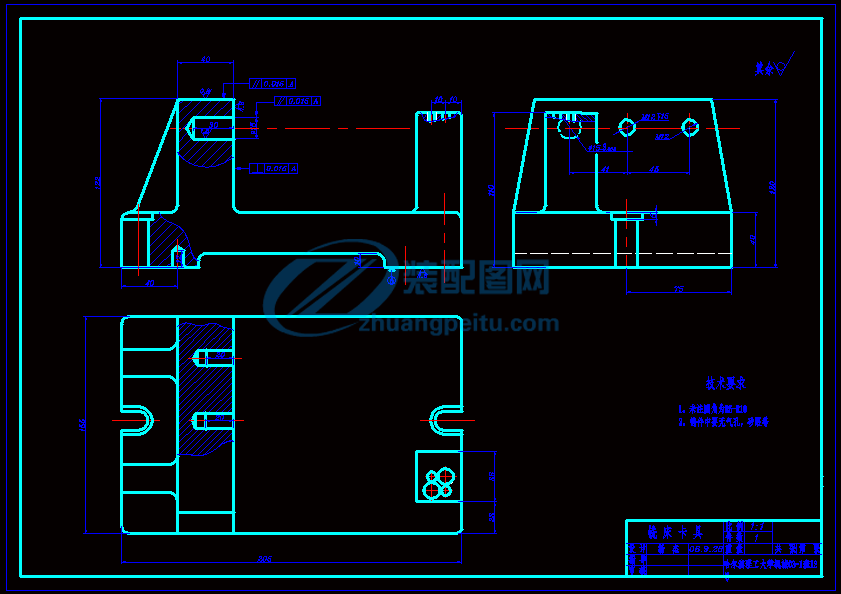
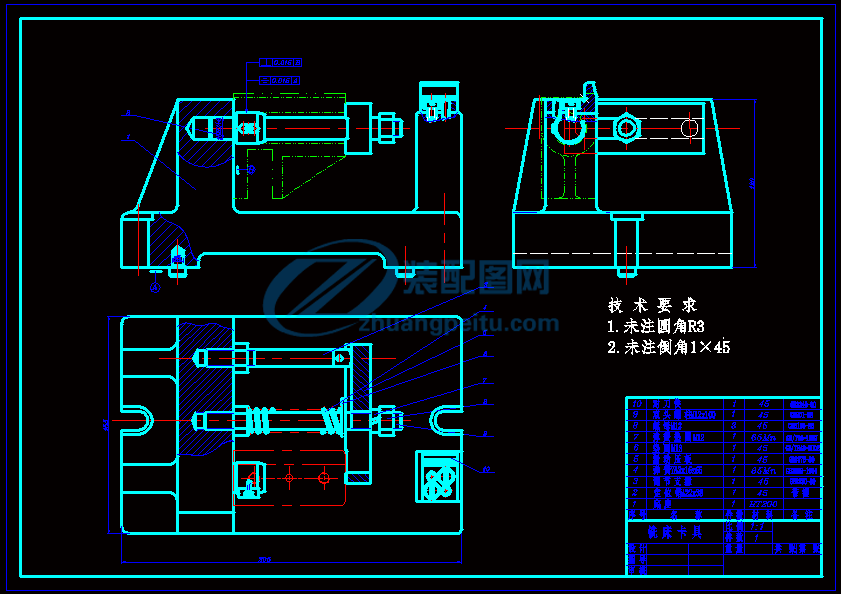
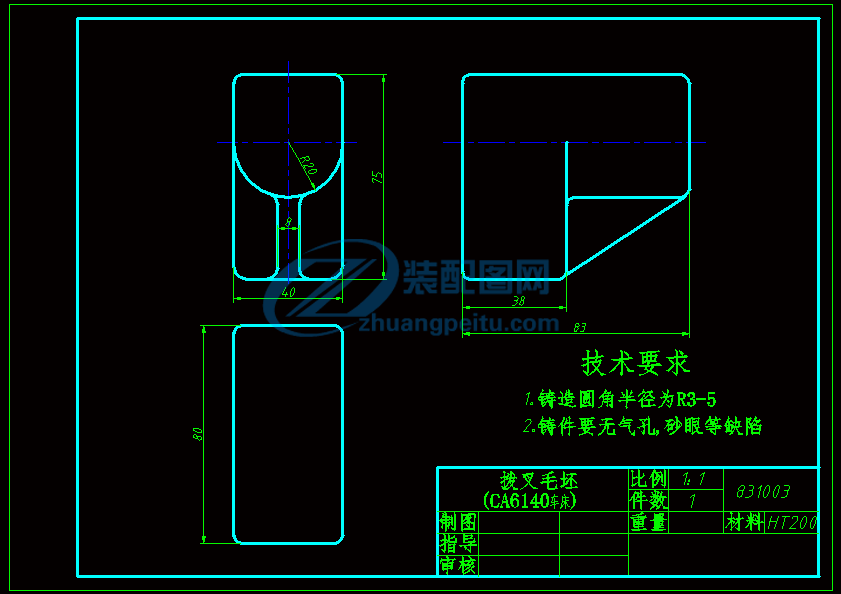
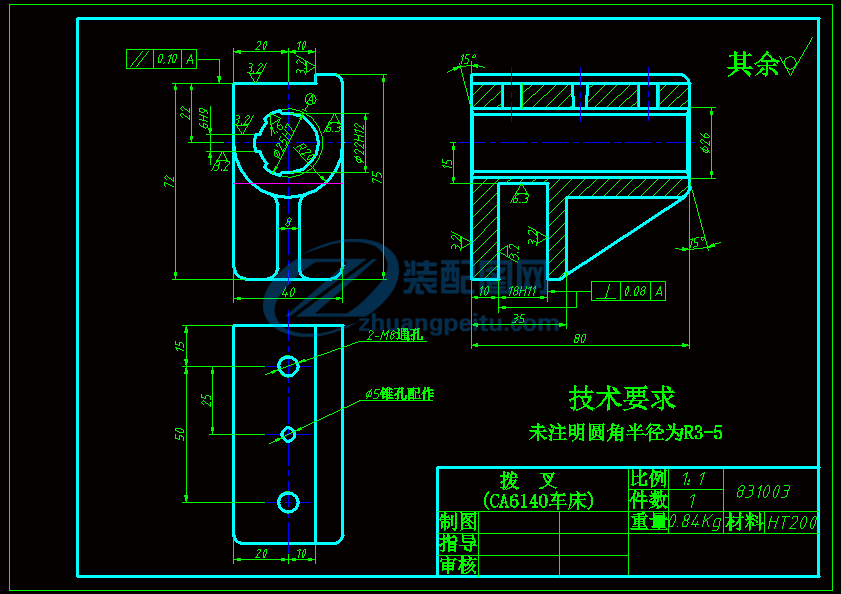

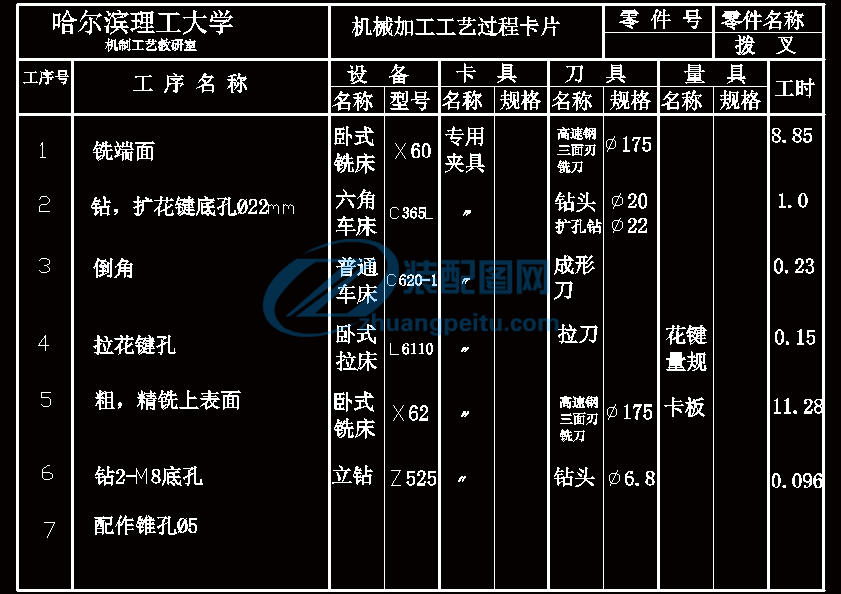
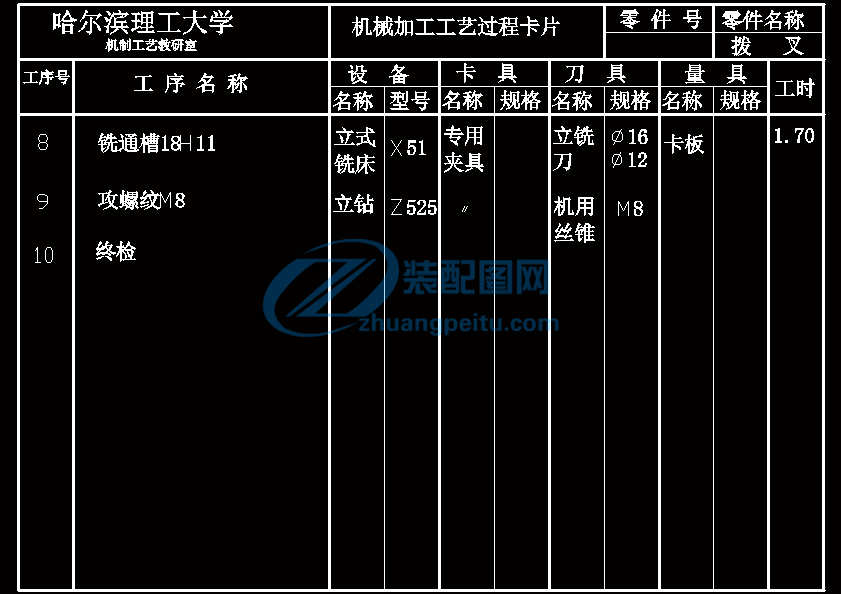
機械制造基礎(chǔ)課程設(shè)計設(shè)計題目:制定撥叉零件的加工工藝,設(shè)計銑 30×80 面的銑床夾具班 級:機械 03-1 班學(xué) 生:楊 杰指導(dǎo)教師:熬 曉 春 哈爾濱理工大學(xué)2006-9-21- 1 -目 錄設(shè)計任務(wù)書一、 零件的分析………………………………………(3)二、 工藝規(guī)程設(shè)計……………………………………(3)(一) 、確定毛坯的制造形式……………………(3)(二) 、基面的選擇………………………………(3)(三) 、制訂工藝路線……………………………(3)(四) 、機械加工余量、工序尺寸及毛坯尺才的確定……………………………………………(4)(五) 、確定切削用量及基本工時………………(5)三、 夾具設(shè)計…………………………………………(11)四、 參考文獻(xiàn)…………………………………………(13)- 2 -哈爾濱理工大學(xué)機械制造工藝及夾具課程設(shè)計任務(wù)書設(shè)計題目:制定撥叉 F 零件的加工工藝,設(shè)計銑 30×80 面的銑床夾具設(shè)計要求:1.中批生產(chǎn);2.盡量選用通用設(shè)備。設(shè)計內(nèi)容:1.填寫設(shè)計任務(wù)書;2.制訂一個中等零件的加工工藝過程,填寫工藝過程卡和工序卡各一張;3.設(shè)計指導(dǎo)教師指定的工序夾具,繪制全套夾具圖紙,要求用計算機繪圖;4.編寫設(shè)計說明書一份,按照畢業(yè)論文的格式寫,要求打印文稿。班 級:機械 03-1 班學(xué) 生:楊 杰 指導(dǎo)教師:熬 曉 春 2006 年 9 月 10 日- 3 -一、零件的分析(一)零件的工藝分析撥叉這個零件從零件圖上可以看出,它一共有兩組加工表面,而這二組加工表面之間有一定的位置要求,現(xiàn)將這二組加工表面分述如下:1.