【溫馨提示】壓縮包內(nèi)含CAD圖有下方大圖片預(yù)覽,下拉即可直觀呈現(xiàn)眼前查看、盡收眼底縱觀。打包內(nèi)容里dwg后綴的文件為CAD圖,可編輯,無水印,高清圖,壓縮包內(nèi)文檔可直接點(diǎn)開預(yù)覽,需要原稿請(qǐng)自助充值下載,所見才能所得,請(qǐng)見壓縮包內(nèi)的文件及下方預(yù)覽,請(qǐng)細(xì)心查看有疑問可以咨詢QQ:11970985或197216396
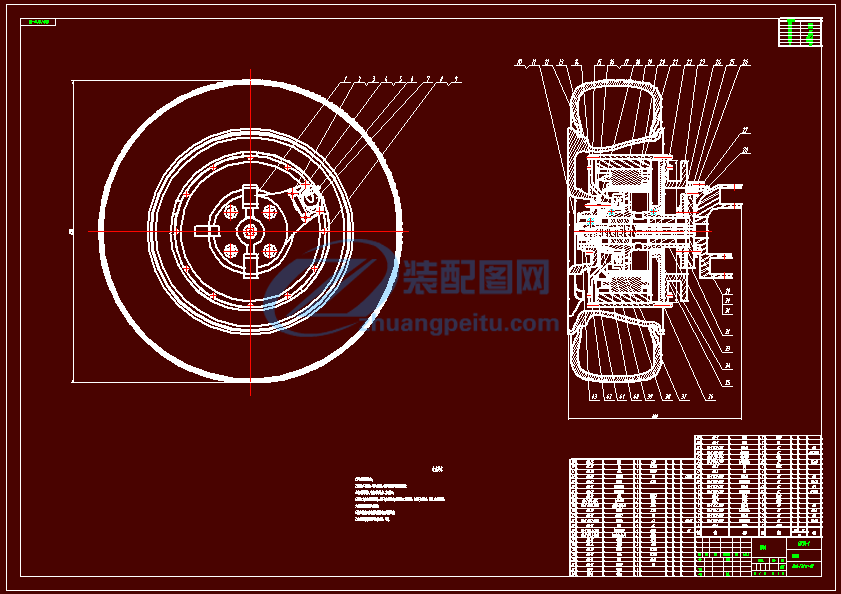

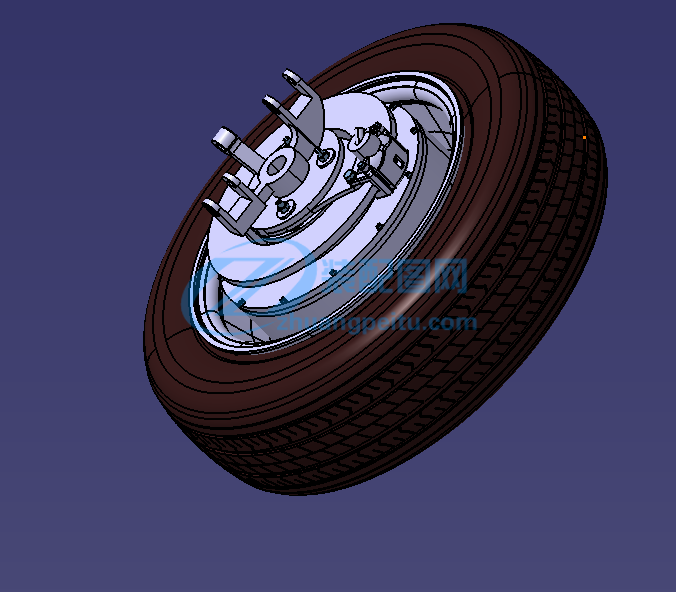
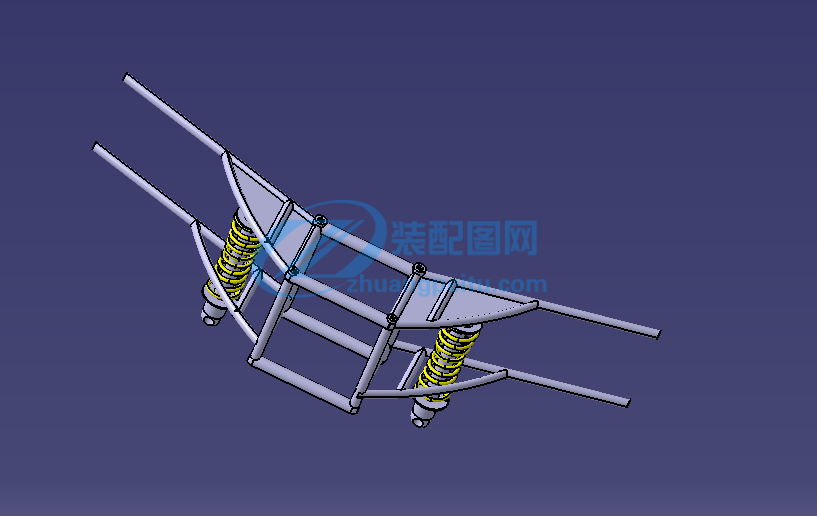

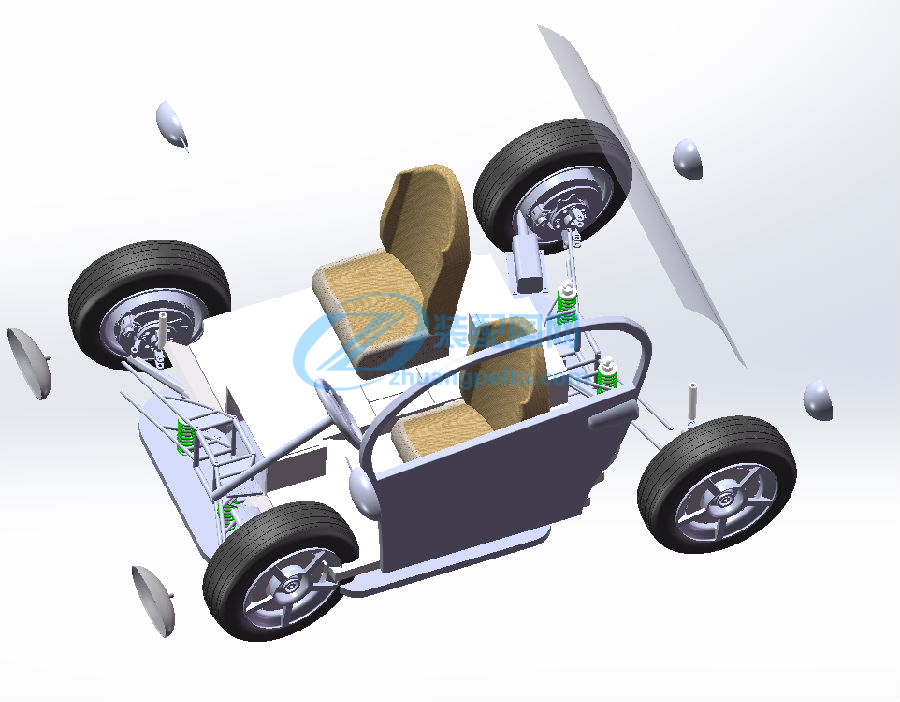
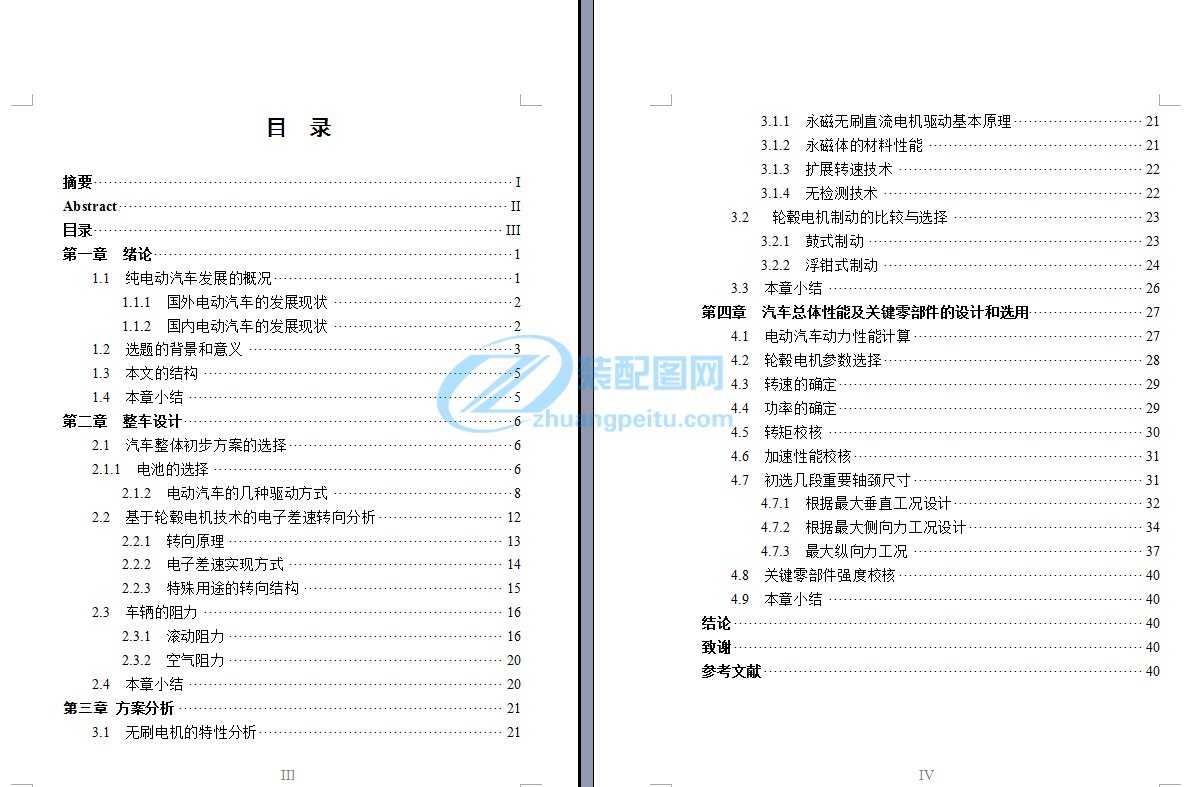

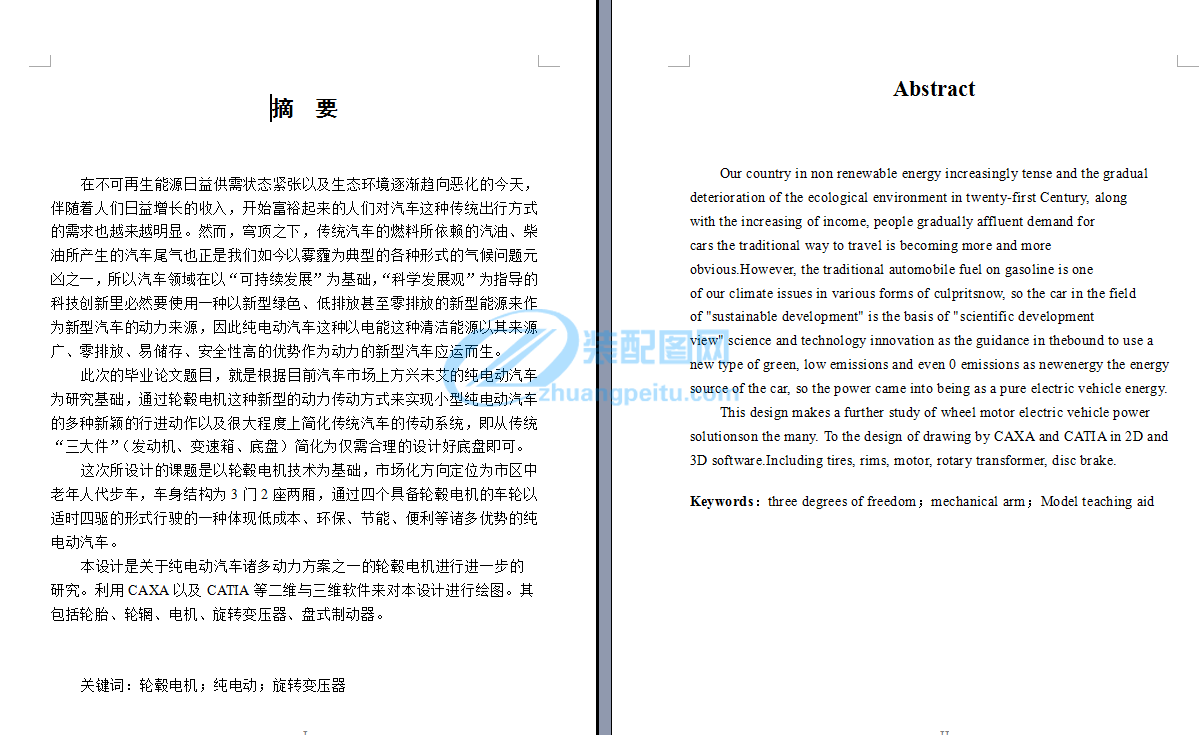
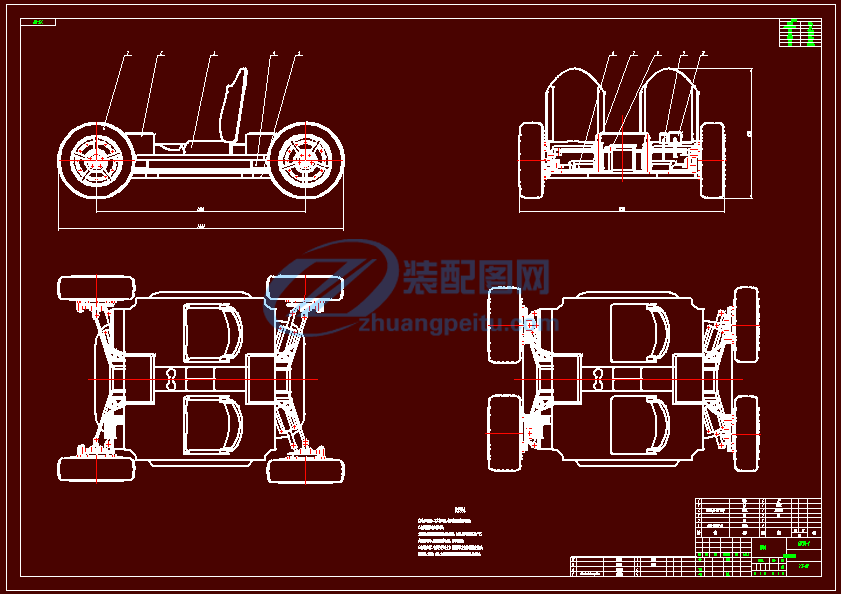
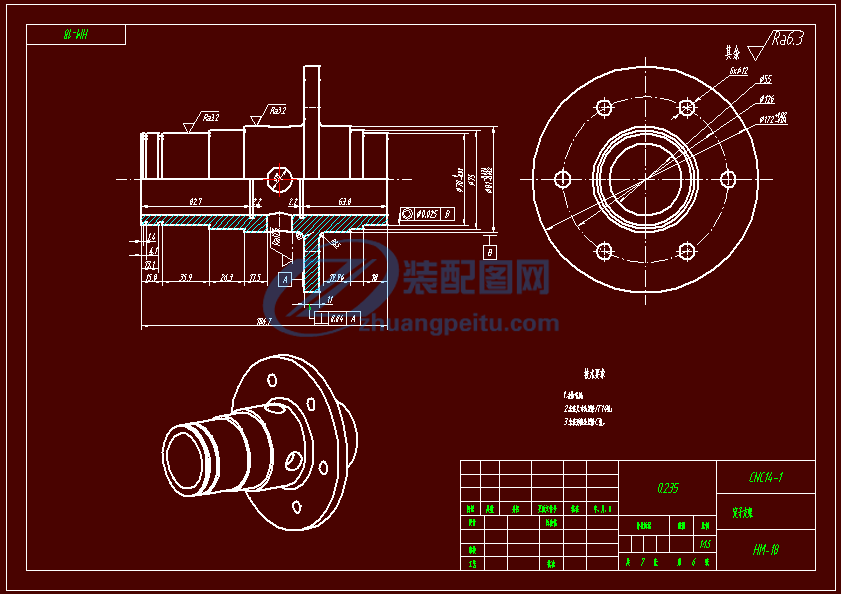

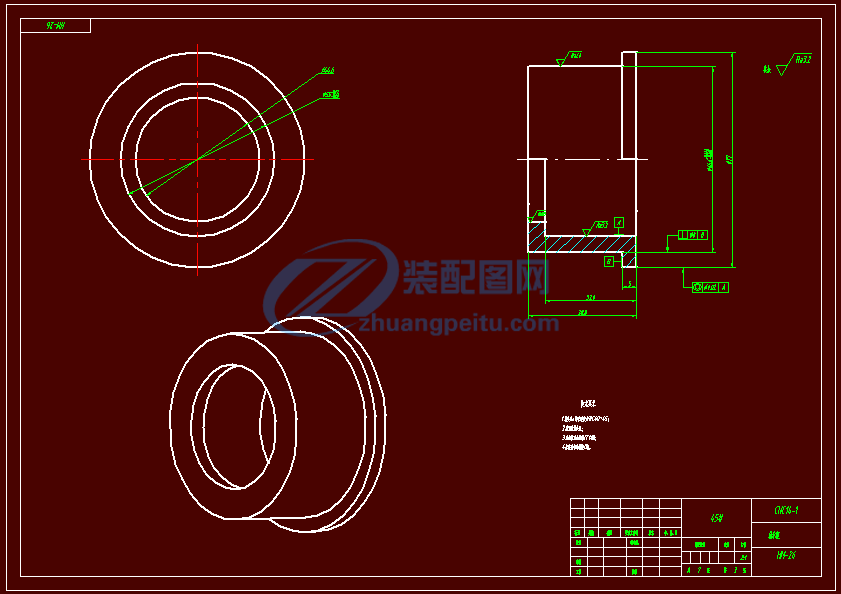
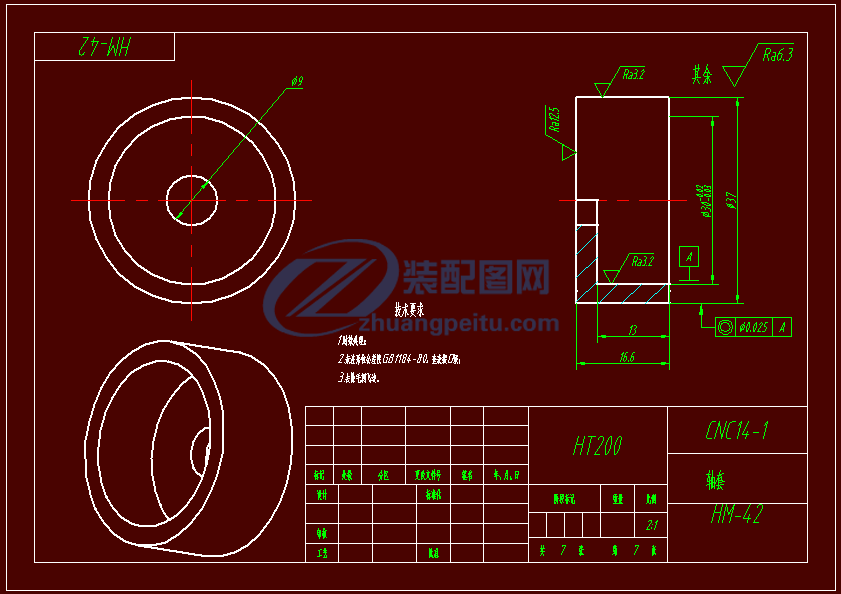
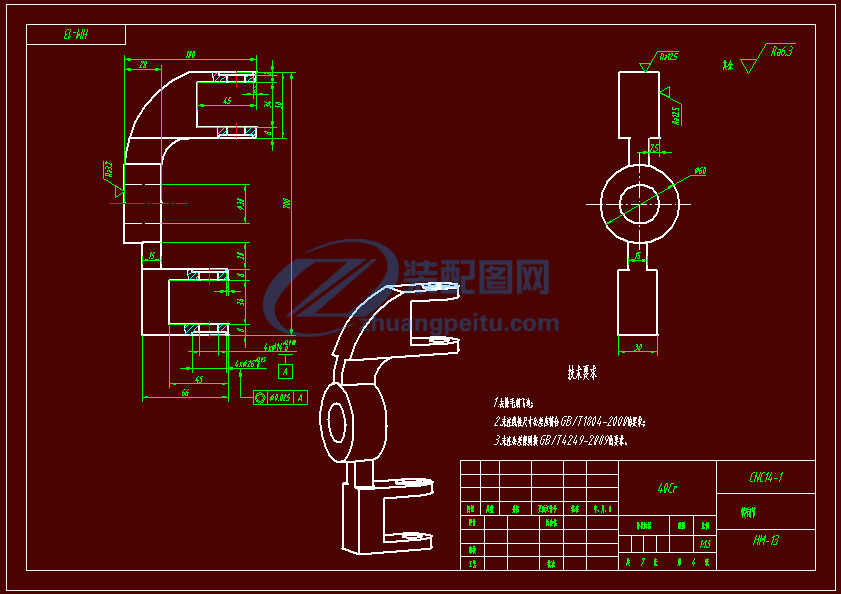
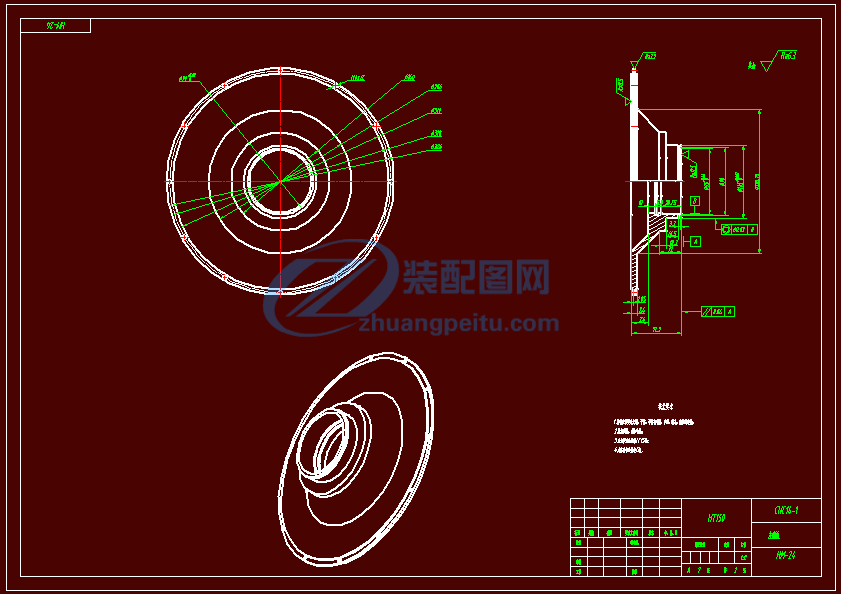
壓縮包內(nèi)含CAD圖紙和三維建模及說明書,咨詢Q 197216396 或 11970985
摘 要
在不可再生能源日益供需狀態(tài)緊張以及生態(tài)環(huán)境逐漸趨向惡化的今天,伴隨著人們?nèi)找嬖鲩L的收入,開始富裕起來的人們對(duì)汽車這種傳統(tǒng)出行方式的需求也越來越明顯。然而,穹頂之下,傳統(tǒng)汽車的燃料所依賴的汽油、柴油所產(chǎn)生的汽車尾氣也正是我們?nèi)缃褚造F霾為典型的各種形式的氣候問題元兇之一,所以汽車領(lǐng)域在以“可持續(xù)發(fā)展”為基礎(chǔ),“科學(xué)發(fā)展觀”為指導(dǎo)的科技創(chuàng)新里必然要使用一種以新型綠色、低排放甚至零排放的新型能源來作為新型汽車的動(dòng)力來源,因此純電動(dòng)汽車這種以電能這種清潔能源以其來源廣、零排放、易儲(chǔ)存、安全性高的優(yōu)勢(shì)作為動(dòng)力的新型汽車應(yīng)運(yùn)而生。
