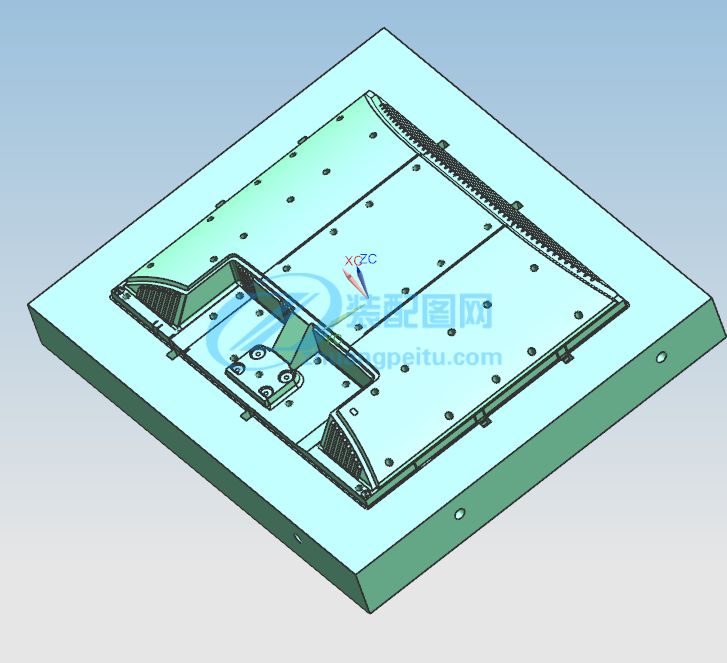
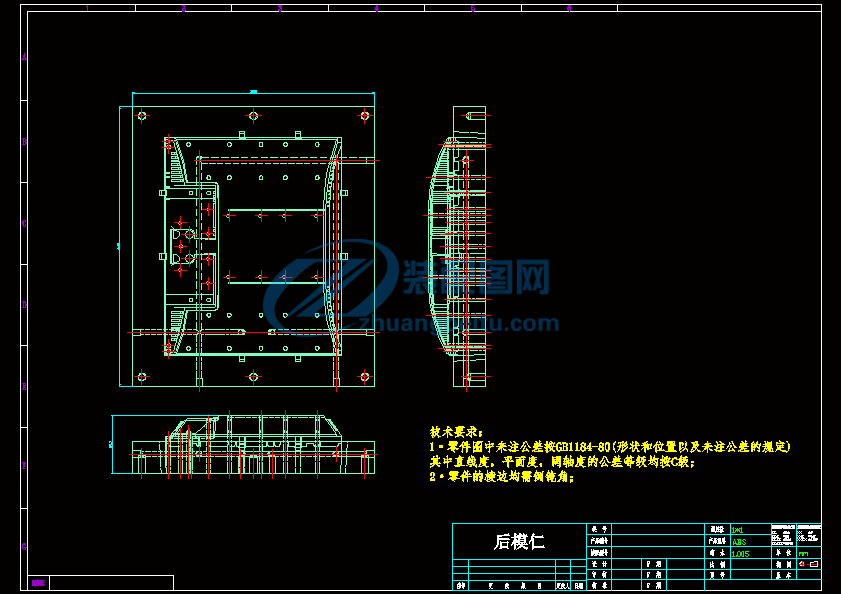
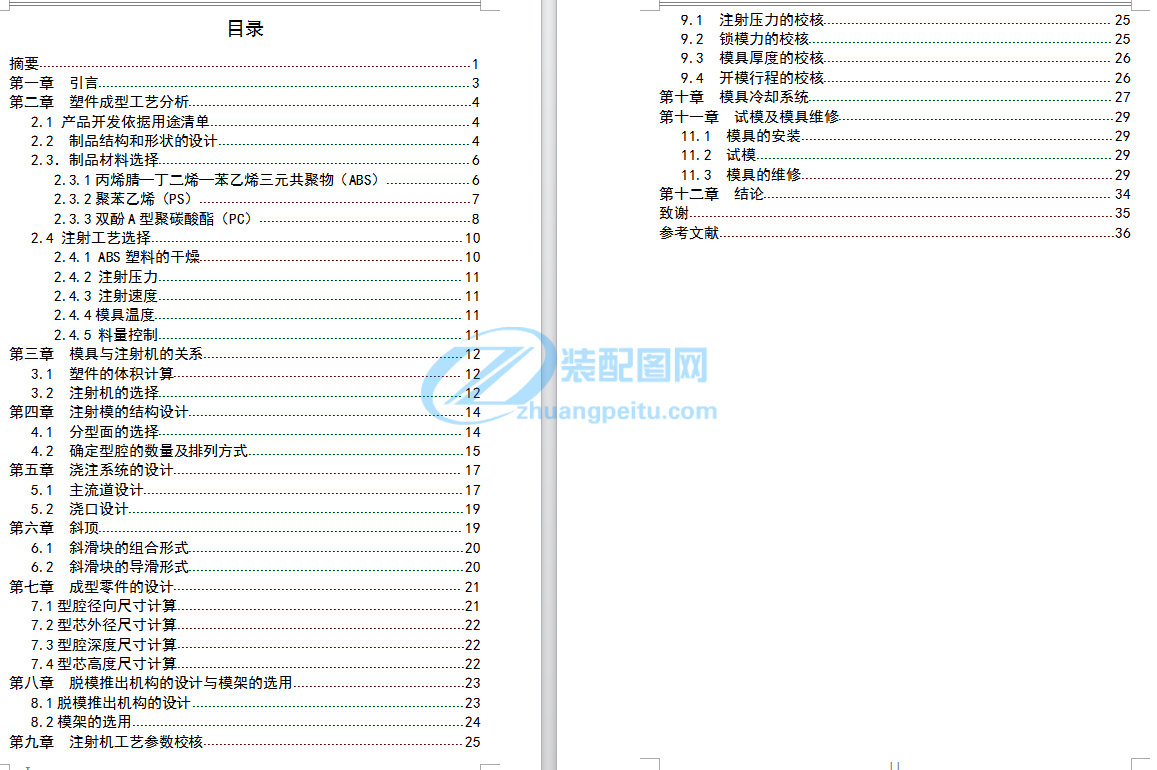
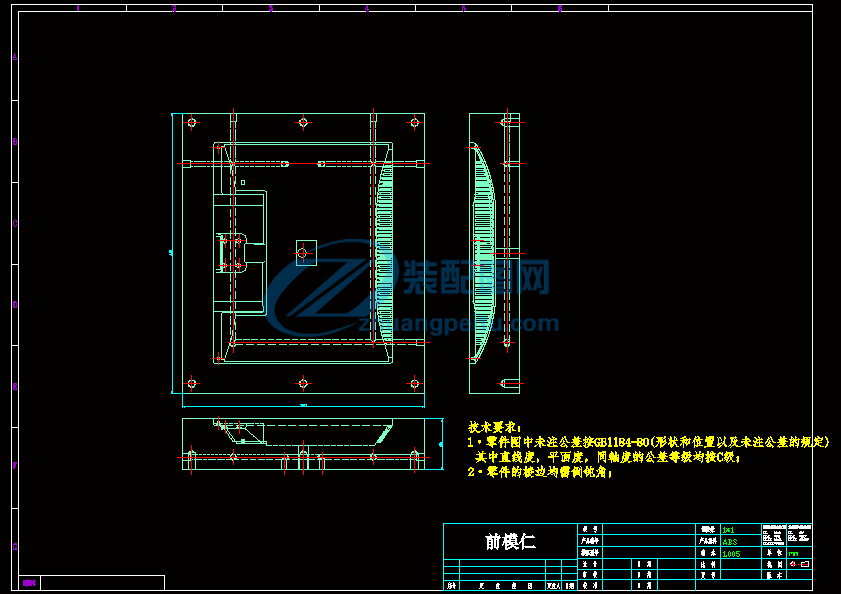
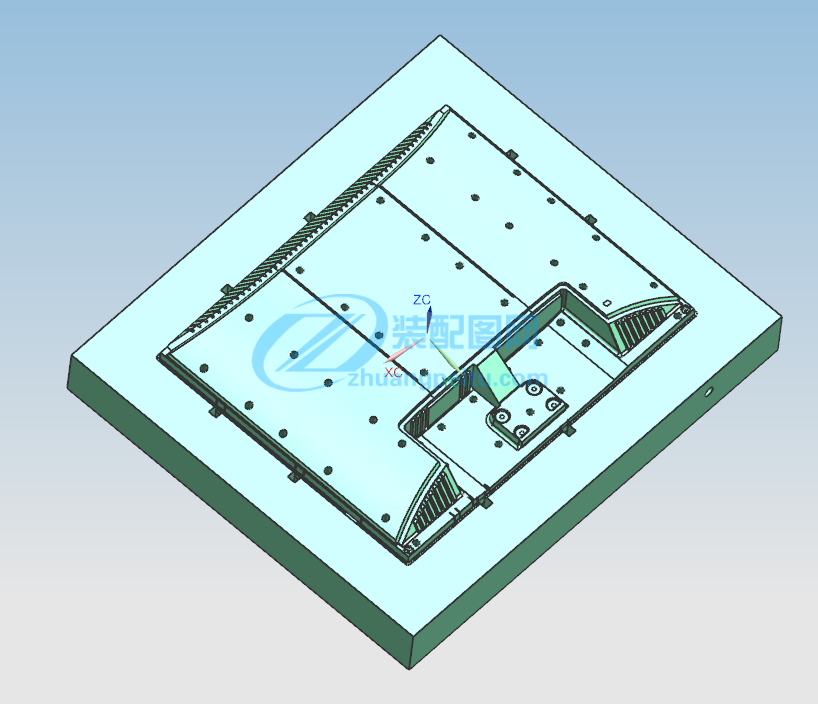
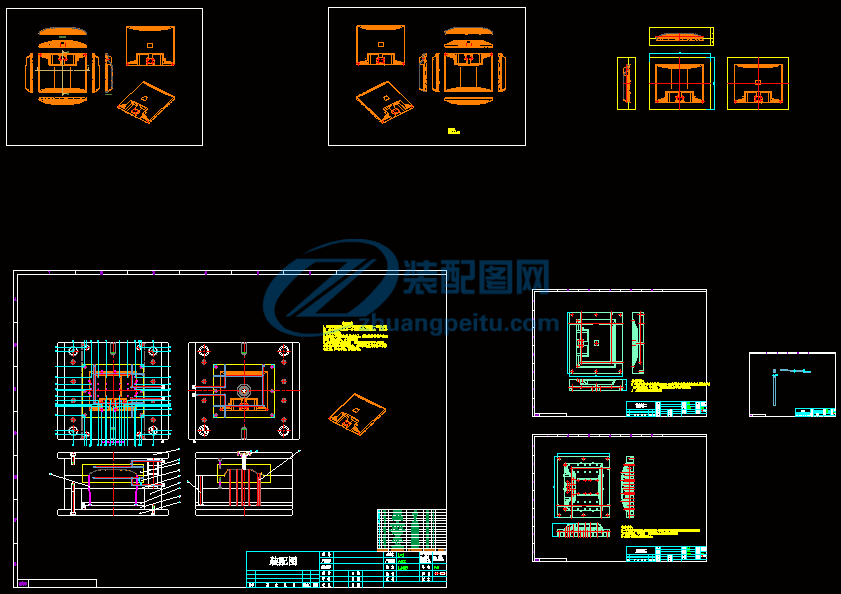
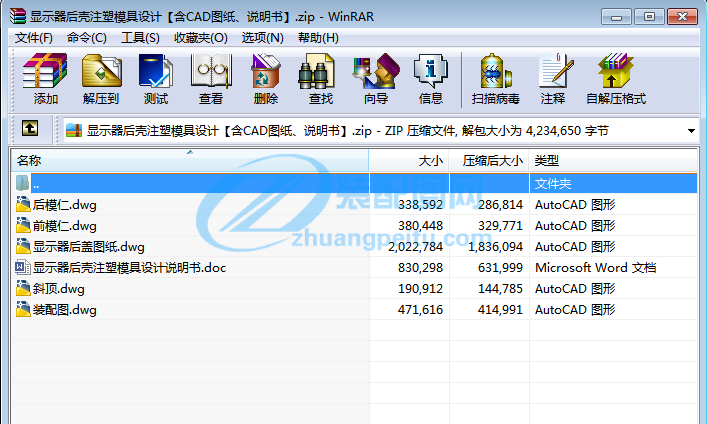
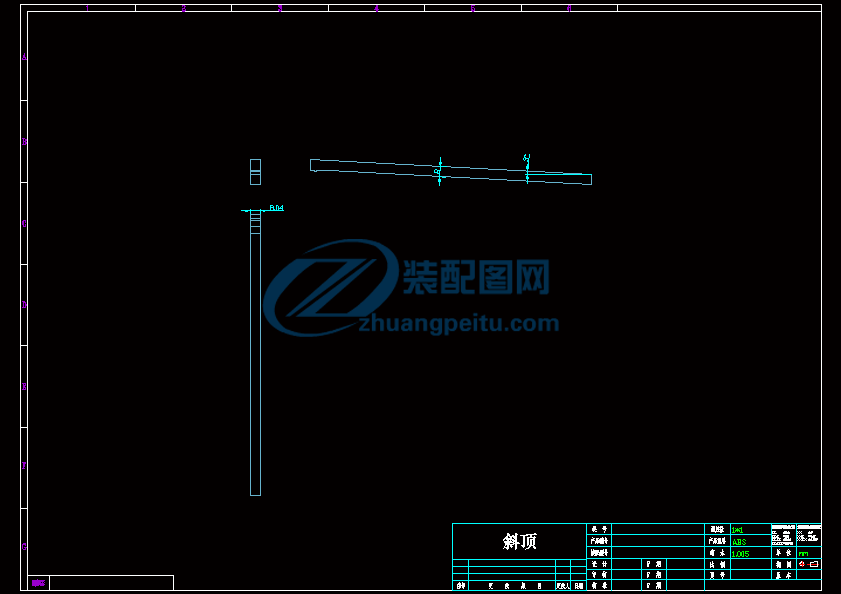
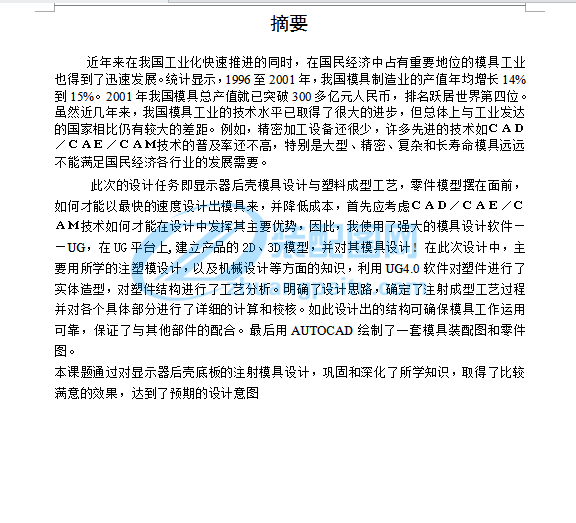
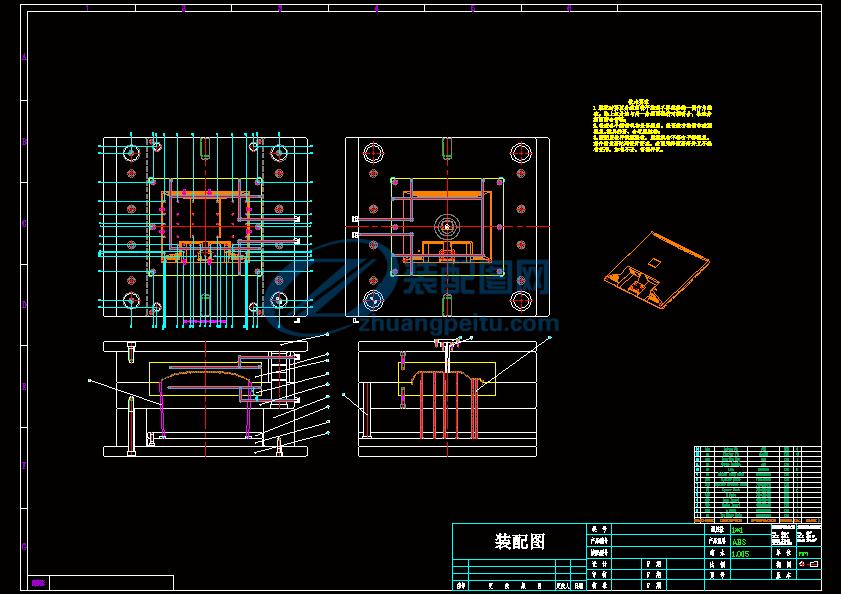
畢 業(yè) 設(shè) 計 說 明 書題目液晶顯示器后殼注塑模具設(shè)計學 生 姓 名專 業(yè) 名 稱 模 具 設(shè) 計 與 制 造指 導 教 師年五月二四日學 號: 目錄畢業(yè)設(shè)計液晶顯示器后殼注塑模具設(shè)計指導教師: 專業(yè)名稱: 模具設(shè)計與制造 論文提交日期: 論文答辯日期: 論文評閱人: 目錄目錄摘要 1第一章 引言 3第二章 塑件成型工藝分析 42.1 產(chǎn)品開發(fā)依據(jù)用途清單 .42.2 制品結(jié)構(gòu)和形狀的設(shè)計 42.3.制品材料選擇 62.3.1 丙烯腈—丁二烯— 苯乙烯三元共聚物(ABS) .62.3.2 聚苯乙烯(PS) 72.3.3 雙酚 A 型聚碳酸酯(PC) 82.4 注射工藝選擇 102.4.1 ABS 塑料的干燥 .102.4.2 注射壓力 .112.4.3 注射速度 .112.4.4 模具溫度 .112.4.5 料量控制 .11第三章 模具與注射機的關(guān)系 .123.1 塑件的體積計算 .123.2 注射機的選擇 .12第四章 注射模的結(jié)構(gòu)設(shè)計 .144.1 分型面的選擇 .144.2 確定型腔的數(shù)量及排列方式 .15第五章 澆注系統(tǒng)的設(shè)計 .175.1 主流道設(shè)計 .175.2 澆口設(shè)計 .19第六章 斜頂 .196.1 斜滑塊的組合形式 .206.2 斜滑塊的導滑形式 .20第七章 成型零 件的設(shè)計 .217.1 型腔徑向尺寸計算 217.2 型芯外徑尺寸計算 227.3 型腔深度尺寸計算 227.4 型芯高度尺寸計算 22第八章 脫模推出機構(gòu)的設(shè)計與模架的選用 .238.1 脫模推出機構(gòu)的設(shè)計 238.2 模架的選用 24第九章 注射機工藝參數(shù)校核 .25目錄9.1 注射壓力的校核 .259.2 鎖模力的校核 .259.3 模具厚度的校核 .269.4 開模行程的校核 .26第十章 模具冷卻系統(tǒng) .27第十一章 試模及模具維修 .2911.1 模具的安裝 2911.2 試模 2911.3 模具的維修 29第十二章 結(jié)論 .34致謝 .35參考文獻 .36摘要0摘要近年來在我國工業(yè)化快速推進的同時,在國民經(jīng)濟中占有重要地位的模具工業(yè)也得到了迅速發(fā)展。統(tǒng)計顯示,1996 至 2001 年,我國模具制造業(yè)的產(chǎn)值年均增長14%到 15%。 2001 年我國模具總產(chǎn)值就已突破 300 多億元人民幣,排名躍居世界第四位。雖然近幾年來,我國模具工業(yè)的技術(shù)水平已取得了很大的進步,但總體上與工業(yè)發(fā)達的國家相比仍有較大的差距。例如,精密加工設(shè)備還很少,許多先進的技術(shù)如CAD/CAE/CAM技術(shù)的普及率還不高,特別是大型、精密、復雜和長壽命模具遠遠不能滿足國民經(jīng)濟各行業(yè)的發(fā)展需要。此次的設(shè)計任務(wù)即顯示器后殼模具設(shè)計與塑料成型工藝,零件模型擺在面前,如何才能以最快的速度設(shè)計出模具來,并降低成本,首先應(yīng)考慮CAD/CAE/CAM技術(shù)如何才能在設(shè)計中發(fā)揮其主要優(yōu)勢,因此,我使用了強大的模具設(shè)計軟件——UG,在 UG 平臺上,建立產(chǎn)品的 2D、3D 模型,并對其模具設(shè)計!在此次設(shè)計中,主要用所學的注塑模設(shè)計,以及機械設(shè)計等方面的知識,利用 UG4.0 軟件對塑件進行了實體造型,對塑件結(jié)構(gòu)進行了工藝分析。明確了設(shè)計思路,確定了注射成型工藝過程并對各個具體部分進行了詳細的計算和校核。如此設(shè)計出的結(jié)構(gòu)可確保模具工作運用可靠,保證了與其他部件的配合。最后用AUTOCAD 繪制了一套模具裝配圖和零件圖。 本課題通過對顯示器后殼底板的注射模具設(shè)計,鞏固和深化了所學知識,取得了比較滿意的效果,達到了預期的設(shè)計意圖 目錄In recent years the rapid advances in our country industrialization in the national economy, meanwhile, occupies an important place in the mold industry also have developed rapidly. Statistics show that in 1996 and 2001, the output value and mould industry average annual growth 14% to 15%. In 2001, China had breakthrough mold output more than 300 million yuan RMB, the ranking destinations in the world in terms of the fourth. Although in recent years, our country of mold industry technical level has made great progress, but in general and industrial developed countries still have larger gap. For example, precision machining equipment is very few, many advanced technologies such as CAD/CAE/CAM technology popularization rate is not high, especially large, precision, complex and long life mould cant satisfy the development needs of national economic sectors.This design task of display shell mould design and after plastic molding process, parts ahead, how can model with the quickest speed design out of the mold, and reduce the cost, you should consider CAD/CAE/CAM technology in design how can play its main advantage, therefore, I use a powerful mold design software - UG, in UG platform, build the product's 2D, 3D model, and the mould design! In this design, the main injection molding design with what they have learned and mechanical design, use the knowledge of the respect such as UG4.0 software to the plastic parts for solid modeling, structure of the plastic parts the technological analysis. Clear the design ideas, determine the injection molding process and to each particular part of the detailed calculated and checked. So designed to ensure the structure, reliable mould work with other components ensures the cooperation. Finally using AUTOCAD painted a set of mold assembly drawing and detail drawings.This topic through the shell of the display floor after injection mould design, strengthening and deepening the knowledge learnt, achieved satisfactory effect, achieve the expected design intent第一章節(jié) 引言2第一章 引言畢業(yè)設(shè)計(論文)是大學生在學校學習的最后一個重要環(huán)節(jié),既是對學生學習、實踐與研究的全面總結(jié),又是對學生素質(zhì)與能力的一次綜合檢驗,還是學生畢業(yè)資格與學位資格認證的重要依據(jù)。