
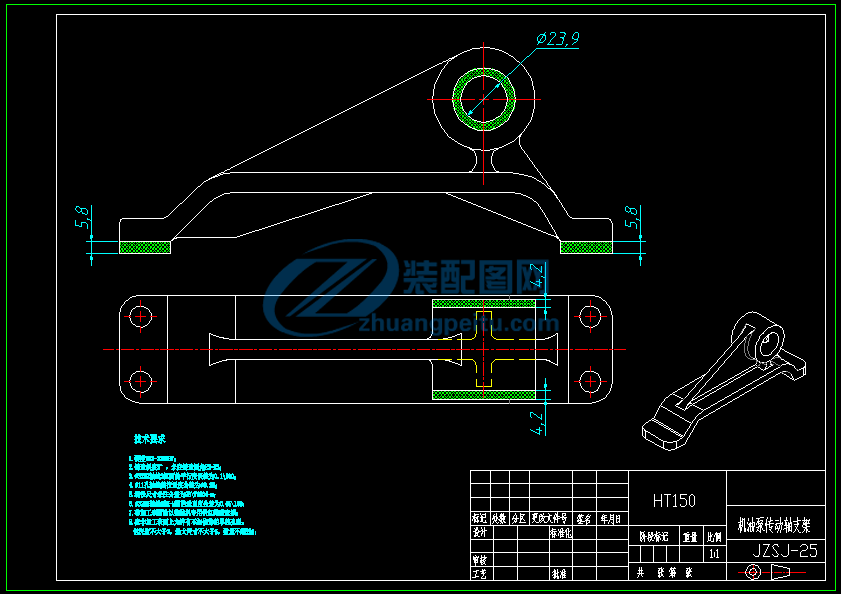
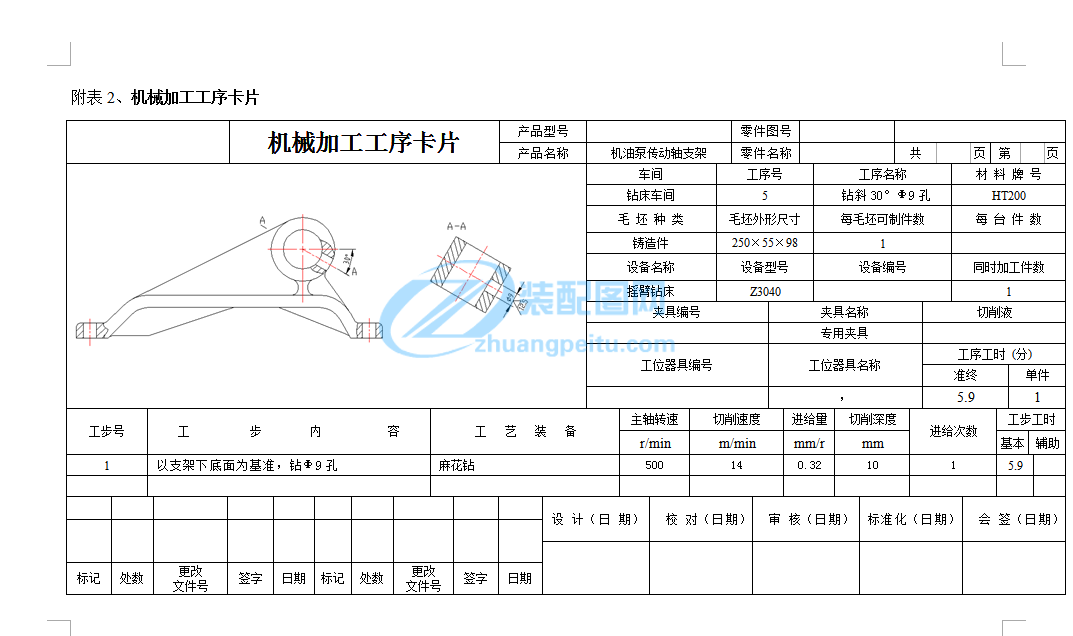
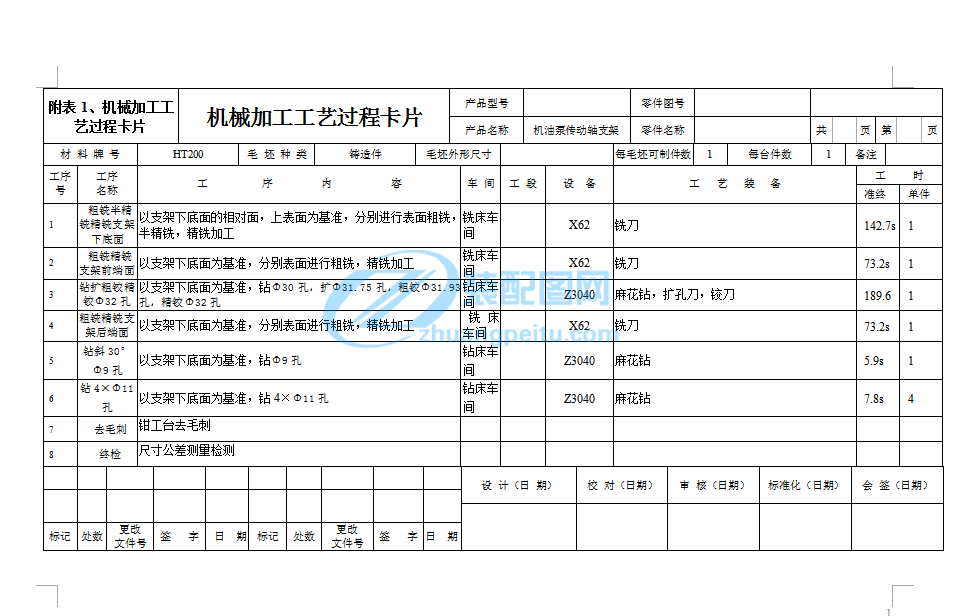
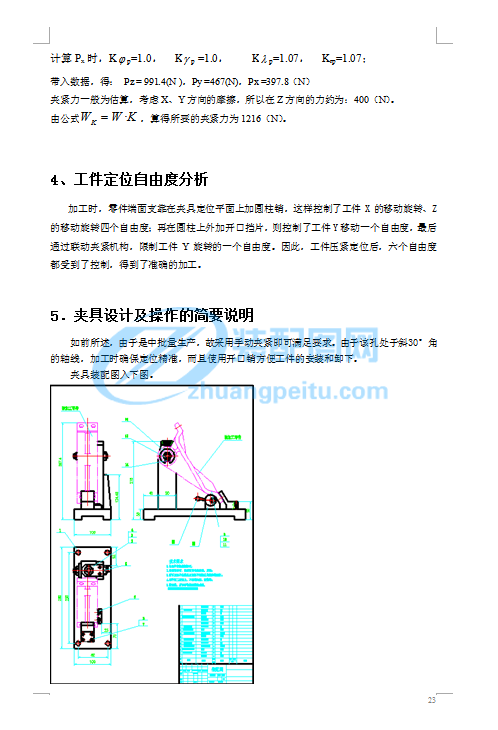

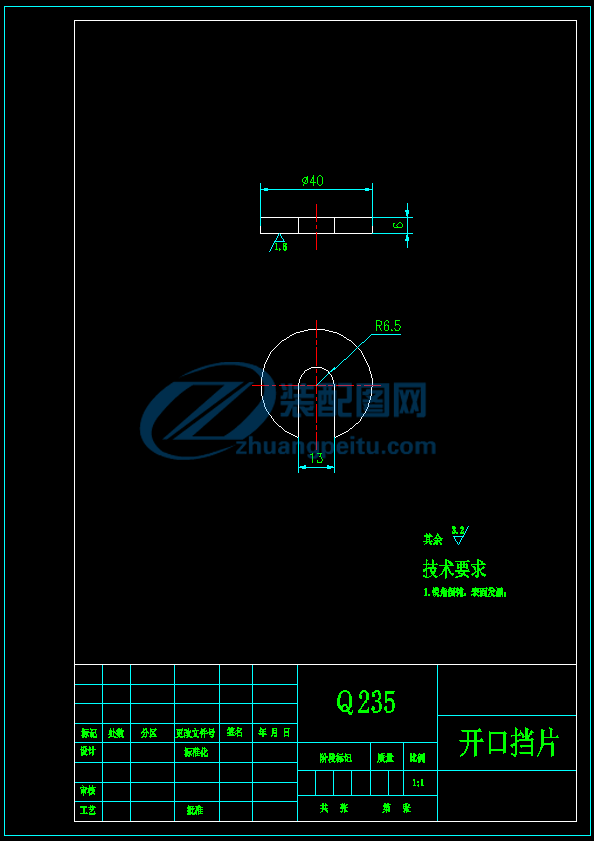
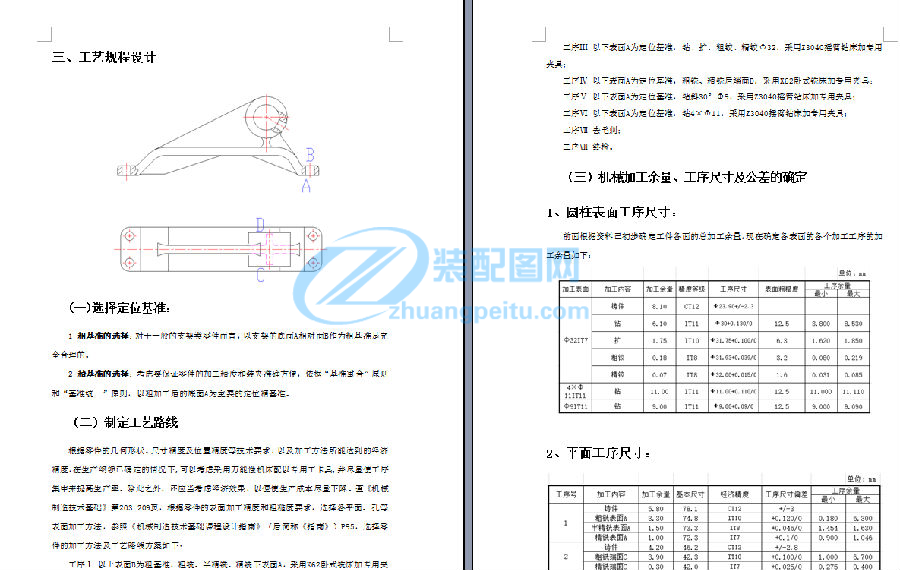
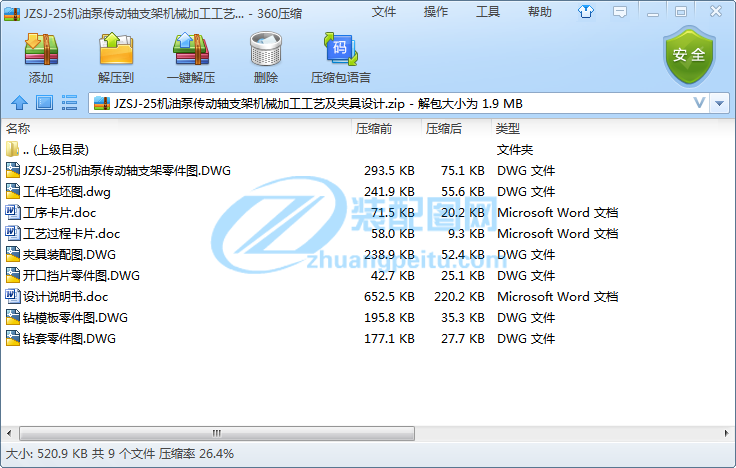
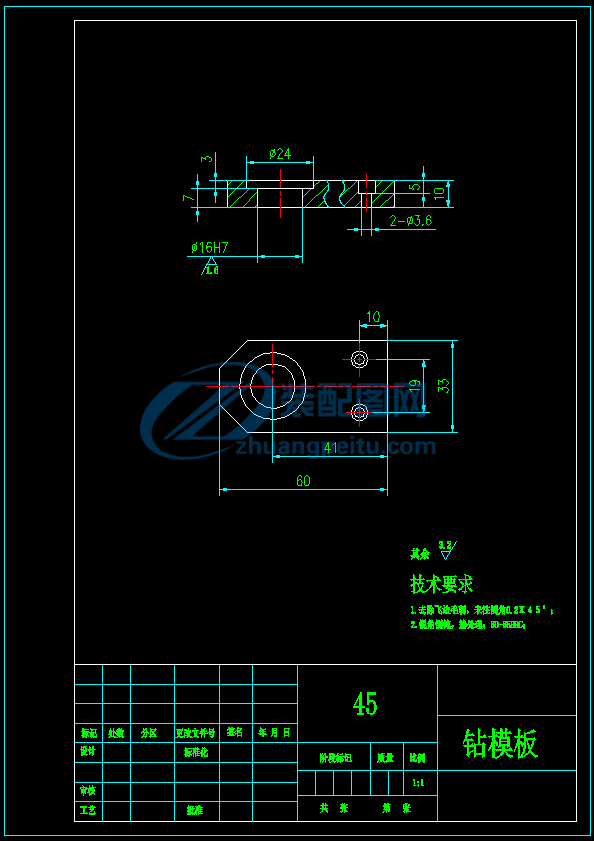
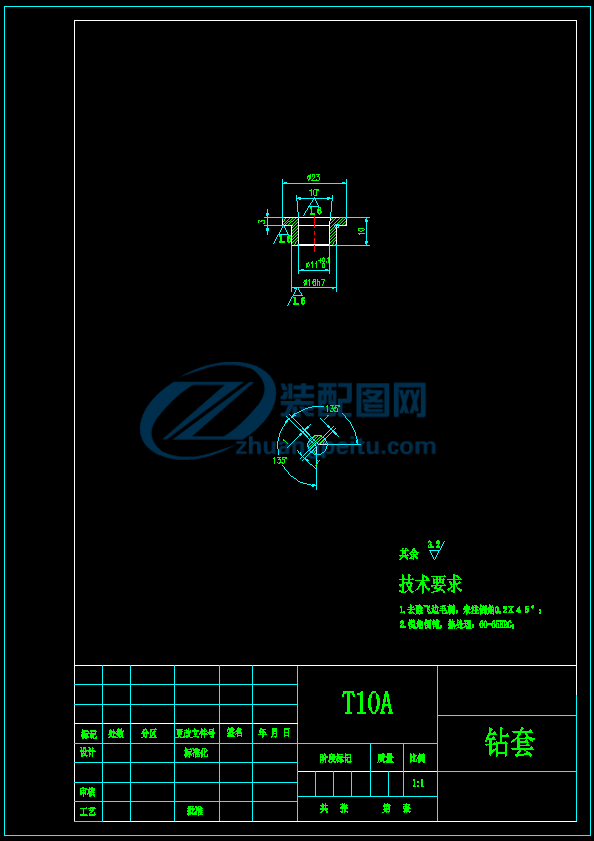
附表2、機械加工工序卡片
機械加工工序卡片
產(chǎn)品型號
零件圖號
產(chǎn)品名稱
機油泵傳動軸支架
零件名稱
共
頁
第
頁
車間
工序號
工序名稱
材 料 牌 號
鉆床車間
5
鉆斜30°Φ9孔
HT200
毛 坯 種 類
毛坯外形尺寸
每毛坯可制件數(shù)
每 臺 件 數(shù)
鑄造件
250×55×98
1
設(shè)備名稱
設(shè)備型號
設(shè)備編號
同時加工件數(shù)
搖臂鉆床
Z3040
1
夾具編號
夾具名稱
切削液
專用夾具
工位器具編號
工位器具名稱
工序工時 (分)
準終
單件
,
5.9
1
工步號
工 步 內(nèi) 容
工 藝 裝 備
主軸轉(zhuǎn)速
切削速度
進給量
切削深度
進給次數(shù)
工步工時
r/min
m/min
mm/r
mm
基本
輔助
1
以支架下底面為基準,鉆Φ9孔
麻花鉆
500
14
0.32
10
1
5.9
設(shè) 計(日 期)
校 對(日期)
審 核(日期)
標準化(日期)
會 簽(日期)
標記
處數(shù)
更改
文件號
簽字
日期
標記
處數(shù)
更改
文件號
簽字
日期
1
1
附表1、機械加工工藝過程卡片
機械加工工藝過程卡片
產(chǎn)品型號
零件圖號
產(chǎn)品名稱
機油泵傳動軸支架
零件名稱
共
頁
第
頁
材 料 牌 號
HT200
毛 坯 種 類
鑄造件
毛坯外形尺寸
每毛坯可制件數(shù)
1
每臺件數(shù)
1
備注
工序號
工序
名稱
工 序 內(nèi) 容
車 間
工 段
設(shè) 備
工 藝 裝 備
工 時
準終
單件
1
粗銑半精銑精銑支架下底面
以支架下底面的相對面,上表面為基準,分別進行表面粗銑,半精銑,精銑加工
銑床車間
X62
銑刀
142.7s
1
2
粗銑精銑支架前端面
以支架下底面為基準,分別表面進行粗銑,精銑加工
銑床車間
X62
