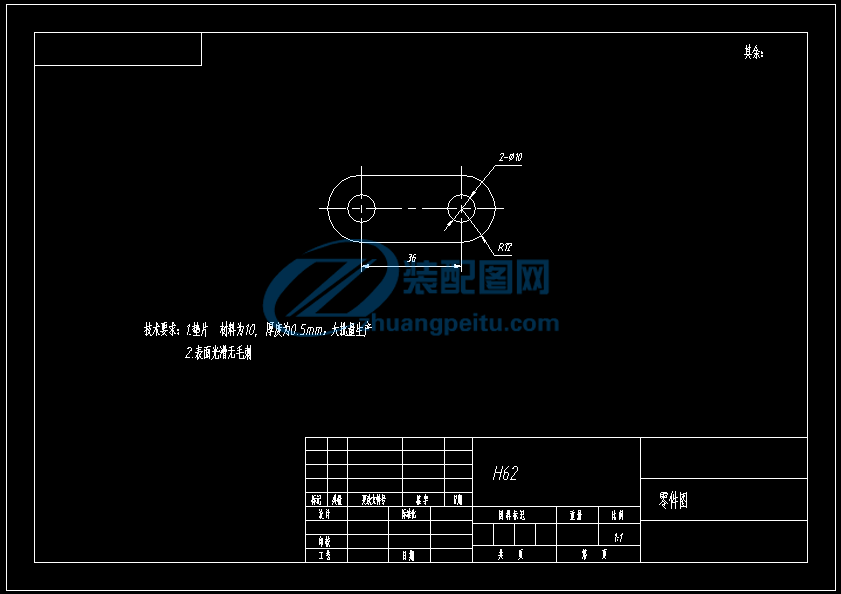
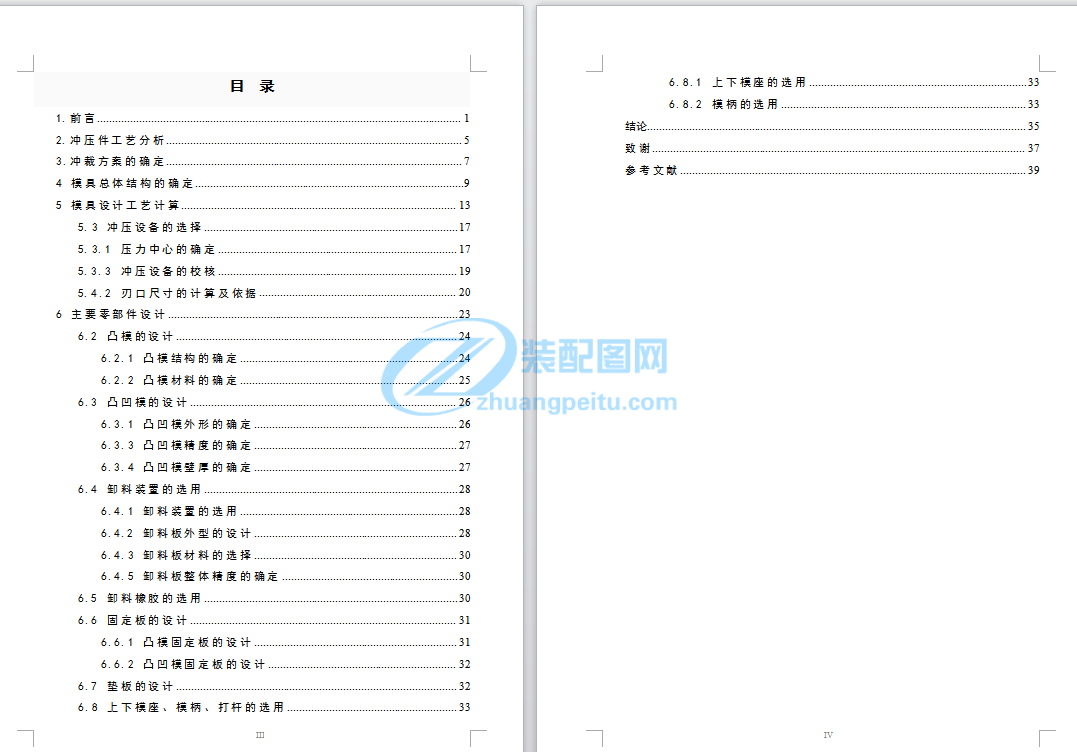
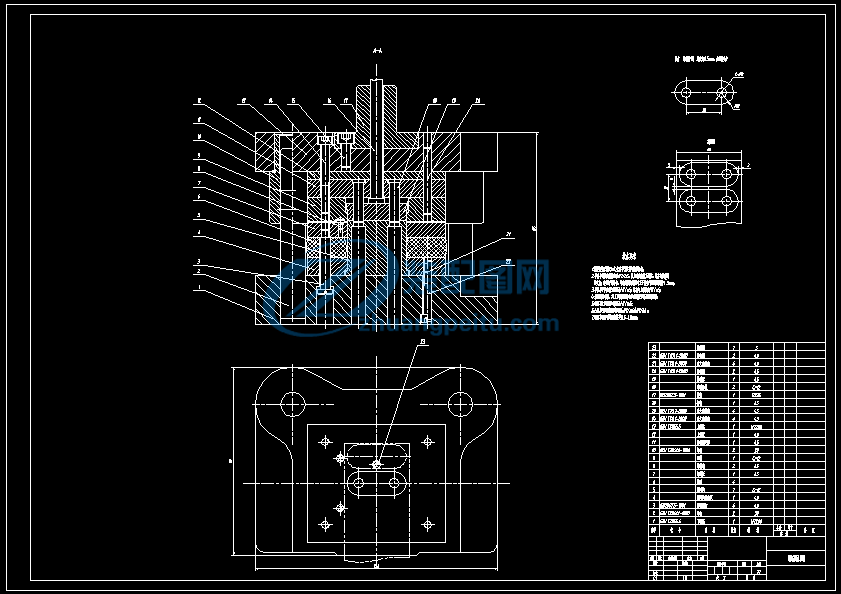
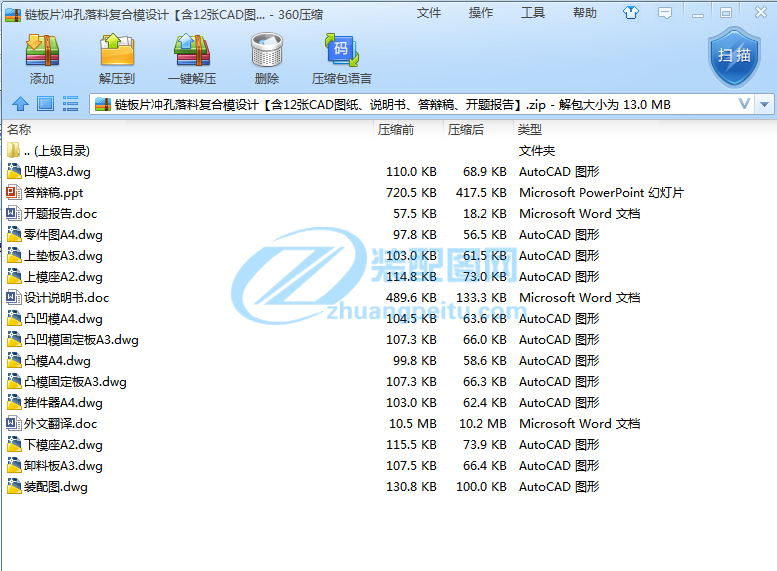
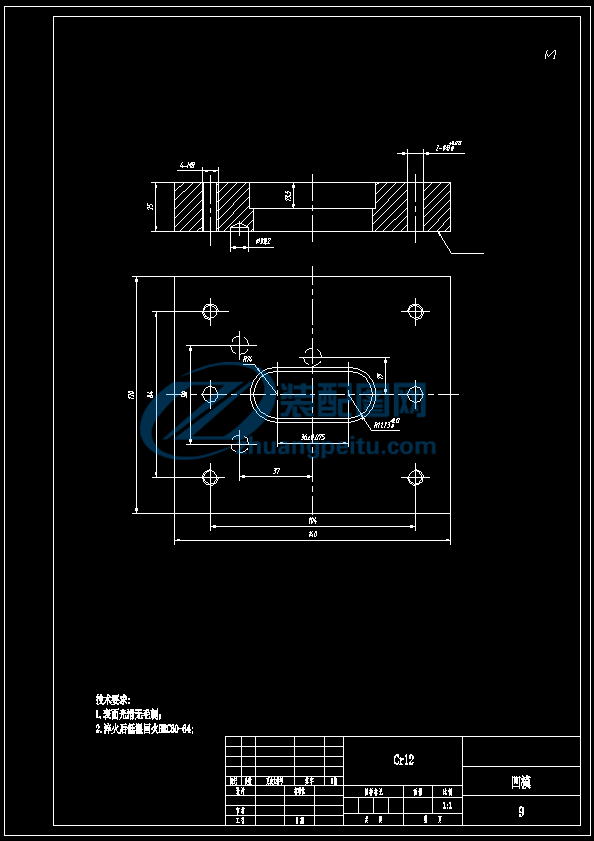

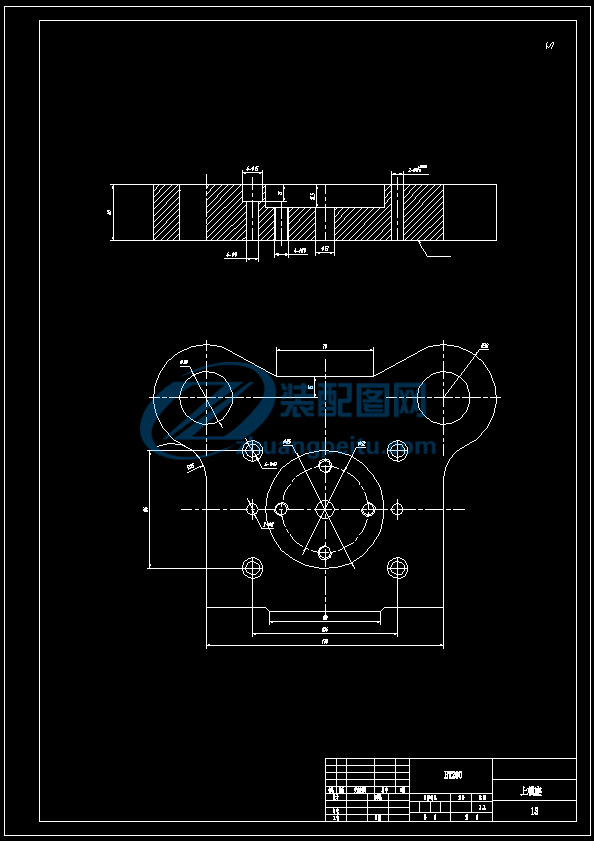
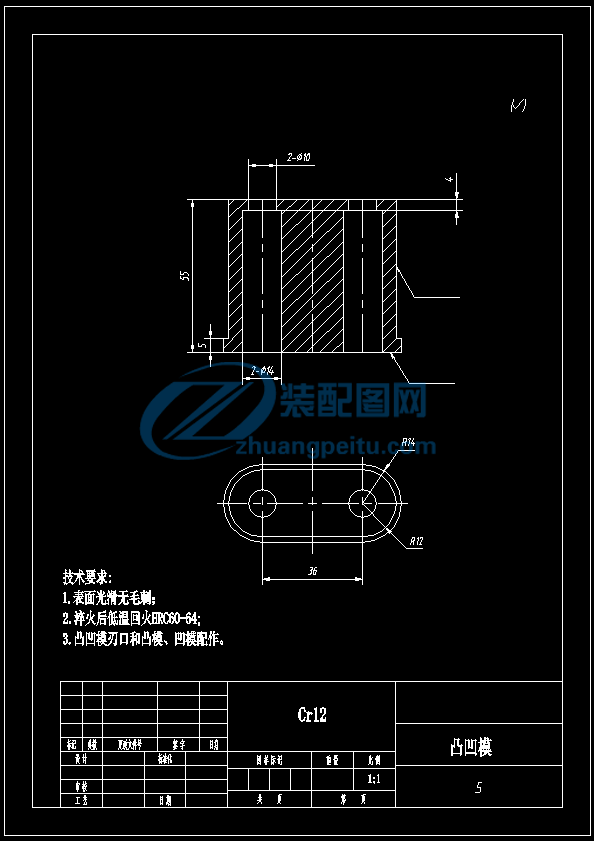

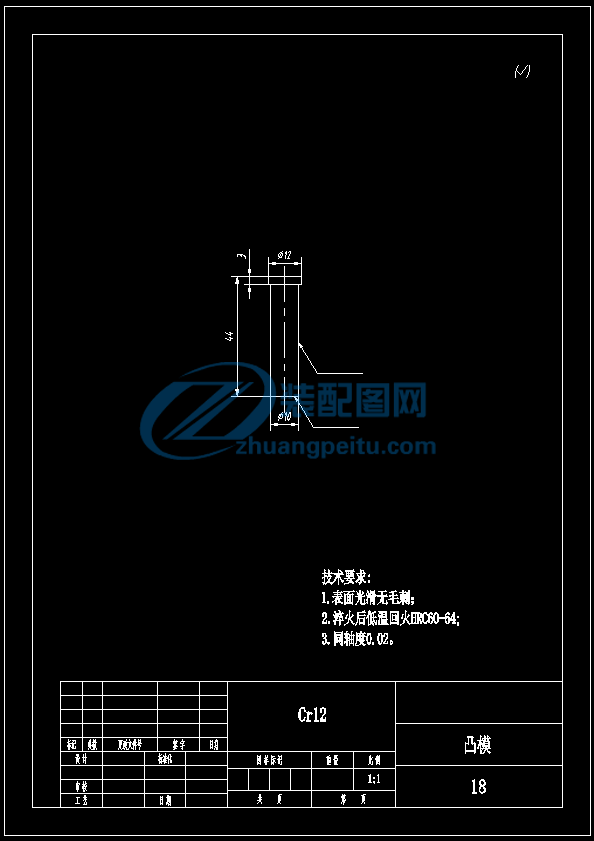
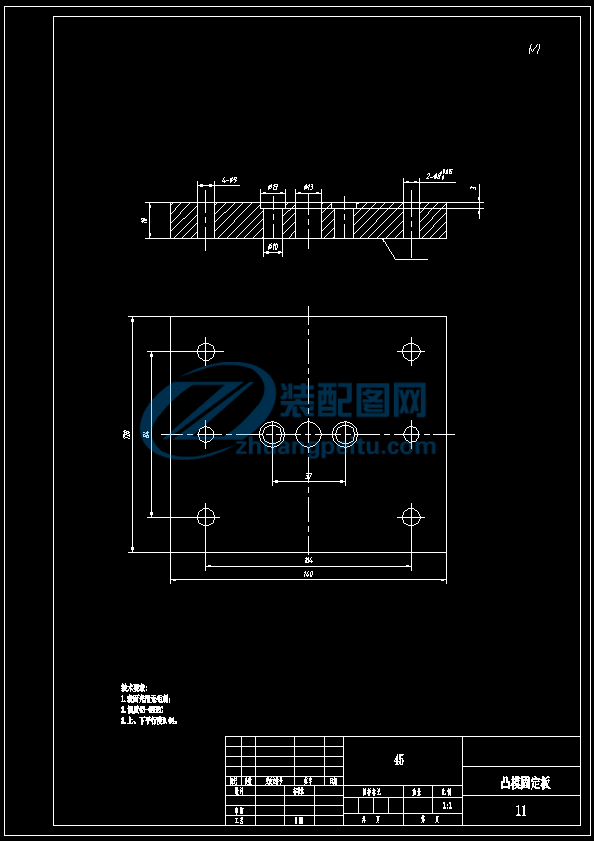
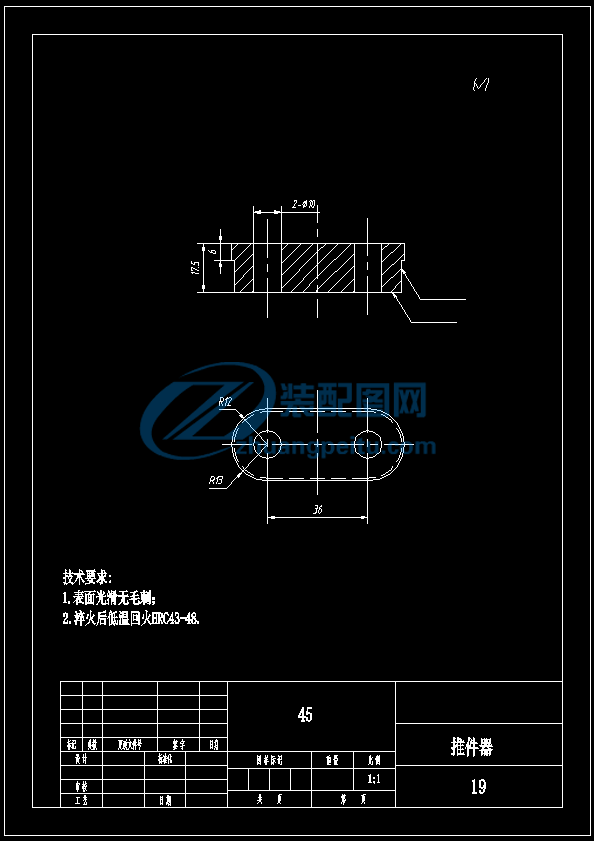
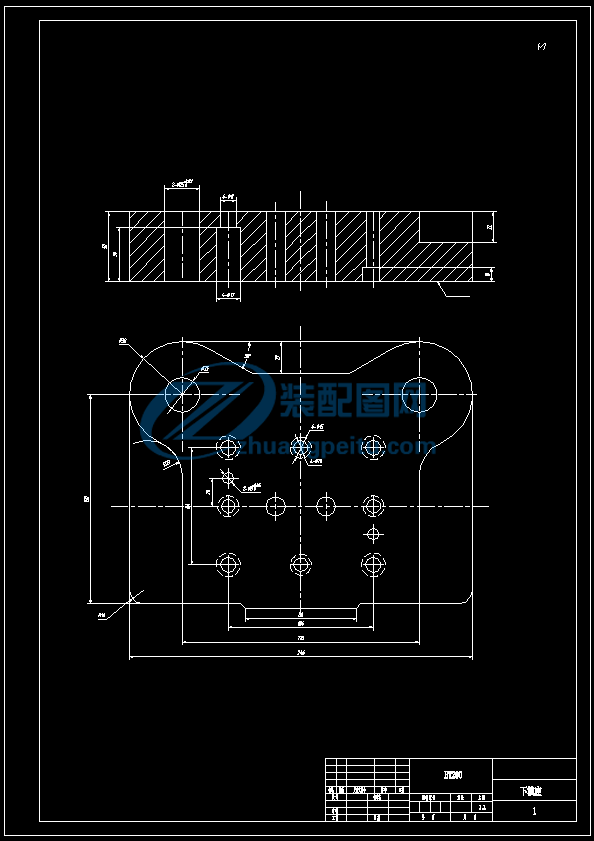