其目的有以下幾方面:(1)培養(yǎng)學生綜合運用所學的基礎(chǔ)理論、專業(yè)知識和基本技能進行分析與解決實際問題的能力,培養(yǎng)學生的創(chuàng)新精神。(2)培養(yǎng)學生收集、整理和分析各種資料的能力,全面提高學生分析和解決實際問題的能力。(3)提高學生設(shè)計、計算和繪圖的能力。提高學生實驗研究和數(shù)據(jù)處理的能力。(4)全面提高學生綜合分析、總結(jié)提高、編制設(shè)計說明書及撰寫科技論文的能力。(5)提高學生外語、計算機應(yīng)用能力。本次設(shè)計的題目是“顯示器后殼注塑模具設(shè)計” ,其內(nèi)容為:(1)學會觀察制品,判斷制件是否符合塑料件的成形條件(比如注意拔模斜度) ,還特別要留意制件影響開模的細部特征;(2)研究制件的排位方式和進澆方式,畫草圖確定模具的整體結(jié)構(gòu),保證結(jié)構(gòu)能循環(huán)工作,穩(wěn)定可靠;(3)在深入研究制件的基礎(chǔ)上確定開模的分型面,以及確定各鑲塊或滑塊、斜頂?shù)姆指蠲娼M或體積塊;(4)對該樣品進行測繪,并在測繪的基礎(chǔ)上對該產(chǎn)品進行模具結(jié)構(gòu)設(shè)計和成型工藝分析(5)用 UG4.0 按照上步的結(jié)果把模具核心的部分:凸凹模分割出來,接著分出各鑲塊、滑塊和斜頂;(6)進一步完善凸凹模和各細微結(jié)構(gòu);(7)調(diào)用 EMX 中適合的模架完成模架設(shè)計;(8)在 UG4.0 中出模具轉(zhuǎn)配圖和模仁圖,以及對模架板塊需要再加工的各組件出工程圖;(9)把 UG4.0 工程圖轉(zhuǎn)入 AUTOCAD 中進行完善。目錄第二章 塑件成型工藝分析2.1 產(chǎn)品開發(fā)依據(jù)用途清單最大幾何尺寸:346.7X281.4X51.2mm環(huán)境:室內(nèi),使用溫度范圍 0℃~60℃無化學品接觸抗沖擊要求:限定量從 2m 高度,0℃下摔下外殼不出現(xiàn)裂縫或者開裂特征剛性要求:在 4Kg 負荷下無變形電氣性能:電絕緣性好外觀要求:部件美觀,外部光潔性一般使用壽命:7 年以上根據(jù)上述使用要求可歸納產(chǎn)品設(shè)計要求為制品材料需要具有一定的抗沖擊性并且由于是電子產(chǎn)品的外殼要有良好的電絕緣性,隨著數(shù)碼產(chǎn)品的大量普及價格也不斷下跌要求生產(chǎn)自動化程度高,成型周期短生產(chǎn)自動化程度高、成型周期短,有較好電絕緣性。2.2 制品結(jié)構(gòu)和形狀的設(shè)計用 UG4.0 軟件進行顯示器后殼的三維建模,三維實體模型更加直觀的表現(xiàn)了產(chǎn)品造型,可以從各個角度對模型進行觀察,軟件可以測量并且還可以根據(jù)三維模型數(shù)據(jù)使用 UG4.0 的 CAE 分析模塊 --塑性顧問進行熔體的充模仿真,可以驗證模具結(jié)構(gòu)的正確性,制品如圖 2.2第二章 塑件成型工藝分析4圖 2.2: 顯示器后殼(用 UG4.0 設(shè)計完成的制品圖)畢業(yè)設(shè)計說明書52.3.制品材料選擇通用塑料如聚丙烯 PP,聚乙烯 PE,聚氯乙烯 PVC 具有應(yīng)用范圍廣、加工性能良好,價格低廉的優(yōu)點,但由于其力學性能較差且成型收縮率較大不易成型尺寸穩(wěn)定的制品故不選用,以下拿三種常用典型材料比較選取。2.3.1丙烯腈—丁二烯—苯乙烯三元共聚物(ABS)ABS 外觀上是淡黃色非晶態(tài)樹脂,不透明,密度與聚苯乙烯基本相同。ABS 具有良好的綜合物理力學性能,耐熱,耐腐,耐油,耐磨、尺寸穩(wěn)定,加工性能優(yōu)良,它具有三種單體所賦予的優(yōu)點。其中丙烯腈賦予材料良好的剛性、硬度、耐油耐腐、良好的著色性和電鍍性;丁二烯賦予材料良好的韌性、耐寒性;苯乙烯賦予材料剛性、硬度、光澤性和良好的加工流動性。改變?nèi)M分的比例,可以調(diào)節(jié)材料性能。ABS 為無定形聚合物,無明顯熔點,熔融流動溫度不太高,隨所含三種單體比例不同,在 160~190℃范圍即具有充分的流動性,且熱穩(wěn)定性較好,在約高于 285℃時才出現(xiàn)分解現(xiàn)象,因此加工溫度范圍較寬。ABS 熔體具有明顯的非牛頓性,提高成型壓力可以使熔體粘度明顯減小,粘度隨溫度升高也會明顯下降。ABS 吸濕性稍大于聚苯乙烯,吸水率約在 0.2%~0.45%之間,但由于熔體粘度不太高,故對于要求不高的制品,可以不經(jīng)干燥,但干燥可使制品具有更好的表面光澤并可改善內(nèi)在質(zhì)量。在80~90℃下干燥 2~3h,可以滿足各種成型要求。 ABS 具有較小的成型收縮率,收縮率變化最大范圍約為 0.3%~0.8%,在多數(shù)情況下,其變化小于該范圍。注塑是 ABS 塑料最重要的成型方法,可以采用柱塞式注塑機,但更長采用螺桿式注塑機,后者更適于形狀復雜制品、大型制品成型 [5]。畢業(yè)設(shè)計說明書62.3.2聚苯乙烯(PS)聚苯乙烯是無色無臭的透明剛硬固體,制品擲地時有金屬般響鳴。聚苯乙烯透光率不低于 80%,霧度約為 3%,折射率較大,在 1.59~1.60 之間,具有特殊光亮性,但儲存時易泛黃。泛黃原因之一是單體純度不夠,特別是在含有微量元素時;二是聚合物在空氣中緩慢老化引起發(fā)黃。聚苯乙烯較輕,密度在 1.04~1.065 之間。①力學性能 聚苯乙烯在熱塑性塑料中屬于典型的硬而脆塑料,拉伸、彎曲等常規(guī)力學性能皆高于聚烯烴,拉伸時無屈服現(xiàn)象。②熱學性能 聚苯乙烯分子鏈雖是剛性鏈,但由于是無定形結(jié)構(gòu),超過玻璃化溫度即開始軟化,軟化點僅 95℃左右,許多力學性能都受到溫度升高的明顯影響。最高連續(xù)使用溫度僅 60~80℃。120℃開始成為熔體,180℃后開始具有流動性,其熱穩(wěn)定性較好,超過 300℃才開始分解,因此聚苯乙烯具有較高的成型加工區(qū)間。③電性能 聚苯乙烯是非極性聚合物,具有頗為優(yōu)異的介電、電絕緣性能,由于吸濕性很小,電性能也不受環(huán)境濕度改變的影響。加工工藝性 吸濕性很小,加工前一般不需要專門的干燥工序成型溫度范圍較寬收縮率及其變化范圍都很小,一般在 0.2%~0.8%有利于成型出尺寸精度較高和尺寸較穩(wěn)定的制品 [5]聚苯乙烯制品容易產(chǎn)生內(nèi)應(yīng)力,并且在空氣中會緩慢老化引起發(fā)黃很顯然不適合選用目錄2.3.3雙酚A型聚碳酸酯(PC)雙酚 A 型聚碳酸酯是無色或者微黃色透明的剛硬、堅韌固體。①力學性能雙酚 A 型聚碳酸酯是典型的硬而韌聚合物,具有良好的綜合力學性能。拉伸、壓縮、彎曲強度均相當于聚酰胺 6、聚酰胺 66,沖擊強度高于所有脂肪族聚酰胺和大多數(shù)工程塑料,抗蠕變性也明顯優(yōu)于聚酰胺、聚甲醛。力學性能方面缺點是耐疲勞性較差,缺口敏感性較明顯②熱性能有良好的耐熱性,玻璃化溫度較高,高于所有的脂肪族聚酰胺,熔融溫度略高于聚酰胺 6 但低于聚酰胺 66,熱變形溫度和最高連續(xù)使用溫度均高于絕大多數(shù)脂肪族聚酰胺,也高于幾乎所有的熱塑性通用塑料。在工程塑料中,他的耐熱性優(yōu)于聚甲醛、脂肪族聚酰胺和 PBT,與 PET 相當,但遜于其他工程塑料。聚碳酸酯具有良好的耐熱性,脆化溫度為-100℃③電性能雙酚 A 型聚碳酸酯是弱極性聚合物,極性的存在對電性能有一定不利影響,在標準條件下電性能雖不如聚烯烴、聚苯乙烯等,但也不失為是電性能較優(yōu)的絕緣材料,特別是因其耐熱性優(yōu)于聚烯烴,可在較寬溫度范圍保持良好的電性能。由于吸濕性較小,環(huán)境溫度對電性能無明顯影響。④其他性能在干燥的氣候條件下物理力學性能基本不變,但在潮濕環(huán)境及強烈日照條件下,會產(chǎn)生表面裂紋并發(fā)暗,在火焰中可緩慢燃燒,離火源后可自熄 [5]。PC 剪切黏度高,充模阻力大,并且由于其在力學性能方面的缺點也不選用。畢業(yè)設(shè)計說明書8表 2.1: 三種材料性能參數(shù)表ABS PS PC密 度 1.05 1.04~1.06 1.18~1.20收 縮 率 0.3~0.8 0.2~0.8 0.5~0.7熔 點 130~160 131~165 220~240熱變形溫度(45N/cm2)65~98 65~90 132~138模具溫度 60~80 40~60 85~120噴嘴溫度 180~190 160~170 250~300中段溫度 180~230 170~190 270~320后段溫度 150~170 140~160 250~270注射壓力 60~100 60~100 50~110塑化形式 螺桿式柱塞式 螺桿式柱塞式 螺桿式柱塞式拉伸強度 33~49 35~63 60~66拉伸彈性模量 1.8 2.8~3.5 2.3彎曲強度 80 61~98 105~113彎曲彈性模量 1.4 - 1.54壓縮強度 18~39 80~112 85缺口沖擊強度 11~20 0.25~0.40 不斷硬 度 R62~86 洛氏 M65~80 11.7HB體積電阻率 1016 1017~1019 1015介電常數(shù) 60Hz2.4~5.0 106 Hz≥2.7 60Hz3.0擊穿電壓 - 19~27 20~30外 觀 淺象牙色或白色不透明無色透明、摔打音清脆透明微黃特 點耐熱、表面硬度高、,尺寸穩(wěn)定、耐化學及電性能好,易成型加工,可鍍鉻耐水、耐化學品、絕緣性好、不耐沖擊不耐溫透明度高、硬而韌、高抗沖、尺寸穩(wěn)定性優(yōu)電絕緣性和耐熱性好、耐開裂耐藥品性差材料最終選定為ABS,其綜合性能優(yōu)異,具有較高的力學性能,流動性好,易于成型;成型收縮率小,理論計算收縮率為0.5% ;溢料值為0.04 mm;比熱容較低,在模具中凝固較快,模塑周期短。