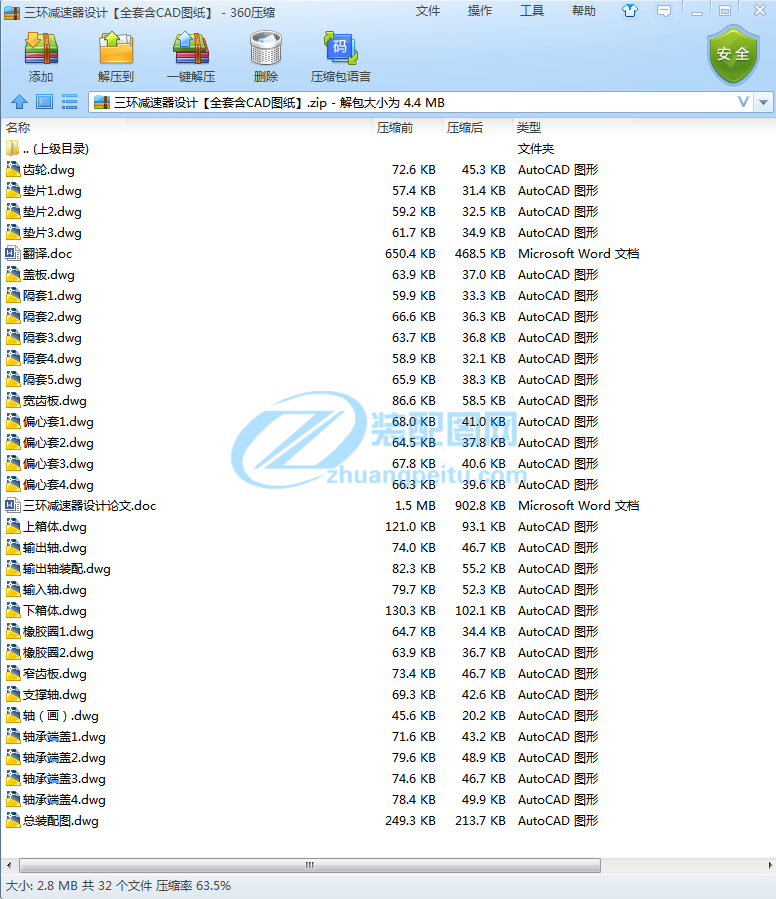
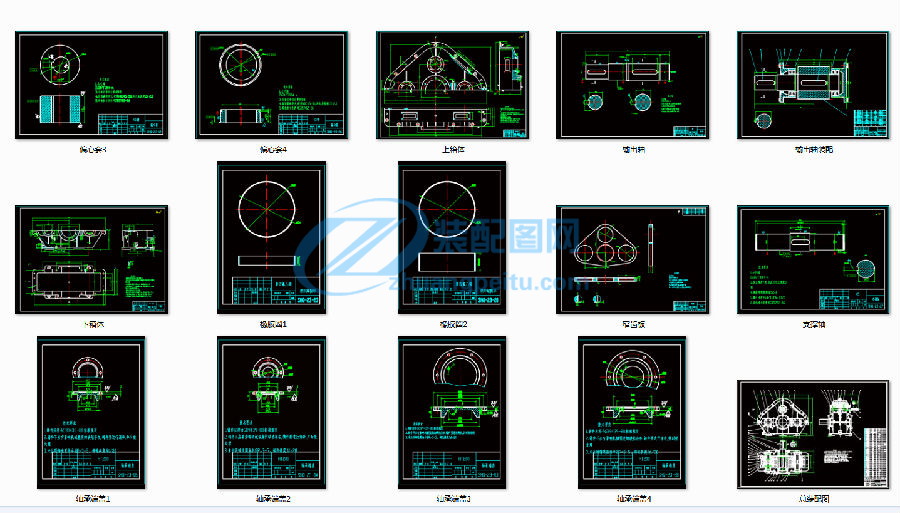

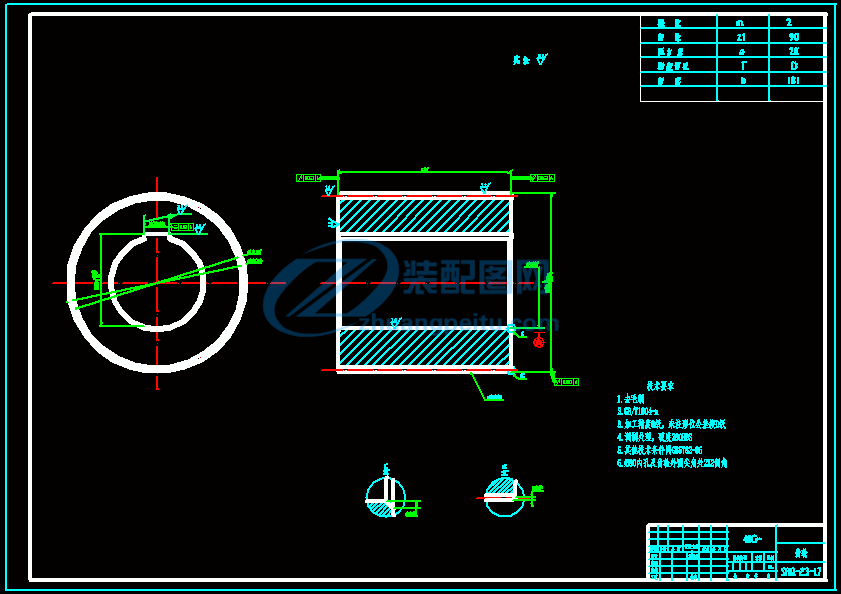

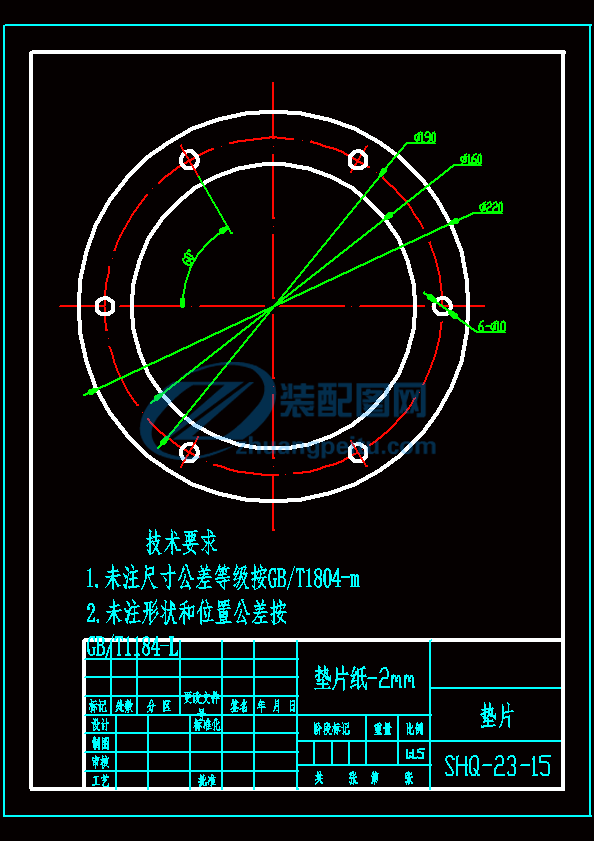


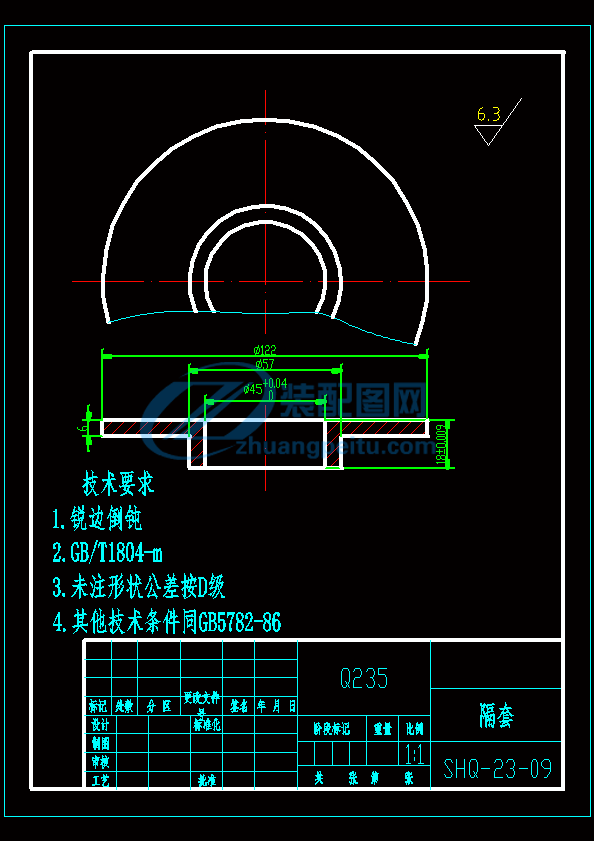
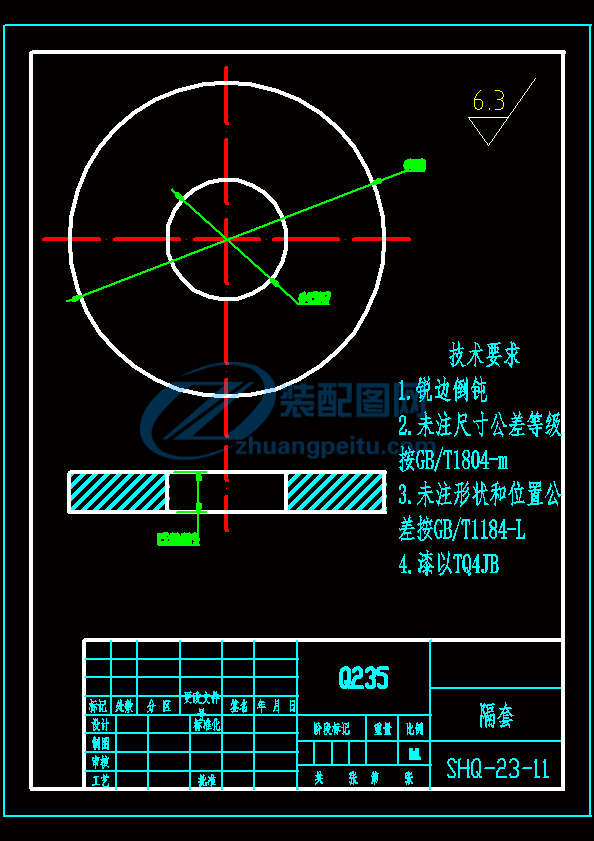
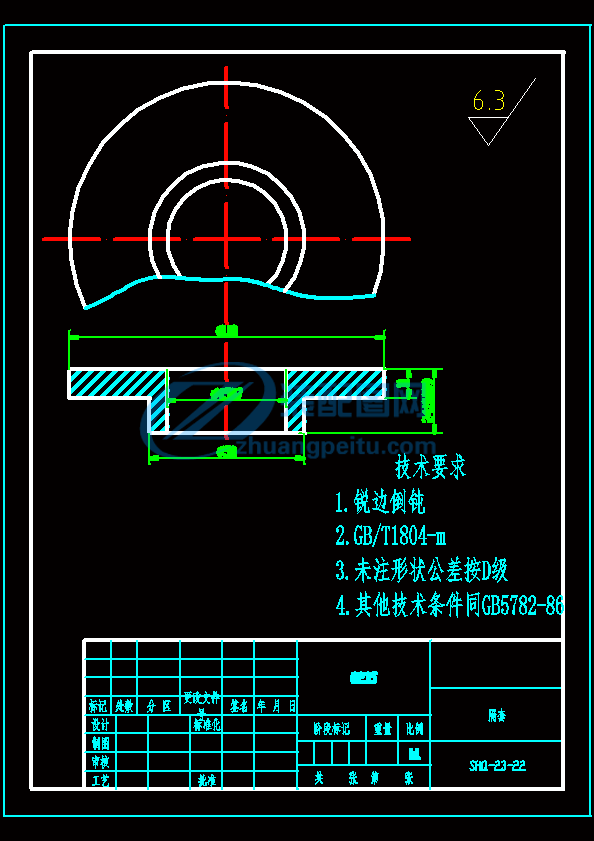

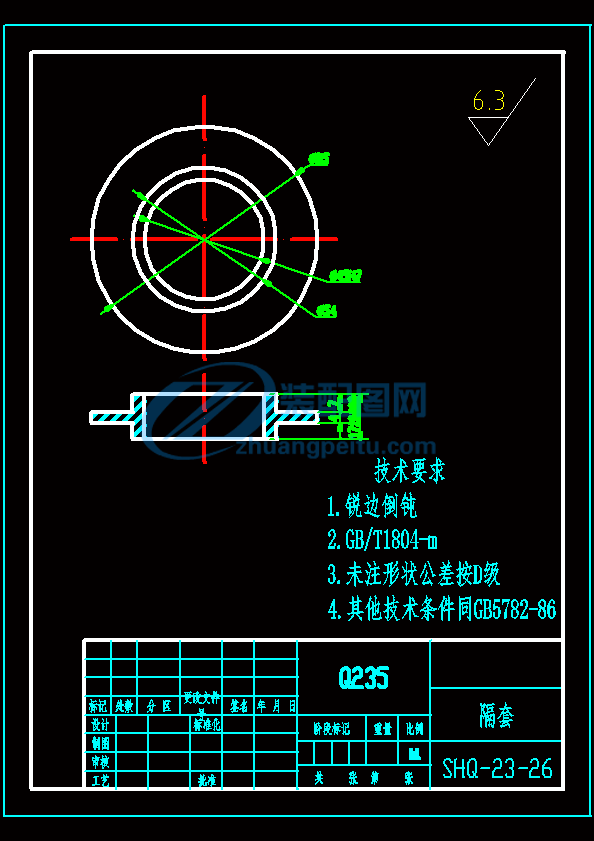
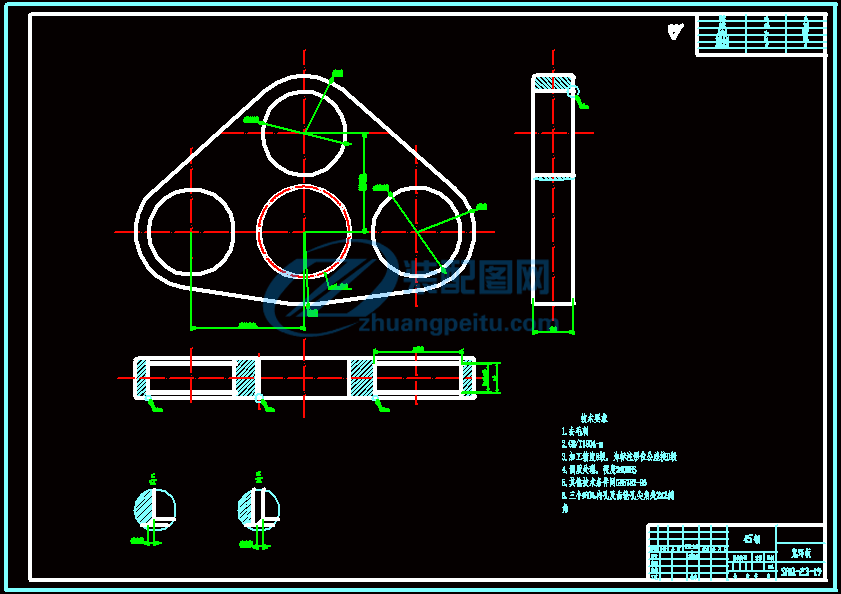


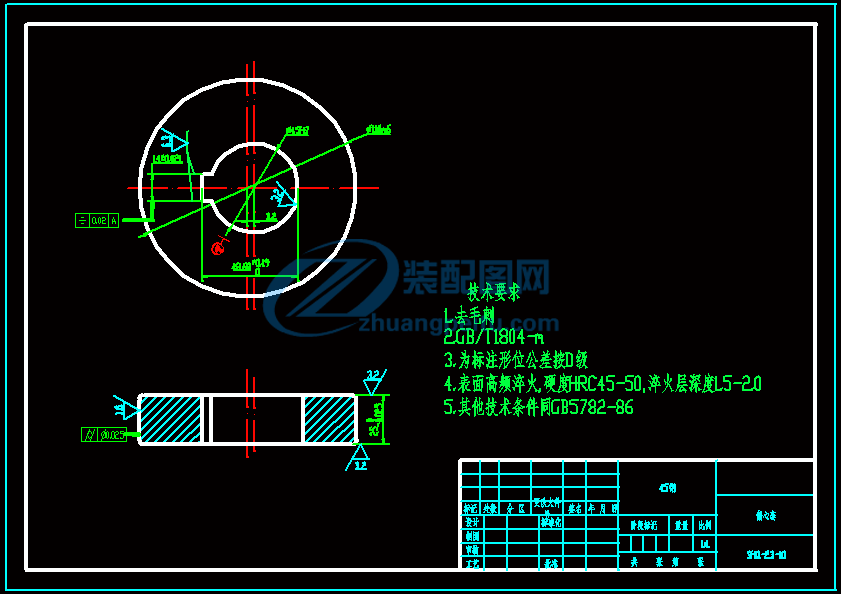

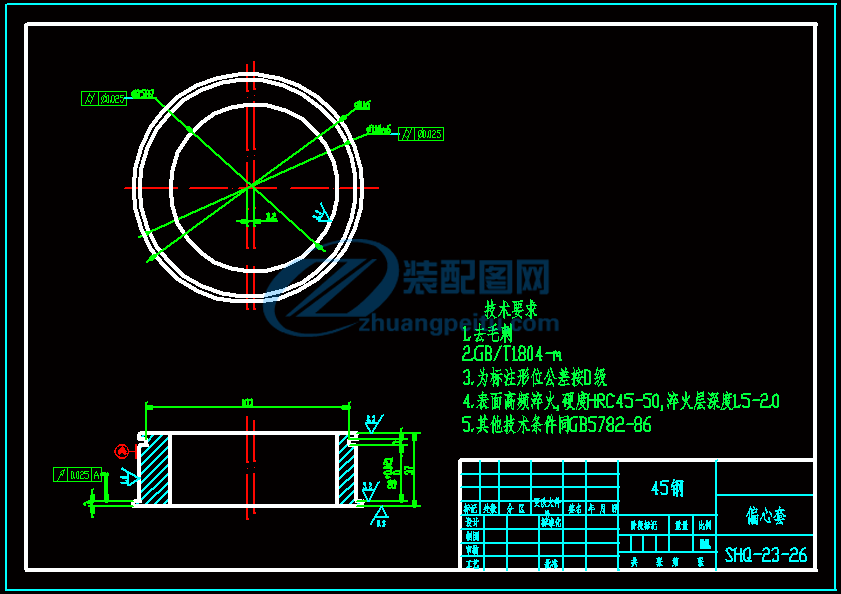
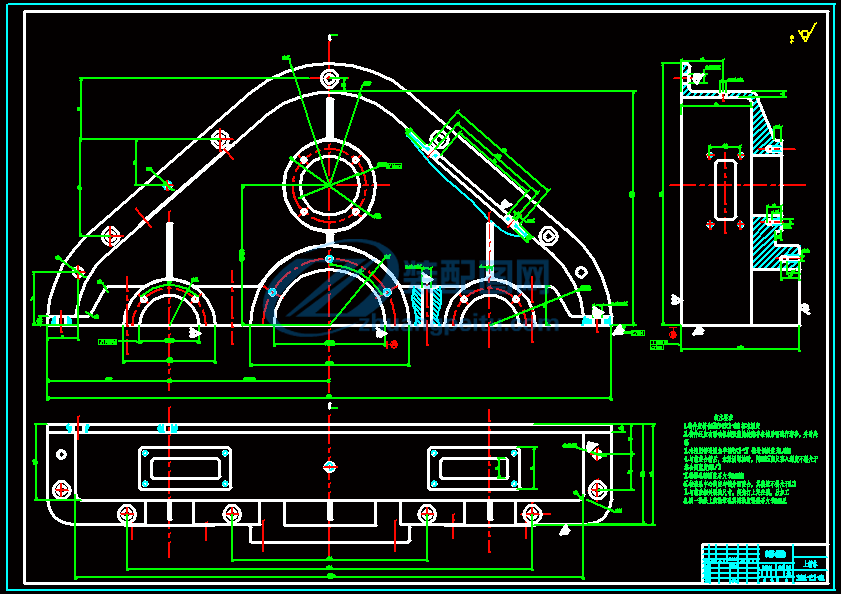
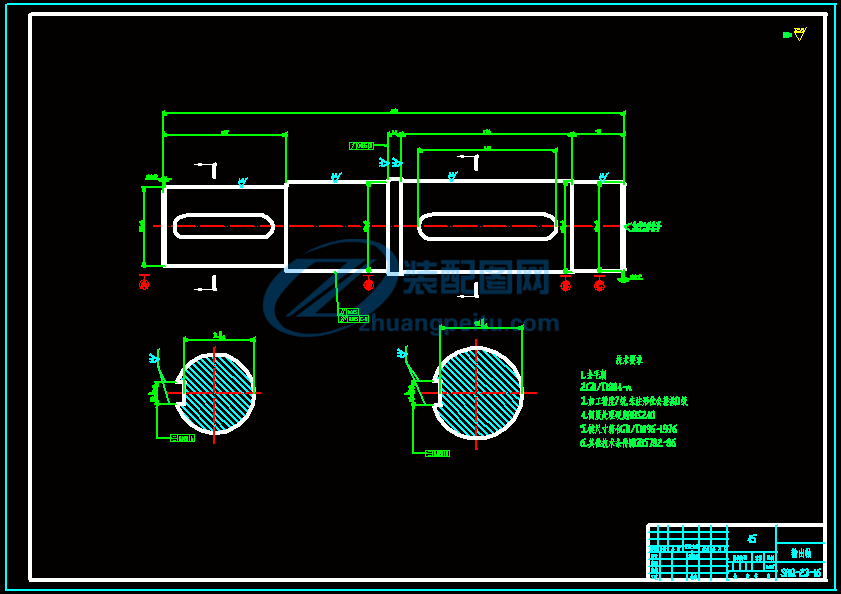
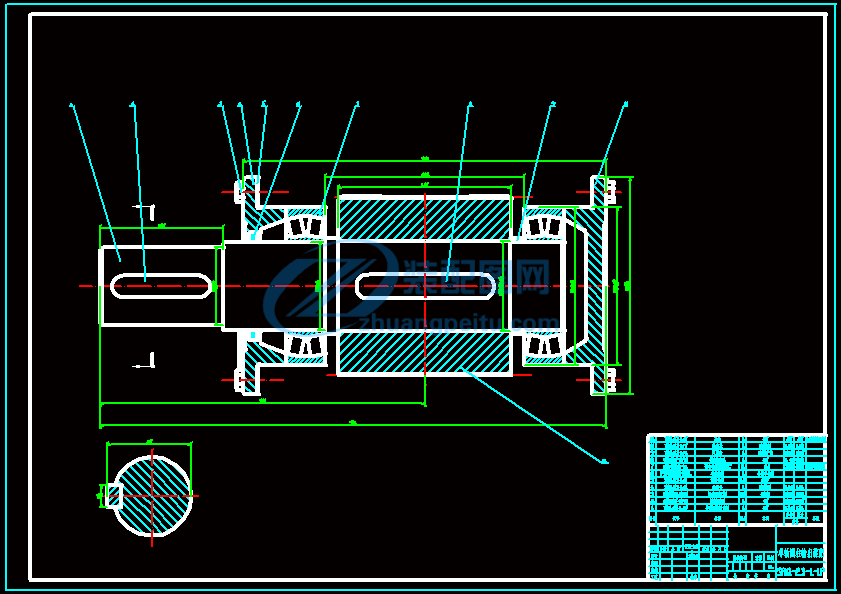

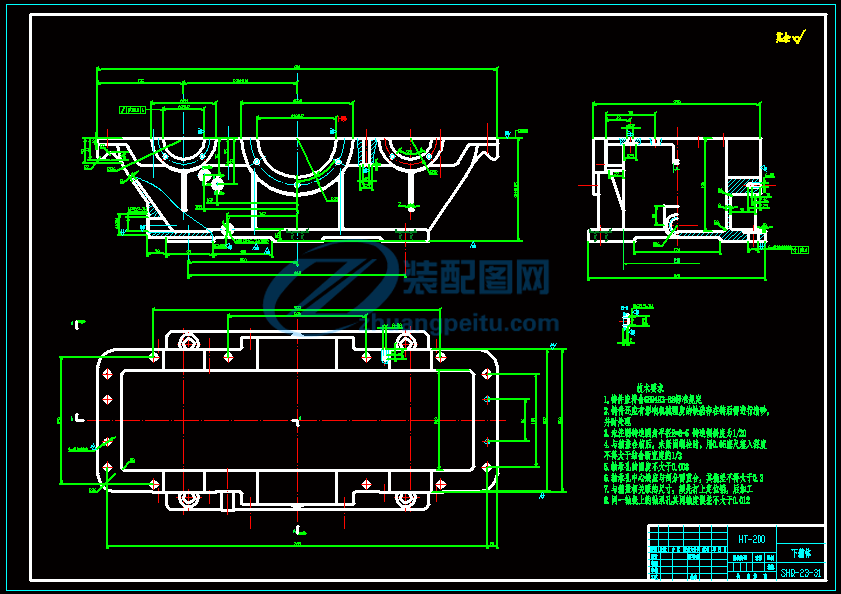
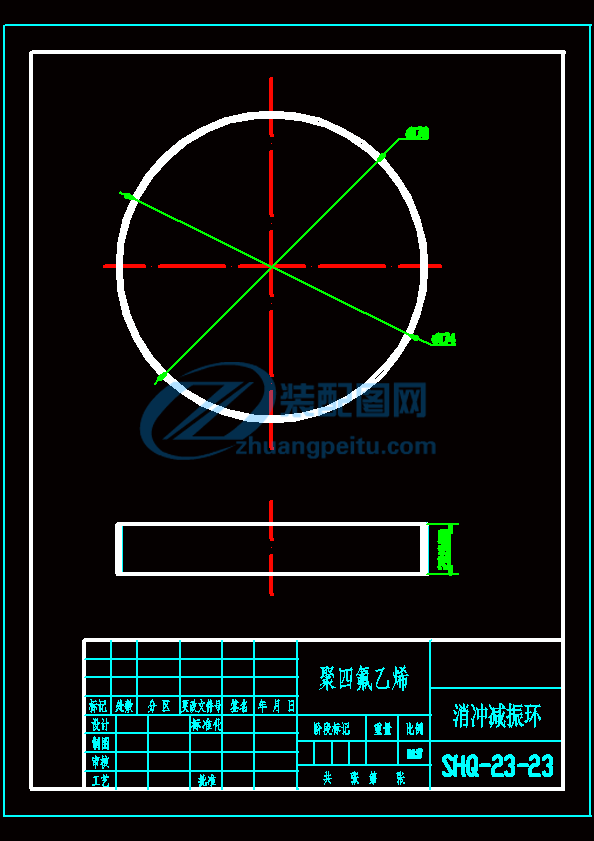

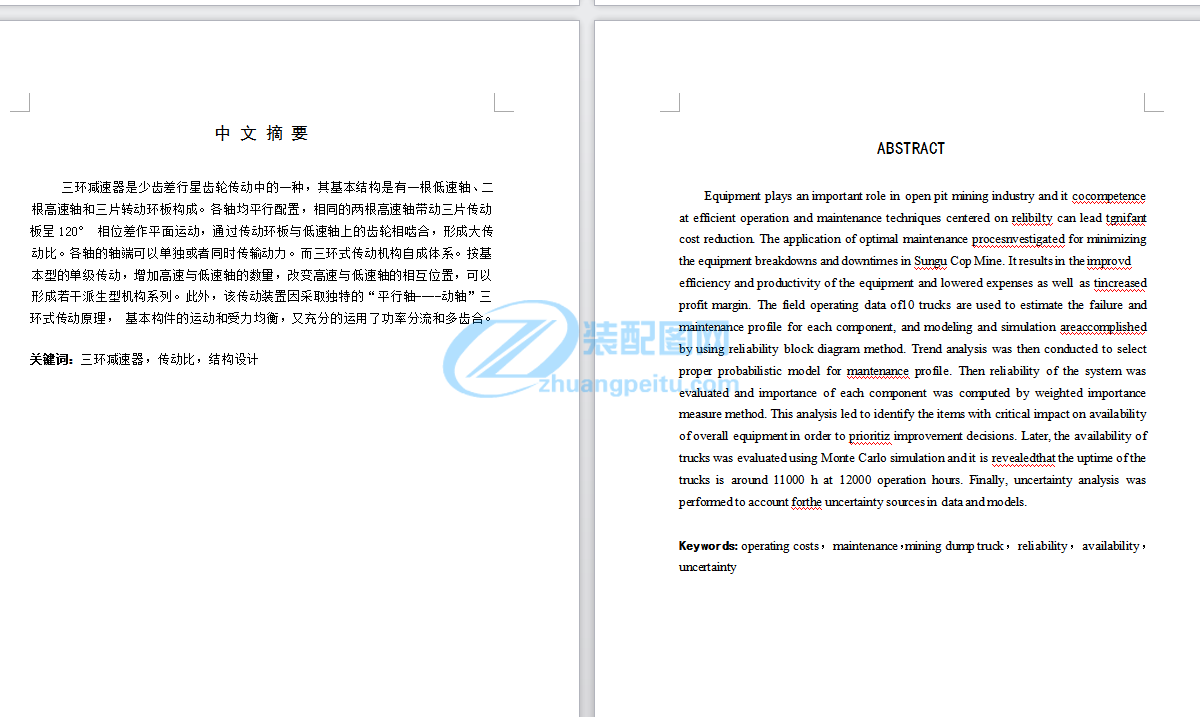

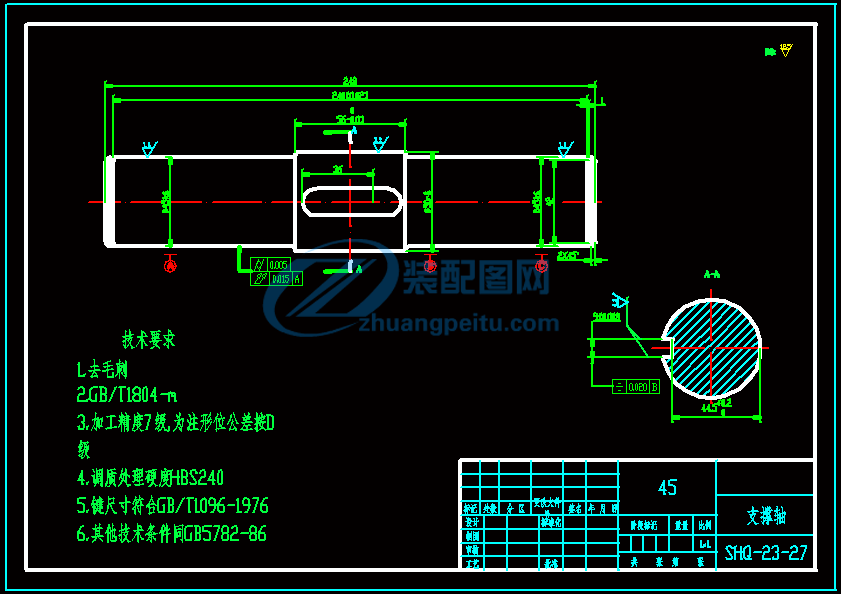
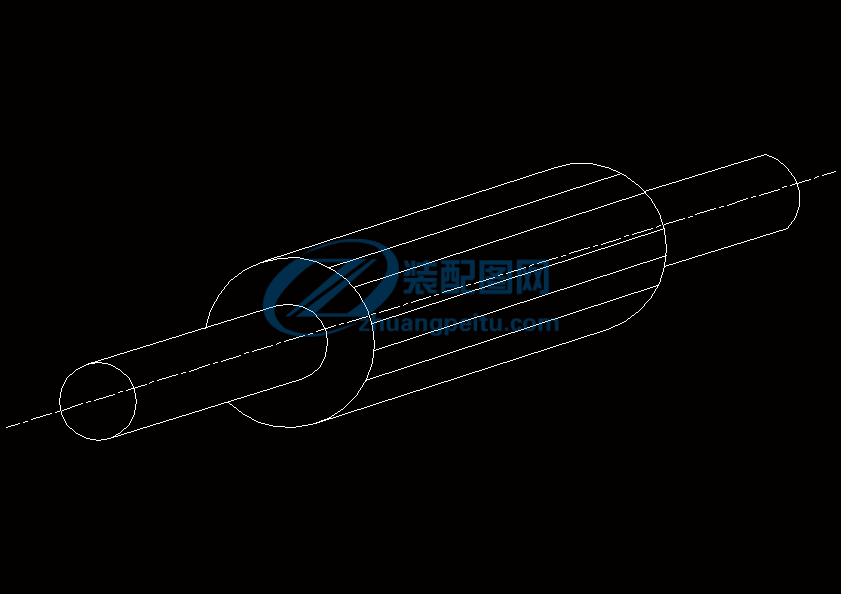
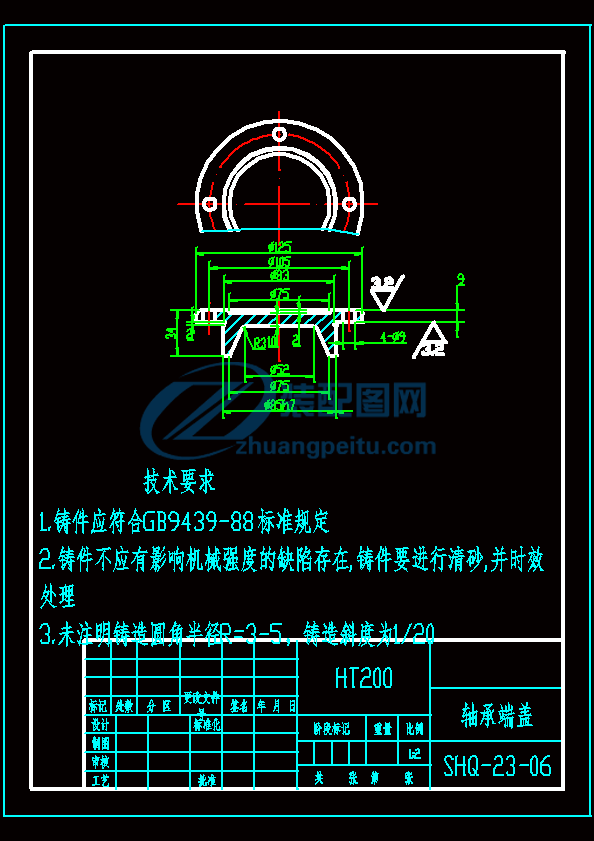
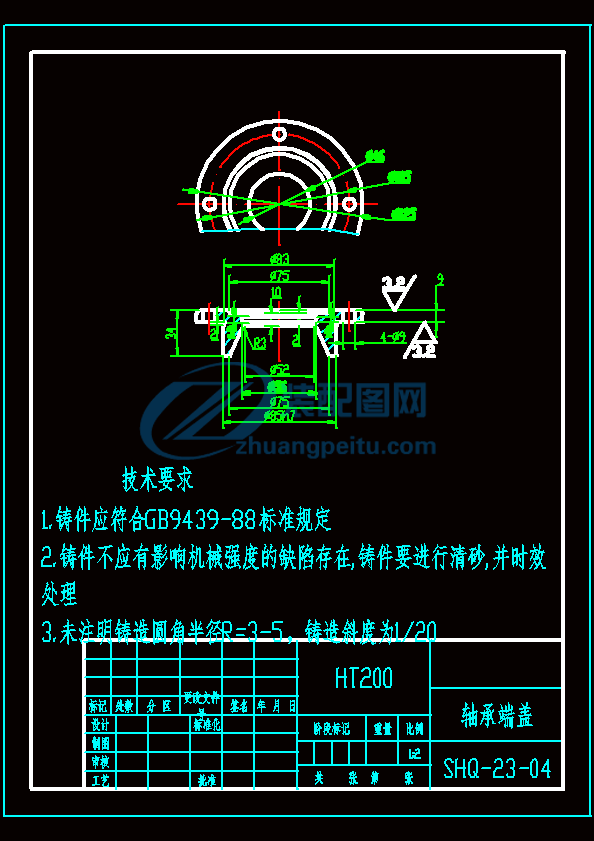
第 0 頁附錄 1 外文文獻(xiàn)Application of reliability-centered maintenance for productivity improvement of open pit mining equipment: Case study of Sungun Copper MineAbstract: Equipment plays an important role in open pit mining industry and its cost competence at efficient operation and maintenance techniques centered on reliability can lead to significant cost reduction. The application of optimal maintenance process was investigated for minimizing the equipment breakdowns and downtimes in Sungun Copper Mine. It results in the improved efficiency and productivity of the equipment and lowered expenses as well as the increased profit margin. The field operating data of 10 trucks are used to estimate the failure and maintenance profile for each component, and modeling and simulation are accomplished by using reliability block diagram method. The field operating data of 10 trucks are used to estimate the failure and maintenance profile for each component, and modeling and simulation are accomplished by using reliability block diagram method Trend analysis was then conducted to select proper probabilistic model for maintenance profile. Then reliability of the system was evaluated and importance of each component was computed by weighted importance measure method. This analysis led to identify the items with critical impact on availability of overall equipment in order to prioritize improvement decisions. Later, Then reliability of the system was evaluated and importance of each component was computed by weighted importance measure method. This analysis led to identify the items with critical impact on availability of overall equipment in order to prioritize improvement decisions. Laterthe availability of trucks was evaluated using Monte Carlo simulation and it is revealed that the uptime of the trucks is around 11000 h at 12000 operation hours. Finally, uncertainty analysis was performed to account for the uncertainty sources in data and models. Key words: operating