【溫馨提示】壓縮包內(nèi)含CAD圖有下方大圖片預覽,下拉即可直觀呈現(xiàn)眼前查看、盡收眼底縱觀。打包內(nèi)容里dwg后綴的文件為CAD圖,可編輯,無水印,高清圖,壓縮包內(nèi)文檔可直接點開預覽,需要原稿請自助充值下載,所見才能所得,請見壓縮包內(nèi)的文件及下方預覽,請細心查看有疑問可以咨詢QQ:11970985或197216396

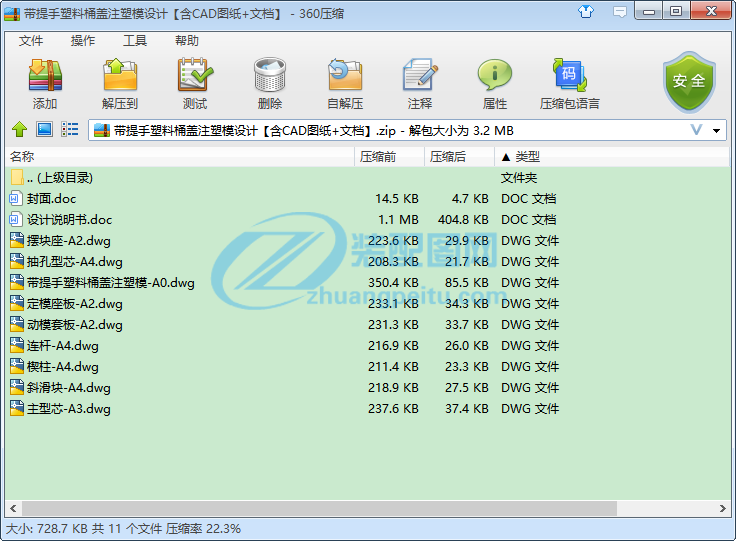
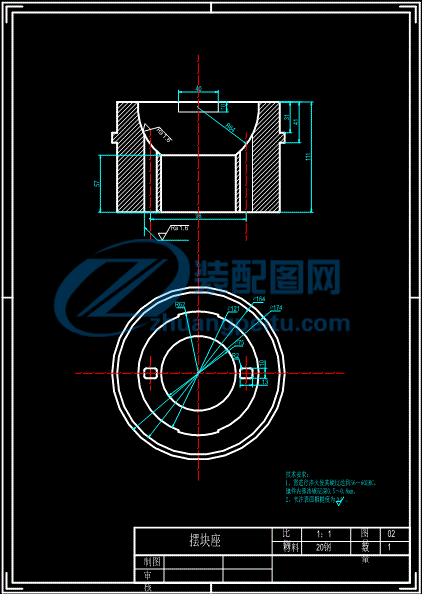
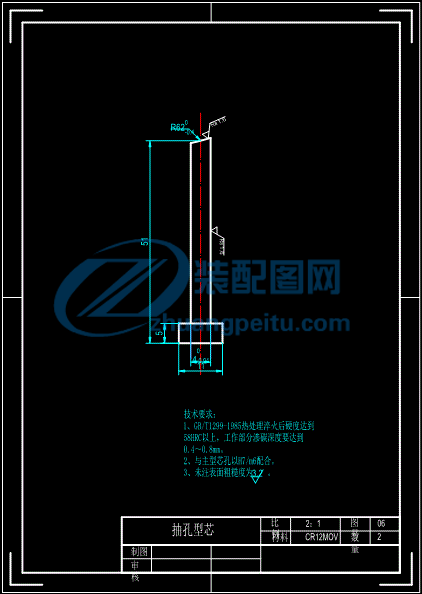
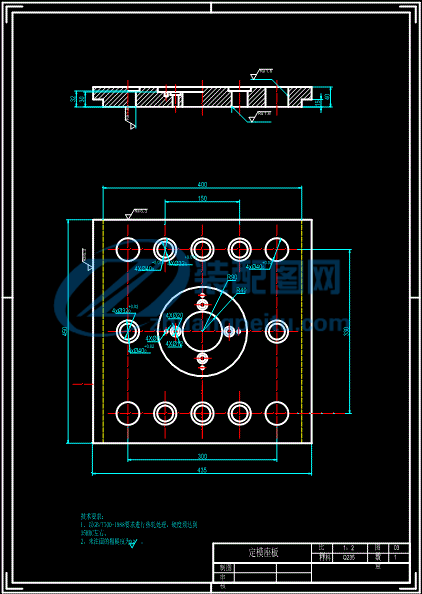

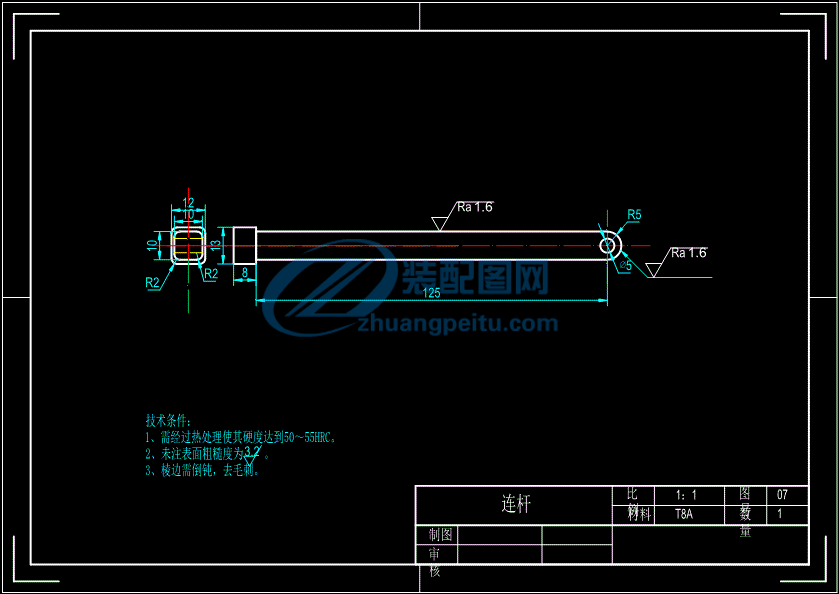
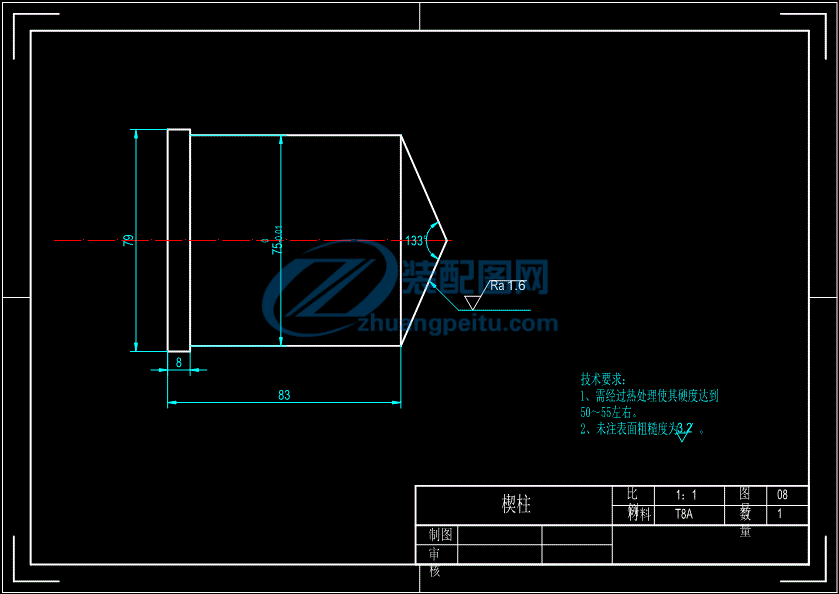
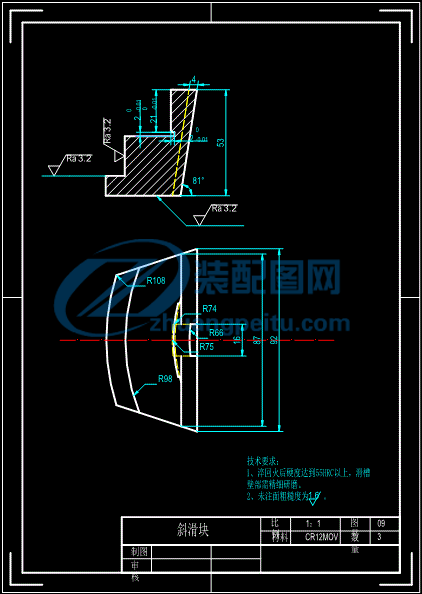
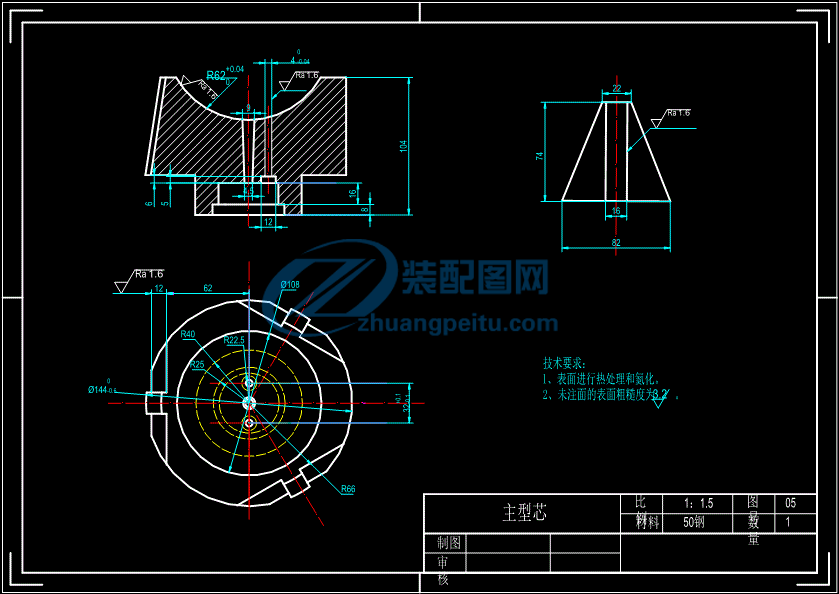
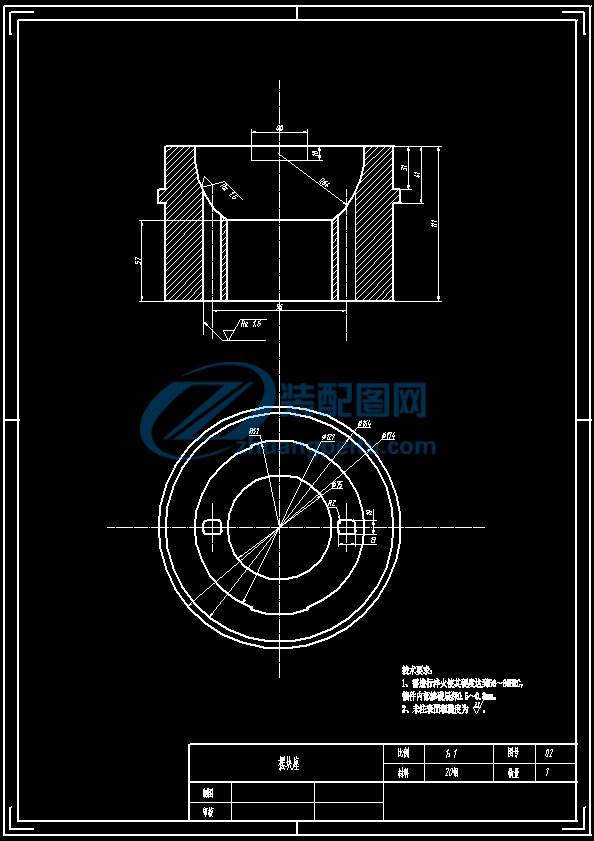
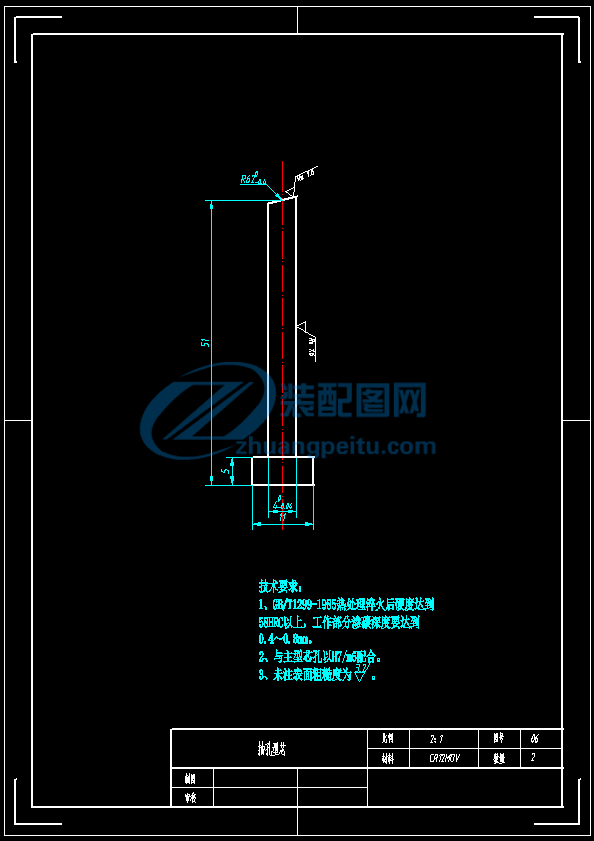
