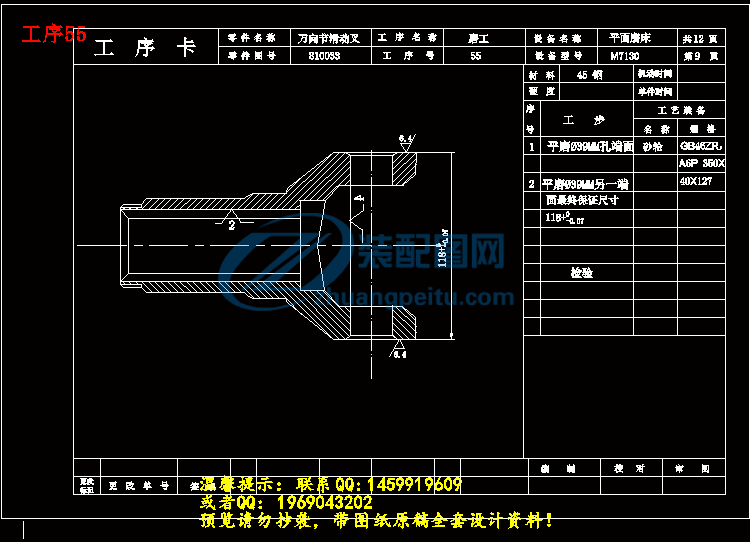
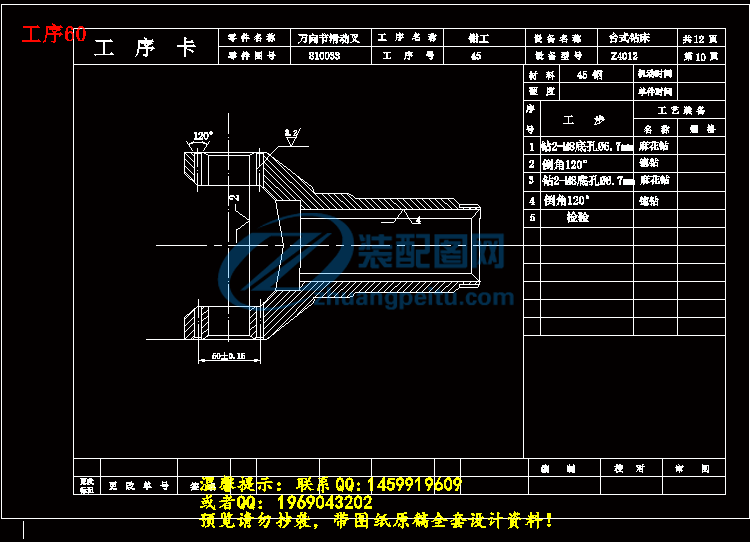
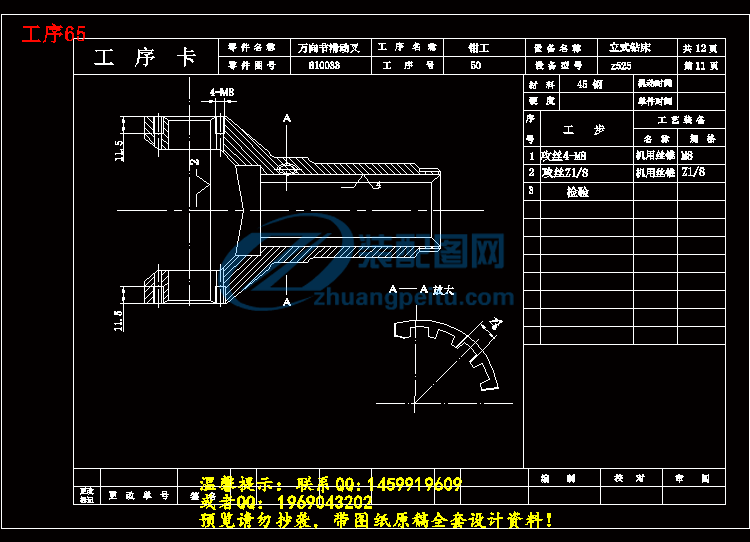
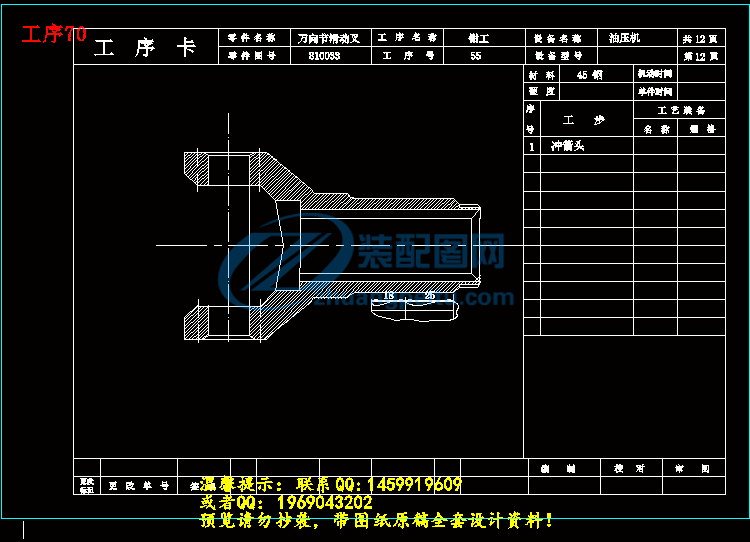
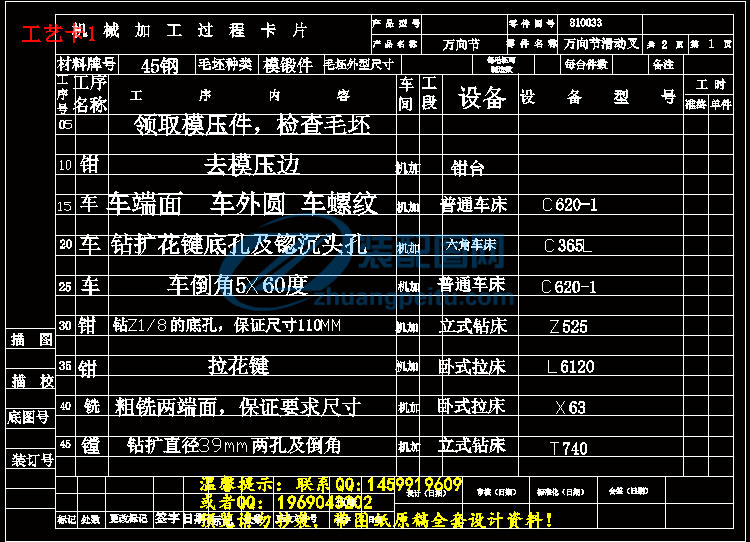

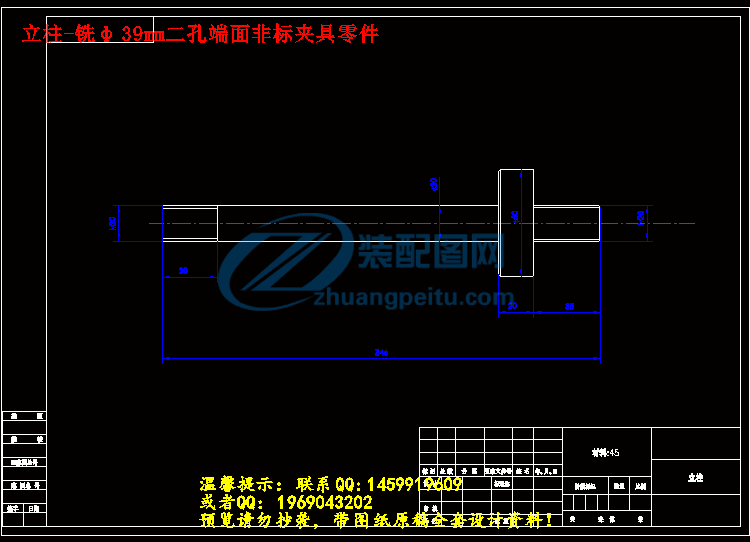
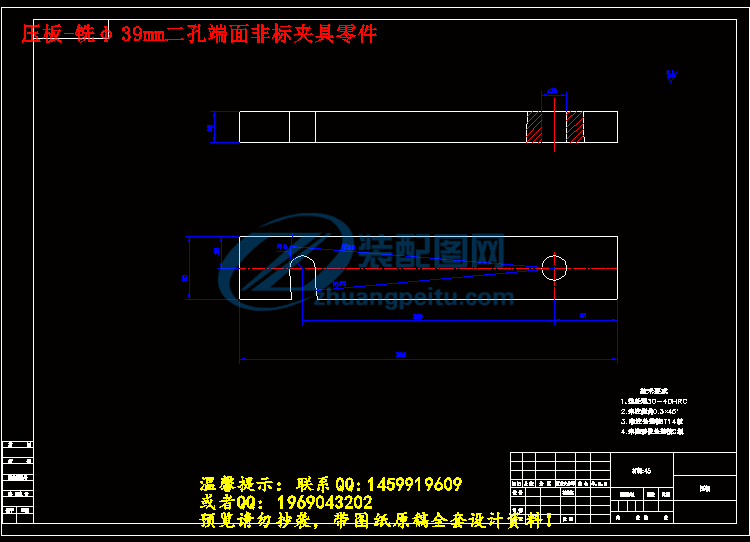



I 摘 要 萬向節(jié)滑動叉主要 用于 在兩個不同的心軸或有一定夾角的軸間傳遞動力, 使用 萬向節(jié) 滑動 叉可以簡化萬向傳動裝置的結(jié)構(gòu),因此對于萬向節(jié) 滑動 叉的研究具有深遠的意義。 本次設(shè)計 的主要 內(nèi)容就是制訂萬向節(jié)滑動叉的相關(guān)工藝規(guī)程,并設(shè)計其中的兩套專用夾具,運用三維軟件建立實體圖并導(dǎo)出裝配動畫和爆炸圖,導(dǎo)出二維圖并應(yīng)用 計內(nèi)容需要運用各方面的機械專業(yè)知識 ,是對我們 學(xué)習(xí)成果 的全面考察也是對專業(yè)軟件應(yīng)用熟練程度的一次考驗 。 總的來說本次設(shè)計是對四年專業(yè)知識學(xué)習(xí)的總結(jié)與提高,是一種知識層次的升華。 關(guān)鍵詞: 萬 向節(jié)滑動叉;工藝分析;專用夾具 is in of of it is or is of of so it is to a of of is by to of it of So we to is In of we to So is of we to AD d is an It is us of 錄 第一章 緒論 ................................................................................................................... 1 究背景 ............................................................................................................ 1 內(nèi)外研究現(xiàn)狀與發(fā)展 ........................................................................................ 1 車零部件企業(yè)存在的問題 ................................................................................. 2 究目的和意義 .................................................................................................. 2 ....................................................................................... 2 第二章 零件的分析 ........................................................................................................ 4 件的作用 ....................................................................................................... 4 件的材料 ....................................................................................................... 4 件的工藝分析 ................................................................................................ 5 構(gòu)分析 ................................................................................................ 5 ............................................................................. 