【溫馨提示】壓縮包內(nèi)含CAD圖有下方大圖片預覽,下拉即可直觀呈現(xiàn)眼前查看、盡收眼底縱觀。打包內(nèi)容里dwg后綴的文件為CAD圖,可編輯,無水印,高清圖,壓縮包內(nèi)文檔可直接點開預覽,需要原稿請自助充值下載,所見才能所得,請見壓縮包內(nèi)的文件及下方預覽,請細心查看有疑問可以咨詢QQ:11970985或197216396

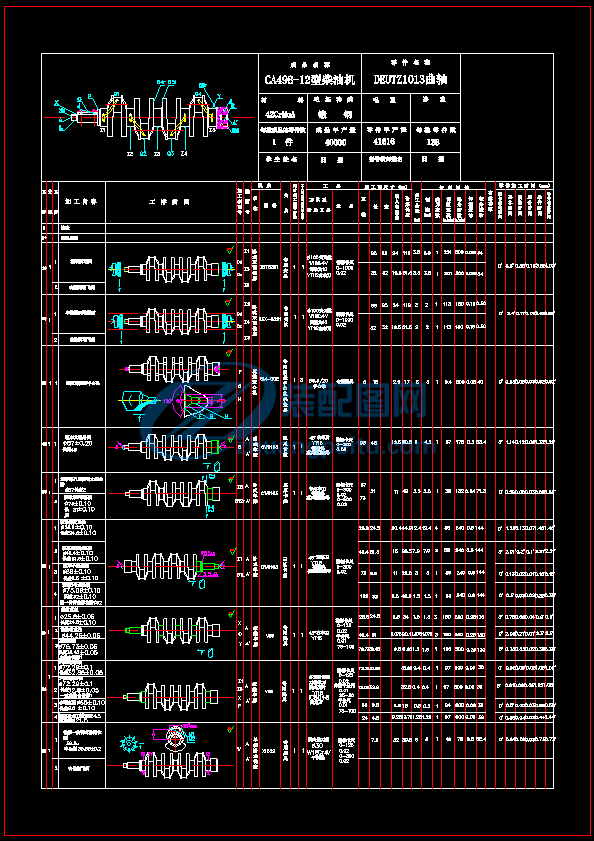

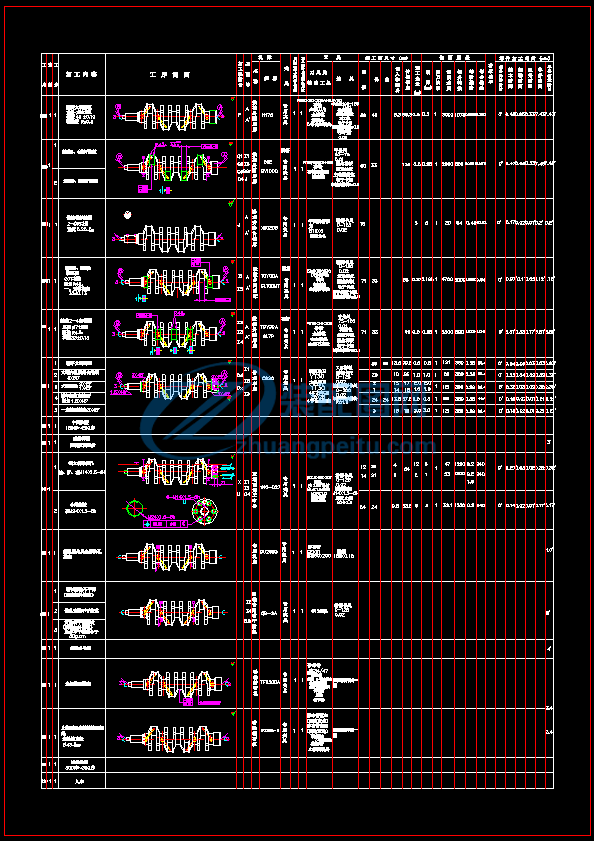
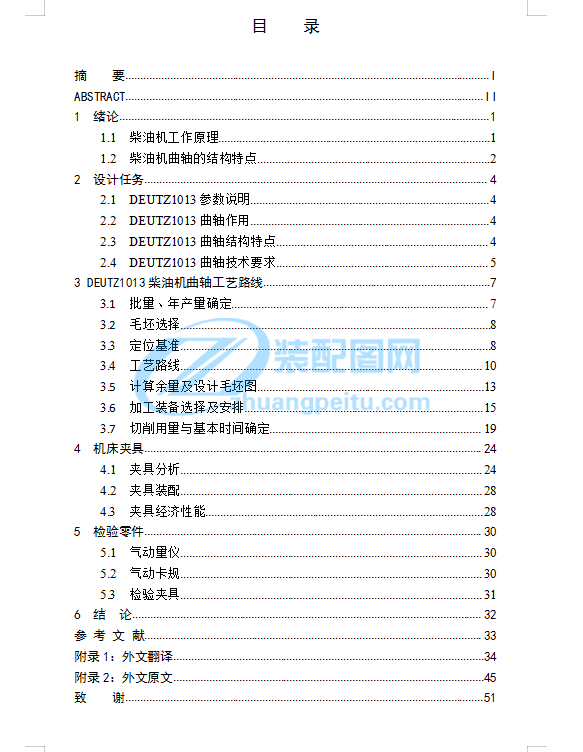
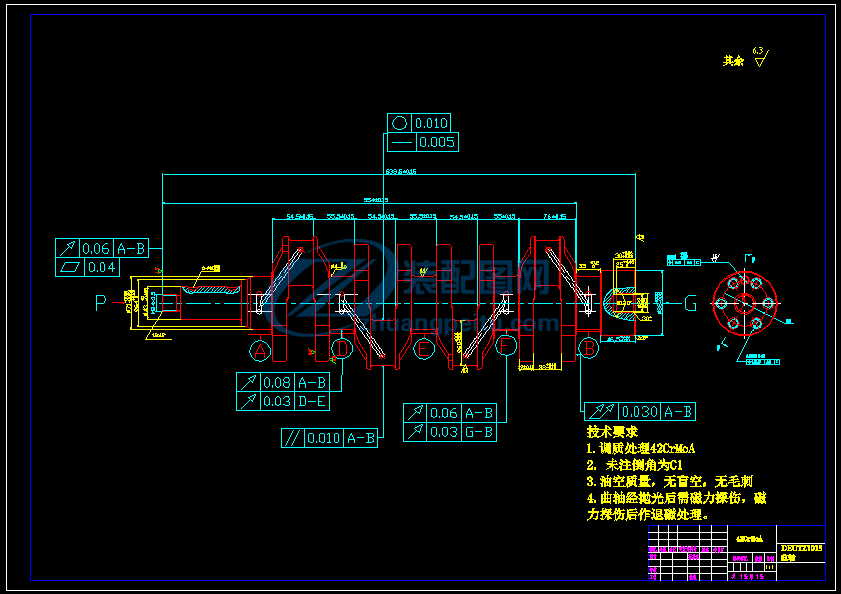

DEUTZ1013柴油機曲軸加工工藝規(guī)程設計
1 緒論
1.1 柴油機工作原理
發(fā)動機本身是一種能夠把其他形式的能轉(zhuǎn)換為機械能的機器。那么,發(fā)動機是如何完成這個轉(zhuǎn)換的過程的呢?換而言之它是如何將其他形式能(熱能)轉(zhuǎn)換為機械能呢?完成此過程需進行進氣,將可燃氣體(或者新鮮的空氣)放入汽缸;隨后把氣缸內(nèi)的混合氣體(或者新鮮的空氣)壓縮,快臨近終點的時候點燃可燃氣體(或者把柴油機的高壓油壓如氣缸內(nèi)并形成壓縮氣體然后點燃);混合氣體燃燒產(chǎn)生熱量,氣體膨脹推動活塞做功;最終排出氣缸內(nèi)的廢氣。故共四個過程:進氣、壓縮、做工、排氣,即為一個工作循環(huán)。不斷重復此循環(huán)從而實現(xiàn)能量的轉(zhuǎn)化,發(fā)動機得以運轉(zhuǎn)。循環(huán)完成一次,對應活塞不間斷做四次上下往返運動,曲軸連轉(zhuǎn)兩圈,我們把這種類型的柴油機稱作四沖程柴油機。工作循環(huán)完成一次,對應曲軸旋轉(zhuǎn)一圈,活塞上下做兩次往復運動,這類柴油機稱作二沖程發(fā)動機。這里主要介紹四沖程發(fā)動機工作的原理和過程。
四沖程柴油機和四沖程汽油機工作原理及過程大體相似,即每一個工作循環(huán)行程相同,但是因為柴油的粘性很大,不容易蒸發(fā),燃點低,與汽油相比差異較大,因此可燃混合氣體的產(chǎn)生、氣體溫度壓力變化、燃燒形式及過程與汽油相比有很大差異。這里主要比較柴油機與汽油機工作時的異同。
⑴進氣
四沖程柴油機進氣過程中與汽油機不同的是,柴油機進入氣缸的工質(zhì)是純空氣而非混合可燃氣體且柴油機進氣系統(tǒng)阻力較小。終點壓力pa=0.85~0.95MPa。與汽油溫度相比略高;終點溫度Ta=300~340k。故與汽油相比略低。
⑵壓縮
與進氣工質(zhì)相同,壓縮的也為純空氣壓縮過程接近終點時,將高壓柴油噴入氣缸內(nèi),進氣門排氣門同時封閉,活塞不停向上移動,使缸內(nèi)體積不斷減小達到終點,缸內(nèi)溫度上升體積減小。缸內(nèi)壓力pc=800~2000kpa,溫度Ta=600~750k,高于汽油機。
⑶做功
在壓縮氣體達到終點時高壓油泵將高壓油噴入燃燒室,與空氣接觸隨即便會燃燒。和、這與汽油機不同,柴油機的可燃混合氣是在進入汽缸后混合而成的。而汽油機則是在外面的化油器里完成的。在燃燒過程中,柴油機氣缸內(nèi)氣體膨脹,容積不變導致壓力迅速上升,最高可到6000~9000kpa,最高溫度可到1800~2000k。
⑷排氣
柴油機與汽油機的排氣過程大體相同,即廢氣經(jīng)排氣管排到外面。氣體排凈時,溫度比汽油機略低,一般為Tr=700~900k。
與汽油不同的是,柴油機的動力性能優(yōu)越、燃燒率高、可燃氣體消耗率低并且價格便宜。所以柴油機燃料性價比高;柴油機環(huán)保(排出的廢氣少)。但是它體積大、轉(zhuǎn)速低、制造成本高、震動噪音大等等。隨著技術的不斷提高,這些缺點也將會被消除,變得越來越完美。
上述介紹的為單杠發(fā)動機,但是現(xiàn)代的汽車大多為多缸四沖程發(fā)動機。二者有何區(qū)別呢?二者都需進行四個行程,即進氣、壓縮、做功、排氣。然而單缸工作過程中只有一個行程做功,其他三個不做功。也就是說在曲軸旋轉(zhuǎn)兩圈的過程中僅有半圈做功。因而運行時平穩(wěn)性差,但是在過程中消耗功率較大。為使轉(zhuǎn)速均勻,通常裝有大飛輪。但多缸的行程為彼此岔開,交替進行的。也就是說曲軸旋轉(zhuǎn)交替做功。故轉(zhuǎn)速均勻,振幅小。因此缸數(shù)與運轉(zhuǎn)平穩(wěn)性成正比,同時也間隔角成反比。
1.2 柴油機曲軸的結(jié)構特性
曲軸的基本構成如下圖所示,由自由端、功率輸出端和曲拐構成。
曲拐6由主軸頸4、連桿軸徑3和曲柄2構成。
自由端1由曲柄、連桿軸徑、主軸頸、功率輸出端、曲拐和平衡塊7構成。
圖1.1
曲軸功率輸出端(飛輪端):飛輪安裝在除最后曲拐以外的部分,用以驅(qū)動機械的銜接和軸端的密封。
曲軸的自由端(前端):是在第一個曲拐以前的部分安裝傳動裝置,它包括:軸端密封裝置、正時齒輪、柴油機輔助系統(tǒng)。此外,高速柴油機的汽缸中還布置了渦流室或預燃室。
曲軸結(jié)構類型分為整體式和組合式。組合式是把分成若干個零件的曲軸分別進行加工,最后拼裝在一起構成完整曲軸。優(yōu)點是便于加工,產(chǎn)品可以通用;缺點是它的結(jié)構剛度低、強度小且組裝復雜。整體式是把自由端,功率輸出端和曲拐連接成一個完整的零件。優(yōu)點是強度高、剛度大、質(zhì)量小和結(jié)構緊湊。缺點是難于加工。故綜合比較后,選擇整體式曲軸。