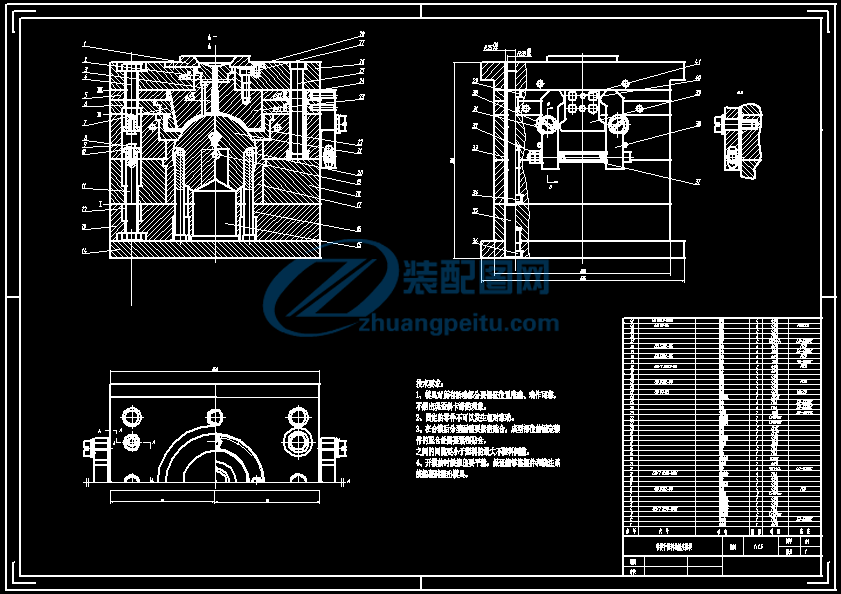
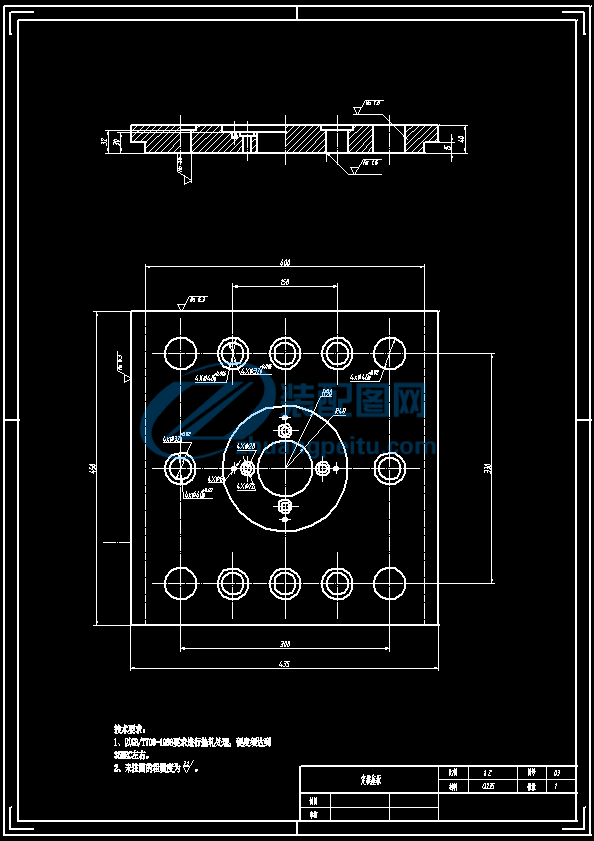
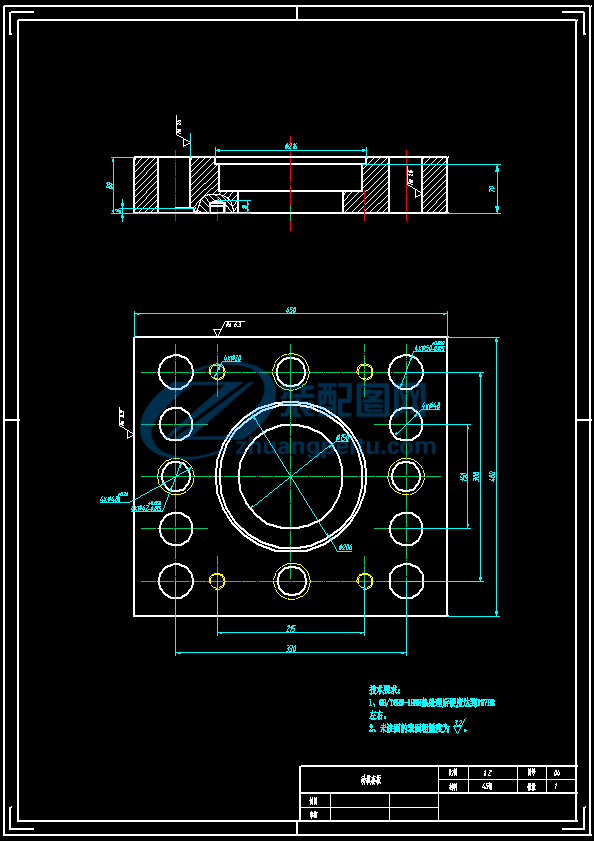
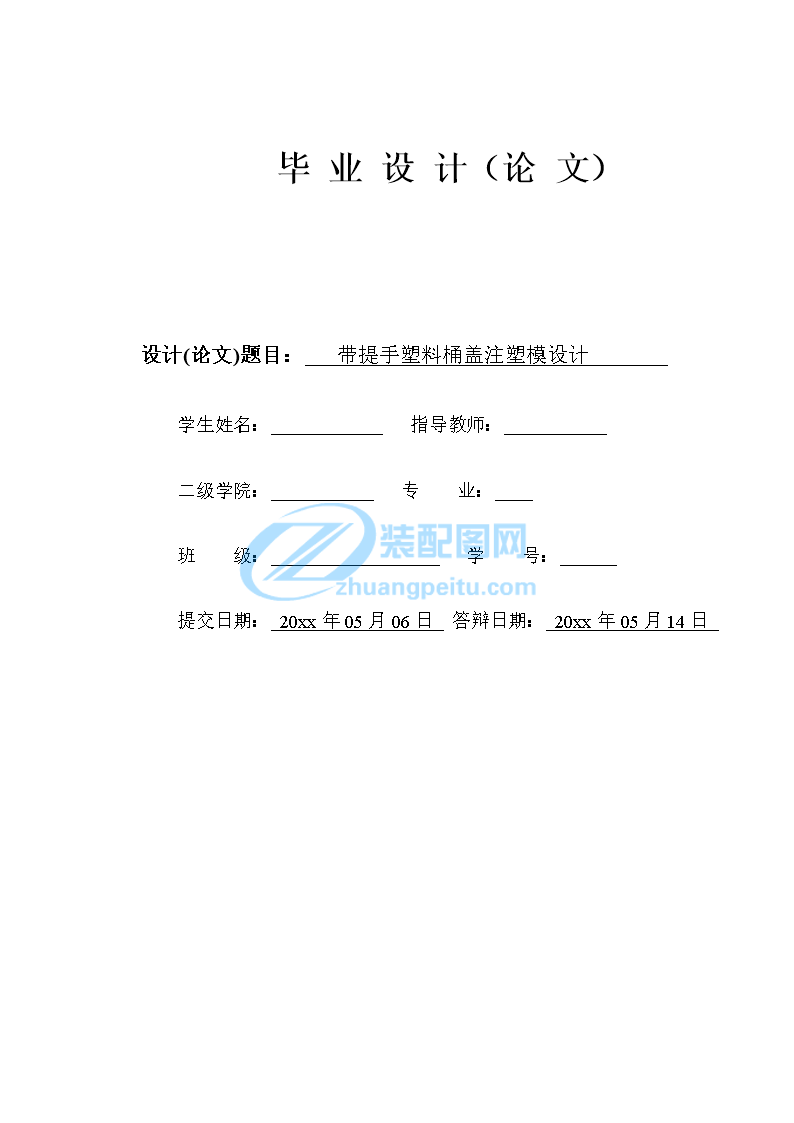
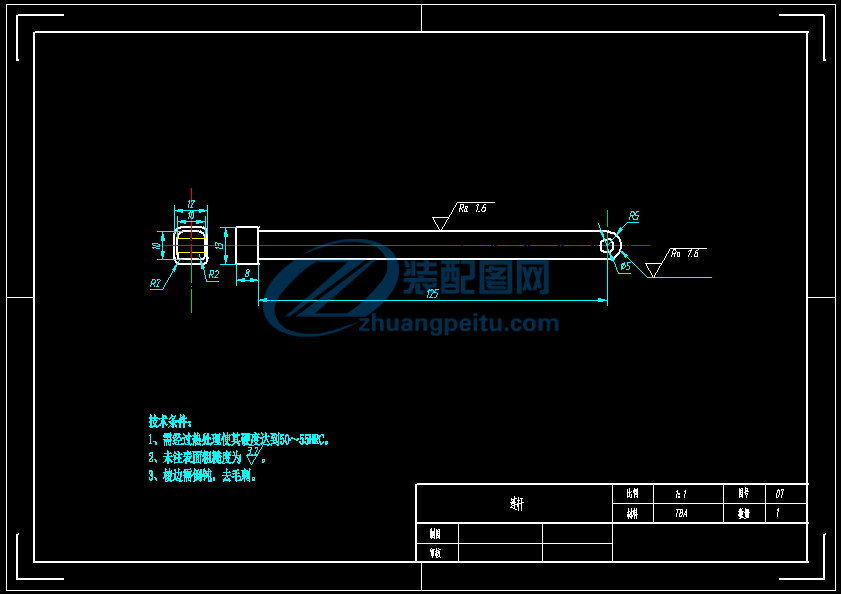
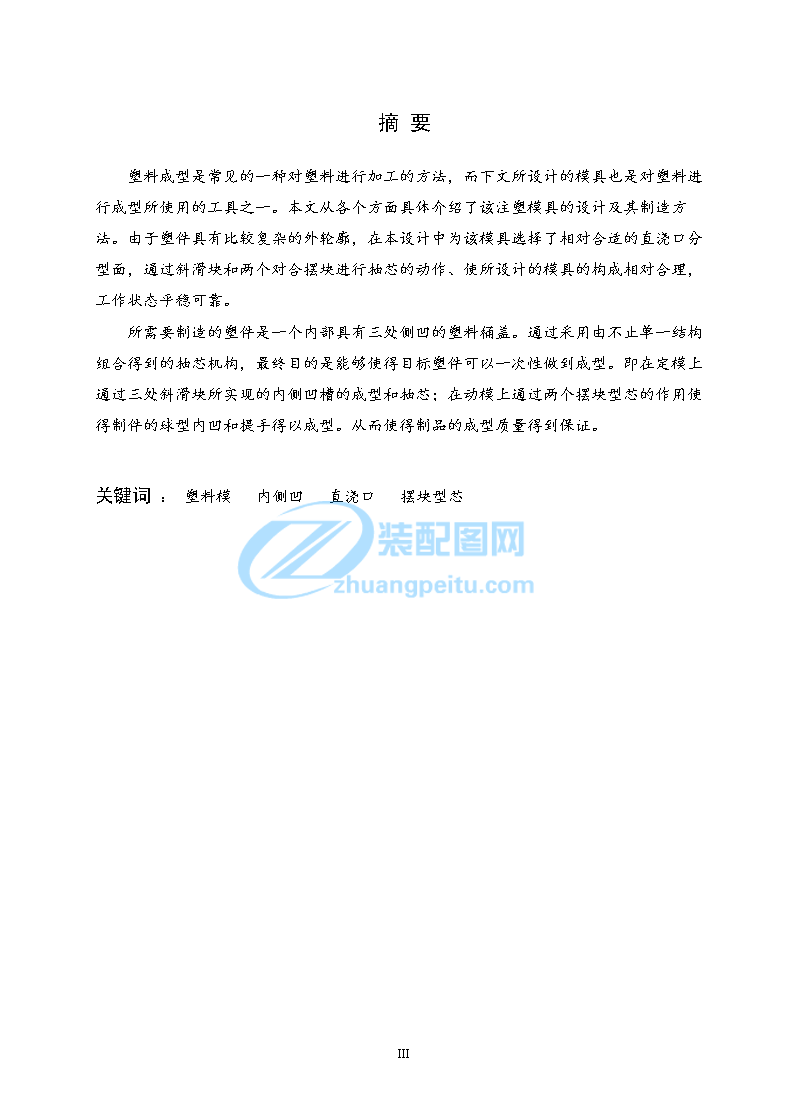
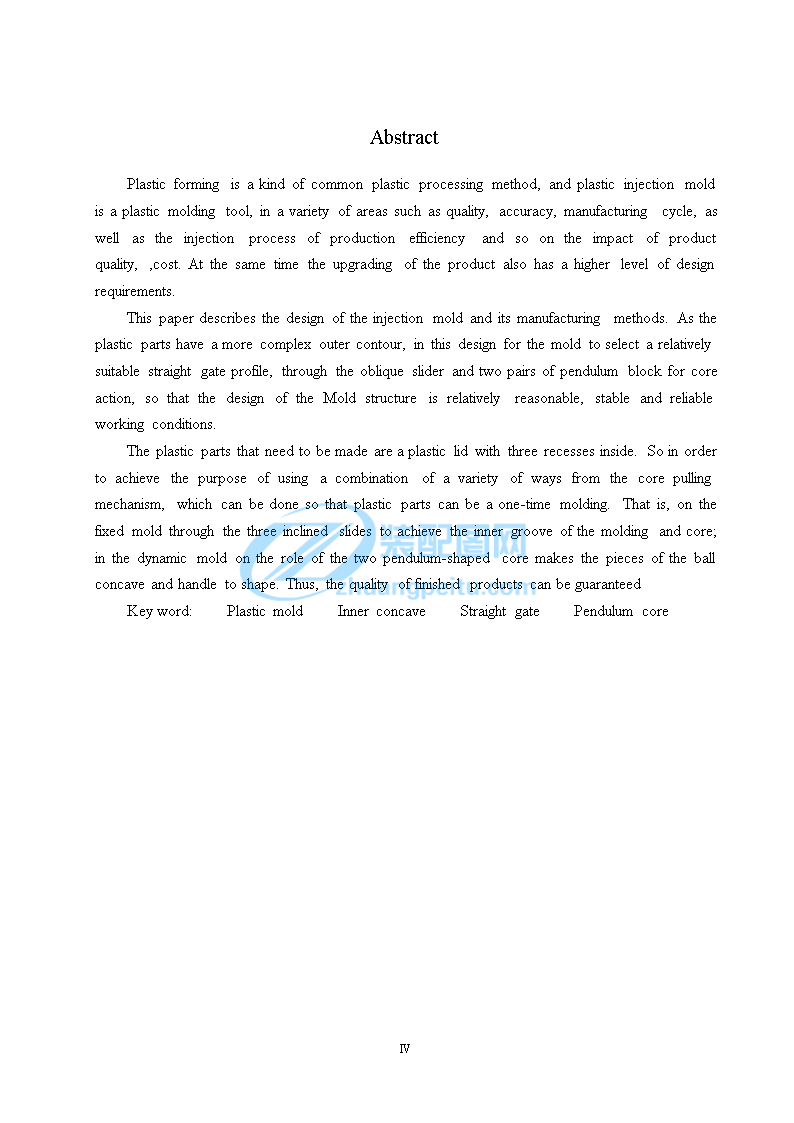
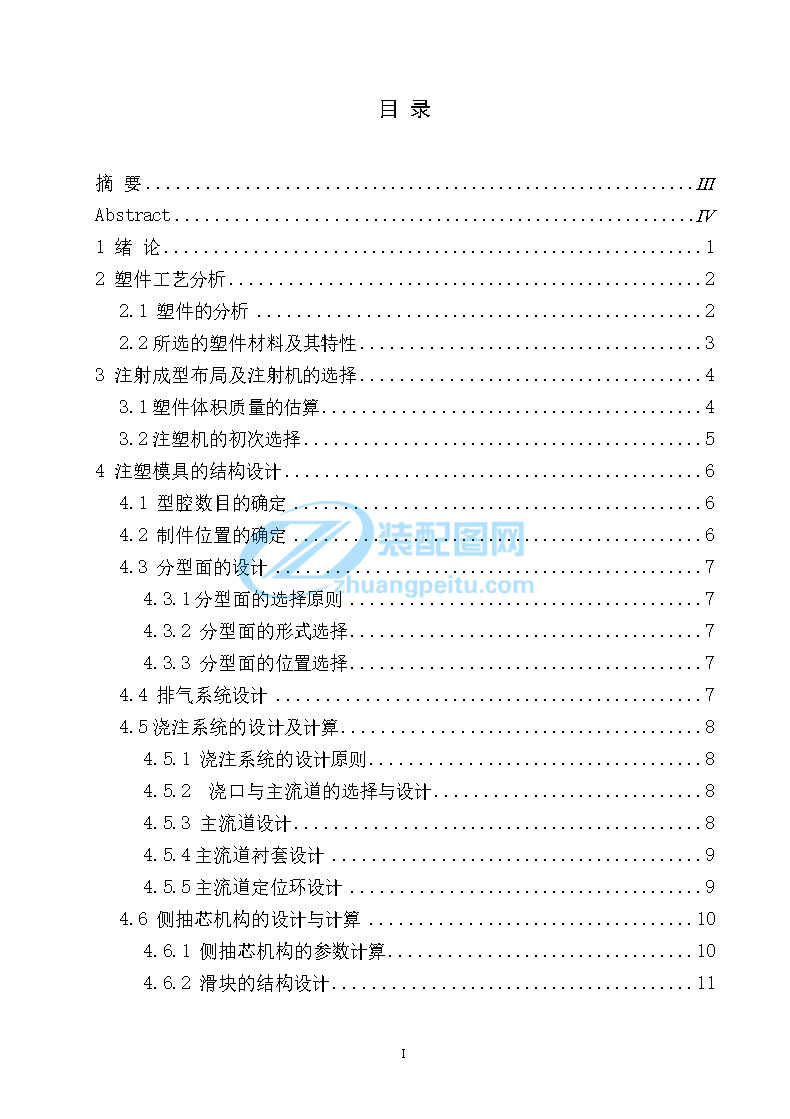
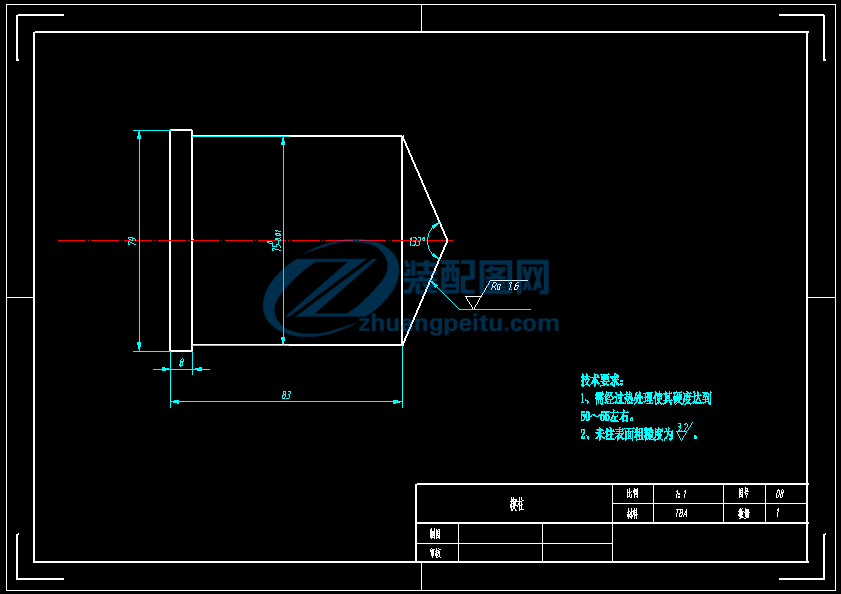
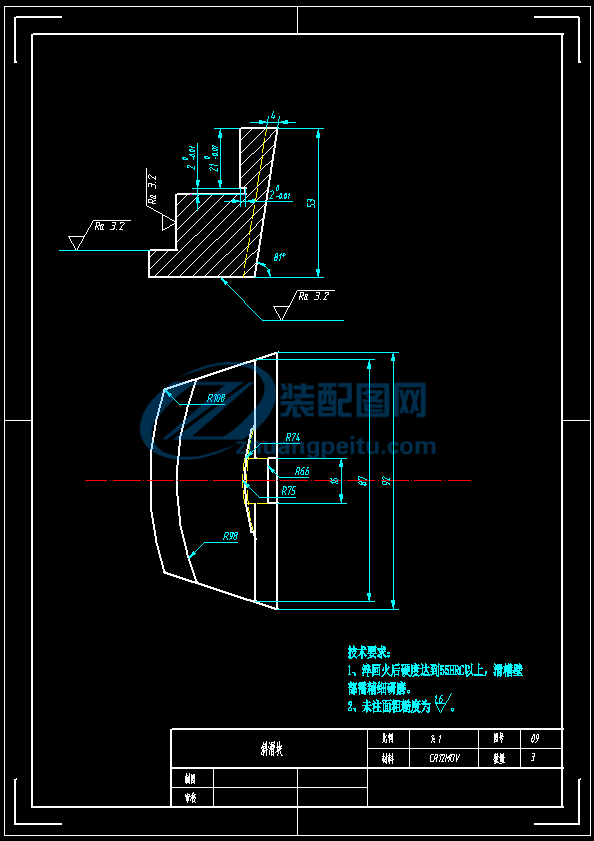
畢 業(yè) 設 計(論 文)
設計(論文)題目: 帶提手塑料桶蓋注塑模設計
學生姓名: 指導教師:
二級學院: 專 業(yè):
班 級: 學 號:
提交日期: 20xx年05月06日 答辯日期: 20xx年05月14日
壓縮包內(nèi)含有CAD圖紙和說明書,咨詢Q 197216396 或 11970985
摘 要