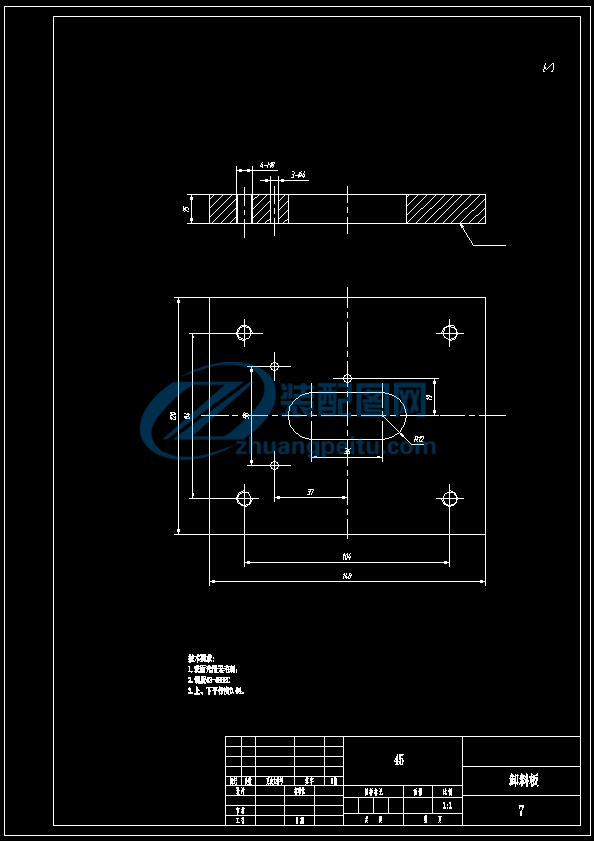
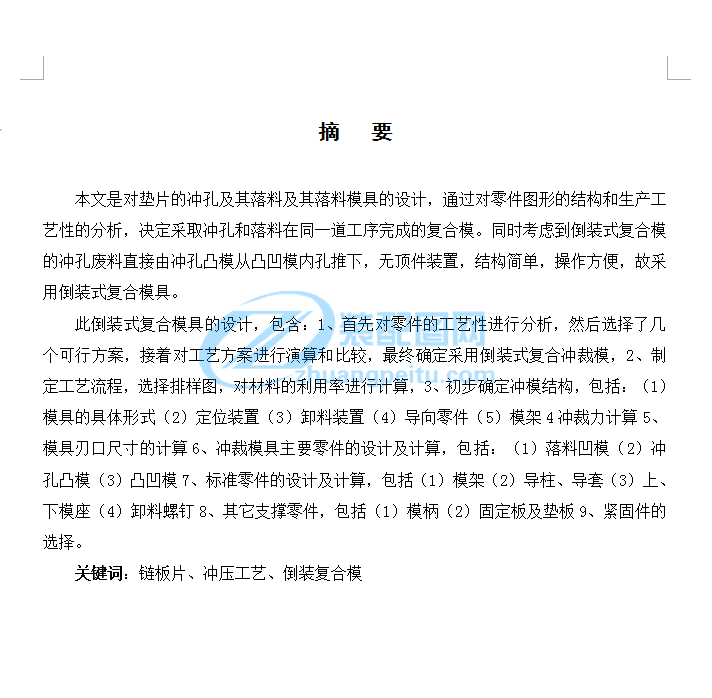
畢業(yè)生論文答辯 鏈板片沖孔落料復合模設計,,1,答辯人: 指導教師:,目錄,,,,主要零部件設計,模具設計工藝計算,模具總體結構的確定,沖裁方案的確定,工藝分析,齒輪螺栓墊片沖壓模設計,對工件進行相關的工藝分析,給出設 計任務,根據分析結果確定工藝方案,工藝分析,,,設計任務—鏈板片沖孔落料復合模設計 鏈板片零件圖 鏈板片的材料為10鋼,厚度為0.5mm,大批量生產。,設計任務,工藝分析,(1)材料:該沖裁件的材料為10號鋼,10號鋼塑性、韌性很好,易冷熱加工成形,具有較好的沖裁成形性性能,適合要求較高的零件。綜合評比均適合沖裁加工。(2)零件結構: 零件結構簡單對稱,無尖角,對沖裁加工較為有利。外形有多處圓弧,里面有兩個圓孔,孔的直徑為10mm,外圓半徑為12mm,凸、凹模允許的最小壁厚4.5mm,小于最小孔邊距5mm,所以,用倒裝式復合模沖壓這個零件。