汽車彈簧液壓彎管機設計
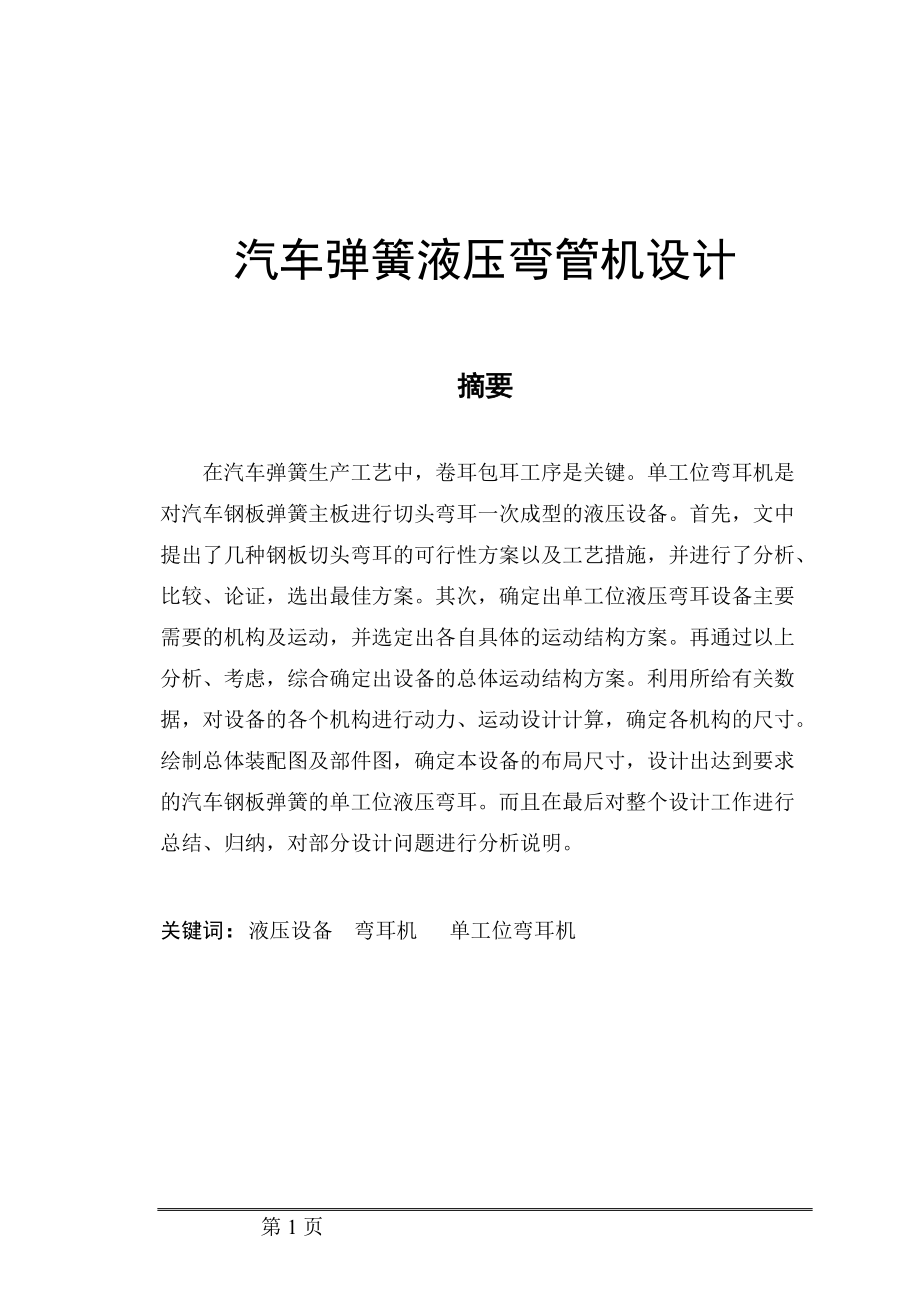


《汽車彈簧液壓彎管機設計》由會員分享,可在線閱讀,更多相關《汽車彈簧液壓彎管機設計(40頁珍藏版)》請在裝配圖網上搜索。
1、 汽車彈簧液壓彎管機設計 摘要 在汽車彈簧生產工藝中,卷耳包耳工序是關鍵。單工位彎耳機是對汽車鋼板彈簧主板進行切頭彎耳一次成型的液壓設備。首先,文中提出了幾種鋼板切頭彎耳的可行性方案以及工藝措施,并進行了分析、比較、論證,選出最佳方案。其次,確定出單工位液壓彎耳設備主要需要的機構及運動,并選定出各自具體的運動結構方案。再通過以上分析、考慮,綜合確定出設備的總體運動結構方案。利用所給有關數據,對設備的各個機構進行動力、運動設計計算,確定各機構的尺寸。繪制總體裝配圖及部件圖,確定本設備的布局尺寸,設計出達到要求的汽車鋼板彈簧的單工位液壓彎耳。而且在最后對整個設計工作進行總結、歸納,
2、對部分設計問題進行分析說明。 關鍵詞:液壓設備 彎耳機 單工位彎耳機 Abstract Bending is the key in the plate spring production.This description is a general design and elucidation relevant to automobile steel plate bending machine what is used as cutting-out the head of the plate spring and bending the plate spri
3、ng. Designed in the description is a single working hydraulic plate bending equipments. First, in this description, it raised several executable programmers and posed several technological specifications to product the automobile plate spring. And then we proceeded to compare and argued the program
4、mers. Be virtue of the argument, we selected the best project. Then make sure the main requirements of the machines and sport construction of the single working hydraulic plate bending equipments, and definitude the specific structures. Then we were virtue of these researches, and combined various o
5、pinions, we made selection out concretely the project again. Sum up the above analysis and consider again, synthesize to make sure the total sport construction of the equipments and the project. Then we can be virtue of the parameter and refer to the reference book, make use of an each organization
6、for count, we proceed to design and calculate of the motive power and sport movement of the equipment, and make sure the size of each organization. Then we drafted the general assembly diagram and parts assembly diagram of this equipment, certain this equipments attain the requests that we needed t
7、o product the spring. At finally proceeds to whole design work, and we can get the equipment of the simplex working bending machine of the automobile spring. Key word: Hydraulic equipment Bending equipment A single working bending equipment 目錄 第一章 總體方案論證 6 1.1 液壓式雙工位彎橢圓耳型設備介紹 6