塑料成型是常見的一種對塑料進行加工的方法,而下文所設計的模具也是對塑料進行成型所使用的工具之一。本文從各個方面具體介紹了該注塑模具的設計及其制造方法。由于塑件具有比較復雜的外輪廓,在本設計中為該模具選擇了相對合適的直澆口分型面,通過斜滑塊和兩個對合擺塊進行抽芯的動作、使所設計的模具的構成相對合理,工作狀態(tài)平穩(wěn)可靠。
所需要制造的塑件是一個內(nèi)部具有三處側凹的塑料桶蓋。通過采用由不止單一結構組合得到的抽芯機構,最終目的是能夠使得目標塑件可以一次性做到成型。即在定模上通過三處斜滑塊所實現(xiàn)的內(nèi)側凹槽的成型和抽芯;在動模上通過兩個擺塊型芯的作用使得制件的球型內(nèi)凹和提手得以成型。從而使得制品的成型質(zhì)量得到保證。
關鍵詞 : 塑料模 內(nèi)側凹 直澆口 擺塊型芯
Abstract
Plastic forming is a kind of common plastic processing method, and plastic injection mold is a plastic molding tool, in a variety of areas such as quality, accuracy, manufacturing cycle, as well as the injection process of production efficiency and so on the impact of product quality, ,cost. At the same time the upgrading of the product also has a higher level of design requirements.
This paper describes the design of the injection mold and its manufacturing methods. As the plastic parts have a more complex outer contour, in this design for the mold to select a relatively suitable straight gate profile, through the oblique slider and two pairs of pendulum block for core action, so that the design of the Mold structure is relatively reasonable, stable and reliable working conditions.