制件尺寸穩(wěn)定,表面光亮。目錄2.4 注射工藝選擇2.4.1 ABS塑料的干燥ABS塑料的吸濕性和對水分的敏感性較大,在加工前進行充分的干燥和預熱,不單能消除水汽造成的制件表面煙花狀泡帶、銀絲,而且還有助于塑料的塑化,減少制件表面色斑和云紋。ABS原料需要控制水分在0.3%以下 [5]。注塑前的干燥條件是:干冬季節(jié)在75~80℃以下,干燥2~3h,夏季雨水天在80~90℃下,干燥4~8h,干燥達8~16h可避免因微量水汽的存在導致制件表面霧斑。在此,由于顯示器后殼外殼屬批量件要求自動化程度高實現(xiàn)連續(xù)化生產(chǎn)選用烘干料斗并裝備熱風料斗干燥器,以免干燥好的ABS在料斗中再度吸潮 [。表2.4: ABS工藝參數(shù)表工藝參數(shù) 通用型 ABS料桶后部溫度 180~200料桶中部溫度 210~230料桶前部溫度 200~210噴嘴溫度/℃ 180~190模具溫度/℃ 50~70ABS塑料非牛頓性較強,在熔化過程溫度升高時,其熔融降低很小,但一旦達到塑化溫度(適宜加工的溫度范圍,如220~250℃),如果繼續(xù)盲目升溫,必將導致耐熱性不太高的ABS的熱降解反而使熔融粘度增大,注塑更困難,制件的機械性能也下降。畢業(yè)設(shè)計說明書102.4.2 注射壓力ABS熔融的粘度比聚苯乙烯或改性聚苯乙烯高,在注射時要采用較高的注射壓力。但并非所有ABS制件都要施用高壓,考慮到本制件小型、構(gòu)造不算非常復雜、厚度中等可以用較低的注射壓力。注制過程中,澆口封閉瞬間型腔內(nèi)的壓力大小決定了制件的表面質(zhì)量及銀絲狀缺陷的程度。壓力過小,塑料收縮大,與型腔表面脫離接觸的機會大,制件表面容易霧化。壓力過大,塑料與型腔表面摩擦作用強烈,容易造成粘模。2.4.3 注射速度ABS塑料采用中等注射速度效果較好。當注射速度過快時,塑料易燒焦或分解析出氣化物,從而在制件上出現(xiàn)熔接痕、光澤差及澆口附近塑料發(fā)紅等缺陷。2.4.4模具溫度ABS的成型溫度相對較高,模具溫度也相對較高。一般調(diào)節(jié)模溫為75~85%,當生產(chǎn)具有較大投影面積制件時,定模溫度要求70~80℃,動模溫度要求50~60℃。2.4.5 料量控制注塑機注塑ABS塑料時,其每次注射量僅達標準注射量的75%。為了提高制件質(zhì)量及尺寸穩(wěn)定,表面光澤、色調(diào)的均勻,注射量選為標定注射量的50%。通常要確保注塑機生產(chǎn)條件及參數(shù)有一個很寬的范圍,使大多數(shù)的產(chǎn)品和生產(chǎn)能力要求包含于這范圍內(nèi),并且在調(diào)整確定這范圍的過程時盡量按常規(guī)的工藝流程,這種生產(chǎn)條件范圍愈大,生產(chǎn)過程愈穩(wěn)定,使注塑產(chǎn)品愈不容易受到生產(chǎn)條件的改變而產(chǎn)生明顯的質(zhì)量降低。目錄第三章 模具與注射機的關(guān)系模具型腔能否充滿與注射機允許的最大注射量密切相關(guān),設(shè)計模具時,應(yīng)保證注射模內(nèi)所需熔體總量在注射機實際的最大注射的范圍內(nèi)。3.1 塑件的體積計算由于塑件上存在一些曲面,形狀復雜,所以只能近似的計算其體積。在UG4.0ngineer 軟件上可算出塑件的總體積V=287893mm 33.2 注射機的選擇塑件的體積應(yīng)該小于或者等于注射機的注射量。其關(guān)系式為:V 件≤0.8V 注V 注——注射機的注射量所以:V 注≥V 件÷0.8=359866mm3=359.866cm3由于模具是一模一穴,所以模具塑件的總體積 V 總=359.866cm3估算澆注系統(tǒng)的凝料體積,由于采用的是直接澆口V 凝料=10 cm3所以估算的總體積為 V=359.866+10=369.866cm3由《塑料模具設(shè)計手冊》表 2-40 熱塑性塑料注射機型號與主要技術(shù)規(guī)格中,根據(jù)以上所得出的體積結(jié)果,初步選 HTF650X2 注射機。其主要技術(shù)規(guī)格如表 5。 畢業(yè)設(shè)計說明書12表 5 XS-ZY—500(立式)注射機主要技術(shù)規(guī)格螺桿直徑(mm) Ф65 鎖模力(kN) 650T注射容量(cm 3) 600 最大注射面積(cm 2)1000注射壓力(MPa) 145 模板行程(mm) 120最大 450 球半徑 15 模具厚度(mm) 最小 300噴嘴(mm) 孔直徑 Ф4.5定位孔直徑(mm) Ф100 0+0.06 中心孔徑(mm) Ф30第三章 模具與注射機的關(guān)系13第四章 注射模的結(jié)構(gòu)設(shè)計注射模的結(jié)構(gòu)設(shè)計包括:分型面的選擇、模具型腔數(shù)目的確定及型腔排列方式和冷卻水道布局以及澆口位置的設(shè)置、模具工件零件的結(jié)構(gòu)設(shè)計、頂出系統(tǒng)設(shè)計等內(nèi)容。4.1 分型面的選擇如何確定分型面,需要考慮的因素比較復雜。由于分型面受到塑件在模具中的成型位置、澆注系統(tǒng)設(shè)計、塑件的結(jié)構(gòu)工藝性及精度、嵌件位置形狀以及推出方法、模具的制造、排氣、操作工藝等多種因素的影響,因此在選擇分型面時應(yīng)綜合分析比較,從幾種方案中優(yōu)選出較為合理的方案。選擇分型面時一般應(yīng)遵循以下幾項原則:1)盡量避免側(cè)凹或內(nèi)凸,盡量選用平面垂直分型面。2)盡量采用簡單分型面。3) 分型面應(yīng)選在塑件外形最大輪廓處。4) 便于塑件順利脫模,盡量使塑件開模時留在動模一邊,有利于設(shè)推出機構(gòu)。5) 保證塑件的精度要求。6) 滿足塑件的外觀質(zhì)量要求。7) 便于模具加工制造。8)把抽芯或分型距離長的置于開模方向上。9) 對成型面積的影響。10) 對排氣效果的影響。11)分型面設(shè)在臺階或轉(zhuǎn)角處,以免顯現(xiàn)分型痕跡。12) 對側(cè)向抽芯的影響。根據(jù)以上原則和結(jié)合實際情況下,本設(shè)計選用如圖1所示分型面:畢業(yè)設(shè)計說明書14上圖: 分型面位置4.2 確定型腔的數(shù)量及排列方式該塑件采用一模一穴成型,型腔布置在模具正中位置,這樣有利于澆注系統(tǒng)的模具平衡。排列方式如圖2所示。第四章 注射模的結(jié)構(gòu)設(shè)計圖2模具結(jié)構(gòu)要求對稱,受力平衡時,模具加工條件好,加工精度高時,可以增加型腔數(shù)目,反之,則減少型腔數(shù)目,甚至用單腔模具。此外,模具型腔越多,表示模具加工周期越長,有時須根據(jù)模具加工周期確定型腔數(shù)目。再者,型腔越多,維修要求越高,頻率越快。確定型腔數(shù)目時,須考慮維修的因素。塑料模具在確定型腔數(shù)目之后,就要安排合理的型腔的排列方式。首先第一步是確定注塑模具的重心,以此來確定各型腔的位置。因為在型腔布置中,要求所有注射力、鎖模力均作用于主流道中心,這樣才能使塑料模具穩(wěn)定可靠地工作。若是各型腔合力作用點中心與主流道不同軸,則模具及鎖模系統(tǒng)的載荷發(fā)生偏載,合模時各邊受力不同,致使受力小的一側(cè)密合不嚴,成型時易產(chǎn)生飛邊溢料。除此之外,各型腔到主流道的距離要盡量短,這樣可以減少凝料量。熔融料進入型腔時,各型腔的溫度要保持一致,使得塑料制品內(nèi)應(yīng)力相近,變形相近。在允許的情況下,使各型腔間距離盡可能大些,以便設(shè)置頂桿、冷卻水道等。型腔在注射時所承受的反作用力的合力,應(yīng)作用于模板中心,以便與機筒中心相對應(yīng)。第五章 澆注系統(tǒng)的設(shè)計16第五章 澆注系統(tǒng)的設(shè)計澆注系統(tǒng)是指熔體從注射機噴嘴射出后到達行腔之前在模具內(nèi)流經(jīng)的通道,澆注系統(tǒng)由主流道,分流道,澆口,冷料穴四部分組成,澆注系統(tǒng)是否合理直接關(guān)系到塑料產(chǎn)品的成型質(zhì)量和生產(chǎn)效率,設(shè)計時應(yīng)遵循以下原則:(1)塑料成型特性(2)塑件大小和形狀(3)模具成型塑件的行腔數(shù)(4)塑件外觀(5)成型效率,冷料(7)應(yīng)有利于排氣5.1 主流道設(shè)計主流道是連接注射機噴嘴和注塑模具的橋梁,也是熔融的塑料進入模具型腔時流過的地方,是從注塑機噴嘴與模具接觸的部位起,到分流道為止的這一段。主流道與注射機噴嘴接觸處多做成半球形的凹坑,兩者應(yīng)嚴密的配合,避免高壓塑料熔體溢出,凹坑球半徑 R2 應(yīng)比噴嘴球頭半徑 R1 大 1-2mm。主流道小端直徑應(yīng)比注射機噴嘴孔直徑大 0.5-1mm。大端直徑應(yīng)比分流道深度大 1.5mm 以上,其錐角不宜太大,一般取 20-60。當主流道貫穿幾塊模板時,必須采用主流道襯套,以避免在模板間的拼縫處溢料,以致主流道凝料無法脫出。