5 第三章 工藝規(guī)程設(shè)計 ..................................................................................................... 7 ................................................................ 7 ................................................................................................. 7 ................................................................................................. 7 ................................................................................................. 7 .......................................................................................... 7 ....................................................................................... 8 ....................................................................................... 8 .............................................................................................. 8 ................................................................................. 9 ................................................................................. 9 .......................................................................................... 9 .................................................................................... 9 .................................................................................. 10 藝路線方案三 ........................................................................... 10 ..................................................................... 11 械加工余量,工藝尺寸及毛坯尺寸的確定 ....................................................... 18 .................................................................................. 20 ............................................................................................... 20 ........................................................................................ 20 第四章 夾具設(shè)計 .......................................................................................................... 32 具設(shè)計的基本要求 ........................................................................................ 32 ........................................................................................ 32 用夾具的設(shè)計方法和步驟 .............................................................................. 32 用夾具設(shè)計方案 ........................................................................................... 33 床專用夾具設(shè)計 ........................................................................................... 34 位方案 .............................................................................................. 34 ..................................................................................... 35 ........................................................................................ 35 削力及夾緊力計算 .............................................................................. 36 .................................................................................. 37 總 結(jié) ........................................................................................................................... 38 致 謝 .......................................................................................................................... 39 參考文獻 ..................................................................................................................... 40 1 第一章 緒論 究背景 在汽車工業(yè)高速發(fā)展的帶動下,我國汽車零部件產(chǎn)業(yè)有了飛速發(fā)展,在全球供應(yīng)鏈中的地位明顯提高。目前 ,我國汽車零部件產(chǎn)品已經(jīng)從售后配件市場開始進入 低附加值產(chǎn)品向高附加值產(chǎn)品轉(zhuǎn)變,特別是一些自主品牌產(chǎn)品開始進入國際采購體系。 2006年,零部件出口連續(xù)第三年實現(xiàn)貿(mào)易額順差。汽車空調(diào)、車身零部件和空氣壓縮機的出口均實現(xiàn)了 100%的增長速度,同時我國比較傳統(tǒng)的汽車零部件產(chǎn)品比如汽車輪胎、汽車玻璃和車輪零部件也有較高的增長速度。 按照國際運行的標準,汽車行業(yè)整車與零部件規(guī)模比例應(yīng)為 1:此可以推算,我國汽車零部件產(chǎn)業(yè)還有很大的提升空間,另據(jù)有關(guān)資料顯示,到 2010年,世界汽車產(chǎn)品貿(mào)易總額將達到 國公司到 2007年底前,計劃在低成本國家采購 500億元的汽車零部件,其中 70%瞄準中國企業(yè)。 內(nèi)外研究現(xiàn)狀與發(fā)展 目前世界上對萬向節(jié)滑動叉的研究還是比較成熟的,給汽車行業(yè)的飛速發(fā)展提供了一個很好的技術(shù)支撐。十字軸式剛性萬向節(jié)具有結(jié)構(gòu)簡單,傳動效率高的優(yōu)點,但在兩軸夾角α不為零的情況下,不能傳遞等角速轉(zhuǎn)動。主要用于傳遞角度的變化,一般由突緣叉、十字軸帶滾針軸承總成、萬向節(jié)叉或滑動叉或花鍵軸叉、滾針軸承的軸向固定件等組成。萬向節(jié)叉是一個叉形零件,一般采用中碳鋼或中碳合金鋼的鍛造件,也 有采用中碳鋼的精密鑄造件。汽車工業(yè)的發(fā)展對高品質(zhì)、低成本鍛件的需求不斷上升。 目前,國內(nèi)各主要鍛造廠主要采用開式模鍛工藝進行生產(chǎn),鍛件成形質(zhì)量差,材料利用率低。因此迫切需要一種新的加工工藝,以提高成形質(zhì)量,減少材料浪費,降低成本。在研究傳統(tǒng)無飛邊鍛造工藝和擠壓工藝的基礎(chǔ)上,開發(fā)了滑動叉無飛邊閉式模鍛新工藝,以滿足滑動叉的無飛邊鍛造的要求。 