costs; maintenance; mining dump truck; reliability; availability; uncertainty第 1 頁analyzing the reliability is based on the observed failure 1 Introduction data and proper statistical techniques [3]. Suitable modeling and interpretation of inter-item relationships Surface mining stands for major way of raw are the most important activities in the reliability material production in contemporary mining and have assessment and improvement of the system performance. been continuously modernized during last decades by Evaluation of the reliability is not singly a right indicator introducing ultra large machinery and highly automated for analyzing of a typical system under the recurrent equipment. Trucking is the most conventional and maintenance. Several types of maintenance could be classical method of haulage system in mining industry. In applied on a system including preventive and corrective this regards, loading and hauling equipments are maintenance in order to restore it to operational mode. considered as the most precious assets of an open pit Therefore, this analysis plays an important role in mine which correspond to the vast amount of capital dependability evaluation of repairable items. The invested. Similar to all kind of machineries, trucks also availability is the probability that a component operates need to be carefully preserved under a cautious at an intended mission time. Due to the application of maintenance program which sometimes contributes as both failure and maintenance downtime data, availability 30% to 50% of the whole haulage costs [1]. Accordingly, is generally used for measuring performance of the the current work was aimed to investigate the repairable items [4]. maintenance related to the mining trucks using This work describes the reliability-centered reliability-centered maintenance. maintenance analysis process of the mining dump trucks Reliability and availability are two suitable metrics in Sungun Copper Mine. The aim of the research is for quantitative evaluation of system survival analysis. firstly to decrease trucks’ sudden failures and Reliability is defined as the probability of the system breakdowns as well as to improve the service lifetime mission implementation without occurrence of failure at and finally to reduce the maintenance costs. The a specified time period [2]. In class of statistical methods, reliability management (e.g. improvement) decreases the analysis investigates the effectiveness of the maintenance policy, though, the mine manager can make the preferred decision about the maintenance policy contrarily. In this work, uncertainty analysis is performed due to the uncertain nature of parameters and 第 2 頁lack of sufficient data.Literature review A reliability, availability and maintainability (RAM) program is crucial in an effective maintenance management. This program is used because