銑刀
73.2s
1
3
鉆擴粗鉸精鉸Φ32孔
以支架下底面為基準,鉆Φ30孔,擴Φ31.75孔,粗鉸Φ31.93孔,精鉸Φ32孔
鉆床車間
Z3040
麻花鉆,擴孔刀,鉸刀
189.6
1
4
粗銑精銑支架后端面
以支架下底面為基準,分別表面進行粗銑,精銑加工
銑床車間
X62
銑刀
73.2s
1
5
鉆斜30°Φ9孔
以支架下底面為基準,鉆Φ9孔
鉆床車間
Z3040
麻花鉆
5.9s
1
6
鉆4×Φ11孔
以支架下底面為基準,鉆4×Φ11孔
鉆床車間
Z3040
麻花鉆
7.8s
4
7
去毛刺
鉗工臺去毛刺
8
終檢
尺寸公差測量檢測
設(shè) 計(日 期)
校 對(日期)
審 核(日期)
標準化(日期)
會 簽(日期)
標記
處數(shù)
更改
文件號
簽 字
日 期
標記
處數(shù)
更改
文件號
簽 字
日 期
1
序言
大三第二學(xué)期我們進行了《機械制造技術(shù)基礎(chǔ)》課程的學(xué)習(xí),并且在大二第一學(xué)期也進行過金工實習(xí)。為了鞏固所學(xué)知識,在我們進行畢業(yè)設(shè)計之前對所學(xué)各課程的進行一次深入的綜合性的總復(fù)習(xí),也是作為一次理論聯(lián)系實際的訓(xùn)練,我們進行了本次課程設(shè)計。
通過這次課程設(shè)計,對自己未來將從事的工作進行了一次適應(yīng)性訓(xùn)練,從中鍛煉了自己分析問題、解決問題的能力,同時,在課程設(shè)計過程中,我們通過認真查閱資料,切實地鍛煉了我們自我學(xué)習(xí)的能力。另外,在設(shè)計過程中,經(jīng)過老師的悉心指導(dǎo)和同學(xué)們的熱心幫助,我順利完成了本次設(shè)計任務(wù)。
由于能力所限,設(shè)計尚有許多不足之處,懇請各位老師給予批評指正。
目錄
一、零件的分析 1
(一)零件的作用 1
(二)零件的工藝分析 1
(三)確定生產(chǎn)類型 1
二、確定毛坯 2
1、確定毛坯種類: 2
2、確定鑄件加工余量、毛坯尺寸及公差: 2
三、工藝規(guī)程設(shè)計 3
(一)選擇定位基準: 3
(二)制定工藝路線 3
(三)機械加工余量、工序尺寸及公差的確定 4
1、圓柱表面工序尺寸: 4
2、平面工序尺寸: 4
3、確定切削用量及時間定額: 5
四、 夾具設(shè)計 20
(一)問題的提出 20
(二)夾具設(shè)計 20
1、定位基準選擇 20
2、夾具夾緊裝置的確定 21
3、夾緊力大小的計算 21
4、工件定位自由度分析 23
5.夾具設(shè)計及操作的簡要說明 23
2
一、零件的分析
(一)零件的作用
