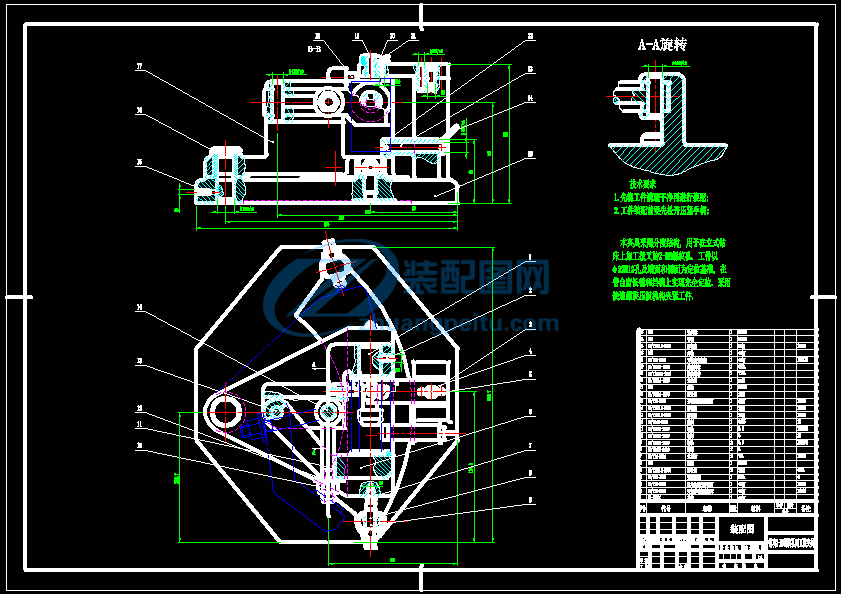
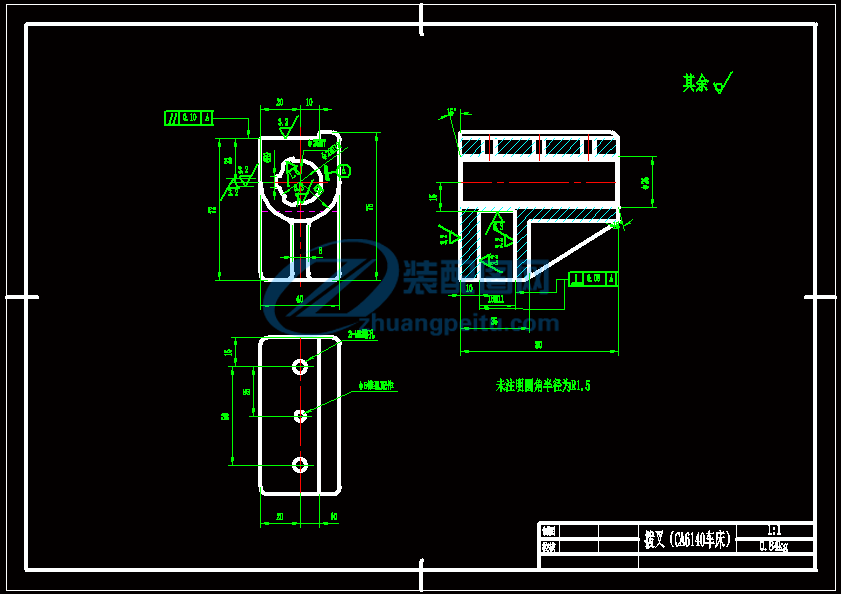
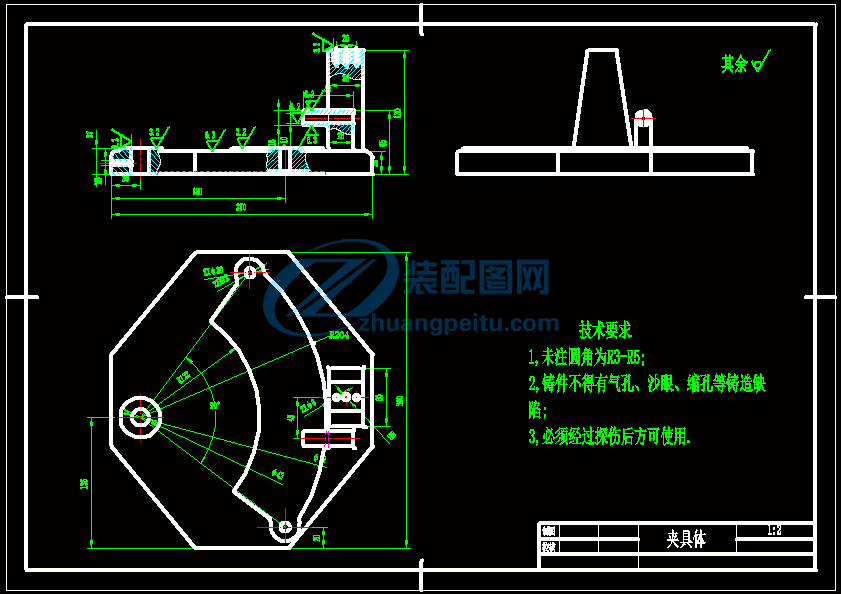
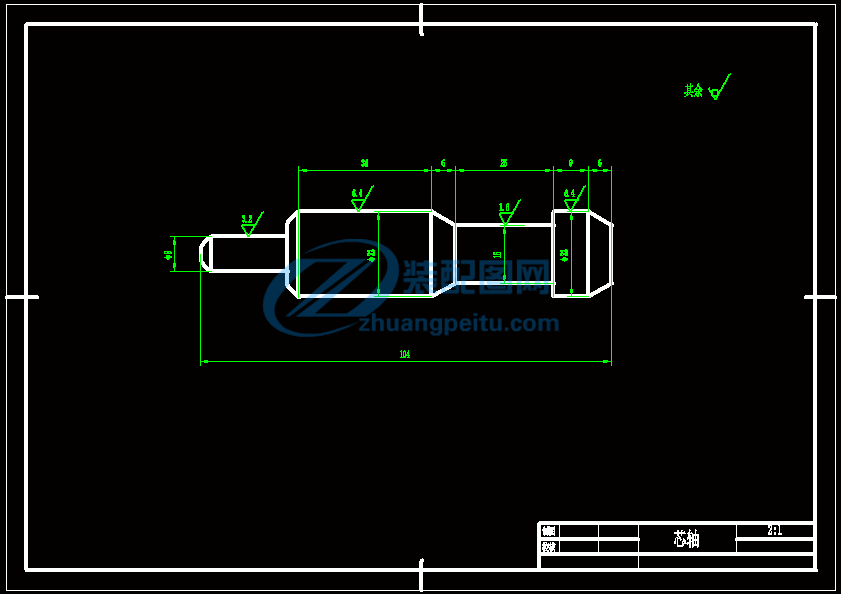

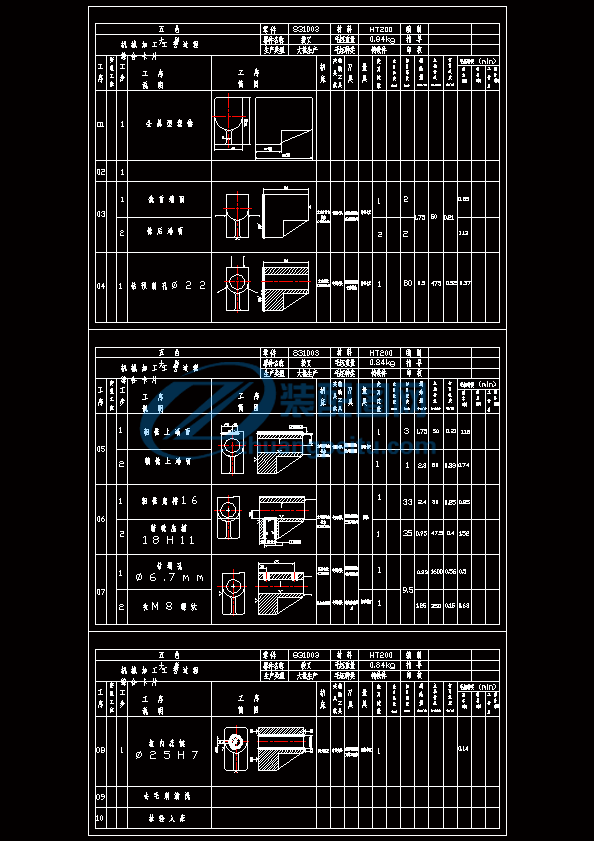
1序言機(jī)械制造工藝學(xué)課程設(shè)計(jì)是在我們學(xué)完了大學(xué)的全部基礎(chǔ)課,技術(shù)基礎(chǔ)課以及大部分專業(yè)課之后進(jìn)行的。這是我們?cè)谶M(jìn)行畢業(yè)設(shè)計(jì)之前對(duì)所學(xué)各課程的一次深入的綜合性的總復(fù)習(xí),也是一次理論聯(lián)系實(shí)際的訓(xùn)練,因此,它在我們四年的大學(xué)生活中占有重要的地位。就我個(gè)人而言,我希望能通過這次課程設(shè)計(jì)對(duì)自己末來將從事的工作進(jìn)行一次適應(yīng)性訓(xùn)練,從中鍛煉自己分析問題,解決問題的能力,為今后參加祖國的“四化”建設(shè)打下一個(gè)良好的基礎(chǔ)。由于能力所限,設(shè)計(jì)尚有許多不足之處,懇請(qǐng)老師給予指導(dǎo)。一、零件的分析(一)零件的作用題目所給的零件是 CA6140 車床的撥叉。它位于車床變速機(jī)構(gòu)中,主要起換擋,使主軸回轉(zhuǎn)運(yùn)動(dòng)按照工作者的要求工作,獲得所需的速度和扭矩的作用。(二)零件的工藝分析撥叉是一個(gè)很重要的零件,因?yàn)槠淞慵叽绫容^小,結(jié)構(gòu)形狀較復(fù)雜,其加工內(nèi)花鍵的精度要求較高,此外還有上端面要求加工,對(duì)精度要求也很高。其底槽側(cè)邊與花鍵孔中心軸有垂直度公差要求,上端面與花鍵孔軸線有平行度要求。因?yàn)槠涑叽缇取缀涡螤罹群拖嗷ノ恢镁?,以及各表面的表面質(zhì)量均影響機(jī)器或部件的裝配質(zhì)量,進(jìn)而影響其性能與工作壽命,因此它們的加工是非常關(guān)鍵和重要的。(三)零件的工藝要求一個(gè)好的結(jié)構(gòu)不但要應(yīng)該達(dá)到設(shè)計(jì)要求,而且要有好的機(jī)械加工工藝性,也就是要有加工的可能性,要便于加工,要能夠保證加工質(zhì)量,同時(shí)使加工的勞動(dòng)量最小。而設(shè)計(jì)和工藝是密切相關(guān)的,又是相輔相成的。設(shè)計(jì)者要考慮加工工藝問題。工藝師要考慮如何從工藝上保證設(shè)計(jì)的要求。其加工有四組加工: 內(nèi)花鍵孔;粗精銑上端面;粗精銑257H?18H11 底槽;鉆、鉸 2-M8 通孔,并攻絲。(1) .以 為主要加工面,拉內(nèi)花鍵槽 ,槽數(shù)為 6 個(gè),21H? 257H?其粗糙度要求是底邊 ,側(cè)邊 , 內(nèi)孔粗糙度6.1?Ra3.Ra?1。6.3Ra?(2) .另一組加工是粗精銑上端面,表面粗糙度要求為 。3.2Ra?(3) .第三組為粗精銑 18H11 底槽,該槽的表面粗糙度要求是兩槽2邊 ,槽底的表面粗糙度要求是 。3.2Ra? 3.6?Ra(4) .鉆并攻絲 2-M8。(四)毛坯的選擇撥叉毛坯選擇金屬型澆鑄,因?yàn)樯a(chǎn)率很高,所以可以免去每次造型。單邊余量一般在 ,結(jié)構(gòu)細(xì)密,能承受較大的壓力,m3~1占用生產(chǎn)的面積較小。并且此零件為中批或大批生產(chǎn)。二、工藝規(guī)程設(shè)計(jì)(一)工藝加工過程由以上分析可知。該撥叉零件的主要加工表面是平面、內(nèi)花鍵和槽系。一般來說,保證平面的加工精度要比保證內(nèi)花鍵的加工精度容易。因此,對(duì)于撥叉來說,加工過程中的主要問題是保證內(nèi)花鍵的尺寸精度及位置精度,處理好內(nèi)花鍵和平面之間的相互關(guān)系以及槽的各尺寸精度。由上工藝分析知,上端面與槽邊均與花鍵軸有位置度公差,所以,保證內(nèi)花鍵高精度是本次設(shè)計(jì)的重點(diǎn)、難點(diǎn)。