the failures cannot be prevented entirely; however, well planned maintenance minimizes both probability of failure (increases the reliability) and its impact on the equipment (decreases the equipment breakdown) [5]. The RAM method could be very beneficial in the mining industry because of the complication of the mining equipment operation and maintenance [6]. KUMAR et al [7] investigated the reliability of the load-haul-dump (LHD) machines. The main objective of their research was to analyze failure based on complete and censored data. Their investigation demonstrated that the choice of each approach in utilization of either complete or censored data leads to various directional results. BARABADY and KUMAR [5] studied the reliability and availability of a crushing plant, studied the importance measure to identify the critical sub-systems and highlighted the planning for system reliability improvement. UZG?REN et al [8] analyzed the mechanical failure data of draglines machine. It is considered as a repairable system and then renewal process approach is applied for statistical modeling of the system. HOSEINIE et al [9] also investigated the reliability of the hydraulic system of drum shearer. Accordingly, the maintenance strategy and proper statistical distribution were selected based on failure behavior of the system. Table 1 summarizes the research articles reviewed in conjunction to the reliability evaluation of different mining equipment and demonstrates the failure process models of the equipment restoration rate after a maintenance operation. Methodology and modeling Methodology and analysis process, as illustrated in Fig. 1, describe the procedure of the model identification and selection of the optimal statistical distribution for analysis of the failure and maintenance data. The study started initially by trend analysis of the truck failure times using graphical method. Basically, trend testing is accomplished using either graphical method [21] (i.e., probability plotting [22?23] and time test on plot [24]) or analytical method [25?26] (i.e., Mann test [27], Laplace test [28] and Military Handbook test [18]). Hence, the repairable and non-repairable items of trucks are 第 3 頁identified and the probabilistic failure process methods are distinguished for modeling the maintenance operations. Generally, reliability analysis of the repairable systems is estimated by several assumptions including renewal process (RP), homogenous Poisson process(HPP), non-homogenous Poisson process (NHPP) and generalized renewal process (GRP) [29]. In this work, the RP method is used when the state of the system after the maintenance is “as good as new” which means the age of the system restored to zero. In cases that the system converts to “as bad as old” state, which means the age of system remains unchanged after the maintenance, NHPP