題目所給的零件是機油泵傳動軸支架 。它位于傳動軸的端部,主要是支撐傳動軸連接油口,也起到固定機油泵的作用。它是拖拉機里用到最普遍的零件之一,結(jié)構(gòu)簡單,體積較小,屬于叉架類零件,其中的Φ32孔要與傳動軸配合,要求精度較高。
(二)零件的工藝分析
零件的材料為HT200,灰鑄鐵生產(chǎn)工藝簡單,鑄造性能優(yōu)良,但塑性較差、脆性高,切削性能良好。以下是機油泵傳動軸支架需要的加工要求:
1)Φ32孔要求精度較高,需要進行精鉸加工;
2)Φ9孔與Φ11孔要求精度較低,使用鉆床加工一次即可
3)Φ11孔下底面要求精度較高,需要進行精銑。
由上面分析可知,可以精加工機油泵傳動軸支架下端面,然后以此作為精基準采用專用夾具進行加工,并且保證位置精度要求。再根據(jù)各加工方法的經(jīng)濟精度及機床所能達到的位置精度,并且此叉架類零件沒有復(fù)雜的加工曲面,所以根據(jù)上述技術(shù)要求采用常規(guī)的加工工藝均可保證。
(三)確定生產(chǎn)類型
依設(shè)計題目知:Q=5000臺/年,n=1件/臺;結(jié)合生產(chǎn)實際,備品率α和廢品率β分別為10%和1%。代入公式N=Qn(1+α)(1+β)得N=5555件/年
零件質(zhì)量為5kg,查表2-1可知其屬輕型零件,生產(chǎn)類型為中批生產(chǎn)。
二、確定毛坯
1、確定毛坯種類:
零件材料為HT200?;诣T鐵抗拉強度不低于150MPa,抗彎強度不低于330MPa,根據(jù)材料性質(zhì),因此應(yīng)該選用鑄造件,由于該零件的產(chǎn)量為5000,已達中批生產(chǎn)的水平,而且零件的輪廓尺寸不大,故可鑄造成型,提高生產(chǎn)效率,保證加工的精度。
2、確定鑄件加工余量、毛坯尺寸及公差:
1)求最大輪廓尺寸。根據(jù)零件圖計算輪廓尺寸,長250mm,寬55mm,高98mm,故最大輪廓尺寸為250mm。
2)選取公差等級CT。由表5-1,鑄造方法選擇砂型手工,鑄造材料按灰鑄鐵,公差等級范圍為11~14級,選取12級。
3)求鑄件公差尺寸公差。根據(jù)加工的基本尺寸和鑄件公差等級CT,由表5-3查得,公差帶相對于基本尺寸對稱分布。
4)求機械加工余量等級。由表5-5查得,鑄造方法選擇砂型手工,鑄造材料按灰鑄鐵,得機械加工余量等級范圍為F~H級,選取G級。
5)求RMA。對所有加工表面取同一個數(shù)值,由表5-4查最大輪廓尺寸為250mm、機械加工余量等級為G級,得RMA數(shù)值為2.8mm。
6)求毛坯基本尺寸。Φ9孔和4×Φ11孔較小,鑄成實心。
A面為單側(cè)加工,毛坯基本尺寸:
R=F+RMA+CT/2=78.1mm
C面和D面屬雙側(cè)加工。由公式求出:
R= F+2RMA+CT/2=50.4mm
Φ32H7孔屬內(nèi)腔加工,由公式求出:
R= F-2RMA-CT/2=23.9mm
表1 支架鑄件毛坯尺寸公差與加工余量
3、繪制鑄件毛坯圖
三、工藝規(guī)程設(shè)計
(一)選擇定位基準:
1 粗基準的選擇:對于一般的支架類零件而言,以支架的底面A相對面B作為粗基準是完全合理的。
2 精基準的選擇:考慮要保證零件的加工精度和裝夾準確方便,依據(jù)“基準重合”原則和“基準統(tǒng)一”原則,以粗加工后的底面A為主要的定位精基準。
(二)制定工藝路線
根據(jù)零件的幾何形狀、尺寸精度及位置精度等技術(shù)要求,以及加工方法所能達到的經(jīng)濟精度,在生產(chǎn)綱領(lǐng)已確定的情況下,可以考慮采用萬能性機床配以專用工卡具,并盡量使工序集中來提高生產(chǎn)率。除此之外,還應(yīng)當(dāng)考慮經(jīng)濟效果,以便使生產(chǎn)成本盡量下降。查《機械制造技術(shù)基礎(chǔ)》第203-209頁,根據(jù)零件的表面加工精度和粗糙度要求,選擇各平面、孔等表面加工方法,參照《機械制造技術(shù)基礎(chǔ)課程設(shè)計指南》(后簡稱《指南》)P95,選擇零件的加工方法及工藝路線方案如下:
工序Ⅰ 以上表面B為粗基準,粗銑、半精銑、精銑下表面A,采用X62臥式銑床加專用夾具;
工序Ⅱ 以下表面A為定位基準,粗銑,精銑前端面C,采用X62臥式銑床加專用夾具;
工序Ⅲ 以下表面A為定位基準,鉆、擴、粗鉸、精鉸Φ32,采用Z3040搖臂鉆床加專用夾具;
工序Ⅳ 以下表面A為定位基準,粗銑、精銑后端面D,采用X62臥式銑床加專用夾具;
工序Ⅴ 以下表面A為定位基準,鉆斜30°Φ9,采用Z3040搖臂鉆床加專用夾具;
工序Ⅵ 以下表面A為定位基準,鉆4×Φ11,采用Z3040搖臂鉆床加專用夾具;
工序Ⅶ 去毛刺;
工序Ⅷ 終檢。
(三)機械加工余量、工序尺寸及公差的確定
1、圓柱表面工序尺寸:
前面根據(jù)資料已初步確定工件各面的總加工余量,現(xiàn)在確定各表面的各個加工工序的加工余量如下:
2、平面工序尺寸:
3、確定切削用量及時間定額:
工序Ⅰ 粗銑、半精銑、精銑下表面A,以上表面B為粗基準;
一.粗銑下表面A
1)加工條件
工件材料:HT200,σb =170~240MPa,鑄造;工件尺寸:aemax=55mm,l=52mm;
加工要求:粗銑下表面A,加工余量3.3mm;
機床:X62臥式銑床;
刀具:YG6硬質(zhì)合金端銑刀。銑削寬度ae≤90,深度ap≤5。
故根據(jù)《指南》表5-113,選取鑲齒三面刃銑刀,刀具直徑d0=100mm,寬L=20mm,孔徑d=27mm,齒數(shù)z=10,該銑刀為標準規(guī)格無需定制。再根據(jù)表5-151,選擇刀具前角γ0=0°后角α0=8°,副后角α0’=10°,刃傾角λs=-10°,主偏角Kr=60°,過渡刃Krε=30°,副偏角Kr’=5°。