8、1.1.1 生產布置 6 1.1.2 工藝措施 6 1.2機械式多工位卷耳設備介紹 7 1.2.1 生產布置 7 1.2.2 工藝措施 7 1.3 液壓式單工位彎耳設備介紹 7 1.3.1 生產布置 8 1.3.2 工藝措施 8 1.4方案分析比較 9 第二章 具體運動結構方案設計 11 2.1 抽芯機構運動結構方案的選定 11 2.2切頭機構運動結構方案選定 12 2.3 定位機構運動結構方案選定 14 2.4 抓緊機構運動結構方案選定 15 2.5壓緊機構運動結構方案選定 15 2.6 轉位彎耳機構運動結構方案選定 16 2.7工作臺升降機構運動結構方
9、案選定 17 第三章 總體方案的選定 19 3.1 設備工作程序如下: 20 第四章 設計參數 21 第五章 計算 22 5.1 動力設計計算 22 5.1.1 壓緊缸載荷分析并選定壓緊缸缸徑 22 5.1.2計算切頭缸載荷并選定切頭缸缸徑。 22 5.1.3計算抓緊缸載荷并選定抓緊缸缸徑 23 5.1.4分析擺動缸載荷并選定擺動缸缸徑 26 5.1.5計算轉動缸載荷并選定轉動缸缸徑 26 5.1.6 分析移位缸載荷并選定移動缸缸徑 27 5.2 運動設計計算 28 5.2.1 確定切頭刀具工作角度: 28 5.2.2 確定齒輪齒條模數及齒輪齒數 29 5.
10、2.3計算抓緊機構轉位角度 29 5.2.4計算轉位缸行程并選定標準行程 30 5.2.5計算切頭缸工作行程并選定標準行程 30 5.2.6分析壓緊缸工作行程并選定壓緊缸標準行程 31 5.2.7選定抓緊缸標準行程 31 5.2.8選定切頭機構移動缸標準行程 31 5.2.9計算切頭機構擺動缸并選定標準行程 32 5.2.10選定抽芯缸標準行程 32 5.2.11選定定位缸標準行程 33 5.3 選定各工作油缸標準型號 34 第六章 部分設計問題說明 35 6.1機架、切頭架及抓緊架結構及材料 35 6.2設備的潤滑措施 35 6.3芯軸的冷卻措施 36 結論 3
11、8 致 謝 39 參 考 文 獻 40 引言 汽車鋼板彈簧是極易損壞的零件,其主要是用于汽車、拖拉機和鐵道車輛中作為一種彈性懸掛裝置,起緩沖和減振作用,也可以在各種機械中作為防振裝置。具有機構簡單,修理方便的特點。它不僅用量大,消耗多,而且對汽車工業(yè)發(fā)展有不可替代作用。汽車彈簧單工位彎耳機是對汽車鋼板彈簧進行切頭彎耳的設備。 去年我到湖北東風汽車公司進行了實習,在實習中我發(fā)現其對鋼板彈簧彎耳工序都采用陳舊的單工位機械式彎耳設備或雙工位液壓式彎耳設備。而國外則大多采用單工位液壓式自動控制設備及工藝。我們對汽車彈簧單工位彎耳機設備的產品開發(fā)和研究可以提高我國的鋼板彈簧彎
12、耳技術,使我國的彈簧彎耳技術跟上國際技術水平,加速我國汽車產業(yè)的發(fā)展。 本文所設計的設備,實現了一機多能即切頭彎耳一機加工,提高生產效率,減低生產成本,使加工工藝變得簡單易行,并且縮短了工作節(jié)拍,提高了加工的質量。采用液壓和PC自動控制,使設備的維護變簡單。 第一章 總體方案論證 目前汽車生產廠家對鋼板彈簧彎耳這一工序主要有以下三種。 1.1 液壓式雙工位彎橢圓耳型設備介紹 該設備主要用于加工橢圓耳型的鋼板彈簧卷耳,該卷耳結構如圖1-1。 圖1-1 1.1.1 生產布置
13、 在生產中設備的布置如圖1-2。 工件→加熱設備—950℃→沖床—切頭→彎耳設備—成型→合格品 圖1-2 1.1.2 工藝措施 將鋼板彈簧加熱至9508C高溫,在沖床上切頭,然后在彎耳機上進行卷耳加工,完成一個合格的卷耳,其工藝流程見圖1-3。 1工位:切頭 2工位1工步:彎耳成型 2工步:抽芯取工件 圖1-3 1.2機械式多工位卷耳設備介紹 該設備用于加工鋼板彈簧卷耳耳型,耳型結構見圖1-4。
14、 卷耳 圖1-4 1.2.1 生產布置 在生產中,設備的布置如圖1-5。 工件→加熱設備—950℃→沖床— 切頭→彎耳設備 —彎耳→整形設備—整型→合格品 圖1-5 1.2.2 工藝措施 鋼板彈簧加熱至9508C高溫后,在沖床上進行切頭,在彎耳設備上分三個工步進行彎耳,最后在整形設備上進行整形,完成一個合格的卷耳耳型,其工藝流程見圖1-6。 工位1:切頭 2工位1工步
15、:初彎 2工步:二次彎曲 3工步:成型 3工位:整形 圖1-6 1.3 液壓式單工位彎耳設備介紹 該設備用于加工平卷耳。這種耳型較上、下卷耳及橢圓卷耳減小了耳型的內應力,因其縱向力作用方向和彈簧主片斷面中線重合,使用性能較上、下卷耳好,因此是以后汽車應用的趨勢,以前應用受阻礙的原因在于其制造較復雜。 平卷耳結構見圖1-7。 圖1-7 1.3.1 生產布置 生產中設備的布置見圖1-8。 工件→加熱設備—950℃→彎耳設備—成型→合格
16、品 圖1-8 1.3.2 工藝措施 將鋼板彈簧加熱至9508C高溫,在彎耳機上分3個工步完成一個彎耳彎曲。 其工藝流程見圖1-9。 工步1:切頭 工步2:抓緊轉位彎耳成型 工步3:抽芯取工件 圖1-9 1.4方案分析比較 從上面的方案分析可以知道:機械式多工位彎耳機設備屬于比較老的設備,其加工方法是靠模板的推移和工件沿模型強制卷曲成型。其模具復雜, 更換調整困難,生產效率不高,并且最后產品精度還須靠整型磨具來保證,提高了成本。雙工位液壓彎耳機雖然相對于機械式多工位彎耳機多了液壓自動制,多了芯軸結構,加工質量較容易保證,但同