The plastic parts that need to be made are a plastic lid with three recesses inside. So in order to achieve the purpose of using a combination of a variety of ways from the core pulling mechanism, which can be done so that plastic parts can be a one-time molding. That is, on the fixed mold through the three inclined slides to achieve the inner groove of the molding and core; in the dynamic mold on the role of the two pendulum-shaped core makes the pieces of the ball concave and handle to shape. Thus, the quality of finished products can be guaranteed
Key word: Plastic mold Inner concave Straight gate Pendulum core
Ⅳ
目 錄
摘 要 Ⅲ
Abstract Ⅳ
1 緒 論 1
2 塑件工藝分析 2
2.1 塑件的分析 2
2.2所選的塑件材料及其特性 3
3 注射成型布局及注射機的選擇 4
3.1塑件體積質(zhì)量的估算 4
3.2注塑機的初次選擇 5
4 注塑模具的結構設計 6
4.1 型腔數(shù)目的確定 6
4.2 制件位置的確定 6
4.3 分型面的設計 7
4.3.1分型面的選擇原則 7
4.3.2 分型面的形式選擇 7
4.3.3 分型面的位置選擇 7
4.4 排氣系統(tǒng)設計 7
4.5澆注系統(tǒng)的設計及計算 8
4.5.1 澆注系統(tǒng)的設計原則 8
4.5.2 澆口與主流道的選擇與設計 8
4.5.3 主流道設計 8
4.5.4主流道襯套設計 9
4.5.5主流道定位環(huán)設計 9
4.6 側抽芯機構的設計與計算 10
4.6.1 側抽芯機構的參數(shù)計算 10
4.6.2 滑塊的結構設計 11
4.7 模具加熱與冷卻系統(tǒng)的設計 11
4.7.1 冷卻系統(tǒng)設計的參數(shù)計算 11
4.7.2 冷卻水道的布置 12
4.8 脫模機構的設計與計算 13
4.8.1 定模頂出機構的設計 13
4.8.2 對合擺塊分模機構的設計 14
4.9 導向機構的設計 16
4.9.1 導柱設計 16
4.9.2 導套的設計 16
4.9.3 限位拉桿的設計 17
4.9.4 彈簧的選用 18
4.10 成型零件的結構設計 18
5 成型零件工作尺寸的計算 19
5.1型芯和型腔工作尺寸的計算 19
5.2 型腔側壁和底板的厚度計算 20
5.3 模具閉合高度的確定 20
5.3.1 模具支撐固定件的設計 20
5.3.2模具閉合高度的確定 21
6 注射機參數(shù)的校核 22
6.1安裝尺寸的校核 22
6.2注射壓力的校核 22
6.3鎖模力的計算 22
6.4模具的開模行程的校核 23
7 模具的工作原理及其特點 24
設計總結 25
參考文獻 26
Ⅱ
第一章 緒論
1 緒 論
塑料模具是對塑件進行成型的模具,是一種型腔模。制定出合理高效的工序流程、使用高效率的裝備設置、使用技術前沿的模具,這三個因素是保證塑料制品能夠順利生產(chǎn)的原因。特別是對于塑料模具,可以使得它成型的要求得到滿足,并且保證它的質(zhì)量,使得它的成本得到降低。那種產(chǎn)品的質(zhì)量足夠優(yōu)良的模具可以進行成型幾十萬次,有的時候都可以達到上百萬次。這個同模具的設計、選材、制造、和維護有著很莫大的關系[1]。
當一個模具在被使用的時候,需要能夠達到生產(chǎn)效率高、自動化程度高、操作簡易、使用壽命充足的要求;在模具制造的方面,需要做到結構設計合理、制造生產(chǎn)容易、成本低廉。
即使現(xiàn)在看來是有許多種的模具的,但是它如要要尋求發(fā)展的話主要還是不僅要能使得它較大的需求量得到滿足,比較高的技術含量在其中也是必不可少的。由此看來,有一部分比較重要的模具標準件也是需要當作重點來進行發(fā)展和開發(fā)的,并且在這個同時也要保證它的發(fā)展速度要比其他模具的發(fā)展速度更快,只有做到這樣,才能夠使得模具標準化的程度不斷的進行提高,從而可以從各個方面提高模具的質(zhì)量,使得它的生產(chǎn)周期得到縮減,生產(chǎn)的成本得到降低[2]。
本次設計的注塑模具主要從塑料的種類以及它的性能和這類產(chǎn)品的使用要求作為設計的出發(fā)點來進行相應的設計,主要介紹了所選材料性能、設計的模具結構及其原理以及相應零件的理論計算幾個方面進行了綜合闡述[4]。
1
1
第二章 塑件工藝分析
2 塑件工藝分析
2.1 塑件的分析
任務書中給出的塑件是一個帶提手的塑料桶蓋,在開始設計模具之前,需要先對要加工的塑料加工產(chǎn)品的性能需求作一個分析,例如產(chǎn)品的外形,構造,還有精確度的需求是什么以及這個產(chǎn)品的質(zhì)量要求。
1)塑件結構分析 這里要設計的是生產(chǎn)一個桶蓋的注塑模具,具體的形狀在下面已經(jīng)展示出來。從塑件的零件圖上可以看出,在這個零件中的球形曲面和提手部位組成了該零件的主要特征,并且可以發(fā)現(xiàn)在蓋的內(nèi)部位置是存在三處內(nèi)側凹的,從這點就要求需要給這個模具設計一個對應的用來進行側向抽芯的機構。如果想要能夠使得這三處的測凹和球形曲面的部位可以一起成型,并且只能通過一種組合式的型芯來進行產(chǎn)品的生產(chǎn)??梢悦黠@的看出來這個塑件算是一種不是特別簡單的類型了。
2)尺寸精度分析 因為考慮到這個塑件是屬于普通的日用品的,所以對于塑件的收縮率來說并沒有太高的要求,由此可以看來它的尺寸精度的相應的要求也不會特別的高,在這里大部分的情況下都是自由精度尺寸。最后再結合要選擇的材料的性能,可以將它的精度等級確定為4級。
結合所要生產(chǎn)的塑件的蓋壁厚度,進行分析后就可以知道:將提手的橫截面和桶蓋的蓋壁的厚度尺寸進行一個比較,可以看出是存在一定的不同的。通過查詢可以知曉PE的最小的壁厚是0.6mm。在這里就采取1.6mm作為它的壁厚,這樣的話就可以保證塑件的成型質(zhì)量,并且還可以把提手部位和蓋體之間的連接強度作一個加強。
3)塑件表面質(zhì)量的分析 在生產(chǎn)這個零件時,需要能夠保證在表型面上不會出現(xiàn)注塑不足、有毛刺等等情況。最后是要保證塑件在投入使用后是能夠滿足要求的,而在其他的地方并沒有什么特別的要求,因此想要滿足上面列出的這些要求并不難實現(xiàn)。
圖2-1、圖2-2分別為上文提及的塑件的三維立體圖和二維示意圖。
圖2-1 三維圖 圖2-2 示意圖
2
2
2.2所選的塑件材料及其特性
在選用這個產(chǎn)品的材料時要考慮到所選的材料是需要有一定的抗張力強度的,并且這種材料在當處于高溫情況的時候出現(xiàn)扭曲的時候的臨界溫度要求是比較高的、在熔融的狀態(tài)下粘性也是需要比較高的,并且要能保持它的化學層面的穩(wěn)定。綜合考慮下最后選用了HDPE作為塑件的材料。這種材料在高溫或者低溫環(huán)境中都可以繼續(xù)的保持它的各種特性,并且剛性和韌性都是能滿足塑件的要求。但是它也有缺點,就是這種材料不透氣、也不吸水,老化現(xiàn)象也會很快出現(xiàn)。
在材料使用前需要做一次收縮率的測定,但是有很多參數(shù)會影響到收縮率,所以在確定的時候是需要把塑件的很多參數(shù)加入考慮范圍的。
通過相應的資料可以知道這種材料的收縮率的范圍是:,可以選取它的平均值來作為計算值,即這個材料的收縮率可以定為2%。
27
第三章 注射成型布局及注射機的選擇
3 注射成型布局及注射機的選擇
3.1塑件體積質(zhì)量的估算
由三維軟件的測量可以知曉塑件的體積,塑件具體的尺寸可以參考圖3-1
1)塑件體積的計算
塑件體積:cm
2)塑件質(zhì)量的計算
這種材料的密度:/cm
那么計算可以得到:cm×cm=
圖3-1
3.2注塑機的初次選擇
所選材料的體積膨脹率的校正系數(shù)c經(jīng)過查閱可以知道是
那么就可以計算出cm 。
可以首先把這個塑件在成型的時候所需要的最大的注塑量先計算出來,因為在這里澆注系統(tǒng)這個部分占有的質(zhì)量部分還是不清楚的。所以要對塑件真正的質(zhì)量值作一個修正。在這里將修正值可以定為。
由相關資料可以知道實際注射量是應該小于0.8倍公稱注射量的,
由公式是可以計算出需要的最大注塑量的
g
在選擇注射機的時候根據(jù)的原則可以暫時選則型注塑機。
這個注射機的具體參數(shù)可以參見下表3-1
表3-1 注塑機參數(shù)
螺桿直徑/mm
50
理論注塑容量cm3
250
注塑壓力MPa
147
鎖模力KN
1800
模板行程mm
500
模具最小厚度mm
200
模具最大厚度mm
350
定位孔直徑mm
100
噴嘴球半徑mm
18
噴嘴孔直徑mm
4
結合實際情況這個模具是采用一模一腔的模具結構的。
第四章 注塑模具的結構設計
4 注塑模具的結構設計
4.1 型腔數(shù)目的確定