以 ?25mm 孔為中心的加工表面。這一組加工表面包括: ?25H7mm 的l 六齒花鍵孔及倒角,尺寸為 80㎜與花鍵孔垂直的兩端面,尺寸為 18H11 與花鍵孔垂直的通槽。2.與 ?25mm 花鍵孔平行的表面。這一組加工表面包括:與花鍵孔中心軸線相距 22㎜的上表面,與上表面垂直的二個 M8 通孔和一個 ? 5 錐孔。這兩組加工表面之間有著一定的位置要求,主要是:1.上表面與 ?25mm 花鍵孔中心線平行度為 0.10㎜ ;2.18H11 通槽兩側(cè)面與與 ?25mm 花鍵孔中心線的垂直度為 0.08㎜。由以上分析可知,對于這二組加工表面而言,我們可以先加工其中一組表面,然后借助于專用夾具進(jìn)行另一組表面的加工,并且保證它們之間的位置精度要求。二、 工藝規(guī)程設(shè)計(一)確定毛坯的制造形式零件材料為 HT200,考慮到該零件在車床中的受力并保證零件的工作可靠性,零件為中批生產(chǎn),而且零件的尺寸不大,因此,毛坯可采用金屬模砂型鑄造。(二)基面的選擇基準(zhǔn)面選擇是工藝規(guī)程設(shè)計中的重要工作之一?;孢x擇的正確與合理,可以使加工質(zhì)量得到保證,生產(chǎn)效率得以提高。否則,加工工藝過程中會問題百出,更有甚者,還會造成零件大批報廢,使生產(chǎn)無法正常進(jìn)行。粗基準(zhǔn)的選擇:以上下表面和兩 側(cè)面作為粗基準(zhǔn),以消除 , , 三個zxy自由度,用以消除 , , 三個自由度,達(dá)到完全定位。xyz對于精基準(zhǔn)而言,根據(jù)基準(zhǔn)重合原則,選用設(shè)計基準(zhǔn)作為精基準(zhǔn)。(三) 制訂工藝路線制訂工藝路線的出發(fā)點,應(yīng)當(dāng)是使零件的幾何形狀,尺寸精度及位置精度等技術(shù)要求得到合理的保證。在生產(chǎn)綱領(lǐng)為中批生產(chǎn)的條件下,可以考慮采用萬能性機床配以專用夾具來提高生產(chǎn)效率。除此以外,還應(yīng)當(dāng)考慮經(jīng)濟(jì)效率,以便使生產(chǎn)成本盡量下降。1.工藝路線方案一工序Ⅰ 銑端面。