【溫馨提示】壓縮包內(nèi)含CAD圖有下方大圖片預覽,下拉即可直觀呈現(xiàn)眼前查看、盡收眼底縱觀。打包內(nèi)容里dwg后綴的文件為CAD圖,可編輯,無水印,高清圖,壓縮包內(nèi)文檔可直接點開預覽,需要原稿請自助充值下載,所見才能所得,請見壓縮包內(nèi)的文件及下方預覽,請細心查看有疑問可以咨詢QQ:11970985或197216396

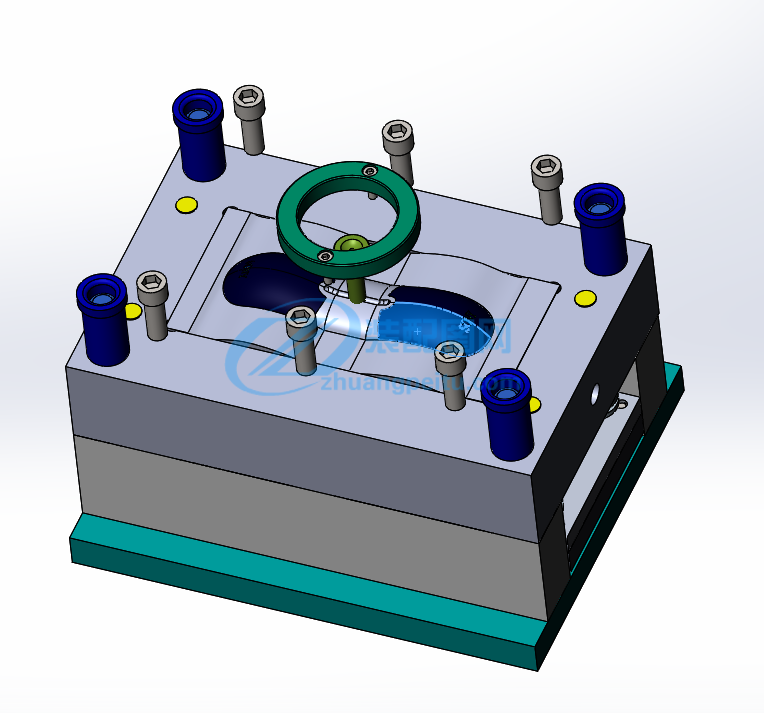
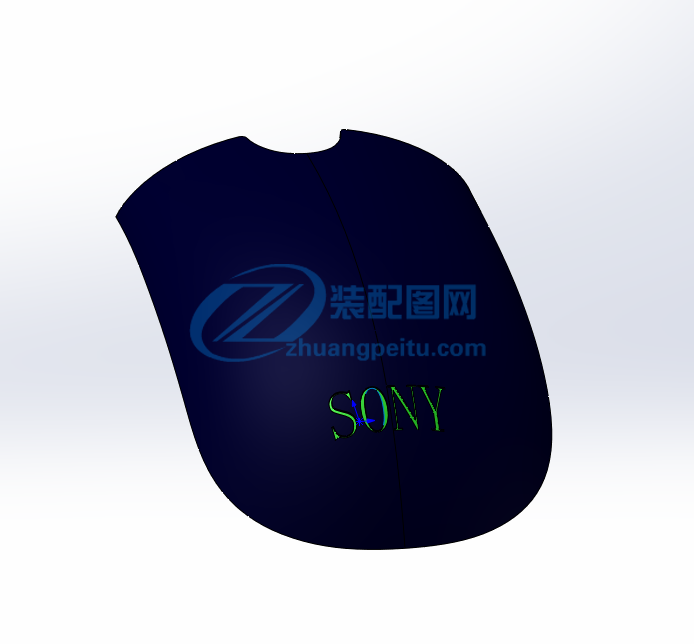
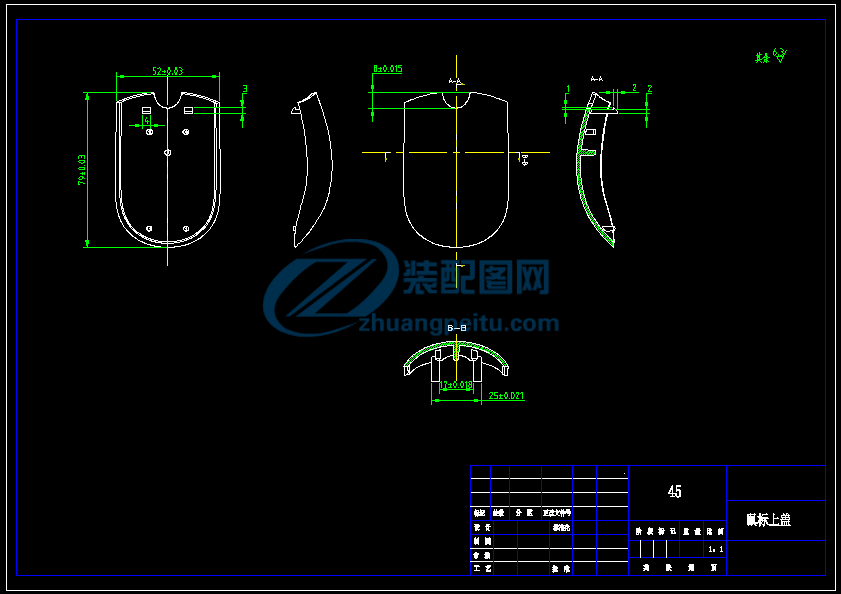
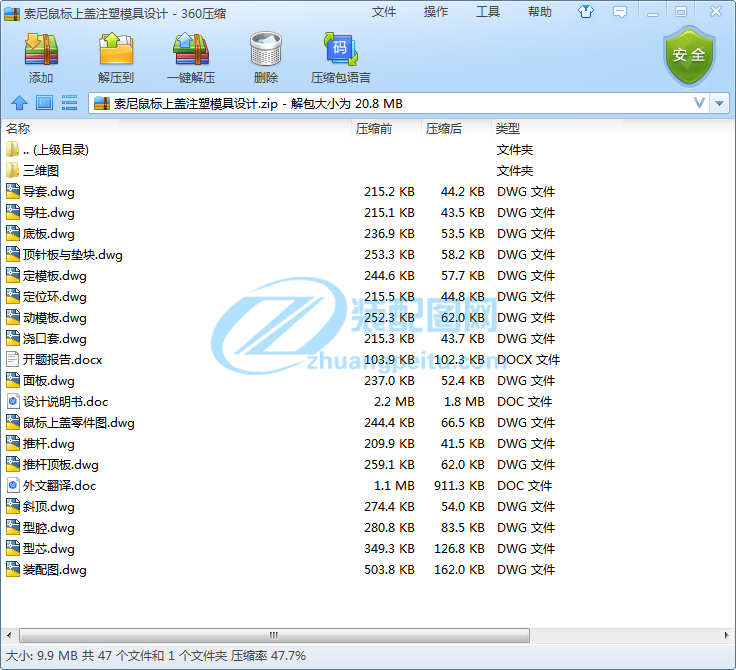
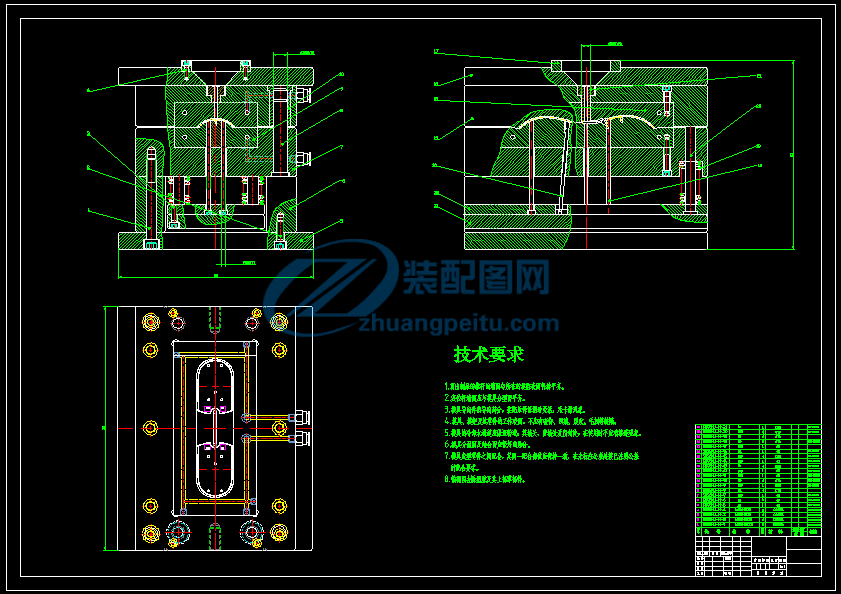


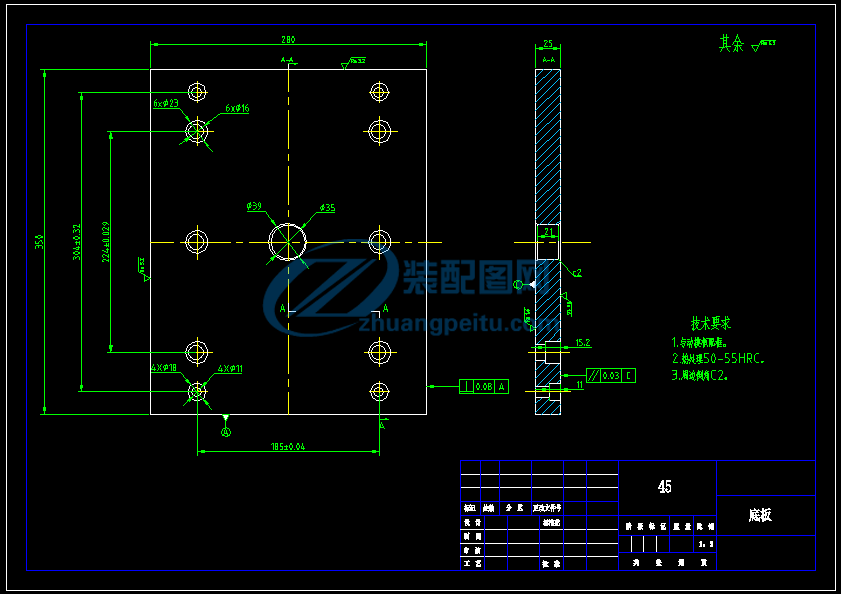
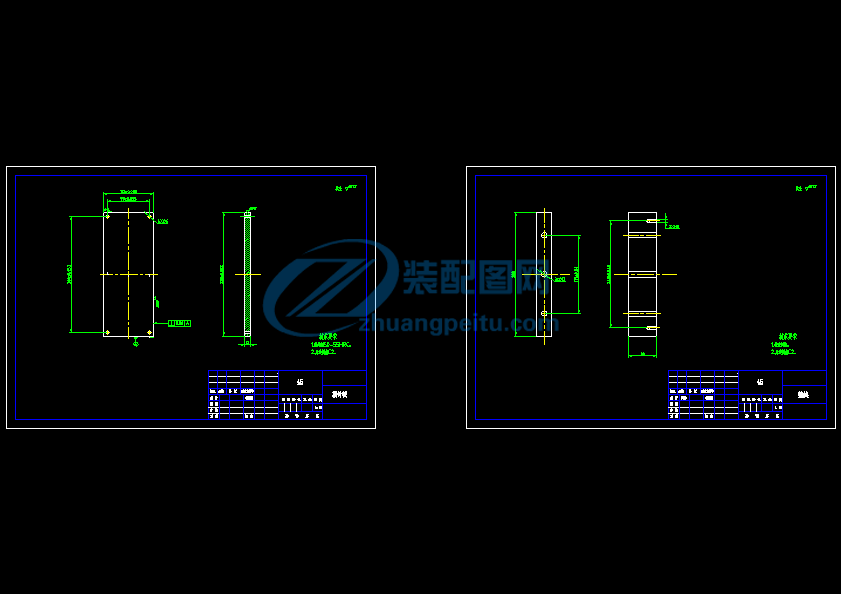
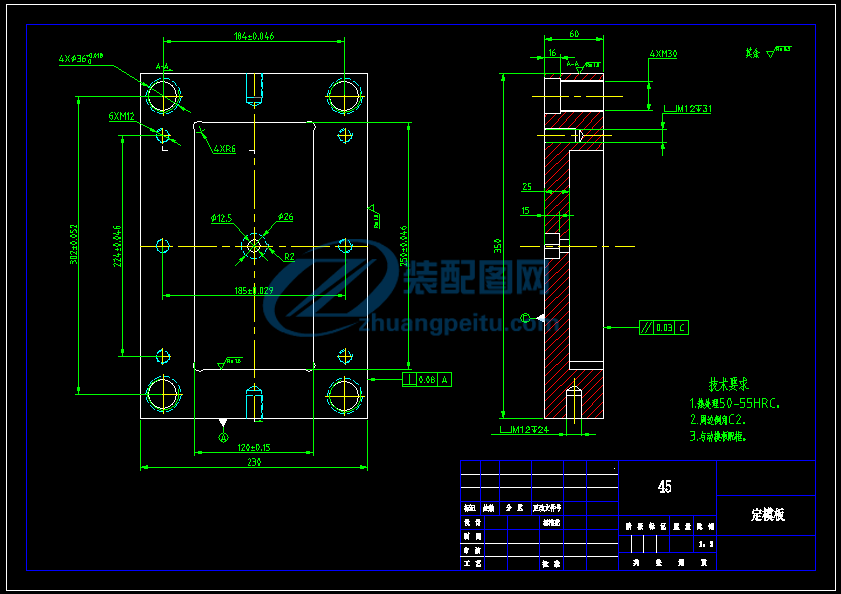
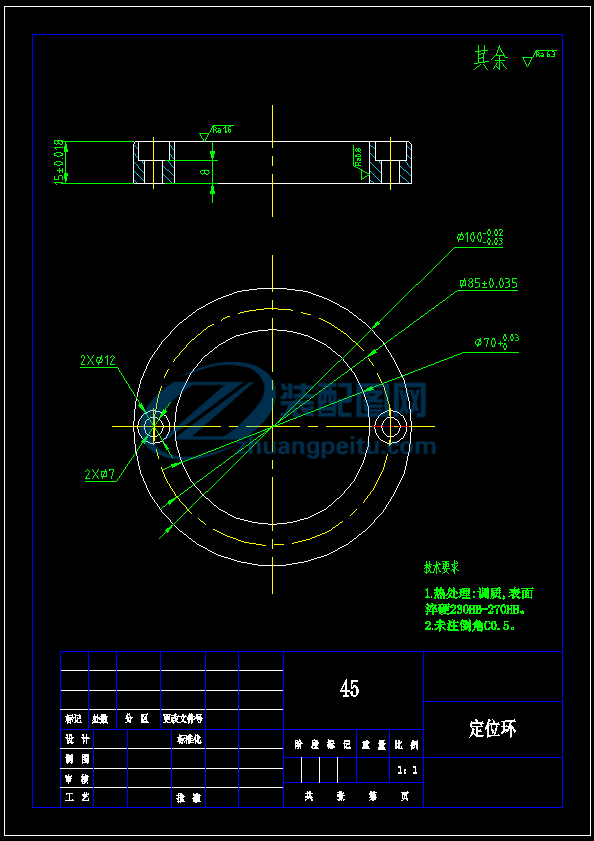

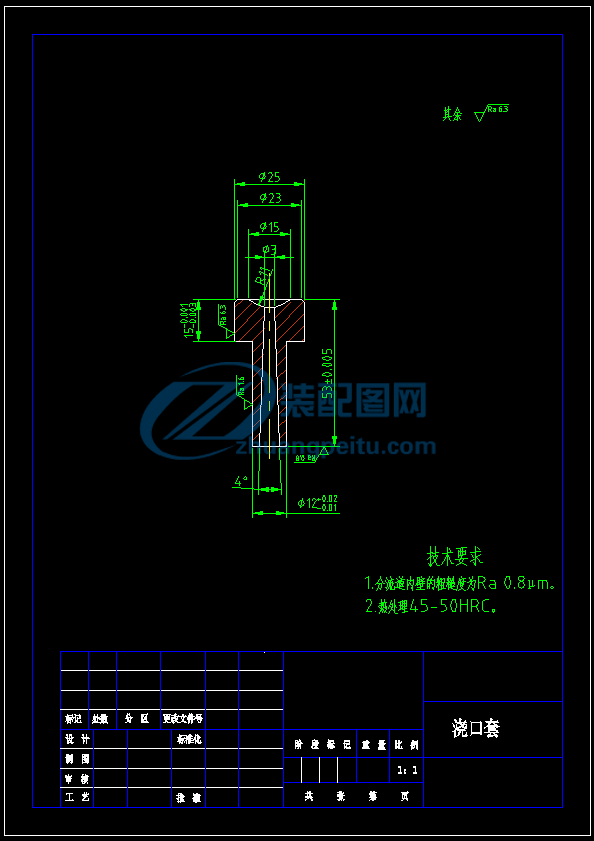
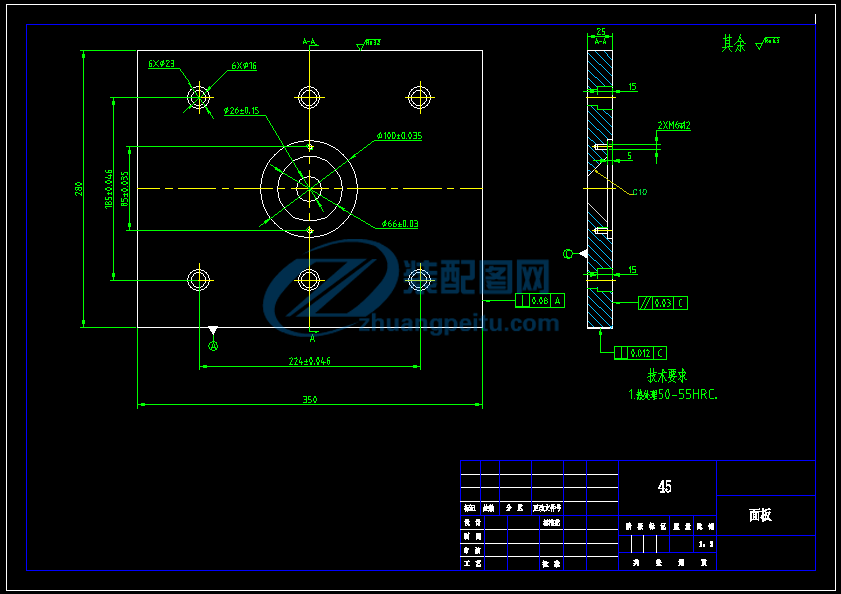
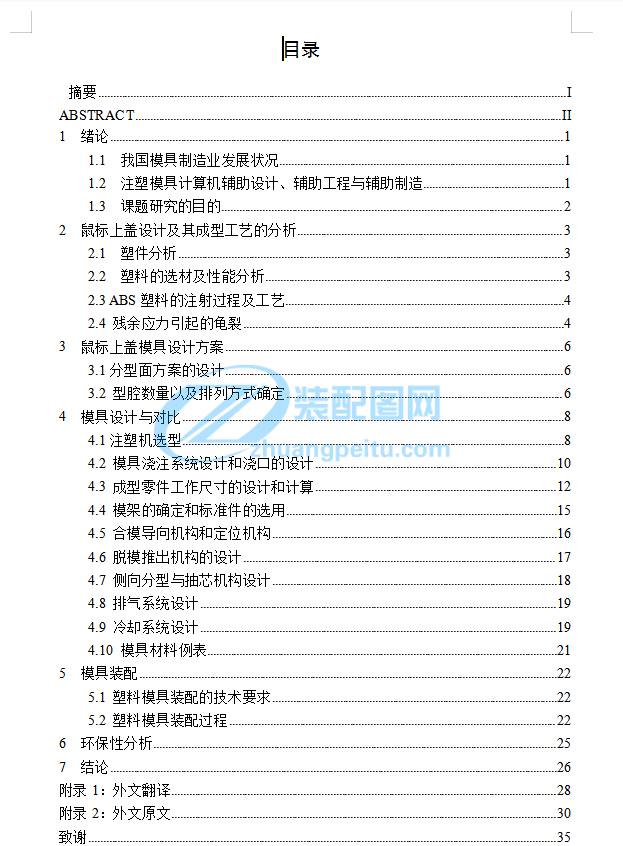
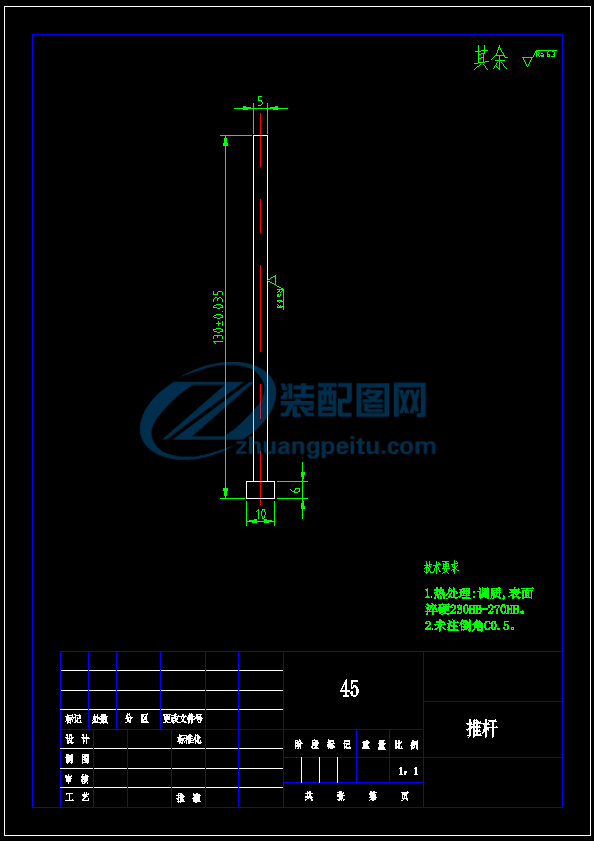
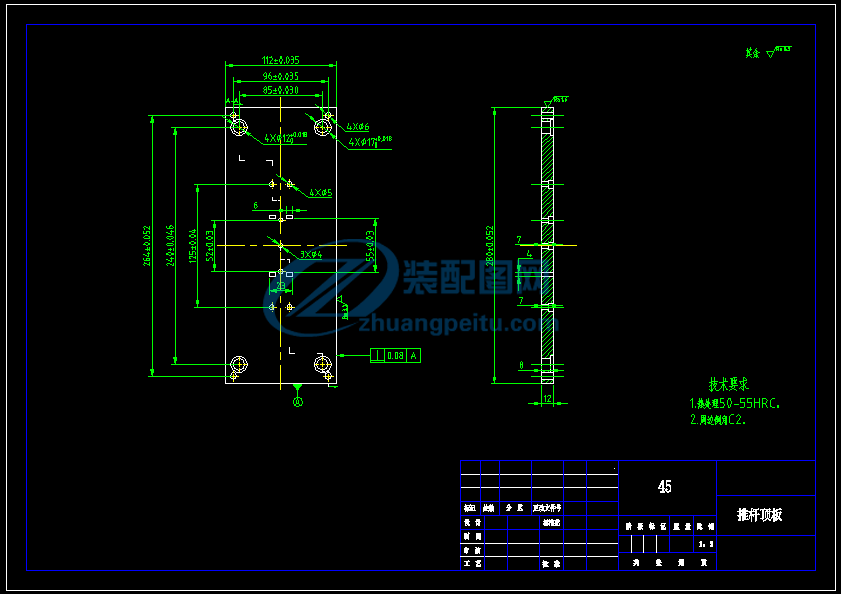
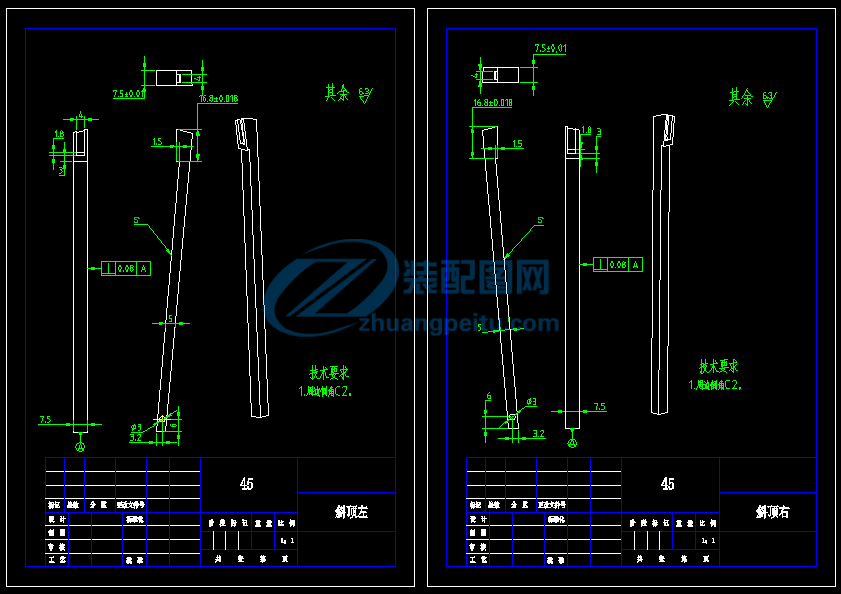
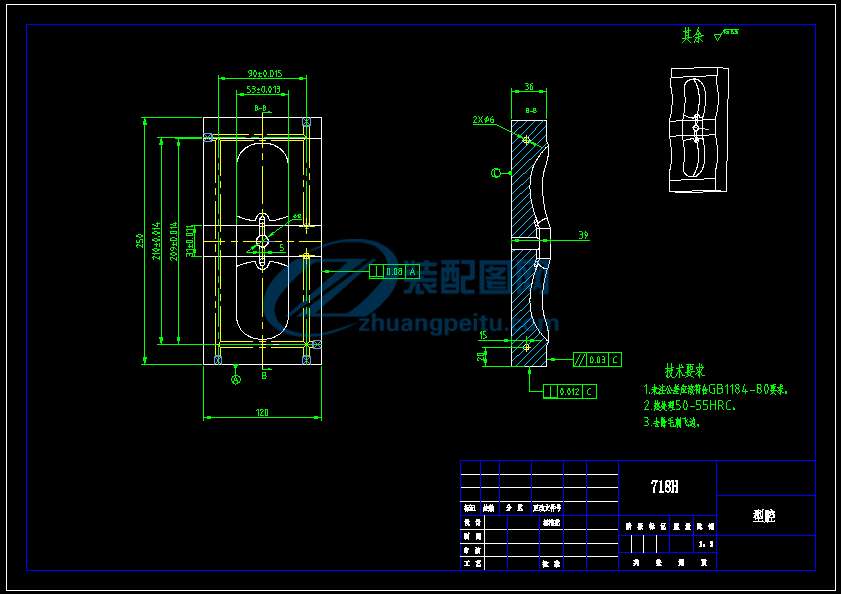
目錄
摘要 I
ABSTRACT II
1 緒論 1