主軸頸、連桿頸:工作時轉(zhuǎn)速很高,在軸承內(nèi)受到載荷作用。所以,對表面粗糙度和精度要求精準。為了提高耐磨性,常用處理方法為淬火和氮化處理。
曲柄:受力最薄弱和復雜的部分,所以它的結(jié)構和連接要特別注意。以下是常見曲軸,如圖2.2示:α圓形、β橢圓形、θ矩形。
圖2.2
曲柄連接著連桿頸與主軸頸,它是核心部件。由于曲柄形狀,它的應力過于集中,因此非常容易產(chǎn)生斷裂。為減小應力集中,在小曲軸軸徑和曲柄銜接處增大強度,增大弧度,使應力減小。但是,過度增大,則軸承受力面積變小從而應力變小,或者加大了柴油機的軸向尺寸。2 設計任務
2.1 DEUTZ1013參數(shù)說明
2.2 DEUTZ1013曲軸作用
曲軸是活塞往返運動以及旋轉(zhuǎn)運動二者之間的介質(zhì),在做功行程里將能量傳遞出去。傳遞能量通過飛輪裝置,由于飛輪裝置位于軸末端,這樣曲軸可以勻速旋轉(zhuǎn)并且其余行程得以正常運轉(zhuǎn)。為增強慣性力的均衡、縮小內(nèi)燃機耗能,還可以在曲柄處加裝平衡裝置。
曲軸,作為發(fā)動機里最重要的部分,可以說是“引擎的心臟”。曲軸執(zhí)行的準確程度決定著引擎是否可以正常發(fā)揮。每一個相對角度都必須精準,否則會嚴重影響氣門正時、點火正時準確度,從而每個汽缸就不能正常運作。另一個重點則是DEUTZ1013曲軸的軸承之間的間隙。為了達到足夠的潤滑性和冷卻性,在連桿軸承與主軸承之間必須留有適當?shù)拈g隙令機油流動。否則磨損增大,機件損傷很大。但是間隙距離如果過大,會使軸承內(nèi)活塞做功增加,從而造成了燃燒室內(nèi)剩余機油過多影響其他行程。因此為DEUTZ1013曲軸工作得以正常進行,在加工DEUTZ1013曲軸的是要確保誤差、強度、剛度等等。
2.3 DEUTZ1013曲軸結(jié)構特點
曲軸的特點是每一個軸心不在一條直線,在機體的中心孔內(nèi)安裝的軸叫做主軸。然而它只能通過座孔繞本身運動;此外,通過曲柄、主軸相連的軸叫做連桿軸,它只繞主軸運轉(zhuǎn)。曲軸,作為最重要與負荷最大的部件,主要作用是活塞往返運動及回轉(zhuǎn)運動之間的介質(zhì)。顯而易見DEUTZ1013曲軸除了周期性扭矩和彎矩,還有扭轉(zhuǎn)振動帶來的附加應力,因此曲軸受力極為復雜。綜上所述,根據(jù)以上曲軸的結(jié)構特點,在加工時要高強度、高剛度、強沖擊韌性及強耐磨性等等。在加工工藝過程中,增大突變面積以減小應力集中,選用高強度材料,經(jīng)過熱處理增大耐磨性……以避免斷裂。
主軸與連桿軸的形狀誤差、定位誤差和表面粗糙度要求精度很高。為不影響每個汽缸之間行程的相位配合,對齒輪偏移量提一點要求。
2.4 DEUTZ1013曲軸技術要求
(1)42CrMoADEUTZ1013曲軸經(jīng)淬火硬度HRC48~53。連桿軸徑、主軸頸進行淬火處理,溫度在830~850℃。淬火深度為3.5~7.0mm。此外每個DEUTZ1013曲軸剛度差須在四個單位以內(nèi)。
(2)42CrMoADEUTZ1013曲軸再進行回火處理,以消除淬火過程中的內(nèi)應力與脆性,增加DEUTZ1013曲軸的韌性和塑性。硬度HRC48~53,溫度260~300。
(3)42CrMoADEUTZ1013曲軸進行調(diào)質(zhì)處理,使鋼件有良好的性能。
(4)主要化學成分:C0.38~0.45%,Si0.17~0.37%,Mn0.50~0.80%,Cr0.90~1.20%,Mo0.15~0.25%。
(5)疲勞強度、韌性、淬透性和強度比40Cr高,熱處理無過熱傾向,狀態(tài)為細晶粒鋼,淬火過程中形變小。
(6)自身有第一回火脆性,焊接性差、冷變形塑性一般、切削加工性好。
(7)DEUTZ1013曲軸磨光加工后的表面不應有黑點、刻痕。加工表面須光潔,不應有壓痕、氣孔、毛刺、裂紋、凹痕、廢舊金屬夾雜物及發(fā)裂。
(8)DEUTZ1013曲軸非加工面須光潔,不得有夾灰、分層、非金屬夾雜物、硬傷、裂縫及夾渣等,不可以使用焊補消除。
(9)DEUTZ1013曲軸應按CA498-12型柴油機規(guī)定做拋光、磁力探傷及退磁處理。
(10)DEUTZ1013曲軸加工后要進行平衡實驗。
3 DEUTZ1013柴油機曲軸工藝路線
3.1 批量、年產(chǎn)量確定
⑴生產(chǎn)綱領40000臺/每年柴油機
Q=40000*1*(1+2%)*(1+2%)=41616
月產(chǎn)量=Q/12=3468
Days=(365-52-14)/12=25天
日產(chǎn)量(一天3班)=月產(chǎn)量/Days=3468/25=138
①生產(chǎn)類型
查手冊知,100公斤以內(nèi)生產(chǎn)性質(zhì):
DEUTZ1013曲軸生產(chǎn)性質(zhì)為大批
②選擇三班制
第一班:2070小時 第二班:2070小時 第三班:1560小時
注:女工人占25%以下,分別為1664小時、1664小時、1248小時
總計時為4556小時
③
其中,-損失系數(shù)
-工作時段設備修理損失
-工人缺勤以及自然需求損失
-清理設備所耗的損失
-工人休息的損失
平均流水線節(jié)拍=4576*60*(1-15%)/52020=4.5min
為保證產(chǎn)品按時完成,任何一道工序單個產(chǎn)品的計算時間要小于該產(chǎn)品的生產(chǎn)節(jié)拍;如果大于,將不能定時完成指標。
