模具的制造技術與制作要點(doc44頁)
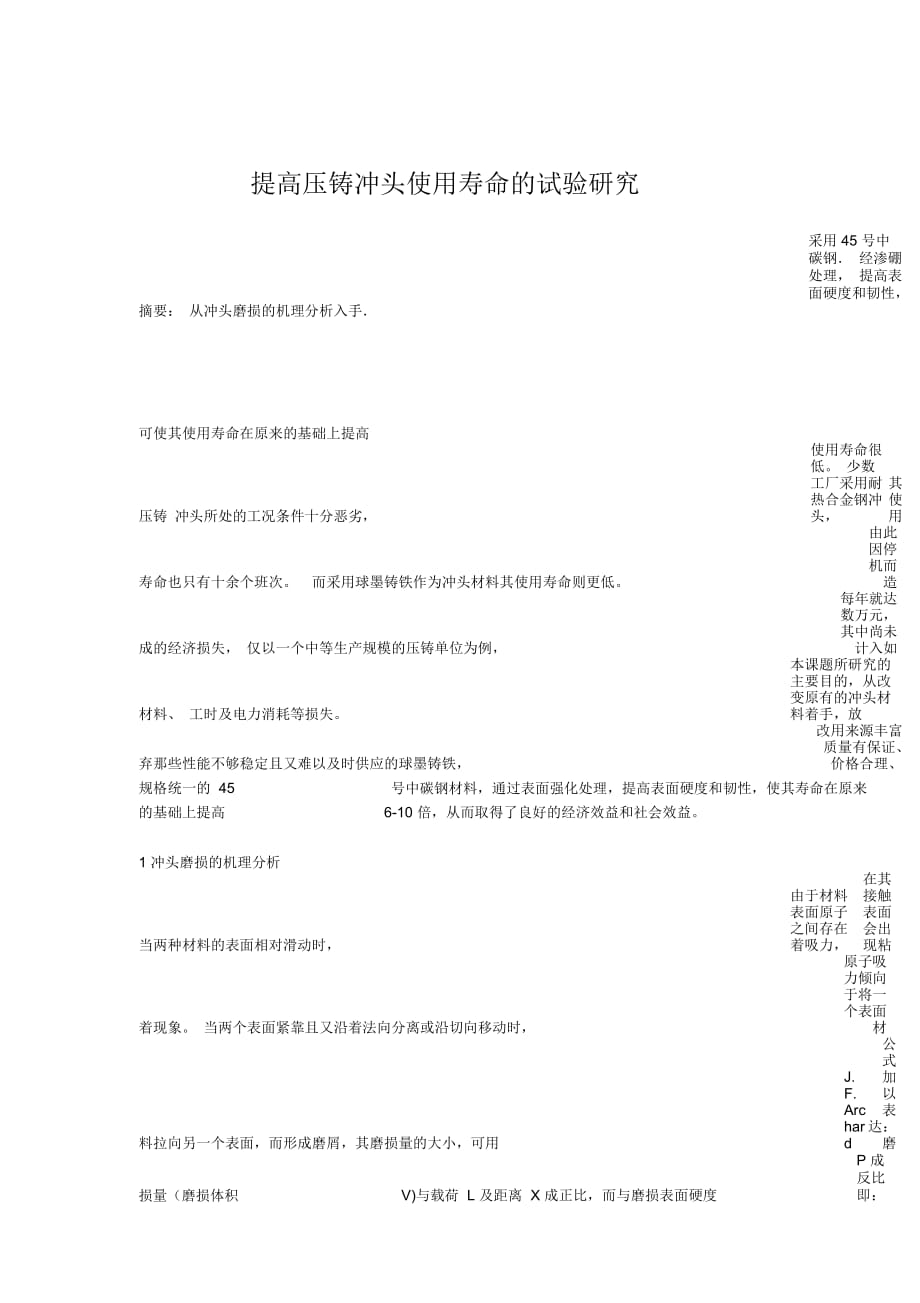


《模具的制造技術與制作要點(doc44頁)》由會員分享,可在線閱讀,更多相關《模具的制造技術與制作要點(doc44頁)(68頁珍藏版)》請在裝配圖網(wǎng)上搜索。
1、 提高壓鑄沖頭使用壽命的試驗研究 摘要: 從沖頭磨損的機理分析入手. 采用 45 號中碳鋼. 經(jīng)滲硼處理, 提高表面硬度和韌性, 可使其使用壽命在原來的基礎上提高 6-10 倍。 壓鑄 沖頭所處的工況條件十分惡劣, 使用壽命很低。 少數(shù)工廠采用耐熱合金鋼沖頭, 其使用 壽命也只有十余個班次。 而采用球墨鑄鐵作為沖頭材料其使用壽命則更低。 由此因停機而造 成的經(jīng)濟損失, 僅以一個中等生產(chǎn)規(guī)模的壓鑄單位為例, 每年就達數(shù)萬元, 其中尚未計入如 材料、 工時及電力消耗等損失。 本課題所研究的主要目的,
2、從改變原有的沖頭材料著手,放 棄那些性能不夠穩(wěn)定且又難以及時供應的球墨鑄鐵, 改用來源豐富、 質(zhì)量有保證、 價格合理、 規(guī)格統(tǒng)一的 45 號中碳鋼材料,通過表面強化處理,提高表面硬度和韌性,使其壽命在原來 的基礎上提高 6-10 倍,從而取得了良好的經(jīng)濟效益和社會效益。 1 沖頭磨損的機理分析 當兩種材料的表面相對滑動時, 由于材料表面原子之間存在著吸力, 在其接觸表面會出現(xiàn)粘 著現(xiàn)象。 當兩個表面緊靠且又沿著法向分離或沿切向移動時, 原子吸力傾向于將一個表面材 料拉向另一個表面,而形成磨屑,其磨損量的大小,可用 J
3、. F. Archard 公式加以表達:磨 損量(磨損體積 V)與載荷 L 及距離 X 成正比,而與磨損表面硬度 P 成反比,即: V=KLX / 3P ( 1 ) 式中: K 為磨擦系數(shù)。 K 與潤滑條件、相配的摩擦金屬有關。 此外,磨損體積與構成磨擦付材料的不同硬度之間,存在著平方反比關系。如令 Vs 和分別代表磨擦付中較軟材料的磨損體積和表面硬度; Vh 和 Ph 代表較硬材料的磨損體積和表面硬度,則其間的關系,可按下式表達。 Ps (VS / Vh) 2 =
4、 (Ph / PS) 2 (2) 從摩擦系數(shù) K 及公式 (2) 中得知:為了減少粘著磨損,在選用材料時應注意: 1) 要求減少磨損的表面應選用硬的材料; 2) 應選用表面之間相互作用小或不相容的配對材料作摩擦付。 因此, 我們研究工作的重點放在: 種類并使用潤滑劑來解決。 為了減少粘著磨損, 可以通過提高硬度和改變配對材料的 2 試驗條件 2. 1 選擇試驗用的工件材料的依據(jù) 工件(沖頭)采用了 45 號中碳鋼,此種鋼種屬于調(diào)質(zhì)鋼,最適宜作滲硼處理。其滲硼后
5、的 組織表面, 可以獲得鋸齒狀的硼化物,與基體結合牢固, 耐磨性好,而且還可以通過滲硼后 的淬火、回火來提高基體強度。 45 號中碳鋼的淬火溫度都在 840^860 ℃范圍,與現(xiàn)有的滲硼溫度接近,使?jié)B后的工件可以直接淬火,減少加熱次數(shù)、節(jié)約能源、降低成本。 2. 2 試驗用的滲劑材料 本試驗采用固體粉末滲劑,取其操作簡單方便,不需添置專用設備,滲后容易與工件分離,便于在生產(chǎn)中推廣應用等諸方面的優(yōu)點。 粉末滲劑的主要組成物中計有:碳化硼 (B4C ),為提供硼原子的主要來源,以氟硼酸鉀 (KBF4
6、 )作為活化劑,可加速催滲過程,以碳化硅 (SiC) 作為載體(填充劑)。 固體粉末滲硼原理屬于氣態(tài)催化反應的氣相滲硼。氟硼酸鉀是活性很高的成分,在 530 0C 就可分解,到 800 OC 即全部分解,其所分解出來的氣態(tài)和固態(tài)硼化物,都是促進滲硼的 重要物質(zhì), 是提高滲劑活性和參與滲硼化學反應最重要的氣體。 在滲硼溫度下由 KBF4 熱分 解所形成的氣態(tài) BF3 的反應式如下: KBF4>530 0C KF+BF3 ↑ BF3 在滲硼溫度下與 B4C
7、 中因氧化而形成的 B203 發(fā)生強烈的還原反應而生成低價的次氧化硼( B202) 而促進滲硼過程,即: 2 B203 +2BF3 =3B202+3F2 ↑ 此處的 B202 是一種極不穩(wěn)定的氧化物, 會按下式分解, 形成穩(wěn)定的 B2C3 同時釋放出活性硼原子: 3B203 =2B203+2 [B] 氟硼酸鉀熱分解生成的 BF3 可與 B4C 直接產(chǎn)生下列反應,析出硼原子和低價的 BF2: 2BF3+B4C=3BF2 ↑ +3 [B] +C 氟硼酸鉀還與 B,C 在氧的參與下,直接進行下述化學反應而析出硼原
8、子: 2KBF4+B4C+02 =K20+4BF2 ↑ +2「 B〕 +CO ↑ 以上兩式的反應產(chǎn)物中均有 BF2 生成,而 BF2 又因不穩(wěn)定而分解,析出硼原子。由此可以確定,以 B4C 為供硼劑的滲劑活性好、滲速快,這也是我們選用滲劑的理論基礎。 2. 3 試驗的工藝參數(shù) 一般視零件的具體要求來加以選擇。凡是要求變形小而滲硼層較薄者可在臨界點 進行,反之可再提高滲硼溫度。本試驗中選取的處理溫度為 9000C ,保溫時間取 (ACl) 以下 4 小時。 2. 4 工件試
9、樣標準 本工件試樣選用最常用的 J1113 型壓鑄機上的 Φ40-0.05-0.08 沖頭作為標準,見圖 1。 2 . 5 磨耗試樣標準 本磨耗試樣采用國家統(tǒng)一標準。 3 試驗用的設備規(guī)格 試驗用的加熱設備系采用上海實驗電爐廠生產(chǎn)的系列產(chǎn)品驗機的型號為 MM-200 。 SX-2-10-1300 箱式電爐。 磨損試 4 滲硼過程中有關工藝的控制 4. 1