17、樣存在即多了沖床設備,擴大了生產面積,增加了工人配額,勞動生產率還是很不高,工人勞動強度同樣過大等機械式多工位彎耳機的缺點。而單工位液壓彎耳設備較前兩種設備有了許多改進和優(yōu)點:首先,它將切頭功能揉合到了設備中實現了一機多能并且無須整型,減少了生產設備,縮小了生產面積,同時提高了生產效率,降低了工人勞動強度,減少了工人配額,降低了板簧生產成本。其次,設備采用了芯軸結構,在切頭時,對芯軸加了V形支承塊,使工藝的實施變得簡單。同時,設備有了切頭機構,縮短了工作節(jié)拍,單件生產時間變短,使工件在加工過程中溫度變化范圍減小,內部組織變動不大,可得到較好的組織結構,不易產生突出的加工應力及變形。因而在以上條
18、件保證下,能較好地保證加工質量,不易產生廢品。最后,該設備采用液壓傳動,便于實現PC自動控制避控制,所以維修簡單同時還確保了設備良好的工作性能及使用性能. 綜合以上的分析、論證,考慮到具體的條件,確定出本設備的設計原則有以下幾點: (1) 高的生產效率。盡量縮短各個動作時間,選用先進的工作方法及技術。 (2) 經濟性原則。盡量減少生產成本,節(jié)約原材料。減少工人配額。 (3) 設備制造、維護、使用簡單方便。盡量采用液壓傳動,以便采用PC自動控制。 (4) 擴大設備加工范圍。考慮鋼板彈簧卷耳規(guī)格的變化及設備的調整適應。 (5) 減輕工人的勞動強度。 第二章 具體運動結構方案設計
19、 在查詢相關資料及通過前面對各種設備方案及加工措施的分析、論證,可以確定出單工位液壓彎耳設備主要需要以下的機構及運動來保證所須零件的加工要求: 1 抽芯機構及運動; 2 切頭機構及運動; 3 定位機構及運動; 4 抓緊機構及運動; 5 壓緊機構及運動; 6 轉位彎耳機構及運動; 7 工作臺升降機構及運動。 其工藝流程圖如下: 現考慮具體的工作條件及工作要求來分析選定各個具體的運動結構方案。 2.1 抽芯機構運動結構方案的選定 液壓式單工位彎耳機增設芯軸來保證板簧加工耳型精度,而抽芯機構就是為了順利地卸出工件,使芯軸能脫離工件,方便地取出工件
20、。按工作條件而言,機構的運動很簡單,一個油缸產生的直線往復運動即可滿足要求。但從工作過程來看,如果芯軸在工件彎耳是固定不動,在抓緊機構抓緊工件后,轉位彎耳機構帶動抓緊機構轉動,工件同芯軸產生滑動摩擦,必然增加轉位機構轉動扭矩,同時因磨損對芯軸壽命也十分不利。但反過來讓芯軸轉動,而芯軸與活塞桿的聯接為固定聯接,在芯軸轉動時,活塞桿必然一起轉動,長期如此工作對油缸來說是絕對不允許的。因此,該機構中芯軸結構要求對活塞桿有相對轉動,同時又能隨活塞桿直線往復運動。在選定這種結構方案時,有許多方法?,F將列舉其中兩個方案進行分析、比較以選定最佳方案。見圖2-1。 方案A:作要求可以實現,但因聯接螺釘的裝拆
21、涉及到空間位置,無法讓開,所以對芯軸更換不便,不可取。 方案B:作能夠滿足要求,同時對裝配、更換芯軸極為有利,因此選用此方案。 方案A 方案B 圖2-1 2.2切頭機構運動結構方案選定 切掉多余的頭部是鋼板彈簧在耳型彎曲加工前必要的工藝,其方法是多種多樣的??梢栽跊_床上進行切頭,再在彎耳設備上進行彎耳,但這樣勢必擴大生產場地,,提高生產成本。從前面的分析論證已知:這樣的工藝不足取。當然也可以在彎耳設備上增設切頭刀具結構,利用彎耳的芯軸作為支承,切削去多余頭部,如圖2-2。但這樣對芯軸的影響很大,特別是對于加工板
22、簧中小耳型時,對芯軸的壽命是一個嚴重影響,甚至影響到工件加工質量,因而不可取??紤]到芯軸的因素,可以在刀具對工件進行切頭時為芯軸加一個支承,讓切削力不由芯軸來承受,見圖2-3。此時,在切削中,刀具、芯軸、V型塊支承和切頭架形成了一個封閉的系統,切削力對芯軸是沒有影響的。切削力的影響取決于切頭架剛性。如在設計中保證切頭架足夠的剛性,則此方案是不錯的。另外,在設計中還應該考慮保證切刀足夠的剛性。方案也有多種,如圖2-4。方案A:擇標準油缸來推動刀具,刀具同活塞桿的聯接依靠接頭,由于活塞桿教細細,而這樣一來,再加上接頭長度,很難保證刀具剛度,所以是不可取的;方案B:樣選擇標準油缸,只是對活塞桿作非標
23、準設計,加粗活塞桿,然后將活塞桿削邊,使刀具直接與活塞桿安裝聯接,縮短了結構長度,同時利用刀具上的導向鍵在切削中承受一部分切削力足以保證刀具的剛性。 圖2-2
24、 圖2-3 方案A 方案B 圖2-4 考慮到抽芯工步實施的需要,切頭機構還應該有以下的動作要求: (1) 機構能夠擺動,以使V型塊充分靠緊或離開芯軸,并為將來機構后移做準備。 (2) 切頭機構能夠后移,以便讓出轉位彎曲耳型時抓緊機構的空間行程位置。 再考慮到鋼板彈簧加工規(guī)格的變化,芯軸定隨之要產生變化。因此V型塊可設計為能更換調整的,以滿足板簧生產規(guī)格變動時的調整需要。 綜合以上分析、比較,選定切頭機構運動結構方案見圖2-5所示。