注:填寫工藝卡時,考慮到客觀因素,按80%的生產(chǎn)節(jié)拍計算。
⑵生產(chǎn)間隔和批量
當最長的工序時間和整體加工的時間確定時,生產(chǎn)率與生產(chǎn)間隔、批量成正比。但與資金周轉(zhuǎn)的快慢與生產(chǎn)率、生產(chǎn)間隔等有關系,因此要多方面考慮。
3.2 毛坯選擇
選擇毛坯時要遵循四項原則,即適用性原則、經(jīng)濟性原則、可行性原則及環(huán)保性原則。這四項原則是相互聯(lián)系的,應在保證第一原則的前提下,力求做到質(zhì)量好,成本低,制造周期短和環(huán)保的原則。并且毛坯的制造方法也同樣重要。對于曲軸的特殊性,要注意材料本身的加工性能、力學性能。
曲軸毛坯的類型主要包括鍛件、焊接件、鑄件和型材等??紤]到零件的特殊性,所以采用鍛件,主要流程采用鍛造。鍛造可以消除冶煉時產(chǎn)生的鑄態(tài)疏松,內(nèi)部通過氣孔與縮孔鏈接,故密封性極強。此外使組織機構內(nèi)金屬纖維合理分布,疲勞強度高、延伸性好及抗沖壓性能高。材料主要有:50Mn、45鋼、20Cr等。
這里采用模鍛,材料選用42CrMoA。因為在大批量生產(chǎn)中,對毛坯要求余量小、精度要求高。
模鍛后,為提高機械性能和加工方便,毛坯需調(diào)質(zhì)處理和去除氧化膜。
3.3 定位基準
3.3.1 DEUTZ1013柴油機曲軸加工工藝
影響曲軸制造的兩個重要因素為:摩擦副和震動副。摩擦副是主要作用于連桿及連桿軸徑二者間的摩擦;震動副是做功行程中受力的作用或者DEUTZ1013柴油機在引燃爆炸過程里對曲軸的沖擊的震動。曲軸雖然形狀復雜,但是也有一定規(guī)律性,根據(jù)曲軸的特點,可以進行如車、鏜、鉆、銑等工藝方法。下面簡要分析一下幾個方面的工藝特點。
形狀
由于主軸徑連桿軸徑分布在不同的軸線上,所以受力不平衡,使加DEUTZ1013曲軸加工工藝變得復雜。為消除不平衡現(xiàn)象,主要采取措施為使用平衡重,在設計中應注意在連桿軸定位時用偏心夾具。對于像大型曲軸這類的不平衡現(xiàn)象明顯的,應使刀具旋轉(zhuǎn),曲軸不轉(zhuǎn)。在曲柄臂端面處銑兩處平面,用來當做確定曲軸角度精確度的輔助基準;軸向定位用齒輪銷孔。
剛度
DEUTZ1013曲軸長徑比(I/D)大,故剛度低。在切削力和自身重力作用下,產(chǎn)生極強的扭矩和彎矩,尤其是單動機床。故注意一下幾點:
⑴制造加工過程中,如粗加工,余量大,切除余料較多。因此機床車刀、夾具等剛度要求高。
⑵曲軸加工時,為增加剛度,中間用支撐架以降低振幅和形變。
⑶為減少扭矩和彎矩,采取高強度機床。傳動方式采取中間傳動或者兩邊傳動。
⑷加工時應盡量減小切削力的影響。
⑸在可能產(chǎn)生形變誤差的工序處,后面添加校正工序
⑹工序要安排合理。
技術要求
上述兩個方面已經(jīng)闡述,剛度差、結(jié)構形狀的復雜性、生產(chǎn)方式及規(guī)模等諸多方面考慮,DEUTZ1013柴油機曲軸的工藝路線要細致周密,工序繁多。其中,磨削占主要工序。
綜上,DEUTZ1013柴油機曲軸技術要求很高。如何提高生產(chǎn)率和生產(chǎn)中如何實現(xiàn)高效率自動化是一個待解救問題。
3.3.2 定位基準
由上述DEUTZ1013曲軸工藝特點分析知,剛度、形狀的復雜度以及各運動件運動關系,定位基準的選擇尤為重要,直接影響著零件的尺寸精度、形變量等。主要加工面包括:端面、端軸頸、主軸頸、曲軸臂以及連桿軸頸等等。由于結(jié)構的特殊性,主軸及連桿軸頸的軸線不在一條線上,所以在加工時應注意以連桿軸頸為基準。
⑴基準選擇原則
①粗基準
a、基準面盡量選擇精確度高的表面
b、余量分配均勻
c、非加工面作粗基準時,選擇位值誤差盡量小的表面。
d、使用原則不可重復
e、粗基準面盡可能光潔,面積足夠大利于裝甲。
②精基準
a、基準不變原則,即統(tǒng)一基準。
b、基準重合原則,即設計基準和定位基準重合。
c、自為基準原則,即對工件兩個相互位置精確度要求高的表面相互為基準。
⑵基準的選擇
①主軸頸及同軸心軸頸
設計基準:主軸頸中心孔
定位基準:對于主軸頸和同軸心軸頸,既要遵循基準選擇原則又要保證軸端面和軸的精確度,選用中心孔定位。首先,先銑端面和中心孔(先粗銑再精銑)。為保證DEUTZ1013曲軸毛坯外徑的軸線與中心孔重合主,故以毛坯外圓端面為粗基準;為減少系統(tǒng)誤差和測量誤差,把3號主軸(中間軸)作為粗基準,余量兩端對稱分配。這樣保證了徑向和軸向余量分布的均勻性。
②連桿軸頸
曲柄臂平面的兩個工藝平面作為輔助精基準,工藝平面距離主軸頸軸心與連桿軸的連線根據(jù)尺寸公差表查出公差值,保證各個方向余量的分布。
連桿的精加工,既要滿足連桿軸曲柄半徑值和主軸的不平衡度又要遵循基準選擇原則,所以選用磨削過的最遠端的主軸作為精基準。這樣一方面便于安裝,滿足技術要求并且形變量??;另一方面連桿軸不在同一平面,1號軸和5號軸裝有定位銷,故運動受限。
對于各軸頸的軸向尺寸公差,定位基準通常采用主軸任意一個端面。
3.4 工藝路線
3.4.1 機械加工工序安排
⑴先基準后其他
⑵先平面后孔
⑶先粗后精
⑷先主后次
3.4.2 確定工藝路線
⑴加工基準面
⑵車、半精車主軸頸
⑶粗車、半精車連桿頸
⑷鉆、擴定位銷孔
⑸鉆擴齒輪定位銷
⑹檢查
⑺感應淬火
⑻校正
⑼粗磨、精磨主軸頸
⑽粗磨、精磨連桿軸頸
⑾鉆油孔
⑿檢查
⒀鉆軸端孔
⒁動平衡、去重
⒂拋光
⒃檢查
3.4.3 DEUTZ1013曲軸表面加工方法的選擇