有限元模擬研究表明,與開式模鍛工藝相比,無飛邊和小飛邊閉式模鍛新工藝具有鍛件精度高、成形質(zhì)量好、材料利用率高、所需設(shè)備噸位小等優(yōu)點,具有很好的工業(yè)應(yīng)用前景。 2 車零部件企業(yè)存在的問題 目前,跨國零部件生產(chǎn)商正在進一步加大對中國的投資,在華進行汽車零部件生產(chǎn)的外商獨資或合資企業(yè)已經(jīng)達到近 1200 家,在零部件一級供應(yīng)商這條鏈上,外資企業(yè)占據(jù)主導(dǎo)地位,尤其是在最近,跨國汽車零部件企業(yè)明顯有把零部件的研發(fā)工作轉(zhuǎn)向中國的趨勢,隨著他們建廠規(guī)模的逐漸擴大和對中國市場的熟悉,本土零部件企業(yè)面對的壓力也將越來越大。 究目的和意義 在工程機械和汽車的傳動裝置中,由于總體布置上的需要,都要用到萬向傳動裝置。它的功用主要是在兩軸不同心或有一定夾角的軸間傳遞動力,在工作中 相對位置不斷發(fā)生變化的兩軸間傳遞動力。萬向傳動裝置一般是由萬向節(jié)和傳動軸組成,有時還要有中間支承,主要用于以下一些位置:發(fā)動機前置后輪驅(qū)動汽車的變速器與驅(qū)動橋之間。當變速器與驅(qū)動橋之間距離較遠時,應(yīng)將傳動軸分成兩段甚至多段,并加設(shè)中間支承。 萬向節(jié)是實現(xiàn)變角度動力傳遞的機件,用于需要改變傳動軸線方向的地方。傳動軸是萬向傳動裝置的組成部分之一,這種軸一般長度較長,轉(zhuǎn)速高;并且由于所連接的部件(如變速箱與驅(qū)動橋)間的相對位置經(jīng)常變化,因而要求傳動軸長度也要相應(yīng)地有所變化,以保證正常運轉(zhuǎn),這就要用到滑動花鍵副。 滑動花鍵副由內(nèi)、外花鍵組成,在工作時滑動副之間的伸縮運動來實現(xiàn)距離變化,用于傳遞長度的變化。 萬向節(jié)滑動叉就是將萬向節(jié)叉和滑動花鍵副的一部分組合起來,使其成為一個零件,其特征是該萬向節(jié)滑動叉為采用管材制作的萬向節(jié)叉與滑動套為一體的整體式結(jié)構(gòu),其端部呈叉形結(jié)構(gòu),并設(shè)有兩個十字銷孔,用于安裝十字萬向節(jié);在管內(nèi)設(shè)有內(nèi)花鍵,這種呈整體式結(jié)構(gòu)的滑動叉,不僅加工容易、成本低,而且強度高,故其使用壽命與傳統(tǒng)的萬向節(jié)叉滑動套合件相比,有了成倍的提高。它的研究和使用可以簡化萬向傳動裝置的結(jié)構(gòu),也滿足功能要求,因此對萬向節(jié)滑動 叉的研究有極大的實際意義。 課題的主要研究內(nèi)容 1)繪制 1: 1比例的零件圖一張; 2)用三維軟件完成零件的三維圖構(gòu)造; 3 3)研究零件的材料、加工精度、技術(shù)要求, 進行工藝路線分析,并制定多種工藝路線進行比較; 4)完成此零件從毛坯到成品全部生產(chǎn)過程的一份完整的工藝規(guī)程; 5)完成此零件生產(chǎn)過程中所用到的專用夾具 2套,并繪制出夾具裝配圖; 6)用三維軟件完成所設(shè)計的專用夾具的三維造型; 7)完成畢業(yè)論文書寫。 4 第二章 零件的分析 件的作用 萬向節(jié)滑動叉主要應(yīng)用于工 程機械和汽車傳動裝置上,主要作用是在兩個不同心軸或有一定夾角的軸間傳遞動力,零件如圖 2示。該部件的 2 個 +在2 個叉頭上,為了起到萬向聯(lián)軸的功能,必須使?jié)L針軸承和十字軸接起來。把大小為55外圓零件和大小為 55花鍵孔以及花鍵軸(在傳動軸的頂端)配合起來,連接起來,才能獲得足夠的傳遞動力。 圖 2向節(jié)滑動叉零件圖 件的材料 萬向節(jié)滑動叉用的是 45號鋼的材料,這種非常好的碳素鋼,在一系列加工后具有良好的工藝和機械性能,在 滿足使用要求的前提下,選材還必須要符合材料的的經(jīng)濟性能,這樣加工出來的工藝才是最合理的 , 而 45號鋼恰恰非常滿足這樣的要求。 表 25鋼調(diào)質(zhì)后機械性能 屈服強度 σ s =550MN/抗拉強度 σ b=750 MN/延伸率 δ s=20% 布氏硬度 35 5 件的工藝分析 構(gòu)分析 零件尺寸如圖 2由兩個叉頭以及一個圓套里面有花鍵孔的部件組成,它的具體功能如下: 1)零件的兩個叉頭部做有兩個 +裝滾針軸承和十字軸,起到萬向聯(lián)軸節(jié)的作用 。 2) 為了不讓零件因為壓力改變形狀,必須要加強零件的剛性和連接強度, 叉頭 和花鍵孔套筒相聯(lián)結(jié)的筋條 起了這樣的作用。 3)為了使傳遞效果更合理,使內(nèi)圓 50? 外圓 65? 互配合。 圖 2萬向節(jié)滑動叉尺寸圖 工表面技術(shù)要求分析 對于萬向節(jié)滑動叉來說,有兩組加工表面上是有位 置方面的要求的。具體如下: 1)以 39? 6 這樣一個加工表面主要由 4個 2 個 +且還有大小為 孔和 2個孔為 +個過程中主要還是加工孔的大小為 + 2) 以 Φ50鍵孔為中心的加工表 面 ; 這一組加工表面包括: 6 齒花鍵孔,尺寸為 55? 