25、 圖2-5 2.3 定位機構運動結構方案選定 鋼板彈簧在進行切頭加工時,需要進行長度定位,工件上已經預先加工出定位孔,采用定位銷配合,即可方便的實現定位。在板簧切頭完畢后,定位銷必須退出定位孔,以保證下一工步彎耳成型的順利進行。定位銷的運動可以采用人工或機械傳動來實現,但都不利于生產效率的提高。因此采用一輔助油缸來實現定位銷的動作,以縮短工作節(jié)拍,提高工作效率。定位機構運動結構方案見圖2-6。 2.4 抓緊機構運動結構方案選定 工件在切頭加工完畢后,將進行卷耳成型加工。加工的原理很簡單:就是使工件包絡芯軸 近一周完成一個耳型。因此,工件及芯軸須轉動一定的
26、角度,因此必須將工件卡緊在芯軸上。運作的實現很簡單,采用一個液壓缸即可。只是設計中盡量降低抓緊機構的高度,以縮短切頭機構的讓位行程。抓緊機構運動結構方案見圖2-7。 抓緊塊 工件 芯軸 圖2-6 圖2-7 2.5壓緊機構運動結構方案選定 工件在切頭時必須將其壓緊,否則切削無法進行。壓緊的方法很多:可以手動壓緊,但生產效率太低,不符合設計要求;還可以采用機械傳動壓緊,但結構復雜,不利于設備制造及自動控制。因此,在本設計中選用液壓自動壓緊,既提高生產效率,降低
27、勞動強度,又便于自動控制。壓緊工件的點應盡量靠近工件被切削點,以防止工件在切削時因夾緊點太遠而發(fā)生饒曲,但太靠近切削位置又不會同抓緊機構發(fā)生干涉,因此以適宜的位置為度來選擇壓緊力作用點。考慮到壓緊塊的自重,應設計一導向柱,以保證壓緊動作的順利實施。另外,還應考慮工作過程需要,板簧在切頭時需要壓緊,而在轉位彎耳時應對工件無壓緊力但又不離開工件,以防止工件的翻轉。彎耳完成以后,才能離開工件以便順利取出工件。因此,也只有液壓傳動才能自動完成這一過程,并且方便、可靠。 壓緊機構運動結構方案見圖2-8。
28、圖2-8 2.6 轉位彎耳機構運動結構方案選定 工件被抓緊機構抓緊塊抓緊后,轉位機構將帶動抓緊機構轉動一定的角度位置,完成一個合格的卷耳。轉動的角位移不超過2(實際最大轉fmax =228.5288,最小轉角fmin=216.9288,見后面運動設計運算)??紤]在機械 選擇上力求簡單,最好能選擇標準的擺動油缸。查資料只能找到BM500型擺動油缸,但其工作壓力太低,不到1Mpa,輸出扭矩太小(*500kg.m)不能滿足使用要求。而設計制造非標準擺動油缸,反而增加了制造的成本。因此,在設計中選擇齒輪齒條機構。以一非標準油缸推動齒條移動,齒條帶動齒輪轉動,齒輪再帶動抓緊機構轉位來實現工作要求
29、。 齒條可相對機體水平布置也可立體布置。但因水平布置太占空間,而立體布置時結構并不超過設備的主體空間,為了使結構緊湊,節(jié)約空間,在本設計中采用齒條立體布置。 轉位彎耳機構運動結構方案見圖2-9。 圖2-9 2.7工作臺升降機構運動結構方案選定 鋼板彈簧有各種不同的規(guī)格,卷耳直徑有大有小(最大卷耳fmax=100mm,最小卷耳fmin=25mm,見后原始數據),因此在工件規(guī)格變換時,工作臺高度應能調整。調節(jié)的措施可用導軌絲杠及液壓升降,但考慮到設備工作臺簡單,重量較輕,升降位移小( 極限位移D=(100-25)/2=37.5mm),且調節(jié)時間較少,設計導軌絲
30、杠升降機構或液壓升降機構不符合經濟性原則,且使結構變得復雜,因此在本設計中采用螺栓螺母調整機構,依靠方桿緊固螺栓(見圖2-10)導向,能夠簡單、方便地保證工作要求。 工作臺升降機構運動結構方案見圖2-11。 圖2-10 圖2-11 第三章 總體方案的選定 通過以上對各個具體的運動方案的分析選定,綜合考慮確定的出設備總體結構方案。 總體運動結構方案見圖3-1。 圖3-1 1—壓緊缸 2—抓緊缸 3—切頭缸 4—擺位缸
31、 5 —移位缸 6—抽芯缸 7—轉動缸 8 —定位缸 9-芯軸 10-V形塊 11-齒輪 12-齒條 13-工件 3.1 設備工作程序如下: (1)950〇C高溫下工人放工件在工作臺上 (2)在設備工作臺上,定位銷對定位孔定位 (3) 1缸伸長壓緊工件 (4)5缸伸長,切頭機構移動到位 (5)4缸伸長,切頭機構擺動抱緊芯軸 (6)3缸伸長,刀具進行加工,對工件進行切頭 (7)3缸收縮,刀具離開工件 (8)4缸收縮,切頭機構擺動回位 (9)5缸收縮,切頭機構移動回位 (10)2缸伸長,抓
32、緊工件 (11)8缸收縮,拔出定位銷 (12)1缸少量收縮 (13)7缸伸長,推動抓緊機構轉位,彎耳卷耳成型 (14)2缸收縮,松開工件 (15)6缸收縮,抽出芯軸 (16)1缸大量收縮,讓位取出工件(工件由人工取出) (17)7缸收縮,抓緊機構因齒輪齒條帶動復位 (18)6缸伸長,芯軸復位 (19)8缸伸長,定位銷復位 (20)進入下一個工作循環(huán)。 第四章 設計參數 設備加工零件參數見表4—1: 表4—1 工件材料 60Si2Mn 工件加工溫度 900〇C—950〇C 工件板料最大厚度 max=15mm 工件板料最大寬度 Bmax
33、=100mm 工件板料最大截面積 Amax=1400mm2 工件最大卷耳直徑 fmax=100mm 工件最小卷耳直徑 fmin=25mm 工件單耳加工節(jié)拍 T=1min 設備加工零件如圖4-1 圖4-1 第五章 計算 5.1 動力設計計算 先根據工作條件確定各個油缸的載荷,再選定各油缸的缸徑。 5.1.1 壓緊缸載荷分析并選定壓緊缸缸徑 板簧在切頭加工時,壓緊缸壓緊工件,且定位銷將工件定位,工件受力分析如圖5-1。 圖5-1 由受力分析圖知:在切頭時,工件受力較復雜,不但受集中載荷切削力F,壓緊N,支持力N1,壓緊塊對工件滑動摩擦力