is the method of choice whereas, HPP model is applied when the failure intensity is constant and the time between failures follows from the exponential distribution. Hence, the GRP model is assumed to generalize all three presented states for mining trucks. Then, the optimal distribution and its parameters need to be obtained via either parametric or non-parametric approaches. Subsequently, reliability of the system and its components should be evaluated. The availability of the trucks is estimated by using maintenance policy data and reliability functions. The Markov chain method is also used to evaluate the performance and availability of some repairable systems [29]. This is a direction for system analysis which is not used in this work. Case study Sungun Copper Deposit is the second largest copper mine in Iran. Geological reserve of the deposit is estimated up to 828 million tons with average copper grade of 0.62%. The mine operation is managed in the mine site by employing a fleet of 52 and 20 Komatsu 32 and 100 ton trucks, respectively, 11 Caterpillar 988 loader, 1 Liebherr 17 cubic meter shovels, 8 Komatsu PC800 excavators and 9 drilling rigs. This work is limited on the maintenance operation analysis of mine trucks only. Data collection Collection of failure data was the first phase in this project. The failure data come from different sources like field data, generic data, test and inspection data. Due to availability of the collected field data, the modeling and analysis are mostly performed by utilization of this field data. The database is composed of operation time, age of the trucks, maintenance data recorded for the truck’s components. The maintenance and operational 第 4 頁Fig. 1 Flowchart of reliability evaluation 第 5 頁data were collected in time interval of 2010—2011. The equivalent operation times for a month and a year are approximately considered as 500 and 6000 h, respectively. A main obstacle in data collection process was the deficiency of adequate data for the appropriate statistical analyses. There are methods to deal with this situation including expert judgment [30], Bayesian updating method [31], and combination of homogenous data method (similar parts of the equipment). Accordingly, it is assumed that the maintenance data are homogenous in this work. Therefore, the combination of homogenous data technique is applied to deal with the scarcity of data. This method is appropriate for the fleet of equipment or the systems with dominant identical components and similar condition [32]. The assumptions are made in a way that the design, hardware, function, operation conditions, procedures, system structure, location and environment are all similar [18]. Moreover, the age of dump trucks was a major factor for justification of the identical conditions of trucks. Since each system has an intrinsic different