(二)確定各表面加工方案一個(gè)好的結(jié)構(gòu)不但應(yīng)該達(dá)到設(shè)計(jì)要求,而且要有好的機(jī)械加工工藝性,也就是要有加工的可能性,要便于加工,要能保證加工的質(zhì)量,同時(shí)是加工的勞動(dòng)量最小。設(shè)計(jì)和工藝是密切相關(guān)的,又是相輔相成的。對(duì)于設(shè)計(jì)撥叉的加工工藝來說,應(yīng)選擇能夠滿足內(nèi)花鍵加工精度要求的加工方法及設(shè)備。除了從加工精度和加工效率兩方面考慮以外,也要適當(dāng)考慮經(jīng)濟(jì)因素。在滿足精度要求及生產(chǎn)率的條件下,應(yīng)選擇價(jià)格較底的機(jī)床。1、在選擇各表面、內(nèi)花鍵及槽的加工方法時(shí),要綜合考慮以下因素(1) .要考慮加工表面的精度和表面質(zhì)量要求,根據(jù)各加工表面的技術(shù)要求,選擇加工方法及分幾次加工。(2) .根據(jù)生產(chǎn)類型選擇,在大批量生產(chǎn)中可專用的高效率的設(shè)備。在單件小批量生產(chǎn)中則常用通用設(shè)備和一般的加工方法。(3) .考慮被加工材料的性質(zhì)。(4) .考慮工廠或車間的實(shí)際情況,同時(shí)也應(yīng)考慮不斷改進(jìn)現(xiàn)有加工方法和設(shè)備,推廣新技術(shù),提高工藝水平。(5) .此外,還要考慮一些其它因素,如加工表面物理機(jī)械性能的特殊要求,工件形狀和重量等。選擇加工方法一般先按這個(gè)零件主要表面的技術(shù)要求選定最終加工方法。再選擇前面各工序的加工方法。2、上端面與孔的加工(1) .查《簡明機(jī)械加工工藝手冊(cè)》表 5-3《平面加工方案》可以3確定,上端面的加工方案為:粗銑——精銑,經(jīng)濟(jì)加工精度等級(jí),加工表面粗糙度為 6.3~0.8um,適用于一般不淬硬的97IT?Ra?平面(端銑的粗糙度可以較?。?。(2) .加工內(nèi)花鍵前的預(yù)制孔 加工21H?查《簡明機(jī)械加工工藝手冊(cè)》表 5-2《孔加工方案》 ,由于預(yù)制孔的精度為 H12,所以確定預(yù)制孔的加工方案為:一次鉆孔,由于在拉削過程中才能保證預(yù)制孔表面精度,所以,在加工內(nèi)花鍵前預(yù)制孔的精度可適當(dāng)降低。(3) .內(nèi)花鍵的加工通過拉刀實(shí)現(xiàn)花鍵的加工,由于拉削的精度高,所以能滿足花鍵表面精度,同時(shí)也能保證預(yù)制孔表面精度。(4) .2-M8 螺紋孔的加工加工方案為:鉆,攻絲。(三)確定定位基準(zhǔn)1、粗基準(zhǔn)的選擇選擇粗基準(zhǔn)時(shí),考慮的重點(diǎn)是如何保證各加工表面有足夠的余量,使不加工表面與加工表面間的尺寸、位置符合圖紙要求。粗基準(zhǔn)選擇應(yīng)當(dāng)滿足以下要求:(1) .粗基準(zhǔn)的選擇應(yīng)以加工表面為粗基準(zhǔn)。目的是為了保證加工面與不加工面的相互位置關(guān)系精度。如果工件上表面上有好幾個(gè)不需加工的表面,則應(yīng)選擇其中與加工表面的相互位置精度要求較高的表面作為粗基準(zhǔn)。以求壁厚均勻、外形對(duì)稱、少裝夾等。(2) .選擇加工余量要求均勻的重要表面作為粗基準(zhǔn)。例如:機(jī)床床身導(dǎo)軌面是其余量要求均勻的重要表面。因而在加工時(shí)選擇導(dǎo)軌面作為粗基準(zhǔn),加工床身的底面,再以底面作為精基準(zhǔn)加工導(dǎo)軌面。這樣就能保證均勻地去掉較少的余量,使表層保留而細(xì)致的組織,以增加耐磨性。(3) .應(yīng)選擇加工余量最小的表面作為粗基準(zhǔn)。這樣可以保證該面有足夠的加工余量。(4) .應(yīng)盡可能選擇平整、光潔、面積足夠大的表面作為粗基準(zhǔn),以保證定位準(zhǔn)確夾緊可靠。有澆口、冒口、飛邊、毛刺的表面不宜選作粗基準(zhǔn),必要時(shí)需經(jīng)初加工。(5) .粗基準(zhǔn)應(yīng)避免重復(fù)使用,因?yàn)榇只鶞?zhǔn)的表面大多數(shù)是粗糙不規(guī)則的。多次使用難以保證表面間的位置精度。要從保證孔與孔、孔與平面、平面與平面之間的位置,能保證撥叉在整個(gè)加工過程中基本上都能用統(tǒng)一的基準(zhǔn)定位。