1.1 我國模具制造業(yè)發(fā)展狀況 1
1.2 注塑模具計算機輔助設計、輔助工程與輔助制造 1
1.3 課題研究的目的 2
2 鼠標上蓋設計及其成型工藝的分析 3
2.1 塑件分析 3
2.2 塑料的選材及性能分析 3
2.3 ABS塑料的注射過程及工藝 4
2.4 殘余應力引起的龜裂 4
3 鼠標上蓋模具設計方案 6
3.1分型面方案的設計 6
3.2 型腔數(shù)量以及排列方式確定 6
4 模具設計與對比 8
4.1注塑機選型 8
4.2 模具澆注系統(tǒng)設計和澆口的設計 10
4.3 成型零件工作尺寸的設計和計算 12
4.4 模架的確定和標準件的選用 15
4.5 合模導向機構(gòu)和定位機構(gòu) 16
4.6 脫模推出機構(gòu)的設計 17
4.7 側(cè)向分型與抽芯機構(gòu)設計 18
4.8 排氣系統(tǒng)設計 19
4.9 冷卻系統(tǒng)設計 19
4.10 模具材料例表 21
5 模具裝配 22
5.1 塑料模具裝配的技術(shù)要求 22
5.2 塑料模具裝配過程 22
6 環(huán)保性分析 25
7 結(jié)論 26
附錄1:外文翻譯 28
附錄2:外文原文 30
致謝 35
摘要
本鼠標上蓋塑料模具設計綜合了產(chǎn)品結(jié)構(gòu)設計,成型工藝分析,模具結(jié)構(gòu)設計等過程于一體。在設計該模具的同時總結(jié)了以往模具設計中常用的方法、步驟,模具設計中常見的模具結(jié)構(gòu)、公式及數(shù)據(jù)。在本次畢業(yè)設計中,通過運用三維實體造型軟件SolidWorks對“鼠標上蓋”外形進行3D造型,同時也設計其塑料外殼注塑模的3D模型;還根據(jù)所設計的模具尺寸選擇安裝相應的模架,最終生成了直觀的結(jié)構(gòu)設計圖;此外還利用CAD繪制了模具裝配圖以及各種成型零件圖。
關(guān)鍵詞:殼體; 注塑模; 模具; SolidWorks; AutoCAD
26
壓縮包內(nèi)含CAD圖紙和三維建模及說明書,咨詢Q 197216396 或 11970985 鼠標上蓋注塑模具設計
ABSTRACT
National revitalization of machinery industry in recent years, every industry pay more and more attention to related to mechanical CAD/CAM technology, not only because of CAD/CAM technology has developed into a relatively mature technology, but also because of the plastic products and mould 3 d design and molding process of 3 d analysis is the plastic mold industry plays a more and more important role.In this graduation design, by using 3 d solid modeling software SolidWorks for \"mouse\" on the cover appearance 3 d modelling, but also design the 3 d model of the plastic shell injection mold;Also according to the design of the mould size choose to install the corresponding die set, the resulting intuitive structure design;In addition to use CAD draw the mold assembly drawing as well as a variety of molding part drawing.