failure random behavior at its service lifetime, in this work, 10 dump trucks are chosen with the age of approximately 15000 operation hours. This age is in the region of useful lifetime of trucks. In the useful lifetime, the failure mostly occurs under a systematic process whereas the failure behavior for a new system is based on the infant failure and in older systems, the failure occurs in wear out region. Modeling of system The system of dump truck is decomposed to its sub-systems and components in order to analyze the system reliability. Figure 2 demonstrates the hierarchical decomposing of dump truck system into the main sub- systems and also further decomposition of each sub-system into its components. The failure mode and effect analysis approach were conducted to assess the significant failure modes for each component [33]. The reliability block required for mission success of the dump truck. Therefore, the weakest link model was found a proper model for this purpose. Trend analysis Non-parametric methods are alternatives for analysis of the failure and repair data trend. This analysis provides a curve of the mean cumulative function for mean number of failure at specified time against service lifetime to illustrate the trend of failure data during 第 6 頁total period [34]. If the failure data plot results a straight line, it is concluded that there is no trend. Based on this analysis, each unit is composed of a staircase function that demonstrates the cumulative number of failures for a particular event. Finally, regression of the generated points describes the trend procedure. Also, assembly of units generates a set of staircase curve of each unit in the population, so that the mean cumulative number of failures is estimated. The serial correlation test is used for studying the independence of the failure data. Serial correlation plot is based on i-th lifetime failure against (i?1)-th one. If only one cluster of points is generated then no trend is observed. The trend exists if two or more clusters, or a straight line is generated [18]. Probability plot is used for estimating the statistical distribution parameters when the failure data follow IID condition whereas the GRP method is used whenever the failure data demonstrate a trend. The testing trend and serial correlation for braking sub-system shows that the IID condition is obtained as shown Fig. 3 and Fig. 4, respectively. Fig. 2 Decomposion of dump truck system 第 7 頁Repairable items The trend test is used for performance analysis of the repairable items to identify the failure behavior. The trend analysis of failure data leads to determination of rate of occurrence. It also determines whether the part has increasing failure intensity (IFI) or decreasing failure intensity (DFI). If the intensity function decreases, the system is improving whereas the increasing