從撥叉零件圖分析可知,選擇撥叉的后端面作為撥叉加工粗基準(zhǔn)。2、精基準(zhǔn)的選擇4精基準(zhǔn)選擇的原則(1) .基準(zhǔn)重合原則。即盡可能選擇設(shè)計(jì)基準(zhǔn)作為定位基準(zhǔn)。這樣可以避免定位基準(zhǔn)與設(shè)計(jì)基準(zhǔn)不重合而引起的基準(zhǔn)不重合誤差。(2) .基準(zhǔn)統(tǒng)一原則,應(yīng)盡可能選用統(tǒng)一的定位基準(zhǔn)?;鶞?zhǔn)的統(tǒng)一有利于保證各表面間的位置精度,避免基準(zhǔn)轉(zhuǎn)換所帶來的誤差,并且各工序所采用的夾具比較統(tǒng)一,從而可減少夾具設(shè)計(jì)和制造工作。例如:軸類零件常用頂針孔作為定位基準(zhǔn)。車削、磨削都以頂針孔定位,這樣不但在一次裝夾中能加工大多書表面,而且保證了各外圓表面的同軸度及端面與軸心線的垂直度。(3) .互為基準(zhǔn)的原則。選擇精基準(zhǔn)時(shí),有時(shí)兩個(gè)被加工面,可以互為基準(zhǔn)反復(fù)加工。例如:對(duì)淬火后的齒輪磨齒,是以齒面為基準(zhǔn)磨內(nèi)孔,再以孔為基準(zhǔn)磨齒面,這樣能保證齒面余量均勻。自為基準(zhǔn)原則。有些精加工或光整加工工序要求余量小而均勻,可以選擇加工表面本身為基準(zhǔn)。例如:磨削機(jī)床導(dǎo)軌面時(shí),是以導(dǎo)軌面找正定位的。此外,像拉孔在無心磨床上磨外圓等,都是自為基準(zhǔn)的例子。此外,還應(yīng)選擇工件上精度高。尺寸較大的表面為精基準(zhǔn),以保證定位穩(wěn)固可靠。并考慮工件裝夾和加工方便、夾具設(shè)計(jì)簡單等。要從保證孔與孔、孔與平面、平面與平面之間的位置,能保證撥叉在整個(gè)加工過程中基本上都能用統(tǒng)一的基準(zhǔn)定位。從撥叉零件圖分析可知,它的 內(nèi)花鍵槽,適于作精基準(zhǔn)使用。257H?選擇精基準(zhǔn)的原則時(shí),考慮的重點(diǎn)是有利于保證工件的加工精度并使裝夾準(zhǔn)。(四)工藝路線的擬訂對(duì)于大批量生產(chǎn)的零件,一般總是首先加工出統(tǒng)一的基準(zhǔn)。撥叉的加工的第一個(gè)工序也就是加工統(tǒng)一的基準(zhǔn)。具體安排是:先加工預(yù)制孔,再以預(yù)制孔定位粗、精加工撥叉上端面、底槽、M8 螺紋孔及錐孔。后續(xù)工序安排應(yīng)當(dāng)遵循粗精分開和先面后孔的原則。1、工序的合理組合確定加工方法以后,就按生產(chǎn)類型、零件的結(jié)構(gòu)特點(diǎn)、技術(shù)要求和機(jī)床設(shè)備等具體生產(chǎn)條件確定工藝過程的工序數(shù)。確定工序數(shù)的基本原則:(1) .工序分散原則工序內(nèi)容簡單,有利選擇最合理的切削用量。便于采用通用設(shè)備。簡單的機(jī)床工藝裝備。生產(chǎn)準(zhǔn)備工作量少,產(chǎn)品更換容易。對(duì)工人的技術(shù)要求水平不高。但需要設(shè)備和工人數(shù)量多,生產(chǎn)面積大,工藝路線長,生產(chǎn)管理復(fù)雜。5(2) .工序集中原則工序數(shù)目少,工件裝,夾次數(shù)少,縮短了工藝路線,相應(yīng)減少了操作工人數(shù)和生產(chǎn)面積,也簡化了生產(chǎn)管理,在一次裝夾中同時(shí)加工數(shù)個(gè)表面易于保證這些表面間的相互位置精度。使用設(shè)備少,大量生產(chǎn)可采用高效率的專用機(jī)床,以提高生產(chǎn)率。但采用復(fù)雜的專用設(shè)備和工藝裝備,使成本增高,調(diào)整維修費(fèi)事,生產(chǎn)準(zhǔn)備工作量大。一般情況下,單件小批生產(chǎn)中,為簡化生產(chǎn)管理,多將工序適當(dāng)集中。但由于不采用專用設(shè)備,工序集中程序受到限制。結(jié)構(gòu)簡單的專用機(jī)床和工夾具組織流水線生產(chǎn)。加工工序完成以后,將工件清洗干凈。清洗是在 的含c??9080.4%—1.1%蘇打及 0.25%—0.5%亞硝酸鈉溶液中進(jìn)行的。