10、 滲硼層厚度的控制 滲硼層的厚度的取得, 主要取決子滲硼溫度的高低和保溫時間的長短, 其間存在著線性關系。 以本工件為例,根據(jù)其使用條件,并從損壞的零件中分析出其失效的主要形式為粘著磨損, 從而得出以提高表面的殘余壓應力、 增加韌性及改進耐熱疲勞性能著眼, 采取平均的滲硼厚 度為 70~80 微米的單相 Fe2B 為宜。 Fe2B 為正方晶體,含硼量為 8. 3% ,熔點為 1389 0 C,硬度約為 HV1400-2000 。 4. 2 滲硼前后工件尺寸變化的規(guī)律 對 45 號中碳鋼沖頭滲硼
11、前后尺寸變化的規(guī)律如表 1 所示,由表可知: 1) 沖頭前部的尺寸, 滲硼以后,其尺寸變化較大; 2) 沖頭后部的尺寸,滲硼以后,其尺寸變化較?。? 3) 沖頭滲硼 前后尺寸變化的幅度一般為 0.022 毫米左右。 判斷 45 號中碳鋼經(jīng)磨削加工后,滲硼前的外徑,要根據(jù)原球墨鑄鐵沖頭與壓室配合間隙的 要求。在室 m 下,壓室內(nèi)徑取 Φ40+0. 027, 沖頭外徑為 (D 40 龍器,相互之間的間隙為 0. 077^0. 107 毫米,兩者皆受到高溫金屬作用后,前者直徑縮小,后者外徑膨脹,其熱狀態(tài) 下的間隙大小,無法檢測,只
12、能通過理論計算求得。 根據(jù)實際使用情況表明, 壓室材料按原來的 3Cr2W8V 鋼,其熱處理工藝不變及尺寸變化規(guī) 律也恒定。但是沖頭材料及熱處理工藝,由于由球鐵改為 45 號中碳鋼以后,其熱膨脹量皆 起了變化。要使 45 號鋼沖頭在受熱膨脹以后的外徑恰好與球鐵沖頭受熱膨脹后的外徑相等, 則必須滿足以下的條件。 即當沖頭的工作溫度如處在 180 ℃,兩種材料的熱膨脹系數(shù)分別為: -6 a 45 鋼= 12 .32 10 / 0C (在 20 ~2000C ) -6 a 球鐵 =11 . 85 10 / 0C
13、 由膨脹公式可知: d=d ?!?1+a ( t-t 。)] 式中: d—最后的直徑, m do — 實物的直徑, mm a— 熱膨脹系數(shù) t— 工作溫度,℃ to 室溫,℃ 為了達到原生產(chǎn)所要求的配合間隙,則必須使: 通過以上計算, 說明滲硼后的沖頭外徑應為 Φ40-0.053-0.083 。根據(jù)實際滲硼后所得到的數(shù)據(jù)中可知, 經(jīng)滲硼后的沖頭,其外徑膨脹了 0.022 毫米左右, ,所以沖頭在加工時經(jīng)過最后一道磨削加工后,其外徑應控制在。 Φ40-0.075-0.105 即 Φ39.895~39.925 毫
14、米范圍內(nèi),即可滿足實際生產(chǎn)的需要。 4. 3 滲硼層表面耐蝕性 滲硼能提高 45 中碳鋼的耐腐蝕性能,在硫酸、鹽酸、檸檬酸及醋酸的稀釋水溶液中分別提 高 50, 60, 15 及 4 倍;在 KOH 及 NaOH 的水溶液中分別提高 4 與 3.6 倍,在 NaCl 液中提高 0.9 倍。 水溶 對于滲硼表面與熔融的純鋁、鋁硅合金及鋅合金等相互作用的結果可參見表 2 45 鋼滲硼表面與熔融合金的相互作用
15、 從以上試驗數(shù)據(jù)中可知,由于滲硼層表面具有較好的耐腐蝕性和與合金所產(chǎn)生的親和力小, 這對沖頭壽命的提高,是有所助益的。因此,滲硼表面只要在 就已可為量大面廣的鋅合金和鋁合金的壓鑄生產(chǎn)創(chuàng)造必要的條件。 況條件有所改善,對于壽命的提高更加有所裨益。 700 0C 以下的條件下工作, 如果沖頭采用水冷, 其工 4. 4 滲硼試樣與氮化試樣相對磨耗試驗結果 磨耗試驗中取氮化后及滲硼后的圓盤試樣, 分別代表壓室及沖頭的實際
16、情況, 經(jīng)成對裝機后, 在受載 50 公斤下對磨,每次以測量精度為 1 / 10000 的精密天平稱其失重量,以檢驗其磨 耗程度。 經(jīng) 223889 次轉(zhuǎn)動后稱重, 氮化試樣總失重量為 0.6782 克,而滲硼試樣為 1.3414 克,即滲硼試樣的磨損比氮化試樣高出一倍,解決了壓室經(jīng)使用后是否會先期磨損的顧慮,為滲硼沖頭的推廣應用,打下良好的基礎。 乘用車發(fā)動機鋁合金缸蓋的低壓鑄造技術 基于成本和力學性能方面綜合考慮, 擴大鋁合金的應用是目前乘用車輕量化, 降低油耗的主要手段, 如發(fā)動機缸蓋現(xiàn)已全實現(xiàn)鋁合金化制造。 盡管鋁合金缸蓋的生產(chǎn)方法
17、有多種, 但主流的制造工藝則是金屬型 鑄造 和低壓鑄造, 其中歐洲和中國以金屬型為主, 而日本、 美國則更多采用低壓鑄造。 相對于重力金屬型鑄造,低壓鑄造由于是在壓力下充型和結晶凝固,因而具有成形質(zhì)量好、 要求高等技術難關。 因此本文著重介紹了鋁合金缸蓋的低壓鑄造技術及其參數(shù)控制要點, 以 期充分發(fā)揮低壓鑄造工藝的技術優(yōu)勢,生產(chǎn)高質(zhì)量的缸蓋鑄件。 2 缸蓋的低壓鑄造工藝要點 2.1 澆注系統(tǒng)實例 缸蓋的低壓鑄造工藝方案一般為一根升液管,多個澆口即多權分流的形式。如 4
18、缸缸蓋, 具有代表性的兩種澆注系統(tǒng)即在燃燒室側(cè)是設置 2 個或 4 個澆口。圖 2 為 2 個澆口的工藝 示意圖,該方案適合于一模一件或一模兩件。 2.2 合金材料及熔化 鋁合金缸蓋的材料一般選擇 AI-Si-Cu 系合金如 ZL105 和 107 。如果對延伸率和耐腐蝕性有要求, 也可以使用 ZL101 和 ZL104 。為獲得高質(zhì)量的金屬液, 標準操作應使用 Ar 氣旋轉(zhuǎn)吹氣精煉并加入 Sr 變質(zhì)及 AJ-Ti-B 細化晶粒。 2.3 澆注工藝 2.3.1 模具維護 模具的定期清