此次的畢業(yè)論文題目,就是根據(jù)目前汽車市場(chǎng)上方興未艾的純電動(dòng)汽車為研究基礎(chǔ),通過輪轂電機(jī)這種新型的動(dòng)力傳動(dòng)方式來實(shí)現(xiàn)小型純電動(dòng)汽車的多種新穎的行進(jìn)動(dòng)作以及很大程度上簡化傳統(tǒng)汽車的傳動(dòng)系統(tǒng),即從傳統(tǒng)“三大件”(發(fā)動(dòng)機(jī)、變速箱、底盤)簡化為僅需合理的設(shè)計(jì)好底盤即可。
這次所設(shè)計(jì)的課題是以輪轂電機(jī)技術(shù)為基礎(chǔ),市場(chǎng)化方向定位為市區(qū)中老年人代步車,車身結(jié)構(gòu)為3門2座兩廂,通過四個(gè)具備輪轂電機(jī)的車輪以適時(shí)四驅(qū)的形式行駛的一種體現(xiàn)低成本、環(huán)保、節(jié)能、便利等諸多優(yōu)勢(shì)的純電動(dòng)汽車。
本設(shè)計(jì)是關(guān)于純電動(dòng)汽車諸多動(dòng)力方案之一的輪轂電機(jī)進(jìn)行進(jìn)一步的研究。利用CAXA以及CATIA等二維與三維軟件來對(duì)本設(shè)計(jì)進(jìn)行繪圖。其包括輪胎、輪輞、電機(jī)、旋轉(zhuǎn)變壓器、盤式制動(dòng)器。
關(guān)鍵詞:輪轂電機(jī);純電動(dòng);旋轉(zhuǎn)變壓器
Abstract
Our country?in non renewable energy?increasingly tense?and the?gradual deterioration of the ecological environment?in twenty-first Century,?along with?the increasing?of income,?people?gradually affluent?demand for cars?the?traditional way to travel?is becoming more and more obvious.However,?the traditional automobile?fuel?on?gasoline?is?one of?our?climate issues?in various forms of?culpritsnow,?so the car?in the field of?"sustainable development" is the?basis of?"scientific development view"?science and technology innovation as the?guidance?in thebound to use?a new type of green,?low emissions?and even?0?emissions?as?newenergy?the energy source?of the car,?so?the?power?came into being?as a pure electric vehicle?energy.