工序Ⅱ 鉆、擴花鍵底孔 ?22mm。- 4 -工序Ⅲ 內(nèi)花鍵孔倒角。工序Ⅳ 拉花鍵孔。工序Ⅴ 銑上、下表面。工序Ⅵ 鉆 2—M8 孔,?5mm 錐孔。工序Ⅶ 銑通槽 18H11㎜。工序Ⅷ 攻螺紋 2—M8。工序Ⅸ 去毛刺。工序Ⅹ 檢查。2.工藝路線方案二工序Ⅰ 銑端面。工序Ⅱ 鉆、擴花鍵底孔 ?22mm。工序Ⅲ 內(nèi)花鍵孔倒角。工序Ⅳ 銑上、下表面。工序Ⅴ 鉆 2—M8 孔,?5mm 錐孔。工序Ⅵ 銑通槽 18H11㎜。工序Ⅶ 拉花鍵孔。工序Ⅷ 攻螺紋 2—M8。工序Ⅸ 去毛刺。工序Ⅹ 檢查。工藝方案的比較與分析上述兩個工藝方案的特點在于:方案一是先拉花鍵孔,再以該花鍵孔為基準(zhǔn)加工其余平面;方案二是先加工上下面,再加工花鍵孔。兩相比較可以看出,方案一可以避免加工上表面和槽的設(shè)計基準(zhǔn)和加工基準(zhǔn)不重合的問題,而方案而不能,所以選用方案一作為零件的加工工序。(四)機械加工余量、工序尺寸及毛坯尺寸的確定 “撥叉”零件材料為 HT200,毛坯重量約為 1.00Kg,生產(chǎn)類型為中批生產(chǎn),采用金屬砂型鑄造。根據(jù)上述原始資料及加工工藝,分別確定各加工表面的機械加工余量、 工序尺寸及毛坯尺寸如下:1. 銑端面考慮左端面的粗糙度 Ra 為 3.2,參照《機械制造工藝設(shè)計手冊 》——以下簡稱“手冊” ,表 1—43,確定工序尺寸為 Z=3.0mm,其中粗加工的加工余量 Z=2.0mm,精加工的加工余量 Z=1.0mm。右端面沒有粗糙度要求,只要求粗加工,所以余量定位 3.0㎜。2. 花鍵孔(6-?25H7×?22H12×6H11) 。要求花鍵孔為外徑定心,故采用拉削加工。內(nèi)孔 ?22H12㎜:鉆孔:?20㎜- 5 -擴鉆:?22㎜ 2Z=2.0㎜拉花鍵孔(6-?25H7×?22H12×6H11)花鍵孔要求外徑定心,花鍵內(nèi)徑拉削時的加工余量為孔的公差 0.17㎜。3.銑表面根據(jù)“手冊”表 1—49,取上表面的機械加工余量為 4.0㎜,下表面的余量為 3.0㎜。粗銑上表面 Z=3.0㎜精銑上表面的臺階面 Z=1.0㎜粗銑下表面 Z=3.0㎜4. 銑通槽 18H11㎜粗銑 16㎜ 2Z=4.0㎜半精銑 18㎜ 2Z=2.0㎜毛坯制造尺寸及技術(shù)要求見毛坯圖。(五)確定切削用量及基本工時工序Ⅰ:銑端面。