在注塑模的型腔數(shù)目準備進行確定的時候,不但有一模一腔的形式可以用于選擇,一模多腔的形式也是可以加入考慮范圍的,但是要注意的是,這幾個重要的前提在確定數(shù)目之前是必須要得到滿足的。
(1)塑件的尺寸精度;
(2)模具制造成本;
(3)生產(chǎn)效益;
(4)模具制造難度。
塑件制造的難度和生產(chǎn)時候的效益的要求決定了型腔數(shù)目的多少。制造時候的難度又主要是因為在進行注射的時候模具的鎖模力、熔融材料塑化能力、注射機的注塑量能否滿足生產(chǎn)的需求、塑件的尺寸的大小、精度要求的高低等也對型腔數(shù)有著一定的限制。
從這個塑件來開始分析,從這個塑件的結構看來,塑件蓋壁厚度的范圍相差是比較大的,所以這個結構算是比較復雜的,從而使得各個部分的加工工藝之間的差異還是很大的,所以為了保證塑件在質(zhì)量方面不出現(xiàn)問題,那么塑件的在進行成型時候的工藝就必須要得到嚴格的控制。
因為這個塑件的結構比較特殊,所以即使塑件對精度方面的要求不是很高,但是為了方便在生產(chǎn)的時候進行抽芯以及之后的脫模過程可以順利的進行,最終選擇了一模一腔結構形式來進行生產(chǎn)。最重要的原因還是當選擇一模多腔的結構形式時,不但不能保證塑件的在成型時不會出現(xiàn)問題,也會讓模具的結構變得更加的復雜,這樣就變相的使得模具的生產(chǎn)成本大幅度提高。
綜合多方面的因素,該塑件在生產(chǎn)時采用一模一腔的設計。
4.2 制件位置的確定
塑件在確定它在模具中的位置的時候需要考慮到以下的方面:
塑件及其配件的主視圖應該和它選擇的注塑機的軸線呈對稱分布在兩邊,這樣的話塑件成型會更加容易。
一個塑件所選取的位置是要能夠利于這個塑件進行脫模操作的,當開模后,塑件最好應該留在動模上,這樣的話進行脫模就會更加的方便。最后在位置確定之前也要仔細考慮到所選用的澆注系統(tǒng)和溫度控制系統(tǒng)的布置形式??梢园凑丈衔牧信e出來的原則,并且結合這個塑件的成型特點來最終確定的它的位置,具體的布置可以參見模具的總裝圖。
4.3 分型面的設計
4.3.1分型面的選擇原則
(1)脫模方便;
(2)外觀無損壞;
(3)便于排氣方便加工;
(4)方便抽芯;
4.3.2 分型面的形式選擇
在選擇分型面之前要考慮到的因素有很多,例如產(chǎn)品的具體結構、處理時的工藝手法、產(chǎn)品的質(zhì)量要求等等,另外所選擇的模具的種類、脫模時使用的方法,型腔的數(shù)目、模具進行排氣的方式、澆口的位置及其形式等各種因素也是會對它造成一定的影響的。
結合該模具的結構特點從而開始分析該模具應該如何選取它的分型面。這個模具的主分型面是準備采用水平分型,但是因為這個塑件的結構不同于其它零件,設計時考慮到為了讓塑件能夠順利的從各個型芯上完成脫模的動作,并且與此同時也能夠保證模具中的其它的機構也能夠順利的運行下去,決定輔以其它兩個分型面來作為輔助。
4.3.3 分型面的位置選擇
綜合各個方面考慮,這個塑件有一個提手處,并且是一個半球型,而且塑件其它地方?jīng)]什么特別的要求,將這些因素綜合起來就可以將主分型面的位置確定出來。
其他兩個起到輔助作用的分型面的具體位置及主分型面的位置可以從裝配圖中查得。
按這樣的方法設計的三個分型面不僅可以使得模具的結構的變得簡潔方便,還可以降低模具在加工時候的難度并能夠保證塑件在脫模時能夠順利。
4.4 排氣系統(tǒng)設計
在塑料熔體開始對型腔進行注射時,在這個過程進行的時候,模具里原本就存在在里面的空氣加上塑料熔體在受熱時產(chǎn)生的氣體是必須要排出去的。如果這些氣體一直在型腔里面,不被排出去的話,就會導致熔體填充不足,從而使得塑件表面會出現(xiàn)一些氣泡,嚴重的話也會發(fā)生出現(xiàn)大接縫和表面輪廓不清楚等等諸多缺陷,有些時候甚至會出現(xiàn)因為高壓氣體產(chǎn)生的高溫從而導致塑料發(fā)生焦化。
因為考慮到這個模具的具體結構是鑲拼式的型腔結構,所以可以通過拼鑲件的縫隙來將氣體排出,另外,這個模具是有三個分型面的,也可以充分利用來進行排氣。在保證制件的成型質(zhì)量沒有問題的前提下,排氣方式已經(jīng)足夠了。因此不需要設置額外的排氣槽來進行排氣。
4.5澆注系統(tǒng)的設計及計算
4.5.1 澆注系統(tǒng)的設計原則
1)排氣要良好,這樣可以避免熔融塑料在對型腔進行填充的時候會產(chǎn)生渦流和紊流,于此同時型腔里的氣體也是能夠順利的排出。
2)在能夠保證使得塑件成型順利并且排氣良好的前提下,填充型腔的時候盡可能選擇短的流程,最好使彎折數(shù)目盡量的少,這樣就可以使得壓力損失減少,填充的時間減少;
3)需要避免熔融塑料和小直徑的型芯和金屬嵌件之間發(fā)生正面的沖擊,這樣就可以避免發(fā)生型芯彎曲變形或者嵌件位移的現(xiàn)象[4]。
4)澆口的位置和規(guī)格要與塑件的形狀結構相結合來進行考慮,這樣就可以方便以后的修理和維護。
5)澆注系統(tǒng)的截面面積和長度決定了澆注系統(tǒng)浪費的材料的數(shù)量,所以要盡量的縮小,這樣就可以減少材料的浪費。
4.5.2 澆口與主流道的選擇與設計
因為這個模具選擇的結構是一模一腔,所以不需要設置分流道。
因為塑件是比較大并且壁厚算是比較薄的,所以準備選擇直接澆口作為這個模具的澆口。因為是一模一腔的結構,所以在生產(chǎn)的時候流程比較短、成型就會很迅速,還能減少壓力的損失。但是這種方式也有一些缺點,因為澆口地方熔體固化會慢一些,這樣的話塑件成型的時間就會相應的延長,殘余應力就會很大從而使?jié)部诘牡胤疆a(chǎn)生裂紋,并且澆口凝料在切除后制件上疤痕也會很大[6]。
4.5.3 主流道設計
主流道是將注塑機噴嘴和分流道互相銜接的一段通道,和注塑機的噴嘴是在同一條軸線上的,橫截面是圓形的,并且是有一定量的錐度的,這個的目的主要是讓冷料在脫模時更加方便,同時也可以改善料流的速度。主流道是需要與注塑機互相配合的,所以它的尺寸大小由注塑機來決定[10]。
型注塑機噴嘴的尺寸參數(shù):
噴嘴前端孔徑
噴嘴前球面半徑
由模具主流道與噴嘴之間的關系可以知道,
主流道的球面半徑
小端的直徑
這樣的話就可以將主流道的球面的半徑和小端直徑確定,分別為,。
在它的長度是比30mm大的時候,可以把大端的直徑定為。那么主流道的設計草圖如圖4-1所示:
圖4-1
4.5.4主流道襯套設計
為了防止在受到熔體反壓力的時候,襯套被推出定模的意外會出現(xiàn),在這里選擇使用B型襯套,具體的結構可以參考圖4.2。
圖4.2.
4.5.5主流道定位環(huán)設計
用來確定直澆口式的主流道的位置的裝置的設計可以參考圖4.3,它的尺寸可以參考注塑機上的用來定位的孔和定模上的用來定位的孔從而來進行互相配合。
圖4.3
4.6 側抽芯機構的設計與計算
在這個設計中,塑件在側面蓋壁的地方是存在三處內(nèi)側的凹進結構的,并且這幾個內(nèi)側凹進的結構都是與脫模的方向呈垂直關系的,并且因為這個塑件的蓋壁的厚度是十分的薄的,而且考慮到在這個模具中,空間是不能夠滿足發(fā)生彈性形變的,因此不能采用強制脫模的手段,最后決定專門來設計一個進行側向抽芯的機構來完成抽芯。由于這個塑件的結構是不同于其它一般的塑件的,如果選擇使用斜導柱機構來進行抽芯的話會就受到一定的限制。所以最后斜滑塊被選中來進行這個抽芯的工作。這里是通過使用開設過導滑槽的滑塊和主型芯進行相互的協(xié)作才得以順利完成抽芯的動作。這種機構的抽芯動作是在塑件的脫出的時候和它一起進行的,并且如果選擇斜滑塊的話,它的剛性一定是比較大的,所以和斜導柱相比較而言,傾斜角可以變得大一些,但是要注意這個角度是需要小于26°的,為了保證在使用時足夠可靠,這種斜滑塊的頂出高度理論上是要小于導滑長度的2/3的[10]。
4.6.1 側抽芯機構的參數(shù)計算
⑴ 抽芯距的確定
臨界時候抽芯的距離可以通過斜滑塊的零件圖來進行確定 。
臨界抽芯距的計算公式 :
那么設計抽芯距:
⑵ 抽芯力的計算
可以通過計算抽芯力的公式:
公式中的具體參數(shù):
型芯被塑件包緊的截面的形狀周長
型芯成型部分的高度
單位面積上型芯所受到的來自塑件的包緊力可以定為,
在這里可以最終取值10Mpa
塑件材料和模具材料之間的摩擦系數(shù) 取0.2
側面凹處的脫模斜度
通過上述的參數(shù)就可以用公式計算出抽芯力
⑶ 滑塊的傾斜角度
在這里可以將滑塊的傾斜角度取為。
4.6.2 滑塊的結構設計
⑴ 滑塊的形式設計
為了能夠使這個塑件的內(nèi)側凹進的結構能夠順利成型是采用斜滑塊進行抽芯的初衷,因為在這里這種塑件的內(nèi)部的側凹是很淺的,并且可以知道抽芯距也很小,并且為了能夠抽芯,斜滑塊是需要具有一定的強度的,同時它還要作滑動的運動,最后決定把滑塊制作成一個整體。
⑵ 滑塊的導滑方式
可以在主型芯上制作相應的導滑槽來為斜滑塊起到導向的作用。一個良好的導滑系統(tǒng)是需要能夠保證整個導滑機構的結構緊湊并且不會出現(xiàn)材料溢出的情況的,為了做到這一點,那么對于滑塊和導滑槽之間的加工精度就有了很高的要求,這就需要采用合適的工藝手法來達到使用的要求。
4.7 模具加熱與冷卻系統(tǒng)的設計
在對這個塑件進行注塑的時候是不需要特別的高的溫度的,因此在這里加熱系統(tǒng)就不需要設置了。但是因為考慮到這個塑件在進行注塑的時候熔料需要鋪滿的地方是挺大的,這樣的話各個部分的材料一定會發(fā)生分布不均勻的情況,為了避免這個現(xiàn)象出現(xiàn),加入一個冷卻系統(tǒng)就是必不可免的需求。
開始的時候可以先憑借經(jīng)驗將工作時候的溫度先設置成,用來進行冷卻的介質(zhì)則可以選擇使用水。
4.7.1 冷卻系統(tǒng)的參數(shù)計算