再有外面大小為 Φ65表面 , 和外螺紋孔大小為 在這樣的 2組加工表面對于其位置方面也是有要求的 , 具體的要求如下 : ①與孔中心連線的垂直度公差必須達到 100比 關(guān)于 1039? 個孔必須滿足如此指標 。 ②大小為 39? 2個孔外端面必須和孔的大小為 39? ③大小為 39? 心線 和 。 根據(jù)以上的分析看,當加工兩個表面時,可以先加工其中一個不太復(fù)雜的表面,然后再利用專用夾具加工其另外一個表面, 并且保證它們之間的位置精確要求。 為了提高零件的疲勞極限,方法有如下兩種: 第一種采用 表面噴砂處理 的方法,因為工件自身容易受正反向沖擊性載荷的影 響而產(chǎn)生疲勞損裂,如此可以加強它的表面硬度。 第二種就是在零件的表面形成殘余壓應(yīng)力,這樣可以和零件工作時造成的拉應(yīng) 力進行抵銷。 7 第三章 工藝規(guī)程設(shè)計 劃零件工藝規(guī)程的規(guī)定以及技術(shù)指導(dǎo) 藝要求 加工一套優(yōu)秀的工藝品,必要要一套合理和正確的工藝過程,而零件的加工工藝 過程又是零件生產(chǎn)過程中一個非常重要的階段,而且一個零件可以 用很多種工藝過程 加工處理,所以工藝過程很重要,也要滿足如下要求: 1)要使加工過程符合圖紙的要求 2)要保證技術(shù)要求才能有高質(zhì)量的產(chǎn)品 3)不斷的改善生產(chǎn)條件和改良生產(chǎn)率 4)要注重經(jīng)濟因素 術(shù)依據(jù) 1)產(chǎn)品的零件圖,裝配圖,技術(shù)要求 2)毛坯生產(chǎn)以及供應(yīng)條件 3)年生產(chǎn)綱領(lǐng) 4)車間的一系列生產(chǎn)要求 5)技術(shù)要求方面的條件 產(chǎn)類型的確定 生產(chǎn)綱領(lǐng)公式: ? ?N Q n 1 & % ( 1 % )?? ? ? ? ( 3 此零件的年產(chǎn)量 Q= 5000件 /年 (產(chǎn)品的年產(chǎn)量) n = 1件 /輛(每輛汽車該零件的數(shù)量) &=4 (零件的備品率) β =1 (零件的廢品率) ? ? ? ?N 5 0 0 0 1 1 4 % 1 1 % 5 2 5 2? ? ? ? ? ? ? 根據(jù)該生產(chǎn)綱領(lǐng)決定成批生產(chǎn)該零件 定毛坯的制造形式 對于材質(zhì)為 45 號的零件,要提高生產(chǎn)率和保證加工的 質(zhì)量,考慮到正向或者反向 行駛的汽車要受到交變載荷或者沖擊載荷的作用,而還要保證它的金屬纖維在這樣的 8 一個過程中不能被割斷,所以要選用鍛件這樣的材料。又考慮到該零件 5252件的生產(chǎn) 量 /每年,這個過程是多量生產(chǎn)的過程。而且零件又不太大,所以會采取用模鍛成型的 方法。 為什么要采取模鍛毛坯,考慮到如下幾個特點: 1)生產(chǎn)的時間較短。 2)生產(chǎn)效率高,產(chǎn)品的質(zhì)量得以保證。 3)模鍛的輪廓外形大小和零件很相似,不需要大量材料。 定工藝路線及其方法 工方法的選擇 零件加工出來的質(zhì)量以及零件生 產(chǎn)過程需要的時間和資金都和零件的各個加工的表面的加工途徑有關(guān)系,加工的方法越合理,加工出來的產(chǎn)品性價比越高。根據(jù)零件表面的大小,精確程度,表面的狀況,還有它的粗糙程度以及零件的整體的結(jié)構(gòu)造成等等,都跟零件的加工在同一個表面上不同的加工方法有關(guān)系。 對主要處理的工作面的工作方法的制定安排: 對于 2個 +采用 2套加工方法: 1)對于生產(chǎn)量不多的零件來說,要求它的加工過程便宜適用,不建議使用鉆和拉的方案。 2)對于零件的尺寸公差和表面粗糙 度,它們沒有較大的要求,所以可以使用鉆和鏜的方法。 采用粗銑和磨的方法對于零件的尺寸外形要求垂直的兩個孔。( 1039? 對于 50? 花鍵孔,選擇鉆 拉的方法,這樣子就不需要先車后拉。 車削 65? 60 準的選擇 考慮到錯誤的基準的要求 會造成零件大量的報廢,甚至沒有辦法正常運用。所以,做工藝的過程中,基準面的選擇很重要,一定要合理,生產(chǎn)出來的零件才不會有問題,質(zhì)量上符合。 9 基準的選擇 外圓為粗基準的軸類工件一般來說肯定是正確的??墒钱敿庸み@樣的零件時,把65? 會產(chǎn)生不對稱的情況,尤其是在零件的外圓住的表面和叉部的外形方面。采用粗基準的方法才加工這樣的零件,粗基準定為叉部位 2個+的表層,為了抵消 x? x? y? y? 四個自由度,利用 2個樣為了抵消 z? z? 這 2個自由度,還得利用自動定位的窄口卡爪,頂在外圓柱面上,這樣才能實現(xiàn)完全定位效果。 基準的選擇 想到基準重合的因素時,精基準為首選。如果制作過程中的基準和本來的工序的基準不能一致時,變換尺寸。 