1)粗銑左端面α =0.25mm/Z (表 3-28)fν=0.35m/s( 21m/min) (表 3-30)采用高速三面刃銑刀,d =175mm,齒數(shù) Z=16。wn = = =0.637r/s (38.2r/min)sd10?π v1753.40?按機床選取 n =31.5r/min=0.522r/s (表 4—17)w故實際切削速度 ν= =0.29m/s10ndsw?π切削工時 l=75mm,l =175mm,l =3mm12t = = =121.2s=2.02minmZnfw2??α 615.0.37??2)粗銑右端面粗銑右端面的進(jìn)給量、切削速度和背吃刀量與粗銑左端面的切削用量相同。切削工時l=45mm,l =175mm,l =3mm12- 6 -t = = =106.8s=1.78minmZnlfw21??α 6125.0.374??3)精銑左端面α =0.10mm/Z (表 3-28)fν=0.30m/s( 18m/min) (表 3-30)采用高速三面刃銑刀,d =175mm,齒數(shù) Z=16。wn = = =0.546r/s (32.76r/min)sd10?π v1753.40?按機床選取 n =31.5r/min=0.522r/s (表 4—17)w故實際切削速度 ν= =0.29m/s10ndsw?π切削工時 l=75mm,l =175mm,l =3mm12t = = =302.92s=5.05minmZnfw2??α 610.5.37??工序Ⅱ:鉆、擴花鍵底孔1)鉆孔 ? 20㎜f=0.75mm/r·K =0.75×0.95=0.71㎜/s (表 3—38)flν=0.35m/s ( 21m/min) (表 3—42)n = = =5.57r/s (334r/min)swd10?π v203.45?按機床選取 n =338r/min=5.63r/s故實際切削速度 ν= =0.35m/s 10ndsw?π切削工時 l=80mm,l = 10mm,l =2mm2- 7 -t = = =23s (0.4min)mf??w21nl71.063528?2)擴孔 ? 22㎜f=1.07 (表 3—54)ν=0.175m/s ( 10.5m/min) n = = =2.53r/s (151.8r/min)swd10?π v23.14750?