This design?makes a further study?of?wheel motor?electric vehicle?power solutionson?the?many.?To?the design of?drawing?by CAXA?and CATIA?in 2D and 3D?software.Including?tires,?rims,?motor,?rotary transformer,?disc brake.
Keywords:three degrees of freedom;mechanical arm;Model teaching aid
目 錄
摘要 I
Abstract II
目錄 III
第一章 緒論 1
1.1 純電動(dòng)汽車發(fā)展的概況 1
1.1.1 國外電動(dòng)汽車的發(fā)展現(xiàn)狀 2
1.1.2 國內(nèi)電動(dòng)汽車的發(fā)展現(xiàn)狀 2
1.2 選題的背景和意義 3
1.3 本文的結(jié)構(gòu) 5
1.4 本章小結(jié) 5
第二章 整車設(shè)計(jì) 6
2.1 汽車整體初步方案的選擇 6
2.1.1 電池的選擇 6
2.1.2 電動(dòng)汽車的幾種驅(qū)動(dòng)方式 8
2.2 基于輪轂電機(jī)技術(shù)的電子差速轉(zhuǎn)向分析 12
2.2.1 轉(zhuǎn)向原理 13
2.2.2 電子差速實(shí)現(xiàn)方式 14
2.2.3 特殊用途的轉(zhuǎn)向結(jié)構(gòu) 15
2.3 車輛的阻力 16
2.3.1 滾動(dòng)阻力 16
2.3.2 空氣阻力 20
2.4 本章小結(jié) 20
第三章 方案分析 21
3.1 無刷電機(jī)的特性分析 21
3.1.1 永磁無刷直流電機(jī)驅(qū)動(dòng)基本原理 21
3.1.2 永磁體的材料性能 21
3.1.3 擴(kuò)展轉(zhuǎn)速技術(shù) 22
3.1.4 無檢測(cè)技術(shù) 22
3.2 輪轂電機(jī)制動(dòng)的比較與選擇 23
3.2.1 鼓式制動(dòng) 23
3.2.2 浮鉗式制動(dòng) 24
3.3 本章小結(jié) 26
第四章 汽車總體性能及關(guān)鍵零部件的設(shè)計(jì)和選用 27
4.1 電動(dòng)汽車動(dòng)力性能計(jì)算 27
4.2 輪轂電機(jī)參數(shù)選擇 28
4.3 轉(zhuǎn)速的確定 29
4.4 功率的確定 29
4.5 轉(zhuǎn)矩校核 30
4.6 加速性能校核 31
4.7 初選幾段重要軸頸尺寸 31
4.7.1 根據(jù)最大垂直工況設(shè)計(jì) 32
4.7.2 根據(jù)最大側(cè)向力工況設(shè)計(jì) 34
4.7.3 最大縱向力工況 37
4.8 關(guān)鍵零部件強(qiáng)度校核 40
4.9 本章小結(jié) 42
結(jié)論 43
致謝 44
參考文獻(xiàn) 45
XII
CONTENTS
Abstract 錯(cuò)誤!未定義書簽。
Chapter1 Introduction 1
1.1 Development of pure electric vehicle 1
1.1.1 Development of electric vehicles abroad 2
1.1.2 Development of electric vehicle in China 2
1.2 Background and significance of the topics 3
1.3 Structure of this paper 5
1.4 Summary of this chapter 5
Chapter2 Vehicle design 6
2.1 Choice of the overall scheme of the car 6
2.1.1 Battery selection 6
2.1.2 Several driving modes for electric vehicles 8
2.2 Electronic differential speed steering analysis 12
2.2.1 Steering principle 13
2.2.2 Electronic differential speed implementation 14
2.2.3 Special purpose steering structure 15
2.3 Vehicle resistance 16
2.3.1 Rolling resistance 16
2.4 Summary of this chapter 20
Chapter3 Plan analysis 20
3.1 Characteristic analysis of brushless motor 21
3.1.1 Permanent magnet brushless DC motor driver 21
3.1.2 Material properties of permanent magnets 21
3.1.3 Extended speed technology 22
3.1.4 No-detection technology 22
3.2 Comparison and selection of wheel motor braking 23
3.2.1 Drum brake 23
3.2.2 Floating clamp brake 24
3.3 Summary of this chapter 26
Chapter4 Overall performance and selection of key parts of vehicle 27
4.1 Electric vehicle power performance calculation 27
4.2 Parameters selection for hub motor 28
4.3 Determination of rotational speed 29
4.4 Determination of power 29
4.5 Torque check 30
4.6 Speed up performance verification 31
4.7 Primary key axis neck size 31
4.7.1 Maximum vertical working condition design 32
4.7.2 Maximum lateral force working condition design 34
4.7.3 Maximum longitudinal force condition 37
4.8 Strength check of key parts 39
4.9 Summary of this chapter 42
Conclusion 43
Thanks 44
Reference 45
第一章 緒 論
1.1 純電動(dòng)汽車發(fā)展的概況
純電動(dòng)汽車發(fā)展至今,種類較多,通常按車輛用途、車載電源數(shù)目以及驅(qū)動(dòng)系統(tǒng)的組成進(jìn)行分類。按照用途不同分類,純電動(dòng)汽車可分為電動(dòng)轎車、電動(dòng)貨車和電動(dòng)客車三種。
(1)電動(dòng)轎車是目前最常見的純電動(dòng)汽車。除了一些概念車,純電動(dòng)轎車已經(jīng)有了小批量生產(chǎn),并已進(jìn)入汽車市場(chǎng)。
(2)電動(dòng)貨車用作功率運(yùn)輸?shù)碾妱?dòng)貨車目前還比較少,而在礦山、工地及一些特殊場(chǎng)地,則早已出現(xiàn)了一些大噸位的純電動(dòng)載貨汽車。
(3)電動(dòng)客車,目前純電動(dòng)小客車也較少見;純電動(dòng)大客車用作公共汽車,在一些城市的公交線路以及世博會(huì)、世界性的運(yùn)動(dòng)會(huì)上,已經(jīng)有了良好的表現(xiàn)。
純電動(dòng)汽車采用電動(dòng)機(jī)中央驅(qū)動(dòng)形式,直接借用了內(nèi)燃機(jī)汽車的驅(qū)動(dòng)方案,由發(fā)動(dòng)機(jī)前置前驅(qū)發(fā)展而來,由電動(dòng)機(jī)、離合器、變速箱和差速器責(zé)成。用電驅(qū)動(dòng)裝置替代了內(nèi)燃機(jī),通過離合器將電動(dòng)機(jī)動(dòng)力與驅(qū)動(dòng)輪進(jìn)行連接或動(dòng)力切斷,變速箱提供不同的傳動(dòng)比以變更轉(zhuǎn)速—功率曲線匹配的需要,變速器實(shí)現(xiàn)轉(zhuǎn)彎時(shí)兩車輪不同車速的行駛。
純電動(dòng)汽車采用雙電動(dòng)機(jī)電動(dòng)輪驅(qū)動(dòng)方式,機(jī)械差速器被兩個(gè)牽引電動(dòng)機(jī)所代替,兩個(gè)電動(dòng)機(jī)分別驅(qū)動(dòng)各自車輪,轉(zhuǎn)彎時(shí)通過電子差速控制以不同車速行駛,省掉了機(jī)械變速器。
現(xiàn)在純電動(dòng)汽車所獨(dú)有的以蓄電池作能量源的一種結(jié)構(gòu),蓄電池可以布置在上的四周,也可以集中布置在車的尾部或者布置在底盤下面。所選用的蓄電池應(yīng)該能提供足夠高的比能量和比功率,并且在車輛制動(dòng)時(shí)能回收再生制動(dòng)能量。具有高比能量和高比功率的動(dòng)力電池對(duì)純電動(dòng)汽車的加速性和爬坡能力。
為了解決一種蓄電池不能同時(shí)滿足對(duì)比能量和比功率的要求這個(gè)問題,可以在純電動(dòng)汽車同時(shí)采用兩種不同的蓄電池,其中一種能提供高比能量,另外一種提供高比功率。兩種電池作混合能量源的基本結(jié)構(gòu),這兩種結(jié)構(gòu)不僅分開了對(duì)比能量和比功率的要求,而且在汽車下坡或制動(dòng)時(shí)可利用蓄電池回收能量。
燃料電池所需的氫氣不僅能以壓縮氫氣、液態(tài)氫或金屬氫化物的形式儲(chǔ)存,還可以由常溫的液態(tài)燃料如甲醇或汽油隨車產(chǎn)生。一個(gè)帶小型重整器的純電動(dòng)汽車的結(jié)構(gòu),燃料電池所需的氫氣由重整隨車產(chǎn)生。