DEUTZ1013曲軸加工面有端面、質(zhì)量中心孔、主軸頸、螺紋、連桿軸頸、中心孔及鍵槽等。
⑴Φ86mm大端軸頸:尺寸公差 表面粗糙度Ra0.8μm,公差等級為IT6。需粗車→半精車→磨削。
⑵Φ71主軸頸:尺寸公差 公差等級為IT5,表面粗糙度Ra0.4μm。
需粗車→半精車→粗磨→半精磨→精磨。
⑶Φ60連桿軸頸:尺寸公差公差等級為IT6,表面粗糙度為Ra0.4μm。
⑷兩端Φ25質(zhì)量中心孔:無尺寸公差,公差等級為IT7,表面粗糙度為Ra6.3μm。需鉆。
⑸小端螺紋M24×1.5:直徑為Φ24,無尺寸公差要求,表面粗糙度為Ra6.3μm。螺紋需攻。螺紋直徑需粗車→半精車→精車。
⑹兩端端面:本零件為軸端端面,故無尺寸公差要求,表面粗糙度為Ra6.3μm。
⑺Φ64小端軸頸:尺寸公差公差等級為IT11,表面粗糙度為Ra6.3μm。需粗車→半精車
⑻Φ43齒輪軸軸頸:尺寸公差 公差等級為IT7,表面粗糙度為Ra0.8μm。需粗車→半精車
⑼Φ16齒輪軸鍵槽:尺寸公差 公差等級為IT12,表面粗糙度為Ra3.2μm。需粗銑→半精銑。
⑽大端M14×1.5-6H螺紋孔,無尺寸公差,表面粗糙度為Ra3.2μm。需鉆→擴→攻。
3.4.4 最終工藝路線
⑴工序
工序10:粗銑兩端端面
工序20:半精銑兩端端面
工序30:鉆Φ25質(zhì)量中心孔
工序40:粗車Φ86大端軸頸
工序50:粗車5號主軸頸→粗車第八曲臂止推臺階
工序60:粗車M24×1.5螺紋直徑→粗車Φ43齒輪軸軸頸→粗車Φ64小端軸頸 →粗車1號主軸頸→第一曲臂止推臺階
工序70:粗車封油軸頸→齒輪軸直徑→螺紋直徑
工序80:半精車1號、5號主軸頸→半精車M24×1.5螺紋直徑→車推刀槽
工序90:粗銑→半精銑第一曲臂對稱定位面
工序100:粗銑、半精銑2~4號主軸頸→擋寬→止推臺階→粗銑、半精銑1~4號連桿軸頸→擋寬
工序110:人工時效
工序120:粗磨全面主軸頸→2~5號主軸擋寬→1號主軸擋寬
工序130:半精車大端端面→鉆、擴大端端面孔
工序140:半精車大端軸頸→半精車小端軸頸→刀檢2、3曲柄臂
工序150:鉆大端Φ10×18定位銷
工序160:粗磨連桿軸頸→粗磨擋寬→粗磨行程
工序170:槍鉆Φ7油道孔→槍鉆Φ8斜油孔
工序180:油孔噴沙
工序190:中檢
工序200:中間清洗
工序210:熱處理
工序220:中間探傷
工序230:精車Φ43齒輪軸軸頸→精車M24×1.5螺紋直徑
工序240:半精磨2~4號主軸頸→半精磨擋寬
工序250:半精磨1、5號主軸頸→半精磨擋寬
工序260:精磨Φ86大端軸頸
工序270:精磨1、4號連桿軸頸→精磨2、3號連桿軸頸
工序280:粗銑、半精銑齒輪軸鍵槽
工序290:精磨1、5號主軸軸頸→擋寬
工序300:精磨2~4號主軸軸頸→擋寬
工序310:精車大端端面→大端倒角→精車螺紋端面→主軸頸倒角
工序320:中檢
工序330:成品探傷
工序340:鉆、擴、攻大端螺紋孔→攻小端螺紋
工序350:油孔倒角、全部油孔拋光
工序360:動平衡測試
工序370:清理毛刺
工序380~390:拋光
工序400:成品檢查
工序410:入庫
3.5 計算余量及設計毛坯圖
3.5.1 計算機械加工余量
鍛造工件的加工余量,根據(jù)鍛件的形狀復雜系數(shù)、質(zhì)量及表面粗糙度等和孔的加工余量,都查表得之。
⑴鍛件的質(zhì)量。根據(jù)毛坯估算其值約為20kg。
⑵鍛件形狀復雜系數(shù)s
設毛坯件長650mm,直徑Φ170mm
查表知,形狀復雜系數(shù)為,較復雜級別。
⑶鍛件加工表面粗糙度參考值Ra≥0.4μm。
⑷對于機械加工余量,查表知各個軸頸余量為0.25~0.5;其他加工面余量為0.5~6。
⑸由于是批量生產(chǎn)并且為提高生產(chǎn)效率、毛坯質(zhì)量,這里采用模鍛。
3.5.2 設計毛坯圖
⑴毛坯公差尺寸的確定
毛坯的公差尺寸要依據(jù)鍛件質(zhì)量m、形狀復雜系數(shù)s、鍛件材質(zhì)系數(shù)以及分模線形狀種類,查表得之。
表3.5.1 DEUTZ1013曲軸毛坯尺寸
零件尺寸
單面加工余量
鍛件尺寸
Φ71
Φ60
Φ86
Φ64
Φ43
Φ24
633.5
54.5
33
46.5
76
38
19
1.5
4
1
2
3.4
4.4
3.5
0.6
0.46
0.4
0.6
4
0.5
Φ73
Φ61.7
Φ95
Φ66
Φ46.4
Φ32
637
55.1
33.46
46.9
76.6
42
19.5
鍛件形狀復雜系數(shù)、鍛件質(zhì)量,42CrMoA的C含量為0.38~0.45%,查表得鍛件材質(zhì)系數(shù)為,采用不對稱彎曲分模線。錯差公差查表的1.4mm,殘留飛邊公差查表的1.4mm。
表3.5.2 毛坯尺寸公差
鍛件尺寸
偏差
依據(jù)
厚度
637
31
+3.3
-1.7
+1.9
-0.9
《機械制造工藝設計簡明手冊》
表2.2-14
內(nèi)表面
Φ66
+1.9
-0.9
外表面
Φ73
Φ61.7
Φ95
Φ46.4
Φ32
+1.9
-0.9
+1.9
-0.9
+2.1
-1.1
+1.9
-0.9
+1.7
-0.8
臺階
55.1
76.6
+1.9
-0.6
+1.9
-0.6
《機械制造工藝設計簡明手冊》
表2.2-16
⑵毛坯圖
3.6 加工裝備選擇及安排
3.6.1選擇機床
⑴選擇機床注意事項
①加工面的精度和機床精度相符合。
②選擇機床時,應盡可能發(fā)揮機床作用及負荷平衡。
③選擇與工件尺寸、形狀相符合的機床規(guī)格。