主流道尺寸如圖 3 所示:第四章 注射模的結(jié)構(gòu)設(shè)計根據(jù)設(shè)計手冊查得HTF650X2型注射機噴嘴的有關(guān)尺寸:噴嘴前端球面孔徑:d 1=4.5mm;噴嘴前端球面半徑:SR 1= 14mm;SR2=SR1+(1-2)mm ; d=d1+(0.5-1)mm;取主流道球面半徑:SR 2=16mm;取主流道的小端直徑:d=3.5mm;定位環(huán)直徑為100mm,定位環(huán)埋入5mm;球面配合高度:h=3~5mm。為了便于將凝料從主流道中拔出,將主流道設(shè)計成圓錐形,其斜度為3 0,經(jīng)換算得:主流大端直徑:D=7.5mm;主流道長度:L=111mm。畢業(yè)設(shè)計說明書185.2 澆口設(shè)計澆口也稱為進料口或內(nèi)流道,它是分流道與塑件之間的狹窄部分,是澆注系統(tǒng)中最短小的部分,也是澆注系統(tǒng)最關(guān)鍵的部分,澆口的形狀,位置和尺寸對塑件的質(zhì)量影響很大。澆口在大多數(shù)情況下是整個流道中斷面尺寸最小的部分,對充模流動起著控制作用,成型后制品與澆注系統(tǒng)從澆口處分離,因此其尺寸又影響著后加工工作量的大小和塑件的外觀。本設(shè)計根據(jù)塑件的成型要求及型腔的排列方式,選用直接澆口,融料從主流道進入型腔,直接澆口的優(yōu)點:流動性好,加工簡單,易充滿型腔,缺點:澆口難分離易產(chǎn)生內(nèi)應(yīng)力,引起塑件變形,設(shè)計如下圖所示:第六章 斜頂6.1斜滑塊的組合斜滑塊的組合形式 根據(jù)塑件的具體情況,斜滑塊通常通常由2-6塊組成瓣合凹模,在某些特殊情況下,斜滑塊還可以分得更多。設(shè)計斜滑塊的組合形式時應(yīng)考慮分型與抽芯的方向要求,并盡量保證塑件具有較好的外觀質(zhì)量,不要使塑件表面有明顯的鑲拼痕跡,另外,還應(yīng)使滑塊的組合部分具有足夠的強度。6.2斜滑塊的導滑形式斜滑塊的導滑形式如圖所示,四種形式中滑塊均沒有鑲?cè)搿檎w式導滑槽其中半圓形也可制成方形。成為斜的梯形槽;圖為鑲拼式,常稱鑲塊導滑或分模楔導滑,導滑部分和分模楔都單獨制造后鑲?cè)肽??,這樣就可以進行熱處理和磨削加工,從而提高了精度和耐磨性,分模楔的位置要有良好的定位,所以用圓柱銷導滑,因滑塊與模套可以同時加工所示平行度容易保證,但應(yīng)注意導柱的斜角要小于模套的斜角。第四章 注射模的結(jié)構(gòu)設(shè)計當塑料制品內(nèi)側(cè)有凹凸時一般采用斜頂方式抽芯,其組成有斜頂,斜頂座,導向塊,所以此設(shè)計采用斜頂抽芯機構(gòu)。斜頂?shù)某榘谓且话氵x取(3-22)°,直身管位長度一般需大于5 mm,為了保證其強度,厚度一般需大于5mm。此次設(shè)計如下圖所示:第七章 成型零件的設(shè)計20第七章 成型零件的設(shè)計常用型腔成型尺寸的計算方法主要有兩種:平均收縮率法和公差帶法,兩種計算方法的區(qū)別在于平均收縮率法計算公式是建立在塑件的成型收縮率和成型零件工作尺寸的制造偏差及其磨損量分別等于它們各自平均值基礎(chǔ)上,當塑件的尺寸精度要求較高或塑件尺寸比較大時,這種誤差有可能會顯著增加,這時一些模具設(shè)計單位就采用公差帶法來進行尺寸計算,平均收縮率法計算簡單無需驗算而公差帶法計算復雜需要經(jīng)過多次初算驗算,且考慮因素較多 [9]??紤]到顯示器后殼模具較簡單制造成本高,設(shè)計時間短故按平均收縮率法計算成型尺寸比較簡單易行 [11]。采用 δ Z ,δ C取固定值的平均收縮率法:Lm---------型腔的徑向工作尺寸 Lm=[Ls+ Ls×Scp-(3/4)△]Ls---------塑件的徑向圖樣尺寸Scp--------收縮率的平均值,查表得 ABS 收縮率范圍是 0.03~0.08△---------塑件尺寸公差δ Z --------型腔制造公差δ C --------型腔最大許用磨損量,δ C 取為塑件尺寸公差△的三分之一表 3.4: 公式表δ Z ,δ C取固定值的平均收縮率法型腔內(nèi)徑尺寸型芯外徑尺寸型腔深度尺寸型芯高度尺寸中心距尺寸查手冊得 ABS 塑料收縮率波動為 0.3~0.8%。7.1 型腔徑向尺寸計算(此題公差為自己標注)以最大徑向尺寸計算,測量得 Ls 為 346.7mm,塑件精度選為 MT2 對應(yīng)的型腔加工精度為 IT9,以該精度查型腔的尺寸公差表,按照 A 類受模具活動部分影響的尺寸公第四章 注射模的結(jié)構(gòu)設(shè)計差查表得△=0.42mm, δ C=△/3=0.14mm畢業(yè)設(shè)計說明書22Lm=[346.7+346.7×(0.003+0.008)/2-(3/4)×0.42]=348.29 0+0427.2 型芯外徑尺寸計算以型芯最大徑向尺寸計算,測量得 Ls 為 341.7mm,塑件精度選為 MT2 對應(yīng)的型腔加工精度為 IT9,以該精度查型腔的尺寸公差表,按照 A 類受模具活動部分影響的尺寸公差查表得△=0.42mm, δ C=△/3=0.14mmLm=[341.7+341.7×(0.003+0.008)/2+(3/4) ×0.42]=343.9 -0.4207.3 型腔深度尺寸計算由 UG4.0 測量得型腔深度為 42.03mm,以 IT9 精度等級制造型腔查手冊,按 B 類不受模具活動部分影響的尺寸公差值查表得△=0.32mm,δ C =0.1mmLm=[42.03+42.03×(0.003+0.008)/2-(3/4)×0.32] 0+0.32=42.020+0.327.4 型芯高度尺寸計算UG4.0 測量得塑件高度尺寸為 39.7mm,以 IT9 精度等級制造查手冊得,按 A 類不受模具活動部分影響的尺寸公差值查表得△=0.20,δ Z=0.067mmhm=[39.7+39.7×(0.003+0.008)/2+(2/3) ×0.20] 0-0.067=40.05 0-0.067mm第八章 脫模推出機構(gòu)的設(shè)計23第八章 脫模推出機構(gòu)的設(shè)計與模架的選用8.1 脫模推出機構(gòu)的設(shè)計制件推出(頂出)是注射成型過程中的最后一個環(huán)節(jié),推出質(zhì)量的好壞將最后決定制品的質(zhì)量,因此,制品的推出是不可忽視的。在設(shè)計推出脫模機構(gòu)時應(yīng)遵循下列原則。1)推出機構(gòu)應(yīng)盡量設(shè)置在動模一側(cè) 由于推出機構(gòu)的動作是通過裝在注射機合模機構(gòu)上的頂桿來驅(qū)動的,所以一般情況下,推出機構(gòu)設(shè)在動模一側(cè)。正因如此,在分型面設(shè)計時應(yīng)盡量注意,開模后使塑件能留在動模一側(cè)。2)保證塑件不因推出而變形損壞 為了保證塑件在推出過程中不變形、不損壞,設(shè)計時應(yīng)仔細分析塑件對模具的包緊力和粘附力的大小,合理的選擇推出方式及推出位置。推力點應(yīng)該作用在制品剛性好的部位,如筋部、凸緣、殼體形制品的壁緣處,盡量避免推力點作用在制品的薄平面上,防止制件破裂、穿孔,如殼體形制件及筒形制件多采用推板推出。 從而使塑件受力均勻、不變形、不損壞。3)機構(gòu)簡單動作可靠 推出機構(gòu)應(yīng)使推出動作可靠、靈活,制造方便,機構(gòu)本身要有足夠的強度、剛度和硬度,以承受推出過程中的各種力的作用,確保塑件順利脫模。4)良好的塑件外觀 推出塑件的位置應(yīng)盡量設(shè)在塑件內(nèi)部,或隱蔽面和非裝飾面,對于透明塑件,尤其要注意頂出位置和頂出形式的選擇,以免推出痕跡影響塑件的外觀質(zhì)量。5)合模時的正確復位 設(shè)計推出機構(gòu)時,還必須考慮合模時機構(gòu)的正確復位,并保證不會與其他模具零件相干涉。推出機構(gòu)的種類按動力來源可分為手動推出,機動推出,液壓氣動推出機構(gòu)。本設(shè)計由于塑件較大,而且有側(cè)向抽芯,經(jīng)過綜合地考慮,方案1,要設(shè)計推出機構(gòu)只能采用頂針推出;方案2,直接采用手動脫模,但時間會加長要增加勞動力。所以,從經(jīng)濟上和時間上考慮決定采用方案1。如下圖所示畢業(yè)設(shè)計說明書248.2 模架的選用本設(shè)計采用CI-7070-A120-B100-C150的標準模架,此模架設(shè)計采用自動脫模,所以適合標準模架。第九章 注射機工藝參數(shù)校核25第九章 注射機工藝參數(shù)校核9.1 注射壓力的校核塑件成型所需要的注射壓力應(yīng)小于或等于注射機的額定注射壓力,其關(guān)系按下式校核:P 成 ≤P 注式中 P 成 ——塑件成型所需的注射壓力( MPa) ;P 注 ——所選注射機的額定注射壓力(MPa) 。本塑件成型材料為 ABS,P 成 =110—140MPa,對于 XS-ZY—500(立式)型注射機,P 注 =145MPa,因此 P 成 ≤P 注 ,所以注射壓力滿足要求。9.2 鎖模力的校核 模具所需的最大鎖模力應(yīng)小于或等于注射機的額定鎖模力,其關(guān)系按下式校核:P 腔 ×F≤P 鎖 =150kN式中 P 腔 ——模具的型腔壓力;F——塑件與澆注系統(tǒng)在分型面上的投影面積(mm 2) ;P 鎖 ——注射機的額定鎖模力(N) 。P 腔 =k×P 成k——損耗系數(shù),這里取 1/3;P 成 ——塑件成型所需的注射壓力(MPa) ,P 成 =110—140MPa,這里 P 成 取140MPa。P 腔 =k×P 成 =1/3×140MPa=46.67MPa。