34、F1,及定位銷對工件反作用F2作用外,還受芯軸對工件的部分分布載荷q作用。因此,以目前的我的理論知識還無法對其進行定量的計算以求出壓緊力N1,因此只好以同型設備類比取壓緊缸的缸徑。壓緊缸缸徑取: D=32mm 5.1.2計算切頭缸載荷并選定切頭缸缸徑。 (1)鋼板彈簧工件在900〇C高溫下進行切頭加工,因而切頭缸產生的推力(即切削力)應大于工件在900〇C下的剪切極限力。 查《模具設計與制造簡明手冊》P67附表2得:50#碳素鋼在900〇C時的剪切強度 t =7kgf/mm2而無60Si2Mn在900〇C時的抗剪強度 t 又查《模具設計與制造簡明手冊》P70附表1得:50#碳素
35、鋼在常溫下的抗剪強度 t = 44—58kgf/mm2 60Si2Mn在常溫下的抗剪強度 t =72kgf/mm2,類比來求60Si2Mn彈簧鋼板在900〇C時的抗剪強度t900C,折換系數k=44/72=0.6111,則 t9008C=7/k=7/0.6111=11.545kgf/mm2 又根據設計參數知:加工的鋼板彈簧工件最大截面積Amax=1400mm2,由此計算出切斷工件所需的最大剪切力F’max F’max=Amaxt9008C=144011.545=16494.845kgf =161649.485N 因此,切頭缸需要的最大推力,但考慮到液壓缸的自重故可取
36、小些 Fmax=F’max=150000N (2)選定切頭缸缸徑 考慮到油缸工作壓力太高時,油缸的價格增高,同時在使用中有漏油等弊病不易解決。因此定油缸工作壓力為中高壓(大于8-16Mpa)以后各油缸定工作壓力同此原則。 因切頭缸推力較大,定其工作壓力為P=16Mpa 由公式D=計算出油缸的缸徑(以后各缸的計算同此公式)。 以上公式摘自《機械設計手冊》第四卷P17-262。 初定油缸時取ht=hmhvhd=0.9511=0.95 用公式求出切頭缸缸徑D,則 D==(4150000/3.140.9516)1/2=112.12mm查《機械設計手冊》第四卷P17-257表17-6-
37、2,取切頭缸缸徑 D=110mm(由于切頭架、液壓缸等自重故不用放大10%,并且工程上允許偏差3%是合格的) 5.1.3計算抓緊缸載荷并選定抓緊缸缸徑 工件在抓緊力N1作用下,繞芯軸中心線同芯軸一道轉動,鋼板發(fā)生塑性變形產生彎曲,此時壓緊塊雖然對工件無壓緊力作用,但工件必然因翅曲對壓緊塊產生一作用力,相應地壓緊塊對工件產生一反作用力N2,工件越難彎曲,N2就越大。工件受力如圖5-2。 圖5-2 現在我們可以反過來分析:假設抓緊力N1絕對能夠抓緊工件,抓緊機構固定不動,工件此時相當于懸臂梁,在力N
38、2的作用下,同樣能產生塑性變形,發(fā)生彎曲。因而可以理解為N2產生的彎矩M=N2L最小應該大于板簧工件在900℃時屈服極限力,才能使工件產生塑性變形而彎曲。即Mmin=∫AyssdA 假定工件受力如圖5-3。 圖5-3 查《材料力學》下冊P316例18-3公式: Mmin≥∫AyssdA=Iss/ymax=bh2ss/6 加工板簧工件最大截面積如圖5-4,由設計參數知: bmax=100mm hmax=
39、15mm 圖5-4 因此Mmin= bh2ss/6=100152 ss /6=3750 ss (1)確定900℃高溫下板簧60Si2Mn的屈服極限ss 由前計算知,60Si2Mn板簧在900℃時的抗剪應力t=11.54kgf/mm2,因而其許用抗剪應力[t]=11.54[ss] 取安全系數[ss]=1.5(因900℃高溫下材料ss/sb較小) [ss]取自《機械零件》P19表2-4 ∴[t]q=t[ss]=11.541.5=17.31kgf/mm2 又查《機械零件》P20表2-5 ?。篬t]q=(0.6~0.8)[s]
40、 [s]b=(1~1.2)[s] 求出許用應力[s]=[t]q/0.8=21.638kgf/mm2 求出許用應力強度[s]b=1.1[s]=1.121.638=23.8kgf/mm2 而sb=[s]b[ss],取安全系數[ss]=1.5 ∴sb=[s]b[ss]=23.81.5=35.7kgf/mm2 又查《機械零件》P19表2-4,取ss/sb=0.6,則 ss=sb0.6=35.70.6=21.42kgf/mm2 求出最小的彎矩Mmin≧3750ss=375021.42=80325kgfmm 又因Mmin=N2L,其中L=140mm(由總圖結構定出) ∴N2
41、=Mmin/L≧80325/140=574kgf 對工件抓緊轉位彎耳過程進行分析,如圖5-5 圖5-5 由圖可見,工件受抓緊力N1及壓緊塊反作用力N2作用,同時還受N1對工件及工件對芯軸產生的摩擦力F1 及F3作用。另N2在壓緊塊處對工件還產生一個摩擦力F2作用在工件上,因此抓緊機構要帶動工件轉位彎耳,必須滿足條件: F1≧F2+F3 其中F1=N1f1,F1相當于鋼和熱鋼的滑動摩擦。(查《機械設計手冊》第一卷,參考類比取摩擦系數f1=0.6) F2=N2f2,F2同樣相當于鋼和熱鋼的滑動摩擦,