Keywords: Shell; Injection mold; Mould; SolidWorks; AutoCAD
VII
1 緒論
1.1 我國模具制造業(yè)發(fā)展狀況
隨著我國經(jīng)濟發(fā)展,模具制造業(yè)得到大力發(fā)展。近年來中國模具創(chuàng)造的利潤高,每年銷售額高達近千億元人民幣,出口額也在幾十億美元。部分產(chǎn)品已經(jīng)達到或者接近國際水平,并且持續(xù)保持快速增長模式。中國模具制造業(yè)的發(fā)展不僅體現(xiàn)在銷售額上,在制造精度和制造難度上也大有提升,高精度的的制造模具業(yè)可以生產(chǎn)高光學級別的車燈模具,以及模數(shù)較小的高精度齒輪模具;不僅如此在模具制造噸位要求上,已達到單套重達50t以上,在腔體數(shù)量上一模近萬腔的塑封模也可以生產(chǎn)。
塑料制件最常用的方法就是注塑成型,對于形狀不規(guī)則復雜程度高,且要求尺寸精確的塑料制件,注塑成型可以滿足這些要求,而且可大批量高效率進行生產(chǎn),市場廣闊前景良好。
雖然我國模具制造業(yè)發(fā)展迅速,經(jīng)過近半個世紀的快速發(fā)展,達到一定的水平,但是與國外先進水平相比,仍然存在很多問題,專業(yè)性與柔性化結(jié)合程度低,利用計算機輔助設計提高模具制造業(yè)整體水平,刻不容緩。
1.2 注塑模具計算機輔助設計、輔助工程與輔助制造
1.2.1 CAD/CAM/CAE對模具設計的作用及意義
目前市場競爭激烈,再加上種類多,更新快,所以必須走向做出高品質(zhì),高質(zhì)量,高效率,縮短設計周期,降低生產(chǎn)成本的道路。
然而,我國塑料模具的發(fā)展還停留在依靠經(jīng)驗豐富的設計工藝人員對所做工件進行分析,對于設計的是否合理,方法運用是否得當,設計的制品有無缺陷,只有做出模具進行試模才能做出判斷,不僅耗費的資金大成本高,而且周期太長,無法跟進市場變化。而采用計算機輔助設計,可以采用模擬設計替代試模,避免傳統(tǒng)方法的各種弊端,例如反復的進行試模,改模,修模。同傳統(tǒng)的方法相比,計算機輔助設計CAD/CAM/CAE技術(shù)在在、減輕勞動強度,提高質(zhì)量,提高效率,降低生產(chǎn)成本、等方面,起到了重要的作用。
近年來公布的數(shù)據(jù)統(tǒng)計表明,國外采用計算機輔助設計CAD/CAM/CAE技術(shù)所體現(xiàn)的效果,成本下降了百分之十、制造時間縮短了百分之三十、設計時間縮短了一半、、塑料原料節(jié)省了百分之七。注射模計算機輔助設計CAD/CAM/CAE技術(shù)作為一種高效的工具,基本上從根本上,解決了傳統(tǒng)模具的一些問題。隨著注射模計算機輔助設計CAD/CAM/CAE技術(shù)發(fā)展,將在我國塑料模具工業(yè)中起到重要作用。
1.2.2 Solidworks簡介
Solidworks軟件功能強大,組件繁多。 Solidworks 可以把想象出來的零部件的立體形狀,展現(xiàn)出來。由于CAD等軟件的二維圖紙的表達復雜性和不夠直觀,需要個人想象能力,正是二維圖紙的這些缺點,促使Solidworks三維輔助軟件的產(chǎn)生,實現(xiàn)縮放、旋轉(zhuǎn)等功能。Solidworks在功能上容易上手,易學易用。SolidWorks 功能強大,成為主流的三維CAD解決方案。其獨特的功能,能夠拖拽功能,使得我們在使用Solidworks時可以在很短的時間內(nèi)完成繪圖裝配出工程圖。SolidWorks可以很方便的存儲 CAD文件。使用SolidWorks ,方便快捷的完成大量工作,滿足市場高質(zhì)量的需求。在目前市場上所見到的三維CAD解決方案中,SolidWorks設計過程簡便方便快捷的完成設計任務。
1.3 課題研究的目的
塑料制品的應用已經(jīng)深入到千家萬戶對人們的生產(chǎn)生活影響深遠,因此對于模具設計的要求不斷提高。本課題以鼠標上蓋為研究對象,對其澆口位臵、冷卻系統(tǒng)、填充系統(tǒng)、翹曲變形進行優(yōu)化分析,從而得到了最佳澆口位臵和模具的相關(guān)結(jié)構(gòu)。整個設計從2 d到3 d視覺設計,實現(xiàn)CAD/CAM/CAE一體化,縮短開發(fā)周期,提高競爭力。
2 鼠標上蓋設計及其成型工藝的分析
2.1 塑件分析
圖2-1 鼠標上蓋
圖2-2 鼠標上蓋三維圖
2.1.1 結(jié)構(gòu)分析如下
好的鼠標符合人機工程學,表面光滑手感舒適,在模具設計和制造上要有良好的加工工藝,該塑件屬于流線型結(jié)構(gòu),由許多曲面構(gòu)成,確保成型零件具有一定的光潔度,模具倒扣部分用斜頂成型完成
2.1.2 成型工藝分析
精度分析 精度要求不高采用5級。
外形分析 該塑件壁厚約為1mm左右,適合注射成型。
拔模斜度分析 由于殼體左右部分比較淺,ABS無定型塑料,成型收縮率較小,所以脫模斜度為1度;由于下面的倒扣需要用到斜頂模斜度也設置為1度。
2.2 塑料的選材及性能分析
綜合該殼體的抗拉性能,硬度要求,耐磨性能,機械性能的要求。具備這些條件的塑料首選:丙烯腈-丁二烯-苯乙烯,簡稱ABS
2.2.1 使用特點
力學輕度高,具有抗沖擊性,穩(wěn)定性高,電學性能良好,易于成型,適合制作機械結(jié)構(gòu)零部件。
2.2.2 成型特征
(1)無定形料,流動性中等,吸濕大,必須充分干燥,表面要求光澤的塑件須長時間預熱干燥80-90度,3小時。
(2)宜取高料溫,高模溫,但料溫過高易分解(分解溫度為>270度).對精度較高的塑件,模溫宜取 50-60度,對高光澤.耐熱塑件,模溫宜取60-80度。
(3)如需解決夾水紋,需提高材料的流動性,采取高料溫、高模溫,或者改變?nèi)胨坏确椒ā?
(4)如成形耐熱級或阻燃級材料,生產(chǎn)3-7天后模具表面會殘存塑料分解物,導致模具表面發(fā)亮,需對模具及時進行清理,同時模具表面需增加排氣位置。
2.3 ABS塑料的注射過程及工藝
注射成型成型
成型前準備,對ABS進行干燥。ABS是吸水的塑料,于室溫下,24小時可吸收0.2%-0.35%水分,雖然這種水分不至于對機械性能構(gòu)成重大影響,但注塑時若濕度超過0.2%,塑料表面會受大的影響,所以對ABS進行成型加工時,一定要事先干燥,而且干燥后的水分含量應小于0.2%。ABS的干燥方法: 常壓熱風干燥 80-85℃ 2-4小時 ;真空熱風干燥 80℃ 1-2小時。
注射過程.
