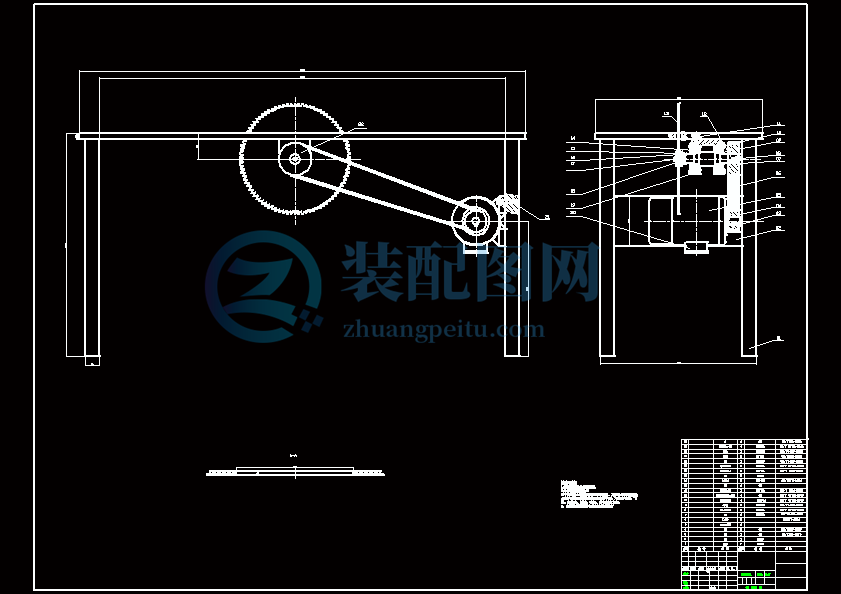
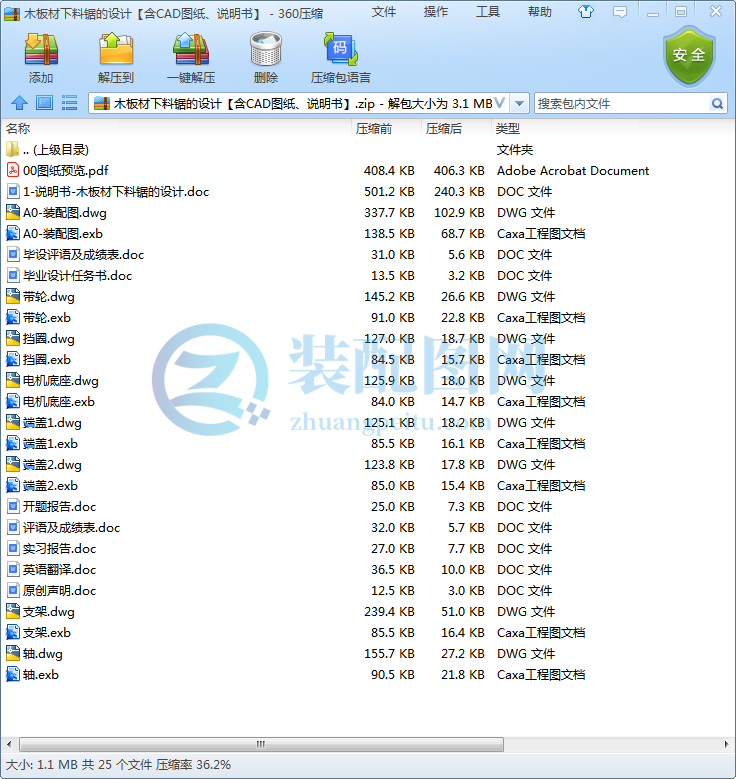
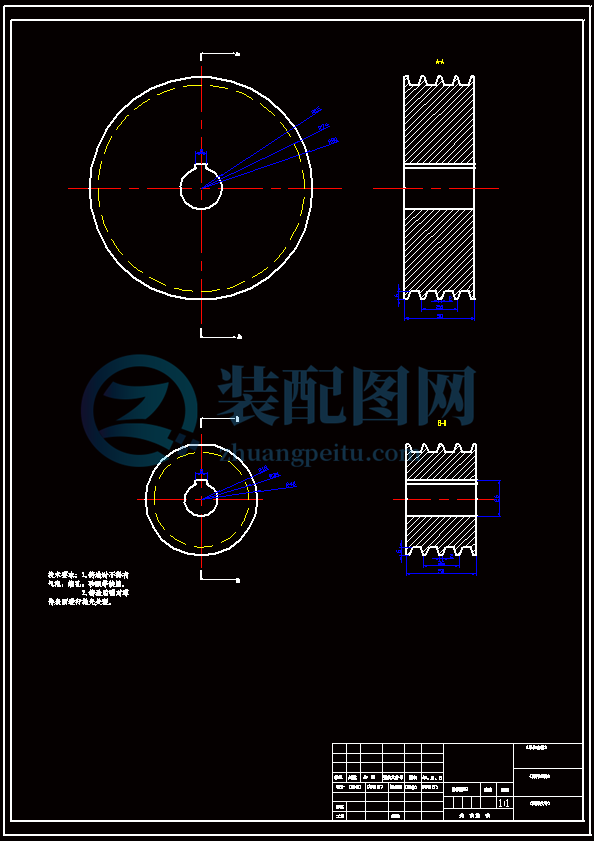
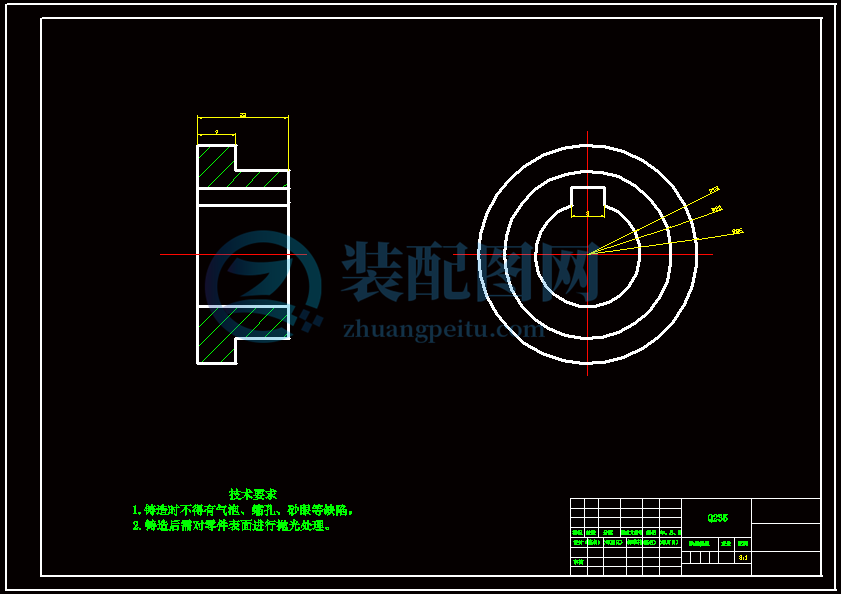
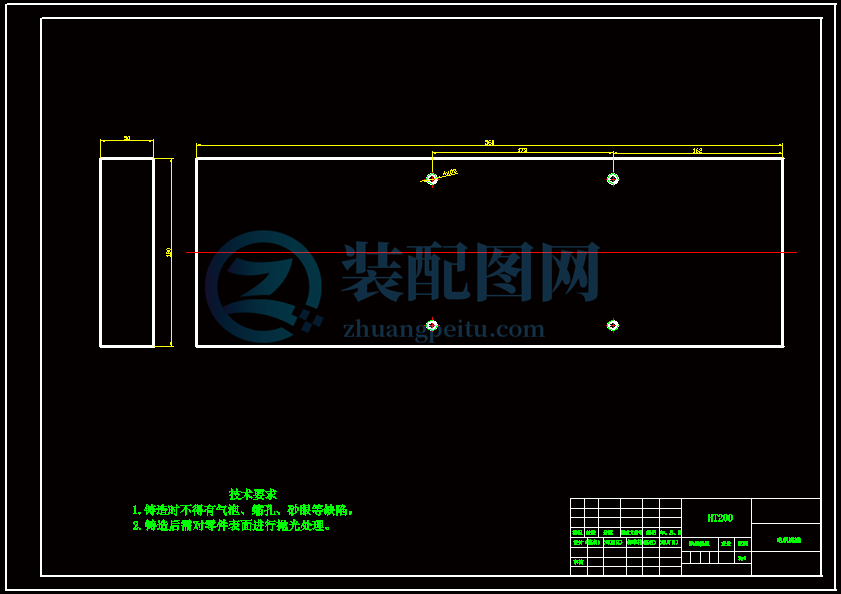
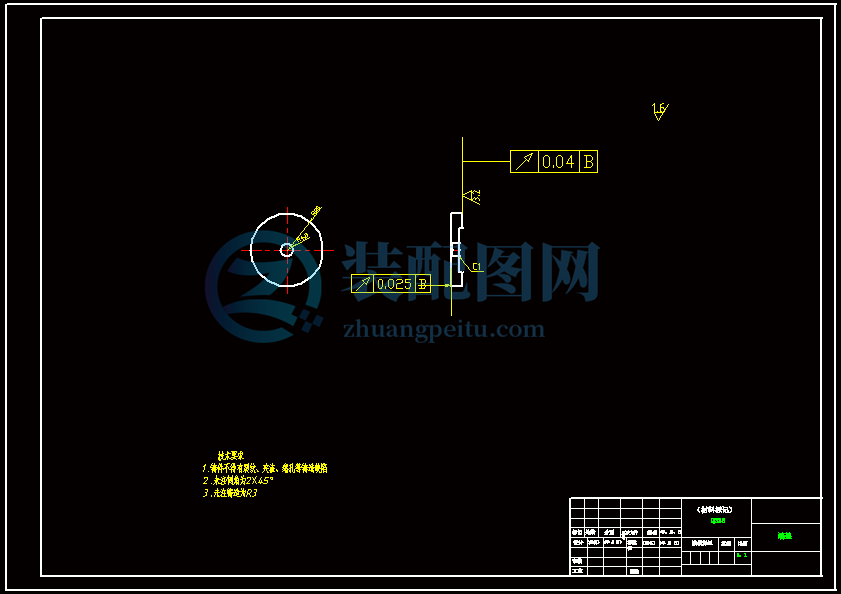
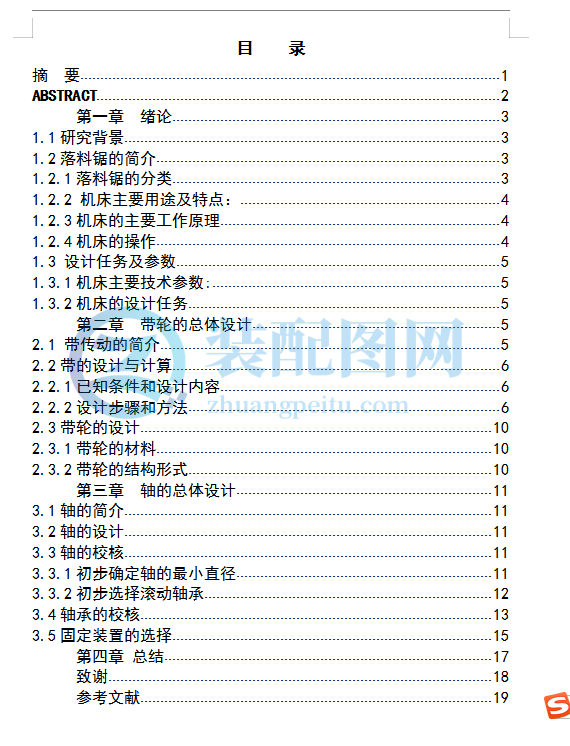
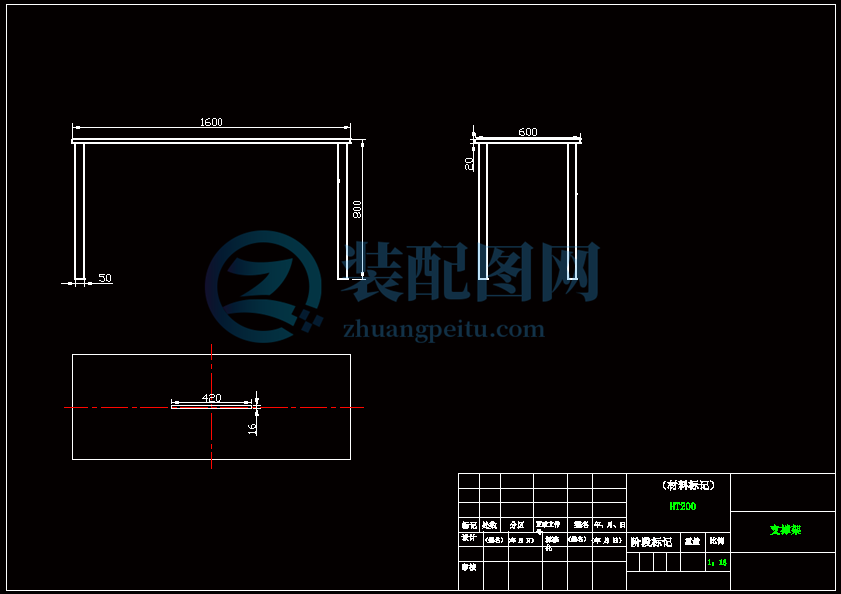
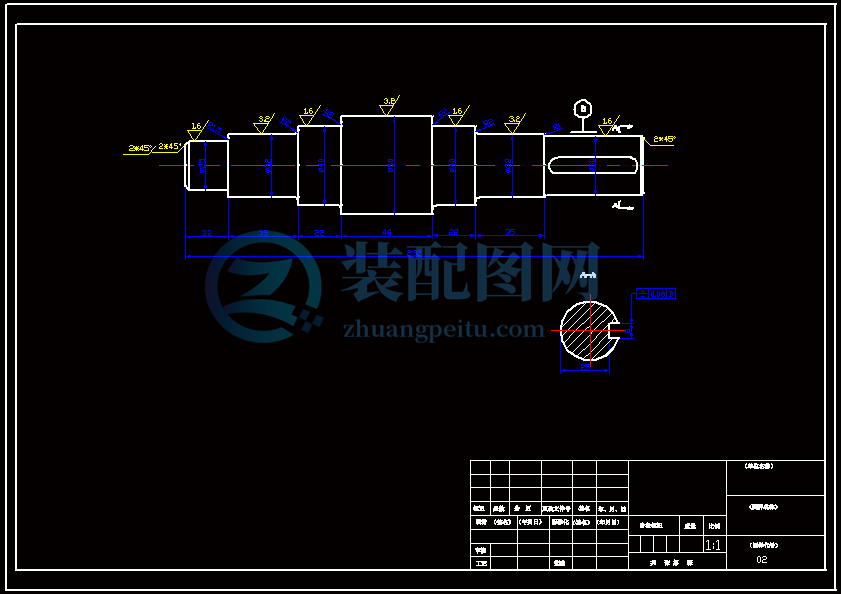
英文資料及中文翻譯
院系名稱 機(jī)械工程學(xué)院
學(xué)生姓名
專業(yè)班級
指導(dǎo)教師
英文原文
Rapid Prototyping and manufacturing
Introduction
The term “rapid prototyping” (RP) is a relatively new expression for the generation of three-dimensional models manufactured without the need for machining or products designed on a computer aided design system, the first rapid prototyping system was introduced on to the US market in 1988 and gave the engineer the opportunity to produce 3 dimensional objects directly from Computer Aided Design (CAD) date and succeed in the cost-effective production of patterns and moulds with complex surfaces.
The principle advantages of using this technology are:
High speed at which the solid model is generated.
The complexity of the model does not form any limitation to its production.
The early use of these models was to assist the designer in determining fitness and form. It also provided the sales team with a 3 dimensional object to show to a prospective customer, this being far better than the traditional orthographic drawing which many people find difficult to interpret. The benefits of RP:
1.Converts 3D CAD images into accurate physical models at a fraction of the cost of traditional methods.
2.Improves design communication and helps eliminate design mistakes.
3.Reduces “time to market” for a new product.
4.Can be used as a powerful marketing tool since the prototype can be seen rather than the drawing.
5..The development of this technology has reached into many of the traditional fields, attracting the interest of artisans whose skill any knowledge has led to 3-D objects being used directly and indirectly as patterns and model for soft tooling.