按機床選取 n =136r/min=2.27r/s故實際切削速度 ν= =0.16m/s 10ndsw?π切削工時 l=80mm,l = 3mm,l =1.5mm2t = = =35s (0.6min)mf??w21nl07.1538?工序Ⅲ:倒角 1.07×15?f=0.05㎜/r (表 3—17)ν=0.516m/s (參照表 3—21) n = = =6.3r/s (378r/min)swd10?π v26.1450?按機床選取 n =380r/min=6.33r/s切削工時 l=2.0mm,l = 2.5mm,1t = = =14s (0.23min)mf??w1nl05.362?工序Ⅳ:拉花鍵孔單面齒升 0.05㎜ (表 3—86)v=0.06m/s ( 3.6m/min) (表 3—88)切削工時 (表 7—21)t =mZSvKlhz??10?- 8 -式中:h——單面余量 1.5㎜(由 ? 22㎜—? 25㎜) ;l——拉削表面長度 80㎜;——考慮標(biāo)準(zhǔn)部分的長度系數(shù),取 1.20;?K——考慮機床返回行程的系數(shù),取 1.40;V——切削速度 3.6m/min;S ——拉刀同時工作齒數(shù) Z=L/t。zt——拉刀齒距,t=(1.25—1.5) =1.35 =12㎜L80Z=L/t=80/12 6 齒??t = =0.15min (9s)m.31042.??工序Ⅴ:銑上、下表面1)粗銑上表面的臺階面α =0.15mm/Z (表 3-28)fν=0.30m/s( 18m/min) (表 3-30)采用高速三面刃銑刀,d =175mm,齒數(shù) Z=16。wn = = =0.546r/s (33r/min)sd10?π v1753.40?按機床選取 n =30r/min=0.5r/s (表 4—17)w故實際切削速度 ν= =0.27m/s10ndsw?π切削工時 l=80mm,l =175mm,l =3mm12t = = =215s=3.58minmZnfw2??α 615.0378??2)精銑臺階面α =0.07mm/Z (表 3-28)fν=0.25m/s( 18m/min) (表 3-30)采用高速三面刃銑刀,d =175mm,齒數(shù) Z=16。w- 9 -n = = =0.455r/s (33r/min)swd10?π v1753.420?