定工藝路線 暫定 2種工藝的路線方法,主要還是考慮到零件的結(jié)構(gòu)大小和技術(shù)層面的要求。如何制定工藝路線,必須要使零件在幾何大 小,精度以及位置等因素都滿足要求,而且還得考慮到零件可能大量生產(chǎn)的情況,提高零件的生產(chǎn)效率。這樣的工藝路線才是最合理的。 藝路線一 00 車 螺紋 , 車外圓尺寸為 6205 2次鉆孔,并且擴花鍵大小為 43锪尺寸 55? 10 倒角 5×60°。 15 鉆 的底孔 20 拉花鍵孔 25 粗銑 39? 2 個 孔端面 30 精銑 39? 2 個 孔端面 35 擴,鉆孔,粗精鉸 2個 39? 45? 度 40 鉆大小為 8的尺寸,底孔大小是 倒角大小尺寸為 120度。 45 需要攻螺紋大小為 8孔大小為 角為 120度。 10 50 沖箭頭。 55 檢查 藝路線二 00 粗銑 39? 孔端面。 05 精銑 39? 孔端面。 10鉆 39? 15鏜 39? 20 精鏜大小為 39的 2個孔,倒角大小為 2 45? 度。 25 車外圓大小分別為 62毫米, 60毫米的尺寸 ,車螺紋大小尺寸為 ? 毫米。 30 鉆,鏜大小為 43大小為 55 35 倒角 5 60? 度 40 鉆 的底孔。 45 拉一下花鍵孔 50 鉆大小為 8螺紋底孔和大小為 孔,倒角大小為 120 度 55 攻螺紋的大小為 8角大小為 120度。 60 沖箭頭 65 檢查。 藝路線方案三 00 車端面并且車大小為 62毫米 ,60毫米的外圓,車尺寸為 ? 05 鉆,擴花鍵尺寸為 43毫米的底孔,锪尺寸為 55毫米的沉頭孔。 10 內(nèi)花鍵孔大小為 5 60? 度的倒角。 15 鉆錐螺紋大小為 的底孔。 20 拉花鍵。 25 粗銑大小為 39孔端面。 30 鉆,擴大小尺寸為 39毫米的 2個孔和倒角。 35 精,細鏜大小為 39 40 磨大小尺寸為 39毫米的二孔端面,他們的大小尺寸為 45 鉆叉部 4 個大小為 8 11 50 攻大小尺寸為 4如此的的螺紋。 55 沖箭頭。 60 終檢。 析和比較工藝方案 比較一下上面提到的 2種方案的優(yōu)缺點: 第一種方案 : 首先加工的是按花鍵孔作為最主要的的表面,接下再按這樣加工出來的面作為基準面加工大小為 39 第二種方案:首先加工大小為 39下來按此 2個孔為基準處理花鍵孔和它的外層表面。 比較:先處理花鍵孔,再用花鍵孔來定位處理大小為 39 個孔,這樣可以確保位置的精確,使用起來也較方便。 但會發(fā)現(xiàn)在第一種方案中 35道工序在替換到第二種方案中的 10,15,20 縮短了裝夾的數(shù)量??墒侨邕@樣在一道工序中就得完成很多的步驟,會造成 加工方面的困擾。 如依據(jù)第二種計劃的要求處理,大小尺寸為 39毫米的 2個孔中心線要和大小尺寸為 55毫米的花鍵孔的中心線互相垂直,則加工大小為 39得以花鍵孔為基準。在如此場景下策劃基準就能和工藝基準一致了,達到了加工指標。在制定的工藝途徑中沒有按照上述這樣做,則無形中違背了基準重合,造成加工方面的誤差。而方案三卻可以合理解決這些問題,所以最后確定了如下加工路線: 00 車大小尺寸分別為 62毫米, 60毫米的外部圓和端面,車削 ? 毫米的螺紋,把 2個 叉耳外輪廓以及大小尺寸為 65毫米的外圓設(shè)置為粗基準,如此過程中裝夾的選定采用專門夾具,和型號為 體見表 3 表 3工序卡 1 12 05 鉆,增添大小尺寸為 43毫米的花鍵孔,锪大小尺寸為 55毫米的沉頭孔,把大小尺寸為 62毫米的外圓設(shè)置為基準,選型號 10 內(nèi)花鍵孔 5 60? 度的到角。選用型號 體見表 3 表 3工序卡 2 15 鉆底孔大小為 的錐螺紋。如此進程中用型號 里考慮到要為下一步拉花鍵抵消回轉(zhuǎn)自由度,從而安排一個定位基準,所以安排鉆 底孔的步驟。具體見表 3 表 3工序卡 3 13 20 拉花鍵孔。這里將利用 位選用花鍵內(nèi)底孔,大小為 55 的錐紋。具體見表 3 表 3工序卡 4 25 粗洗大小尺寸為 39毫米的 2孔端面,定位是花鍵孔。這里出來是用型號 體見表 3 表 3工序卡 5 14 30 鉆,擴大小尺寸為 39毫米的 2個孔。定位是花鍵孔和 端面。利用型號為 體見表 3 表 3工序卡 6 35 精,細鏜大小為 39個孔。加工的方法為利用夾具和 臥式金剛鏜床,定位為花鍵內(nèi)孔和端面。具體見表 3 15 表 3工序卡740磨大小為 39 2個孔端面,確保它的尺寸為 定位為大小為39里用 具體見表 3 表 3工序卡 8 16 45 鉆叉部 4個 里選用型號為 式和專們夾具處 理,定位為花鍵孔和大小尺寸為 39毫米的孔。 具體見表 3 表 3工序卡 9 50 攻螺紋 4。 具體見表 3 表 3工序卡 10 17 55 沖箭頭。 具體見表 3 表 3工序卡 11 60 終檢。 18 械加工余量,工藝尺寸及毛坯尺寸的確定 開始萬向節(jié)滑動叉的材質(zhì)設(shè)為 45號鋼,它的硬度要求選為: 207 到 241此同時毛坯重量大概定為 6理毛坯的方式為模鍛,因為該類型需要大批量生產(chǎn)。 