19、理和保養(yǎng)對于穩(wěn)定生產(chǎn)高質(zhì)量的缸蓋鑄件和延長模具的使用壽命是相當重要 的。一般應在每生產(chǎn) 500-700 件后即進行模具維護,其主要內(nèi)容是將模具拆開,用軟刷清 理型腔表面涂料及清除滲入到頂桿間隙、 排氣孔中的鋁屑、 涂料顆粒等, 確保鑄件外形質(zhì)量、 頂出順利和排氣順暢。 2.3.2 涂料 澆注前模具預熱至 200 ℃左右噴涂料。 缸蓋的形狀復雜, 應特別注意不同部位的涂料厚度不 同。一般部位涂料厚度控制在 0.1---0.2mm: 精度要求高如燃燒室表面應采用顆粒細小的涂料,厚度為 O.OSmn 。左右 ;而對于澆口、冒口、內(nèi)澆道等需要緩慢凝
20、固的位置可適當厚一些,一般為 0.5-1 mm 左右。 2.3.3 過濾網(wǎng) 放置過濾網(wǎng)的目的是防止升液管中氧化物雜質(zhì)進入型腔及形成層流充填。 可采用價格便宜效 果良好的鍍鋅金屬網(wǎng),網(wǎng)線直徑叨 .4---0.6mm, 1214 目。 2.3.4 溫度 鋁液溫度對缸蓋內(nèi)部缺陷、外觀質(zhì)量有很大的影響。澆注沮度在 680-730 的范圍內(nèi)為宜, 實際操作中溫度偏差應控制在 20℃以內(nèi)。 低壓鑄造的特點是獲得良好的順序凝固, 后此報具溫度控制在低壓鑄適中待別重要。 理想的 模溫分布是從澆口到上模逐漸降低
21、,一改具各部具體表度控制范圍為獲得 .上述溫度場及提 高缸蓋鑄件性能和縮短生產(chǎn)周期,必須對上模和側(cè)模實施強制冷卻。一般分為水冷和氣冷, 采用多路設置,每路單獨自動控制 ( 流量和壓力 )。水冷卻采用壓送式水泵,以解決模具內(nèi)部 因高溫汽化產(chǎn)生氣阻造成水流不暢的難題,氣冷則是通以壓縮空氣。 因缸蓋具有多個澆口, 兩個澆口之間的距離近會導致位于澆口間的鑄件部位溫度上升, 使?jié)? 口和該部位的凝固順序相反。因此須在此部位設置局部強制冷卻,以得到所需的溫度梯度。 從模具壽命和安全性考慮, 冷卻時應以間接冷卻為主, 在局部鑄件厚度較大處可采用直接冷
22、卻方法。對于冷卻強度有時間控制和溫度控制兩種方式,時間控制即控制通水或氣的時間, 該方法簡單易行, 但精度不高。 溫度控制則是在冷卻位置出設置熱電偶, 根據(jù)熱電偶測得的溫度大小由 PC 來開啟或關閉冷卻水或氣,控制精度相對較高。 近年來, 凝固數(shù)值模擬技術的發(fā)展為缸蓋的低壓鑄造工藝優(yōu)化提供了很好的參考依據(jù), 它可 充分把握不同條件下的凝固測試結果,強化鑄造工藝過程控制,確保鑄件質(zhì)量。 2.3.5 加壓時間 從充型到澆口凝固的時間稱為加壓時間, 受溫度的影響很大。 在穩(wěn)定生產(chǎn)條件下, 加壓時間雖然因缸蓋的重量不同而有所變化, 但一般控制在 2
23、-8min 。若從提高生產(chǎn)效率的角度考慮,可采取一模 2 件、 2 段加壓等方法縮短時間閉。 2.3.6 起模時間 同加壓時間一樣,因溫度的變化而變化。時間短時鑄件易變形 ;時間過長則鑄件易卡在模具 內(nèi),取不出來。所以一般控制在加壓時間的 1/3 左右。為提高鑄件冷卻速度,起模時可先開 脫模阻力小的側(cè)模,冷卻一定時間后再開上模。 2.3.7 加壓曲線 加壓壓力直接影響到金屬液的流動充填性能和補縮效果, 加壓曲線是低壓鑄造工藝控制中的重要一環(huán)。加壓壓力可由下式算出 : P=γ x(1+S/A) x H x 1
24、0 -2 上式中 P-壓力 (MPa), γ-鋁液比重 (2.4- 2.5) , H -鋁液上升高度 (m), S-- 升液管截面積 (m2), A 一型腔截面積 (m2)o 冒口的補縮壓力一般在 0.005-0.01MPa 左右。雖然壓力大補縮效果好,但如果壓力超過 0. 1 Mpa ,會導致涂料剝離、鋁液堵塞模具排氣孔及滲入到砂芯中。澆注過程中及時排出砂 芯燃燒產(chǎn)生的氣體是非常必要的, 但因缸蓋所用砂芯結構復雜、 數(shù)最多, 在模具中設置大量的排氣孔很困難。 此時,將冒口補縮壓力提高到上限附近, 可有效防止氣體卷入
25、到鑄件里面。 柑塌內(nèi)的液面高度變化影響到加壓曲線的重復再現(xiàn)性, 因此柑禍內(nèi)的壓力應能自動補償。于缸蓋鑄件,可通過設置傳感器,以精確控制加壓曲線的零點 I81 。連續(xù)工作加壓曲線示愈圖如圖 3 所示。 對 另外, 若升液管下端與柑拐底部間的間隔過短加壓時溶液易產(chǎn)生紊流流動。 溶液使用的情況下,升液管下端與柑鍋底部間的間隔在 200mm 左右為宜。
26、 因此,在不影響 3 鑄造缺陷與對策 表 1 列出了低壓鑄造常見的缺陷及應采取的暇止措施。針對缸蓋這樣復雜的零件,各種參 數(shù)的細書波動就可能影響鑄件質(zhì)。 因此必須對工藝方案、 奄具設計、 澆注工藝等各方面進行細致的分析和調(diào)查明確缺陷產(chǎn)生的各種原因,在此基礎上來采取相應白解決措施。
27、 4 結束語 迄今為止鋁合金缸蓋是適合于低壓鑄造的幾個有限的汽車零件之一, 因此充分發(fā)揮其工藝出 品率搞、 內(nèi)部質(zhì)量好的優(yōu)點, 擴大國內(nèi)低壓鑄造技術在鋁合金缸蓋的生產(chǎn)應用, 以適應我國 轎車工藝快速發(fā)展。 ( 鎂合金壓鑄工藝難成功的原因與新工藝選擇 鎂合金壓鑄工藝難成功的原因與新工藝選擇 對鋁合金材料或鋁合金壓鑄工藝有所認識的人都知道, 鋁合金分含硅高 (約 10% )的 “壓鑄鋁合金 ”、含硅中等(約