因此,該制件具有良好的沖壓工藝性,比較適合沖裁。(3)尺寸精度: 由于本零件給定的精度都按生產所需經濟精度要求IT14,查閱相關資料,發(fā)現普通沖裁能夠滿足零件精度要求。,工藝方案,該零件包括落料、沖孔兩個基本工序,現有以下三種工藝方案:(1)在壓力機一次行程內只完成一個沖壓工序的沖裁模即單工序沖裁。(2)在壓力機一次行程內,在模具的同一位置同時完成兩個或兩個以上的沖壓工序即復合沖裁。(3)把沖裁件的若干個沖壓工序,排列成一定的順序,在壓力機的一次行程中條料在沖模的不同位置上,分別完成工件所要求的工序即級進沖裁。由于該零件的生產要求的是大批量生產、零件的尺寸較小,制造相對比較難,為提高生產率,根據上述方案分析、比較,宜采用復合模沖裁。,模具結構,模具結構,模具類型,按照復合模工作零件的安裝位置不同,分為正裝式復合模和倒裝式復合模兩種,兩種類型的優(yōu)點、缺點及適用范圍見下表:,模具類型,正裝式復合模適合于沖制材質較軟或板料較薄的平直度要求較高的沖裁件,還可以沖制孔邊距離較小的沖裁件。