按機床選取 n =30r/min=0.5r/s (表 4—17)故實際切削速度 ν= =0.27m/s10ndsw?π切削工時 l=80mm,l =175mm,l =3mm12t = = =467s=7.7minmZnfw2??α 6170.538??3)粗銑下表面保證尺寸 75㎜本工步的切削用量與工步 1)的切削用量相同 切削工時 l=40mm, l =175mm,l =3mm2t = = =181.7s=3.03minmZnfw21??α 615.0374??工序Ⅵ:鉆 2-M8 底孔(? 6.80㎜)f=0.36㎜/r (表 3—38)ν=0.35m/s (參照表 3—42) n = = =16.39r/s (983.4r/min)swd10?π v8.6450?按機床選取 n =960r/min=16r/s故實際切削速度 ν= =0.34m/s10ndsw?π切削工時(表 7—5) l=9.5mm,l = 4mm,l =3㎜12t = = =2.86 (0.048min)mf??wn36.04?工序Ⅶ:銑槽 18H111)粗銑 α =0.10㎜/s (表 3-28)f- 10 -ν=0.30m/s( 21m/min) (表 3-30)采用粗齒直柄立銑刀,d =16mm,齒數(shù) Z=3。wn = = =5.97/s (358.2/min)swd10?π v613.40?按機床選取 n =380r/min=6.33/s (表 4—16)故實際切削速度 ν= =0.32/s10ndsw?π切削工時 l=34mm,l =2mm,l =0mm12t = = =19smZnfw2??α 301.64??因為要走刀兩次,所以切削工時為 38s。2)精銑通槽α =0.07/s(表 3-28)fν=0. 25m/s(15m/min) (表 3-30)采用細(xì)齒直柄立銑刀,d =12mm,齒數(shù) Z=5。wn = = =6.63s (397.8min)sw10?π v213.450?按機床選取 n =380r/min=6.33/s (表 4—16)故實際切削速度 ν= =0.24s10ndsw?π切削工時 l=35mm,l =2mm,l =0mm12t = = =16smZnfw2??α 507.36??因為走刀兩次,所以切削工時為 64s。