清洗后用壓縮空氣吹干凈。保證零件內(nèi)部雜質(zhì)、鐵屑、毛刺、砂粒等的殘留量不大于 。mg202、工序的集中與分散制訂工藝路線時(shí),應(yīng)考慮工序的數(shù)目,采用工序集中或工序分散是其兩個(gè)不同的原則。所謂工序集中,就是以較少的工序完成零件的加工,反之為工序分散。(1) .工序集中的特點(diǎn)工序數(shù)目少,工件裝,夾次數(shù)少,縮短了工藝路線,相應(yīng)減少了操作工人數(shù)和生產(chǎn)面積,也簡化了生產(chǎn)管理,在一次裝夾中同時(shí)加工數(shù)個(gè)表面易于保證這些表面間的相互位置精度。使用設(shè)備少,大量生產(chǎn)可采用高效率的專用機(jī)床,以提高生產(chǎn)率。但采用復(fù)雜的專用設(shè)備和工藝裝備,使成本增高,調(diào)整維修費(fèi)事,生產(chǎn)準(zhǔn)備工作量大。(2) .工序分散的特點(diǎn)工序內(nèi)容簡單,有利選擇最合理的切削用量。便于采用通用設(shè)備。簡單的機(jī)床工藝裝備。生產(chǎn)準(zhǔn)備工作量少,產(chǎn)品更換容易。對(duì)工人的技術(shù)要求水平不高。但需要設(shè)備和工人數(shù)量多,生產(chǎn)面積大,工藝路線長,生產(chǎn)管理復(fù)雜。工序集中與工序分散各有特點(diǎn),必須根據(jù)生產(chǎn)類型。加工要求和工廠的具體情況進(jìn)行綜合分析決定采用那一種原則。一般情況下,單件小批生產(chǎn)中,為簡化生產(chǎn)管理,多將工序適當(dāng)集中。但由于不采用專用設(shè)備,工序集中程序受到限制。結(jié)構(gòu)簡單的專用機(jī)床和工夾具組織流水線生產(chǎn)。由于近代計(jì)算機(jī)控制機(jī)床及加工中心的出現(xiàn),使得工序集中的優(yōu)點(diǎn)更為突出,即使在單件小批生產(chǎn)中仍可將工序集中而不致花費(fèi)過多的生產(chǎn)準(zhǔn)備工作量,從而可取的良好的經(jīng)濟(jì)效果。63、加工階段的劃分零件的加工質(zhì)量要求較高時(shí),常把整個(gè)加工過程劃分為幾個(gè)階段:(1) .粗加工階段粗加工的目的是切去絕大部分多余的金屬,為以后的精加工創(chuàng)造較好的條件,并為半精加工,精加工提供定位基準(zhǔn),粗加工時(shí)能及早發(fā)現(xiàn)毛坯的缺陷,予以報(bào)廢或修補(bǔ),以免浪費(fèi)工時(shí)。粗加工可采用功率大,剛性好,精度低的機(jī)床,選用大的切前用量,以提高生產(chǎn)率、粗加工時(shí),切削力大,切削熱量多,所需夾緊力大,使得工件產(chǎn)生的內(nèi)應(yīng)力和變形大,所以加工精度低,粗糙度值大。一般粗加工的公差等級(jí)為 IT11~IT12。粗糙度為Ra=80~100μm。(2) .半精加工階段半精加工階段是完成一些次要面的加工并為主要表面的精加工做好準(zhǔn)備,保證合適的加工余量。半精加工的公差等級(jí)為IT9~IT10。表面粗糙度為 Ra=10~1.25μm。(3) .精加工階段精加工階段切除剩余的少量加工余量,主要目的是保證零件的形狀位置幾精度,尺寸精度及表面粗糙度,使各主要表面達(dá)到圖紙要求.另外精加工工序安排在最后,可防止或減少工件精加工表面損傷。精加工應(yīng)采用高精度的機(jī)床小的切前用量,工序變形小,有利于提高加工精度.精加工的加工精度一般為 IT6~IT7,表面粗糙度為 Ra10~1.25μm。(4) .光整加工階段對(duì)某些要求特別高的需進(jìn)行光整加工,主要用于改善表面質(zhì)量,對(duì)尺度精度改善很少。一般不能糾正各表面相互位置誤差,其精度等級(jí)一般為 IT5~IT6,表面粗糙度為 Ra1.25~0.32μm。此外,加工階段劃分后,還便于合理的安排熱處理工序。由于熱處理性質(zhì)的不同,有的需安排于粗加工之前,有的需插入粗精加工之間。但須指出加工階段的劃分并不是絕對(duì)的。在實(shí)際生活中,對(duì)于剛性好,精度要求不高或批量小的工件,以及運(yùn)輸裝夾費(fèi)事的重型零件往往不嚴(yán)格劃分階段,在滿足加工質(zhì)量要求的前提下,通常只分為粗、精加工兩個(gè)階段,甚至不把粗精加工分開。