42、取f2=0.6。 F3=N1f3,F3相當于熱鋼在軌道上摩擦。(查《機械設計手冊》第一卷,取f3=0.3) 故N1f1≧N2f2+N1f3 得:N1=1148(kgf)=11250(N) (2)計算選定抓緊缸缸徑 由計算出的抓緊缸載荷N1=11250N由公式計算出缸徑的步驟方法同前D= 其中ht=0.95,P取16Mpa ∴D=(411250/0.95163.14)1/2=30.71mm 按計算值增加10﹪,查《機械設計手冊》第四卷P17-257表17-6-2,取抓緊缸缸徑 D=32mm 5.1.4分析擺動缸載荷并選定擺動缸缸徑 擺動缸載荷只取決于切頭機
43、構自重,而切頭機構自重估算不大于500㎏,因此,查《機械設計手冊》第四卷P17-257表17-6-2,取擺動缸缸徑 D=32mm 5.1.5計算轉動缸載荷并選定轉動缸缸徑 板簧在彎耳時,轉動機構受力見圖5—6 由受力分析可見,工件在彎耳時齒條的推動油缸的推力F對轉動中心的力矩必須大于等于軸承摩擦力對轉動中心的力矩之和,才能使抓緊機構轉動實現彎耳動作,而軸承摩擦力矩很小,在此可忽略不計。即 Fa≧F2(Rmax+dmax) 由前計算知: F2=N2f2=5740.6=344.4kgf=3375.12N 而a=D/2=150/2=75(D為齒輪分度圓直徑,由后運動計算可知) Rm
44、ax+dmax=50+15=65(由設計參數得知) ∴F≧F2(Rmax+dmax)/a=3375.1265/75=2925.11N 同前,由公式計算得出轉動缸缸徑 D= 取ht=0.95,P=16Mpa 則轉動缸的缸徑: D=(42925.11/0.95163.14)1/2=15.66mm 按計算值增加10﹪,查《機械設計手冊》第四卷P17-257表17-6-2,取轉動缸缸徑 D=32mm 圖5—6 5.1.6 分析移位缸載荷并選定移動缸缸徑 移位缸承受的載荷主要是因切頭機構因自重在導柱導套處滑動軸承中產生的滑動摩擦載荷,而
45、切頭機構自重由估算知不大(不大于500㎏),因而產生的摩擦載荷很小。對于移動缸選擇缸徑來說,載荷不是主要因素,考慮到移動缸的行程較長(由后運動計算知行程為500㎜)因而缸徑如取的太小,雖然能滿足載荷要求,但活塞桿太小,壓桿穩(wěn)定性較差,查《機械設計手冊》第四卷P17-257表17-6-2,取移位缸缸徑: D=50mm 5.1.7 分析定位缸載荷并選定定位缸缸徑 定位缸承受的載荷主要是定位銷的重量,而定位銷直徑很小,長度也短,因而重量也輕。在此對載荷不作考慮??紤]到使定位機構結構緊湊,因而,查《機械設計手冊》第四卷P17-257表17-6-2,取抓緊缸缸徑: D=20mm 5.1.8分析
46、抽芯缸載荷并選定抽芯缸缸徑 工件在耳型彎曲成型后,抓緊塊松開,工件此時不受任何載荷。然后抽芯缸動作,將芯軸抽出,以便取出工件。因此抽芯缸載荷極小,僅為芯軸及接頭的自重。但考慮到活塞桿長期在芯軸及接頭自重作用下彎曲變形,因此缸徑在選擇時不宜太小,以免活塞桿太細。 查《機械設計手冊》第四卷P17-257表17-6-2,取抽芯缸的缸徑為: D=32mm 5.2 運動設計計算 根據設備總體結構及各機構具體工作要求,確定各油缸工作行程及各機構運動參數。 5.2.1 確定切頭刀具工作角度: 如果切頭刀具相對工件垂直安裝,對于機構總體受力效果是好的。但是由于抓緊機構要占據一定空間位置
47、,因而如刀具相對工件垂直工作時,必然會產生切頭機構與抓緊機構的相互干涉,因此,在參考同型設備后,確定切頭刀具的工作角度為a=30。 見圖5-7 圖5-7 5.2.2 確定齒輪齒條模數及齒輪齒數 按類比,取轉位機構: 齒輪齒條模數m=5,齒輪齒數z=30 齒輪分度圓直徑D=zm=530=150mm 5.2.3計算抓緊機構轉位角度 抓緊機構轉位過程如圖5-8。 w 圖5-8 當工件的彎耳直徑為最大fm
48、ax=100時,其需要的轉位角度最大由圖知wmax=360—120—amin 其中amin=arcos((50-1)/50)=arcos(49/50)=12.75 ∴wmax=360—120—amin=360—120—12.75=227.25 當工件彎耳直徑為最小wmin=25mm時,其需要的轉位角度最小。由圖示知: wmin=360—120amax 其中amax=arcos((12.5-1)/12.5)=arcos(11.5/12.5)=25.64 ∴fmin=360-120-25.64=214.36 5.2.4計算轉位缸行程并選定標準行程 由前取的齒輪齒條模數及齒輪齒數
49、和前計算出的最大轉位角度來計算齒條需要移動的長度(即為轉位缸的行程) 而齒條的移動長度應等于齒輪分度圓轉動最大圓周長,則齒輪分度圓最大轉動圓周長= (pDwmax)/360 =3.14150227.25/360 =297.32mm 園整取轉動缸最大移動行程Smax=300mm 查《機械設計手冊》第四卷P17-257表17-6-2,取轉動缸標準行程: S=320mm 5.2.5計算切頭缸工作行程并選定標準行程 當加