28、 5% ),適合重力鑄造、低壓鑄造或金屬模鑄造的 “鑄造鋁合金 ”,以及適用于擠壓、鍛壓等壓力加工,含硅量很少( 1%-2% 以下)或基本不含硅的 “變形鋁合金”。 不少人以為,在鋁合金或鎂合金中加硅,主要是為了增加合金的流動性,其實并不全面正確,且有認識的偏差與誤導。 在合金中加硅,作用主要確有兩項: 第一是增加流動性。 但這主要是對重力鑄造等很低的壓強下充型而言的。檢測與實踐都表 明,不加硅的合金與加了硅的合金,在超過 1MPa 的充型壓強下充型,差異并不大。當今 的壓鑄機與壓鑄工藝, 充型壓強可以超過 100MPa
29、 ,即使是最差流動性的合金 (變形鋁合金、變形鎂合金等) ,都不存在充型不足的困難。 第二是減少 “液 — 固 ”相的相變體積收縮率 —— 這一項才是最重要與最關鍵的。有研究指,含硅量到 20% 左右的鋁合金(如 A390 ),相變體積可以基本不變。所以,用于高溫場合的鋁活塞,總是硅含量較高的合金。因為壓鑄工藝的本質(zhì)特性,屬單方向的高壓強充型鑄造, 不具有反向補縮功能, 這是它與低壓鑄造、 重力鑄造具有反向補縮充型的工藝特性完全不同 的地方。正是這個原因, 行業(yè)上才特意配制相變收縮率比較低,含硅量盡量去到最高, 專門 為了壓鑄工藝不能反向補縮的鋁合金牌號。
30、 增加硅在合金中的含量會付出很大的代價:大幅削弱了合金的強度,并使合金變脆,延伸 率顯著降低。壓鑄鋁合金(如 ZL107 、 ADC12 )普遍就比變形鋁合金的強度低了一半甚至 大半,約在 200MPa 范圍。對比 A356 、6061(LY 硬鋁)、ZL101 合金強度在 400MPa ,7075 ( LC 超硬鋁)強度達 600MPa 就可知了。硅還是非金屬,不能陽極氧化與著色。故從本質(zhì)上說,硅對合金歸屬為一種有害的或雜質(zhì)類的元素。 所以,我們一般都將壓鑄件稱為方,如有高強度、延伸率高(不脆)合金基本就不能用了。 “結構件
31、 ”,很多功能上有要求,被稱為 “功能件 ”所用的地、耐高溫、表面著色、耐沖擊韌性要求等場合的,壓鑄 實踐上,用壓鑄工藝生產(chǎn)含硅量在 5% 左右的鑄造類合金(如生產(chǎn)鋁合金輪轂的 A356 、 ZL101 牌號合金),毛坯合格率明顯降低,縮孔縮松非常嚴重。原因在于,該類鑄造合金的 體積收縮率較大,本來就只適合于有補縮系統(tǒng)的鑄造工藝的(如重力鑄造、 金屬模鑄造、低 壓鑄造)。用沒有補縮系統(tǒng)的壓鑄工藝生產(chǎn),明顯勉為其難,縮孔縮松缺陷又怎不明顯增加 呢。 現(xiàn)時的壓鑄機,能產(chǎn)生一定補縮作用的手段有兩個: 一是加快壓射的速度,讓熔體
32、有一定的動能(加速) ,這會產(chǎn)生一定的補縮作用,卻極不可靠,且實踐上也是可笑的 —— 加大壓射速度,不就更容易卷氣產(chǎn)生氣孔缺陷了嗎? 二是靠壓射沖頭的 “加力 ”(幾十年前所稱的 “精速密壓鑄 ”)。請注意,壓射沖頭的 “加力 ”,本質(zhì)上只是加了壓強,而不是直接加力于毛坯體本身物理概念的做功(鍛壓) 。這種 “加力 ”,可理解為重力鑄造或低壓鑄造中對一個位置的補縮 —— 這同時還要加大內(nèi)澆道(所謂大水口)才能有效果。 但對于需在多個位置進行補縮的毛坯, 單靠壓射沖頭的作用顯然生產(chǎn)不出 合格產(chǎn)品。兩者相比,以壓射沖頭的 “加力 ”,作用遠好于對熔體的 “加速 ”充型。
33、 現(xiàn)時的 “多功能 ”低壓鑄造機,其實是將復雜的重力鑄造充型與補縮系統(tǒng)機械化,本質(zhì)上已是 “中低壓鑄造充型 +多點擠壓鑄造補縮 ”,具有多工位補縮的工藝裝備:即熔體的充型速度 與壓力, 實現(xiàn)無級調(diào)節(jié)的機械化, 同時具有對毛坯多個需補縮的位置的壓力強制補縮。 這種“低壓鑄造機 ”,其實就是用了多向連鑄連鍛、多向壓鑄模鍛的工藝思路,只是缺了對毛坯主 投影面進行鍛壓的功能而已。 回過頭來看, 就知道鎂合金壓鑄為什么艱難: 它與用壓鑄工藝生產(chǎn) A356 、ZL101 、ZL203等重力鑄造鋁合金毛坯, 碰到的是同一類問題 —— 如何補縮的問題, 卻是
34、難度甚高、 極大的問題。因為現(xiàn)時的鎂合金牌號,只有含硅量很低( 1%-2% )、體積收縮率極大的 “鑄造鎂合金”,而根本沒有體積收縮率比較低的 “壓鑄鎂合金 ”。其難度 (主要是體積收縮率極大與變形合金所需的壓力加工特性 —— 高位合金極易晶粒粗大與偏析) ,相當于用壓鑄工藝生產(chǎn) 6061 、6063 合金,相當于挑戰(zhàn)壓鑄工藝那不可思議的絕對禁區(qū)! 這就得出兩個極重要的結論: 一是現(xiàn)時的鑄造牌號鎂合金, 只應適用于擁有多功能的具有復雜良好補縮系統(tǒng)的低壓鑄造 裝置生產(chǎn), 而基本不適合沒有補縮能力的壓鑄工藝生產(chǎn)。 別相信現(xiàn)時的所謂 “鎂合金壓鑄機 ”,
35、 因為它只是相對于傳統(tǒng)壓鑄工藝僅提高了壓射充型的速度,但這能起到的補縮作用卻甚差,比以壓射沖頭的加力作用與 “大水口 ”工藝還要差得多。 可以說,以傳統(tǒng)壓鑄工藝,或所謂的 “鎂合金壓鑄機 ”生產(chǎn)鎂合金壓鑄件,其 “成功 ”只具有 偶然性或特殊性,不具有普遍性與工業(yè)性;以傳統(tǒng)的壓鑄工藝(包括所謂的鎂合金壓鑄機) 搞鎂合金壓鑄件生產(chǎn), 根本就是選錯了裝備走錯了方向, 工藝基本不可行, 不具工業(yè)上的普 遍適應性,更多的會以失敗告終 —— 如同以壓鑄工藝生產(chǎn) 6061 、 6063 、5052 、 2024 等變 形鋁合金材料一樣的慘敗告終。