塑料在注射機內(nèi)經(jīng)過加熱、塑化達到流動狀態(tài)后,由模具的澆注系統(tǒng)進入模具型腔成型,起過程可分為充模、壓實、保壓、倒流、和冷卻5個階段。
2.4 殘余應力引起的龜裂
殘余應力主要由于以下三種情況,即充填過剩、脫模推出和金屬鑲嵌件造成的。作為在充填過剩的情況下產(chǎn)生的龜裂,其解決方法主要可在以下幾方面入手。
(1)由于直澆口壓力損失最小,所以,如果龜裂最主要產(chǎn)生在直澆口附近,則可考慮改用多點分布點澆口、側(cè)澆口及柄形澆口方式。
(2)在保證樹脂不分解、不劣化的前提下,適當提高樹脂溫度可以降低熔融粘度,提高流動性,同時也可以降低注射壓力,以減小應力。
(3)一般情況下,模溫較低時容易產(chǎn)生應力,應適當提高溫度。但當注射速度較高時,即使模溫低一些,也可減低應力的產(chǎn)生。
(4)注射和保壓時間過長也會產(chǎn)生應力,將其適當縮短或進行Th次保壓切換效果較好。
白化現(xiàn)象最主要發(fā)生在ABS樹脂制品的推出部分。脫模效果不佳是其主要原因。可采用降低注射壓力,加大脫模斜度,增加推桿的數(shù)量或面積,減小模具表面粗糙度值等方法改善,當然,噴脫模劑也是一種方法,但應注意不要對后續(xù)工序,如燙印、涂裝等產(chǎn)生不良影響。
3 鼠標上蓋模具設計方案
3.1分型面方案的設計
分型面是模具上用來取出塑件和澆注系統(tǒng)料可分離的接觸面稱為分型面,分型面的選擇對模具設計方式影響最大,分型面設計是否合理對塑件質(zhì)量和模具復雜程度具有很大的影響?;旧鲜且环N分型面對應著一種模具設計方案,所以分型面的選擇決定著模具總體的設計方案。
3.1.1分型面的選擇原則
(1)使分型面容易加工。
(2)保證塑料制品能夠脫模。
(3)盡量避免側(cè)向抽芯。
(4)使側(cè)向抽芯盡量短。
(5)有利于排氣。
(6)有利于保證塑件的外觀質(zhì)量。
(6)盡量減少塑件在合模方向的投影面積。
(7)盡可能使塑件留在動模一側(cè)。
(8)盡可能滿足塑件的使用要求。
(9)有利于簡化模具結(jié)構(gòu)。
(10)長型芯應置于開模方向。
綜上所述,由于該塑件曲面多,分型面不可能在一個平面上,為了順利脫模,分型面采用如下模具結(jié)構(gòu),只需要斜頂出模,加工成本經(jīng)濟,塑件成型精度可靠。
圖3.1 分型面形式與位置
3.2 型腔數(shù)量以及排列方式確定
6
圖3.2 型腔排列方式
鼠標上蓋主要為流線型結(jié)構(gòu),遂采取一模兩腔設計。有如下優(yōu)點:
(1)產(chǎn)品結(jié)構(gòu)較小,采用該設計能保證順利走膠,改善注射件品質(zhì);
(2)有利于注塑產(chǎn)品產(chǎn)能提升,減少生產(chǎn)成本,提高生產(chǎn)效率
7
4 模具設計與對比
4.1注塑機選型
注射機是安裝在注射機上使用的設備,因此設計注射模應該詳細了解注射機的技術(shù)規(guī)范,才能設計出符合要求的模具。
注射機規(guī)格的確定主要是根據(jù)塑件的的大小及型腔的模具和排列方式,在確定模具結(jié)構(gòu)形式及初步估算外形尺寸的前提下,設計人員應對模具所需的注射量、鎖模力、注射壓力、拉桿間距、最大和最小模具厚度、推出形式、推出位置、推出行程、開模距離進行計算。根據(jù)這些參數(shù)選擇一臺和模具相匹配的注射機,倘若用戶自己提供型號和規(guī)格,設計人員必須對其進行校核,若不能滿足要求,則必須自己調(diào)整或與用戶取得商量調(diào)整。
4.1.2型腔數(shù)量的校核及注射機有關(guān)工藝參數(shù)的校核
(1)型腔數(shù)量的校核
由注射機料筒塑化速率校核型腔數(shù)量
(4.1)
t取60s, 符合要求。
式中 K——注射機最大注射量的利用系數(shù),非結(jié)晶型塑料一般取0.8;
M——注射機的額定塑化量,改注射機為16.8g/s;
T——成型周期,因塑件還比較大,壁厚,取30s;
m1——單個塑件的質(zhì)量,取106.3g ;
m2——澆注系統(tǒng)的質(zhì)量,取1.04g ;
按注射機的最大注射量校核型腔數(shù)量
符合要求。
式中 ——注射機允許的最大注射量,該注射機為140g。
其他符號意義與取值同前。
按注射機的額定鎖模力校核型腔數(shù)量
殼體正反兩面產(chǎn)生的脹模力由內(nèi)模殼抵消;左右兩行位壓力由導柱和前模板的斜面抵消,取這兩處力的一半為正壓力:
8
分型面合模處的作用面積:
塑料熔體對型腔的成型壓力是,一般是注射壓力的30%-65%,
取平均壓力為:
(4.2)
(4.3)
符合要求。
(2)注射機工藝參數(shù)的校核
注射量的校核
注射量以容積表示最大注射容積為:
最少注射容積:
而
符合要求。
鎖模力的校核
前面計算過,符合要求。
最大注射壓力的校核
注射機的額定注射壓力即為該機器的最高壓力
應該大于注射成型所需調(diào)用的注射壓力的 即
式中;
為70—90;
代入數(shù)據(jù)計算,符合要求。
(3)安裝尺寸的校核
最大與最小模具厚度
模具厚度H應滿足
式中
該套模具厚度H=25+60+70+80+25=260mm 。
很明顯,選擇該注射機能滿足模具設計的要求。
(4)開模行程校核
——注射機動模板的開模行程,取270mm,見表4.2;
——塑件推出行程取22mm;
——為包括流道凝料在內(nèi)的塑件高度;
代值計算發(fā)現(xiàn)開模行程能滿足。
4.2 模具澆注系統(tǒng)設計和澆口的設計
澆注系統(tǒng)是引導凝料熔體從注射機噴嘴到模具型腔的進料通道,具有傳質(zhì)、傳壓和傳熱的功能。
4.2.1 主流道的設計
主流道是連接注射機的噴嘴與分流道的一段通道,通常和注射機噴嘴在同一軸線上,斷面為圓形,具有一頂?shù)腻F度,以便熔體的流動和開模時主流到凝料的順利拔除。
(1)主流道尺寸和澆口的設計
主流道的小端直徑 D =注射機噴嘴直徑+(0.5~1)
=3+(0.5~1),取D=3.5mm 。
主流道的球面半徑 SR =注射機噴嘴球頭半徑+(1~2)
=15+(1~2),取SR=16mm 。
球面的配合高度 ,取h=3mm 。
主流道的長度 取L=22+43.5=65.5mm。
主流道大端直徑 (半錐角)
取
澆口套總長
(2)澆口套的設計
主流道小端入口處與注射機噴嘴反復接觸,屬易損件,對材料要求比較嚴,因而模具主流道部分常設計成可拆卸更換的主流道襯套形式即澆口套,以便有效的選用優(yōu)質(zhì)鋼材單獨進行加工和熱處理,常采用碳素工具鋼,如T8A、T10A等,熱處理硬度為50HRC~55HRC,如圖4.1所示。
(3)定位圈的設計與固定
由于該模具主流道比較長,定位圈和襯套設計成分體式,注射機定位孔尺寸為 ,定位圈尺寸取 ,兩者之間呈較松的間隙配合。
定位圈結(jié)構(gòu)尺寸如圖4.2所示。
圖4.1 澆口套
圖4.2 定位圈
4.2.2 澆口和流道的設計
選擇點進膠,如圖4.3,塑料熔體直接流入型腔,因而壓力損失小,進料速度快,成型比較容易。另外傳遞壓力好,保壓補縮作用強.
圖4.3 點澆口和流道的設置形式
4.3 成型零件工作尺寸的設計和計算
模具中決定塑件幾何形狀和尺寸的零件稱為成型零件,包括凹模、型芯、鑲塊、成型桿和成型環(huán)等。成型零件工作時,直接與塑料接觸,塑料熔體的高壓、料流的沖刷,脫模時與塑件間還發(fā)生摩擦。因此,成型零件要求有正確的幾何形狀,較高的尺寸精度和較低的表面粗糙度,此外,成型零件還要求結(jié)構(gòu)合理,有較高的強度、剛度及較好的耐磨性能。
設計成型零件時,應根據(jù)塑料的特性和塑件的結(jié)構(gòu)及使用要求,確定型腔的總體結(jié)構(gòu),選擇分型面和澆口位置,確定脫模方式、排氣部位等,然后根據(jù)成型零件的加工、熱處理、裝配等要求進行成型零件結(jié)構(gòu)設計,計算成型零件的工作尺寸,對關(guān)鍵的成型零件進行強度和剛度校核。
工作尺寸是零件上直接用以成型塑件部分的尺寸,主要有型腔和型芯的徑向尺寸,型腔深度和型芯高度尺寸和中心距尺寸等。
ABS的成型收縮率為0.4%--0.7%所以平均收縮率取 s=0.55%。
塑件尺寸公差按SJ1372--78標準中的5級精度成型。
4.3.1 動模部分的型芯與型腔
鼠標上蓋前部兩小孔用絲筒成型并頂出, 絲筒針的前部設置1度脫模角度,方便加工和替換。
(1) 長方體型芯(見圖4.4)
圖4.4 型芯三維圖
采用臺肩固定的形式,下底面用模珂與動模壓緊。
塑件的尺寸公差源自《塑料成型工藝與模具設計》的塑件公差數(shù)值表。
塑件尺寸 ,,,。
式中 s——塑料的平均收縮率,ABS為0.55%;
——塑件外徑尺寸(取25.64mm);
——修正系數(shù)(取0.75);
——塑件尺寸公差,見上塑料尺寸公差值;
——模具制造誤差,其他誤差忽略,當尺寸小于50mm時, ;當塑件尺寸大于50mm 時,。
(2) 動模模仁(見圖4.5)
圖4.5 動模型腔
模仁為鑲?cè)胧?,通過沉頭螺釘固定在動模板上。