2)切削用量
①確定切削深度ap
因為余量較小,故選擇ap=3.3mm,一次走刀即可完成。
②確定每齒進給量fz
由于本工序為粗加工,尺寸精度和表面質(zhì)量可不考慮,從而可采用不對稱端銑,以提高進給量提高加工效率。根據(jù)《指南》表5-106,使用YG6硬質(zhì)合金端銑刀加工,機床功率為7.5kw(據(jù)《指南》表5-154,X62臥式銑床)時:
fz=0.14~0.24mm/z
故選擇:fz=0.18mm/z。
③確定刀具壽命及磨鈍標準
根據(jù)《指南》表5-156,銑刀刀齒后刀面最大磨損量為1.5mm;由于銑刀直徑d0=100mm,故刀具使用壽命T=180min(據(jù)《指南》表5-157)。
④計算切削速度vc和每分鐘進給量vf
根據(jù)《指南》表5-156,當(dāng)d0=100mm,Z=10,ap≤3.5,fz≤0.18mm/z時,、、.各修正系數(shù)為:kMV= 1.0,kSV= 0.8。切削速度計算公式為:
其中ae = 55mm,a p = 3.3mm,Cv = 245,qv = 0.2,xv = 0.15,yv = 0.35,kv = kMv × kSv = 1.0 ′ 0.8 = 0.8,uv = 0.2,pv = 0,m = 0.32,T = 180min,f z = 0.18mm/ z,Z =10,為切削條件改變時的切削速度修正系數(shù),單位為m/min;將以上數(shù)據(jù)代入公式:
上數(shù)據(jù)代入公式:
確定機床主軸轉(zhuǎn)速:
根據(jù)《指南》表5-82,選擇
則實際切削速度為:
工作臺每分鐘進給量為:
根據(jù)X62型臥式銑床工作臺進給量表《指南》表5-83,選擇,則實際的每齒進給量為
⑤校驗機床功率
根據(jù)《指南》表5-134,近似為Pcc=4.9kw,根據(jù)機床使用說明書,主軸允許功率Pcm=7.5×0.75kw=5.625kw>Pcc。故校驗合格。最終確定:ap=3.3mm,nc=190r/min,,vc=60m/min,fz=0.16mm/z。
3)計算基本工時
根據(jù)《指南》表2-28,端面銑刀的基本時間計算公式為
∴,,
代入數(shù)據(jù),得加工時間:
二.半精銑下表面A
1)加工條件
刀具:YG6硬質(zhì)合金端銑刀;
機床:X62臥式銑床;
2)切削用量
①確定切削深度ap
左右端面加工余量Z=1.5mm,因為余量較小,故ap=1.5mm
②確定每齒進給量fz
本道工序是半精銑下表面A,根據(jù)《指南》表5-154,使用YG6硬質(zhì)合金端銑刀加工,據(jù)《指南》表5-78,X62臥式銑床的功率為7.5kw時:每轉(zhuǎn)進給量,現(xiàn)取,則每齒進給量。