36、二是改用具有多向強制補縮與多向鍛壓功能的多向壓鑄模鍛、 產(chǎn),直接生產(chǎn)出如壓鑄件一樣結構復雜的鎂合金鍛壓件。 形鋁合金鍛壓件,也能生產(chǎn)完全不含硅的變形鎂合金鍛壓件。 多向連鑄連鍛工藝與裝備生 這項工藝, 可生產(chǎn)完全不含硅的變 連鑄連鍛、壓鑄模鍛工藝裝備,源于強制鍛壓補縮的液態(tài)模鍛工藝思維,是直接擠壓鑄造 (液態(tài)模鍛、熔湯鍛造)與間接擠壓鑄造工藝相結合的技術,是我國原創(chuàng)的發(fā)明專利技術,已相當成熟可靠,已在廣東肇慶鴻銀機電科技有限公司實現(xiàn)工業(yè)化生產(chǎn)。 下蓋壓鑄模的設計和制造 摘要:本文以下蓋鑄件為例詳細闡述了兩
37、板式側(cè)澆口 壓鑄 模具的結構設計要點與工作過程。 筆者結合自己多年實踐經(jīng)驗,通過采用華鑄 CAE 軟件進行流動分析,最后得出了一道合理 而實用的澆鑄、 排溢系統(tǒng)方案, 使得模具的壓鑄缺陷大大降低, 進而提高了鑄件的內(nèi)在質(zhì)量 和改善其工作性能。 壓鑄是近代金屬加工工藝中發(fā)展較快的一種高效率、 少無切削的金屬成型精密 鑄造方法。與 其他鑄造方法相比, 由于壓鑄工藝的生產(chǎn)流程短、 工序簡單而集中, 不需要繁多的設備和龐 大的工作場所, 且鑄件質(zhì)量優(yōu)、 精度高、 表面光潔度好, 所以不僅可以節(jié)省大量的機械加工工序、設備和工時,而且具有金屬工
38、藝出品率高,節(jié)省能源、節(jié)省原材料等優(yōu)點,所以壓鑄 是一種 “好、快、省 ”的高經(jīng)濟效益的鑄造方法。目前,壓鑄這種工藝方法已廣泛應用在國民經(jīng)濟的各行各業(yè)中,如兵器、汽車、摩托車和航空航天行業(yè)的產(chǎn)品零部件,以及電器儀表、無線電通信、電視機、計算機、農(nóng)業(yè)機具、醫(yī)療器械、洗衣機、電冰箱、鐘表、照相機、建筑裝飾和日用五金等各種產(chǎn)品零部件的生產(chǎn)方面。 現(xiàn)在我國生產(chǎn)的一些壓鑄件,最小的只有幾克,最大的鋁合金鑄件重達 50kg ,最大的直徑 可達 2m 。一些國家則依靠技術進步促使鑄件薄壁化、輕量化,因而導致以往以鑄件產(chǎn)量評 價一個國家鑄造技術發(fā)展水平的觀念發(fā)生了根本性的改變,
39、 轉(zhuǎn)而用技術進步的水平作為衡量 一個國家鑄造水平的重要依據(jù)。 而鑄件質(zhì)量的好壞最終取決于壓鑄模結構設計、 澆注系統(tǒng)設 計以及排溢系統(tǒng) (包括抽真空 )設計是否合理。 圖 1 所示殼體屬于多筋類零件,成型非常困難,因此對該模具的設計提出了更高的技術要 求。在優(yōu)化該模具結構的基礎上,筆者通過應用華鑄 CAE 軟件進行模擬流動分析,最后得 到了一個合理的流動設計方案, 并在此基礎上通過采用溢流排氣系統(tǒng)來減少壓鑄缺陷, 從而 保證了鑄件的質(zhì)量和外觀。 鑄件 一
40、、鑄件工藝分析 該下蓋鑄件最小壁厚 =1.2mm ,易造成鋁液填充不良,成型困難,使鋁合金熔接不好,鑄件表面易產(chǎn)生冷隔等缺陷,并給壓鑄工藝帶來困難。 該零件材料為鋁硅合金,除鋁以外的雜質(zhì)總量 ≤0.6%,抗拉強度 ≥345MPa,屈服強度 ≥180 MPa ,延伸率 ≤ 1.6%,硬度 HBS≤ 160 ,外觀鋁錠為銀白色,產(chǎn)品壓鑄成型后表面應平整光 潔,粗糙度達到圖樣規(guī)定的要求,不得有影響該產(chǎn)品外觀和裝配的變形、裂紋和錯邊, 非加 工表面不得有嚴重的流痕、拉傷、冷隔、縮陷、氣泡、飛邊、欠鑄和多肉等工藝缺陷。 該零件斜度的作用是減少鑄件與模具
41、型腔的摩擦, 容易取出鑄件, 保證鑄件表面不拉傷, 從 而延長壓鑄模使用壽命,故將其脫模斜度設定為外表面 (單邊 ) 3,內(nèi)表面 (單邊 )4 ,芯銷 孔 (單邊 )3 。在壓鑄件的連接處采用適當?shù)膱A角 (3) 過渡, 避免零件上因沒有圓角的存在而 產(chǎn)生應力集中導致開裂, 可以延長壓鑄模的使用壽命, 不因模具型腔尖角的存在而導致崩角 或開裂。 為了不影響產(chǎn)品外觀,決定采用如圖 1 所示的側(cè)澆口進料,通過排溢系統(tǒng)進行抽真空,加 快鑄件的完整成型和收集料流前鋒的雜質(zhì)和冷料等,從而大大減少氣孔和夾渣等現(xiàn)象的產(chǎn)生,確保鑄件成型
42、質(zhì)量優(yōu)良及其外觀。 壓鑄成型工藝條件為:收縮率為 0.55% ,壓室直徑為 95mm ,每模周期為 40s ,低速壓鑄速 度為 (0.26 0.05)m/s ,高速壓鑄速度為 (2.1 0.2)m/s ,高速壓鑄起點位置為 (260 20) mm , 鑄造壓力為 (67.7 1.9)MPa ,料餅厚度為 (20 5)mm ,湯溫為 (660 20) ℃,留模時間為 (13 2) s,模溫為 (160 20) ℃。 二、模具結構設計 1.分型面的選擇 分型面是壓鑄模具動模和定模的接合面, 主要根據(jù)鑄件的具體結構確定。 分型面在
43、鑄件上會留下痕跡, 該痕跡稱為分型線。 因此在選擇分型面時,要充分考慮一些注意事項, 以避免由于分型面的選擇不當所造成的不良影響。 在綜合考慮鑄件順利脫模、 澆口布置和模芯的機加工工藝性等幾方面因素的前提下,最后決定采用如圖 2 所示的分模設計方法。 鑄件分模設計 2.澆注系統(tǒng)及排溢系統(tǒng)的設計 該模具采用 1 模 1 腔結構,由于鑄件正反面都有加強筋,成型又非常困難,只能開設 3 個 大截面?zhèn)葷部谶M料, 采用分流錐導流, 且分流
44、錐與澆口套采用 6錐度研配, 料餅厚度約為 2 3mm 。整個澆注系統(tǒng)是由直澆道、橫澆道與內(nèi)澆口三部分組成,橫澆道截面形狀大體為扇形,根部及角落處需倒圓角以進行更好地引流。橫澆道和內(nèi)澆口分別開設在動、定模芯上, 為了保證鑄件成型完全,盡量采用較大截面的內(nèi)澆口。通過運用華鑄 CAE 軟件進行流動分析,最后得到如圖 3 所示最佳的測澆口數(shù)量與位置,合理的流道系統(tǒng)形狀和排布位置,并 對模芯尺寸、 內(nèi)澆口尺寸和直橫流道尺寸等進行優(yōu)化設計, 最終得到一種切實可行的流動設計方案。 為了改善壓鑄件內(nèi)部組織和減少壓鑄缺陷,最后決定在產(chǎn)品末端開設溢流槽 (圖 3) ,