必須明確劃分階段是指整個(gè)加工過程而言的,不能以某一表面的加工或某一工序的性質(zhì)區(qū)分。例如工序的定位精基準(zhǔn)面,在粗加工階段就要加工的很準(zhǔn)確,而在精加工階段可以安排鉆小空之類的粗加工。4、加工工藝路線方案的比較在保證零件尺寸公差、形位公差及表面粗糙度等技術(shù)條件下,7成批量生產(chǎn)可以考慮采用專用機(jī)床,以便提高生產(chǎn)率。但同時(shí)考慮到經(jīng)濟(jì)效果,降低生產(chǎn)成本,擬訂兩個(gè)加工工藝路線方案。見下表:表 1.1 加工工藝路線方案比較表方案Ⅰ 方案Ⅱ工序號(hào)工序內(nèi)容 定位基準(zhǔn) 工序內(nèi)容 定位基準(zhǔn)010 前后端面 底面和側(cè)面 前后端面 底面和側(cè)面020 鉆預(yù)制孔 底面和側(cè)面 鉆預(yù)制孔 底面和側(cè)面030 粗、精銑上端面已加工預(yù)制孔和側(cè)面拉內(nèi)花鍵25H7?已加工預(yù)制孔和側(cè)面040 粗、精銑18H11 底槽已加工預(yù)制孔和側(cè)面粗、精銑18H11 底槽內(nèi)花鍵和側(cè)面050 鉆 2-M8、錐孔,通孔,攻絲已加工預(yù)制孔和側(cè)面粗、精銑上端面內(nèi)花鍵和側(cè)面060 拉內(nèi)花鍵25H7?已加工預(yù)制孔和側(cè)面鉆 2-M8、錐孔,通孔,攻絲內(nèi)花鍵和側(cè)面070 去毛刺,清洗去毛刺,清洗080 檢驗(yàn) 檢驗(yàn)加工工藝路線方案的論證:方案Ⅰ、Ⅱ主要區(qū)別在于在加工上端面及以下工序時(shí),所選定位基準(zhǔn)不同,方案Ⅰ選用預(yù)制孔為主要定位基準(zhǔn),方案Ⅱ選用花鍵作主要定位基準(zhǔn),考慮到花鍵的加工精度最高,并且防止鉆孔時(shí)對(duì)花鍵的表面精度有所損壞,所以選擇第一種加工方案。由以上分析:方案Ⅰ為合理、經(jīng)濟(jì)的加工工藝路線方案。具體的工藝過程如下表:表 1.2 加工工藝過程表工序號(hào) 工 種 工作內(nèi)容 說 明010 鑄造 金屬型澆鑄 鑄件毛坯尺寸:長: 寬: 80m40高: 75預(yù)制孔、底槽不鑄出8020 熱處理退火 去應(yīng)力退火030 銑 前后端面 專用夾具裝夾;立式升降臺(tái)銑床(X5032)040 鉆 鉆預(yù)制孔 21H?專用夾具裝夾;立式鉆床( )AZ5132050 銑 粗、精銑上端面 專用夾具裝夾;立式升降臺(tái)銑床(X5032)060 銑 銑底槽 18H11,深 35mm 專用夾具裝夾;立式升降臺(tái)銑床(X5032)070 鉆、鉸、攻絲鉆通孔 6.7mm?攻 M8 螺紋專用夾具裝夾;搖臂鉆床 (3025)Z組合攻絲機(jī)080 拉 拉內(nèi)花鍵 257H專用夾具裝夾;臥式拉床(L6120)090 去毛刺清洗100 檢驗(yàn)入庫(五)撥叉的偏差,加工余量,工序尺寸及毛坯尺寸的確定撥叉的制造采用的是金屬型澆鑄,其材料是 HT200,生產(chǎn)類型為中大批量生產(chǎn),采用鑄造毛坯。1、毛坯的結(jié)構(gòu)工藝要求(1) .撥叉為鑄造件,對(duì)毛坯的結(jié)構(gòu)工藝有一定要求:①、鑄件的壁厚應(yīng)合適、均勻,不得有突然變化。②、鑄造圓角要適當(dāng),不得有尖棱、尖角。③、鑄件的結(jié)構(gòu)要盡量簡化,并要有合理的起模斜度,以減少分型面、型芯。并便于起模。④、加強(qiáng)肋的厚度和分布要合理,以免冷卻時(shí)鑄件變形或產(chǎn)生裂紋。9⑤、鑄件的選材要合理,應(yīng)有較好的可鑄性。(2) .設(shè)計(jì)毛坯形狀、尺寸還應(yīng)考慮到:①、各加工面的幾何形狀應(yīng)盡量簡單。②、工藝基準(zhǔn)以設(shè)計(jì)基準(zhǔn)相一致。③、便于裝夾、加工和檢查。④、結(jié)構(gòu)要統(tǒng)一,盡量使用普通設(shè)備和標(biāo)準(zhǔn)刀具進(jìn)行加工。在確定毛坯時(shí),要考慮經(jīng)濟(jì)性。雖然毛坯的形狀尺寸與零件接近,可以減少加工余量,提高材料的利用率,降低加工成本,但這樣可能導(dǎo)致毛坯制造困難,需要采用昂貴的毛坯制造設(shè)備,增加毛坯的制造成本。