下面分別來確定加工余量,和工序尺寸以及毛坯的尺寸 62? 60×1 考慮到要在模鍛進程中簡化毛坯的外在,雖說加工的長度大小為 90毫米,但和它相接是直徑大小為 65 毫米的非加工表層,所以這里還是定它的外圓表面直徑的大小為65層的無拘束尺寸的共差的大小定為 62毫米,它的表層粗糙度大小尺寸指標為這里選 =的是粗加工的方法,直徑剩余量 2所有都能符合加工的需要。 里在軸線方向上 — 端面: ? 毫米) 通過查相關(guān)資料,可以設(shè)定鍛件的 6量, 繁雜外形系數(shù) , 廓的大小尺寸應(yīng)該需符合大于 180米 。 通過查手冊定其余量大小為 9坯設(shè)定實心,不沖出孔。所以 2個類孔精度安排在 間。 下面核定工序尺寸和余量: 鉆孔: 25? 孔 : 37? 2Z 大小尺寸為 12毫米 擴鉆 : 2Z 大小尺寸為 精鏜 : 2Z 大小尺寸為 細鏜 : + 2 4. 花鍵孔 ( 0 . 0 3 9 + 0 . 1 6 + 0 . 0 4 80 0 01 6 5 0 m m 4 3 m m 5 m m?? ? ? ? ?) 這里要求拉削加工(花鍵孔 — 外徑定心) 定內(nèi)孔的尺寸大小為 : 孔的加工余量如下: 鉆大小為 25孔, 鉆大小為 41鉆大小為 42的孔 19 拉花鍵孔( 0 . 0 3 9 + 0 . 1 6 + 0 . 0 4 80 0 01 6 5 0 m m 4 3 m m 5 m m?? ? ? ? ?) 查找手冊,暫定拉削時的處理余量為 2Z 為 1毫米。外徑定心 — 花鍵孔。 個外端面的加工余量計算長度: ) 參照手冊定加工過程中精度為 件的重量設(shè)為 6此合計下來,在 2孔外端面,它的單邊加工余量大概在 間, 定 。 2) 磨削余量:單側(cè)為 削公差定為: 3) 銑削余量:單邊的銑削公差余量為 Z= 洗削公差:在粗洗的進程中定 而定 因為在每一道工步和毛坯的處理過程中都存在加工公差,所以把這里的加工余量只是名義上的。而在實際操作中是有最小和最大加工余量的區(qū)別的。 這里考慮到零件是多量生產(chǎn),應(yīng)選用合理的加工方法去計算最大和最小的加工余量。 39? 毫米兩孔外端面 尺寸加工余量和加工過程中的工序間余量和公差安排如圖 3 圖 3序間余量和公差安排 根據(jù)圖可以計算出: 20 毛坯名義尺寸大小為: 118 2 2?? =122毫米 毛坯的最大尺寸大小為: 122 ?? =米 毛坯最小尺寸大?。?122 ?? =米 粗銑后最大尺寸大小: 118 ?? =米 粗銑后 米 由此得出磨后大小和零件圖大小一樣都是 定切削用量和基本工時 在第 15道工序:車削端面和外圓以及螺紋。這里的切削用量多少由計算的方法而定。 工條件 工件材質(zhì):給 45 號剛進行正火處理, σ模鍛。 加工安排:第一粗車 60? 毫米,第二斷面和大小尺寸分為 60毫米 ,62毫米的外圓, , 三車大小尺寸為 ? 毫米的螺 紋。 選用 選材質(zhì)為 刀片,刀桿的大小為 16 25? r 90? ??, 5度, а0大小為 12度, r? 為 選用 60度的螺紋車刀,刀片的材質(zhì)為 算切削用量 ? 1)核定毛坯在跨越年度方向的最大處理余量為 里因為毛坯長度方向的處理余量為 毫米,參照 7度的模鍛拔模斜度),但是現(xiàn)實處理過程中還得考慮為了空出一個尺寸大小為 40毫米的心部,之后鉆花鍵底孔時處理掉,并且不用全部處理掉,所以實際的端面最大處理余量設(shè)為 米,并且用 2道工步搞定,а p=3用 2)當?shù)稐U尺寸為 m m 2 5 m m 3 m ,以及工件直徑為 60, 進給量 f=r 21 3)參照手冊計算切削速度 X v Y c C v / T m f k m / m i n T 6 0 m i ( )這里: C v 2 4 2 X v 0 . 1 5 Y v 0 . 3 5 m 0 . 2? ? ? ?, , , 參照手冊修正系數(shù) m v s v k v k r v B v k 1 . 4 4 k 0 . 8 k 1 . 0 4 k 0 . 8 1 k 0 . 9 7? ? ? ? ?, , , , 。因此: 0 . 2 0 . 1 5 0 . 3 5V c 2 4 2 / 6 0 3 0 . 5 1 . 4 4 0 . 8 1 . 0 4 0 . 8 1 0 . 9 7 1 0 8 . 6? ? ? ? ? ? ? ? ? 4) 確定機床主軸轉(zhuǎn)速 s c 0 0 0 v / d 5 3 2 m / m i n??? ( )參照手冊機床轉(zhuǎn)速為每分鐘 532轉(zhuǎn),和它靠近的分別是每分鐘 480 轉(zhuǎn)和每分鐘 600轉(zhuǎn),而當 8 0 r / M 會造成速度損失,所以選用 0 0 r / M 這樣實際的切削速度為 122m/ 5) 切削工時,根據(jù)手冊 1 2 3 l 6 5 4 0 / 2 1 2 . 