由 UG4.0 分析測量,估算塑件的表面積:A=97516mm 2 注射機噴嘴球半徑 14mm,孔直徑 Ф4.5mm,根據(jù)成型塑料,取主流道直徑D1=7mm,故澆注系統(tǒng)在分型面上的投影面積 A1=π(7/2) 2=38.46mm2。所以 F=A+ A1=97561mm2+38.46mm2=97599mm2P 腔 ×F=46.67MPa×97599mm2=455×103NP 模 =455×103N畢 業(yè) 設(shè) 計 說 明 書題目液晶顯示器后殼注塑模具設(shè)計學 生 姓 名專 業(yè) 名 稱 模 具 設(shè) 計 與 制 造指 導 教 師年五月二四日學 號: 目錄畢業(yè)設(shè)計液晶顯示器后殼注塑模具設(shè)計指導教師: 專業(yè)名稱: 模具設(shè)計與制造 論文提交日期: 論文答辯日期: 論文評閱人: 目錄目錄摘要 1第一章 引言 3第二章 塑件成型工藝分析 42.1 產(chǎn)品開發(fā)依據(jù)用途清單 .42.2 制品結(jié)構(gòu)和形狀的設(shè)計 42.3.制品材料選擇 62.3.1 丙烯腈—丁二烯— 苯乙烯三元共聚物(ABS) .62.3.2 聚苯乙烯(PS) 72.3.3 雙酚 A 型聚碳酸酯(PC) 82.4 注射工藝選擇 102.4.1 ABS 塑料的干燥 .102.4.2 注射壓力 .112.4.3 注射速度 .112.4.4 模具溫度 .112.4.5 料量控制 .11第三章 模具與注射機的關(guān)系 .123.1 塑件的體積計算 .123.2 注射機的選擇 .12第四章 注射模的結(jié)構(gòu)設(shè)計 .144.1 分型面的選擇 .144.2 確定型腔的數(shù)量及排列方式 .15第五章 澆注系統(tǒng)的設(shè)計 .175.1 主流道設(shè)計 .175.2 澆口設(shè)計 .19第六章 斜頂 .196.1 斜滑塊的組合形式 .206.2 斜滑塊的導滑形式 .20第七章 成型零 件的設(shè)計 .217.1 型腔徑向尺寸計算 217.2 型芯外徑尺寸計算 227.3 型腔深度尺寸計算 227.4 型芯高度尺寸計算 22第八章 脫模推出機構(gòu)的設(shè)計與模架的選用 .238.1 脫模推出機構(gòu)的設(shè)計 238.2 模架的選用 24第九章 注射機工藝參數(shù)校核 .25目錄9.1 注射壓力的校核 .259.2 鎖模力的校核 .259.3 模具厚度的校核 .269.4 開模行程的校核 .26第十章 模具冷卻系統(tǒng) .27第十一章 試模及模具維修 .2911.1 模具的安裝 2911.2 試模 2911.3 模具的維修 29第十二章 結(jié)論 .34致謝 .35參考文獻 .36摘要0摘要近年來在我國工業(yè)化快速推進的同時,在國民經(jīng)濟中占有重要地位的模具工業(yè)也得到了迅速發(fā)展。統(tǒng)計顯示,1996 至 2001 年,我國模具制造業(yè)的產(chǎn)值年均增長14%到 15%。 2001 年我國模具總產(chǎn)值就已突破 300 多億元人民幣,排名躍居世界第四位。雖然近幾年來,我國模具工業(yè)的技術(shù)水平已取得了很大的進步,但總體上與工業(yè)發(fā)達的國家相比仍有較大的差距。例如,精密加工設(shè)備還很少,許多先進的技術(shù)如CAD/CAE/CAM技術(shù)的普及率還不高,特別是大型、精密、復雜和長壽命模具遠遠不能滿足國民經(jīng)濟各行業(yè)的發(fā)展需要。此次的設(shè)計任務(wù)即顯示器后殼模具設(shè)計與塑料成型工藝,零件模型擺在面前,如何才能以最快的速度設(shè)計出模具來,并降低成本,首先應(yīng)考慮CAD/CAE/CAM技術(shù)如何才能在設(shè)計中發(fā)揮其主要優(yōu)勢,因此,我使用了強大的模具設(shè)計軟件——UG,在 UG 平臺上,建立產(chǎn)品的 2D、3D 模型,并對其模具設(shè)計!在此次設(shè)計中,主要用所學的注塑模設(shè)計,以及機械設(shè)計等方面的知識,利用 UG4.0 軟件對塑件進行了實體造型,對塑件結(jié)構(gòu)進行了工藝分析。明確了設(shè)計思路,確定了注射成型工藝過程并對各個具體部分進行了詳細的計算和校核。如此設(shè)計出的結(jié)構(gòu)可確保模具工作運用可靠,保證了與其他部件的配合。最后用AUTOCAD 繪制了一套模具裝配圖和零件圖。 本課題通過對顯示器后殼底板的注射模具設(shè)計,鞏固和深化了所學知識,取得了比較滿意的效果,達到了預期的設(shè)計意圖 目錄In recent years the rapid advances in our country industrialization in the national economy, meanwhile, occupies an important place in the mold industry also have developed rapidly. Statistics show that in 1996 and 2001, the output value and mould industry average annual growth 14% to 15%. In 2001, China had breakthrough mold output more than 300 million yuan RMB, the ranking destinations in the world in terms of the fourth. Although in recent years, our country of mold industry technical level has made great progress, but in general and industrial developed countries still have larger gap. For example, precision machining equipment is very few, many advanced technologies such as CAD/CAE/CAM technology popularization rate is not high, especially large, precision, complex and long life mould cant satisfy the development needs of national economic sectors.This design task of display shell mould design and after plastic molding process, parts ahead, how can model with the quickest speed design out of the mold, and reduce the cost, you should consider CAD/CAE/CAM technology in design how can play its main advantage, therefore, I use a powerful mold design software - UG, in UG platform, build the product's 2D, 3D model, and the mould design! In this design, the main injection molding design with what they have learned and mechanical design, use the knowledge of the respect such as UG4.0 software to the plastic parts for solid modeling, structure of the plastic parts the technological analysis. Clear the design ideas, determine the injection molding process and to each particular part of the detailed calculated and checked. So designed to ensure the structure, reliable mould work with other components ensures the cooperation. Finally using AUTOCAD painted a set of mold assembly drawing and detail drawings.This topic through the shell of the display floor after injection mould design, strengthening and deepening the knowledge learnt, achieved satisfactory effect, achieve the expected design intent第一章節(jié) 引言2第一章 引言畢業(yè)設(shè)計(論文)是大學生在學校學習的最后一個重要環(huán)節(jié),既是對學生學習、實踐與研究的全面總結(jié),又是對學生素質(zhì)與能力的一次綜合檢驗,還是學生畢業(yè)資格與學位資格認證的重要依據(jù)。