④這里選擇的生產(chǎn)方式為大批量生產(chǎn),故應選高產(chǎn)率的機床。
⑵選擇機床
①具體機床選擇
1) 工序10~20是粗銑和半精銑,各個工序步驟少且為大批量生產(chǎn),零件的外廓尺寸適中并且精度要求 適中,因此選用ZBT8261型臥式雙面銑床。
2) 質(zhì)量中心孔尺寸小,它的精度要求適中,故選擇SM-002質(zhì)量定心機。
3) 工序40~90主要是粗車,所以精度要求不是很高且加工零件是回轉(zhuǎn)體,故選CW6163型臥式車床。
4) 工序100~120需要半精車,精度要求比較高,考慮到尺寸及加工要求,選用V36數(shù)控車床。
5) 工序130為銑第一曲臂定位基準面,所以要求精度精準,另外還需要去除毛刺,故選X1532單柱臥式銑床。
6) 工序130~150只要為內(nèi)銑,加工復雜,表面粗糙度小,精度要求高,故選GPM240F2-3型內(nèi)銑機床。
7) 工序170為磨削及工序28中的1號、5號主軸頸,精度要求高,故選擇MQ1350型外圓磨床。
8) 工序190~210主要為半精車,考慮到鍛件材質(zhì)等,選用CA6140型普通車床
9) 工序220定位銷,需用專門的定位銷孔專機,這里選用的型號為JS274。
10) 工序230為內(nèi)部粗磨,加工復雜,要求精度高,故選MQ8260型外圓磨床。
11) 工序240,對于加工油孔,需用專門的油孔專機,這里選用MS-U028型油孔專機。
12) 工序260~270及350~380主要為精車,因此精度要求高,故選C620普通車床。
13) 工序280~290主要是精磨,表面粗糙度較小,宜用磨床,故選H173數(shù)控外圓磨床。
14) 工序300~310工序為內(nèi)部精磨,所以加工復雜,故選5SEGV100C型外圓磨床。
15) 工序320齒輪軸鍵槽,加工尺寸小,考慮到加工面,故選X6020B臥式升降臺銑床。
16) 工序330,由于1號、5號主軸頸在兩端外部,考慮到結(jié)構,故選TOYODAGL100MT數(shù)控外圓磨床。
17) 工序340,2~4號主軸頸在中間,由于結(jié)構復雜性,故選TOYODAGL7P數(shù)控外圓磨床。
18) 工序390~400主要為鉆孔等,加工復雜,為了保證精度,故選YNC-027雙端面加工中心。
3.6.2 量具的選擇
由于生產(chǎn)方式是批量生產(chǎn)模式,故通常選用通用量具。這里采用按計量器的測量方法極限誤差選擇。
如粗磨各Φ71主軸頸,查表得T=0.05,K=0.25,極限誤差為12.5
表3.2 加工面所用量具
加工面尺寸
尺寸公差
量具
Φ86
0.022
測量范圍0~300的游標卡尺,測量范圍0~125的游標卡尺,分度值為0.02
Φ71
0.013
Φ64
0.2
Φ60
0.02
Φ43
0.025
633.5
0.3
分度值為0.1,測量范圍0~1000的游標卡尺
554
0.3
74
0.3
分度值為0.05,測量范圍0~150的游標卡尺
55
0.3
38
0,2
33
0.2
30
0.2
19
0.2
25
0.03
分度值為0.05,測量范圍0~100的深度千分尺
3.6.3 選擇夾具
夾具的設計與使用有提高產(chǎn)率、擴大機床使用范圍、保證加工制造的質(zhì)量及減緩勞動力很大作用。另外,夾具的正確使用還有促進精密零件的掌握情況和解決繁多復雜的工藝等等。具體分析請見后面夾具設計。
3.6.4 刀具選擇
選擇刀具的過程主要包括刀具材料、構造及類型??紤]因素主要包括:加工精度、粗糙度、加工方法、生產(chǎn)率、經(jīng)濟性及加工件形狀等等。
原則是主要采用標準刀具,特殊情況采用專用刀具。
⑴銑端面工序選用YT15右車刀;粗車工序:粗車大端軸頸、5號主軸頸、螺紋直徑、齒輪軸軸頸、小端軸頸1號主軸、第一曲臂止推臺階、封油軸頸,及半精車工序:半車大端端面,查表后選用右車刀YT15;考慮到加工精度及角度等因素,半精車兩端軸頸選用右車刀YT15;精車小端螺紋端面選用右車刀。
⑵粗車5號主軸頸以及曲臂止推臺階采用專用車刀。
⑶在數(shù)控車是。車1號、5號主軸頸、小端軸頸及其推刀槽時,選用多方向切割桿車刀、機夾刀片。
⑷精車螺紋直徑以及齒輪軸直徑,分別選用機夾刀和機夾刀。
⑸精車大端端面采用專門的端面車刀YT30。
⑹銑第一曲臂基準面,由于精度要求高,選用機夾銑刀盤。
⑺內(nèi)銑2~4號主軸及連桿軸頸,選用主軸刀盤和連桿軸刀盤。
⑻粗磨工序。粗磨主軸頸選用P750×34×305A46M6V35砂輪;連桿軸頸選用P900×35×305A46M6V35。
⑼半精磨工序。2~4號主軸頸,選用P11×34×305A46M6V35;1號和5號主軸頸P750×33×305A46M6V35。
⑽精磨工序。大端軸頸選用P900×50×305A46M6V35;連桿軸頸p1100/1065×34×35砂輪;1號和5號主軸頸選用P500×350×30CBN砂輪;2~4號主軸頸選用P915×34×305砂輪
⑾銑齒輪鍵槽,查表知采用B16×5、齒數(shù)8的半圓鍵槽銑刀。
⑿鉆質(zhì)量中心孔選用B6.3/20中心鉆;鉆大端定位銷選用錐柄麻花鉆Φ10鉆、擴、攻;大端螺紋孔分別采用Φ12.5×60×107鉆頭、Φ12.5擴孔鉆、M14×1.5絲錐;槍鉆油道孔Φ7選用Φ7槍鉆;直油孔劃窩Φ10及Φ8,深度2,根據(jù)查表選用劃窩鉆;槍鉆連桿軸斜油孔Φ6選用Φ6槍鉆。
3.6.2 工序尺寸確定