③確定刀具壽命及磨鈍標準
根據(jù)《指南》表5-156,銑刀刀齒后刀面最大磨損量為0.5mm;由于銑刀直徑d0=100mm,故刀具使用壽命T=180min(據(jù)《指南》P205表5-157)。
④確定切削速度和工作臺每分鐘進給量。按《指南》表2-17中公式計算,得,
根據(jù)《指南》表5-82,選擇
則實際切削速度:
工作臺每分鐘進給量為:
根據(jù)X62型臥式銑床工作臺進給量表《指南》表5-83,選擇,則實際的每齒進給量為
3) 計算基本工時
根據(jù)《指南》表2-28,端面銑刀的基本時間計算公式為
∴,,
代入數(shù)據(jù),得加工時間:
三.精銑下表面A
1)加工條件
刀具:YG6硬質(zhì)合金端銑刀;
機床:X62臥式銑床;
2)切削用量
①確定切削深度ap
左右端面加工余量Z=1.0mm,因為余量較小,故ap=1.0mm
②確定每齒進給量fz
本道工序是精銑下表面A,根據(jù)《指南》表5-154,使用YG6硬質(zhì)合金端銑刀加工,據(jù)《指南》表5-78,X62臥式銑床的功率為7.5kw時:每轉(zhuǎn)進給量,現(xiàn)取,則每齒進給量。
③確定刀具壽命及磨鈍標準
根據(jù)《指南》表5-156,銑刀刀齒后刀面最大磨損量為0.5mm;由于銑刀直徑d0=100mm,故刀具使用壽命T=180min(據(jù)《指南》P205表5-157)。
④確定切削速度和工作臺每分鐘進給量。按《指南》表2-17中公式計算,得,
根據(jù)《指南》表5-82,選擇
則實際切削速度:
工作臺每分鐘進給量為:
根據(jù)X62型臥式銑床工作臺進給量表《指南》表5-83,選擇,則實際的每齒進給量為
4) 計算基本工時
根據(jù)《指南》表2-28,端面銑刀的基本時間計算公式為
∴,,
代入數(shù)據(jù),得加工時間:
工序Ⅱ 粗銑精銑前端面C,以下表面A為定位基準
一.粗銑前端面C
1)加工條件
工件材料:HT200,σb =170~240MPa,鑄造;工件尺寸:aemax=52mm,l=52mm;
加工要求:粗銑前端面C,加工余量3.9mm;
機床:X62臥式銑床;
刀具:YG6硬質(zhì)合金端銑刀。銑削寬度ae≤90,深度ap≤5。
故根據(jù)《指南》表5-113,選取鑲齒三面刃銑刀,刀具直徑d0=100mm,寬L=20mm,孔徑d=27mm,齒數(shù)z=10,該銑刀為標準規(guī)格無需定制。再根據(jù)表5-151,選擇刀具前角γ0=0°后角α0=8°,副后角α0’=10°,刃傾角λs=-10°,主偏角Kr=60°,過渡刃Krε=30°,副偏角Kr’=5°。
2)切削用量