其目的有以下幾方面:(1)培養(yǎng)學生綜合運用所學的基礎(chǔ)理論、專業(yè)知識和基本技能進行分析與解決實際問題的能力,培養(yǎng)學生的創(chuàng)新精神。(2)培養(yǎng)學生收集、整理和分析各種資料的能力,全面提高學生分析和解決實際問題的能力。(3)提高學生設(shè)計、計算和繪圖的能力。提高學生實驗研究和數(shù)據(jù)處理的能力。(4)全面提高學生綜合分析、總結(jié)提高、編制設(shè)計說明書及撰寫科技論文的能力。(5)提高學生外語、計算機應(yīng)用能力。本次設(shè)計的題目是“顯示器后殼注塑模具設(shè)計” ,其內(nèi)容為:(1)學會觀察制品,判斷制件是否符合塑料件的成形條件(比如注意拔模斜度) ,還特別要留意制件影響開模的細部特征;(2)研究制件的排位方式和進澆方式,畫草圖確定模具的整體結(jié)構(gòu),保證結(jié)構(gòu)能循環(huán)工作,穩(wěn)定可靠;(3)在深入研究制件的基礎(chǔ)上確定開模的分型面,以及確定各鑲塊或滑塊、斜頂?shù)姆指蠲娼M或體積塊;(4)對該樣品進行測繪,并在測繪的基礎(chǔ)上對該產(chǎn)品進行模具結(jié)構(gòu)設(shè)計和成型工藝分析(5)用 UG4.0 按照上步的結(jié)果把模具核心的部分:凸凹模分割出來,接著分出各鑲塊、滑塊和斜頂;(6)進一步完善凸凹模和各細微結(jié)構(gòu);(7)調(diào)用 EMX 中適合的模架完成模架設(shè)計;(8)在 UG4.0 中出模具轉(zhuǎn)配圖和模仁圖,以及對模架板塊需要再加工的各組件出工程圖;(9)把 UG4.0 工程圖轉(zhuǎn)入 AUTOCAD 中進行完善。目錄第二章 塑件成型工藝分析2.1 產(chǎn)品開發(fā)依據(jù)用途清單最大幾何尺寸:346.7X281.4X51.2mm環(huán)境:室內(nèi),使用溫度范圍 0℃~60℃無化學品接觸抗沖擊要求:限定量從 2m 高度,0℃下摔下外殼不出現(xiàn)裂縫或者開裂特征剛性要求:在 4Kg 負荷下無變形電氣性能:電絕緣性好外觀要求:部件美觀,外部光潔性一般使用壽命:7 年以上根據(jù)上述使用要求可歸納產(chǎn)品設(shè)計要求為制品材料需要具有一定的抗沖擊性并且由于是電子產(chǎn)品的外殼要有良好的電絕緣性,隨著數(shù)碼產(chǎn)品的大量普及價格也不斷下跌要求生產(chǎn)自動化程度高,成型周期短生產(chǎn)自動化程度高、成型周期短,有較好電絕緣性。2.2 制品結(jié)構(gòu)和形狀的設(shè)計用 UG4.0 軟件進行顯示器后殼的三維建模,三維實體模型更加直觀的表現(xiàn)了產(chǎn)品造型,可以從各個角度對模型進行觀察,軟件可以測量并且還可以根據(jù)三維模型數(shù)據(jù)使用 UG4.0 的 CAE 分析模塊 --塑性顧問進行熔體的充模仿真,可以驗證模具結(jié)構(gòu)的正確性,制品如圖 2.2第二章 塑件成型工藝分析4圖 2.2: 顯示器后殼(用 UG4.0 設(shè)計完成的制品圖)畢業(yè)設(shè)計說明書52.3.制品材料選擇通用塑料如聚丙烯 PP,聚乙烯 PE,聚氯乙烯 PVC 具有應(yīng)用范圍廣、加工性能良好,價格低廉的優(yōu)點,但由于其力學性能較差且成型收縮率較大不易成型尺寸穩(wěn)定的制品故不選用,以下拿三種常用典型材料比較選取。2.3.1丙烯腈—丁二烯—苯乙烯三元共聚物(ABS)ABS 外觀上是淡黃色非晶態(tài)樹脂,不透明,密度與聚苯乙烯基本相同。ABS 具有良好的綜合物理力學性能,耐熱,耐腐,耐油,耐磨、尺寸穩(wěn)定,加工性能優(yōu)良,它具有三種單體所賦予的優(yōu)點。其中丙烯腈賦予材料良好的剛性、硬度、耐油耐腐、良好的著色性和電鍍性;丁二烯賦予材料良好的韌性、耐寒性;苯乙烯賦予材料剛性、硬度、光澤性和良好的加工流動性。改變?nèi)M分的比例,可以調(diào)節(jié)材料性能。ABS 為無定形聚合物,無明顯熔點,熔融流動溫度不太高,隨所含三種單體比例不同,在 160~190℃范圍即具有充分的流動性,且熱穩(wěn)定性較好,在約高于 285℃時才出現(xiàn)分解現(xiàn)象,因此加工溫度范圍較寬。ABS 熔體具有明顯的非牛頓性,提高成型壓力可以使熔體粘度明顯減小,粘度隨溫度升高也會明顯下降。ABS 吸濕性稍大于聚苯乙烯,吸水率約在 0.2%~0.45%之間,但由于熔體粘度不太高,故對于要求不高的制品,可以不經(jīng)干燥,但干燥可使制品具有更好的表面光澤并可改善內(nèi)在質(zhì)量。在80~90℃下干燥 2~3h,可以滿足各種成型要求。 ABS 具有較小的成型收縮率,收縮率變化最大范圍約為 0.3%~0.8%,在多數(shù)情況下,其變化小于該范圍。注塑是 ABS 塑料最重要的成型方法,可以采用柱塞式注塑機,但更長采用螺桿式注塑機,后者更適于形狀復雜制品、大型制品成型 [5]。畢業(yè)設(shè)計說明書62.3.2聚苯乙烯(PS)聚苯乙烯是無色無臭的透明剛硬固體,制品擲地時有金屬般響鳴。聚苯乙烯透光率不低于 80%,霧度約為 3%,折射率較大,在 1.59~1.60 之間,具有特殊光亮性,但儲存時易泛黃。泛黃原因之一是單體純度不夠,特別是在含有微量元素時;二是聚合物在空氣中緩慢老化引起發(fā)黃。聚苯乙烯較輕,密度在 1.04~1.065 之間。①力學性能 聚苯乙烯在熱塑性塑料中屬于典型的硬而脆塑料,拉伸、彎曲等常規(guī)力學性能皆高于聚烯烴,拉伸時無屈服現(xiàn)象。②熱學性能 聚苯乙烯分子鏈雖是剛性鏈,但由于是無定形結(jié)構(gòu),超過玻璃化溫度即開始軟化,軟化點僅 95℃左右,許多力學性能都受到溫度升高的明顯影響。最高連續(xù)使用溫度僅 60~80℃。120℃開始成為熔體,180℃后開始具有流動性,其熱穩(wěn)定性較好,超過 300℃才開始分解,因此聚苯乙烯具有較高的成型加工區(qū)間。③電性能 聚苯乙烯是非極性聚合物,具有頗為優(yōu)異的介電、電絕緣性能,由于吸濕性很小,電性能也不受環(huán)境濕度改變的影響。加工工藝性 吸濕性很小,加工前一般不需要專門的干燥工序成型溫度范圍較寬收縮率及其變化范圍都很小,一般在 0.2%~0.8%有利于成型出尺寸精度較高和尺寸較穩(wěn)定的制品 [5]聚苯乙烯制品容易產(chǎn)生內(nèi)應(yīng)力,并且在空氣中會緩慢老化引起發(fā)黃很顯然不適合選用目錄2.3.3雙酚A型聚碳酸酯(PC)雙酚 A 型聚碳酸酯是無色或者微黃色透明的剛硬、堅韌固體。①力學性能雙酚 A 型聚碳酸酯是典型的硬而韌聚合物,具有良好的綜合力學性能。拉伸、壓縮、彎曲強度均相當于聚酰胺 6、聚酰胺 66,沖擊強度高于所有脂肪族聚酰胺和大多數(shù)工程塑料,抗蠕變性也明顯優(yōu)于聚酰胺、聚甲醛。力學性能方面缺點是耐疲勞性較差,缺口敏感性較明顯②熱性能有良好的耐熱性,玻璃化溫度較高,高于所有的脂肪族聚酰胺,熔融溫度略高于聚酰胺 6 但低于聚酰胺 66,熱變形溫度和最高連續(xù)使用溫度均高于絕大多數(shù)脂肪族聚酰胺,也高于幾乎所有的熱塑性通用塑料。在工程塑料中,他的耐熱性優(yōu)于聚甲醛、脂肪族聚酰胺和 PBT,與 PET 相當,但遜于其他工程塑料。聚碳酸酯具有良好的耐熱性,脆化溫度為-100℃③電性能雙酚 A 型聚碳酸酯是弱極性聚合物,極性的存在對電性能有一定不利影響,在標準條件下電性能雖不如聚烯烴、聚苯乙烯等,但也不失為是電性能較優(yōu)的絕緣材料,特別是因其耐熱性優(yōu)于聚烯烴,可在較寬溫度范圍保持良好的電性能。由于吸濕性較小,環(huán)境溫度對電性能無明顯影響。④其他性能在干燥的氣候條件下物理力學性能基本不變,但在潮濕環(huán)境及強烈日照條件下,會產(chǎn)生表面裂紋并發(fā)暗,在火焰中可緩慢燃燒,離火源后可自熄 [5]。PC 剪切黏度高,充模阻力大,并且由于其在力學性能方面的缺點也不選用。畢業(yè)設(shè)計說明書8表 2.1: 三種材料性能參數(shù)表ABS PS PC密 度 1.05 1.04~1.06 1.18~1.20收 縮 率 0.3~0.8 0.2~0.8 0.5~0.7熔 點 130~160 131~165 220~240熱變形溫度(45N/cm2)65~98 65~90 132~138模具溫度 60~80 40~60 85~120噴嘴溫度 180~190 160~170 250~300中段溫度 180~230 170~190 270~320后段溫度 150~170 140~160 250~270注射壓力 60~100 60~100 50~110塑化形式 螺桿式柱塞式 螺桿式柱塞式 螺桿式柱塞式拉伸強度 33~49 35~63 60~66拉伸彈性模量 1.8 2.8~3.5 2.3彎曲強度 80 61~98 105~113彎曲彈性模量 1.4 - 1.54壓縮強度 18~39 80~112 85缺口沖擊強度 11~20 0.25~0.40 不斷硬 度 R62~86 洛氏 M65~80 11.7HB體積電阻率 1016 1017~1019 1015介電常數(shù) 60Hz2.4~5.0 106 Hz≥2.7 60Hz3.0擊穿電壓 - 19~27 20~30外 觀 淺象牙色或白色不透明無色透明、摔打音清脆透明微黃特 點耐熱、表面硬度高、,尺寸穩(wěn)定、耐化學及電性能好,易成型加工,可鍍鉻耐水、耐化學品、絕緣性好、不耐沖擊不耐溫透明度高、硬而韌、高抗沖、尺寸穩(wěn)定性優(yōu)電絕緣性和耐熱性好、耐開裂耐藥品性差材料最終選定為ABS,其綜合性能優(yōu)異,具有較高的力學性能,流動性好,易于成型;成型收縮率小,理論計算收縮率為0.5% ;溢料值為0.04 mm;比熱容較低,在模具中凝固較快,模塑周期短。