Ⅷ:攻螺紋 2—M8v=0.35m/s (表 3—42)- 11 -n = = =13.9 (834min)swd10?π v83.1450?按機床選取 n =850r/min=14.2s 故實際切削速度 ν= =0.357m/s。10ndsw?π三、專用夾具設(shè)計為了提高勞動生產(chǎn)率,保證加工質(zhì)量,降低勞動強度,需要設(shè)計專用夾具。(一) 切削力及夾緊力的計算切削刀具:高速鋼直齒三面刃銑刀,則主切削力 zFfwFueyxpz KndZaCF6081.9??式中: 3.1?65.0F83.0?Fu0Fw83.0Fqmap16?ae8.f 67.)3.019(.zFk計算結(jié)果 = 2448Nz由于切削力對夾緊力影響不大,故夾緊力只需達(dá)到將工件固定即可。(二) 定位誤差分析(1) 定位元件尺寸及公差確定。夾具的主要定位元件為 孔的定位銷,孔與銷間隙配合。25?(2) 工件的工序基準(zhǔn)為孔心,當(dāng)工件孔徑為最大,定位銷的孔徑為最小時,孔心在任意方向上的最大變動量等于孔與銷配合的最大間隙量。本夾具是用來在臥式鏜床上加工,所以工件上孔與夾具上的定位銷保持固定接觸。此時可求出孔心在接觸點與銷中心連線方向上的最大變動量為孔徑公差多一半。工件的定位基準(zhǔn)為孔心。工序尺寸方向與固定接觸點和銷中心連線方向相同,則其定位誤差為: Td=Dmax-Dmin 基準(zhǔn)位移誤差△y 由于孔和銷都有制造誤差,為工件裝卸方便還有最小間隙(次間隙可以在調(diào)刀尺寸和對刀時消除)- 12 -由制造誤差引起的△y=(Dmax-dmin)/2-(Dmin-dmax)/2=(0.023+0,020)/2=0.02150.08在垂直度要求范圍內(nèi)本工序采用一定位銷,一擋銷定位,工件始終靠近定位銷的一面,而擋銷的偏角會使工件自重帶來一定的平行于夾具體底版的水平力,因此,工件不在在定位銷正上方,進(jìn)而使加工位置有一定轉(zhuǎn)角誤差。但是,由于加工是自由公差,故應(yīng)當(dāng)能滿足定位要求。四、參考文獻(xiàn)1.《機械制造工藝學(xué)課程設(shè)計指導(dǎo)書》 機械工業(yè)出版社 趙家齊 編2.《機械制造工藝設(shè)計手冊》 機械工業(yè)出版社 王紹俊 編3.《機床夾具設(shè)計》 哈爾濱工業(yè)大學(xué)出版社 王啟平 編