intensity function leads to deterioration of the system. According to flowchart process exhibited in Fig. 1, the parameters of failure probabilistic distribution of repairable items are computed using GRP technique. GRP model is selected Fig. 7 Downtime for each component 第 8 頁because of its capability to consider the imperfect maintenance data in truck items. Therefore, the TBF data are collected as the input parameter of the PLP model to estimate the statistical parameters. Weibull++8 software is used as the computation tool for the calculations in this work. It is assumed here that the maintenance is imperfect in determining system behavior after a maintenance task on the system components. The restoration rate is estimated for the components after a repair task whose value is specified in range of 0 to 1, where restoration value 0 means no improvement in component status after repair and restoration value 1 is perfect repair making unit as good as new. In this approach the assumptions are more realistic in comparison with traditional methods discussed above which they only consider either minimal repair state (NHPP) or perfect repair state. However, a main challenge in the method is to estimate the restoration rate of item after completion of a maintenance task. It leads to the consider ation of the uncertainties of model for assessment of confidence level in estimation process. Accordingly, two types of maintenance is considered for corrective maintenance activities which are called Types I and II. Type I model assumes that the repairs can remove some portion of the damage which has accumulated since the last repair. In other words, the age of the components after the m-th maintenance immediately return to the age of the (m?1) maintenance considering coefficient of maintenance effectiveness. The model Type II assumes that the repairs can remove a portion of all damage that has accumulated since the system was new. The models of Types I and II are used for calculation respectively as followsConclusions The RAM analyses are essential in the maintenance of the heavy machinery as productivity of the equipment strongly depends on it. In this work, the reliability- centered maintenance is evaluated for the Komatsu mining trucks at the Sungun Copper Mine. The analysis process is comprised for both repairable and non- repairable items. The reliability analysis is implemented for each sub-system at various mission time. The probabilistic failure process modeling is performed for repairable and non-repairable items using the GRP and RP methods, respectively. The importance measure analysis indicates that the wheels are the most critical component. Later, the analysis based on the availability indicates that the mean availability of the dump truck is 91.8% at 12000 operation hours. 