通常來說,確定工序尺寸的方法為由后推前,既有最后加工工序先前推,零件尺寸標注要按工序尺寸標注?;A不重合時,選擇工藝尺寸鏈計算;無轉(zhuǎn)換基礎時,同一加工面的工序尺寸只與加工余量相關。
規(guī)定寬度為垂直刀具的方向;長度為沿刀具的方向。
注:工件為回轉(zhuǎn)體或者加工圓面時,長度等于寬度。
例如圖3.6.1,由寬度知,工件直徑小于刀劍直徑可方便進行銑削。機動時間通過切入超出、長度來確定。
圖3.6.1
注:加工圓面時,對于車、磨等其他工序直徑為未加工時的尺寸;長度為工件進給的尺寸。
動機時間(基本時間)由加工面的切入超出、長度確定,關于切入超出的詳細計算在后面進行詳細論述。
3.7 切削用量與基本時間確定
⑴工序10。本工序為粗銑和半精銑,加工材料為42CrMoA,鍛件。機床為ZBT8261型臥式雙面銑床,專用夾具裝夾。
①確定粗銑兩端面的切削用量 選用刀具為材料W18Cr4V、=50mm、齒數(shù)z=10,查表知,,,,。
a.確定切削深度
考慮到公差和模鍛斜度等,可以走到次數(shù)為1,則
確定進給量f。查表知,=3.5,故進給量f范圍為0.03~0.3mm/r。根據(jù)根據(jù)直徑,取進給量f=0.068mm/r。根據(jù)進給量f,查表得切入和超出量為24,f=34mm/min。
b.確定切削速度。
其中,t-刀具耐用度
f-進給量
-切削深度
根據(jù)上面表格,查得t=200。代入上面公式,解得v251min/s。
在計算轉(zhuǎn)速 n=497,
按ZBT8261型臥式車床轉(zhuǎn)速表查得,n=500
注:根據(jù)實際情況,驗算是否在主軸轉(zhuǎn)數(shù)的級數(shù)之內(nèi),理論值是否可以達到,根據(jù)相應機床轉(zhuǎn)速表選擇相近數(shù)值即可。
c.計算切削力。
查表的切削力
其中-側(cè)吃刀量
-進給方向吃刀量
- 背吃刀量
Z-銑刀齒數(shù)
-銑刀直徑
故=9,81×101×××10×=5.50N
②基本時間
a.單個工件的時間組成如下,
其中, —服務時間是指工作地方的時間。如刀具的更換和變調(diào)、去除切削、等。一般可按照=(3.0%~5.0%)估算。本次工藝卡填寫按照5%估算。
—基本時間。因為這里設計的加工工序,故也叫機動時間。機動時間是直接影響加工零件的尺寸、形狀、表面質(zhì)量等方面的時間變化值。
—輔助時間。在保證基礎時間的基礎上,完成輔助動作所用的時間。如測量、操作機床、裝卸工件、切削用量的變化等等。此時間可查表選擇,也可依據(jù)公式=(10.0%~20.0%)計算。這里按照10.0%估算。
—準備與終結(jié)時間。在了解工件內(nèi)容、領取毛坯、選擇并安裝設備等一系列工作中,一個工序完成后單件額定時間不計入其中。由于這里生產(chǎn)方式為批量生產(chǎn),所以為零。
b.基本時間計算
其中,—加工長度(mm)
—加工切入(mm)
—加工超出(mm)
===3.50
將=3.50代入下列式中,
=0.1×=0.350
=0.05×=0.181
=3.50+0.350+0.181=4.03min
故,=3.55min
圖3.7.1 銑端面
⑵工序20。本工序為半精銑,加工材料為42CrMoA,鍛件。機床為S3X-5021型臥式雙面銑床,專用夾具裝夾。
①半精銑兩端的切削用量 選用刀具為材料W18Cr4V、=50mm、齒數(shù)z=10,查表知,,,,。
a.確定切削深度
考慮到公差和模鍛斜度等,可以走到次數(shù)為1,則
b.確定進給量f。查表知,=2,故進給量f范圍為0.12~0.18mm/r。根據(jù)根據(jù)直徑,取進給量f=0.18mm/r。根據(jù)進給量f,查表得切入和超出量為24,f=0.30mm/min。
c.確定切削速度。
根據(jù)(1)中耐用度表格,查得t=200。代入上面公式,解得v=113min/s。
在計算轉(zhuǎn)速 n=181,
按S3x-5021型臥式車床轉(zhuǎn)速表查得,n=180
d.計算切削力。
其中-側(cè)吃刀量
-進給方向吃刀量
- 背吃刀量
Z-銑刀齒數(shù)
-銑刀直徑
故=9,81×101×××10×=2.81N
②計算基本時間
其中,—加工長度(mm)
—加工切入(mm)
—加工超出(mm)
===3.46
將=3.46代入下列式中,
=0.1×=0.346
=0.05×=0.173
=3.46+0.346+0.173=3.979min
=3.66min
⑶工序30。
鉆兩端質(zhì)量中心孔。切削用量=3,進給量=0.08mm/r,=40mm/min,轉(zhuǎn)速n=500,切削速度=9.4m/min。=0.53。
⑷工序40。
粗車大端軸頸。 切削用量=4.5,進給量f=0.3mm/r,f=53.4mm/min,轉(zhuǎn)速n=178,切削速度=57m/min。=1.32。
⑸工序50。
粗車第八曲臂止推臺階。切削用量=3.5,進給量f=0.54mm/r,f=71.3mm/min,轉(zhuǎn)速n=132,切削速度36=m/min。=0.68。
粗車5號主軸頸。切削用量=3.5,進給量f=0.54mm/r,f=71.3mm/min,轉(zhuǎn)速n=132,切削速度=36m/min。=0.68。
其余工序參數(shù)值請見工序卡。
4 機床夾具
4.1 夾具分析
4.1.1 夾具功能
⑴加工時確保精度。加工工件是通過夾具來固定、加工。加工的精度通過兩個方面來保證。一方面,運用定位元件確定準確位置;另一方面,運用加緊機構來保證加工過程中零件的固定。