因此,毛坯的種類形狀及尺寸的確定一定要考慮零件成本的問題但要保證零件的使用性能。在毛坯的種類形狀及尺寸確定后,必要時(shí)可據(jù)此繪出毛坯圖。2、撥叉的偏差計(jì)算(1)預(yù)制孔及花鍵孔的偏差及加工余量計(jì)算加工預(yù)制孔時(shí),由于鑄造是沒鑄出,且為一次鉆出,通過拉削后保證花鍵尺寸 ,預(yù)制孔尺寸 ,查《機(jī)械加工工257Hm?21Hm?藝手冊(cè)》表 2.3-54,得花鍵拉削余量為 0.7~0.8mm,取 0.8mm,即預(yù)制孔加工到 ,一次拉削到設(shè)計(jì)要求,查《機(jī)械加工工藝手1.冊(cè)》表 1.12-11,得花鍵偏差為 0.45?(2) .撥叉上端面的偏差及加工余量計(jì)算根據(jù)工序要求,其加工分粗、精銑加工。各工步余量如下:粗銑:參照《機(jī)械加工工藝手冊(cè)第 1 卷》表 3.2-23。其余量值規(guī)定為 ,現(xiàn)取 。表 3.2-27 粗銑平面時(shí)厚度偏差取m4.3~70.3。28.0?精銑:參照《機(jī)械加工工藝手冊(cè)》表 2.3-59,其余量值規(guī)定為。1鑄造毛坯的基本尺寸為 根據(jù)《機(jī)械加工工藝手723.016m??。冊(cè)》表 2.3-11,鑄件尺寸公差等級(jí)選用 CT7,再查表 2.3-9 可得鑄件尺寸公差為 1.m。毛坯的名義尺寸為: .。毛坯最小尺寸為: 76054??毛坯最大尺寸為: ?粗銑后最大尺寸為: 213m粗銑后最小尺寸為: .87.2精銑后尺寸與零件圖尺寸相同,即保證尺寸 72mm,表面與花鍵軸的平行度公差為 0.1mm。(3) .18H11( )槽偏差及加工余量:0.18?10鑄造時(shí)槽沒鑄出,參照《機(jī)械加工工藝師手冊(cè)》表 21-5,得粗銑其槽邊雙邊機(jī)加工余量 2Z=2.0mm,槽深機(jī)加工余量為 2.0mm,再由參照參考文獻(xiàn)[1]表 21-5 的刀具選擇可得其極限偏差:粗加工為,精加工為 。0.1?0.13?粗銑兩邊工序尺寸為: ;8216m??粗銑后毛坯最大尺寸為: ;0?粗銑后毛坯最小尺寸為:16+0=16mm;粗銑槽底工序尺寸為:33mm;精銑兩邊工序尺寸為: ,已達(dá)到其加工要求: 。0.138? 0.18?(4) 、2-M8 螺紋偏差及加工余量:參照《機(jī)械加工工藝手冊(cè)》表 2.2-2,2.2-25,2.3-13 和《互換性與技術(shù)測量》表 1-8,可以查得:鉆孔的精度等級(jí): ,表面粗糙度 ,尺寸偏差是12?IT12.5Raum?0.15m查《機(jī)械加工工藝手冊(cè)》表 2.3-47,表 2.3-48,表 2.3-71。確定工序尺寸及加工余量為:加工該組孔的工藝是:鉆——攻絲鉆孔: 6.7?攻絲:攻 2-M8 螺紋孔。(六)確定切削用量及基本工時(shí)(機(jī)動(dòng)時(shí)間)工序 1:銑削前后端面機(jī)床:立式升降臺(tái)銑床(X5032)刀具:查《金屬機(jī)械加工工藝人員手冊(cè)》表 10-40,選高速鋼鑲齒套式面銑刀,加工到前后端面的距離為 80mm。每齒進(jìn)給量:根據(jù)《金屬機(jī)械加工工藝人員手冊(cè)》表 14-69,取 。zmaf /3.0~15.? z/2.0maf?銑削速度:查《金屬機(jī)械加工工藝人員手冊(cè)》表 14-71 得sv/2.機(jī)床主軸轉(zhuǎn)速: in/8.4701.361rdvn????查《金屬機(jī)械加工工藝人員手冊(cè)》 ,取 5?實(shí)際銑削速度: smv/21.6.510進(jìn)給量: Znaff 702.???工作臺(tái)每分鐘進(jìn)給量: in/5/.svffm?前端面被切削長度:由毛坯尺寸可知: l4前端面的刀具切入長度: dl2)~1(5.1?11刀具切出長度: 走刀次數(shù):1ml2?機(jī)動(dòng)時(shí)間: min85.012451???ft后端面被切削長度:由毛坯尺寸可知: l73?后端面的刀具切入長度: l421?刀具切出長度: 走刀次數(shù):2ml2機(jī)動(dòng)時(shí)間: min1.0531 ??????ft工序 2:鉆預(yù)制孔機(jī)床:立式鉆床 AZ52刀具:查《機(jī)械加工工藝手冊(cè)》表 3.3-9,選高速鋼直柄長麻花鉆,鉆預(yù)制孔到 。