1.1.1 國外電動(dòng)汽車的發(fā)展現(xiàn)狀
美國在今年第二季度在全世界范圍內(nèi)銷售了7931臺(tái)電動(dòng)車,這一數(shù)字領(lǐng)先于其他所有市場(chǎng),銷量環(huán)比上漲28%。其他市場(chǎng)的數(shù)字分別是日本4240臺(tái),法國2056,德國1284。而在中國,今年的第一季度僅有235臺(tái)電動(dòng)汽車售出,比上一季度的343臺(tái)下降了31%。
日本將會(huì)是這個(gè)產(chǎn)業(yè)的領(lǐng)頭羊,到2017年,日本將生產(chǎn)77.9萬輛電動(dòng)車,占其汽車生產(chǎn)總量的9.7%。德國和美國也有可能將電動(dòng)汽車的產(chǎn)量推升至21.83萬輛和36.23萬輛,分別占汽車市場(chǎng)總產(chǎn)量的3.55%和3%。在此期間,中國的產(chǎn)量可能會(huì)達(dá)到273150輛,僅為汽車總產(chǎn)量的1%。
隨著電動(dòng)汽車行業(yè)競爭的不斷加劇,大型電動(dòng)汽車企業(yè)間并購整合與資本運(yùn)作日趨頻繁,國內(nèi)優(yōu)秀的電動(dòng)汽車企業(yè)愈來愈重視對(duì)行業(yè)市場(chǎng)的研究,特別是對(duì)企業(yè)發(fā)展環(huán)境和客戶需求趨勢(shì)變化的深入研究。正因?yàn)槿绱?,一大批國?nèi)優(yōu)秀的電動(dòng)汽車品牌迅速崛起,逐漸成為電動(dòng)汽車行業(yè)中的翹楚。
1.1.2 國內(nèi)電動(dòng)汽車的發(fā)展現(xiàn)狀
新能源汽車的發(fā)展方向有多種,但其中之一的氫燃料電池技術(shù)不成熟,成本昂貴,是20年之后的技術(shù)。中國也沒有氫燃料電池反應(yīng)所必需的鉑。雖然沒有公開申明,但據(jù)傳國家內(nèi)部決策層曾明確表示中國不適宜發(fā)展氫燃料電池汽車,只作為科研跟蹤。
從技術(shù)發(fā)展成熟程度和中國國情來看,純電動(dòng)汽車應(yīng)是大力推廣的發(fā)展方向,而混合動(dòng)力作為大面積充電網(wǎng)絡(luò)還沒建立起來之前的過渡技術(shù)。
但混合動(dòng)力車動(dòng)力系統(tǒng)復(fù)雜,成本昂貴。比亞迪F3DM有兩套動(dòng)力系統(tǒng),其公布的動(dòng)力系統(tǒng)成本增加了5萬元,相當(dāng)于每年要節(jié)省8千元的油費(fèi)才能比傳統(tǒng)汽油車經(jīng)濟(jì)。
混合動(dòng)力的優(yōu)勢(shì)是保留了傳統(tǒng)汽油汽車的使用生活方式,根據(jù)汽油機(jī)和電動(dòng)機(jī)混合程度,充電次數(shù)和傳統(tǒng)汽油汽車加油次數(shù)相當(dāng),或者不用充電。行駛距離也不受限制。
純電動(dòng)車省去了油箱、發(fā)動(dòng)機(jī)、變速器、冷卻系統(tǒng)和排氣系統(tǒng),相比傳統(tǒng)汽車的內(nèi)燃汽油發(fā)動(dòng)機(jī)動(dòng)力系統(tǒng),電動(dòng)機(jī)和控制器的成本更低,且純電動(dòng)車能量轉(zhuǎn)換效率更高。因電動(dòng)車的能量來源——電,來自大型發(fā)電機(jī)組,其效率是小型汽油發(fā)動(dòng)機(jī)甚至混合動(dòng)力發(fā)動(dòng)機(jī)所無法比擬的。純電動(dòng)汽車因此使用成本在下降。按比亞迪F3e純電動(dòng)車公布的數(shù)據(jù),百公里行駛耗電12度,依照0.5元的電價(jià)算,百公里使用成本才6元。而其原形車F3汽油車百公里耗油7.6升,按目前6.2元的油價(jià),成本是46.5元。相比之下,電動(dòng)車的使用成本才是傳統(tǒng)汽油汽車的八分之一。
純電動(dòng)車的缺點(diǎn)是它改變了傳統(tǒng)汽車的使用生活方式,需要每天充電。傳統(tǒng)的汽車使用習(xí)慣是大致一到兩周加一次油。而且每次出行也有幾百公里的距離限制,雖然一個(gè)家庭遠(yuǎn)距離出行可能一年就這么幾次。
1.2 選題的背景和意義
汽車在全球保有量的不斷增加使人類社會(huì)面臨能源短缺、全球變暖、空氣質(zhì)量水平下降等諸多挑戰(zhàn),同時(shí)也推動(dòng)的汽車自身技術(shù)的發(fā)展,為此汽車工程師正在不斷努力降低油耗的方法,尋求各種代用燃料以及開發(fā)不用或少用汽油的新型車輛;越來越多的認(rèn)識(shí)已認(rèn)識(shí)到各種類型電動(dòng)汽車和燃料電池汽車是實(shí)現(xiàn)清潔汽車的解決方案,全世界的汽車業(yè)界也正在為此努力并投入巨大的資金和人力。
眾所周知,電動(dòng)汽車相對(duì)于傳統(tǒng)汽車最大的特點(diǎn)是在行駛過程中很少甚至沒有排放污染,熱輻射低,噪聲低且環(huán)境友好。然而輪轂電機(jī)技術(shù)特點(diǎn)在于將動(dòng)力、傳動(dòng)和制動(dòng)裝置都整合到輪轂內(nèi),因此將電動(dòng)車輛的機(jī)械部分大大簡化。輪轂電機(jī)技術(shù)并非新生事物,早在1900年,就已經(jīng)制造出了前輪裝備輪轂電機(jī)的電動(dòng)汽車,在20世紀(jì)70年代,這一技術(shù)在礦山運(yùn)輸車等領(lǐng)域得到應(yīng)用。而對(duì)于乘用車所用的輪轂電機(jī),日系廠商對(duì)于此項(xiàng)技術(shù)研發(fā)開展較早,目前處于領(lǐng)先地位,包括通用、豐田在內(nèi)的國際汽車巨頭也都對(duì)該技術(shù)有所涉足。
輪轂電機(jī)驅(qū)動(dòng)系統(tǒng)根據(jù)電機(jī)的轉(zhuǎn)子型式主要分成兩種結(jié)構(gòu)型式:內(nèi)轉(zhuǎn)子式和外轉(zhuǎn)子式。其中外轉(zhuǎn)子式采用低速外轉(zhuǎn)子電機(jī),電機(jī)的最高轉(zhuǎn)速在1000-1500r/min,無減速裝置,車輪的轉(zhuǎn)速與電機(jī)相同;而內(nèi)轉(zhuǎn)子式則采用高速內(nèi)轉(zhuǎn)子電機(jī),配備固定傳動(dòng)比的減速器,為獲得較高的功率密度,電機(jī)的轉(zhuǎn)速可高達(dá)10000r/min。隨著更為緊湊的行星齒輪減速器的出現(xiàn),內(nèi)轉(zhuǎn)子式輪轂電機(jī)在功率密度方面比低速外轉(zhuǎn)子式更具競爭力。
輪轂電機(jī)的優(yōu)點(diǎn),相對(duì)于傳統(tǒng)以電動(dòng)機(jī)為動(dòng)力的純電動(dòng)汽車的優(yōu)越性在于:
省略大量傳動(dòng)部件,讓車輛結(jié)構(gòu)更簡單,可實(shí)現(xiàn)多種復(fù)雜的驅(qū)動(dòng)方式,便于采用多種新能源車技術(shù)等等。
對(duì)于輪轂電機(jī)技術(shù)近年來的應(yīng)用現(xiàn)狀,國外輪轂電機(jī)驅(qū)動(dòng)技術(shù)的應(yīng)用主要體現(xiàn)在兩個(gè)方面:一是以輪胎生產(chǎn)商或汽車零部件生產(chǎn)商為代表的研發(fā)團(tuán)隊(duì)開發(fā)的集成化電動(dòng)系統(tǒng);二是整車生產(chǎn)商與輪轂電機(jī)驅(qū)動(dòng)系統(tǒng)生產(chǎn)商聯(lián)合開發(fā)的電動(dòng)汽車。而在我國國內(nèi)對(duì)于輪轂電機(jī)的研究多集中于高校,產(chǎn)品均為電動(dòng)汽車,與此同時(shí),自主品牌汽車廠商也紛紛推出了自己的輪轂電機(jī)技
4
術(shù)產(chǎn)品,國內(nèi)的汽車商雖然能夠生產(chǎn)電動(dòng)汽車,但是對(duì)于輪轂電機(jī)驅(qū)動(dòng)技術(shù)的研究尚不成熟,尤其是在高轉(zhuǎn)矩輪轂電機(jī)開發(fā)方面,與國外先進(jìn)產(chǎn)品仍有一定差距。
1.3 本文的結(jié)構(gòu)
本文的第1章為引入的緒論,概括了純電動(dòng)汽車發(fā)展的現(xiàn)狀和趨勢(shì);
本文的第2章為方案分析,較為詳細(xì)的闡述了輪轂電機(jī)方案選擇及其優(yōu)缺點(diǎn);
本文的第3章為主要零部件的選擇和設(shè)計(jì)分析,選取電池、電動(dòng)機(jī)整體為對(duì)象具體的分析和設(shè)計(jì);
本文的第4章為電機(jī)整體的參數(shù)設(shè)計(jì),零件的設(shè)計(jì)與校核。
1.4 本章小結(jié)
本章緒論部分主要對(duì)本次畢業(yè)設(shè)計(jì)的選題及研究目標(biāo)進(jìn)行了相關(guān)的介紹,主要目的是能夠?qū)υ擃}目有個(gè)初步的了解并確定設(shè)計(jì)方向。對(duì)于輪轂電機(jī)技術(shù)選題的意義以及它在國外和國內(nèi)相關(guān)領(lǐng)域的發(fā)展情況進(jìn)行了簡要的介紹,讓大家對(duì)輪轂電機(jī)技術(shù)的起源發(fā)展及歷史有一定了解。
47
第二章 整車設(shè)計(jì)
2.1 汽車整體初步方案的選擇
2.1.1 電池的選擇
電動(dòng)汽車電池分兩大類,蓄電池和燃料電池。
蓄電池適用于純電動(dòng)汽車,包括鉛酸蓄電池、鎳基電池、鈉硫電池、二次鋰電池、空氣電池。
燃料電池專用于燃料電池電動(dòng)汽車,包括堿性燃料電池(AFC)、磷酸燃料電池(PAFC)、熔融碳酸鹽電池(MCFC )、固體氧化物燃料電池(SOFC)、質(zhì)子交換膜燃料電池(PEMFC )、直接甲醇燃料電池(DMFC )。