倒裝式冷沖模不宜沖制孔邊距離較小的沖裁件,但倒裝式冷沖模結構簡單,可以直接利用壓力機打桿裝置進行推件,卸件可靠,便于操作,并為機械化出件提供了有利條件,故應用十分廣泛。綜上所述,該制件結構形狀簡單,精度要求較低,孔邊距較大,宜采用倒裝式復合模。由以上沖壓工藝分析可知,采用復合模沖壓,模具類型為倒裝式復合模。,送料方式,條料在模具送料平面必須有兩個方向的限位:一是在與條料方向垂直的方向上的限位,保證條料沿正確的方向送進,稱為送進導向;二是在送料方向上的限位,控制條料一次送進的距離稱為送料定距。 送進導向的定位零件有導料銷、導料板、側壓板等;送料定距的定位零件有用擋料銷、導正銷、側刃等。由于零件的生產批量是大批量及模具類型的確定,合理安排生產可采用前后自動送料方式。,定位方式,因為該模具采用的是條料,控制條料的送進方向采用導料銷,無側壓裝置。控制條料的送進布局采用擋料銷定距。而第一件的沖壓位置因為條料長度有一定余量,可以靠操作工目測來定。,卸料、出件方式,工件平直度較高,料厚為0.5mm相對較薄,卸料力不大,由于彈性卸料模具比剛性卸料模具方便,操作者可以看見條料在模具中的送進狀態(tài),且彈性卸料板對工件施加的柔性力,不會損傷工件表面,故可采用彈性卸料。,,排樣設計,沖裁力計算,沖壓設備選擇,刃口尺寸,工藝計算,,排樣設計,一、確定搭邊值搭邊起補償條料的剪裁誤差,送料步距誤差以及補償于條料與導料板之間有間隙所造成的送料歪斜誤差的作用。使凸,凹模刃口雙邊受力,受力平衡,合理間隙一易破壞,模具壽命與工件斷面質量都能提高。對于利用搭邊自動送料模具,搭邊使條料有一定的剛度,以保證條料的連續(xù)送進。搭邊的合理數值主要決定于材料厚度、材料種類、沖裁件的大小以及沖裁件的輪廓形狀等。一般板料愈厚,材料愈軟以及沖裁件尺寸愈大,形狀愈復雜,則搭邊值也應愈大。選擇工件間搭邊值為3mm,側面搭邊值為3mm。,排樣設計,二、送料步距與條料寬度的計算 采用直對排的排樣方案,如圖所示。 