50、工板簧彎耳直徑為最大fmax=100mm,板料為最厚dmax=15mm時,刀具需要移動的位移即為切頭缸的最大工作行程。其最大工作行程參考圖5-9計算: 估計取工件切頭工作開始前,刀尖距工件的距離為50mm,工件切頭完畢后,刀尖距切頭完成點距離為10mm。 由圖知: 刀具最大工作行程: Smax=50+10+AB/cos30 其中: AB=ED+OD+OC =Rmax+dmax+Rmaxsin30 圖5-9
51、 AB =50+15+25 =90 ∴Smax=50+10+90/cos30 =60+101.01=161.01mm 查《機械設計手冊》第四卷P17-257表17-6-2,取切頭缸標準行程為: S=200mm 5.2.6分析壓緊缸工作行程并選定壓緊缸標準行程 由設計參數知:板簧最大卷耳直徑Dmax=100mm,最大板料厚度為dmax=15mm,因此加工工件最大輪廓直徑D’max=130mm,考慮到取卸工件的方便,壓緊缸行程應大于130mm。查《機械設計手冊》第四卷P17-257表17-6-2,取壓緊缸標準行程為:
52、 S=200mm 5.2.7選定抓緊缸標準行程 鑒于設備總體結構要求:抓緊機構的高度應盡量小,以縮小切頭機構的讓位行程,并抓緊動作對行程并無特殊要求。 查《機械設計手冊》第四卷P17-257表17-6-2,取抓緊缸的標準行程為: S=25mm 5.2.8選定切頭機構移動缸標準行程 因總體結構要求工件在彎耳轉位時,抓緊機構轉動的空間位置不會同切頭機構發(fā)生干涉,因而移動缸的行程取決于抓緊機構至運動中心的高度,從設計總圖上得抓緊機構自轉動中心高度H為480mm。 查《機械設計手冊》第四卷P17-257表17-6-2,取切頭機構移動缸標準行程: S=500mm 5.2.9計算切頭機
53、構擺動缸并選定標準行程 根據加工要求:工件在切頭完畢后。V形塊應離開芯軸,當工件最大彎耳直徑fmax=100mm時,即芯軸最大直徑fmax=100mm,按標準V形塊結構,V形塊完全離開工件的讓位高度查《機床夾具零件及部件》國標得Hmax=21.8mm,又芯軸直徑隨工件彎耳規(guī)格變化而變化,根據前面的設計參數知其變動范圍為Rmax-Rmin=100/2-25/2=37.5mm,因此V形塊總計需移動最大位移s’max=Hmax+37.5=21.8+37.5=59.3mm。 根據設計總圖得切頭機構位置尺寸見圖5-10。 圖5-10 由圖可見,擺動油缸的最大工作行程Smax
54、 Smax=S’max560/790=59.3560/790=42.04mm 查《機械設計手冊》第四卷P17-257表17-6-2,取擺動缸標準行程: S=50mm 5.2.10選定抽芯缸標準行程 從設計參數知,工件最大加工寬度bmax=100mm,因而芯軸工作寬度最大為100mm。再考慮到芯軸支承長度及與活塞桿接頭長度和方便地更換芯軸的空間位置,從總圖上確定抽芯缸的最大工作行程S’max=300mm。 查《機械設計手冊》第四卷P17-257表17-6-2,取抽芯缸標準行程: S=320mm 5.2.11選定定位缸標準行程 從設計參數知:工件最大板料厚度dmax=15mm,即定
55、位孔最大深度Hmax=15mm,因而定位缸行程應小于Hmax而大于Hmax/2。 查《機械設計手冊》第四卷P17-257表17-6-2,取定位缸標準行程: S=16mm 5.3 選定各工作油缸標準型號 根據前面計算分析已選定各工作油缸缸徑和行程,結合各工作油缸安裝形式查《機械設計手冊》選定各工作油缸標號見下表5-11。 表5-11 油缸 代號 油缸 名稱 缸徑 (D)mm 行程(s)mm 安裝型式 油缸的標準型號 R1 壓緊缸 32 200 頭部法蘭固定 GT32200.B7.1.9.00 R2 抓緊缸 32 25 頭部法蘭固定 G
56、T3225.B7.1.1.00 R3 切頭缸 110 200 頭部法蘭固定 GT100200.B7.6.5.00 R4 擺動缸 32 50 尾部耳環(huán)懸掛 S3250.B5.1.3.00 R5 移動缸 50 500 軸向底部安裝 G50500.B6.3.10.00 R6 抽芯缸 32 320 頭部法蘭固定 GT32320.B7.1.11.00 R7 轉動缸 32 320 頭部法蘭固定 GT32320.B7.1.11.00 R8 定位缸 20 16 頭部法蘭固定 按類比設計 第六章 部分設計問題說明 6.1機架、
57、切頭架及抓緊架結構及材料 本設計對機架、切頭架及抓緊架等大小結構幾乎全部采用焊接結構。材料選用碳素鋼板,保證良好的焊接性,在結構設計中采用各種措施保證結構的剛性。詳見總圖及部件零件圖。這樣既能保證使用要求,同時又可以保證良好的經濟性。 6.2設備的潤滑措施 本設計需要重點保證切頭機構導柱導套滑動軸承,切頭機構同機體聯接銷軸滑動軸承及抓緊機構滾動支承軸承的潤滑。 對于擺動缸活塞桿與切頭機構聯接銷軸,壓緊機構單向導柱及芯軸與滑動軸承等次要,不方便部位采用人工每班定期注油潤滑。 對于滾動軸承的潤滑采用脂潤滑,再定期更換潤滑脂,簡單、方便、可靠。 對于切頭機構導柱導套滑動軸承及切頭機構與機