45、其后又開設排氣槽并進行抽真空處理, 以便能及時排出型腔中的氣體、 氣體夾雜物、 涂料殘渣及冷污合金等, 作為保證鑄件質(zhì)量和消除某些壓鑄缺陷的重要措施之一。 排氣槽設在分型面及溢 流槽的尾部,排氣槽深度 ≤0.4mm,寬度為 10mm ,并且采用曲折排氣槽進行排氣,以防溢流,同時鑄件還可利用模芯和鑲塊的配合間隙以及頂桿與頂桿孔的配合間隙進行排氣。
46、 下蓋壓鑄模 3.脫模機構設計 為了順利頂出鑄件, 在該模具下端面周向均勻設置頂桿進行頂出。 整個脫模機構采用復位桿 (圖 3 中 24) 進行復位,通過推板導柱 (圖 3 中 28) 和導套 (圖 3 中 29) 進行導向定位。同時, 依靠限位 螺釘 (圖 3 中 23) 和前限位柱 (圖 3 中 26) 進行限位,并且加工時必須保證 4 個限位 螺釘和 4 個前限位柱分別等高,以保證鑄件頂出時平穩(wěn)可靠。 4.模溫調(diào)節(jié)系統(tǒng)設計 該模溫調(diào)節(jié)系統(tǒng)主要根據(jù)動、 定模芯的結構特點以及模
47、具元件的分布來布置水道。 為了避免 冷卻水道與相關的模具元件不發(fā)生干涉,且不影響其冷卻效果,決定采用如圖 3 所示的一 進一出的冷卻水道,以增加其冷卻效果。水道直徑為 10mm ,并在動、定模芯進水口與出水 口處安裝銅制冷卻水管, 而模具上所有冷卻水管全部集結在壓鑄機的鋼制積水包上。 為防止 分流錐處熱量過于集中,在分流錐 上采用如圖 3 所示的分流錐嵌件 (圖 3 中 38) 進行導流冷 卻處理。分流錐 (圖 3 中 36) 與澆口套 (圖 3 中 33)的冷卻水道直徑為 8mm ,均為一進一出的 冷卻水路。同時,合模前壓鑄機噴淋裝置會自動噴冷卻液來冷卻模具。
48、 5.模具結構及工作過程 該模具屬于兩板模,其最大外形尺寸為 800mm 800mm 700mm ,模架定制。根據(jù)鎖模力 大于脹型力的設計原則,以壓鑄模厚度和允許開模距離為依據(jù),最后決定選用 UBE900t 壓 鑄機。 模具所有活動部分保證定位準確, 動作可靠,不得有任何歪斜和卡滯現(xiàn)象, 固定零件 不得有相對竄動,其結構如圖 3 所示。 模具工作過程為:動、定模合模,熔融鋁液通過湯勺 (其規(guī)格為 2.1Kg) 注入模具澆口套 (圖 3 中 33) 中,通過壓鑄機的沖頭將鋁液壓入密封型腔內(nèi),經(jīng)
49、保壓、冷卻后,開模。開模時,動、定模分開,到達設定開模行程 400mm 后,壓鑄機頂出油缸開始工作,模具頂出機構在裝有 油缸的壓鑄機頂桿帶動下將鑄件從動模芯 (圖 3 中 8) 中頂出,當運動到設定頂出行程 40mm 后取出鑄件 (含定模側(cè)的流道、積渣包及氣道中的凝料 )。接著壓鑄機噴淋裝置會自動噴冷卻 液來冷卻模具, 隨之動、 定模合模, 壓鑄機頂出油缸帶動模具頂出機構復位,一個壓鑄周期也隨之完成。 三、壓鑄模選材和熱處理要求 在進行壓鑄模具設計時, 選材非常重要, 如果模具材料選擇得不恰當, 很可能會影響模具的 使用壽命和工作效率, 因
50、此,必須嚴格按照制造工藝合理選擇模具材料。 材料選擇好后還必須制訂嚴格的熱處理方法和硬度, 如果熱處理不當, 很可能導致模具壽命急劇下降, 從而影響公司的正常生產(chǎn),如表所示。 四、模具組裝技術要求 壓鑄件尺寸精度的高低主要取決于模具的組裝技術要求, 為了生產(chǎn)出優(yōu)質(zhì)的壓鑄件, 必須對 模具的組裝提出嚴格的要求。該模具的的組裝技術要求如下。 (1) 模具分型面與安裝平面或支承面之間的平行度偏差, 在 200mm 長度以內(nèi)不大于 0.05mm 。 (2) 模具安裝在壓鑄機上時,其分型面應保持良好的閉合狀態(tài)。允許有不大于 0.0
51、5mm 的間 隙( 排氣槽除外 )。 (3) 成型鑲塊和澆口系統(tǒng)零件的分型面不允許低于模板分型面,其高出不得大于 0.1mm 。 (4) 導柱和導套在裝配后,其軸線與模板平面的垂直度偏差,在 200mm 內(nèi)不大于 0.03mm 。 (5) 模具的各活動零部件裝配后應靈活,在室溫狀態(tài)下用手施力時,各相互關聯(lián)的活動零部件不應產(chǎn)生卡滯現(xiàn)象。 (6) 頂桿允許高出成型表面不超過 0.1mm ,復位桿則應與定模的分型面接觸為準,允許低于分型面不超過 0.05mm 。 (7) 推桿在推桿固定板中應靈活轉(zhuǎn)動,允許其軸向竄動量不
52、大于 0.05mm 。 (8) 模具上開設的排氣槽應呈曲折狀引出,其深度在 0.1 ~ 0.15mm ,嚴禁將排氣槽從型腔直 接引向操作者的一側(cè)。 (9) 流道轉(zhuǎn)接處應光滑連接,鑲拼處應密合,拔模斜度 ≥ 5表面粗糙度。, Ra≤ 0.4 μm。 五、結束語 該模具設計在克服壓鑄件成型時間短、多筋類薄殼鑄件成型較為困難等工藝缺陷的基礎上, 通過合理采用側(cè)澆口進料
53、來澆注壓鑄件, 經(jīng)生產(chǎn)實踐驗證, 該模具結構設計合理, 動作平穩(wěn)、可靠,壓射出的壓鑄件尺寸精度高,表面平整、光潔,無任何影響外觀和產(chǎn)品性能的變形、 裂紋和錯邊等工藝缺陷。 (end) 影響鋁擠壓模具壽命的因素探討 1、前言 延長擠壓模具的使用壽命一直是鋁加工企業(yè)十分關注的問題, 模具壽命的長短直接影響 到企業(yè)的生產(chǎn)效率及產(chǎn)品成本, 采取哪些得力措施來延長模具的使用壽命, 不少企業(yè)都有自 己的獨到之處。 為了更好地改善鋁擠壓模具的質(zhì)量和提高其使用壽命, 本文從模具的材質(zhì)選 擇、模具的優(yōu)化設計、 熱處理工藝的選擇與模具的科學使用四個方面作了