⑵提高工件產(chǎn)率。夾具的使用可以大大的減少輔助時間,如對刀、劃線、找正等。
⑶即加強了安全,又減小了勞動強度。
4.1.2夾具設計分析
夾具的分類方式主要依據(jù)其特點和機床。依據(jù)機床可包括鏜床夾具、車床夾具及鉆床夾具等;銑床夾具依據(jù)使用特點可包括:可調(diào)夾具、組合夾具、通用夾具及專用夾具等。本設計為批量生產(chǎn),故多用專用夾具。(專用夾具:為加工工件某一工序而專門設計的夾具,通常用在批量生產(chǎn)中)
關于裝夾方法,一是先在圖樣上劃線,再在裝夾的時候通過指示表或者劃針找正之后,再裝夾于工作臺(或者花盤)上。這種裝夾方式通常用于小批量(或者單件)生產(chǎn);二是加工工件通過夾具再安裝在機床上。這種方式一般適用于成批量(大批量)生產(chǎn)中。
4.1.3確定定位與夾緊方案
這里采用的是無需反復定位的夾具,這樣可以大大地提高了生產(chǎn)率。因為5號軸、1號軸的軸心與銷孔中心線共線的原因,所以定位時主軸中心及1、4曲拐是關鍵。
依據(jù)定位夾緊的選擇原則以及確保定位銷的順利加工,定位曲拐中心時,選用自動定心夾緊裝置,用主軸中心軸線定位來限制旋轉(zhuǎn)方向自由度;主軸軸線選用兩端頂尖定位孔,采用的是活頂尖,因此可以限制4個自由度;大端端面緊靠夾具體,軸向自由度可以限制。它的工作原理是先把工件預定,通過液壓控制使夾緊機構中上下夾板以相同速度向中心運動,使得主軸中心線與機床中心線組成的平面一直和夾具面始終平行。機構優(yōu)點是無論曲軸軸徑尺寸是否精準,都不會產(chǎn)生影響。
軸向旋轉(zhuǎn)定位選擇5號曲軸,這樣可以使切削力與夾緊點距離更近,直徑大的軸離定位點遠,可以使加工精準。
4.1.4夾具設計
⑴預定位
正式定位之前,要先進行工件預定位。預定位元件選擇的是圓柱形擋棍及兩個短V形塊。擋塊放于1號曲拐下處,短形V形快放在2、4號主軸頸處,三者要略低于曲軸下面。
⑵主軸中心線定位與夾緊
①定位
主軸中心線定位方式選用頂尖定位,頂尖選擇浮動頂尖。定位裝置用液壓控制,左端液壓缸直徑比右端直徑小,二者工作時運動方向是從右向左推進,大端端面靠近夾具體,從而限制方向自由度。
②夾緊
夾緊機構選擇自動化夾緊機構,通過等速位移來消除尺寸誤差。
⑶曲軸定位與夾緊
①定位
在整個設計制造中,最重要且最有難度的是曲軸定位加工。因為曲軸的中心 線與主軸回轉(zhuǎn)中心線不同,定位元件選擇錐度心軸,限制以及Y、Z的旋轉(zhuǎn)。
②夾緊
曲軸夾緊裝置選擇自動夾緊裝置。通過兩夾板將將工件向軸心雙向夾緊以保證孔的加工精度。兩個夾板分別在兩個絲杠上,絲杠螺紋的旋向相反,絲杠由二級齒輪來傳遞。其中,第一級齒輪是通過與液壓缸活塞相連的齒條傳遞,齒條被活塞推動作往復運動,,再由齒輪傳遞給絲杠。如圖4.1.1所示。
圖4.1.1
注:夾緊機構基本條件:夾緊時,工件既要保持既定位置不變又要不離開定位支撐。夾緊力的選擇要保證工件的定位又要避免工件變形、位移及振動,保證夾緊行程順利進行。自動化夾緊機構中的自動化程度、復雜程度要與成產(chǎn)方式相匹配。
4.1.5夾緊行程確定
本設計采用的夾緊機構是由液壓缸控制,所以與活塞桿有密切聯(lián)系。預定位時存在距離差,差值為4。為消除差值在兩個夾板處移動6。故絲杠中二級齒輪模數(shù)M為2;齒數(shù)為18、58、21。
故第二級齒輪轉(zhuǎn)數(shù):
第二級齒輪轉(zhuǎn)過距離: =40.91
4.1.6計算夾緊力
①確定夾緊力
夾緊力是依據(jù)切削力估算得出來的,所以計算夾緊力的時候結(jié)合切削力以及夾緊力結(jié)構列出靜平衡方程,求出安全系數(shù)k,進而求出實際夾緊力。在計算時,要把夾具和加工工件看作統(tǒng)一的剛性系統(tǒng),工件受力情況要在切削力方向、大小和作用點最不利的情況考慮。
其中,—計算夾緊力
—實際夾緊力
K—安全系數(shù)
其中,一般安全系數(shù)
—加工性質(zhì)系數(shù)
—刀具頓化系數(shù)
—斷續(xù)切削系數(shù)
查《機械制造裝備設計》表格,計算k=2.5
粗加工鉆孔時力矩最大,可以求出和
其中,M—切削扭矩
f—進給量
—修正系數(shù)
—鉆頭直徑
由于工件材料為結(jié)構鋼、刀具材料為高速鋼,所以代入上式得:
=1.233
綜上,將代入解得:
圖4.1.2 受力分析
列靜平衡方程
→
其中,N=2840N
列力矩平衡方程
→
其中,
解得
其中,
②檢驗
計算最大夾緊力P
其中,
注:工作壓力p取值范圍為1.0~5.0,這里取3.5
將以上計算值代入上式解得
綜上,符合設計要求。
4.2 夾具裝配
⑴整體裝配
二級傳動齒輪中的齒條與活塞桿連接后,再把二級齒輪裝配于齒輪箱,齒輪軸再和絲杠相連。將液壓缸緊固于夾具。先把油缸底座、鉆模支架套安裝在夾具之上,再把頂尖放于二者之上后裝入鉆模。最后安裝擋塊和短V形塊。
安裝檢查后再把夾具緊固于機床上。
⑵局部裝配
將圓螺母和壓板與齒輪軸和齒條兩兩相連,完畢后連接齒條。齒輪軸上的推力軸承與絲杠安裝完畢后與夾具固定。
4.3 夾具經(jīng)濟性能
在夾具設計過程中,除了要考慮工藝方面的性能,也要對經(jīng)濟性進行分析。
⑴控制裝置應多選取機動控制裝置而非手動裝置,這樣有利于提高產(chǎn)率、減輕勞動力;也有利于實現(xiàn)遠端控制。
⑵夾具中應多選用標準件,這樣有利于降低成本;也有利于避免更換零件時的重復設計,從而減少更換用時。
⑶夾具設計時盡量使精加工面面積最小,以降低成本。