5 m m l 2 m m l 0 l 0? ? ? ? ? ?( ) , , ,1 2 3t m l l l / n w f i 1 2 . 5 2 / 6 0 0 0 . 5 0 . 0 9 6 m i n? ? ? ? ? ? ? ( )2. 粗車大小為 62刻還得檢驗機床功率和進給機構(gòu)強度。 1)切削深度 定 需一次切除。 2)根據(jù)手冊采用 3)計算切削速度 : 116(m/4)確定主軸的轉(zhuǎn)速為 : s c 0 0 0 v / d 5 6 8 r / m i n??? ( )因為之前的機床轉(zhuǎn)速 00轉(zhuǎn)。 因此加工過程中切削速度為 : ? ?V d n / 1 0 0 0 6 5 x 6 0 0 / 1 0 0 0 1 2 2 m / m i n??? ? ? 5)根據(jù)機床功率 按機床手冊得主要加工切削力公式: ? ? n 8 4 3 r / m i n? F c F c F c F 7 9 5 X 1 . 0 Y 0 . 7 5 n 0 . 1 5? ? ? ? ?, , ,( / 6 5 0 )P = . 7 5 0 . 1 5F c 2 7 9 5 1 . 5 0 . 5 1 2 2 0 . 9 4 0 . 8 9?? ? ? ? ? ?=以切削加工時消耗的功率 ? 410 ) 22 綜上所述選用功率為 620且主軸轉(zhuǎn)速每分鐘600轉(zhuǎn)時,主軸傳送的最大功率會達到 到加工指標。 6) 校核機床進給 系統(tǒng)強度 主切削力設(shè)定 F c 10 1 ? 根據(jù)手冊徑向切削力 F F Fp p y p c a f v k?這里F p F p F p F 9 4 0 x 0 . 9 y 0 . 6 n 0 . 3? ? ? ? ?, , ,( / 6 5 0 )P = . 9 0 . 6 0 . 3F p 1 9 4 0 1 . 5 0 . 5 1 2 2 0 . 8 9 7 0 . 5?? ? ? ? ? ?=195N 切削力 (軸向 ): F F Ff f y p c a f v k?F f F f F f F 8 8 0 x 1 . 0 y 0 . 5 n 0 . 4? ? ? ? ?, , ,( / 6 5 0 ) =削力(軸向): 0 . 5 0 . 4 8 8 0 1. 5 0 . 5 1 2 2 0 . 9 2 3 1. 1 7?? ? ? ? ? ?=480N 考慮到磨合系數(shù)為 軌和床鞍),進給部分在縱向前進方向上獲得的切削力大小為:f c p F F F F?? ? ?( )=480+95) =600N 結(jié)合手冊, 3530N 為機床縱向進給部分能夠接受的最大縱向力,因此機床可以正常運轉(zhuǎn)。 7) 切削工時 12t l l l / n f? ? ?12l 9 0 l 4 l 0? ? ?, ,因此 t 9 0 4 / 6 0 0 0 . 5 0 . 3 1 m i n? ? ? ? ( ) 3. 車大小為 60外圓柱面 根據(jù)手冊f=r v Y c C v k / T m 里 242 m=k =k =23 則 ? ?V c 1 5 9 m / m i n? ? ? n 8 4 3 r / m 參照說明書 70r/削工時 12t l l l / n f? ? ?( )其中:12l 2 0 l 4 l 0? ? ?因此 t 2 0 4 / 7 7 0 0 . 5 0 . 0 6 2 m i n? ? ? ?( ) ( ) 4. 車螺紋 ? )參照手冊核算切削過程中速度,定 T 為 60壽命(高速螺紋車刀),粗車螺紋 а p =刀 次數(shù) 為 2次。 X v Y c C v k / T m 這里 m=距 t=1 1 . 7 5 6 3 7 / 0 . 6 1. 1 1 k 0 . 7 5??( ) ,因此粗車螺紋時: ? ?V c 2 1. 5 7 m / m i n? 精車螺紋時 ? ? V c 3 6 . 8 m / m i n? 2)確定主軸轉(zhuǎn)速 粗車螺紋時 0 0 v / D 1 0 0 0 2 1 . 5 7 / 6 0 1 1 4 . 4 r / m i n??? ? ? ( )參照機床說明書得 n 184r / M 所以加工的切削速度便為每分鐘 34 米 3) 切削過程中 切入長度1l 3車螺紋工時 ? ?1? 1t l l / n f 0 . 7 5 m i ? ?( )精車螺紋 21t l l / n f 0 . 1 8? ? ?( ) t=m/ 24 5? mm f=r (參照切削手冊 ) v= 0 0 0 v / d 1 0 0 0 1 2 . 2 5 / 2 5 1 5 5 r / m i n??? ? ? ? (考慮到工藝手冊中對機床的要求, 這里定 36轉(zhuǎn) 因此實際加工過程中切削速度 : d n /