6.Production of models by machining has a number of limitations.
7. Material removed during forming is difficult to reclaim.
8.Machining in the form of drilling turning milling spark erosion etc., is limited by the shapes it can produce.
9.In the event of design change, conventional tooling such as patterns ,core boxes, dies, jigs etc. ,become expensive to alter ,and in many cases, may require complete re-manufacture.
What RP&M CAN DO?
To substantially shorten the time for developing patterns, moulds, and prototypes, some manufacturing enterprises have started to use rapid prototyping methods for complex patterns making and component prototyping. Over the past few years, a variety of new rapid manufacturing technologies, generally called Rapid Prototyping and Manufacturing(RP&M),have emerged ;the technologies developed include Stereo lithography (SL), selected laser sintering(SLS),fused deposition modeling(FDM),laminated object manufacturing(LOM),and three dimensional printing (3D Print).They have a common important feature ;the prototype part is produced by adding materials rather than removing materials. This simplifies the 3D part producing processes to 2D layer adding processes so that a part can be produced directly from its computer model.
Rapid prototyping differs with conventional manufacturing methods by adding material layer by layer until the desired sharp is achieved, immediately reducing or avoiding the loss of material.
THE BASIC PROCESS IN RP
RP machines process CAD data by slicing the computer model into layers ,each layer being typically 0.1-0.25mm thick the machine then uses this data to construct the model layer by layer ,each layer being bonded to the previous until a solid object is formed. Due to this laminated method of construction a stepped surface is developed on curved faces, the removal of which is essential if maximum advantage of the process is to be realized. Schematic representation of the stepped construction, which requires post processing, is on the above Figure8.1.
DEVELOPMENT
More recent developments have been prompted by problems caused by the expansion of the model where it is used as a disposable pattern (like the wax pattern in the lost wax process), Where the resin model is produced to form solid walls, expansion during the “burning-out” stage weakens the ceramic shell, and can cause failure in the firing and/or casting stages.
The company, 3D System GmbH, has developed a machine and software, which together allow for the model to be constructed in the form of a honeycomb. The honeycomb structure collapses in on itself during “burning-out” thus avoiding the problems of expansion. Each pocket of the honeycomb structure is connected to its neighbor by a small hole that allows for the uncured resin to be drained prior using. Other methods of producing tooling directly from the rapid prototype-such as metal spraying –are also being developed, and this seems to have potential in the production of less complex parts, although it is inevitable that some detail will be lost. Prototyping Company ARRK EUROPE LTD, London, has developed a thin layer technology, which removes many of the inaccuracies inherent in mechanical finishing. It claims to be the first company in the world to achieve 0.05mm layer build accuracy.
ARRK’s development team used a combination of subtle mechanical alterations to setting up of its four stereo lithography (SL) rapid prototyping machines and proprietary techniques to over come de-wetting. It also called upon its knowledge of resins.
THE BASIC PROCESS IN RP
RP machines process CAD data by slicing the computer model into layers ,each layer being typically 0.1-0.25mm thick the machine then uses this data to construct the model layer by layer ,each layer being bonded to the previous until a solid object is formed. Due to this laminated method of construction a stepped surface is developed on curved faces, the removal of which is essential if maximum advantage of the process is to be realized. Schematic representation of the stepped construction, which requires post processing, is on the above Figure8.1.
Using this new technology, the company is now able to produce extremely accurate high-quality master parts and tooling. With 0.05mm layer, the build is more precise and all but eliminates the stair-stepping effect. In addition, the need for finishing is dramatically reduced. As a result, the process is ideal for switches, electronic components or any finely details part.
Current Application Areas of RP&M
Design Engineering
(1) Visualization
With RP&M, the prototype of a complex part can be built in short time, therefore engineers canevaluate a design very quickly, for it isn’t difficult to visualize exactly what the actual complex product will look like.
(2) Verification and optimization
Improving product quality is always an important issue of manufacturing. An RP&M prototype can be produced quickly without substantial tooling and labor cost. As a result, the product quality can be improved within the limited time frame and with affordable cost.
(3) Iteration
With RP&M technology, it is possible to go through multiple design iterations within a short time and substantially reduce the model development time.