尺寸計算。塑件的尺寸公差源自《塑料成型工藝與模具設計》的塑件公差數(shù)值 ,,,
(4.5)
式中各符號同前。
4.3.2 型腔零件剛度和強度校核
由于塑件成型部分采用模仁,再從模板上開框把模仁鑲?cè)?,用螺絲吃緊。成型部分離模仁有滿足條件的規(guī)定距離(20~25mm),而模仁離模板四周也有滿足條件的規(guī)定距離,所以成型時型腔零件完全滿足強度和剛度的要求,在這里就不一一校核。在動模板上,由于成型壓力很大部分垂直壓在其上,底部為了節(jié)約材料不打算采用支撐板。
4.4 模架的確定和標準件的選用
根據(jù)前面型腔的布局以及互相位置尺寸,再根據(jù)成型零件尺寸結(jié)合標準模架,選用結(jié)構(gòu)形式為CI2335 60 70 80 01 S。即采用數(shù)量為1的工字標準模架。
(1)定模座板(280mm x 350mm、厚為25mm)
定模座板是模具與注射機連接固定的板,材料為45鋼。
通過4個M12的內(nèi)六角圓柱螺釘與定模固定板連接;定位圈通過2個M8的內(nèi)六角圓柱螺釘與其連接;定模座板與澆口套為H8/f8配合。
(2)定模板(230mm x 350mm,厚60mm)
用于固定型芯、導套。固定板應有一定的厚度,并有足夠強度,一般用45號鋼,調(diào)質(zhì)到230HB~270HB。其上的導柱和導套一端采用H7/k6配合,另外一段采用H7/f7配合;定模板與澆口套采用H7/m6配合[7]。
(3)動模座板(280mm x350mm、厚為25mm)
材料為45鋼,其上的注射機頂孔為直徑40 mm。
(4)動模板(230mm x 350mm,厚70mm)
行位滑塊通過矩形導滑槽在模套中滑動,以完成側(cè)向分型和合模復位,材料為45鋼。其上的導柱和導柱孔為H7/k6配合。
(5)墊塊(43mm x 350mm 厚80mm)
主要作用
在動模座板與支撐板之間形成推出機構(gòu)的動作空間,或是調(diào)節(jié)模具的總厚度,以適應注射機的模具安裝厚度要求。
結(jié)構(gòu)形式
可以是平行墊塊或拐角墊塊,該模具采用平行墊塊。
墊塊材料
墊塊材料為Q235A,也可以用HT200、球墨鑄鐵等。改套模具采用Q235A制造。
(6)推板(140mm x 350mm,厚度15mm)
材料為45鋼,其上的推板導套孔與推板導套采用H7/k6配合。用M6的內(nèi)六角圓柱螺釘與推桿固定板固定。
(7)推桿固定板(140mm x 350mm,厚度20mm)
鋼材為45鋼,其上的推板導套孔與推板導套采用H7/f9配合。
模架如圖(4.6)所示:
圖4.6 模架
4.5 合模導向機構(gòu)和定位機構(gòu)
采用標準模架,模架本身帶有導向裝置,按模架規(guī)格選取即可。
4.5.1 導向機構(gòu)的總體設計
(1)導向零件應合理地均勻分布在模具的周圍或靠近邊緣的部分,其中心至模具邊緣應有足夠的距離,以保證模具的精度,防止壓入導柱和導套后變形。
(2)該導套采用4根導柱,其布置為等直徑導柱不對稱布置。
(3)導柱安裝在支承板和模套上,導套安裝在定模固定板上。
(4)為了保證分型面很好的接觸,導柱和導套在分型面處應只有承屑槽,在導柱孔口倒角。
(5)在合模時,保證導向零件首先接觸,避免凸模先進入型腔,導致模具損壞。
(6)動定模板采用合并加工時,可確保同軸度要求。
4.5.2 導柱設計
(1)采用帶頭導柱,加油槽,如圖4.9所示。
(2)導柱長度必須比凸模端面高度高出6mm ~8mm。
(3)為了使導柱能順利地進入導向孔,導柱端部常做成圓錐形的先導部分。
(4)導柱的直徑應根據(jù)模具尺寸來確定,應保證有足夠的抗彎強度。
(5)導柱的安裝形式,導柱固定部分與模板按H7/k6配合,導柱滑動部分按H7/f7或H8/f7間隙配合。
(6)導柱工作部分的表面粗糙度為0.2um。
(7)導柱應具有堅硬耐磨的表面、不易折斷的內(nèi)芯。多采用低碳鋼經(jīng)滲碳淬火處理或碳素工具鋼T8A、T10A經(jīng)淬火處理,硬度為50HRC以上或45鋼經(jīng)調(diào)質(zhì)、表面淬火、低溫回火、硬度為50HRC以上。
圖4.7 導柱
4.5.3 導套設計
導套與安裝在另外一半模上的導柱相配合,用以確定動、定模的相對位置,以保證模具運動導向精度的圓套形零件。導套常用的結(jié)構(gòu)形式有兩種:直導套、帶頭導套。
(1)采用帶頭導套,如圖4.10所示。
(2)導套的端面應倒圓角,導柱孔最好做成通孔,利于排出孔內(nèi)剩余空氣。
(3)導套孔的的滑動部分按H8/f7 H7/f7的間隙配合,表面粗糙度為0.4um。
導套外徑與模板一端采用H7/k6配合;另外一端采用H7/e7配合鑲?cè)肽0濉?
(4)導套材料可用淬火鋼或銅等耐磨材料制造,該模具中采用T8A。
圖4.8 導套
4.6 脫模推出機構(gòu)的設計
注射成型每一循環(huán)中,塑件必須準確無誤地從模具的凹模中或型芯上脫出,完成脫出塑件的裝置稱為脫模機構(gòu),也常稱為推出機構(gòu)。
4.6.1 脫模推出機構(gòu)的設計原則
塑件推出(頂出)是注射成型過程中的最后一個環(huán)節(jié),推出質(zhì)量的好壞將最后決定塑件的質(zhì)量,因此,塑件的推出是不可忽視的,應遵循以下原則。
(1)推出機構(gòu)應近盡量設置在動模一側(cè)。
(2)保證塑件不因推出而變形損壞。
(3)機構(gòu)簡單,動作可靠。
(4)良好的塑件外觀。
(5)合模時的準確復位。
4.6.2 塑件的推出機構(gòu)
該套模具的塑件采用推桿推出,推桿的形式為圓形。
(1) 推桿如圖4.11所示,共4根推桿。
圖4.9 帶肩圓筒推桿
(2)推桿應設置在脫模阻力大的地方。
(3)推桿應布置均勻。
(4)推桿應設在塑件強度、剛度較大的地方。
(5)推桿直接與模板上的推桿空采用H8/f8間隙配合。
(6)通常推桿裝入模具后,其端面應與型腔地面平齊或高出型腔底面0.05mm~0.10mm。
(7)推桿與推桿固定板,通常采用單邊0.5mm的間隙,這樣可以降低加工要求,又能在多推桿的情況下,不因各板上的推桿孔加工誤差引起軸線不一致而發(fā)生卡死現(xiàn)象。
(8)推桿的材料常用T8、T10碳素工具鋼,熱處理要求硬度50HRC以上,工作端配合部分的表面粗糙度為 u=0.8um。
4.7 側(cè)向分型與抽芯機構(gòu)設計
當在注射成型的塑件上與開合模方向不同的內(nèi)側(cè)或外側(cè)有孔、凹穴或凸臺時,塑件就不能直接由推桿等推出機構(gòu)推出脫模,此時,模具上成型該處的零件必須制成可側(cè)向移動的活動型芯,以便在塑件脫模推出之前,先將側(cè)向成型零件抽出,然后在把塑件從模內(nèi)推出,否則就無法脫模。
4.7.2 斜頂?shù)脑O計
斜頂設置在動模,有足夠的強度。
斜導柱頂端用模珂和定模板固定并磨到和定模板平,在開模時能隨驅(qū)使滑塊沿動模板上的導滑槽滑動。
斜頂傾斜角為5度。
斜頂相對位置以及脫模推出完成后的相對位置如圖4.12所示。
需要側(cè)抽芯的距離是:1.5mm
斜頂頂出塑件的抽芯距離:遠大于1.5mm
所以抽芯距離滿足要求,塑件能正常取出。
圖4.10 斜頂分型與抽芯分析
4.8 排氣系統(tǒng)設計
模板分型面上設置1mm深的排氣槽用于排氣,而且在成型殼體內(nèi)腔的型芯上設置了6根推桿,排氣條件足夠。
4.9 冷卻系統(tǒng)設計
4.9.1 加熱系統(tǒng)
該套模具的模溫要求在70以下,又是小型模具,所以無需設置加熱裝置。
4.9.2 冷卻系統(tǒng)
ABS塑料注射到模具內(nèi)的塑料溫度為180—190 左右,而塑料固化后
從模具型腔中取出時其溫度在60 以下,熱塑性塑料在注射成型后,須對模具進行有效的冷卻,使熔融塑料的熱量盡快地傳給模具,以使塑料可靠冷卻定型并可迅速脫模。
ABS的成型溫度和模具溫度分別為180~190 、50~70 ,用常溫水對模具進行冷卻。
(1)冷卻介質(zhì)
冷卻介質(zhì)有冷卻水和壓縮空氣,但用冷卻水比較多,因為冷卻水熱容量大、傳熱系數(shù)大,成本低。用水冷卻,即使在模具型腔周圍或者內(nèi)部開設冷卻水道。
(2)冷卻系統(tǒng)的簡略計算
如果忽略模具因空氣對流、熱輻射以及與注射機接觸所散發(fā)的熱量,不考慮模具金屬材料的熱阻,可對模具冷卻系統(tǒng)進行初步的簡略計算。
求塑料固化時每分鐘釋放的熱量
查表得ABS單位質(zhì)量放出的熱量 ,故
式中 W—單位時間內(nèi)注入模具中的塑料質(zhì)量(kj/min),模具每分鐘注射1次。
冷卻水的體積流量
(4.7)
式中 ——冷卻水的密度,為;
——冷卻水出口溫度,取25;
——冷卻水進口溫度,取20;
C——冷卻水的比熱容,為4.187;
冷卻管道的直徑
為使冷卻水處于湍流狀態(tài),查資料取d=6mm。
冷卻水在管道內(nèi)的流速
(4.8)
冷卻水管道水孔壁與冷卻水之間的傳熱膜系數(shù)
查參考文獻中的表取f =7.22,水溫為25時,因此
(4.9)
冷卻管道的總傳熱面積
(4.10)
模具上應開設的冷卻水孔數(shù)
(4.11)
式中 l—模珂長度,為150mm.