①確定切削深度ap
因為余量較小,故選擇ap=3.9mm,一次走刀即可完成。
②確定每齒進給量fz
由于本工序為粗加工,尺寸精度和表面質(zhì)量可不考慮,從而可采用不對稱端銑,以提高進給量提高加工效率。根據(jù)《指南》表5-106,使用YG6硬質(zhì)合金端銑刀加工,機床功率為7.5kw(據(jù)《指南》表5-154,X62臥式銑床)時:
fz=0.14~0.24mm/z
故選擇:fz=0.18mm/z。
③確定刀具壽命及磨鈍標準
根據(jù)《指南》表5-156,銑刀刀齒后刀面最大磨損量為1.5mm;由于銑刀直徑d0=100mm,故刀具使用壽命T=180min(據(jù)《指南》表5-157)。
④計算切削速度vc和每分鐘進給量vf
根據(jù)《指南》表5-156,當(dāng)d0=100mm,Z=10,ap≤3.5,fz≤0.18mm/z時,、、.各修正系數(shù)為:kMV= 1.0,kSV= 0.8。切削速度計算公式為:
其中ae = 52mm,a p = 3.9mm,Cv = 245,qv = 0.2,xv = 0.15,yv = 0.35,kv = kMv × kSv = 1.0 ′ 0.8 = 0.8,uv = 0.2,pv = 0,m = 0.32,T = 180min,f z = 0.18mm/ z,Z =10,為切削條件改變時的切削速度修正系數(shù),單位為m/min;將以上數(shù)據(jù)代入公式:
上數(shù)據(jù)代入公式:
確定機床主軸轉(zhuǎn)速:
根據(jù)《指南》表5-82,選擇
則實際切削速度為:
工作臺每分鐘進給量為:
根據(jù)X62型臥式銑床工作臺進給量表《指南》表5-83,選擇,則實際的每齒進給量為
⑤校驗機床功率
根據(jù)《指南》表5-134,近似為Pcc=4.5kw,根據(jù)機床使用說明書,主軸允許功率Pcm=7.5×0.75kw=5.625kw>Pcc。故校驗合格。最終確定:ap=3.9mm,nc=190r/min,,vc=60m/min,fz=0.16mm/z。
3)計算基本工時
根據(jù)《指南》表2-28,端面銑刀的基本時間計算公式為
∴,,
代入數(shù)據(jù),得加工時間:
二.精銑前端面C
1)加工條件
刀具:YG6硬質(zhì)合金端銑刀;
機床:X62臥式銑床;
2)切削用量
①確定切削深度ap
左右端面加工余量Z=0.3mm,因為余量較小,故ap=0.3mm
②確定每齒進給量fz
本道工序是精銑前端面C,根據(jù)《指南》表5-154,使用YG6硬質(zhì)合金端銑刀加工,據(jù)《指南》表5-78,X62臥式銑床的功率為7.5kw時:每轉(zhuǎn)進給量,現(xiàn)取,則每齒進給量。
③確定刀具壽命及磨鈍標準