58、體聯接銷軸滑動軸承的潤滑應采取各個獨立潤滑,但考慮到結構的獨特性,設備的經濟性和潤滑的簡單、方便,因此在本設計中采用一個針閥式注油油杯對兩大潤滑部分同時潤滑。 其結構見圖6-1。 圖6-1 另外,轉位彎耳機構中,齒條在本設計中采用立式布置,這樣雖然縮小了結構空間,使總體結構變得緊湊,但對齒輪齒條的潤滑不利,如果對齒輪齒條的潤滑采用油潤滑,比如會出現漏油等不易處理的問題。鑒于本機構中齒輪的餓轉速很低(約8r/min,由轉位工作時間計算知),而載荷并不高(由前計算知F=2925.11N),因此查《機械課程設計手冊》,選普通潤滑脂ZG-2對齒輪齒條潤滑。 6.3芯
59、軸的冷卻措施 設計參數規(guī)定,板簧在900℃高溫下進行切頭卷耳,從工件過程看,芯軸與工件在高溫下間歇地接觸,其接觸時間為52s(從控制過程定出),間歇時間僅為8s,芯軸在接觸時間里從工件中大量傳導熱量,影起芯軸溫度升高,而間歇時間很短,散熱極小,芯軸長期循環(huán)工作,如無冷卻處理,必然出現芯 軸長期在高溫狀態(tài)下工作,這對芯軸強度剛性及壽命都是極為不利的。因而必須采取措施對芯軸實施冷卻。冷卻的方案有以下兩種,見 圖6-2。 方案A 方案B 圖6-2 方案A的措施是在
60、芯軸中加工一通孔,冷卻水從孔的一端進,從另一端出來。這樣的結構對冷卻效果而言是最佳的。但同樣存在無法避免的弊端:在芯軸抽芯時,會有余水泄漏出來,長期循環(huán)工作,必然會污染生產場地,同時對設備有一定腐蝕。 方案B的措施是在芯軸中加工一盲孔,在盲孔中安裝一通管,冷卻水從管子進入后冷卻芯軸內部再流出,此方案冷卻效果不及方案1,但解決了冷卻水泄漏的弊端。 考慮到保護生產場地的清潔衛(wèi)生,以及對設備的防腐因素,在本設計中選擇方案B來解決芯軸的冷卻問題。 結論 本設計從汽車彈簧單工位液壓彎耳機的基本原理出發(fā),經過以上的分析、設計、計算,得出了能達到要求的設備。本設備實現了一機多能,將切頭和彎
61、耳功能揉合到了一個設備中并且無須整型,減少了生產設備,縮小了生產面積,提高了生產效率,降低了工人勞動強度和板簧生產成本。其次,設備采用了芯軸結構,在切頭時,對芯軸加了V形支承塊,使工藝的實施變得簡單。同時,有了切頭機構,縮短了工作節(jié)拍,單件生產時間變短,使工件在加工過程中溫度變化范圍減小,內部組織變動不大,不易產生突出的加工應力及變形。因而能較好地保證加工質量,不易產生廢品。另外,該設備采用液壓傳動,便于實現PC自動控制,使控制的實現變得簡單、易行。 致 謝 這篇論文的完成,是我精心準備后的結晶,也離不開周圍人的支持。在整個畢業(yè)設計中,我遇到了許多困難,也得到了各位老師的幫助。在此
62、我要特別感謝導師于春海老師的細心指導,他是一位非常負責且知識淵博的老師,在論文選題資料整理、文章結構等方面都給予了許多方向性的建議。在此論文完成之際,我要特別感謝導師的教誨和啟迪。同時,我還要感謝在大學四年里教育和培養(yǎng)我的老師們,以及為這篇論文提出過中肯意見的許多朋友和同學,最后,我 要向所有辛勤勞動的老師說聲:謝謝你們! 參 考 文 獻 ⑴ 吳宗澤、羅圣國.機械設計課程設計手冊, 第二版.高等教育出版社.1999 ⑵ 陳炎嗣、郭景儀.沖壓模具設計與制造技術, 第二版.高等教育出版社.1999 ⑶ 楊可楨、程光蘊.機械設計基礎.高等教育出版社.1981
63、⑷ 楊興駿.互換性與與技術測量. 中國計量出版社.2000 ⑸ 駱志斌.金屬工藝學. 上??茖W技術出版社.1999 ⑹ 季 云.機械制造工藝及設備設計指導手冊. 機械工業(yè)出版社. 1997 ⑺ 王啟平.機械制造工藝學.哈爾濱教育出版社. 1999, ⑻ 單輝祖.材料力學. 高等教育出版社. 1999 ⑺ 陳炎嗣、郭景儀.沖壓模具設計與制造技術, 第二版.高等教育出版社.1999 ⑼ 成大先.機械設計手冊, 第四版(第1卷).化學工業(yè)出版社. 2000 ⑽成大先.機械設計手冊, 第四版(第2卷).化學工業(yè)出版社. 2000 ⑾ 成大先.機械設計手冊, 第四版(第3卷).化學工業(yè)出版社.2000 ⑿ 成大先.機械設計手冊,第四版(第4卷).化學工業(yè)出版社. 2000 第 40 頁
- 溫馨提示:
1: 本站所有資源如無特殊說明,都需要本地電腦安裝OFFICE2007和PDF閱讀器。圖紙軟件為CAD,CAXA,PROE,UG,SolidWorks等.壓縮文件請下載最新的WinRAR軟件解壓。
2: 本站的文檔不包含任何第三方提供的附件圖紙等,如果需要附件,請聯系上傳者。文件的所有權益歸上傳用戶所有。
3.本站RAR壓縮包中若帶圖紙,網頁內容里面會有圖紙預覽,若沒有圖紙預覽就沒有圖紙。
4. 未經權益所有人同意不得將文件中的內容挪作商業(yè)或盈利用途。
5. 裝配圖網僅提供信息存儲空間,僅對用戶上傳內容的表現方式做保護處理,對用戶上傳分享的文檔內容本身不做任何修改或編輯,并不能對任何下載內容負責。
6. 下載文件中如有侵權或不適當內容,請與我們聯系,我們立即糾正。
7. 本站不保證下載資源的準確性、安全性和完整性, 同時也不承擔用戶因使用這些下載資源對自己和他人造成任何形式的傷害或損失。