⑴ 單位質(zhì)量的熔融材料放出的熱量
其中所選材料的比熱容經(jīng)過查閱可以知道是。
熔體在進行對模具填充時候的溫度取,
塑件在被推出的時候的溫度取,
所選材料的熔化質(zhì)量焓為
那么計算可得
那么總共產(chǎn)出的熱量
m =0.07kg(前文已經(jīng)確定)
綜上,經(jīng)過計算Q的值確定為
⑵ 沒有擴散到空氣的熱量
⑶ 冷卻管道總的熱量傳導面積的計算
公式內(nèi)參數(shù)確定:
熔體在進入模具時候的溫度與冷卻液之間溫度的平均差值取為。
選擇的用來冷卻的液體和管道孔壁之間的熱傳導系數(shù)可以 通過公式來確定。
在這個公式中,經(jīng)過參考一些資料,冷卻管道的直徑可以將它定為,其中冷卻液體在里面的平均流速可以取為。
因為所選用的介質(zhì)是水,查表可以知道
綜合上述可以知道=。
那么可以由此算出=。
⑷ 冷卻管道的孔數(shù)
通過公式可以知道
。 需要布置兩條冷卻管道。
4.7.2 冷卻水道的布置
要生產(chǎn)的塑件的形狀和塑件在各個不同位置的壁厚無時不刻的影響冷卻管道的位置。正因為是冷卻管道,所以就應該在模具散熱困難的地方進行布置,這樣將所要成型的塑件的周圍都用冷卻管道圍繞起來,并且將它排列均勻就是一種很好的布置方式[14]。
因為這個模具的結構是拼鑲而成的,并且正是在這個鑲件上,塑件進行了成型,所以這樣的的鑲件是不適合再加工冷卻管道的,最后是決定按照圖4.4所示的樣子進行了相應的布置:
圖4.4
這樣的話就可以把兩條直通式的冷卻水道設置在動模的套板上。
4.8 脫模機構的設計與計算
這個塑件因為提手部分的結構是不同于其它一般的結構的,最后只能通過驅(qū)動連桿來讓兩個半球型的活動型芯完成脫模。另外為了能夠保證塑件能夠從定模的主型芯上順利完成脫模,這里選擇了推件板定模頂出機構。在定模頂出系統(tǒng)工作時,它的開模行程必須嚴格控制,防止當開模行程太大時使得動模與定模頂出裝置之間的拉桿發(fā)生斷裂。
在使用上述的系統(tǒng)的時候,為了避免廢料比例增加以及成型中壓力損失太大的問題,在主流道較長時可以加長噴嘴從而深入模具的內(nèi)部進行注射的方法,這樣就可以變相的讓主流道的長度變小。
4.8.1 定模頂出機構的設計
1)脫模力的計算
為了方便計算,先暫時將主型芯上滑動鑲塊的作用放在一邊,這樣能夠方便的對該塑件進行更加詳盡的受力分析??梢粤谐鱿鄳钠胶夥匠?,具體可以見圖4.6。
方程參數(shù):摩擦力為F 為脫模力,為包緊力 摩擦系數(shù)為 脫模斜度=。
其中
將定為0.2,則包容面積A=10790.7 , 單位面積包緊力p可以定為10Mpa。
通過公式計算得
=20643.7N。
圖4.6
2)推件板厚度的確定
可以通過公式來進行相應的計算。
通過手冊的查閱,推件板變形量定為
E彈性模量取為
取為450mm
B取400mm。
有上述數(shù)據(jù)可以計算出推件板厚度為t=30.8mm。
3)定模頂出機構的工作行程
這個頂出機構的目的就是使得塑件在脫離主型芯時能夠順利,與此同時還必須要完成內(nèi)抽芯這項工序,最后主澆道還要能夠自動脫落.為了達到以上目的,所以必須精準的確定開模行程.根據(jù)上文確定的主澆道的長度和塑件的總體的高度的數(shù)據(jù),初次把開模的行程定為80mm,如果有什么不合適的地方,將會在之后的設計再度進行相應的調(diào)整。
4.8.2 對合擺塊分模機構的設計
在塑件把手的地方那里內(nèi)凹的球面和把手部分是由兩個對合的擺塊型芯進行相應的成型工藝的,當工作的時候按照圓弧形的軌跡擺動就可以進行抽芯動作,根據(jù)這個道理設計出了由擺塊型芯、軸、擺塊座和連桿一起組成的圓弧抽芯機構。
這種類型的抽芯機構進行橫向的分模抽芯的工作主要是通過驅(qū)動兩瓣活動的型芯進行轉(zhuǎn)動才得以進行.在工作時,這個機構開始先通過彈簧從而使得這個模具在首先分型前先后移楔柱,從而使得連桿和半球形的活動型芯得以運行,具體動作就是半球型的活動型芯圍繞著軸再向著兩側外開始擺動從而得以完成橫向的分模和抽芯工作。
這類機構在工作的時候會受到很多因素的影響,因此很多的數(shù)據(jù)很難精確的確定下來。其中最關鍵的參數(shù)就是開模的方向上連桿此時的距離L。這個距離要保證兩型芯是可以順利脫離半球型的曲面并使得提手部位的分模過程順利完成。L具體的距離可以參考相應的的動作示意圖4.7。
兩個活動型芯在模具開模的方向上的臨界狀態(tài)下的運動的距離
兩個活動型芯在進行橫向的抽芯的時候在臨界狀態(tài)下的距離b
圖4.7
通過以下關系式:
=R-h
b= Rsin h=Rcos
其中公式中的參數(shù)通過測試可以確定大約為。型芯的工作公稱尺寸就可以作為半徑R的尺寸,即為62.9mm。
綜合以上通過計算可以確定出
那么L取值可以大約取為35mm。并且連桿在開模方向上的運動距離L是需要略微小于分型面的開模距離的,這樣的話它就可以和限位拉桿的限位距離互相對應了。即可去的開模行程取為42mm。
最后楔柱的作用也是很重要的,它不僅起到了鎖緊作用還起到了定位的作用。這樣可以充分避免制件在成型的時候出現(xiàn)質(zhì)量問題甚至缺陷。所以楔柱的圓錐形狀頭部也要能和半球型芯上的錐形孔的尺寸能夠相互對應。具體尺寸會在零件圖中給出。
4.9 導向機構的設計
通常通過導向機構就能夠使那種精度要求不是太高的模具的動、定模之間的位置確定變得準確。導向機構主要分為導柱導向和錐面導向定位兩種方法,該設計采用的是導柱導向[14]。
4.9.1 導柱設計
考慮到導柱自身的配合直徑d和模板的尺寸,最后決定將為動模推件板導向的導柱定為的標準直形導柱。
它的標準參數(shù)值取d=㎜,㎜ ㎜ ㎜
再綜合上該模具的上模部分的高度,選擇㎜mm。選擇T8A作為它的材料。
此外整個模具的導向系統(tǒng)則可以選擇d=40mm的直導柱來進行導向,可以通過總裝圖來知道它的具體結構,它的尺寸參數(shù)如下:d=㎜,㎜ ㎜ ,考慮到方便固定所以取S=85㎜,最后綜合上述內(nèi)容,將模具的總高度L定為315㎜。
具體結構見下圖4.8:
圖4.8
4.9.2 導套的設計
因為為了能夠和導柱進行配合,所以選擇了相應的標準導套。它的結構與尺寸經(jīng)過查閱可以確定下來:在這里可以選擇帶肩導套I型。詳情如圖4.9
圖4.9
它的標準參數(shù)值可以這么取 ㎜ ㎜ ㎜ ㎜ ㎜㎜ ㎜ R=1.5 ㎜
因為要保證導柱在上下模的導向精確,所以選擇和所選的d= 40㎜的導柱互相配合的導套,它們的共同參數(shù)分別為 ㎜ ㎜ ㎜ ,那么各個導套的長度通過模板厚度來確定,分別可以選擇為:㎜,㎜,㎜,㎜。
因為定模具頂出機構是這個模具所采用的頂出結構,這樣在開模的時候推件板和墊板都需要使用導柱,從而起到導向的作用,因此對應的中間軸套需要為導柱來進行相應的設計。因為它的配合直徑尺寸和之前的導套尺寸是一樣的,并且它的長度和推件板加上墊板的厚度總和是一樣的,就不再多說。
這個模具的導柱在布置的時候就是選用四根直徑相同的導柱然后把它們呈對稱布置,并且為頂出機構起到導向作用的導柱也是按找對稱來進行分布的。動模板零件圖上展示了它具體的布置和尺寸[14]。
4.9.3 限位拉桿的設計
如圖4.10所示,可以通過使用模板的厚度來進行將限位拉桿的長度確定,此外,開模行程會對整個限位的距離來做出限制。在該設計中,可以將動定模的上限位拉桿的長度可以分別確定為和。直徑d取為,D取為。
圖4.10
4.9.4 彈簧的選用
這個模具在進行首先分模時使用了彈簧作為限制,參考到彈簧在模具中大概會受到的沖擊次數(shù)是在次之間,并且結合與它所配合的限位拉桿的直徑,最后決定選擇使用直徑=38mm的標準彈簧。
彈簧的其他參數(shù):
彈簧絲的直徑d=4.5mm
節(jié)距t=12.9mm
最大的工作負荷=
最大工作負荷的時候單圈的形變=。
4.10 成型零件的結構設計
該模具的工作零件分為半球狀型芯、主型芯和動模鑲件這幾個零件。
⑴ 動模鑲件的設計
因為考慮到是否方便加工和能否不浪費材料等因素,這個模具的凹模選擇了鑲嵌式結構。
⑵ 凸模設計
這個模具中的半球形狀的型芯、 主型芯 、抽孔型芯以及滑塊型芯都是凸模類零件的一部分。其中半算是比較復雜的結構就是球狀型芯的結構了。并且需要考慮到滑塊型芯和主型芯導滑槽之間的需要做到高配合,在進行加工的時候它們的精度是十分需要得到保證的。
第五章 成型零件工作尺寸的計算
5 成型零件工作尺寸的計算
由前文計算可以知道已經(jīng)確定了所選用材料的收縮率為。再考慮到所要成型的零件的尺寸與塑件的尺寸精度公差的關系,取模具的制造公差。
5.1型芯和型腔工作尺寸的計算
具體的計算過程見表5.1。
種 類
零件名稱
塑件的尺寸
計算公式
零件的尺寸
型
腔
計
算
動
模
鑲
塊
型
芯
半
球
型
芯
型
腔
計
算
型
腔
主
型
芯
型
芯
型
芯
抽
孔
型
芯
滑
塊
型
芯
表5.1
5.2 型腔側壁和底板的厚度計算
1)動模鑲件側壁和底板的厚度計算
動模鑲件型腔可以看作是一個整體式的圓形型腔,
通過能夠計算整體式型腔壁厚的公式
參數(shù)說明:模腔壓力?。ǎ?,那么取=;
動模鑲件所選的材料是鋼,材料的=。
那么綜上可以得出:=35.3。
通過底板厚度的計算公式
計算得出底板厚度是34.4㎜。
因為模具中不單單只有這些零件安裝,還有其他零件也需要進行安裝,所以最終將動模鑲件的外形的尺寸確定為210mm
2)動模鑲件提手部位的側壁厚度計算
通過上述公式
可以計算得提手部位的側面蓋壁的厚度為6.5mm,并將其整取為10mm。
5.3 模具閉合高度的確定
5.3.1 模具支撐固定件的設計