4.9.3 冷卻裝置布置方案的確定
我們在上下模仁上各開設兩條水道,用于冷卻塑件的兩側(cè)面,這樣才能使塑件各個方面都能得到冷卻,防止了受熱不均勻?qū)е碌穆N首。從裝配圖上可查看“冷卻水路示意圖” 。
4.10 模具材料例表
表4.7 該模具的選材及熱處理見表
零件名稱
材料牌號
熱處理
硬度
說明
模仁
718H
預硬化
36HRC-38HRC
保證加工后獲得較高的形狀和尺寸精度,易于拋光
圓柱型芯
Cr12MoV
淬火
58HRC-62HRC
淬透性好,熱處理變形小、耐磨性好
斜導柱
T7A
淬火
52HRC-55HRC
動模型芯
718H
淬火
42HRC-54HRC
保證加工后獲得較高的形狀和尺寸精度,沿脫模方向拋光
動定模座板
45
調(diào)質(zhì)
230HB-270HB
墊塊
Q235
調(diào)質(zhì)
230HB-270HB
支撐柱
S50C
調(diào)質(zhì)
225HB-240HB
推板固定板
45
調(diào)質(zhì)
230HB-270HB
主流道襯套
T10A
淬火
50HRC-55HRC
導柱導套
T10A
淬火
54HRC-58HRC
定位圈
45
調(diào)質(zhì)
230HB-270HB
復位桿
45
淬火
43HRC-48HRC
5 模具裝配
5.1 塑料模具裝配的技術(shù)要求
塑料模具種類較多,結(jié)構(gòu)差異很大,裝配的具體內(nèi)容與要求也不同。一般注射、壓縮和擠出模具結(jié)構(gòu)相對復雜,裝配環(huán)節(jié)多,工藝難度大。其他類型的塑料模具結(jié)構(gòu)較為簡單。無論哪種類型的模具,為保證成形制品的質(zhì)量,都應具有一定的技術(shù)要求。
(1)模具裝配后各分型面應貼合嚴密,主要分型面的間隙應小于0.05mm;在模具適當?shù)钠胶馕恢脩b有吊環(huán)或起吊孔;模具的外形尺寸、閉合高度、安裝固定及定位尺寸、推出方式、開模行程等均應符合設計圖樣要求,并與所使用的設備條件相匹配,模具應有標記,各模板應打印順序編號及加工與裝配時使用的基準標記。
(2)導向或定位精度應滿足設計要求,動、定模開合運動平穩(wěn),導向準確,無卡阻、咬死或刮傷現(xiàn)象,安裝精定位元件的模具時,應保證定位精度、可靠,且不得與導柱、導套發(fā)生干涉。
(3)成型零件的形狀與尺寸精度及表面粗糙度應符合設計圖樣要求,表面不得有碰傷、劃痕、裂紋、銹蝕等缺陷;拋光方向應與脫模方向一致,成形表面的文字、圖案與脫模方向一致;活動成形零件或鑲件應定位可靠。配合間隙適當,活動靈活,不產(chǎn)生溢料。
(4)澆注系統(tǒng)表面光滑,尺寸與表面粗糙度符合設計要求。
(5)推出機構(gòu)應運動靈活,工作平穩(wěn)、可靠;推出元件不應承受側(cè)向力;既不允許放生溢料,也不得有卡阻現(xiàn)象。
(6)側(cè)向分型與抽芯機構(gòu)應運動靈活、平穩(wěn);斜導柱不應承受側(cè)向力;滑塊鎖挈應固定可靠,工作時不得產(chǎn)生變形。
(7)模具加熱元件應安裝可靠、絕緣安全、無破損,能達到設定溫度要求;模具冷卻水道應通暢,無堵塞,連接部位密封可靠。
5.2 塑料模具裝配過程
塑料模的總裝過程因模具結(jié)構(gòu)的不同而不同,但其主要的總裝配順序不變,具體如下:
(1)確定裝配基準。
(2)安裝導柱導套和型芯、型腔并使間隙均勻。
(3)安裝側(cè)抽芯機構(gòu)和推出機構(gòu)等。
(4)其他零件的裝配。
(5)檢驗、試模。
下面以裝配圖上的編號為準,裝配時以導柱、導套為基準件,裝配過程如下。
5.2.1 裝配動模部分
(1)裝配模仁、型芯
先把圓柱型芯12和長方塊型芯09壓入動模仁16,使09和11的底部與16持平,并高出12有0.01-0.02mm的間隙,以防止型芯松動。再把動模仁16放入動模板并壓平,用穿過動模板的內(nèi)六角螺絲把模珂吃緊在動模板上。
(2)裝配推出機構(gòu)
推板放在動模固定板上,將推桿套裝在固定板上推桿孔內(nèi)并穿入型芯固定板的推桿孔內(nèi),在套裝到推板導柱上,使推板和推桿固定板重合。在推桿固定板板螺孔內(nèi)涂紅丹粉,將螺釘孔復印到推板上。然后,取下推板固定板,在推板上鉆孔攻絲后,重新合攏并擰緊螺釘固定。裝配后,進行滑動配合檢查,經(jīng)調(diào)整使其滑動靈活,無卡阻現(xiàn)象。最后,將卸料板拆下,把推板放到最大極限位置,檢查推桿在型芯固定板上平面露出的長度,將其修磨到與型芯固定板上平面平齊或低0.02mm。
5.2.2 裝配定模部分
總裝配前澆口套、導套都已裝配結(jié)束并經(jīng)驗合格。裝配時,將定模板套在導柱上并與已裝澆口套的定模座板合攏,找正位置,用平行夾頭夾緊,以定模座板上的螺釘孔定位,對定模板鉆錐窩,然后拆開,在定模板上鉆孔、攻絲后重新合攏,用螺釘擰緊固定,最后鉆、鉸定位銷釘孔打入定位銷釘。
經(jīng)以上裝配后,要檢查定模板和澆口套的澆道錐孔是否對正,如果在接逢處有錯位,需要進行鉸削修整,使其光滑一致。
圖5-1 總體裝配三維圖
圖5-2 三維爆炸圖
6 環(huán)保性分析
自從進入20世紀90年代以來,世界各國對環(huán)境的重視程度越來越高。每個國家也開始制定自己的環(huán)境保護法律法規(guī)。一個企業(yè)對環(huán)境的影響程度也越來越?jīng)Q定著自己的經(jīng)營產(chǎn)值。一個產(chǎn)品是否有著良好的環(huán)保性,也成為了國際市場上重要的競爭標準之一。
本產(chǎn)品利用ABS樹脂進行生產(chǎn)成型的,其有以下優(yōu)缺點:
(1)其無毒,不會對環(huán)境和人體造成傷害;
(2)只有溫度達到250℃以上才會產(chǎn)生有毒的揮發(fā)性物質(zhì),而本產(chǎn)品的成型溫度在180~190℃,所以是安全的;
(3)ABS只有在強紫外線下才容易降解,也可以使用專用的塑料粉碎機和造料機就可以對其回收利用,制成再生材料;
(4)整個生產(chǎn)過程中使用水就能進行冷卻,稍作處理,冷卻水就能循環(huán)不會對環(huán)境產(chǎn)生影響;
(5)由于是小型塑件,不會產(chǎn)生大的噪音,因此也是環(huán)境有好的。
總的來說,產(chǎn)品是環(huán)境友好型產(chǎn)品,不會對環(huán)境巨大破壞。
7 結(jié)論
通過本次設計,并經(jīng)過查閱大量相關(guān)文獻,不僅使我對于塑料模具有了更加深入的了解,對模具的設計過程有了更加清晰的認識,并對所學知識加以鞏固如機械制圖、Solidworks、公差、Autodesk等,可謂受益匪淺。
在模具設計完成后,總結(jié)如下:
采用了一模兩腔的型腔排布方式,可以提高生產(chǎn)效率。采用潛伏式澆口有利于實現(xiàn)自動化生產(chǎn)。
利用CAD/CAE技術(shù)設計模具,可以優(yōu)化模具結(jié)構(gòu)、提高效率、縮短周期、降低成本。
利用solidworks繪制了澆注系統(tǒng)、冷卻系統(tǒng)、標準模架、以及脫模機構(gòu)等,可以立體、直觀地再現(xiàn)尚未加工出的模具體,提高模具的設計質(zhì)量及效率。
經(jīng)過本次設計受益很多,但也有許多不足的地方,由于沒有真正意義上的加工制造過零部件,在設計時對零件沒有過多的考慮其經(jīng)濟性。
參考文獻
[1] 濮良貴.機械設計[M].北京:高等出版社,2013.5
[2] 池成忠.注塑成型工藝與模具設計[M].北京:化學工業(yè)出版社,2010.7.
[3] 劉貫軍.機械工程材料與成型技術(shù)[M].北京:電子工業(yè)出版社,2011.3.
[4] 葉久新.塑料成型工藝及模具設計[M].北京:機械工業(yè)出版社,2008.
[5] 肖祥芷.王義林.模具CAD/CAE/CAM[M].北京:電子工業(yè)出版社,2004.
[6] 俞芙芳主編.塑料成型工藝與模具設計[M].武漢:華中科技大學出版社,2007.
[7] 洪慎章.實用注塑成型及模具設計[M].北京:機械工業(yè)出版社,2006.
[8] 吳生緒主編.塑料成形模具設計手冊[M].北京:機械工業(yè)出版社,2008.
[9] 申開智.塑料成型模具(第2版)[M].北京:中國輕工業(yè)出版社,2009.
[10] 覃鵬翱.塑料模具設計技巧[M].北京:電子工業(yè)出版社,2010.
[11] 何文主編,注塑模具設計實例詳解[M].沈陽:遼寧科學技術(shù)出版社,2009.
[13] 劉鴻文.材料力學I[M].北京:高等教育出版社,2004.
[14] 毛平淮主編.互換性與測試技術(shù)基礎.-2版[M].北京:機械工業(yè)出版社,2010.
[15] 艾勇.基于CAE技術(shù)的注塑模具設計[J].產(chǎn)能經(jīng)濟,2016(07).