制件尺寸穩(wěn)定,表面光亮。目錄2.4 注射工藝選擇2.4.1 ABS塑料的干燥ABS塑料的吸濕性和對水分的敏感性較大,在加工前進行充分的干燥和預熱,不單能消除水汽造成的制件表面煙花狀泡帶、銀絲,而且還有助于塑料的塑化,減少制件表面色斑和云紋。ABS原料需要控制水分在0.3%以下 [5]。注塑前的干燥條件是:干冬季節(jié)在75~80℃以下,干燥2~3h,夏季雨水天在80~90℃下,干燥4~8h,干燥達8~16h可避免因微量水汽的存在導致制件表面霧斑。在此,由于顯示器后殼外殼屬批量件要求自動化程度高實現(xiàn)連續(xù)化生產(chǎn)選用烘干料斗并裝備熱風料斗干燥器,以免干燥好的ABS在料斗中再度吸潮 [。表2.4: ABS工藝參數(shù)表工藝參數(shù) 通用型 ABS料桶后部溫度 180~200料桶中部溫度 210~230料桶前部溫度 200~210噴嘴溫度/℃ 180~190模具溫度/℃ 50~70ABS塑料非牛頓性較強,在熔化過程溫度升高時,其熔融降低很小,但一旦達到塑化溫度(適宜加工的溫度范圍,如220~250℃),如果繼續(xù)盲目升溫,必將導致耐熱性不太高的ABS的熱降解反而使熔融粘度增大,注塑更困難,制件的機械性能也下降。畢業(yè)設(shè)計說明書102.4.2 注射壓力ABS熔融的粘度比聚苯乙烯或改性聚苯乙烯高,在注射時要采用較高的注射壓力。但并非所有ABS制件都要施用高壓,考慮到本制件小型、構(gòu)造不算非常復雜、厚度中等可以用較低的注射壓力。注制過程中,澆口封閉瞬間型腔內(nèi)的壓力大小決定了制件的表面質(zhì)量及銀絲狀缺陷的程度。壓力過小,塑料收縮大,與型腔表面脫離接觸的機會大,制件表面容易霧化。壓力過大,塑料與型腔表面摩擦作用強烈,容易造成粘模。2.4.3 注射速度ABS塑料采用中等注射速度效果較好。當注射速度過快時,塑料易燒焦或分解析出氣化物,從而在制件上出現(xiàn)熔接痕、光澤差及澆口附近塑料發(fā)紅等缺陷。2.4.4模具溫度ABS的成型溫度相對較高,模具溫度也相對較高。一般調(diào)節(jié)模溫為75~85%,當生產(chǎn)具有較大投影面積制件時,定模溫度要求70~80℃,動模溫度要求50~60℃。2.4.5 料量控制注塑機注塑ABS塑料時,其每次注射量僅達標準注射量的75%。為了提高制件質(zhì)量及尺寸穩(wěn)定,表面光澤、色調(diào)的均勻,注射量選為標定注射量的50%。通常要確保注塑機生產(chǎn)條件及參數(shù)有一個很寬的范圍,使大多數(shù)的產(chǎn)品和生產(chǎn)能力要求包含于這范圍內(nèi),并且在調(diào)整確定這范圍的過程時盡量按常規(guī)的工藝流程,這種生產(chǎn)條件范圍愈大,生產(chǎn)過程愈穩(wěn)定,使注塑產(chǎn)品愈不容易受到生產(chǎn)條件的改變而產(chǎn)生明顯的質(zhì)量降低。目錄第三章 模具與注射機的關(guān)系模具型腔能否充滿與注射機允許的最大注射量密切相關(guān),設(shè)計模具時,應(yīng)保證注射模內(nèi)所需熔體總量在注射機實際的最大注射的范圍內(nèi)。3.1 塑件的體積計算由于塑件上存在一些曲面,形狀復雜,所以只能近似的計算其體積。在UG4.0ngineer 軟件上可算出塑件的總體積V=287893mm 33.2 注射機的選擇塑件的體積應(yīng)該小于或者等于注射機的注射量。其關(guān)系式為:V 件≤0.8V 注V 注——注射機的注射量所以:V 注≥V 件÷0.8=359866mm3=359.866cm3由于模具是一模一穴,所以模具塑件的總體積 V 總=359.866cm3估算澆注系統(tǒng)的凝料體積,由于采用的是直接澆口V 凝料=10 cm3所以估算的總體積為 V=359.866+10=369.866cm3由《塑料模具設(shè)計手冊》表 2-40 熱塑性塑料注射機型號與主要技術(shù)規(guī)格中,根據(jù)以上所得出的體積結(jié)果,初步選 HTF650X2 注射機。其主要技術(shù)規(guī)格如表 5。 畢業(yè)設(shè)計說明書12表 5 XS-ZY—500(立式)注射機主要技術(shù)規(guī)格螺桿直徑(mm) Ф65 鎖模力(kN) 650T注射容量(cm 3) 600 最大注射面積(cm 2)1000注射壓力(MPa) 145 模板行程(mm) 120最大 450 球半徑 15 模具厚度(mm) 最小 300噴嘴(mm) 孔直徑 Ф4.5定位孔直徑(mm) Ф100 0+0.06 中心孔徑(mm) Ф30第三章 模具與注射機的關(guān)系13第四章 注射模的結(jié)構(gòu)設(shè)計注射模的結(jié)構(gòu)設(shè)計包括:分型面的選擇、模具型腔數(shù)目的確定及型腔排列方式和冷卻水道布局以及澆口位置的設(shè)置、模具工件零件的結(jié)構(gòu)設(shè)計、頂出系統(tǒng)設(shè)計等內(nèi)容。4.1 分型面的選擇如何確定分型面,需要考慮的因素比較復雜。由于分型面受到塑件在模具中的成型位置、澆注系統(tǒng)設(shè)計、塑件的結(jié)構(gòu)工藝性及精度、嵌件位置形狀以及推出方法、模具的制造、排氣、操作工藝等多種因素的影響,因此在選擇分型面時應(yīng)綜合分析比較,從幾種方案中優(yōu)選出較為合理的方案。選擇分型面時一般應(yīng)遵循以下幾項原則:1)盡量避免側(cè)凹或內(nèi)凸,盡量選用平面垂直分型面。2)盡量采用簡單分型面。3) 分型面應(yīng)選在塑件外形最大輪廓處。4) 便于塑件順利脫模,盡量使塑件開模時留在動模一邊,有利于設(shè)推出機構(gòu)。5) 保證塑件的精度要求。6) 滿足塑件的外觀質(zhì)量要求。7) 便于模具加工制造。8)把抽芯或分型距離長的置于開模方向上。9) 對成型面積的影響。10) 對排氣效果的影響。11)分型面設(shè)在臺階或轉(zhuǎn)角處,以免顯現(xiàn)分型痕跡。12) 對側(cè)向抽芯的影響。根據(jù)以上原則和結(jié)合實際情況下,本設(shè)計選用如圖1所示分型面:畢業(yè)設(shè)計說明書14上圖: 分型面位置4.2 確定型腔的數(shù)量及排列方式該塑件采用一模一穴成型,型腔布置在模具正中位置,這樣有利于澆注系統(tǒng)的模具平衡。排列方式如圖2所示。第四章 注射模的結(jié)構(gòu)設(shè)計圖2模具結(jié)構(gòu)要求對稱,受力平衡時,模具加工條件好,加工精度高時,可以增加型腔數(shù)目,反之,則減少型腔數(shù)目,甚至用單腔模具。此外,模具型腔越多,表示模具加工周期越長,有時須根據(jù)模具加工周期確定型腔數(shù)目。再者,型腔越多,維修要求越高,頻率越快。確定型腔數(shù)目時,須考慮維修的因素。塑料模具在確定型腔數(shù)目之后,就要安排合理的型腔的排列方式。首先第一步是確定注塑模具的重心,以此來確定各型腔的位置。因為在型腔布置中,要求所有注射力、鎖模力均作用于主流道中心,這樣才能使塑料模具穩(wěn)定可靠地工作。若是各型腔合力作用點中心與主流道不同軸,則模具及鎖模系統(tǒng)的載荷發(fā)生偏載,合模時各邊受力不同,致使受力小的一側(cè)密合不嚴,成型時易產(chǎn)生飛邊溢料。除此之外,各型腔到主流道的距離要盡量短,這樣可以減少凝料量。熔融料進入型腔時,各型腔的溫度要保持一致,使得塑料制品內(nèi)應(yīng)力相近,變形相近。在允許的情況下,使各型腔間距離盡可能大些,以便設(shè)置頂桿、冷卻水道等。型腔在注射時所承受的反作用力的合力,應(yīng)作用于模板中心,以便與機筒中心相對應(yīng)。第五章 澆注系統(tǒng)的設(shè)計16第五章 澆注系統(tǒng)的設(shè)計澆注系統(tǒng)是指熔體從注射機噴嘴射出后到達行腔之前在模具內(nèi)流經(jīng)的通道,澆注系統(tǒng)由主流道,分流道,澆口,冷料穴四部分組成,澆注系統(tǒng)是否合理直接關(guān)系到塑料產(chǎn)品的成型質(zhì)量和生產(chǎn)效率,設(shè)計時應(yīng)遵循以下原則:(1)塑料成型特性(2)塑件大小和形狀(3)模具成型塑件的行腔數(shù)(4)塑件外觀(5)成型效率,冷料(7)應(yīng)有利于排氣5.1 主流道設(shè)計主流道是連接注射機噴嘴和注塑模具的橋梁,也是熔融的塑料進入模具型腔時流過的地方,是從注塑機噴嘴與模具接觸的部位起,到分流道為止的這一段。主流道與注射機噴嘴接觸處多做成半球形的凹坑,兩者應(yīng)嚴密的配合,避免高壓塑料熔體溢出,凹坑球半徑 R2 應(yīng)比噴嘴球頭半徑 R1 大 1-2mm。主流道小端直徑應(yīng)比注射機噴嘴孔直徑大 0.5-1mm。大端直徑應(yīng)比分流道深度大 1.5mm 以上,其錐角不宜太大,一般取 20-60。當主流道貫穿幾塊模板時,必須采用主流道襯套,以避免在模板間的拼縫處溢料,以致主流道凝料無法脫出。主流道尺寸如圖 3 所示:第四章 注射模的結(jié)構(gòu)設(shè)計根據(jù)設(shè)計手冊查得HTF650X2型注射機噴嘴的有關(guān)尺寸:噴嘴前端球面孔徑:d 1=4.5mm;噴嘴前端球面半徑:SR 1= 14mm;SR2=SR1+(1-2)mm ; d=d1+(0.5-1)mm;取主流道球面半徑:SR 2=16mm;取主流道的小端直徑:d=3.5mm;定位環(huán)直徑為100mm,定位環(huán)埋入5mm;球面配合高度:h=3~5mm。