54、剖析, 并有針對性 地提出切實可行的對策。 2、影響因素分析 2. 1 模具材料性能的影響 擠壓模具是在高溫高壓下作業(yè), 并承受周期載荷的作用, 因此對模具鋼的性能要求相當高,一般制造模具的材料應具有熱穩(wěn)定性、熱疲勞性、熱耐磨性和足夠的韌性。前些年國內(nèi)常采用 3Cr2W8V 鋼制造模具,但它的韌性低,抗疲勞強度不好,即使采用高溫淬火等工藝 處理措施亦不能滿足要求,模具的早期失效十分嚴重,近年來已被優(yōu)質(zhì)模具鋼 4Cr5MoSiV 1( H13 鋼,其化學成分見表 1 )所取代,與 3Cr2W8V 鋼相比, 4Cr5MoSiV1 鋼具有兩個 突出特點:一
55、是有良好的高溫綜合性能和較高的熱疲勞抗力;.二是組織中含有較多的 Cr 、 Mo 元素,氮化處理時能生成豐富穩(wěn)定的氮化物并彌散分布。所以,就延長模具的使用壽命 而言,選用 H13 鋼加工模具還是比較合適的。統(tǒng)計數(shù)字表明:用 H13 鋼和 3Cr2W8V 造同種模具,前者的使用壽命是后者的 3~ 5 倍。 鋼制 表 1 4Cr5MoSiV1 的化學成分 2. 2 模具設計方案的影響 模具設計的合理得當, 是延長其使用壽命
56、的重要環(huán)節(jié)。 擠壓鋁型材一般存在斷面不對稱 和壁厚不相等現(xiàn)象, 在設計模具時應給予重視, 既要考慮??孜恢玫呐帕?, 又要結合具體情 況,通過改變??坠ぷ鲙У母叨葋砀纳平饘俚牧鲃有浴?下面就模具設計存在的一般問題略作 分析: ( 1)對于壁厚不相等的型材,采用不等長工作帶的方法設計。見圖 1 的丁字型材,通 常依據(jù)經(jīng)驗公式 h1/h2 = b1/b2 來確定工作帶的高度。 式中 h1 、 h2----表示截面處的相應工作帶高度; b1 、 b2----表示截面處的相應型材厚度。 因為這樣設計更能保證金屬流動的均勻性。
57、 圖 1 壁厚不相等的丁字型材 ( 2)適當調(diào)整過渡圓角的半徑和工作帶長度,以避免應力集中現(xiàn)象。見圖 1 , A 處過 渡圓角流動阻力較大,金屬不易充滿,此處工作帶的設計應稍小于正常值,而 B 處過渡圓 角的流動阻力就較小,金屬易充滿,對應的工作帶長度應略大于正常值。 ( 3)??壮叽绲拇_定應綜合考慮型材性質(zhì)和模具材料的收縮率,對于 6063 鋁合金與 常用模具鋼 4Cr5MoSiV1 ,
58、設計時模孔的收縮率應取 1. 01% -1 . 09% (可根據(jù)??壮叽? 的大小適當選?。?。 ( 4)根據(jù)延伸系數(shù)確定模孔數(shù)目。??讛?shù)目直接影響到延伸系數(shù)的大小,擠壓比過大 會使擠壓力超過正常值而損壞模具, 過小則會使擠壓制品的機械性能下降, 一般擠壓系數(shù)(延伸系數(shù))宜在 10 -50 之間。 ( 5)合理布置??孜恢?。在設計時不宜將模孔布置得過于靠近邊緣,否則將會降低模 具強度,導致死區(qū)金屬參與流動而影響制品表面質(zhì)量。擠壓三角型材時,圖 2 的??撞贾镁捅容^適宜。
59、 圖 2 角型材??撞贾脠D 2. 3 熱處理工藝的影響 要延長模具的使用壽命, 熱處理工藝的恰當與否甚為重要, 影響熱處理質(zhì)量的主要因素有加熱速度、淬火溫度、 淬火速度和回火溫度等。 經(jīng)過分析與實踐,下列熱處理工藝適合一 般企業(yè),能滿足 4Cr5MoSiV1 鋼在高溫下的機械性能要求(見圖 3 )。 圖 3 4Cr5MoSiV1 鋼的熱處理工藝示意圖 ( 1)預熱:溫度為 600 - 630 ℃,保溫時間為 1 . 5- 2. Oh (視模具大小而定),然 后
60、升溫到 830 ~ 850 ℃,保溫 1 .5- 2 .Oh 。此工藝過程為淬火前的預處理,它能合理調(diào)整工件內(nèi)部的微觀缺陷,為淬火準備必要的條件。 ( 2)淬火:在預處理的基礎上,把加熱溫度升高到 1040 - 1080 ℃,保溫 2 - 2.5h 出爐油淬,待工件溫度降到 130 ℃左右時從油中取出空冷。 (3)回火:淬火后的模具內(nèi)部有較大的內(nèi)應力,必須在 1 ~2h 內(nèi)對工件進行回火,以 消除淬火時產(chǎn)生的應力。 為了避免工件開裂, 回火前也應加熱均勻,具體方法為: 把工件加 熱到 380 -400 ℃保溫 1 小時左右再緩慢升溫到 580 - 600 ℃進行一
61、次回火, 保溫時間為 2.O h,然后出爐空冷至常溫后進行二次回火,回火溫度為 560 - 580 ℃,保溫時間為 2h ,隨后 出爐空冷。 針對上述熱處理工藝,需要補充說明的是:由于 4Cr5MoSiVI ( H13 )鋼對淬火溫度很 敏感(見圖 4 ),且在高溫下的淬火性能優(yōu)良,所以應對其實行高溫淬火。 圖 4 淬火溫度與疲勞強度的關系 2. 4 模具使用機制的影響 要延長模具的壽命, 科學地使用模具也是不容忽視的一個方面。 由于模具的工作環(huán)境極為惡劣 (高溫高壓), 生產(chǎn)中要采取一定的措施來確保它
62、的組織性能。以下列出要注意的三 個重要方面: ( 1)采用適宜的擠壓速度。在擠壓過程中,當擠壓速度過快時,會造成金屬流動不均 勻、模具溫度較高等現(xiàn)象, 如果此時金屬變形產(chǎn)生的余熱不能及時帶走,模具就可能因局部 過熱而失效,當擠壓速度較適宜時,就避免了上述不良后果的發(fā)生,擠壓速度一般控制在2 5mm/s 以下。 ( 2)采用低一高一低的使用強度。模具剛進入服役期時,組織性能還處在浮動階段, 此時應采用低強度的作業(yè)方案, 使模具向平穩(wěn)期過渡; 模具使用中期, 可適當提高使用強度, 因為此時模具的綜合性能處在最佳狀態(tài); 到模具的使用后期, 其