Manufacturing
We can use the RP&M prototype for productively studies. By providing a physical product at an earlier design stage, we can speed up process planning and tooling design. In addition, by accurately describing complex geometry, the prototype can help reduce problems in interpreting the blue prints on the shop floor. It can also be used in tooling development for mould and master pattern for castings.
Marketing
To assist product sales, a prototype can be used to demonstrate the concept, design ideas, as well as the company’s ability to produce it. The reality of the physical model illustrates the feasibility of the design. Also, the prototype can be used to gain customs’ feedback for design modification so that the final product will meet customs’ requirement.
中文翻譯
快速成型和生產(chǎn)
介紹
快速成型這個術(shù)語是對于不通過機(jī)器和工具的三維造型生產(chǎn)而產(chǎn)生的一種新的相關(guān)的表示.通過快速生產(chǎn)的準(zhǔn)確能力,用電腦設(shè)計系統(tǒng)幫助切實的造型的設(shè)計生產(chǎn),第一個快速成型的系統(tǒng)于1988年在美國的市場內(nèi)被引進(jìn)并且給工程師一個通過CAD 來設(shè)計三維實物的機(jī)會且成功的生產(chǎn)出復(fù)雜表面的模型.
使用這項技術(shù)的操作優(yōu)勢如下:
固態(tài)模型的高速產(chǎn)生.
這個模型的復(fù)雜性對于生產(chǎn)不能形成任何的限制.
最早使用這些模型是用來幫助設(shè)計者決定形狀和適當(dāng)性.它也能提供給預(yù)期的顧客展示三維實物的銷售群,這將遠(yuǎn)遠(yuǎn)優(yōu)于那些很多人發(fā)現(xiàn)很難去解釋的傳統(tǒng)直角作圖.
快速成型的好處:
1.一小部分傳統(tǒng)方法的價值是把準(zhǔn)確的物理模型轉(zhuǎn)化成三維影象.
2.改進(jìn)設(shè)計的訊息幫助刪除設(shè)計的錯誤.
3.對于新的產(chǎn)品減短上市的時間.
4.自從原形相比做圖更能被理解后它就能作為一種強(qiáng)有力的工具.
5.這技術(shù)的發(fā)展到達(dá)了入許多傳統(tǒng)領(lǐng)域,吸引技巧和知識導(dǎo)致了直接地和間接地使用作為樣式和模型的三維對象為軟的工具模型。
6.模型的生產(chǎn)是通過用機(jī)器制造有一定數(shù)量的限制。
7.在成形期間被除去的材料是難回收的。
8.用機(jī)器制造以鉆井轉(zhuǎn)動的碾碎的火花電蝕等的形式。 由它可能導(dǎo)致的形狀限制。
9.在設(shè)計變動情形下,常規(guī)鑿出的裝飾例如樣式,核心裝箱,模子,夾具等。 變得昂貴而難變更,并且在許多情況下,可以要求完全再制造??焖俪尚头ㄊ遣煌谝酝ㄟ^增加物層數(shù)的常規(guī)制造方法,直到達(dá)到所期望的銳利程度,立刻減少或避免材料的損失層數(shù)。
RP&M能做什么?
為開發(fā)的樣式、模子和原型去極大地縮短時間。一些制造業(yè)企業(yè)開始對于一些復(fù)雜部件的制造和成型的成分使用快速成型的方法。在過去幾年,各種各樣新的迅速制造業(yè)技術(shù),通常稱為快速成型和制造(RP&M),已經(jīng)涌現(xiàn)了;被開發(fā)的技術(shù)包括立體聲石版印刷(SL),所選擇的激光焊接(SLS),合并的證言塑造(FDM),薄片疊成物體的制造業(yè)(LOM),和3D打印(3D Print)。他們有一個共同的重要特點; 原型零件是通過增加材料而不是除去材料導(dǎo)致的。這簡化3D部分生產(chǎn)過程到增加過程的第2層數(shù),以便零件可以直接地由它的計算機(jī)模型生產(chǎn)。
快速成型的基本過程
快速成型的機(jī)器是通過切計算機(jī)模型來制造處理CAD數(shù)據(jù)入層數(shù),每層數(shù)是典型地0.1-0.25毫米厚的機(jī)器然后使用這數(shù)據(jù)一層一層去修建,每一層都將被拈合成以前的樣子直到一個堅實對象被形成。由于這個建筑被碾壓的方法一個有臺階的表面在彎曲的表面上被開發(fā),如果過程的最大好處被了解,那么其中是根本的將被撤除,有臺階建筑的圖示,是要求分步處理的.