燃料電池由。燃料在陽極氧化,氧化劑在陰極還原。如果在陽極(即外電路的負(fù)極,也可稱燃料極)上連續(xù)供給氣態(tài)燃料(氫氣),而在陰極(即外電路的正極,也可稱空氣極)上連續(xù)供給氧氣(或空氣),就可以在電極上連續(xù)發(fā)生電化學(xué)反應(yīng),并產(chǎn)生電流。由此可見燃料電池與常規(guī)電池不同,它的燃料和氧化劑不是儲(chǔ)存在電池內(nèi),而是儲(chǔ)存在電池外部的儲(chǔ)罐中。當(dāng)它工作(輸出電流并做功)時(shí),需要不間斷地向電池內(nèi)輸人燃料和氧化劑并同時(shí)排出反應(yīng)產(chǎn)物。因此,從工作方式上看,它類似于常規(guī)的汽油或柴油發(fā)電機(jī)。由于燃料電池工作時(shí)要連續(xù)不斷地向電池內(nèi)送入燃料和氧化劑,所以燃料電池使用的燃料和氧化劑均為流體(氣體或液體)。最常用的燃料為純氫、各種富含氫的氣體(如重整氣)和某些液體(如甲醇水溶液),常用的氧化劑為純氧、凈化空氣等氣體和某些液體(如過氧化氫和硝酸的水溶液等)[1]。
燃料電池陽極的作用是為燃料和電解液提供公共界面,并對(duì)燃料的氧化產(chǎn)生催化作用,同時(shí)把反應(yīng)中產(chǎn)生的電子傳輸?shù)酵怆娐坊蛘呦葌鬏數(shù)郊靼搴笤傧蛲怆娐穫鬏?。陰極(氧電極)的作用是為氧和電解液提供公共界面,對(duì)氧的還原產(chǎn)生催化作用,從外電路向氧電極的反應(yīng)部位傳輸電子。由于電極上發(fā)生的反應(yīng)大多為多相界面反應(yīng),為提高反應(yīng)速率,電極一般采用多孔材料并涂有電催化劑。
電解質(zhì)的作用是輸送燃料電極和氧電極在電極反應(yīng)中所產(chǎn)生的離子,并能阻止電極間直
接傳遞電子。
隔膜的作用是傳導(dǎo)離子、阻止電子在電極間直接傳遞和分隔氧化劑與還原劑。因此隔膜必須是抗電解質(zhì)腐蝕和絕緣的物質(zhì),并具有良好耐潤濕性。
圖2-1 燃料電池 圖2-2 特斯拉磷酸鐵鋰電池組
1)電池組
電動(dòng)汽車電池組由多個(gè)電池串聯(lián)疊置組成。一個(gè)典型的電池組大約有96個(gè)電池,充電到4.2V的鋰離子電池而言,這樣的電池組可產(chǎn)生超過400V的總電壓。盡管汽車電源系統(tǒng)將電池組看作單個(gè)高壓電池,每次都對(duì)整個(gè)電池組進(jìn)行充電和放電,但電池控制系統(tǒng)必須獨(dú)立考慮每個(gè)電池的情況。如果電池組中的一個(gè)電池容量稍微低于其他電池,那么經(jīng)過多個(gè)充電/放電周期后,其充電狀態(tài)將逐漸偏離其它電池。如果這個(gè)電池的充電狀態(tài)沒有周期性地與其它電池平衡,那么它最終將進(jìn)入深度放電狀態(tài),從而導(dǎo)致?lián)p壞,并最終形成電池組故障。為防止這種情況發(fā)生,每個(gè)電池的電壓都必須監(jiān)視,以確定充電狀態(tài)。此外,必須有一個(gè)裝置讓電池單獨(dú)充電或放電,以平衡這些電池的充電狀態(tài)。
電池組監(jiān)視系統(tǒng)的一個(gè)重要考慮因素是通信接口。就PC板內(nèi)的通信而言,常用的選項(xiàng)包括串行外設(shè)接口(SPI)總線、I2C總線,每種總線的通信開銷都很低,適用于低干擾環(huán)境。另一個(gè)選項(xiàng)是控制器局域網(wǎng)(CAN)總線,這種總線在汽車應(yīng)用中被廣泛使用。CAN總線具有誤差檢測(cè)和故障容限特性,但是它的通信開銷很大,材料成本也很高。盡管從電池系統(tǒng)到汽車主CAN總線的連接是值得要的,但在電池組內(nèi)采用SPI或I2C通信是有優(yōu)勢(shì)的。
綜上所述,對(duì)于本文中的電動(dòng)汽車所面臨的使用環(huán)境(市區(qū)為主),考慮到使用環(huán)境中對(duì)安全性及結(jié)合當(dāng)前充電樁等相關(guān)配套設(shè)備的實(shí)用性,所以本設(shè)計(jì)中將采用在比亞迪S6等車型中所使用的磷酸鐵鋰電池,盡管能量密度并非最高,但其所帶來的安全性和可循環(huán)充電次數(shù)、可預(yù)見的經(jīng)濟(jì)性等方面的優(yōu)異行仍是本方案的最佳選擇。
2.1.2 電動(dòng)汽車的幾種驅(qū)動(dòng)方式
在現(xiàn)代電驅(qū)動(dòng)系概念性的視于圖2-3中。該電驅(qū)動(dòng)系有三個(gè)主要的子系統(tǒng)組成:電動(dòng)機(jī)驅(qū)動(dòng)、能源和輔助子系統(tǒng)。電動(dòng)機(jī)驅(qū)動(dòng)子系統(tǒng)由車輛控制器、電力電子變換器、電動(dòng)機(jī)、機(jī)械傳動(dòng)裝置和驅(qū)動(dòng)輪組成;能源子系統(tǒng)包含能源、能量管理單元和能量的燃料供給單元;輔助子系統(tǒng)由功率控制單元和輔助電源組成。
圖2-3 通用EV結(jié)構(gòu)的概念性圖示
基于來自加速和制動(dòng)踏板的控制輸入,車輛控制器想電力電子變換器給出正確的控制信號(hào),變換器行駛控制電動(dòng)機(jī)與能源之間的功率流的功能。起因于EV再生制動(dòng)所導(dǎo)致的反向功率流,以及該再生能量可儲(chǔ)存與能源之中,構(gòu)成了有接受能量能力的能源。大多數(shù)的EV蓄電池組、超級(jí)電容器組以及飛輪組都可容易的具有接收再生能量的能力。能量管理單元與車輛控制器相配合,控制再生制動(dòng)及其能量的回收,它與能量的燃料供給單元一起控制燃料供給單元,并監(jiān)控能源的使用性能。輔助電源為所有的EV輔助設(shè)備,尤其是車內(nèi)氣候控制和功率控制單元,提供不同電壓等級(jí)的所需功率。
由于在電驅(qū)動(dòng)特性和能源方面的多樣性,可有各種可能的EV結(jié)構(gòu)形式,如圖2-4所示。
1)圖2-4a表明了第一種可供選擇的結(jié)構(gòu),其中電驅(qū)動(dòng)裝置替代了傳統(tǒng)車輛驅(qū)動(dòng)系的內(nèi)燃機(jī),它由電動(dòng)機(jī)、離合器、變速器和差速器組成。離合器和變速箱可有自動(dòng)傳動(dòng)裝置予以替代,離合器用以將電動(dòng)機(jī)的動(dòng)力連接到驅(qū)動(dòng)輪,或從驅(qū)動(dòng)輪處脫開。變速箱提供一組傳動(dòng)比,以變更轉(zhuǎn)速—功率(轉(zhuǎn)矩)曲線匹配在和的需求。差速器是一種機(jī)械器件(通常是一組行星齒輪),當(dāng)車輛沿著玩去的路徑行駛時(shí),它使兩側(cè)車輪以不同的轉(zhuǎn)速驅(qū)動(dòng)。
圖2-4 a)
2) 如圖2-24 b所示,借助于電動(dòng)機(jī)在大范圍轉(zhuǎn)速變化中所具有的恒功率特性,可用固定當(dāng)?shù)凝X輪傳動(dòng)裝置替代多速變速箱,并縮減了對(duì)離合器的需要。這一結(jié)構(gòu)不僅減小了機(jī)械傳動(dòng)裝置的尺寸和重量,而且由于不需要換擋,故可簡化驅(qū)動(dòng)系的控制。
圖2-4 b)
3)如圖2-4c所示,類似于如2-2b中的驅(qū)動(dòng)系,電動(dòng)機(jī)、固定當(dāng)?shù)凝X輪傳動(dòng)裝置和差速器可進(jìn)一步集成為單個(gè)組合件,而其兩側(cè)的軸連接兩邊的驅(qū)動(dòng)輪。整個(gè)驅(qū)動(dòng)系由此得以進(jìn)一步的簡化和小型化。
圖2-4 c)
4)在圖2-4d中,機(jī)械差速器被兩個(gè)牽引電動(dòng)機(jī)所替代。該兩電動(dòng)機(jī)分別驅(qū)動(dòng)相應(yīng)側(cè)的車輪,并當(dāng)車輛沿彎曲路徑行駛時(shí),兩者以不同的轉(zhuǎn)速運(yùn)轉(zhuǎn)。
圖2-4 d)
5)如圖2-4e所示,為進(jìn)一步簡化驅(qū)動(dòng)系,牽引電機(jī)可安置在車輪內(nèi),即使用本文所涉及的輪轂電機(jī)。這種配置是通常所說的輪式驅(qū)動(dòng)。一個(gè)薄型行星齒輪組可用以降低電動(dòng)機(jī)轉(zhuǎn)速,并增大電動(dòng)機(jī)轉(zhuǎn)矩。該薄型行星齒輪組具有高減速比以及輸入和輸出軸縱向配置的優(yōu)點(diǎn)。
圖2-4 e)
6) 如圖2-4f所示,通過完全舍棄電動(dòng)機(jī)和驅(qū)動(dòng)輪之間任何的機(jī)械傳動(dòng)裝置,應(yīng)用于論事驅(qū)動(dòng)的低速外轉(zhuǎn)子型電動(dòng)機(jī)可直接連接至驅(qū)動(dòng)輪。此時(shí)電動(dòng)機(jī)的轉(zhuǎn)速控制等價(jià)于輪速控制。然而,這一配置要求電動(dòng)機(jī)在車輛啟動(dòng)和加速運(yùn)行時(shí)具有高轉(zhuǎn)矩性能。
圖2-4 f)
a) 配置多檔傳動(dòng)裝置和離合器的傳統(tǒng)驅(qū)動(dòng)系 b) 無離合器需求的單擋傳動(dòng)裝置 c)固定擋的傳動(dòng)裝置和差速器的集成 d) 兩個(gè)獨(dú)立的電動(dòng)機(jī)和帶有驅(qū)動(dòng)軸的固定擋傳動(dòng)裝置 e)配置兩個(gè)獨(dú)立電動(dòng)機(jī)和固定擋傳動(dòng)裝置的直接驅(qū)動(dòng) f) 兩個(gè)分離的輪式驅(qū)動(dòng)形式
C—離合器 D —差速箱 FG—固定擋的齒輪傳動(dòng)裝置 GB—變速箱 M—電動(dòng)機(jī)
綜上所述,使用輪轂電機(jī)技術(shù)的f型傳動(dòng)方式無疑在驅(qū)動(dòng)結(jié)構(gòu)上極大的簡化了傳動(dòng)裝置,所以在技術(shù)研發(fā)的過程中可以節(jié)約大量的人力資源,縮短研發(fā)周期,極大的降低汽車成本?;诒疚闹械脑O(shè)計(jì)需要,故選擇四個(gè)具有輪轂電機(jī)的車輪作為動(dòng)力源的f方案。
2.2 基于輪轂電機(jī)技術(shù)的電子差速轉(zhuǎn)向分析
由于本文是基于輪轂電機(jī)技術(shù)而設(shè)計(jì)的車型,對(duì)于汽車的轉(zhuǎn)向方式,出于輪轂電機(jī)技術(shù)的特性,進(jìn)而可以選擇很多更具靈活性的結(jié)構(gòu),比如電子差速轉(zhuǎn)向。