第 9 頁The uncertainty analysis is done to find the confidence interval of the estimated equipment reliability and availability. Research findings are provided to the maintenance management team for planning better decisions about the maintenance operation, condition monitoring of the critical items, inventory of the spare parts and their re-order level which leads to reduction in the equipment downtime. This leads to an improvement of the equipment productivity and reduction of the operating costs. The future researches are planned about maintenan第 10 頁附錄 2 中文翻譯應(yīng)用可靠性為中心的維護(hù)效率改善露天采礦設(shè)備:Sun gun 銅礦的案例研究文摘: 設(shè)備扮演著一個(gè)重要的角色在露天采礦行業(yè)及其成本能力,高效的操作和維護(hù)技術(shù)集中在可靠性可能會(huì)導(dǎo)致顯著的降低成本。應(yīng)用最優(yōu)維護(hù)過程是追究最小化Sungun 銅礦的設(shè)備故障和宕機(jī)。它導(dǎo)致設(shè)備提高效率和生產(chǎn)率和降低費(fèi)用以及利潤的增加。10 輛卡車的現(xiàn)場操作數(shù)據(jù)被用來估計(jì)為每個(gè)組件故障和維護(hù)配置文件,和建模與仿真是通過使用可靠性框圖法。然后進(jìn)行趨勢分析為維護(hù)配置文件選擇適當(dāng)?shù)母怕誓P?。然后系統(tǒng)的可靠性進(jìn)行了評(píng)價(jià),計(jì)算了每個(gè)組件的重要性加權(quán)重要性度量方法。這分析導(dǎo)致識(shí)別的項(xiàng)目關(guān)鍵影響整體設(shè)備的可用性,以優(yōu)先改進(jìn)決策。后,卡車的可用性評(píng)估使用蒙特卡羅模擬和顯示卡車的正常運(yùn)行時(shí)間是大約 11000 h 12000 營業(yè)時(shí)間。最后,進(jìn)行不確定性分析,數(shù)據(jù)和模型的不確定性來源。關(guān)鍵詞:運(yùn)營成本:維護(hù),礦業(yè)自動(dòng)傾卸卡車,可靠性,可用, ;不確定介紹地表采礦站為主要原料生產(chǎn)方式在當(dāng)代采礦和不斷現(xiàn)代化通過引入近幾十年來超大型機(jī)械和高度自動(dòng)化設(shè)備。公路運(yùn)輸是最傳統(tǒng)和古典的方法在礦業(yè)運(yùn)輸系統(tǒng)。在這方面,裝載和搬運(yùn)設(shè)備視為最寶貴的資產(chǎn)是露天礦相對(duì)應(yīng)的大量資本投資。類似于各種機(jī)械、卡車也需要精心保存在一個(gè)謹(jǐn)慎的維護(hù)程序,有時(shí)會(huì)為整個(gè)運(yùn)輸成本的30%到 50%。因此 ,當(dāng)前工作的目的是探討維護(hù)相關(guān)采礦卡車使用可靠性為中心的維護(hù)??煽啃院涂捎眯允莾蓚€(gè)合適的系統(tǒng)生存分析的定量評(píng)價(jià)指標(biāo)??煽啃缘亩x是系統(tǒng)任務(wù)實(shí)現(xiàn)而不發(fā)生故障的概率在指定時(shí)間。在類的統(tǒng)計(jì)方法, 可靠性分析是基于觀察到的故障數(shù)據(jù)和適當(dāng)?shù)慕y(tǒng)計(jì)技術(shù)。合適的建模和解釋項(xiàng)間關(guān)系是最重要的活動(dòng)的可靠性評(píng)估和改善系統(tǒng)的性能。單獨(dú)評(píng)估的可靠性并不是正確的指標(biāo)分析復(fù)發(fā)性下的一個(gè)典型的系統(tǒng)維護(hù)。幾種類型的維護(hù)可以應(yīng)用在一個(gè)系統(tǒng)包括預(yù)防和糾正維修以恢復(fù)其運(yùn)營模式。因此,這種分析中發(fā)揮著重要作用可靠性評(píng)價(jià)修復(fù)項(xiàng)目??捎眯缘母怕适且粋€(gè)組件運(yùn)行在一個(gè)預(yù)期的任務(wù)時(shí)間。由于故障和停機(jī)檢修時(shí)間數(shù)據(jù)的應(yīng)用,可用性通常用于測量性能的修復(fù)項(xiàng)目。本工作描述的可靠性為中心的維修分析過程在 Sungun 銅礦礦山自卸卡車。這項(xiàng)研究的目的是首先減少卡車突然失敗和第 11 頁故障以及改善服務(wù)生命周期和最終減少維護(hù)成本。可靠性管理(如改進(jìn))減少失敗的意想不到的失敗,估計(jì)時(shí)間和一個(gè)適當(dāng)?shù)木S修計(jì)劃等預(yù)防性維修和檢驗(yàn)加強(qiáng)服務(wù)生命周期,減少維護(hù)成本。可用性分析調(diào)查的有效性維護(hù)策略,然而,我的經(jīng)理可以首選決定維護(hù)政策相反。在這工作,不確定性分析是由于執(zhí)行的不確定參數(shù)和缺乏足夠的數(shù)據(jù)的性質(zhì)。文獻(xiàn)綜述可靠性、可用性和可維護(hù)性(RAM)計(jì)劃是一個(gè)有效的維修管理的關(guān)鍵。使用這個(gè)程序,因?yàn)楣收喜荒芡耆柚沽?然而,計(jì)劃維護(hù)最小化的概率失敗 (增加了可靠性)及其對(duì)設(shè)備的影響(減少了設(shè)備故障)。RAM 在采礦業(yè)方法可能非常有益,因?yàn)閺?fù)雜的采礦設(shè)備操作和維護(hù)。KUMAR 等調(diào)查的可靠性 load-haul-dump(方面)的機(jī)器。他們的研究的主要目的是分析基于完整和審查數(shù)據(jù)失敗。調(diào)查表明,每種方法的選擇利用完整或?qū)彶閿?shù)據(jù)導(dǎo)致多種定向結(jié)果。BARABADY 和 KUMAR 研究了破碎裝置的可靠性和可用性,研究了測量來確定重要性的關(guān)鍵子系統(tǒng)和強(qiáng)調(diào)了規(guī)劃系統(tǒng)可靠性的改進(jìn)。