發(fā)展
更多的發(fā)展由與模型的擴(kuò)展而引起的問題已經(jīng)提示了,使用它就像一個一次性部件(象蠟本身在失去蠟過程中),那里的合成樹脂模型導(dǎo)致了形成堅實的墻壁,擴(kuò)展在“燃燒的”階段期間來減弱陶瓷的外殼,并且在生火和鑄件階段都能導(dǎo)致失敗。
3D系統(tǒng)GmbH公司,開發(fā)了機(jī)器和軟件,一起允許模型以蜂窩的形式被修建。 蜂窩結(jié)構(gòu)在本身崩潰在“燃燒的”因而避免擴(kuò)展的問題。 蜂窩結(jié)構(gòu)的每個口袋通過一個小孔連接到它的旁邊從而考慮到未固化的樹脂在使用之前被排泄出去。
其它快速成型的工具直接加工的方法-比如金屬噴鍍-也被開發(fā),并且看上去這在較不復(fù)雜零件的生產(chǎn)似乎有潛力,但不可避免的一些細(xì)節(jié)將丟失。
ARRK有限公司是快速成型的歐洲公司,倫敦,已經(jīng)開發(fā)了薄片技術(shù),這除去了很多在機(jī)械加工中固有的不準(zhǔn)確性。他們宣稱他們是世界上第一家能夠達(dá)到0.05毫米厚度的準(zhǔn)確制造。ARRK的開發(fā)小組使用了微妙的機(jī)械改變的組合到它的四個立體聲石版印刷(SL),快速成型的機(jī)器安裝,并且私有的技術(shù)去克服濕度。 它也要求了對于樹脂的知識.
使用這種新技術(shù),公司現(xiàn)在能生產(chǎn)極端準(zhǔn)確優(yōu)質(zhì)主要零件和工具。 以0.05mm層數(shù),所有的修造是精確的,除了消滅臺階跨步的作用。 另外,顯著減少對精整的需要。 結(jié)果,過程作為理想的開關(guān),電子元件是理想的或其中任一微小的詳細(xì)的部件。
快速成型和制造的當(dāng)前應(yīng)用的區(qū)域
設(shè)計工程
?。?) 形象
運用快速成型和制造技術(shù), 一個復(fù)雜部分的原型在短期可以被制作,因此工程師能非常迅速的評估設(shè)計,因為這很難確切的使實際復(fù)雜的產(chǎn)品看上去形象化。
?。?) 證明和優(yōu)化
改進(jìn)產(chǎn)品質(zhì)量總是制造業(yè)的一個重要問題。快速成型和制造能夠快速的生產(chǎn)不用堅固的工具和人工成本。結(jié)果,產(chǎn)品質(zhì)量可以改進(jìn)在有限的時間表之內(nèi)和以付得起的費用。
?。?) 疊代
運用快速成型和制造技術(shù),在短時間內(nèi)審閱多樣的設(shè)計疊代和極大地減少式樣研制時間是可能的。
制造
我們可以為有生產(chǎn)力地使用快速成型和制造原型學(xué)習(xí)。 通過提供一個物理產(chǎn)品在更加初期的設(shè)計,我們可以加速處理計劃和鑿出的裝飾設(shè)計。 另外,通過準(zhǔn)確描述復(fù)雜幾何,原型在解釋方案可能幫助減少問題在車間上。 可能也用于工具的發(fā)展為模子和主模澆鑄。
營銷
要協(xié)助產(chǎn)品銷售,原型可以用于展示概念,設(shè)計想法,是由公司的能力導(dǎo)致它。物理模型的現(xiàn)實說明設(shè)計的可行性。 并且,原型可以用于獲取顧客的反饋為設(shè)計修改,以便最終的產(chǎn)品將符合顧客的要求。