送料步距A:送料步距的大小應為條料上沖裁件的對應點之間的距離,每次沖1個零件的步距按式:A=寬+a1,A=24+3=27mm條料寬度B:B:B=長+2a=(60+2×3)mm=66mm,沖壓件的毛坯面積的計算, 利用cad測量得面積1316.4mm2,排樣設計,三、材料利用率的計算,材料利用率是指沖裁件的實際面積與所用板料面積的百分比,他是衡量合理利用材料的經濟性指標,一個步距內的材料利用率計算式為:,式中,A為一個步距內沖裁件的實際面積,B為條料寬度,S為步距,即每次條料送進模具的距離。所以計算得加工該零件的材料利用率如下:,沖裁力計算,計算沖裁力的目的是為了選擇合適的壓力機,設計模具和檢驗模具的強度,壓力機的噸位必須大于所計算的沖裁力,以適宜沖裁的要求,普通平刃沖裁模,其沖裁力F一般按如下計算: 落料力: Fl=147.4×0.5×360≈27KN。 卸料力: Fx=0.04×27=1.1 KN。 沖孔力: Fc= 62.8×0.5×360≈12KN。 推件力: Ft=8×0.05×12=4.8 F總=F落+F沖孔+F卸+F推=27+12+1.1+4.8=44.9KN,,壓力機公稱壓力的確定:沖裁時,壓力機的公稱壓力必須大于或等于各沖裁工藝力的總和:,沖壓設備選擇,計算得總沖壓力是44.9KN,所選壓力機的公稱壓力必須大于或等于總沖壓力的1.3倍。所以選用公稱壓力為160KN的機械壓力機。,刃口尺寸,,,根據實用間隙表查得材料不銹鋼的最小雙面間隙Zmin=0.04mm,最大雙面間隙Zmax=0.06mm。具體計算見下表:,主要零部件設計,一、凹模的設計 二、凸模的設計 三、凸凹模設計 四、墊板的設計,凹模的設計,凸模的設計,凸模高度為:L=h1+h2+附加長度 (7-5) 式中:h1-凸模固定板厚度,可得:h1=18mm;h2-凹模厚度,可得:h2=25mm; 附加長度包括凸模的修磨量,凸模進入凸凹模的深度。