63、內(nèi)部組織已部分惡化, 熱疲勞強度也較低,應適當降低模具的使用強度,以免使用中出現(xiàn)模具變形、裂紋等缺陷。 ( 3)使用前期對模具進行反復氮化處理。滲氮處理能使模具在保持足夠韌性的情況下大大提高其表面硬度,以減少模具使用時的熱磨損,但表面氮化并不是一次性就能完成的, 在模具服役期間, 應對之進行 3 - 4 次反復滲氮處理, 一般要使氮化層厚度達到 0.15- 0.2 0mm 。 3、結束語 擠壓模具的使用壽命是一個綜合性的技術問題,以上介紹的四個方面只是其中的部分,要全面理解模具使用壽命的含義, 在模具的加工制造中選擇最佳工藝和模具使用后的及時修正,對延長模具的壽命
64、也至關重要。 壓鑄模具中的表面處理技術 壓鑄模具是模具中的一個大類。 隨著我國汽車摩托車工業(yè)的迅速發(fā)展, 壓鑄行業(yè)迎來了發(fā)展 的新時期。 同時,也對壓鑄模具的綜合力學性能、 壽命等提出了更高的要求。要滿足不斷提 高的使用性能需求僅僅依靠新型模具材料的應用仍然很難滿足, 必須將各種表面處理技術應 用到壓鑄模具的表面處理當中才能達到對壓鑄模具高效率、 高精度和高壽命的要求。 壓力 鑄 造是使熔融金屬在高壓、 高速下充滿模具型腔而壓鑄成型, 在工作過程中反復與熾熱金屬接 觸,因此要求壓鑄模具有較高的耐熱疲勞、導熱性耐磨性、耐蝕性、沖擊
65、韌性、紅硬性、良 好的脫模性等。 因此,對壓鑄模具的表面處理技術要求較高近年來, 各種壓鑄模具表面處理 新技術不斷涌現(xiàn),但總的來說可以分為以下三個大類: (1) 傳統(tǒng)熱處理工藝的改進技術; (2) 表面改性技術,包括表面熱擴滲處理、表面相變強化、 電火花 強化技術等; (3) 涂鍍技術, 包括化學鍍等。 1 傳統(tǒng)熱處理工藝的改進技術 傳統(tǒng)的壓鑄模具熱處理工藝是淬火 -回火,以后又發(fā)展了表面處理技術。由于可作為壓鑄模 具的材料多種多樣, 同樣的表面處理技術和工藝應用在不同的材料上會產(chǎn)生不同的效果。 史 可夫最近提出針
66、對模具基材和表面處理技術的基材預處理技術, 在傳統(tǒng)工藝的基礎上對不同 的模具材料提出適合的加工工藝, 從而改善模具性能, 提高模具壽命。 熱處理技術改進的另 一個發(fā)展方向, 是將傳統(tǒng)的熱處理工藝與先進的表面處理工藝相結合, 提高壓鑄模具的使用 壽命。如將化學熱處理的方法碳氮共滲,與常規(guī)淬火、回火工藝相結合的 NQN( 即碳氮共滲 - 淬火 -碳氮共滲 )復合強化,不但得到較高的表面硬度,而且有效硬化層深度增加、滲層硬 度梯度分布合理、 回火穩(wěn)定性和耐蝕性提高, 從而使得壓鑄模具在獲得良好心部性能的同時,表面質(zhì)量和性能大幅提高。 2 表面改性技術 2.1 表面熱擴滲技術 這一類型中包括有滲碳、滲氮、滲硼以及碳氮共滲、硫碳氮共滲等。 2.1.1 滲碳和碳氮共滲 滲碳工藝應用于冷、熱作和 塑料 模具表面強化中,都能提高模具壽命。如 3Cr2W8V 鋼制的 壓鑄模具, 先滲碳、 再經(jīng) 1140 ~ 1150 ℃淬火, 550 ℃回火兩次,
- 溫馨提示:
1: 本站所有資源如無特殊說明,都需要本地電腦安裝OFFICE2007和PDF閱讀器。圖紙軟件為CAD,CAXA,PROE,UG,SolidWorks等.壓縮文件請下載最新的WinRAR軟件解壓。
2: 本站的文檔不包含任何第三方提供的附件圖紙等,如果需要附件,請聯(lián)系上傳者。文件的所有權益歸上傳用戶所有。
3.本站RAR壓縮包中若帶圖紙,網(wǎng)頁內(nèi)容里面會有圖紙預覽,若沒有圖紙預覽就沒有圖紙。
4. 未經(jīng)權益所有人同意不得將文件中的內(nèi)容挪作商業(yè)或盈利用途。
5. 裝配圖網(wǎng)僅提供信息存儲空間,僅對用戶上傳內(nèi)容的表現(xiàn)方式做保護處理,對用戶上傳分享的文檔內(nèi)容本身不做任何修改或編輯,并不能對任何下載內(nèi)容負責。
6. 下載文件中如有侵權或不適當內(nèi)容,請與我們聯(lián)系,我們立即糾正。
7. 本站不保證下載資源的準確性、安全性和完整性, 同時也不承擔用戶因使用這些下載資源對自己和他人造成任何形式的傷害或損失。
最新文檔
- 2025年高考政治一輪復習:統(tǒng)編版選擇性必修1-3【共3冊重點知識點匯總】
- 2025年高考政治一輪復習:七冊教材重點考點匯總
- 2025年高考生物一輪復習:高中生物必修+選必修5冊教材重點知識點匯總
- 2025政府工作報告要點速覽發(fā)展總體要求和政策取向
- 《哪吒2》與DEEPSEEK年輕力量的崛起助力中國突破重圍
- 建設金融強國做好金融五篇大文章的指導意見
- 落實高質(zhì)量發(fā)展要求如期完成既定目標任務更新理念科學統(tǒng)籌切實增強規(guī)劃執(zhí)行的系統(tǒng)性整體性協(xié)同性
- 如何成為一名暖護暖護的概念與職責
- 藥品儲存與養(yǎng)護醫(yī)療護理藥品儲存藥品養(yǎng)護藥品常識
- 手術室職業(yè)暴露與防護診療護理等過程中被患者血液體液等污染自身皮膚或黏膜導致的感染
- XX企業(yè)中層管理者領導力提升培訓課程
- 醫(yī)院新員工入職培訓醫(yī)院新員工必備主要職業(yè)意識醫(yī)院新員工必備工作觀
- 人工智能技術介紹人工智能DeepSeek人工智能的未來展望與發(fā)展
- 養(yǎng)娃要有松弛感家庭教育讓孩子在具有松弛感的家庭里慢慢成長
- 醫(yī)院新員工入職培訓醫(yī)院新員工必備主要職業(yè)意識