因為前文已經(jīng)將各個機構的活動空間的尺寸參數(shù)和工作零件的尺寸參數(shù)已經(jīng)確定,那么就可以來確定模具的支撐與固定件的尺寸參數(shù)了。通過查閱相關資料,可以選擇的標準模板,材料則選擇為Q235鋼。
在能夠保證圓弧抽芯的分模機構能夠順利工作的前提之下,可以將模具的定模固定板厚度定為63㎜,此外考慮到動定模的座板的厚度在確定的時候需要滿足的原則,一是能夠在進行裝配時滿足各個需要,二是能夠使用的時候強度能夠達到需求,這就意味著需要在進行加工或者工作時不發(fā)生變形(鎖模時受壓力,開模時受拉力)。
可以通過分析所得,開模的時候受拉力,所以各個螺釘?shù)乃闹苁艿郊羟辛?,此時機床的壓板和螺釘便會和模板進行對拉從而造成彎曲,如此便可以根據(jù)這個原則進行相應的計算。顯然當模板的面積越大,它的厚度越厚,在這里可以將定模座板的尺寸確定出來,即=40㎜,動模座板的=25㎜。
在這里它外形的尺寸就可以定成,由此可得它的其它的模板尺寸也可以確定為。以及定模墊板=20㎜,定模的推件板=30㎜(已定)。通過這些零件的具體的裝配要求可以確定出標準模板厚度,取為=80㎜ ,在能夠使得圓弧抽芯機構順利運行的前提下可以確定動模墊板的尺寸,即=。
綜上模板的具體結構、尺寸以及公差精度方面的要求,可以參照相應的零件圖。固定件則可以通過模具的外形尺寸來選用相應的標準螺栓。
5.3.2模具閉合高度的確定
綜合上文所述可以計算出模具的閉合高度:
H=++++++
=40+20+30+80+80+63+25
=338㎜
第六章 注射機參數(shù)的校核
6 注射機參數(shù)的校核
6.1安裝尺寸的校核
通過上文可以了解到,該模具的外形尺寸可以定為。型注塑機的模板的最大安裝尺寸為,所以可以使得模具的安裝要求得到滿足。
通過上文可以計算出模具在閉合時的高度,型注塑機能夠允許的模具的最小厚度=,最大厚度=,這樣就可以確定模具是滿足安裝條件的。
6.2注射壓力的校核
經(jīng)過相關資料可以知道,HDPE在注射時的壓力一般在到之間,而所選注射機的公稱注射壓力為,現(xiàn)在可以將它的安全系數(shù)取為,那么計算可以得出K1×=91Mpa-136.5Mpa<,于是注射機壓力是滿足條件的。
6.3鎖模力的計算
開模為了防止有溢料這種情況出現(xiàn),設計準備選擇的這個注射機的鎖模力一定比它的型腔里產(chǎn)生的壓力所導致的開模力要大。分析可得影響鎖模力最主要的原因就是塑件在模具分型面上的投影面積的大小[14]。
通過公式
式中參數(shù):--注射時型腔壓力 經(jīng)過查閱相應的參考文獻取其為
--塑件在分型面上的投影出來的面積()
--澆注系統(tǒng)在分型面上的投影出來的面積()
--注射機的額定鎖模力,按型號的注射機 那么額定的鎖模力為
計算可得塑件及澆注體系在分型面上投影出來的面積為
那么經(jīng)計算可得 176.7 cm2 ×110MPa = 1767KN<1800KN
因此可以確定注射機的鎖模力是合格的。
6.4模具的開模行程的校核
通過前文可以知道塑件與主流道的總長度是80㎜,其中一個分型面的開模行程為42㎜,主分型面的開模行程可暫時定為35㎜。并且可以知道型注塑機的最大開模行程=。
=80+35+40+10
=165㎜
此外考慮到在進行側分型的時候抽芯距對模具的行程的影響是很小的,由此看來所選注塑機的開模行程是足夠的。
綜上所述,型注塑機是可以讓使用要求的得到滿足的。
第七章 模具的工作原理及其特點
7 模具的工作原理及其特點
在這個模具開始開模時,動模先往后開始進行移動,通過彈簧的作用,其中的分型面Ⅰ開始進行第一次的分型運動,在運動開始后,楔柱不再保持鎖緊狀態(tài)。在分型的距離足夠的時候,連桿使這個時候就會配合固定板和軸來驅(qū)使兩個半球型的擺塊型芯繞軸轉(zhuǎn)動,從而可以完成圓弧抽芯的工序。分型面Ⅰ的分形過程在定距拉桿與擋片限位之后結束這個過程。
隨即分型面Ⅱ開始它的分型動作,這個時候塑件開始脫離動模鑲件的型腔,最后塑件是停留在定模上的。分型面Ⅱ它的第一次的分型在當擺鉤成功拉住凸塊的時候結束。
在此之后開始分開分型面Ⅲ,這個時候塑件開始被定模推板推動從而得以脫離型芯,同樣的在這個時候斜滑塊就同時順著型芯的斜向燕尾槽作滑行運動從而得以完成內(nèi)側抽芯的動作。當分型面Ⅲ分型結束的時候需要擋片對定模推板有一定的限制。當動模在進行運動的時候會產(chǎn)生拉力,這個拉力可以通過擺鉤和凸塊斜面之間的相互作用,可以讓兩個擺鉤圍繞各自的銷軸螺釘并且與此同時也可以往鉤子段所張開的方向開始進行擺動的動作,這樣的話彈簧就會被壓縮,最后擺鉤和凸塊就會被強行的分離,這樣的話分型面Ⅱ就可以開始它的第二次的分型動作,在這次分型到位后就可以將塑件和流道里的凝固的原材料取出來。在擺鉤和凸塊分離之后,通過彈簧和固定在動模套板上的限位銷可以把擺鉤的位置限定住。
在這個模具進行合模時,三個分型面按照Ⅲ、Ⅱ、Ⅰ的順序依次閉合,擺鉤可以擺動直到越過凸塊后就可以復位,這個同時斜滑塊也可以復位,之后兩個半球型的擺塊型芯也隨即復位閉合,楔柱在這個時候?qū)⑺i緊。
這個模具的最主要的特點就是在定模上設置的那三個斜滑塊可以將塑件的那三處內(nèi)側凹槽得以成型;在動模上也是同樣的,設置了用于將塑件的半球型內(nèi)凹和提手部分進行成型的對稱的半球型的擺塊型芯,這對型芯可以按照圓弧軌跡進行擺動從而可以進行抽芯動作。整個模具結構不臃腫、工作方便靠得住,是可以達到全自動工作的目的。
設計總結
設計總結
經(jīng)歷過這次畢業(yè)設計,我了解到了關于模具方面的許多綜合知識,也彌補了自己在這一方面知識的欠缺。特別是對很多的理論知識有了更深層次的認識。也是對當初所學習的知識進行了一次匯總。最重要的是使得我收集、整理和運用各方面資料的能力得到了提高,并且使得我們獨立思考和解決問題的能力的得到了全面的培養(yǎng)和提高。設計中所需要使用的一些繪圖軟件也讓我對它們更加熟練的掌握。畢業(yè)設計的完成不僅可以培養(yǎng)了我各方面的綜合能力,還讓我了解了更多的知識并且熟練了許多軟件設備,這是一次綜合的全面考察,為將來以后的工作作出了充足的準備。
回想起整個設計過程,在模具設計方面我有以下總結:
對于模具的結構要合理選擇,記得要適應所選材料的成型特性。這是設計出在布局方面較為合理,質(zhì)量方面十分可靠,容易操作的模具的前提。
模具成型零件的尺寸以及各個方面都對所要生產(chǎn)的塑件的形狀,尺寸和表面質(zhì)量有著很重要的影響,這是不能忽視的。
設計時要做到制造方便,并且盡可能的節(jié)省材料,從而保證工件的經(jīng)濟性和設計的合理性相結合。
設計開始前要充分考慮到塑件的結構上的特殊之處。盡可能減少澆口,溢邊的尺寸,減少后加工量。
設計時要考慮到模具的效率,可靠性以及壽命。
參考文獻
參考文獻
[1] 馮剛, 張朝閣. 三種不同類型注塑模具的特點與發(fā)展現(xiàn)狀[J]. 工程塑料應用, 2013, 41(7): 11-15.
[2] 2013-2018 年中國工程塑料市場供需預測及投資前景研究報告. 中企顧問網(wǎng).
[3] 江健. 淺析注塑模具發(fā)展[J]. 廣西輕工業(yè), 2011, 11(7): 2-5.
[4] 楊永順. 塑料成型工藝與模具設計[M]. 北京, 機械工業(yè)出版社, 2011.
[5] Mok C, Chin K. Ho, J. K. L. An interactive knowledge-based CAD system for mould design in injection moulding processes [J]. The International Journal of Advanced Manufacturing Technology, 2001, 17 (1): 7-12.
[6] 王孝培. 塑料成型工藝及模具簡明手冊[M]. 北京, 機械工業(yè)出版社, 2000: 87-92.
[ 7 ] 趙軍 . 注塑模具結構分析與優(yōu)化方法研究 [ D ] . 上海: 上海交通大學,
2011.
[8] 周利民. 塑料模具的現(xiàn)狀與發(fā)展[J]. 中國模具信息, 2009, 12(10) : 4-5.
[9] 金鵬. 模具設計中 CAD/CAE/CAM 綜合應用的研究[D]. 保定: 華北電力大學, 2013.
[10] 高軍, 李熹平, 高田玉, 褚興榮. 注射成型工藝分析及模具設計指導[M]. 北京:
化學工業(yè)出版社, 2009: 1-23.
[11] 林權. CAD/CAE技術注塑模優(yōu)化設計[J]. 重慶工商大學(自然科學版), 2012. 29(7):
11–16.
[12] 張孝民. 塑料模具技術[M]北京, 機械工業(yè)出版社, 2004: 3-12.
[13] 石峰. 基于軟計算的注塑模智能設計系統(tǒng)關鍵技術研究[D]. 上海: 上海交通大學,
2003
[14] 楊化林. 基于知識的注塑模具設計若干技術研究[D]. 杭州: 浙江大學, 2006.
[15] 齊衛(wèi)東. 簡明模具設計手冊[M]. 北京, 北京理工大學出版社, 2008: 8-9.
[16] J. Y. H. Fuh、Y. F. Zhang、A. Y. C. Nee、W. Fu. Computer-Aided injection Mold
Design and Manufacture[J], 2010: 18-29.
[17] 李雯雯, 盧軍, 劉洋. Moldflow 軟件在注塑模具 CAE 中的應用[J]. 工程塑料應用 , 2009, 37(9): 2-6.