電子差速的方法是通過駕駛者輸入信號(hào),恐怕那個(gè)之氣改變車輪速度實(shí)現(xiàn)轉(zhuǎn)向,如圖2-5所示。方向盤的轉(zhuǎn)動(dòng)軸底部直接連接一個(gè)誤差為0.5%的唯一傳感器,該傳感器的位移范圍是(0~200)mm,模擬電壓輸出范圍為(0~5)V,作為電子差速轉(zhuǎn)向系統(tǒng)的指令輸入。
1. 方向盤 2.轉(zhuǎn)軸 3.轉(zhuǎn)向節(jié) 4.轉(zhuǎn)向橫拉桿 5.萬向節(jié) 6.輪轂電機(jī)
圖2-5 電子差速的轉(zhuǎn)向機(jī)構(gòu)控制器
2.2.1 轉(zhuǎn)向原理
四輪電子差速需要對(duì)4個(gè)輪轂電機(jī)同時(shí)進(jìn)行速度控制和差速計(jì)算,是一個(gè)復(fù)雜的控制系統(tǒng)。硬件結(jié)構(gòu)包括方向盤、位移傳感器、控制器、4個(gè)輪轂電機(jī)、每個(gè)電機(jī)的轉(zhuǎn)子位置傳感器。圖4為電子差速轉(zhuǎn)向總體控制框圖。
電子差速轉(zhuǎn)向系統(tǒng)通過調(diào)整電機(jī)轉(zhuǎn)速,改變車輪的轉(zhuǎn)速實(shí)現(xiàn)差速轉(zhuǎn)向。當(dāng)電動(dòng)汽車需要轉(zhuǎn)向時(shí),轉(zhuǎn)向的內(nèi)側(cè)車輪速度小于外側(cè)車輪速度。由于內(nèi)外輪測(cè)的速度差異,相同時(shí)間內(nèi),內(nèi)側(cè)車輪駛過的距離較小,外側(cè)車輪駛過的距離較大,車體必然向內(nèi)側(cè)偏轉(zhuǎn),從而實(shí)現(xiàn)轉(zhuǎn)向。具體轉(zhuǎn)向過程如下:首先將方向盤的角度輸出轉(zhuǎn)換成控制系統(tǒng)可以接收的模擬信號(hào),在執(zhí)行轉(zhuǎn)向之前,定義方向盤的角度輸出與模擬量之間的關(guān)系;然后對(duì)模擬信號(hào)的變化范圍進(jìn)行分析,經(jīng)過計(jì)算即可得到不同的方向盤位置與轉(zhuǎn)向時(shí)各個(gè)車輪轉(zhuǎn)速的分配;內(nèi)外側(cè)車輪產(chǎn)生速度差異,實(shí)現(xiàn)轉(zhuǎn)向。
圖2-6 電子差速轉(zhuǎn)向總體控制框圖
2.2.2 電子差速實(shí)現(xiàn)方式
電動(dòng)汽車在進(jìn)行電子差速轉(zhuǎn)向時(shí),其當(dāng)前的運(yùn)行方式對(duì)電子差速方案的實(shí)施有著重要的影響。根據(jù)不同的工作模式,電子差速運(yùn)行時(shí),當(dāng)前電動(dòng)汽車的速度狀態(tài)和轉(zhuǎn)向角度指令都要作相應(yīng)的變化和調(diào)整。
電動(dòng)汽車在進(jìn)行勻速前進(jìn)時(shí),由于路面存在高低不平、輪胎參數(shù)有差異,4個(gè)車輪速度必然會(huì)受到影響,導(dǎo)致4個(gè)車輪轉(zhuǎn)速不同。如果不進(jìn)行糾正,就會(huì)引起電動(dòng)汽車向轉(zhuǎn)速較慢的那一方轉(zhuǎn)向,若四輪車速相差較大更會(huì)引起車輛行駛的不穩(wěn)定。利用PD調(diào)速方法對(duì)電機(jī)轉(zhuǎn)速進(jìn)行閉環(huán)控制,可提高電機(jī)調(diào)速的響應(yīng)時(shí)間和調(diào)速穩(wěn)定性,有利于4個(gè)輪轂電機(jī)轉(zhuǎn)速的一致性協(xié)調(diào)。轉(zhuǎn)速一致性協(xié)調(diào)遵循一下法則:在電動(dòng)汽車直線前進(jìn)時(shí),在采樣點(diǎn)時(shí)刻求出4個(gè)車輪轉(zhuǎn)速的最小值,使其他3個(gè)車輪的轉(zhuǎn)速與其始終保持一致,其流程如圖2-7所示。
當(dāng)電動(dòng)汽車在加速前進(jìn)時(shí),加速踏板發(fā)出的速度指令在不斷變化,控制器根據(jù)加速指令的變化改變控制器的PWM占空比輸出,輪轂電機(jī)的轉(zhuǎn)速也相應(yīng)在變化。此時(shí)產(chǎn)生轉(zhuǎn)向指令,若保持電機(jī)處于加速狀態(tài)同時(shí)進(jìn)行轉(zhuǎn)向操作,必然會(huì)導(dǎo)致在轉(zhuǎn)向過程中電動(dòng)汽車的不穩(wěn)定運(yùn)行。本文采取的策略是記錄向指令發(fā)生時(shí)刻的PWM占空比值和車速,并保持PWM占空比值不變。根據(jù)車速和轉(zhuǎn)向角度計(jì)算4個(gè)車輪的各自的轉(zhuǎn)速,并開始實(shí)施轉(zhuǎn)向;當(dāng)轉(zhuǎn)向指令結(jié)束后,PWM的占空比值從轉(zhuǎn)向指令發(fā)生時(shí)可記錄的數(shù)據(jù)開始隨之加速踏板指令變化,車速也隨著作相應(yīng)變化。具體實(shí)施策略如圖2-8所示。圖中v是電動(dòng)的車輪速度,T是電動(dòng)汽車車輪的轉(zhuǎn)矩。
圖2-7四輪速度協(xié)調(diào)流程圖 圖2-8加減速運(yùn)行時(shí)電動(dòng)車轉(zhuǎn)向策略流程圖
2.2.3 特殊用途的轉(zhuǎn)向結(jié)構(gòu)
前幾節(jié)中所提到的均為日常行駛過程中的轉(zhuǎn)向方式,但在實(shí)際生活中,基于輪轂電機(jī)技術(shù)的汽車通過特殊的轉(zhuǎn)向結(jié)構(gòu)還可以實(shí)現(xiàn)特殊環(huán)境下獨(dú)特的轉(zhuǎn)向方式,例如側(cè)方位停車以及汽車的倒庫出庫等與汽車駕駛息息相關(guān)的駕駛動(dòng)作。
本文中,電子差速系統(tǒng)雖然在日常行駛過程中足以滿足正常的使用要求,但是仍然沒有進(jìn)一步發(fā)揮輪轂電機(jī)技術(shù)的優(yōu)勢(shì)。所以本文在懸掛系統(tǒng)、底盤結(jié)構(gòu)的選擇及設(shè)計(jì)上進(jìn)行了一些調(diào)整與變更,即選用橫臂式獨(dú)立懸掛并為4個(gè)輪胎各配備一個(gè)氣壓缸使輪胎的擺動(dòng)角度可以大大提高,即0~120°之間。如下圖2-10所示,如果在汽車的電控系統(tǒng)中單獨(dú)為氣壓缸設(shè)定一個(gè)轉(zhuǎn)向模式,當(dāng)駕駛者在需要進(jìn)行側(cè)方位停車、汽車的倒庫出庫、原地轉(zhuǎn)向等駕駛動(dòng)作時(shí)啟用,電控系統(tǒng)向氣壓缸傳遞電信號(hào)使活塞桿伸出所需長度使輪胎完成所需角度的旋轉(zhuǎn),再通過四個(gè)輪轂電機(jī)的正反轉(zhuǎn)配合,可以很大程度上簡化了停車、轉(zhuǎn)向的程序并很大程度的節(jié)約了這些過程所用的時(shí)間。如果在電控系統(tǒng)中通過汽車前后雷達(dá)配以很多廠商結(jié)合自己車型所設(shè)計(jì)的自動(dòng)泊車系統(tǒng)應(yīng)用到使用輪轂電機(jī)技術(shù)的汽車上,無疑會(huì)為汽車帶來不一樣的操縱樂趣的同時(shí)大大降低停車過程中由于新手司機(jī)技術(shù)上的不足所引發(fā)的汽車之間的刮蹭事故。
圖2-9 汽車底盤懸掛 圖2-10 汽車側(cè)位停車圖
2.3 車輛的阻力
2.3.1 滾動(dòng)阻力
如圖2-11所示,與其運(yùn)動(dòng)方向相反的車輛阻力包括輪胎滾動(dòng)阻力、空氣阻力Fw以及爬坡阻力。
圖2-11 作用于上坡行駛車輛上的力
在硬地面上,輪胎的滾動(dòng)阻力基本上起因于輪胎材料的滯變作用。圖2-12表明作用于停頓狀態(tài)輪胎上的力P通過其中心。這樣,在輪胎和地面之間接觸面上的壓力對(duì)稱于中心線分布,而所產(chǎn)生的反作用力Pz與P共線。在加載和卸載過程中,作為載荷P的函數(shù)的形變z,如圖2-12所示。由于橡膠材料形變狀態(tài)下的滯變作用,對(duì)于相同的形變z,處于加載情況下的載荷大于卸載時(shí)的在和(見圖2-13)。當(dāng)輪胎滾動(dòng)時(shí),如圖2-14a所示,在接觸面的前半部分為加載,而后半部分為卸載。從而,滯變作用導(dǎo)致地面反作用力的不對(duì)稱分布,使接觸面前半部分的壓力大于后半部分的壓力(見圖2-14a)。這一現(xiàn)象的結(jié)果是地面反作用力向前偏移。該向前偏移的地面反作用力和作用于車輪中心、鉛錘方向的載荷產(chǎn)生了一個(gè)抵制車輪滾動(dòng)的扭矩。在軟地面上,滾動(dòng)阻力基本上起因于地面的變形,如圖2-14b所示。此時(shí),地面反作用力幾乎完全地偏移至接觸面的前半部分。
圖2-12 在接觸表面上的壓力分布 圖2-13在加載和卸載情況下作為輪胎形變函數(shù)
圖2-14 輪胎的撓曲及其滾動(dòng)阻力
a) 硬路面 b)軟路面
由合成的地面反作用力向前偏移所產(chǎn)生的轉(zhuǎn)矩被成為滾動(dòng)阻力轉(zhuǎn)矩,即:
為保持車輪轉(zhuǎn)動(dòng),作用于車輪中心的力F應(yīng)與滾動(dòng)阻力距相平衡,即此力應(yīng)為:
其中,rd 為輪胎的有效半徑;fr=a/rd稱為滾動(dòng)阻力系數(shù)。這樣,滾動(dòng)阻力距可通過作用于車輪中心且其指向與車輪運(yùn)動(dòng)方向相反的一個(gè)水平力予以等值替代。這一等值力被稱為滾動(dòng)阻力,即:
式中,P為作用于滾動(dòng)車輪中心的鉛錘方向的載荷。當(dāng)車輛運(yùn)行在有坡度的地面上時(shí),鉛錘方向的載荷P應(yīng)由與地面蒸餃的分量所替代,即:
其中,α為地面的傾斜角。
滾動(dòng)阻力系數(shù)fr是取決于輪胎材料、輪胎結(jié)構(gòu)、輪胎溫度、輪胎充氣壓力、外胎面的幾何形狀、路面粗糙度、路面材料和路面上有無液體的函數(shù),它對(duì)應(yīng)于各種不同特征路面的典型值列于表2-1。
由在混凝土路上,轎車的滾動(dòng)阻力系數(shù)可用下列經(jīng)驗(yàn)公式計(jì)算:
其中V為車速(km/h);f0和fs取決于輪胎的充氣壓力。
車輛性能計(jì)算中,對(duì)混凝土路面行駛的轎車,可應(yīng)用如下適合于最一般充氣壓力范圍的公式:
表2-1 不同特征路面的典型值
狀況
滾動(dòng)阻力系數(shù)
混凝土或?yàn)r青路面上的汽車輪胎
0.013
壓實(shí)的沙礫路面上的汽車輪胎
0.02
瀝青碎石路
0.025
未鋪路面
0.05
田野
0.1~0.35
混凝土或?yàn)r青路面上的載貨汽車輪胎
0.006~0.01
鐵軌上的車輪
0.001~0.002
2.3.2 空氣阻力
以特定速度運(yùn)動(dòng)的車輛將遇到阻礙其運(yùn)動(dòng)的空氣阻力的作用,即形狀阻力和外殼摩擦力。
即形狀阻力,而空氣阻力的表達(dá)式為:
式中,車速是V,車輛迎風(fēng)正面的面積Af,車身形狀和空氣密度的函數(shù),CD是車身形狀特空氣阻力系數(shù);Vw是車輛運(yùn)動(dòng)方向上的風(fēng)速分量[2]。
2.4 本章小結(jié)
本章的主要是介紹了一些關(guān)于汽車總體上根據(jù)本論文所面市場(chǎng)而選定的一些方案以及整體驅(qū)動(dòng)的數(shù)據(jù)計(jì)算所依據(jù)的公式,為后續(xù)更詳盡的數(shù)據(jù)的計(jì)算展開鋪墊。并且在轉(zhuǎn)向結(jié)構(gòu)的設(shè)計(jì)上為相對(duì)與傳統(tǒng)汽車的轉(zhuǎn)向系統(tǒng)提供了一種新的思路。
第3章 方案分析
3.1 無刷電機(jī)的特性分析
3.1.1 永磁無刷直流電機(jī)驅(qū)動(dòng)基本原理
???用詞無刷直流電動(dòng)機(jī)驅(qū)動(dòng)主要有無刷直流電動(dòng)機(jī)、基于數(shù)字信號(hào)處理器(DSP)的控制器和基于電力電子的功率變換器所構(gòu)成。由位置檢測(cè)器檢測(cè)電動(dòng)機(jī)轉(zhuǎn)子的位置。轉(zhuǎn)子的位置信息輸入到基于DSP的控制器,隨即由該控制器向功率變換器提供門控信號(hào),從而導(dǎo)通和關(guān)斷特定的電動(dòng)機(jī)定子磁極繞組。按這種方式,控制電機(jī)的轉(zhuǎn)矩和轉(zhuǎn)速[3]。
3.1.2 永磁體的材料性能
目前用于電機(jī)的永磁體材料有三類:
1)鋁鎳鈷(Al、Ni、Co、Fe);
2)陶瓷(鐵氧體),例如鋇鐵氧體(BaOx6Fe2O3)和鐵酸鍶(SrOx6Fe2O3);
3)稀土永磁材料,即釤鈷(SmCo)和釹鐵硼(NdFeB)。
1)鋁鎳鈷
鋁鎳鈷的主要優(yōu)點(diǎn)是其高剩余磁通密度和低溫度系數(shù)。這種材料剩磁Br的溫度系數(shù)為0.02%/,且其最高工作溫度為520。這些優(yōu)點(diǎn)使很高的氣隙磁密,以及高運(yùn)行溫度成為可能。遺憾的是,矯頑力很低,且其退磁曲線呈現(xiàn)高度的非線性。因此,鋁鎳鈷不僅易于磁化,而且也很容易退磁。鋁鎳鈷永磁體已用于額定功率為幾瓦到150kW范圍內(nèi)的電機(jī)。
2)鐵氧體
鋇鐵氧體、鐵酸鍶與鋁鎳鈷相比鐵氧體具有較高的矯頑力,但同時(shí)剩磁較低。鐵氧體的溫度系數(shù)相對(duì)較高,即Br的溫度系數(shù)為0.20%/,矯頑力Hc的溫度系數(shù)為0.27%/。最高工作溫度為400。鐵氧體的主要優(yōu)點(diǎn)是低成本和高阻抗,這意味著永磁體內(nèi)無渦流損耗。
3)稀土永磁體
現(xiàn)今,釤鈷市一中廣泛接受的硬磁材料,它具有高剩磁、高矯頑力、高能量積、線性退磁曲線和低溫度系數(shù)的優(yōu)點(diǎn)。其溫度系數(shù)(0.03~0.045)%/,而Hc的溫度系數(shù)為(0.14~0.40)%/。最高工作溫度為250~300。釤鈷非常適合做小體積的電機(jī),從而電機(jī)具有高比功率和低轉(zhuǎn)動(dòng)慣量。價(jià)格昂貴是釤鈷唯一的缺點(diǎn)。
3.1.3 擴(kuò)展轉(zhuǎn)速技術(shù)
永磁無刷直流電動(dòng)機(jī)由于其受到限制的弱磁能力,故其固有的恒功率范圍小。這起因于永磁體磁場(chǎng)的存在,該磁場(chǎng)只能通過與轉(zhuǎn)子磁場(chǎng)反向的定子磁場(chǎng)成分予以弱化。其轉(zhuǎn)速比通常小于2[5]。
最近,已開發(fā)使用附加的勵(lì)磁繞組來擴(kuò)展永磁無刷直流電動(dòng)機(jī)的轉(zhuǎn)速范圍。該技術(shù)的關(guān)鍵是控制勵(lì)磁電流,使得由永磁體提供的氣隙磁場(chǎng)在高速恒功率運(yùn)行期間可被弱化。由于永磁體和勵(lì)磁繞組的存在,這種電動(dòng)機(jī)被稱作永磁混合式電動(dòng)機(jī)。永磁混合式電動(dòng)機(jī)可獲得的轉(zhuǎn)速比約為4。永磁混合式電動(dòng)機(jī)驅(qū)動(dòng)的最佳效率圖如圖所示。但是,永磁混合式電動(dòng)機(jī)具有結(jié)構(gòu)相對(duì)復(fù)雜的缺點(diǎn),其轉(zhuǎn)速比仍不足以滿足車輛性能需求,特別是在越野汽車中,因此需要有多檔的傳動(dòng)裝置。
3.1.4 無檢測(cè)技術(shù)
永磁無刷直流電動(dòng)機(jī)驅(qū)動(dòng)的運(yùn)行主要依賴于位置檢測(cè)器[6],以獲得轉(zhuǎn)自位置信息,從而恰當(dāng)?shù)膱?zhí)行各相的導(dǎo)通或關(guān)斷。位置檢測(cè)器通常不是三維霍爾效應(yīng)傳感器,就是光編碼器。這些位置檢測(cè)器都是高成本、易損的原件。因此,位置檢測(cè)器的存在不僅提高了電動(dòng)機(jī)驅(qū)動(dòng)的成本,而且嚴(yán)重地降低了系統(tǒng)的可靠性,并限制了其在某些環(huán)境中的應(yīng)用,如軍用。如果位置檢測(cè)器失效,則無位置檢測(cè)器技術(shù)可有效的繼續(xù)系統(tǒng)的運(yùn)行。
已有幾種無檢測(cè)器技術(shù)被開發(fā),這些技術(shù)的大多數(shù)都是以電壓、電流和反電動(dòng)勢(shì)的檢測(cè)為基礎(chǔ)的,主要分為四類:
1) 使用所檢測(cè)的電流、電壓、電機(jī)的基本方程和代數(shù)計(jì)算的一類;
2) 使用觀測(cè)器的一類;
3) 使用反電動(dòng)勢(shì)法的一類;
4)與前三類不同,采用新技術(shù)的一類。
3.2 輪轂電機(jī)制動(dòng)的比較與選擇
3.2.1 鼓式制動(dòng)
鼓式制動(dòng)器也叫塊式制動(dòng)器(如圖3-1),是靠制動(dòng)塊在制動(dòng)輪上壓緊來實(shí)現(xiàn)剎車的。鼓式制動(dòng)是早期設(shè)計(jì)的制動(dòng)系統(tǒng),其剎車鼓的設(shè)計(jì)1902年就已經(jīng)使用在馬車上了,直到1920年左右才開始在汽車工業(yè)廣泛應(yīng)用。鼓式制動(dòng)器的主流是內(nèi)張式,它的制動(dòng)塊(剎車蹄)位于制動(dòng)輪內(nèi)側(cè),在剎車的時(shí)候制動(dòng)塊向外張開,摩擦制動(dòng)輪的內(nèi)側(cè),達(dá)到剎車的目的[7]。近三十年中,鼓式制動(dòng)器在轎車領(lǐng)域上已經(jīng)逐步退出讓位給盤式制動(dòng)器。但由于成本比較低,仍然在一些經(jīng)濟(jì)類轎車中使用,主要用于制動(dòng)負(fù)荷比較小的后輪和駐車制動(dòng)。
優(yōu)點(diǎn):
鼓式制動(dòng)器造價(jià)便宜,而且符合傳統(tǒng)設(shè)計(jì)。 四輪轎車在制動(dòng)過程中,由于慣性的作用,前輪的負(fù)荷通常占汽車全部負(fù)荷的70%-80%,前輪制動(dòng)力要比后輪大,后輪起輔助制動(dòng)作用,因此轎車生產(chǎn)廠家為了節(jié)省成本,就采用前盤后鼓的制動(dòng)方式。不過對(duì)于重型車來說,由于車速一般不是很高,剎車蹄的耐用程度也比盤式制動(dòng)器高,因此許多重型車至今仍使用四輪鼓式的設(shè)計(jì)。
缺點(diǎn):
鼓式制動(dòng)器的制動(dòng)效能和散熱性都要差許多,鼓式制動(dòng)器的制動(dòng)力穩(wěn)定性差,在不同路面上制動(dòng)力變化很大,不易于掌控。而由于散熱性能差,在制動(dòng)過程中會(huì)聚集大量的熱量。制動(dòng)塊和輪鼓在高溫影響下較易發(fā)生極為復(fù)雜的變形,容易產(chǎn)生制動(dòng)衰退和振抖現(xiàn)象,引起制動(dòng)效率下降。另外,鼓式制動(dòng)器在使用一段時(shí)間后,要定期調(diào)校剎車蹄的空隙,甚至要把整個(gè)剎車鼓拆出清理累積在內(nèi)的剎車粉。
圖3-1 鼓式制動(dòng)器
3.2.2 浮鉗式制動(dòng)
盤式制動(dòng)器有液壓型的(如圖3-2),由液壓控制,主要零部件有制動(dòng)盤、分泵、制動(dòng)鉗、油管等。盤式制動(dòng)器散熱快、重量輕、構(gòu)造簡單、調(diào)整方便。特別是高負(fù)載時(shí)耐高溫性能好,制動(dòng)效果穩(wěn)定,而且不怕泥水侵襲,在冬季和惡劣路況下行車,很多轎車采用的盤式制動(dòng)器有平面式制動(dòng)盤、打孔式制動(dòng)盤以及劃線式制動(dòng)盤,其中劃線式制動(dòng)盤的制動(dòng)效果和通風(fēng)散熱能力均比較好。
盤式制動(dòng)器沿制動(dòng)盤向施力,制動(dòng)軸不受彎矩,徑向尺寸小[8]。
優(yōu)點(diǎn):
一般無摩擦助勢(shì)作用,因而制動(dòng)器效能受摩擦系數(shù)的影響較小,即效能較穩(wěn)定;浸水后效能降低較少,而且只須經(jīng)一兩次制動(dòng)即可恢復(fù)正常;在輸出制動(dòng)力矩相同的情況下,尺寸和質(zhì)量一般較?。恢苿?dòng)盤沿厚度方向的熱膨脹量極小,不會(huì)象制動(dòng)鼓的熱膨脹那樣使制動(dòng)器間隙明顯增加而導(dǎo)致制動(dòng)踏板行程過大;較容易實(shí)現(xiàn)間隙自動(dòng)調(diào)整,其他保養(yǎng)修理作業(yè)也較簡便。