5 檢驗零件
5.1 氣動量儀
曲軸的主軸頸用用氣動量儀檢測,如圖5.1.1所示為氣動量儀的工作原理。過濾壓縮的空氣通過穩(wěn)壓室1經(jīng)由主噴嘴2進到測量氣室內(nèi),從輸出管道6溢出,這樣管內(nèi)壓強產(chǎn)生變化。利用U形管的前后差值,反應管內(nèi)壓強變化值,繼而間接測量出主噴嘴處流速的變化值,其函數(shù)關系式為P=f(S)。其數(shù)值通過刻度尺9來記錄。
圖5.1.1
5.2氣動卡規(guī)
該器件用作曲軸生產(chǎn)之用,如圖所示。被測工件的尺寸變化產(chǎn)生的彈性形變使噴嘴1二者之間間隙發(fā)生變化,變化值通過氣動量儀的刻度尺記錄。
5.3檢驗夾具
首先,先把曲軸放于支架1、5之上,皮帶輪端的頂尖孔用頂尖6頂住。使3號主軸頸的右端臺肩靠在軸向定位件3處,通過百分表9記錄數(shù)據(jù)。
圖5.3.1
6 結(jié)論
通過DEUTZ1013柴油機曲軸加工工藝規(guī)程設計,使我感受頗多。由于學校組織安排實習的地方是大連機車車輛有限公司,參觀過生產(chǎn)曲軸的車間。因此可以讓我和生產(chǎn)實踐可以完美結(jié)合,在現(xiàn)有工藝基礎上并結(jié)合前端科技技術,設計更高產(chǎn)率、更小勞動強度的工藝。結(jié)合在實習期間做的筆記以及圖書館相關資料,還有最重要的是甄恒洲老師的耐心指導,讓我的規(guī)程設計得以順利的完成。
在設計中,充分體現(xiàn)了理論結(jié)合實踐的道理。首先,任何工序都必須要滿足可操作性。這個設計最大的特色是在現(xiàn)有條件基礎上融入先進生產(chǎn)技術模式。其次,這讓我把這四年學的全部知識可以綜合應用。耗時五個月的畢業(yè)設計讓我有有一個自己完整地獨立設計、思考機會,大到工序編排小到每個工步。這不僅是我學習的檢驗,也是我毅力的磨練!
參考文獻
[1]譚建芳,鐘安飛,楊浩等. 曲軸加工工藝的優(yōu)化[J].裝備制造技術,2004,(3):103-105,114.
[2]徐鵬宇. 曲軸機械加工工藝淺析[J].職業(yè)技術,2014,(6):94-94.
[3]楊洪武. 曲軸的加工工藝及工裝設計[J].中國化工貿(mào)易,2016,8(3):205-206.
[4]楊梓嘉. 基于機械加工的三拐曲軸加工工藝研究[J].機械工程師,2016,(3):86-87.
[5]李思樂,陳根,卞露英. 中速柴油機曲軸孔精鏜質(zhì)量控制[J].現(xiàn)代制造技術與裝備,2015,(3)77-79.
[6]李洪偉,劉旭,龐恭賀,王領. 典型曲軸零件加工工藝分析及專用銑夾具設計[J]. 工具技術,2016,(05):80-82.
[7]劉德嶺. 機車柴油機曲軸連桿頸隨動磨削工藝研究[J].機械研究與應用,2006,(05):173-175.
[8]吳紅亮. DF7柴油機曲軸設計開發(fā)[D].清華大學,2011.
[9]王軍. 中速柴油機曲軸關鍵加工工藝的研究[D].大連交通大學,2012.
[10]李波. 4V75柴油機曲軸系設計及CAE分析[D].湖南大學,2012.
[11]何睿,吳潔霞,賴立強,李躍朋,吳方圓,張云星. 發(fā)動機曲軸專利技術現(xiàn)狀研究[J].汽車工業(yè)研究,2015,(06):54-58.
[12]段紹林,毛澤永,宋利強. 曲軸機加工工藝與設備現(xiàn)狀及發(fā)展趨勢[J].內(nèi)燃機,2010,(02):27-30.
[13]王琛. 內(nèi)燃機曲軸強度的現(xiàn)狀和發(fā)展[J].科技創(chuàng)新與應用,2014,(18):84.
[14]Zissimos P. Mourelatons. A crankshaft system model for structural dynamic analysis of internal combustion engines. Computers & Structures, 2001,79(20-21): 2009-2027.
[15]Matin O’Driscoll Design for manufacture Journal of Materials Proccessing Technology,2002, 122:318~321.
[16]Tsai-C.Kuo,Samuel H. Huang,Hong-C Zhang, Design for manufacture and design for “X”:concept,applications,andperspectives,Computers&industrialengineering,2001,(141):241~260.
51
附錄1:外文翻譯
基于ANSYS的一二缸曲軸諧波分析
talikoti巴薩瓦拉杰醫(yī)師研究學者 機械工程系。K. Pillai博士M.瓦大學工程媒體研究,新本韋爾,馬哈拉施特拉,印度
S. N. Kurbet博士教授和機械工程帶頭人。機械工程系。basveshwar大學工程系,Bagalkot,卡納塔克邦,印度
V. V. Kuppast博士教授在機械工程。機械工程系。basveshwar大學工程,Bagalkot,卡納塔克邦,印度
Arvind M. Yadwad教授,機械工程系副教授,國家工程mysore-570008,卡納塔克邦研究所,印度
摘要---曲軸是內(nèi)燃機的主要部分,它在汽車工業(yè)中起著舉足輕重的作用。由于曲軸的失效造成巨大的損失,其市場的穩(wěn)定和可靠