根據(jù)《指南》表5-156,銑刀刀齒后刀面最大磨損量為0.5mm;由于銑刀直徑d0=100mm,故刀具使用壽命T=180min(據(jù)《指南》P205表5-157)。
④確定切削速度和工作臺每分鐘進給量。按《指南》表2-17中公式計算,得,
根據(jù)《指南》表5-82,選擇
則實際切削速度:
工作臺每分鐘進給量為:
根據(jù)X62型臥式銑床工作臺進給量表《指南》表5-83,選擇,則實際的每齒進給量為
5) 計算基本工時
根據(jù)《指南》表2-28,端面銑刀的基本時間計算公式為
∴,,
代入數(shù)據(jù),得加工時間:
工序Ⅲ 鉆、擴、粗鉸、精鉸Φ32,以下表面A為定位基準
一、鉆Φ30mm
1)加工條件
刀具:選擇高速鋼麻花鉆鉆頭,粗鉆時do=30mm,選取主偏角=59°,鉆頭采用雙錐后磨橫刀,
機床:Z3040搖臂鉆床。
2)選擇切削用量
①確定進給量
按加工要求確定進給量:查《指南》表5-135, f = 0.54 ~ 0.66mm/ r,l /d = 42/32 =1.31 <3,由《指南》表5-135,修正系數(shù)為0.5,則:
f = (0.54 ~ 0.66) ′ 0.5 = (0.27 ~ 0.33)mm/ r
根據(jù)《指南》表5-70,最終選擇進給量f = 0.32mm/ r。
由于是通孔加工,為避免即將鉆穿時鉆頭折斷,故應(yīng)在即將鉆穿時停止自動進給而改為手動進給。
根據(jù)《指南》表2-15查出,鉆孔時軸向力
其中CF=420,zF=1,yF=0.8,軸向力修正系數(shù)為=1.06,代入數(shù)據(jù)得Ff=5368N。根據(jù)表5-68查Z3040搖臂鉆床,機床進給機構(gòu)允許的最大軸向力為16000N﹥Ff,故所選進給量可用。
②確定鉆頭磨鈍標準及壽命
查《指南》表5-138,后刀面最大磨損限度,1.2mm,壽命T = 75min.
③切削速度
查《指南》表2-13,切削速度計算公式為:
其中,Cv =11.1,d 0 = 30mm,zv = 0.25,m = 0.125,ap = d/2=15,xv = 0,yv = 0.4,f = 0.32,查得修正系數(shù):kTv = 1.0,=,klv = 0.85,ktv = 1.0,故實際的切削速度:
確定機床主軸轉(zhuǎn)速:
根據(jù)《指南》表5-69,選擇
則實際切削速度為:
④檢驗機床扭矩及功率
查《指南》表2-15,轉(zhuǎn)矩與功率的計算公式:
其中CM=0.206,zM=2.0,yM=0.8,修正系數(shù)為=1.06,代入數(shù)據(jù)得MC=79N*M, PC=1.6kW。
查機床使用說明書,PE = 3′0.81 = 2.43kw。
由于PC
收藏