m.1?進(jìn)給量:查《機(jī)械加工工藝手冊(cè)》表 3.1-2,取 rmf/5.0?切削速度:根據(jù)《機(jī)械加工工藝手冊(cè)》表 14-36,得 sv48機(jī)床主軸轉(zhuǎn)速: in/6.423.1.3080rdvn????按照《機(jī)械加工工藝手冊(cè)》表 3.1-36,取 75所以實(shí)際切削速度: ./100v s切削工時(shí)被切削層長度 :l8m?刀具切入長度 :1 21.(~)5.962rdctgkctgm??????刀具切出長度 : 取2l4l3走刀次數(shù)為 1機(jī)動(dòng)時(shí)間 :2jt8063.7in.5jLfn???工序 3:粗、精銑上端面機(jī)床:立式升降臺(tái)銑床 2X刀具:查《金屬機(jī)械加工工藝人員手冊(cè)》表 10-40,選高速鋼鑲齒套式面銑刀,加工到前后端面的距離為 80mm。 ,規(guī)格為:,齒數(shù)為 10 齒。27,36,80d??DL(1) 、粗銑上端面銑削深度 :pam每齒進(jìn)給量:根據(jù)《金屬機(jī)械加工工藝人員手冊(cè)》表 14-69,取 。zf /3.0~5.? z/2.0maf?銑削速度:查《金屬機(jī)械加工工藝人員手冊(cè)》表 14-71 得sv/2.12機(jī)床主軸轉(zhuǎn)速 :nmin/8.4701.36210rdvn????查《金屬機(jī)械加工工藝人員手冊(cè)》 ,取 in/50r?實(shí)際銑削速度: sdnv21.610.35???進(jìn)給量: Zaff /72.??工作臺(tái)每分鐘進(jìn)給量: min05.svffm?被切削層長度 :由毛坯尺寸可知l 8l刀具切入長度: d42)~1(5.01?刀具切出長度 :取2ll2?走刀次數(shù)為 1機(jī)動(dòng)時(shí)間 :jt min18.0581?fvll2.精銑上端面切削深度 :pam?根據(jù)《實(shí)用機(jī)械加工工藝師冊(cè)》表 11-91 查得:每齒進(jìn)給量,取 ,根據(jù)《實(shí)用機(jī)械加工工藝師冊(cè)》0.1~.2/f z?0.2/faz表 11-94 查得切削速度 min18v?機(jī)床主軸轉(zhuǎn)速 :ni/.74.3rd???按照《機(jī)械加工工藝手冊(cè)》表 3.1-74 取 n0實(shí)際切削速度 :v s/3.6108.?進(jìn)給量 :fVmZnaff 22.???工作臺(tái)每分進(jìn)給量 :m in/1/.svff被切削層長度 :由毛坯尺寸可知,l l3刀具切入長度: d4)~1(5.01??刀具切出長度 :取2ll2走刀次數(shù)為 1機(jī)動(dòng)時(shí)間 :2t min74.016821?fvll本工序機(jī)動(dòng)時(shí)間 i9.7408.??t工序 4:粗、精銑 18H11 底槽機(jī)床:立式升降臺(tái)銑床 532X刀具:根據(jù)《實(shí)用機(jī)械加工工藝師手冊(cè)》表 21-5 選用高速鋼鑲齒三13面刃銑刀。外徑 160mm,內(nèi)徑 40mm,刀寬粗銑 16mm,精銑18mm,齒數(shù)為 18 齒。(1) 、粗銑 16 槽銑削深度 :pa3m?每齒進(jìn)給量 :查《機(jī)械加工工藝手冊(cè)》表 2.4-75,得f,取 。0.2~/f z?0.2/faz銑削速度 :查《機(jī)械加工工藝師手冊(cè)》表 30-33,得V 14minV?機(jī)床主軸轉(zhuǎn)速 :n11427.9/min3.60nrD???查《機(jī)械加工工藝手冊(cè)》表 3.1-74 取 30/minr?實(shí)際切削速度 :v3.146.250Ds????進(jìn)給量 :fV.2//ffaZn工作臺(tái)每分進(jìn)給量 : m.14/infVs?被切削層長度 :由毛坯尺寸可知l lm刀具切入長度 :110.5(~2)lD??=81mm刀具切出長度 :取2ll2?走刀次數(shù) 1 次機(jī)動(dòng)時(shí)間 :jt140812.5minjmlf???2.