1)熱穩(wěn)定性較好。因?yàn)橹苿?dòng)摩擦襯塊的尺寸不長,其工作表面的面積僅為制動(dòng)盤面積的12%~6%,故散熱性較好。
2)水穩(wěn)定性較好。因?yàn)橹苿?dòng)襯塊對(duì)盤的單位壓力高,易將水?dāng)D出,同時(shí)在離心力的作用下沾水后也易于甩掉,再加上襯塊對(duì)盤的擦拭作用,因而,出水后只需經(jīng)一、二次制動(dòng)即能恢復(fù)正常;而鼓式制動(dòng)器則需經(jīng)過十余次制動(dòng)方能恢復(fù)正常制動(dòng)效能。
3)制動(dòng)力矩與汽車前進(jìn)和后退行駛無關(guān)。
4)在輸出同樣大小的制動(dòng)力矩的條件下,盤式制動(dòng)器的質(zhì)量和尺寸比鼓式要小。
5)盤式的摩擦襯塊比鼓式的摩擦襯片在磨損后更易更換,結(jié)構(gòu)也較簡單,維修保養(yǎng)容易。
6)制動(dòng)盤與摩擦襯塊間的間隙小(0.05~0.15mm),這就縮短了油缸活塞的操作時(shí)間,并使制動(dòng)驅(qū)動(dòng)機(jī)構(gòu)的力傳動(dòng)比有增大的可能。
7)制動(dòng)盤的熱膨脹不會(huì)像制動(dòng)鼓熱膨脹那樣引起制動(dòng)踏板行程損失,這也使間隙自動(dòng)調(diào)整裝置的設(shè)計(jì)可以簡化。
缺點(diǎn):
盤式制動(dòng)器有自己的缺陷。例如對(duì)制動(dòng)器和制動(dòng)管路的制造要求較高,摩擦片的耗損量較大,成本貴,而且由于摩擦片的面積小,相對(duì)摩擦的工作面也較小,需要的制動(dòng)液壓高,必須要有助力裝置的車輛才能使用是效能較低,故用于液壓制動(dòng)系統(tǒng)時(shí)所需制動(dòng)促動(dòng)管路壓力較高,一般要用伺服裝置。
兩個(gè)粘有摩擦襯面的摩擦盤能在花鍵軸上來回滑動(dòng),是制動(dòng)器的旋轉(zhuǎn)部分。當(dāng)制動(dòng)時(shí),能在極短時(shí)間使車輛停止。再加上壓盤上球槽的傾斜角不可能無限大,所以制動(dòng)不平順。
綜上所述,顯然盤式制動(dòng)器在安全性及性能上更加貼合本文對(duì)制動(dòng)性能的要求,所以即在本次設(shè)計(jì)中四個(gè)裝備有輪轂電機(jī)的車輪均由浮鉗式制動(dòng)器來對(duì)電動(dòng)汽車進(jìn)行制動(dòng)。
圖3-2 浮鉗式制動(dòng)器
3.3 本章小結(jié)
本章主要通過分析了電機(jī)部分的幾種性能的比較得出永磁無刷直流電動(dòng)機(jī)的性能參數(shù)更符合本文輪轂電機(jī)技術(shù)對(duì)電機(jī)部分的要求以及在制動(dòng)器的選擇上,通過永磁無刷直流電動(dòng)機(jī)和浮鉗式制動(dòng)器的配合,對(duì)整車的制動(dòng)性能可以有一個(gè)更加出色的制動(dòng)效果,使得整車的安全性、可靠性、耐久性方面比其他幾種方案更加合適。
第四章 汽車總體性能及關(guān)鍵零部件的設(shè)計(jì)和選用
4.1 電動(dòng)汽車動(dòng)力性能計(jì)算
當(dāng)電動(dòng)汽車在坡路上加速形式是,所受到的阻力包括滾動(dòng)阻力、空氣阻力、坡度阻力與加速阻力,電動(dòng)汽車的驅(qū)動(dòng)力等于阻力的總和,電動(dòng)汽車的行駛方程為:
(4-1)
式中:m為汽車總質(zhì)量;f為滾動(dòng)阻力系數(shù);為坡度;為空氣阻力系數(shù);A為迎風(fēng)面積;為行駛車速;為車輛旋轉(zhuǎn)質(zhì)量換算系數(shù)[9]。
電動(dòng)汽車的總功率等于滾動(dòng)阻力消耗的功率、空氣阻力消耗的功率、坡度阻力所消耗的功率與加速阻力所消耗的功率之和,電動(dòng)汽車的功率平衡方程為:
式中,為電動(dòng)機(jī)輸出總功率。電動(dòng)汽車的動(dòng)力性能評(píng)價(jià)指標(biāo)與傳統(tǒng)燃油車相同,主要評(píng)價(jià)指標(biāo)有三種:最高車速、加速時(shí)間與最大爬坡角度[10]。電動(dòng)汽車的最高車速是指在無風(fēng)條件下,在水平良好路面上滿載時(shí)所能達(dá)到的最高車速;加速時(shí)間是指在無風(fēng)條件下電動(dòng)汽車以最強(qiáng)的動(dòng)力啟動(dòng)后加速到某一時(shí)速所需時(shí)間;最大爬坡角度是指電動(dòng)汽車在良好平整路面滿載時(shí)以最低車速上坡行駛的最大坡度。
電動(dòng)汽車最高車速可以通過電動(dòng)機(jī)最高轉(zhuǎn)速與輪胎外徑確定,即
(4-2)
式中:D為輪胎外徑;為電動(dòng)機(jī)的最高轉(zhuǎn)速。
電動(dòng)汽車從速度加速到速度所需時(shí)間為:
(4-3)
電動(dòng)汽車最大爬坡角度為:
(4-4)
4.2 輪轂電機(jī)參數(shù)選擇
輪轂電機(jī)參數(shù)的選擇要依據(jù)電動(dòng)汽車的基本參數(shù),包括迎風(fēng)面積A、汽車總質(zhì)量m、最高時(shí)速、加速與爬坡能力、輪轂與輪胎的相關(guān)參數(shù)等。為適應(yīng)實(shí)際需求以及體現(xiàn)設(shè)計(jì)的合理性 ,本文參考用途與某德系公司電動(dòng)車中的小型乘用車相像的車型的相關(guān)指標(biāo)用以進(jìn)行相應(yīng)參考計(jì)算,選取電動(dòng)汽車相關(guān)參數(shù)如表所示[11]。
表4-1 某德系汽車相關(guān)參考參數(shù)
車輛主要參數(shù)要求
單位
數(shù)值
迎風(fēng)面積
2.38
汽車總質(zhì)量
1500
最高時(shí)速
110
最大爬坡角度
18
爬最大坡度時(shí)速
20
0~60km/h加速時(shí)間
20
輪轂外徑
381
輪胎外徑
500
滾動(dòng)阻力系數(shù)
0.016
空氣阻力系數(shù)
0.4
旋轉(zhuǎn)質(zhì)量換算系數(shù)
1.03
4.3 轉(zhuǎn)速的確定
電動(dòng)機(jī)轉(zhuǎn)速的確定不僅與電動(dòng)汽車行駛速度有關(guān),還與輪胎的外徑相關(guān)。
城市中通暢的道路平均車速為40~60km/h,應(yīng)選定電動(dòng)機(jī)經(jīng)常工作的轉(zhuǎn)速在額定轉(zhuǎn)速附近。本文選擇,根據(jù)上節(jié)公式可得電動(dòng)機(jī)的額定轉(zhuǎn)速,同時(shí)根據(jù)電動(dòng)汽車最高時(shí)速可確定電動(dòng)機(jī)的最大轉(zhuǎn)速。
4.4 功率的確定
電動(dòng)機(jī)額定功率的選擇是非常關(guān)鍵的,在電動(dòng)汽車的運(yùn)行中,應(yīng)該經(jīng)常使輪轂電機(jī)運(yùn)行在額定功率附近。若電動(dòng)機(jī)的額定值選擇過小,則運(yùn)行時(shí)要經(jīng)常處于過載狀態(tài),使之壽命降低;若額定值選擇過大,則運(yùn)行時(shí)要經(jīng)常處于欠載狀態(tài),對(duì)電動(dòng)機(jī)沒有充分利用,使電動(dòng)汽車的綜合效率降低,通常,從保證汽車預(yù)期的車速、加速能力和爬坡能力來初步選擇電動(dòng)機(jī)應(yīng)有的功率。
電動(dòng)汽車以最大速度在水平路面上行駛消耗的功率為:
(4-5)
電動(dòng)汽車以某一車速爬上一定坡度消耗的功率為:
(4-6)
電動(dòng)汽車在水平路面上加速行駛消耗的功率為:
(4-7)
電動(dòng)汽車的最大功率應(yīng)滿足汽車對(duì)最高車速、加速度以及爬坡度的要求,所以電動(dòng)汽車電動(dòng)機(jī)的最大功率為:
當(dāng)電動(dòng)汽車以最高時(shí)速在水平路面上行駛時(shí),通過公式得出消耗功率。由于當(dāng)電動(dòng)汽車以時(shí)速爬坡角度時(shí),通過公式得出消耗功率。由于電動(dòng)汽車加速時(shí)并不是勻加速運(yùn)動(dòng),公式中的不是常數(shù),加速運(yùn)行時(shí)每個(gè)時(shí)刻消耗功率不能簡單的用公式進(jìn)行計(jì)算。車輛經(jīng)常的形式速度要低于最高車速,也不會(huì)經(jīng)常以時(shí)速爬最大坡角,所以選擇電動(dòng)汽車的額定功率為20kW,每個(gè)輪轂電機(jī)的額定功率為5kW。由于永磁同步電動(dòng)機(jī)有較強(qiáng)的過載能力,電動(dòng)汽車的最大功率為30kW,每個(gè)輪轂電機(jī)最大功率為7.5kW,這也為加速與爬坡留下了足夠的后備功率[12]。
4.5 轉(zhuǎn)矩校核
任意時(shí)刻的轉(zhuǎn)矩、功率與轉(zhuǎn)速三者的關(guān)系是:
電動(dòng)汽車以最大速度在水平路面上行駛的最大轉(zhuǎn)矩為:
(4-8)
在爬坡的工況下電動(dòng)汽車最大轉(zhuǎn)矩表達(dá)式為:
(4-9)
通過公式計(jì)算得出功率與轉(zhuǎn)速的選擇滿足水平路面最大速度和在最大爬坡的工況下最大轉(zhuǎn)矩的要求[13]。
4.6 加速性能校核
加速時(shí)間是加速性能最重要的指標(biāo),車速從0加速到所需要的時(shí)間為:
(4-10)
式中:為車輪轉(zhuǎn)矩;為輸出功率。
通過公式先計(jì)算得出,可進(jìn)一步算出車速從0~60km/h的加速時(shí)間t為20s,從而滿足加速要求[14]。
4.7 初選幾段重要軸頸尺寸
根據(jù)電機(jī)的峰值功率=7.5kW,和電機(jī)的峰值轉(zhuǎn)速,可求出電機(jī)受力部分的最小軸頸:
(4-12)
考慮電機(jī)軸采用40Cr,通過查表可知,A=103,故
根據(jù)電機(jī)的工作需求,初定電機(jī)輸出軸結(jié)構(gòu)如圖4.1所示。下述進(jìn)行各段重要軸頸的選取。
圖4-1 電機(jī)軸結(jié)構(gòu)示意圖
4.7.1 根據(jù)最大垂直工況設(shè)計(jì)
(4-