為了便于將凝料從主流道中拔出,將主流道設(shè)計成圓錐形,其斜度為3 0,經(jīng)換算得:主流大端直徑:D=7.5mm;主流道長度:L=111mm。畢業(yè)設(shè)計說明書185.2 澆口設(shè)計澆口也稱為進料口或內(nèi)流道,它是分流道與塑件之間的狹窄部分,是澆注系統(tǒng)中最短小的部分,也是澆注系統(tǒng)最關(guān)鍵的部分,澆口的形狀,位置和尺寸對塑件的質(zhì)量影響很大。澆口在大多數(shù)情況下是整個流道中斷面尺寸最小的部分,對充模流動起著控制作用,成型后制品與澆注系統(tǒng)從澆口處分離,因此其尺寸又影響著后加工工作量的大小和塑件的外觀。本設(shè)計根據(jù)塑件的成型要求及型腔的排列方式,選用直接澆口,融料從主流道進入型腔,直接澆口的優(yōu)點:流動性好,加工簡單,易充滿型腔,缺點:澆口難分離易產(chǎn)生內(nèi)應(yīng)力,引起塑件變形,設(shè)計如下圖所示:第六章 斜頂6.1斜滑塊的組合斜滑塊的組合形式 根據(jù)塑件的具體情況,斜滑塊通常通常由2-6塊組成瓣合凹模,在某些特殊情況下,斜滑塊還可以分得更多。設(shè)計斜滑塊的組合形式時應(yīng)考慮分型與抽芯的方向要求,并盡量保證塑件具有較好的外觀質(zhì)量,不要使塑件表面有明顯的鑲拼痕跡,另外,還應(yīng)使滑塊的組合部分具有足夠的強度。6.2斜滑塊的導滑形式斜滑塊的導滑形式如圖所示,四種形式中滑塊均沒有鑲?cè)?。為整體式導滑槽其中半圓形也可制成方形。成為斜的梯形槽;圖為鑲拼式,常稱鑲塊導滑或分模楔導滑,導滑部分和分模楔都單獨制造后鑲?cè)肽??,這樣就可以進行熱處理和磨削加工,從而提高了精度和耐磨性,分模楔的位置要有良好的定位,所以用圓柱銷導滑,因滑塊與模套可以同時加工所示平行度容易保證,但應(yīng)注意導柱的斜角要小于模套的斜角。第四章 注射模的結(jié)構(gòu)設(shè)計當塑料制品內(nèi)側(cè)有凹凸時一般采用斜頂方式抽芯,其組成有斜頂,斜頂座,導向塊,所以此設(shè)計采用斜頂抽芯機構(gòu)。斜頂?shù)某榘谓且话氵x取(3-22)°,直身管位長度一般需大于5 mm,為了保證其強度,厚度一般需大于5mm。此次設(shè)計如下圖所示:第七章 成型零件的設(shè)計20第七章 成型零件的設(shè)計常用型腔成型尺寸的計算方法主要有兩種:平均收縮率法和公差帶法,兩種計算方法的區(qū)別在于平均收縮率法計算公式是建立在塑件的成型收縮率和成型零件工作尺寸的制造偏差及其磨損量分別等于它們各自平均值基礎(chǔ)上,當塑件的尺寸精度要求較高或塑件尺寸比較大時,這種誤差有可能會顯著增加,這時一些模具設(shè)計單位就采用公差帶法來進行尺寸計算,平均收縮率法計算簡單無需驗算而公差帶法計算復雜需要經(jīng)過多次初算驗算,且考慮因素較多 [9]??紤]到顯示器后殼模具較簡單制造成本高,設(shè)計時間短故按平均收縮率法計算成型尺寸比較簡單易行 [11]。采用 δ Z ,δ C取固定值的平均收縮率法:Lm---------型腔的徑向工作尺寸 Lm=[Ls+ Ls×Scp-(3/4)△]Ls---------塑件的徑向圖樣尺寸Scp--------收縮率的平均值,查表得 ABS 收縮率范圍是 0.03~0.08△---------塑件尺寸公差δ Z --------型腔制造公差δ C --------型腔最大許用磨損量,δ C 取為塑件尺寸公差△的三分之一表 3.4: 公式表δ Z ,δ C取固定值的平均收縮率法型腔內(nèi)徑尺寸型芯外徑尺寸型腔深度尺寸型芯高度尺寸中心距尺寸查手冊得 ABS 塑料收縮率波動為 0.3~0.8%。7.1 型腔徑向尺寸計算(此題公差為自己標注)以最大徑向尺寸計算,測量得 Ls 為 346.7mm,塑件精度選為 MT2 對應(yīng)的型腔加工精度為 IT9,以該精度查型腔的尺寸公差表,按照 A 類受模具活動部分影響的尺寸公第四章 注射模的結(jié)構(gòu)設(shè)計差查表得△=0.42mm, δ C=△/3=0.14mm畢業(yè)設(shè)計說明書22Lm=[346.7+346.7×(0.003+0.008)/2-(3/4)×0.42]=348.29 0+0427.2 型芯外徑尺寸計算以型芯最大徑向尺寸計算,測量得 Ls 為 341.7mm,塑件精度選為 MT2 對應(yīng)的型腔加工精度為 IT9,以該精度查型腔的尺寸公差表,按照 A 類受模具活動部分影響的尺寸公差查表得△=0.42mm, δ C=△/3=0.14mmLm=[341.7+341.7×(0.003+0.008)/2+(3/4) ×0.42]=343.9 -0.4207.3 型腔深度尺寸計算由 UG4.0 測量得型腔深度為 42.03mm,以 IT9 精度等級制造型腔查手冊,按 B 類不受模具活動部分影響的尺寸公差值查表得△=0.32mm,δ C =0.1mmLm=[42.03+42.03×(0.003+0.008)/2-(3/4)×0.32] 0+0.32=42.020+0.327.4 型芯高度尺寸計算UG4.0 測量得塑件高度尺寸為 39.7mm,以 IT9 精度等級制造查手冊得,按 A 類不受模具活動部分影響的尺寸公差值查表得△=0.20,δ Z=0.067mmhm=[39.7+39.7×(0.003+0.008)/2+(2/3) ×0.20] 0-0.067=40.05 0-0.067mm第八章 脫模推出機構(gòu)的設(shè)計23第八章 脫模推出機構(gòu)的設(shè)計與模架的選用8.1 脫模推出機構(gòu)的設(shè)計制件推出(頂出)是注射成型過程中的最后一個環(huán)節(jié),推出質(zhì)量的好壞將最后決定制品的質(zhì)量,因此,制品的推出是不可忽視的。在設(shè)計推出脫模機構(gòu)時應(yīng)遵循下列原則。1)推出機構(gòu)應(yīng)盡量設(shè)置在動模一側(cè) 由于推出機構(gòu)的動作是通過裝在注射機合模機構(gòu)上的頂桿來驅(qū)動的,所以一般情況下,推出機構(gòu)設(shè)在動模一側(cè)。正因如此,在分型面設(shè)計時應(yīng)盡量注意,開模后使塑件能留在動模一側(cè)。2)保證塑件不因推出而變形損壞 為了保證塑件在推出過程中不變形、不損壞,設(shè)計時應(yīng)仔細分析塑件對模具的包緊力和粘附力的大小,合理的選擇推出方式及推出位置。推力點應(yīng)該作用在制品剛性好的部位,如筋部、凸緣、殼體形制品的壁緣處,盡量避免推力點作用在制品的薄平面上,防止制件破裂、穿孔,如殼體形制件及筒形制件多采用推板推出。 從而使塑件受力均勻、不變形、不損壞。3)機構(gòu)簡單動作可靠 推出機構(gòu)應(yīng)使推出動作可靠、靈活,制造方便,機構(gòu)本身要有足夠的強度、剛度和硬度,以承受推出過程中的各種力的作用,確保塑件順利脫模。4)良好的塑件外觀 推出塑件的位置應(yīng)盡量設(shè)在塑件內(nèi)部,或隱蔽面和非裝飾面,對于透明塑件,尤其要注意頂出位置和頂出形式的選擇,以免推出痕跡影響塑件的外觀質(zhì)量。5)合模時的正確復位 設(shè)計推出機構(gòu)時,還必須考慮合模時機構(gòu)的正確復位,并保證不會與其他模具零件相干涉。推出機構(gòu)的種類按動力來源可分為手動推出,機動推出,液壓氣動推出機構(gòu)。本設(shè)計由于塑件較大,而且有側(cè)向抽芯,經(jīng)過綜合地考慮,方案1,要設(shè)計推出機構(gòu)只能采用頂針推出;方案2,直接采用手動脫模,但時間會加長要增加勞動力。所以,從經(jīng)濟上和時間上考慮決定采用方案1。如下圖所示畢業(yè)設(shè)計說明書248.2 模架的選用本設(shè)計采用CI-7070-A120-B100-C150的標準模架,此模架設(shè)計采用自動脫模,所以適合標準模架。第九章 注射機工藝參數(shù)校核25第九章 注射機工藝參數(shù)校核9.1 注射壓力的校核塑件成型所需要的注射壓力應(yīng)小于或等于注射機的額定注射壓力,其關(guān)系按下式校核:P 成 ≤P 注式中 P 成 ——塑件成型所需的注射壓力( MPa) ;P 注 ——所選注射機的額定注射壓力(MPa) 。本塑件成型材料為 ABS,P 成 =110—140MPa,對于 XS-ZY—500(立式)型注射機,P 注 =145MPa,因此 P 成 ≤P 注 ,所以注射壓力滿足要求。9.2 鎖模力的校核 模具所需的最大鎖模力應(yīng)小于或等于注射機的額定鎖模力,其關(guān)系按下式校核:P 腔 ×F≤P 鎖 =150kN式中 P 腔 ——模具的型腔壓力;F——塑件與澆注系統(tǒng)在分型面上的投影面積(mm 2) ;P 鎖 ——注射機的額定鎖模力(N) 。P 腔 =k×P 成k——損耗系數(shù),這里取 1/3;P 成 ——塑件成型所需的注射壓力(MPa) ,P 成 =110—140MPa,這里 P 成 取140MPa。P 腔 =k×P 成 =1/3×140MPa=46.67MPa。由 UG4.0 分析測量,估算塑件的表面積:A=97516mm 2 注射機噴嘴球半徑 14mm,孔直徑 Ф4.5mm,根據(jù)成型塑料,取主流道直徑D1=7mm,故澆注系統(tǒng)在分型面上的投影面積 A1=π(7/2) 2=38.46mm2。所以 F=A+ A1=97561mm2+38.46mm2=97599mm2P 腔 ×F=46.67MPa×97599mm2=455×103NP 模 =455×103N