UZGOREN 等拉鏟挖土機(jī)機(jī)器的機(jī)械故障數(shù)據(jù)分析。它被認(rèn)為是一個(gè)可修系統(tǒng),然后更新過程的統(tǒng)計(jì)建模方法是應(yīng)用系統(tǒng)。HOSEINIE 等也調(diào)查機(jī)的液壓系統(tǒng)的可靠性。因此,維護(hù)策略和選擇適當(dāng)?shù)慕y(tǒng)計(jì)分布基于故障系統(tǒng)的行為。表總結(jié)了研究文章綜述結(jié)合不同采礦設(shè)備的可靠性評(píng)估和演示設(shè)備的故障過程模型維護(hù)操作后恢復(fù)率。方法和建模方法和分析過程,如在圖 1 中,描述了過程模型的識(shí)別和選擇的最優(yōu)統(tǒng)計(jì)分布分析的故障和維護(hù)數(shù)據(jù)。趨勢分析研究開始最初的卡車故障時(shí)間使用圖解法?;旧?趨勢測試完成 (即使用圖形化的方法。,概率策劃(22?23)情節(jié))和時(shí)間測試或分析方法 (即。,曼測試,拉普拉斯試驗(yàn)[28]和軍事手冊測試)。因此,修復(fù)和 non-repairable 物品的卡車識(shí)別和失敗概率過程的建模方法是杰出的維護(hù)操作。一般來說,可修系統(tǒng)的可靠性分析估計(jì)幾個(gè)假設(shè)包括更新過程(RP)、同質(zhì)泊松過程(水電),吸泊松過程(NHPP)和廣義更新過程(GRP)。在這項(xiàng)工作中,RP 方法時(shí)使用系統(tǒng)后維護(hù)的狀態(tài)是“像新的一樣”這意味著年齡的系統(tǒng)恢復(fù)到零。在這種情況下,系統(tǒng)轉(zhuǎn)換為“壞舊”狀態(tài),這意味著系統(tǒng)保持不變的年齡后維護(hù)、NHPP 是選擇的方法而進(jìn)行模型應(yīng)用失效強(qiáng)度恒定時(shí),故障間隔時(shí)間是指數(shù)分布。因此,GRP 模型假設(shè)概括這三個(gè)州采礦卡車。然后,需要獲得最優(yōu)分布及其參數(shù)通過參數(shù)或非參數(shù)方法。隨后,系第 12 頁統(tǒng)的可靠性及其組件應(yīng)該評(píng)估??ㄜ嚨目捎眯砸跃S護(hù)政策,估計(jì)數(shù)據(jù) 4 案例研究。Sungun 銅礦是伊朗的第二大銅礦。地質(zhì)儲(chǔ)備存款估計(jì)多達(dá) 8.28 億噸的銅品位0.62%的平均水平。我的操作管理我的網(wǎng)站采用的 52 個(gè)和 20 個(gè)小松 32 和 100 噸卡車,分別 11 988 年卡特彼勒裝載機(jī),1 利勃海爾 17 立方米鏟子,8 小松 PC800 挖掘機(jī)和 9 鉆機(jī)。這項(xiàng)工作是有限的維護(hù)操作。數(shù)據(jù)采集故障數(shù)據(jù)收集是我們這個(gè)項(xiàng)目的第一階段。失敗來自不同數(shù)據(jù)源的數(shù)據(jù)字段數(shù)據(jù),通用數(shù)據(jù)、測試和檢驗(yàn)數(shù)據(jù)。由于收集現(xiàn)場數(shù)據(jù)的可用性,執(zhí)行的建模和分析主要是利用這一領(lǐng)域的數(shù)據(jù)。數(shù)據(jù)庫是由操作時(shí)間、年齡的卡車,卡車的記錄維護(hù)數(shù)據(jù)組件。維護(hù)和操作數(shù)據(jù)收集 2010 - 2011 年的時(shí)間間隔。相當(dāng)于操作時(shí)間為一個(gè)月,一年大約是 500 年和 6000 年,分別。數(shù)據(jù)收集過程的一個(gè)主要障礙是缺乏足夠的適當(dāng)?shù)慕y(tǒng)計(jì)分析數(shù)據(jù)。有方法來處理這種情況包括專家判斷,貝葉斯更新方法,并結(jié)合同類數(shù)據(jù)的方法(類似部分的設(shè)備)。因此,假設(shè)同質(zhì)維護(hù)數(shù)據(jù)開展這方面的工作。因此,同質(zhì)數(shù)據(jù)技術(shù)的結(jié)合應(yīng)用于處理數(shù)據(jù)的匱乏。這種方法適合設(shè)備或系統(tǒng)的艦隊(duì)主要相同組件和相似條件。的假設(shè)是,設(shè)計(jì)、硬件、功能、操作條件、過程、系統(tǒng)結(jié)構(gòu)、位置和環(huán)境都是相似的。此外,自卸卡車的年齡是一個(gè)主要因素的理由相同條件的卡車。因?yàn)槊總€(gè)系統(tǒng)都有一個(gè)內(nèi)在的不同故障隨機(jī)行為在其服務(wù)壽命,在這工作,選擇 10 自卸卡車的年齡大約 15000 營業(yè)時(shí)間。這個(gè)年齡是在該地區(qū)的有用的一生的卡車。有用的一生,失敗主要發(fā)生在一個(gè)系統(tǒng)的過程,而行為的新系統(tǒng)是基于嬰兒失敗和在舊系統(tǒng)中,發(fā)生故障時(shí)的磨損。系統(tǒng)的建模系統(tǒng)的自動(dòng)傾卸卡車分解子系統(tǒng)和組件以分析系統(tǒng)的可靠性。下圖演示了自動(dòng)傾卸卡車系統(tǒng)的層次分解為主要的附屬系統(tǒng),也進(jìn)一步分解每個(gè)子系統(tǒng)為其組件。失效模式與效應(yīng)分析方法進(jìn)行評(píng)估的重要失效模式為每個(gè)組件。的系統(tǒng)的可靠性框圖開發(fā)基于其結(jié)構(gòu)。由于卡車的設(shè)計(jì)配置系統(tǒng),考慮接頭的操作——系統(tǒng)所需的任務(wù)自動(dòng)傾卸卡車的成功。因此,最薄弱的一環(huán)模型被發(fā)現(xiàn)一個(gè)合適的模型。第 13 頁Fig. 1 Flowchart of reliability evaluation 第 14 頁趨勢分析的非參數(shù)方法替代分析故障和修復(fù)數(shù)據(jù)的趨勢。這種分析提供了一種曲線的平均累積函數(shù)平均數(shù)量的失敗在指定的時(shí)間對(duì)服務(wù)生命周期總期間說明故障數(shù)據(jù)的趨勢[34]。如果故障數(shù)據(jù)分析結(jié)果一條直線,得出沒有趨勢。在此基礎(chǔ)上分析,每個(gè)單元由一個(gè)階梯函數(shù),證明了失敗的累積數(shù)量為特定事件。最后,生成的點(diǎn)描述趨勢回歸過程。另外,組裝單元生成一組樓梯曲線中每個(gè)單元的人口,這樣平均累積