[16] 馮剛,張朝閣,江平.我國注塑模具關(guān)鍵技術(shù)的研究與應用進展[J]. 塑料工業(yè),2014(04).
[17] 李林鑫,任小鴻,何文德.鼠標上下蓋澆口位置研究[J].塑料注塑模技術(shù),2011(01).
[18] 高茂濤.注塑模具發(fā)展綜述[J].輕工科技,2014(02).
[19] 孫錫紅.我國塑料模具發(fā)展現(xiàn)狀及發(fā)展建議[J].電加工與模具.2010(S1)
[20] 何政軍.基于實例的注塑模具CAD/CAE/CAM技術(shù)研究與應用[D].華北電力大學,2014.
[21] 王偉.注塑模具冷卻系統(tǒng)關(guān)鍵技術(shù)研究與開發(fā)[D].上海交通大學,2013.
[22] 孫化云.鼠標上蓋注塑模具設計[D].中國石油大學(華東),2012.
[23] Rui Wang School of Engineering Anhui Agricultural University Hefei,Anhui Province,China Xiaoling Kong School of Engineering Anhui Agricultural University Hefei,Anhui Province,China.Application Research of Moldflow in Gate Design of Injection Mould[C].2010 Second International Asia Symposium on Intelligent Interaction and Affective Computing and 2010 Second International Conference on Innovation Management (ASIA-ICIM 2010) .中國湖北武漢,2010-12-4.
[24] Jian ZHOU , Lijun LIa , Yihua HU ,Jianguo YANG ,Ke CHENG.Plastic mold design of top-cover of out-shell of mouse based on CAE.[J]Procedia Engineering 15 (2011) 4441 – 4445
[25]] SCHENK O, HILLMANN M.Optimal design of metal forming die surfaces with evolution strategies.Computers & Structures,2004, 82(10):1695-1705.
[26] YANG Hua-lin, DENG Fang, ZHAI Hong-yan, Research on mold base design technology based on uniform assembly model,Journal of Engineering Design,2009,16(2):8-43. (in Chinese).
附錄1:外文翻譯
注塑成型模具的新設計特點
——減少廢料
1.介紹
過去一個世紀觀察到塑料的迅速增長及其向所有市場的擴散。根據(jù)世界原材料消耗量的重量,塑料是最高的與其他舊材料相比鋁,鋼,橡膠,銅和鋅,由其性能和降低生產(chǎn)成本[1,2]。注塑是塑料制品生產(chǎn)中最重要的工藝之一,約占三分之一的所有塑料通過注塑成型工藝轉(zhuǎn)化成零件[3]。注塑成型的應用工藝在許多行業(yè)如包裝,航空航天和建筑中顯著增加建筑,汽車部件和家用物品[1,3,4]。注射部件的最終質(zhì)量成型取決于材料特性,模具設計和工藝條件[4-6]。有三種注塑成型的基本操作。首先,塑料顆粒將轉(zhuǎn)變成熔體。然后,熔融塑料將通過澆道,澆道和澆口系統(tǒng)在壓力下注入模腔中最后,模具工具將被打開以將部件從空腔[1,7,8]中排出。
將評估注射部件的質(zhì)量的參數(shù)之一是流道系統(tǒng)。 流道系統(tǒng)是一個澆口和澆口之間的連接線。流道系統(tǒng)的主要目的是轉(zhuǎn)移熔融塑料澆口到門。在冷流道系統(tǒng)中,廢料的主要來源是在澆注之后來自澆道和澆口系統(tǒng)的廢料。因此,將評估不同的規(guī)則用于轉(zhuǎn)輪系統(tǒng)設計,以證明轉(zhuǎn)輪的重要性注塑成型中的系統(tǒng)如(a)較小的流道尺寸以最小化廢料; (b)容易從模具中取出工具和從模制部件中移除; (c)用最小的凹痕和熔接線快速填充空腔[9-12]。將被認為是流道系統(tǒng)設計的基本參數(shù)的三個因素是橫截面流道形狀,直徑和腔體布局[9]。轉(zhuǎn)輪的橫截面形狀有7種系統(tǒng)為不同的應用[9,10,13]。最后,根據(jù)要求,不同類型的轉(zhuǎn)輪交叉可以推薦[14]。
本文在考慮現(xiàn)有不同橫截面形狀之后的貢獻是定義流道系統(tǒng)的橢圓幾何形狀作為有效橫截面形狀。我們的基本目標設計和使用本文定義的橢圓形橫截面形狀基本上是具有較小的流道尺寸以最小化廢料,減少注射的總循環(huán)時間并且容易地從模具中彈出部件。除了我們的預期,檢測到與工藝參數(shù)和新的相關(guān)的顯著現(xiàn)象將在另一篇論文中討論的轉(zhuǎn)輪系統(tǒng)的幾何形狀。對于本文,將介紹流道系統(tǒng)的橢圓形或橫截面形狀的設計標準,并進行流道系統(tǒng)的圓形和半橢圓形之間的比較。作者最好的知識,在注塑中已經(jīng)對工藝參數(shù)和材料進行了許多嘗試特征,然而對于包括澆道,澆口和澆道的注射系統(tǒng),存在一些出版物,但沒有提及分析和模擬流道系統(tǒng)的橢圓形橫截面形狀。在本文中,簡單介紹了轉(zhuǎn)輪系統(tǒng)的結(jié)構(gòu),并對橢圓轉(zhuǎn)輪的優(yōu)點進行了評價。然后,注塑部件帶澆道和澆口系統(tǒng)是通過SolidWorks設計的。為了得到準確的仿真結(jié)果,通過SolidWorks Plastic有限元法進行考慮。
2.流道系統(tǒng)的橫截面形狀
流道系統(tǒng)的主要目的是通過澆口將熔融塑料從澆口轉(zhuǎn)移到所有腔體。有流道系統(tǒng)的不同橫截面形狀和它們中的每一種具有不同的應用[13]。設計師應評估不同因素,為特定產(chǎn)品選擇適當?shù)牧鞯老到y(tǒng)形狀。最多兩板模具具有最高效率的流道系統(tǒng)的流行形狀是圓形。適用于Threeplate工具,梯形和修改的梯形是最好的選擇,如果跑步只有在制造一半的模板,但仍然是不能接受的,因為門不能放在一條線上中心流[10]。從具有矩形,正方形和多邊形形狀的腔中推出流道系統(tǒng)具有挑戰(zhàn)性的。它是從不同橫截面的現(xiàn)有拐角產(chǎn)生的。壓降導致如果設計者沒有完全填充空腔和高水平的熱傳遞到模具壁將發(fā)生確定流道系統(tǒng)的適當橫截面形狀及其尺寸[9,13,15]。因此,不同可以考慮流道系統(tǒng)的橫截面來調(diào)節(jié)熔融塑料的流速。最后,形狀和通道的長度對于具有最佳流動和因此具有較少缺陷的最佳產(chǎn)品是重要的[16]。
3.具有橢圓形橫截面形狀的轉(zhuǎn)輪系統(tǒng)
在注塑成型中,流道系統(tǒng)最常見的截面形狀是圓形。在選擇輪形狀對于特定零件設計,應評估的三個主要元素是(a)較小的流道尺寸,以最小化廢料; (b)更容易從模具中彈出; (c)用最小的凹痕快速填充空腔,焊接線和沒有短射。 [9-11]。因此,考慮用于流道系統(tǒng)的新幾何形狀以最小化廢料,以與門的中央流動流成直線,適當?shù)靥畛湟粋€或多個腔,并且彈出該部分容易從模具工具是本文的目標。最后,考慮橢圓形橫截面形狀轉(zhuǎn)輪系統(tǒng)。
為了得到具有最小塑料缺陷的注塑部件,進行準確的比較需要在轉(zhuǎn)輪系統(tǒng)的圓形和橢圓形橫截面形狀之間。為了證明轉(zhuǎn)子的橢圓形橫截面形狀的意義及其選擇的原因在模具設計中的重要問題,評估其他幾何形狀的澆道系統(tǒng)是必要的。最好的幾何截面來比較圓和橢圓是矩形和正方形。矩形是一種有不同的正方形寬度。根據(jù)不同的應用,將選擇具有不同寬度比的矩形澆道系統(tǒng)。與正方形相比,矩形形狀的優(yōu)點之一是最小化流道系統(tǒng)的廢料,并且更容易從模具中彈出,但是壓降是將會發(fā)生的缺點之一減小方形的寬度[13]。
圓和橢圓之間具有與正方形和矩形相同的結(jié)構(gòu)。 D是圓的直徑,a是長軸長度,b是橢圓的短軸長度。主軸長度固定,短軸長度具有不同的速率,這取決于不同的工業(yè)應用。雖然為減少廢料,更容易將部件排出腔外,并且減少循環(huán)時間,最好減少次要的長度軸,這取決于零件設計。因此,b的不同比率取決于部件設計的許多因素,例如尺寸和厚度。減少廢料,更容易將部件排出腔,循環(huán)時間減少和中心流動的澆口系統(tǒng)與圓形相比具有橢圓形橫截面形狀的優(yōu)點。
附錄2:外文原文
Available online at www.sciencedirect.com
ScienceDirect
Procedia Manufacturing 2 (2015) 241 – 245
2nd International Materials, Industrial, and Manufacturing Engineering Conference, MIMEC2015, 4-6 February 2015, Bali Indonesia
New Design Feature of Mold in Injection Molding For Scrap
Reduction
Mehdi Moayyediana,*Kazem Abharya, Romeo Mariana
aUniversity of South Australia, School of Engineering, Mawson Lakes Campus
Abstract
This paper presents a new cross sectional shape of runner system in the injection molding. The aim of the new geometry is to reduce the scrap and cycle time and also the easier ejection of runner system from mold tools. Short shot defect in the plastic part during the injection molding process is analyzed by SolidWorks Plastic to validate the new proposed geometry. Runner system with elliptical cross section is proposed with different ratio