(附加長度取1mm) 由公式得L=18+25+1=44(mm) 由以上可得凸模簡圖如圖所示,凸凹模的設計,,凸凹模外形的確定 凸凹模的外形由本套模具所設計的零件圖樣外形確定 凸凹模材料的選取 在該模具中凸凹模材料選用Cr12 凸凹模精度的確定 外形精度公差為IT7 凸凹模壁厚的確定 凹模內外刃口間壁厚校核:根據沖裁件結構凸凹模內外刃口最小壁厚為1.8mm,該壁厚為1.8mm即可,本設計中凸凹模的壁厚為7mm,故該凸凹模的側壁強度要求足夠 凸凹模洞口類型的選取 選擇直通式洞口,如圖所示,,墊板的設計,它的作用是直接承受和擴散凸模傳遞的壓力,如果凸模的端部對材料的壓力超過材料的許用壓力,需在凸模端部與模座之間加上墊板防止模具損壞。 墊板外形尺寸可與固定板相同,其厚度一般取3~10mm,查參考文獻沖壓模具設計與制造 22.5-17JB/T7643.3-1994,墊板尺寸為140mm×120mm×8mm。,裝配圖,工作過程:1、前后方向進料;2、導料銷進行導料3、定位銷進行定位4、 由零件18進行沖孔,后續(xù)工位19進行落料5、料由大氣壓吹出,謝謝各位老師!,,