精銑 18 槽切削深度 :pa35?根據(jù)《機(jī)械加工工藝手冊(cè)》表 查得:進(jìn)給量 ,查2.476?0.5/famz?《機(jī)械加工工藝手冊(cè)》表 2.4-82 得切削速度 ,23/inV機(jī)床主軸轉(zhuǎn)速 :n,102345.8/min.160Vnrd????查《機(jī)械加工工藝手冊(cè)》表 3.1-74 取 47.5/inr?實(shí)際切削速度 :v.1600Dms????進(jìn)給量 :fV0.524./.9/ffaZn工作臺(tái)每分進(jìn)給量 : m857infVs?被切削層長度 :由毛坯尺寸可知 ,l 0l14刀具切入長度 :1l10.5(~2)lD??=81mm刀具切出長度 :取2lml2?走刀次數(shù)為 1機(jī)動(dòng)時(shí)間 :jt140812.5in7jmlf???本工序機(jī)動(dòng)時(shí)間 12.3mjjtt??工序 5:鉆 孔并攻絲8M機(jī)床:搖臂鉆床 305Z刀具:根據(jù)參照《機(jī)械加工工藝手冊(cè)》表 4.3-9 硬質(zhì)合金錐柄麻花鉆頭。1.鉆孔 6.7?鉆孔前鑄件為實(shí)心,根據(jù)上文所的加工余量先鉆孔到 再攻絲,6.7m?所以 。.Dm?鉆削深度 :pa9.5進(jìn)給量 :根據(jù)《機(jī)械加工工藝手冊(cè)》表 2.4-38,取f rf/3.0?切削速度 :參照《機(jī)械加工工藝手冊(cè)》表 2.4-41,取V 41Vs機(jī)床主軸轉(zhuǎn)速 ,有:n,100.4169.31/min37vnrd????按照《機(jī)械加工工藝手冊(cè)》表 3.1-31 取 160/inr?所以實(shí)際切削速度 :v.47.50dms????切削工時(shí)被切削層長度 :l42m刀具切入長度 :116.7(~)01.8932rDlctgkctg???????刀具切出長度 : 取2l42lm走刀次數(shù)為 1,鉆孔數(shù)為 2 個(gè)機(jī)動(dòng)時(shí)間 :jt 30.5in0.16jLfn????2.攻 2-M8 螺紋通孔刀具:釩鋼機(jī)動(dòng)絲錐進(jìn)給量 :查《機(jī)械加工工藝手冊(cè)》表 1.8-1 得所加工螺紋孔螺距f,因此進(jìn)給量1.5pm?1.25/fmr?切削速度 :參照《機(jī)械加工工藝手冊(cè)》表 2.4-105,取V150.13/7.98/minVs?機(jī)床主軸轉(zhuǎn)速 : ,取017.9831.6/min4Vrd????350/minr?絲錐回轉(zhuǎn)轉(zhuǎn)速 :取回 35/inr回實(shí)際切削速度 :?.50./1s被切削層長度 :l9.m?刀具切入長度 :1(~3).23.7fm??刀具切出長度 : ,加工數(shù)為 22l 5( )機(jī)動(dòng)時(shí)間 :jt12122 99.53.70.13min1301jlltfnf????????回( ) ( )本工序機(jī)動(dòng)時(shí)間 : 。jt2.5.6minjjt?工序 6:拉內(nèi)花鍵 57H?機(jī)床:臥式拉床 L6120。刀具:查《復(fù)雜刀具設(shè)計(jì)手冊(cè)》表 1.3-1,選擇拉刀類型為矩形花鍵拉刀第三型號(hào),該刀具特點(diǎn):拉削長度大于 30mm,同時(shí)加工齒數(shù)不小于 5。材料:W18Cr4V 做拉刀材料,柄部采用 40Cr 材料(具體刀具設(shè)計(jì)見拉刀設(shè)計(jì)) 。拉削過程中,刀具進(jìn)給方向和拉削方向一致,拉刀各齒齒升量詳見拉刀設(shè)計(jì),拉削的進(jìn)給量即為單面的齒升量。查《機(jī)械加工工藝手冊(cè)》表 2.4-118 和 2.4-119,確定拉削速度 =0.116~0.08 ,取vms。0.1mvs?拉削工件長度 : ;l80m?拉刀長度 : (見拉刀設(shè)計(jì)) ;1753拉刀切出長度 =5~10mm,取 。2l210l?走刀次數(shù)一次。根據(jù)以上數(shù)據(jù)代入公式(計(jì)算公式由《機(jī)械加工工藝手冊(cè)》表 2.5-20 獲得) ,得機(jī)動(dòng)時(shí)間 jt